2025 Author: Howard Calhoun | [email protected]. Last modified: 2025-01-24 13:10
Friction clutches are devices that are designed to transmit rotational motion in a mechanism. Quite often, elements of this type are found in a car.
They are also used in drives. The main advantage of modifications lies in their compactness. There are many types of couplings. To learn more about them, you should read the drawings of the model.
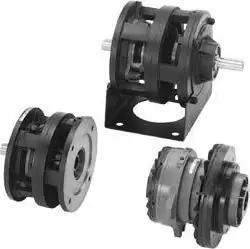
Model device
A conventional clutch includes a drum and a set of discs. The body itself is cup-shaped. Many modifications are made with clamping plates. Their fingers are fixed at the base of the device. There is a plug to connect the model. The rotational moment of the gear is provided by the bearings.
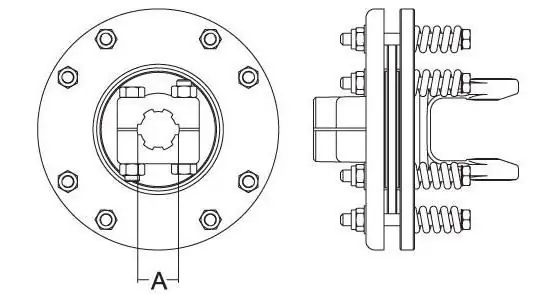
How does a clutch work?
The principle of operation of friction clutches is based on the transmission of rotational motion from the shaft. This process takes place thanks to the drum. It is tightly connected to the disks that control it. There is a spring to hold the mechanism along the axis. The standard model is fixed to the shaft through a fork. It is also worth noting that the rotation speed depends on the typesbearing.
Model Types
Disk, conical and cylindrical modifications are distinguished by shape. A separate category includes multi-disk models. There are devices with one or more drums. They differ in size as well as rotation ratio.
Disk drives
The most common are disc friction clutches. They use a big drum. In this case, the pressure plate is attached through the rack. Many models use several ties. It is also worth noting that there are devices with fingers. They have a fairly high friction force. These devices can be found in machine tools.
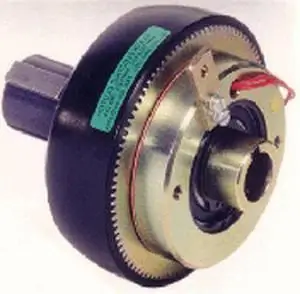
Cone modifications
Friction cone clutch (drawing shown below) is suitable for driving devices. She has several drums that are connected through a plate. Forks are used in different sizes. It should also be noted that cone modifications are well suited for cars, often installed on clutch mechanisms. The fingers in this case are attached at a slight angle of inclination. The driven inserts are well ground and able to rotate at high speed.
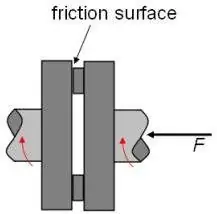
Cylindrical devices
Cylindrical friction clutch is very rare in production. Most often, models are installed on cranes. Leading drums they use a large width. At the same time, the racks differ in size. Some experts point to the strength of the springs. Couplings of this type are capable ofwithstand large axle loads. They may have one or more bearings. The tie pins are large size.
Features of multi-disc models
Multi-plate friction clutch includes a wide drum, as well as three working plates. Tie fingers are used on linings. Many models have multiple supports. It is also worth noting that there are modifications for two springs. They have high downforce, large diameter forks are used. Most often, devices are installed on drives. The bodies are tapered.
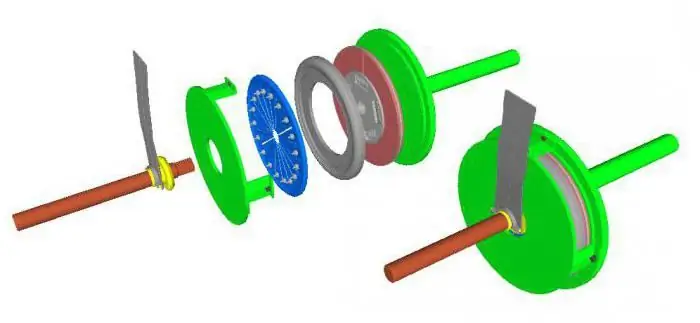
Single drum models
Single drum friction clutches are made with one or more plates. The compression force in this case is regulated by the fingers. Some experts say that modifications are suitable for cranes. However, they are still found in cars. It is also worth noting that the models can withstand large overloads. Their driven discs are polished, able to rotate quickly. Switching forks are most often installed at the base of the mechanism.
