2025 Author: Howard Calhoun | [email protected]. Last modified: 2025-01-24 13:10
Mechanical action with fine-grained abrasives has long proved its effectiveness in the treatment of various surfaces. Even a small air gun allows you to clean difficult traces of corrosion damage, scale and the effects of chemical burns. However, in a large construction or industrial production environment, the capacity and coverage of handheld sandblasters may not be sufficient. In such situations, a shot blasting machine is used, which can operate on the same principle of supplying abrasives, but with different operating parameters.
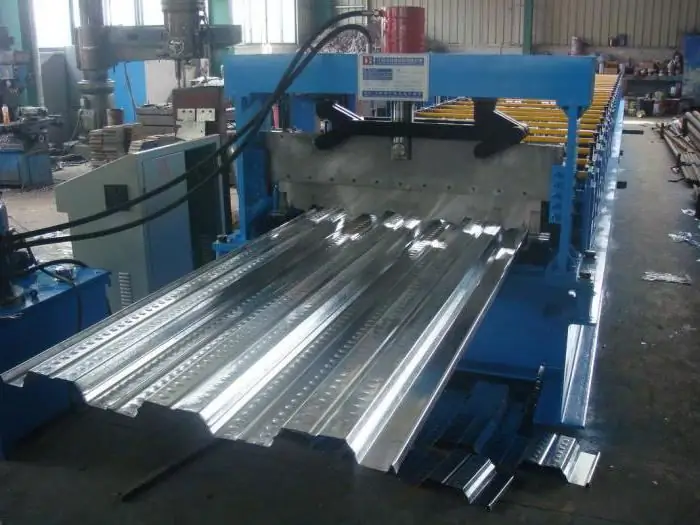
What is a shot blaster?
To understand the purpose and features of such units, it is worth considering the principle of operation of abrasive blasting machines as such. Through a special nozzle, small guns are fed onto the working surface with sand, which, when colliding with the material being processed, ensures its cleaning. The force for feeding the abrasive can be provided by different methods. The most common supply of compressed air, which provides a compressor unit. Less popular is the direction of the water jet, which contains the same sand particles. However, to work withboth technologies are not suitable for large volumes. In solving such problems, a shot blasting unit is used, which operates on the principle of mechanical supply of abrasive with special blades. The features of this type of units include the use of metal particles as an active cleaning component.
General arrangement of shot blasting units
Almost any shot blasting machine is based on an impeller provided with blades that feed the abrasive. This is the main functional component, which is also subjected to the greatest physical stress. Therefore, the blades and the wheel base are made of high-alloy cast iron, which has increased resistance to abrasion. In addition, the shot blasting machine is equipped with durable bearings, the material of which is also designed for operation under conditions of intense mechanical stress. The fact is that the wheel and the working units adjacent to it directly interact with the working metal abrasives. The work is carried out at high speed, so the loads on the materials are considerable. In this case, the wheel is in a special chamber made on the basis of a steel alloy. The target object is placed in this chamber, after which the processing process starts.
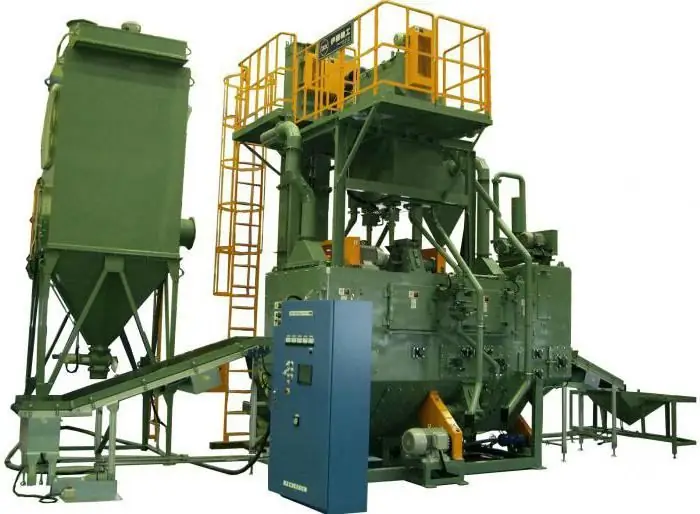
Hardware highlights
The quality of cleaning, as in the case of manual sandblasting, is determined by the power of the unit. But if in the operation of conventional pneumatic devices, the performance depends on the function of the compressor, then the performanceshot blasters is determined by the power of the electric motor, which drives the wheel with blades. The power potential of the motor averages 10-15 kW. Such a capacity, for example, has a shot blasting plant for cleaning sheet metal and building metal structures available for placement in the chamber. Thus, the average parameters of products available for cleaning in such equipment are about 700 x 700 x 1200 mm. There are also restrictions on the mass of loaded parts - as a rule, the maximum weight reaches 1 ton. As for the performance of the installation itself, it reaches 100-150 kg / min. At the same time, several devices can serve one camera at once.
