2025 Author: Howard Calhoun | [email protected]. Last modified: 2025-01-24 13:10
Every commercial enterprise strives to ensure that there are no downtime in its work, which can adversely affect financial results. This business continuity assumes that there is some residual work in progress in processing at the end of the reporting period. The correctness of the calculation of the cost of finished products directly depends on how correctly the volume of work in progress is determined. It is important to be able to evaluate these data correctly, because the size of tax payments and many other indicators depend on them.
What is work in progress
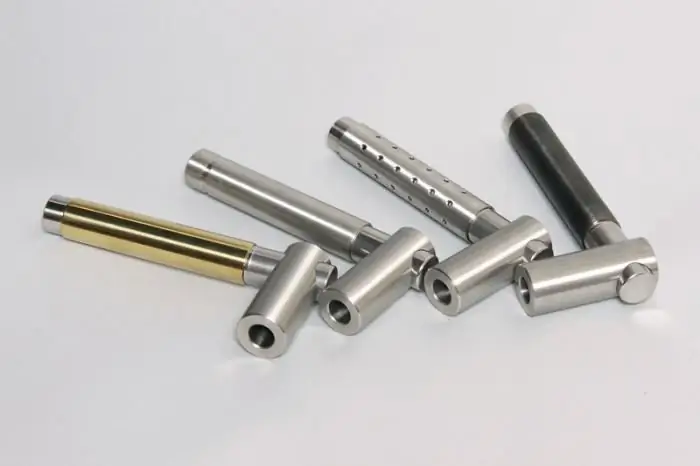
By definition, work in progress is products, goods or products that have not passed all the necessary stages of processing provided for them by technology. Thus, the following types of products may belong to it:
- raw materials and semi-finished products, the processing of which has already begun in order to turn them into finished products;
- short items;
- goods that have not passed the technicalacceptance or required testing;
- completed works (services) that have not yet been accepted by the customer.
In other words, work in progress in accounting is the cost of costs sent to production (materials, resources consumed, depreciation, wages accrued to employees) and other costs for products whose production has already begun, but as of the reporting date was not completed.
This amount of costs collected at the end of the period is not written off to other accounting accounts, but remains on the corresponding production account (for example, 20 or 23). And even if there was no production in the reporting period, but the costs were incurred, then such costs will be accounted for as work in progress. Subsequently, they will be attributed to the cost of finished products. The concept of "work in progress" is encountered even by those enterprises that are engaged in trade or the provision of services and do not produce any products. Costs incurred during the reporting period will be treated as WIP until the goods (services) are sold.
Accounting
The volume of work in progress and its composition are very different for enterprises in various industries. The duration of the production cycle and the amount of costs can vary greatly depending on the nature of the products and the organization of the industrial process. Therefore, work in progress in the accounting of different enterprises can be considered different from each other.ways.
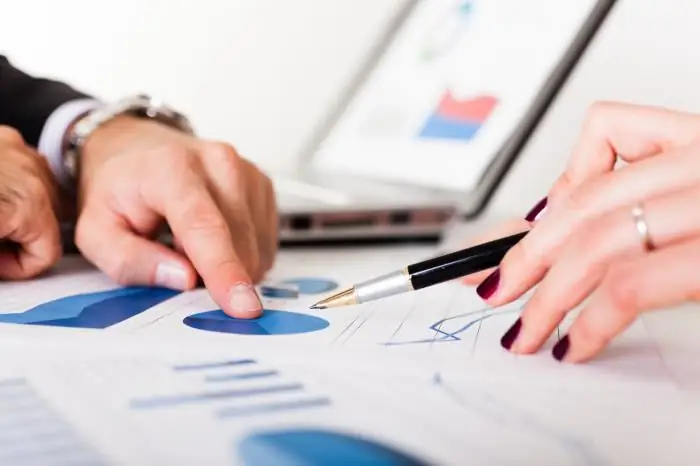
For companies with a long production cycle and for providing complex services (design, scientific, construction, etc.), the sale can be recognized as follows:
- upon completion of all work and signing the necessary documents;
- as each individual stage of work progresses.
