2025 Author: Howard Calhoun | [email protected]. Last modified: 2025-01-24 13:10
In the history of mankind, there are many materials that have accompanied people almost from the very beginning of civilization. Wood is the first thing that comes to mind, but don't forget about ceramics - baked clay, which has been used to make dishes since time immemorial.
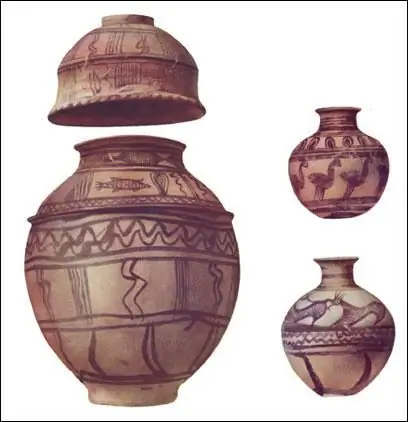
This material has enough positive qualities: ceramic is durable, resistant to chemical and high-temperature influences, it is completely environmentally safe, and everything is in order with its appearance. In addition, fired clay tiles do not rot or become covered with fungus, which makes them suitable for use in a wide variety of technological spaces and bathrooms.
In general, ceramics are dishes or other things made of clay (with or without mineral additives), obtained by molding and subsequent high-temperature firing. To make the appearance of such products more beautiful, they are glazed.
What materials can be used in production?
We have already said that mainly clay is used for these purposes, but there are exceptions. So onceramics can go the following materials:
- Plastic base. This is just the same clay or kaolin (a rock consisting of kaolinite).
- Materials that minimize slump during firing, help keep the shape of the product. High-quality quartz sand, substandard porcelain (fight), fireclay are used.
- Rocks that give a dense glassy mass during sintering. Ideal feldspar, pegmatite.
- Glaze. It can be used as a material from natural raw materials, as well as numerous analogues obtained by chemical synthesis.
Classification
So we learned that ceramics is a specially processed clay. As factors that predetermine the consumer qualities of a product, they distinguish the type of ceramics, the method of decorating or molding them.
Distinguish between fine ceramics (fine granularity on the breaking of the shard) and coarse ceramics (coarse granularity). Of the fine varieties, everyone is familiar with porcelain, semi-porcelain, as well as faience, tiles from which are found in almost every bathroom. Accordingly, rough ceramics (you will find a photo in the article) are pottery pots. The thing is not very common among us, but known from the deepest antiquity.
Properties of different types of ceramics
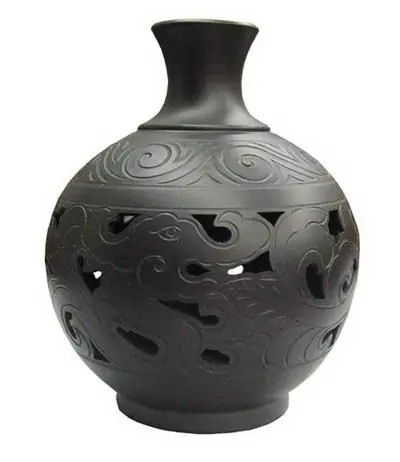
A distinctive feature of porcelain is a thin, dense and white fine-grained shard. The material absorbs moisture very poorly (up to 0.2%). Valuable vases or cups (very thin) can be viewed against the light. The edges of the side (usually the bottom) are not covered with glaze due to the firing technology. Forproduction mainly uses kaolin and feldspar.
Semi-porcelain is an intermediate option between the above-described porcelain and faience. Somewhat coarser, water absorption from 3 to 5%, most often used in the manufacture of household dishes.
As for the faience itself, it is distinguished by a thick porous shard, which has a slightly yellowish tint when broken. The ability to absorb water is high, within 9-12%. It is because of this, and also because of the high porosity, that any ceramics of this type are necessarily covered with a layer of thin glaze.
Since the glazing used is very unstable to thermal effects, this type of ceramics is used exclusively in the production of inexpensive dishes for everyday use, as well as for household containers. For dressing, they take not too high-quality varieties of clay, chalk and quartz sand. The ceramic technology of this grade also allows the use (as a base) of broken porcelain. Of course, before starting production, it is crushed and finely ground.