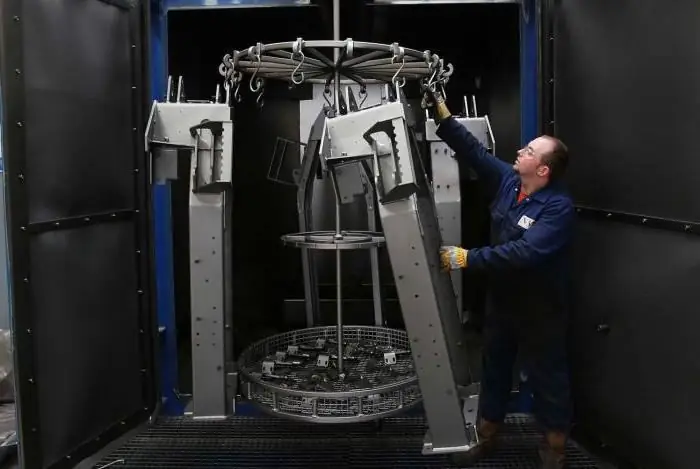
The principle of operation of suspended installations
These are units with tunnels in which blanks are cleaned. The suspension principle of operation is effective due to the fact that working operations can be carried out from different sides. The structure that fixes the product is a special conveyor that moves in the tunnel. The operator can use the suspended type shot blasting machines according to the flow principle, that is, to perform serial processing of parts. True, the possibility of such operation depends on the system for collecting ejected metal particles - abrasives. The fact is that the classic shot blasting machine is designed for a one-time operation.
At least after processing one element, it takes a small amount of time to complete the collection of hardware. Moreover, it takes timethe process of separating the abrasive mass from contaminants that have been discarded as a result of the supply of active material. Sometimes automatic work on shot blasting plants is also provided, during which there is a continuous process of collecting, cleaning and ejecting hardware.
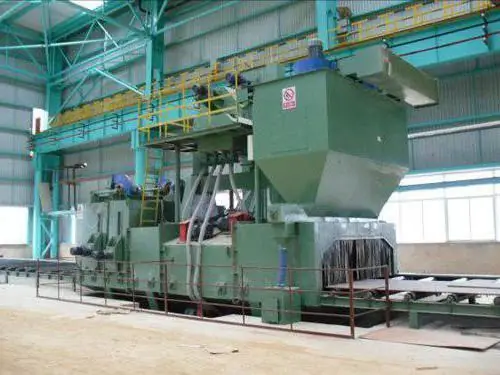
The principle of operation of through models
This is the basic model of the continuous shot blaster family. Its functional basis is a metal mesh conveyor that moves the workpiece inside the cleaning chamber. The process is carried out in a closed working chamber, which can be provided with a different number of turbines. The advantages that a through-type shot blasting machine has include the ability to ensure thorough and uniform processing of parts. Most importantly, the workflow does not require the item to be flipped. Thanks to the shutter system as well as the blowing mechanisms, you can also count on high cleaning quality. Passing units are actively used today for processing parts in machine-building production, when cleaning building metal sheets, in the manufacture of aluminum alloys, etc.