In most cases, the first option is used.
Work in progress in accounting is found both in the main and in auxiliary production, as well as in the work of service farms. Accordingly, the information collected on the following accounts of the same name is used:
- score 20;
- score 23;
- score 29.
Debit balances of the indicated accounts at the end of the month - this is work in progress at the enterprise.
For the second case, account 46 "Completed stages of work in progress" is provided. The account collects information about the completed stages of work, each of which has an independent value and is provided for by the concluded contract.
Possible accounting entries involving the account:
Accounting entry | Content of business transaction |
Dt 46 - Ct 90/1 | Revenue recognition in the amount of the cost of one completed stage of work when paid by the customer |
Dt 62 - Ct 46 | Write-off of the full cost of all works paid by the customer aftercompletion of all stages |
Work in progress in the accounting of trading companies involves the balance of unsold products and the costs attributable to it.
In the process of its work, the seller company faces a number of costs: the purchase of goods, the costs associated with the provision of trade services (rental of space, advertising costs, staff salaries, transportation costs, etc.). In trade, these costs are called distribution costs. In the presence of unsold goods, companies cannot fully write off the distribution costs incurred during the reporting period. The amounts of such expenses should be distributed, while the share attributable to the balance of unsold goods remains on account 44 "Sales expenses".
Valuation of work in progress
Russian legislation considers several options for assessing WIP. All of them are spelled out in paragraph 64 of the PVBU. So, let's look at them in order.
Calculation using actual cost
Ultimately accurate method. In this case, all those costs that are associated with the release of products are collected. Its essence lies in the fact that the number of refinery units available at the end of the month is multiplied by the calculated average cost of a refinery unit.
Calculation using standard (or planned) cost

Using this method assumes that the company's economists calculate the accounting (planned) price for a WIP unit. The advantage of the method is thatusing accounting prices, the evaluation of work in progress as a process is greatly simplified. The downside can be considered a more time-consuming process of calculating the cost of finished products. Deviations between accounting prices and the actual cost of WIP must be taken into account on account 20.
Calculation using direct cost items
The peculiarity of the method is that only the amounts of direct costs directly related to production are sent to the cost of work in progress. All other costs are transferred to the cost of finished products. The list of these expenses is determined by the accounting policy of the enterprise.
Calculation based on the cost of raw materials used
This method is similar to the previous one, with the difference that the cost includes only the cost of raw materials released into production (including semi-finished products).
However, these options are not available to all organizations. The choice of valuation method usually depends on the type of production. For a company engaged in piece and single-piece production, only accounting at actual cost is available. Organizations with mass and serial production of products have the opportunity to choose any of the four accounting methods.
Cost of WIP
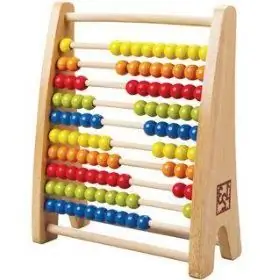
The cost of work in progress is the amount of funds spent on the creation of products (performance of work, provision of services), which at the end of the reporting period is still in the process of processing.
Cost calculation - completelynecessary process. Data on the cost of work in progress and ready-to-release products will be required in the preparation of financial statements. You can't do without them when forming the price and assortment policy of the enterprise.
To understand how the concepts of costs in work in progress and the cost of finished goods are related, consider the following formula:
GP=WIP (balance at the beginning of the period) + Costs - WIP (balance at the end of the period). Where:
GP - the cost of production in the actual estimate;
Costs - production costs per month (debit turnover on account 20);WIP - balances, respectively, at the beginning or end of the month on account 20.
Calculating WIP cost
Economic elements
When managing the cost, it is worth remembering the planning and rationing of expenses. This will require the division of costs into various components in order to analyze the structure and control the change in the value of each of them. In domestic practice, classifications are used according to various criteria. In one of them, the costs are divided into economic elements, and in the other, into costing items.