Majolica is a very attractive externally ceramics. The price for it is about a thousand rubles for an average vase. A distinctive feature is a very porous shard that can absorb up to 15% moisture. Despite this, the products are distinguished by thin shiny surfaces, have a small wall thickness. The latter is due to the fact that majolica is made using casting technology. As a rule, products are decorated with glazing, and decorative bas-reliefs are also often found. In the production of this varietyceramics, white-burning clays, quartz sand, chalk and plavni are used.
Pottery ceramics (the photo of which is in the article). It is distinguished by a shard of a specific red-brown color (red-burning clay) and a very large porosity. Moisture absorption coefficient - up to 18%. For coloring, special clay paints, engobes, are used. To protect them from moisture, the products are covered with a thin layer of colorless glaze on top. As for the scope of use, the range is represented not only by decorative pots, but also quite practical dishes for the household.
In addition, warm ceramics belong to the same category. This is the name of bricks made of roughly fired clay. In the production of this kind of ceramics, special foaming agents are used, which dramatically increase the porosity of the material, and therefore its thermal insulation qualities become much better.
How is the production process?
The production of ceramics itself can be easily divided into several stages:
- Extraction and related preparation of raw materials.
- Shaping, decorating or making functional holes.
- Casting, semi-dry stamping.
- Editing, first drying.
- High temperature treatment.
- Glazing.
- Re-fired.
- Decorative treatment (warm ceramics and analogues do not need it).
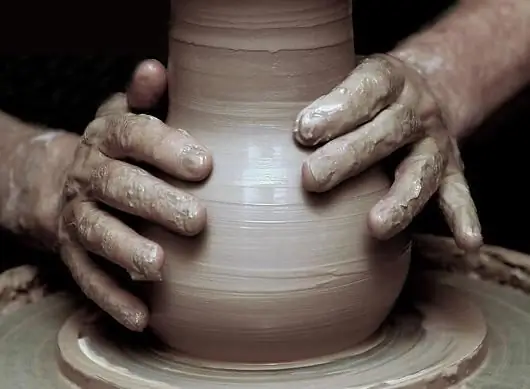
The quality indicators of the finished product are determined by the characteristicsappearance, full compliance with the functional purpose, as well as durability.
Production technology
We talked about the main stages of production, so now let's discuss each of them separately. To prepare the initial ceramic mass, the following technological operations are performed: the raw material is thoroughly cleaned of extraneous mineral and organic impurities, crushed and ground. After that comes the turn of mixing and adding various additives.
Product molding
Shaping is performed from liquid or plastic ceramic masses. Plastic molding has a number of advantages. First of all, this is expressed in the fact that you can make products of almost any shape and size. In addition, even the simplest and most technologically advanced equipment can be adapted for their manufacture.
As for casting, a mass with a moisture content of 34-36% is used for this. Pouring is done in plaster molds. This is an indispensable method for the manufacture of truly complex ceramic products, the shape of which physically does not allow the use of other molding methods. In addition, this is how tiles are made. Ceramics for it are not made from the best grades of clay (below the requirement), but the thickness of the finished products should be as uniform as possible.
Casting can be either manual or fully automated. After the initial drying, the products are taken out of the molds, after which various decorative and functional elements are glued, for the attachment of which it is usedspecial glue. In the past, clay dough was used for this purpose, but it did not provide very high strength.
Drying
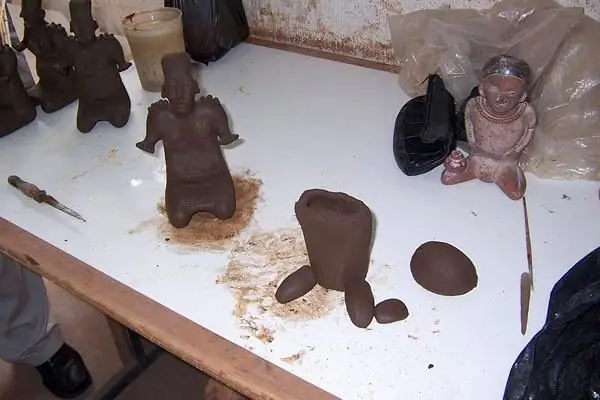
Drying is the most important stage, since both the mechanical strength of the product and its decorative characteristics depend on the correctness of its implementation. Of course, the correct distribution of glaze is also extremely important, on which the resistance of products to water, as well as chemical agents depends. Drying is a prerequisite for the production of ceramics. For it, conveyor, radiation and chamber dryers are used. The temperature throughout the process should not exceed 70-90 °C.