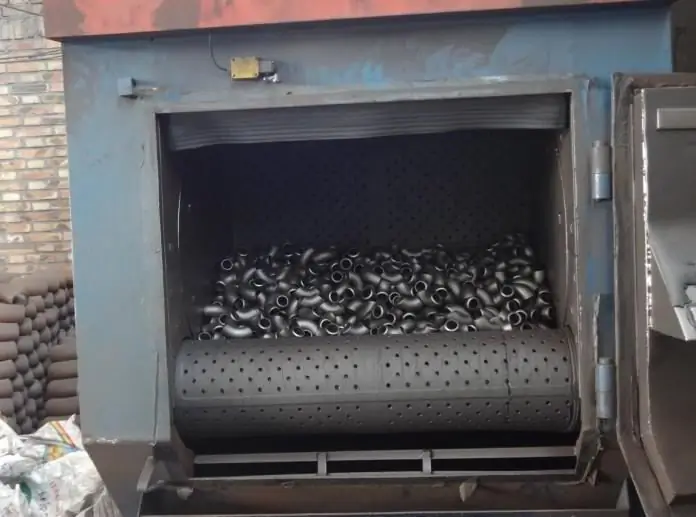
The principle of operation of drum shot blasters
This is a rather practical unit, which is most often used in the metallurgical industry for the final processing of obtained alloys. For example, such a system can rid surfaces of traces of molding solutions, scale and burns. Moreover, given the choiceWith the right abrasive, you can achieve the desired surface roughness. So, two main components are involved in the workflow: a hydraulic lift that fills the workpieces, and the drum itself, where cleaning takes place. During the operation, the container, made of perforated metal tape, rotates, allowing you to process products from different sides. Accordingly, the drum-type shot blasting plant also makes it possible to obtain high-quality cleaned products at the output. In this case, the operator can move the drum turbine manually or by means of special control panels. However, control systems should be considered separately.
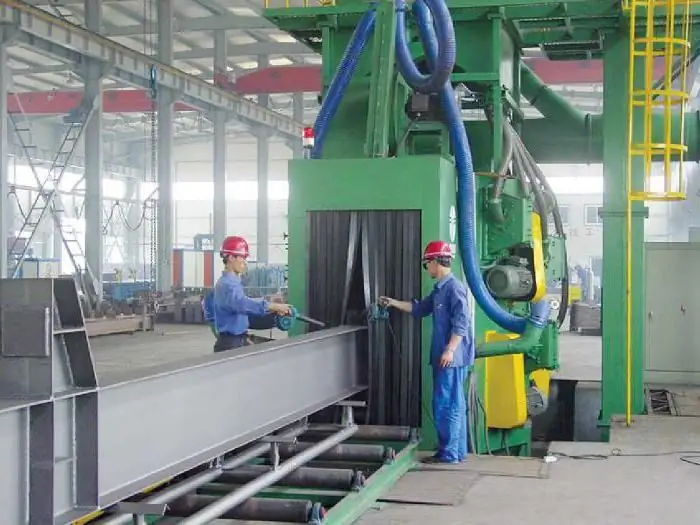
Equipment control system
The latest versions of such equipment provide for the use of special controllers based on a programmable module. This means that the user can pre-set the operating parameters of the mechanisms. The main indicators that can be controlled in this way include: feed rate, intensity of movement inside the working chamber, as well as the interval at which one workpiece is in the vehicle. The way the operator interacts with the controller depends on the design of the shot blasting machine itself. The principle of operation may provide for small dimensions, which make it possible to equip the main structure with a control point. If the equipment is part of a common production line, then the control point in the formcabinet can be located at a considerable distance from the place of operation.
What to consider when choosing an installation?
When choosing a shotgun, you should pay attention to several parameters. First of all, the power and design of the equipment is determined. It is important to understand what materials the unit will work with - it can be sheet metal, wire, as well as small parts that require delicate cleaning. As for the design, it may involve integration into the production complex or act as a separate technological area. For example, shot blast machines are suitable for serial processing of parts of different sizes, so they are suitable for use in large-scale production. It is also worth considering the presence of additional functions, including automatic assembly of the released abrasive and cleaning of parts during processing.
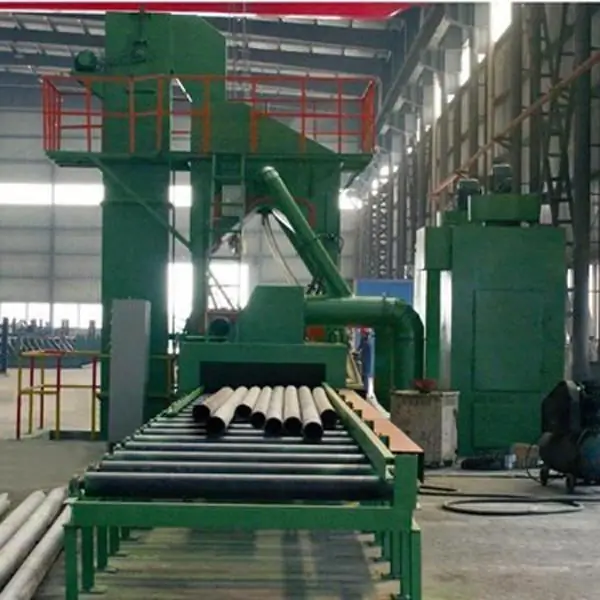
Conclusion
Familiar to many car mechanics and painters, sandblasting machines in some versions correspond to shot blasters in terms of processing quality. The main difference in terms of the characteristics of the result obtained is reduced to the coverage area. That is, the quality of processing can be equal, but in one session, the shot blasting machine will service several times more parts than traditional pneumatic machines. This is due to the prevalence of abrasive blasting equipment of this kind in industry and on large construction sites. In a small-scale cleaning format, the use of such equipmentimpractical, primarily for energy efficiency reasons.