The composition of economic elements is established by PBU 10/99, it is the same for all commercial organizations:
- cost of raw materials and supplies;
- workers' wages;
- contributions to social funds;
- depreciation;
- other expenses.
Calculation articles
Of course, usually the costs in the unfinishedproduction is not limited to this list. The list of costing items is more extensive and is determined by the enterprise independently, depending on the nature of production. However, the legislation has proposed a model nomenclature, including the following items:
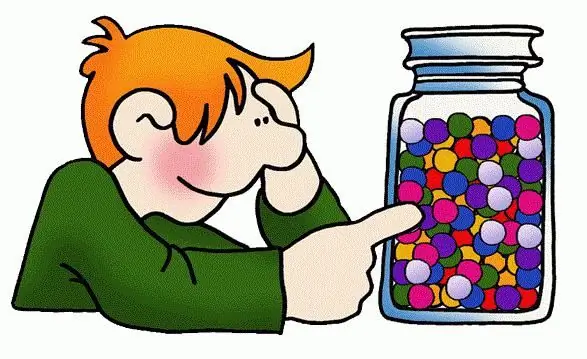
- own raw materials and supplies;
- purchased semi-finished products or products, services rendered from outside;
- returnable waste (string to be subtracted);
- energy and fuel for technological purposes;
- salary of production workers;
- compulsory contributions and contributions to social funds;
- expenses associated with the preparation and development of production;
- general production expenses (maintenance of the main and auxiliary production);
- general expenses (expenses related to management);
- marriage losses;
- other production costs;
- sales expenses (so-called selling expenses).
The first 11 lines form the production cost. In order to calculate the total cost of manufactured products, you need to add up all 12 items.
To effectively manage costs, it is useful to use both of the described groupings.
Inventory of work in progress
No online accounting can guarantee the absolute accuracy of the resulting credentials. In order to clarify them, the organization conducts an inventory. The procedure for its implementation is determined by the Methodological Instructions. Beforeinventory, all materials, parts or semi-finished products for which processing is completed at this stage are handed over to warehouses. The rest of the raw materials, what is already at the workplace, but the processing of which has not yet begun, is recorded separately. The same applies to rejected parts, they cannot be attributed to the rest of work in progress.
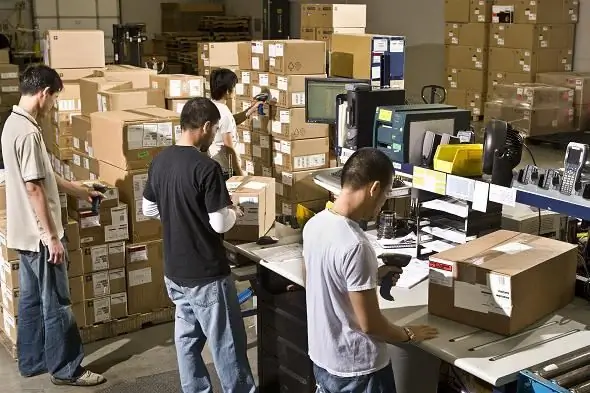
According to current guidelines, an inventory must be carried out before compiling the annual balance sheet. In addition, depending on the specifics of production, enterprises conduct it quarterly or monthly.
The appointed permanent commission, approved by the order of the head, conducts an inventory by weighing, measuring and actually counting. For each separate structural unit, a separate inventory is drawn up, which indicates the names of reserves, their stage or degree of readiness, volume or quantity. Thus, the exact balances of work in progress available at the enterprise are determined.
When the inventory of work in progress is completed, the completed acts are transferred to the accounting department for processing. If discrepancies are identified from the accounting data, collation statements are filled in, and surpluses or shortages are recorded by the relevant accounting entries. The commission needs to identify the perpetrators and the reasons for the deviations found in order to determine the procedure for writing off these amounts.