The only exception is tiles. The ceramic in this case is very thick, so in some cases it is possible to use the high temperature mode for a short time.
Firing
The second most important technological step is the firing of ceramics. The goal is to form a crock with precisely specified physical and chemical properties, to fix the coloring composition and glaze on the surface. Firing is important because in its course many physical and chemical processes take place, which predetermine the main consumer qualities of the product. Normally the firing is carried out in two stages, but if paint has been applied to the surface of the glaze, the so-called muffle firing (third stage) is carried out.
The first stage is carried out at a temperature of 900 to 1250 °C (depending on the type and grade of ceramics). The second stage requires a temperature regime from 1020 to 1410 °C. Last valueused exclusively for porcelain. Other ceramics are rarely fired in this mode, as the risk of cracking is high. If we are talking about the average red clay, then products made from it are often “burned” once, at a temperature not higher than 960-1020 degrees Celsius.
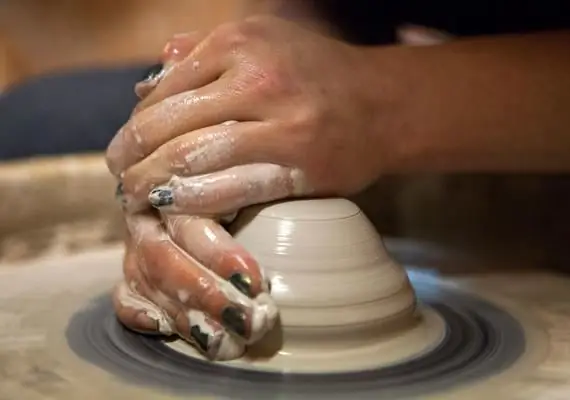
Two types of kilns for ceramics can be used for firing: periodic (forges) and continuous ones. There are a lot of varieties of the latter, but tunnel and roller ones are the most common.
About various defects
The specifics of the manufacture of ceramic products is that at various stages of production, a large number of a wide variety of defects may occur. There are damages to the shard, glaze or decorative coating. As for defects in the shard, they most often appear at the stage of primary molding and initial drying.
Some part of the manufacturing defect appears almost immediately, and stains or something like that appear only after firing. Due to the "capriciousness" of the final product, there is a requirement to strictly control the cleanliness of all tools used in production.
Description of basic concepts
Glaze is a special melt that is applied to the surface of the finished product. Their thickness is 0.12-0.40 mm. The purpose of glazes is quite diverse. Firstly, the surface of the tile or dish is covered with a dense decorative layer, which not only contributes to a pleasant appearance, but also significantly increasesmechanical strength. In addition, the coating provides reliable protection against physical and chemical influences, which is especially important for household utensils.
Decoration refers to the application of decorative coloring or patterns. Often in the conditions of industrial production curly stamps are used, with the help of which the mass production of the same type of products. A stamp roller is used to apply the pattern to the edges of the pot. Accordingly, the final operations are to eliminate minor defects, polish the legs and edges.
Some information about glazes and colors
Glazes are divided into transparent and opaque varieties, they are colored and completely colorless. Ceramic paints are used to decorate almost all types of baked clay products. They are based on either metals or their oxides. When heated, they form stable compounds that are not only beautiful, but also very durable. Such ceramics, reviews of which are always excellent, have long been an adornment in many we althy homes.