Recommended:
Electroerosive machine: scope and principle of operation
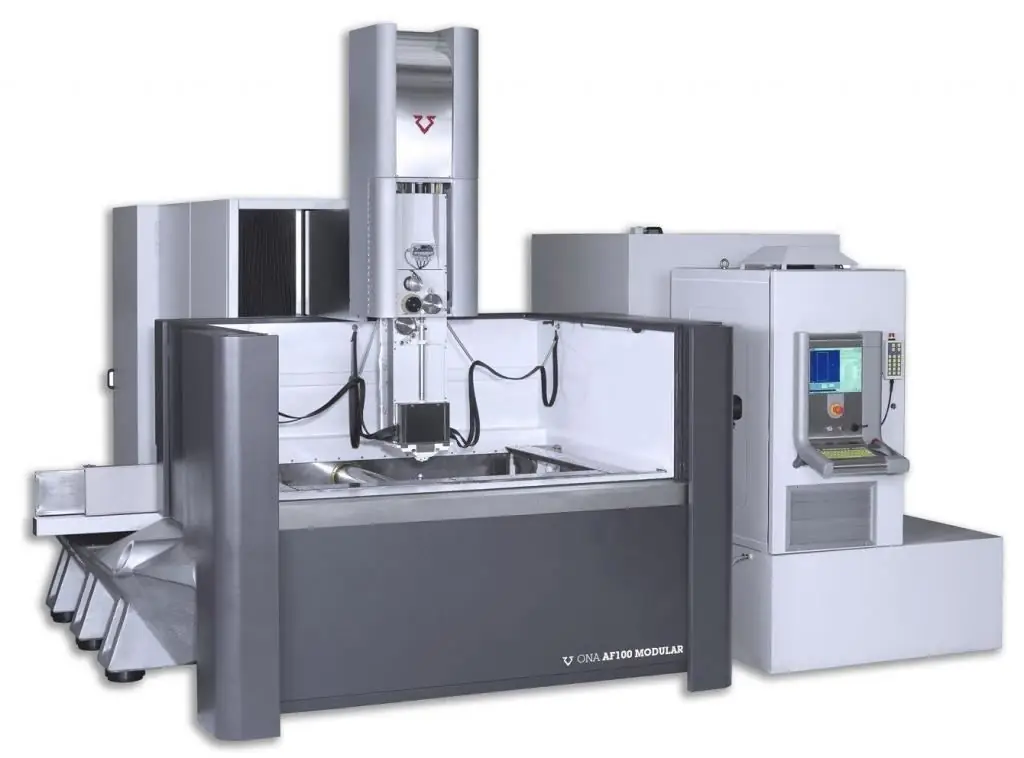
If before the EDM machine was a rarity, today such equipment is no longer a surprise. Electroerosion is understood as the destruction of interatomic forces of interaction in metals under the influence of an electric charge. The electroerosive machine owes its appearance to the developments of Soviet scientists B. R. Lazarenko and N. I. Lazarenko. Such equipment is universal. It allows you to process and shape any grade of metals and alloys
Electric locomotive 2ES6: history of creation, description with photo, main characteristics, principle of operation, features of operation and repair
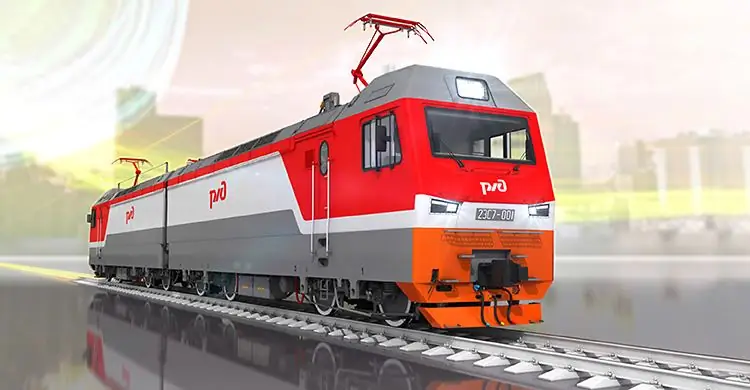
Today, communication between different cities, passenger transportation, delivery of goods is carried out in a variety of ways. One of these ways was the railroad. Electric locomotive 2ES6 is one of the types of transport that is currently actively used
Packaging machine: overview of models, principle of operation, photo
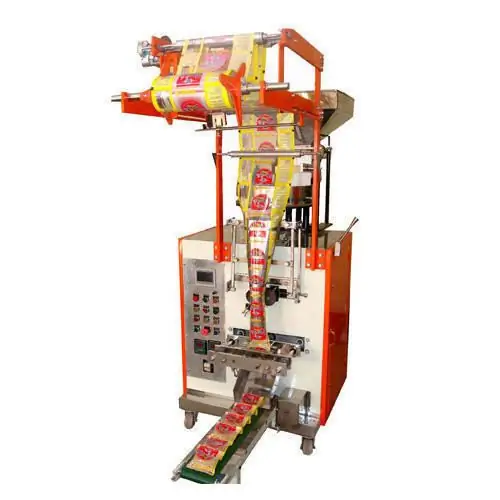