Accounting entry | Maintenance of economicoperations | |
Dt 94 - Ct 20 | Write-off of the amount found during the inventory shortage within the limits of attrition rates | |
Dt 94 - Ct 73/2 Dt 20 - Fr 94 |
Write-off of the amount of the shortage that occurred due to the fault of the personnel | |
Dt 94 - Ct 91 Dt 20 - Fr 94 |
Write-off of shortage in the event that the perpetrators are not found | |
Dt 20 - Fr 91 | The actual balance of work in progress does not match the accounting data. Surplus identified and credited |
Determination of WIP volume
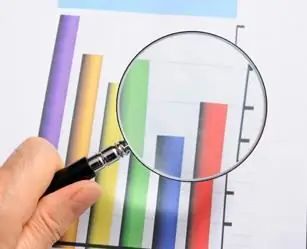
Reducing the amount of work in progress is useful in that it helps to accelerate its turnover, which, in turn, has a direct positive effect on turnover and profit. This can be achieved by reducing the duration of one production cycle while optimizing production and labor at the enterprise. At the same time, inventories in work in progress, their size and composition must be formed in such a way that maximum uninterrupted and rhythmic industrial process is ensured. The definition of these values is called the rationing of work in progress.
The standard of work in progress is the minimum amount of working capital that can ensure the continuous and uniform operation of the enterprise. This value must always be available to the company. For its calculation, there is the followingformula:
WIP=Volume average day x Cycle length x Coefficient. increasing, where:
Average day volume - the cost of production per day (in monetary terms);
Cycle length - the duration of one production cycle (measured in days);Coefficient.increase - cost increase factor.
Thus, it can be seen that the WIP standard is directly proportional to the volume of production of the enterprise, the duration of the industrial cycle and the degree of increase in costs.
Let's consider the content of the formula in more detail.
The average daily output is determined by dividing the value of output per year by the number of working days in a year. Obviously, the work schedule of the enterprise directly affects the final amount.
The length of the cycle means the time required for the raw materials (materials) sent to production to be converted into finished products.
The growth rate shows the degree of completion of products and is calculated using the ratio of the average cost of WIP to the production cost of HP.
Coefficient increase=WIP cost avg.: Cost price of HP production
This is not all the information that you may need to calculate the necessary inventory in work in progress. Experienced economists remember that underestimated volumes can cause the work to "stand up", there will be a shortage of resources, up to the inability of the enterprise to pay its obligations on time. And excess stocks can lead to the fact that the fundswhich could "turn around" and generate income, will come to a state of "freeze". Hence, losses, decrease in profitability and an increase in the amount of payments of various taxes are possible.
Work in progress. Active or Passive?
WIP meets all the necessary criteria to be considered an asset - it is a resource (property) owned by the enterprise and capable of bringing material benefits in the future. In turn, as far as we remember, the balance sheet asset is divided into two important parts: long-term (non-current) and short-term (current) funds.
Work in progress is often one of the main components of the company's working capital. At the same time, work in progress is not separately displayed in the balance sheet of the enterprise. Data about it is contained in the section "Current assets", line "Inventories" (1210). This line contains collective information about the following items:
- inventories;
- deferred expenses (DEP);
- shipped goods;
- work in progress;
- finished products;
- goods for resale;
- other inventory and costs.
For enterprises with a long production cycle, it is possible to display WIP in the "Non-current assets" section.
Work in progress in the balance sheet can be reflected in a separate line. This happens if the cost of it is a significant amount. You will also need to provide more detailed information.in the appendix to the balance sheet and form 2 "Statement of financial results".
WIP in small business reporting
Since 2013, some changes have been made to the procedure for submitting financial statements. New forms have also been developed. The basic principles in them remained unchanged, as before, the balance sheet is divided into two halves: Asset and Liability, the results of which must match. But for small businesses, a simplified form has now been proposed, in which there are no sections, and the number of indicators is less than in the old one. Such a company can independently decide for itself which reporting option to choose, having previously fixed its decision in the accounting policy.
In the new form, as in the previous one, work in progress is an asset of the balance sheet, there is still a line "Stocks" for it. Thus, both the name and line code for small businesses remain the same.