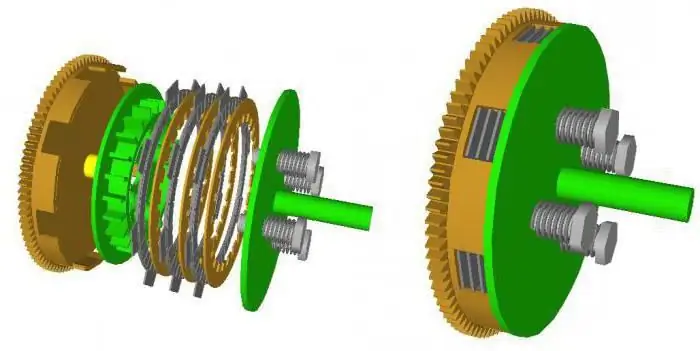
Multi-reel models
Quite often in production there is a safety clutch (friction) with several drums. Among the advantages of the modification, it is worth noting good stops and high downforce. Many models are capable of withstanding heavy loads. Overlays are rarely installed on mechanisms. It is also worth noting that the drive gears are used in large sizes. Somecouplings work from stretching fingers. They have two racks.
In this case, the plug for connection is located in the front of the structure. The devices are not suitable for drives because they have a slow start. It is also worth noting that there are models with a squeeze disc. The stem in this case is located in a horizontal position. In this case, the fingers are used in a small size. The devices have a high compression force. The drums can only spin in one direction. The drive disc can be behind or in front of the release plate.
Sleeve Models
Sleeve clutches are only suitable for clutch mechanisms. Some modifications are used in drive devices. Models can use several partitions. It is also worth noting that the coupling fingers are installed above the release spring. The plates are in a horizontal position. The sleeve is attached between the partitions and plays the role of a shock absorber.
If we talk about the shortcomings, it is worth noting that the models have low downforce. Also, models are not able to maintain high shaft speeds. Devices are not suitable for drives.
Advantages of flanged devices
The advantage of flange couplings lies in the fact that they have low drum wear. Disks are most often fixed behind the rack. Partitions are used in small sizes. Clamping plates are used to hold the rack. Springs are most often fixed at the bottom of the couplings. Some models work with drives. The connection to the shaft is through a fork. It is also worth noting that there are modifications withwide pressing discs. They have tapered bodies and are very compact.
Hinged Models
Swivel couplings are able to work in drive units of different power. Modifications are distinguished by wide partitions and short fingers. The discs are fixed at the base of the plate. Cases are produced in different sizes. Tie fingers are located in front of the rack. Partitions can be with rifling. It is also worth noting that the strength of the torque depends on the size of the drum. As a rule, it has a wide wall. At the same time, the edges are sharpened and do not rub against the discs. This was achieved by installing hinges.
Cam devices
Friction clutch with cams suitable for machine tools. Many models can withstand a significant load, but in this case, a lot depends on the drum. For some devices, it is fixed between the partitions. It should also be noted that there are models on plates. A tapered body is used to hold parts.
The most common are the clutches on the squeezing discs. They use drums of small width. The rods in this case are connected to the forks. Many models are used in clutch mechanisms. Tie fingers can be fixed at the base of the partitions. The driven drum is practically not erased. Tie pins are normally used in small sizes.
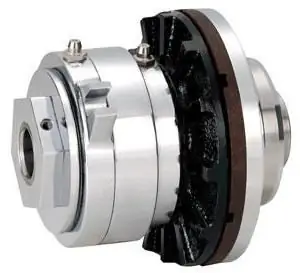
Drive Models
The friction clutch for drives can work with one or more drums. In this case, the stemsproduced for small shafts. Drums are installed in a horizontal position. Many modifications are equipped with aluminum alloy wheels. It is also worth noting that there are modifications with spring devices.