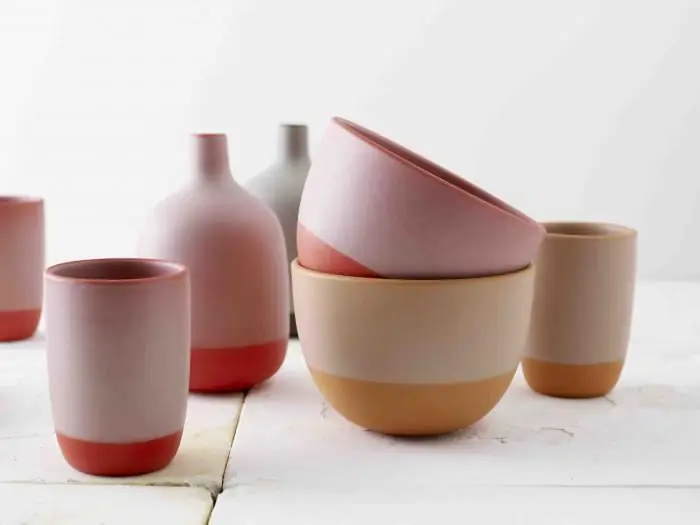
Paints are divided according to the way they are applied: either on the glaze layer, or under it. As you can understand, in the latter case, the coloring composition is applied directly to the shard. Only then it is covered with a layer of glaze, and the product is fired in a kiln. If the composition is applied directly to the glaze layer, it is fixed with a temperature of at least 600-850 ° C.
As for auxiliary materials, they are used to make molds for firing and casting.
Detailsabout making molds
In order to make sufficiently strong and high-quality molds, molding plaster is used. It is made by finely grinding the powder of calcium sulfate hemihydrate. The peculiarity of such gypsum is that when mixed with water, it should turn into a fairly plastic and elastic dough. But the main thing is that this composition must be set in precisely defined terms, which guarantees a really high-quality firing. If for some reason there is no gypsum, carborundum refractory fireclay can be used. Other refractory materials may be used.
That's what pottery is. This is a material without which it is impossible to imagine any kitchen or bathroom. However, there is another variety of it, products from which can be real decorations for any home.
Artistic pottery
Under "artistic" refers to products decorated with particularly fine relief or stucco. Of course, there are actually no other differences from ordinary ceramics, but there are many subtleties in manufacturing technology. We will talk about them now.
Initial preparation of raw materials
As you understand, artistic ceramics are not much different from their "household" counterparts, but in its manufacture it is necessary to be more demanding in the selection of raw materials. Everything is the same as in the previous case, but all operations are performed more subtly. In addition, only finely divided kaolin (particle diameter less than 2 µm) should be used.
What does it give? This approach makes it possible to obtain a much more ductilemass, and also at least doubles the strength of dried products. In addition, only fine quartz sand should be taken, as it dramatically reduces the sedimentation of the finished product, which is extremely important for artistic ceramics.
Drying art pottery
As we mentioned in the first part of the article, drying is one of the most important steps. If we talk about artistic ceramics, then this statement becomes even more relevant. You should be aware that shrinkage phenomena during firing of thin products proceed unevenly, which can lead to big troubles, up to damage to the entire product. Therefore, it is extremely important to choose the right heating mode so that artistic ceramics do not turn into a bunch of shards.
If the products are flat, then it is strongly advised to dry them exclusively in forms. First, they are slightly dried until the future ceramics acquire the required density, and only after that it can be removed and dried to a moisture content of 1-2.5%.
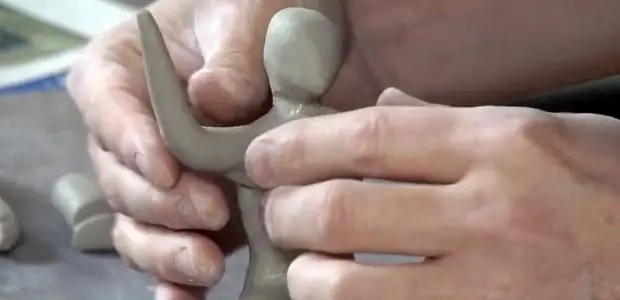
To carry out this process in large quantities, special conveyor dryers are used. In particularly difficult cases, drying is carried out in devices that operate on a periodic basis. This is done so that thin ceramics do not dry out and crack. Drying time ranges from 30 minutes to three hours.