Instead of a conclusion
The topic discussed is quite extensive and complex, especially when it comes to a large industrial enterprise. In our article, we touched on many issues, but, of course, it was impossible to consider all the difficulties and nuances that arise in the work of an accountant when accounting for work in progress.
Recommended:
Accounting documents are The concept, rules for registration and storage of accounting documents. 402-FZ "On Accounting". Article 9. Primary accounting documents
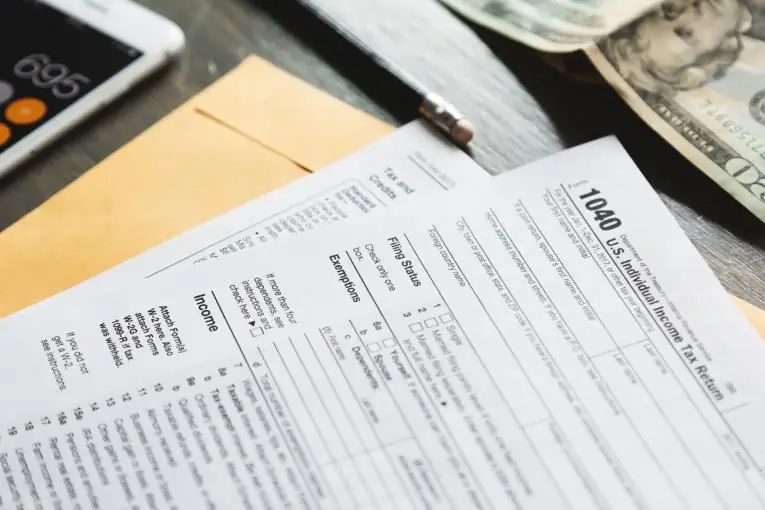
Proper execution of accounting documentation is very important for the process of generating accounting information and determining tax liabilities. Therefore, it is necessary to treat documents with special care. Specialists of accounting services, representatives of small businesses who keep independent records should know the main requirements for the creation, design, movement, storage of papers
Accounting policy for the purposes of tax accounting: the formation of an enterprise accounting policy
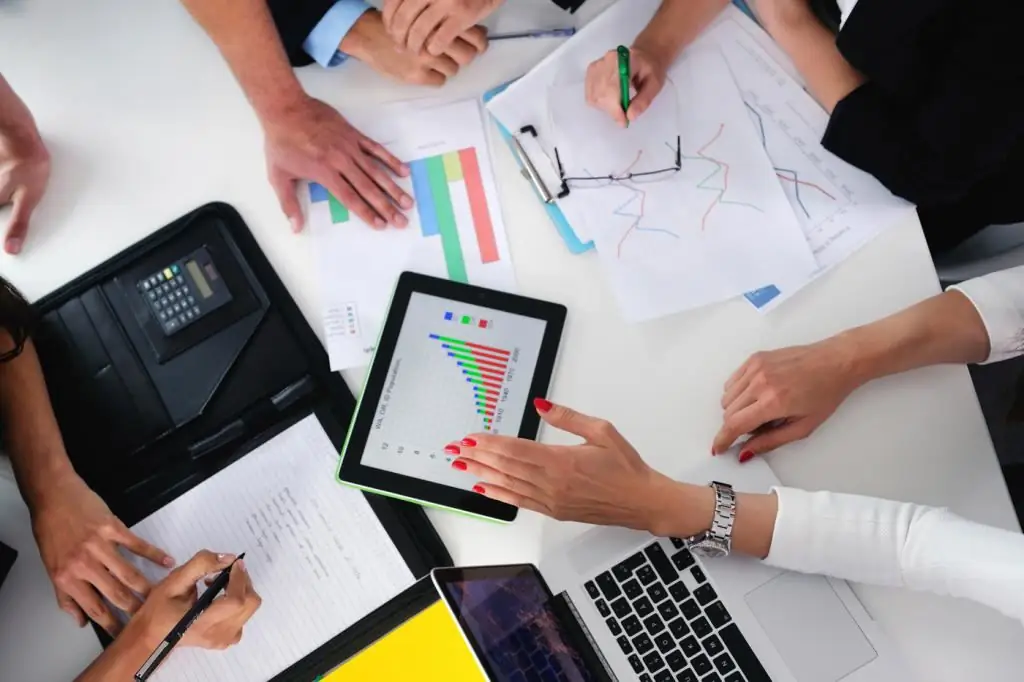
A document that defines an accounting policy for tax accounting purposes is similar to a document drawn up according to accounting rules in accounting. It is used for tax purposes. It is much more difficult to draw up it due to the fact that there are no clear instructions and recommendations for its development in the law