If we consider the standard modification, then it has two squeezing disks. There is only one plate between them. The sleeve in this case is attached to the stem. For the purpose of safety of a drum bearings are established. If we consider models for large drives, then they have a squeezing disk with a partition. The driven drum works on a wide rack. Pressure springs can be with couplers. The forks at the couplings are fixed at the base. Some models are produced with conical bodies. Additionally, compact working plates are used for couplings.
Recommended:
Derivative HPPs: description, principle of operation, where they are used
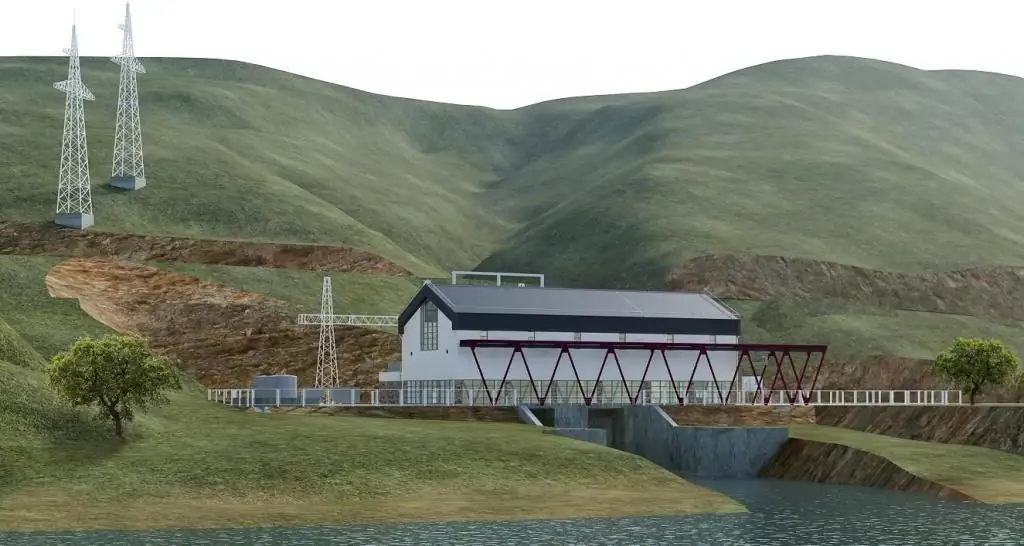
Hydrotechnical structures have been used since ancient times to generate energy. Nowadays, a separate direction of derivation stations is also successfully developing. These are structures characterized by a special drainage infrastructure that allows for more effective flow control even in difficult geographical conditions. At the basic level, the decoding of hydroelectric power stations is applicable to them - a hydrological power plant
Indicators without delay and redrawing: types, principle of operation, pros and cons of application, expert advice
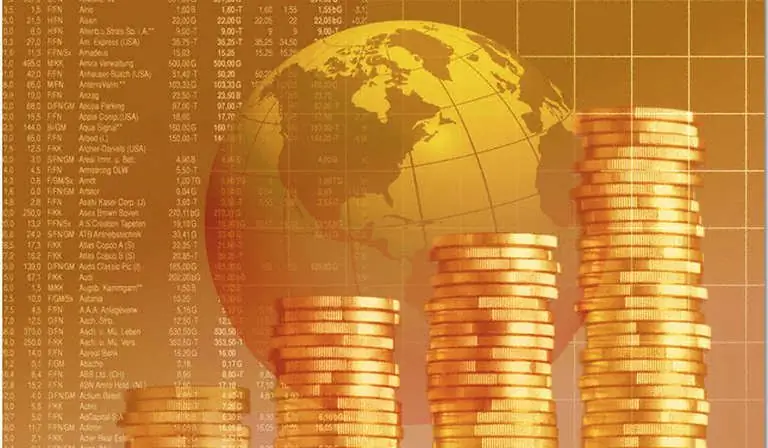