Any successful production today needs packaging equipment. Such machines and mechanisms allow automatic or manual packaging of a wide variety of products. They are able to quickly and efficiently carry out many operations and are reliable assistants in production. Packing machines and equipment can either be part of a production line or function autonomously
Low pressure heaters: definition, principle of operation, technical characteristics, classification, design, operation features, application in industry
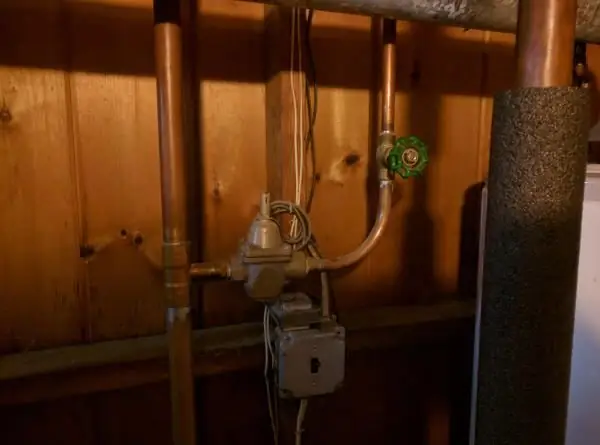
Low pressure heaters (LPH) are currently used quite actively. There are two main types that are produced by different assembly plants. Naturally, they also differ in their performance characteristics
Gas piston power plant: the principle of operation. Operation and maintenance of gas piston power plants
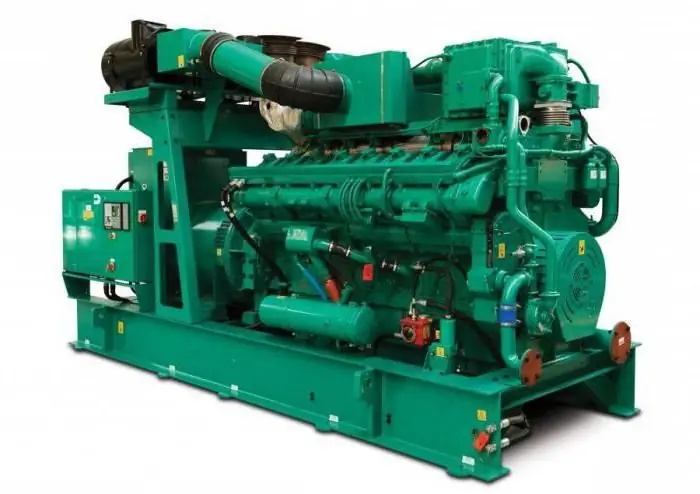
Gas piston power plant is used as a main or backup source of energy. The device requires access to any type of combustible gas to operate. Many GPES models can additionally generate heat for heating and cold for ventilation systems, warehouses, industrial facilities