Work permit for work in electrical installations. Rules for work in electrical installations. Work permit
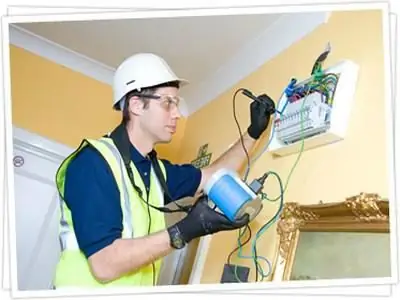
From August 2014, Law No. 328n comes into force. In accordance with it, a new edition of the "Rules on labor protection during the operation of electrical installations" is being introduced
Accounting for working hours in the summary accounting. Summarized accounting of the working time of drivers with a shift schedule. Overtime hours with summarized accounting of wor
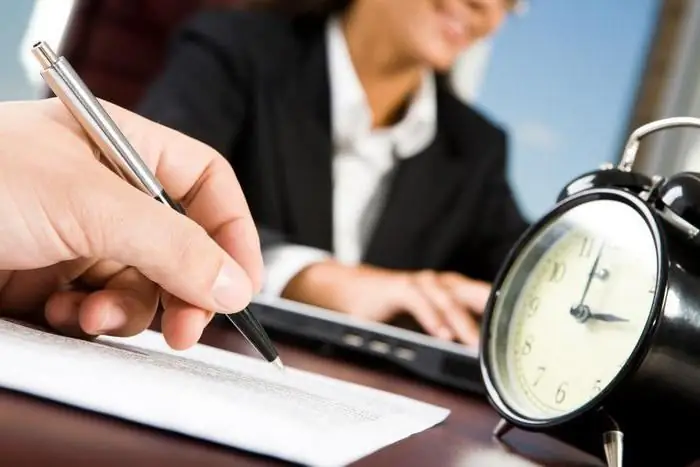
The Labor Code provides for work with a summarized accounting of working hours. In practice, not all enterprises use this assumption. As a rule, this is due to certain difficulties in the calculation
Accounting and tax accounting at a manufacturing enterprise: definition, maintenance procedure. Normative accounting documents
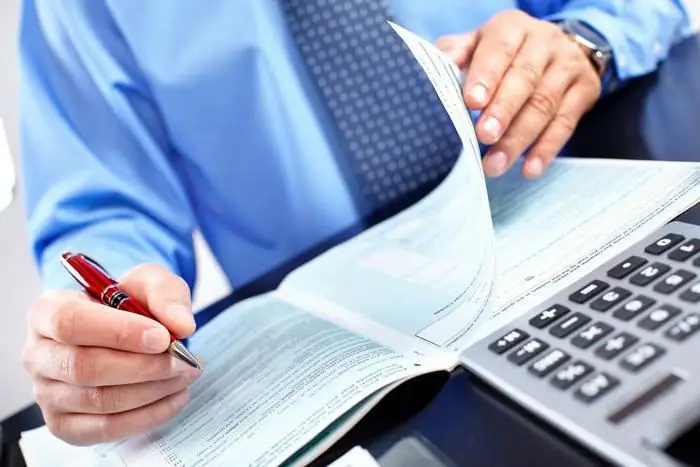
In accordance with PBU 18/02, since 2003, the accounting should reflect the amounts arising from the discrepancy between accounting and tax accounting. At manufacturing enterprises, this requirement is quite difficult to fulfill. The problems are related to the difference in the rules for valuation of finished goods and WIP (work in progress)