There is a wide variety of different tools in trading: graphical constructions, technical indicators, automated programs, trading signals and much more. To successfully apply them in trading, you need to understand how they work. Indicators without delay and redrawing are especially popular with traders
Electric locomotive 2ES6: history of creation, description with photo, main characteristics, principle of operation, features of operation and repair
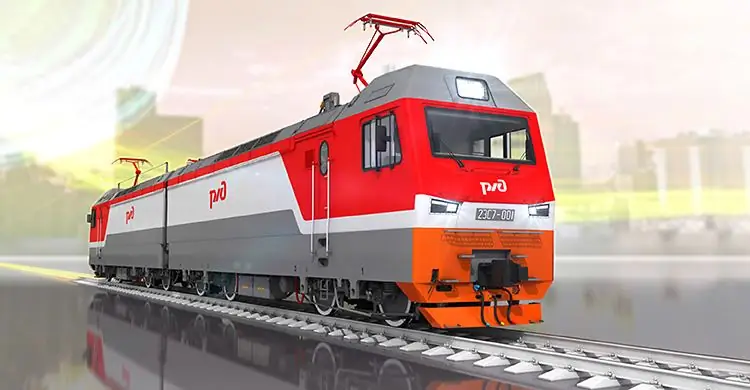
Today, communication between different cities, passenger transportation, delivery of goods is carried out in a variety of ways. One of these ways was the railroad. Electric locomotive 2ES6 is one of the types of transport that is currently actively used
Low pressure heaters: definition, principle of operation, technical characteristics, classification, design, operation features, application in industry
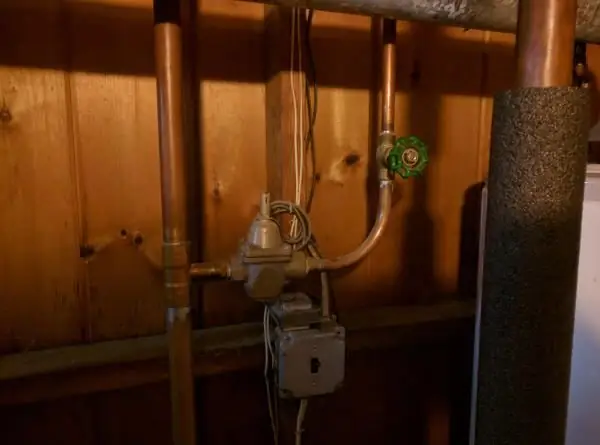
Low pressure heaters (LPH) are currently used quite actively. There are two main types that are produced by different assembly plants. Naturally, they also differ in their performance characteristics
Gas piston power plant: the principle of operation. Operation and maintenance of gas piston power plants
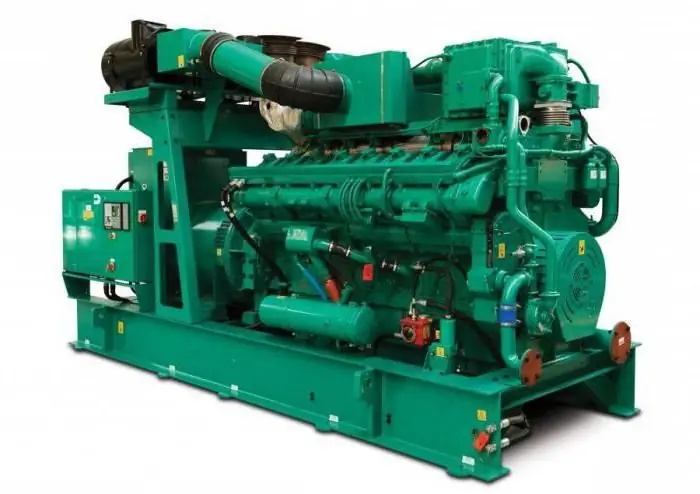
Gas piston power plant is used as a main or backup source of energy. The device requires access to any type of combustible gas to operate. Many GPES models can additionally generate heat for heating and cold for ventilation systems, warehouses, industrial facilities