So you have learned what ceramics is. This is one of the oldest materials that has ever been produced by mankind. Despite its antiquity, ceramics are in great demand to this day.
Recommended:
Production and production systems: concept, patterns and their types
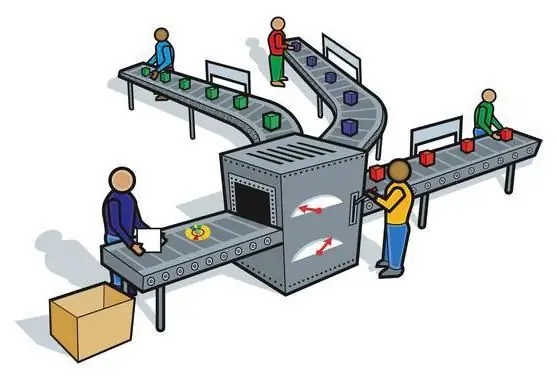
Production systems are structures that involve people and equipment working together. They perform their functions in a certain space, conditions, working environment in accordance with the tasks
Modern production. The structure of modern production. Problems of modern production

Developed industry and a high level of the country's economy are key factors influencing the we alth and well-being of its population. Such a state has great economic opportunities and potential. A significant component of the economy of many countries is the production
Gas production. Gas production methods. Gas production in Russia
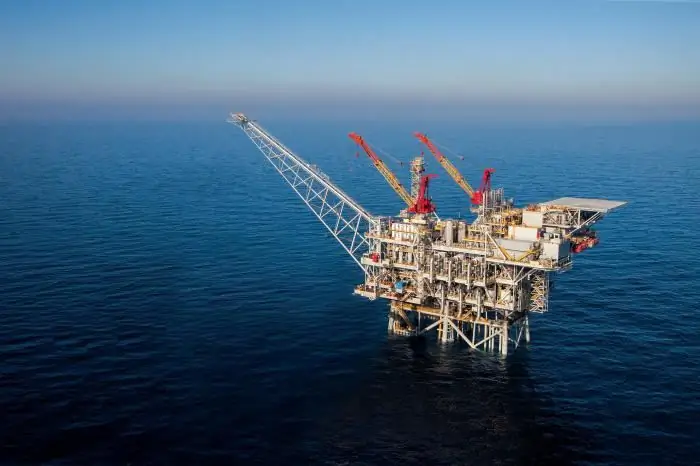
Natural gas is formed by mixing various gases in the earth's crust. In most cases, the depth of occurrence ranges from several hundred meters to a couple of kilometers. It is worth noting that gas can form at high temperatures and pressures. In this case, there is no access of oxygen to the place. To date, gas production has been implemented in several ways, each of which we will consider in this article. But let's talk about everything in order
Crop production - what kind of activity is this? Branches and areas of crop production
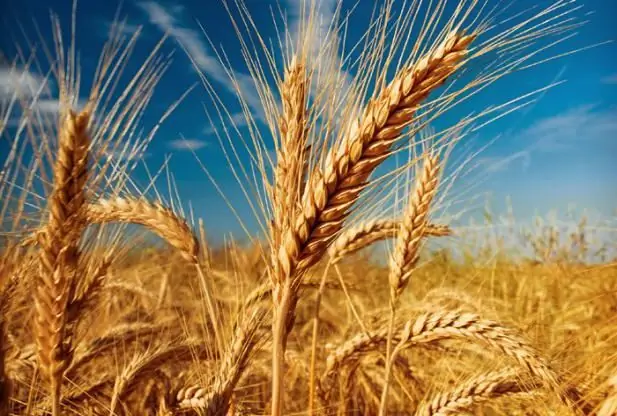
More than two-thirds of the products consumed by the population of the planet are provided by the leading branch of agriculture - crop production. This is the fundamental basis of world agricultural production. Consider its structure and talk about the achievements and development prospects of this world economy
A production cooperative is The Federal Law on production cooperatives. Legal entity - cooperative

Business is not only a means of personal enrichment, but also a way to significantly support financially that area or other entity in which the segment of small or medium-sized businesses is significantly developed. Knowing this, most of the self-government bodies actively support (sometimes not even on paper) the initiatives of citizens