2025 Author: Howard Calhoun | [email protected]. Last modified: 2025-01-24 13:10
In the processes of obtaining high-strength steels, alloying operations and modification of the base composition play an important role. The basis of such procedures is the technique of adding metal impurities of various properties, but gas-air regulation is also of no small importance. It is this technological operation that the operation of the oxygen converter, which is widely used in metallurgy in the production of steel alloys in large volumes, is oriented.
Converter design
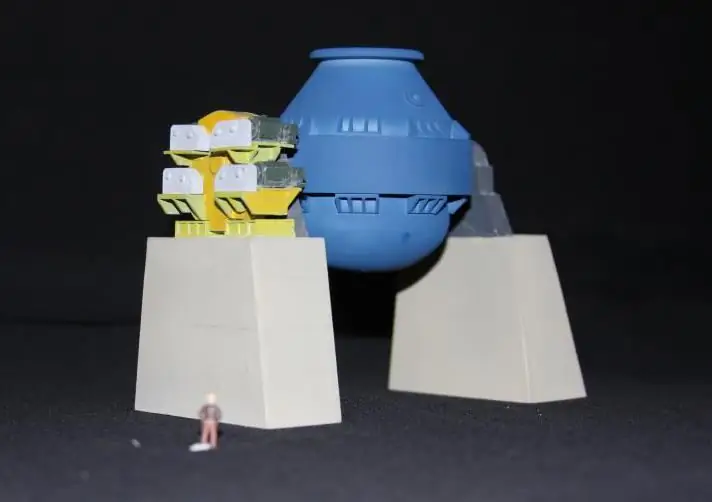
The equipment is a pear-shaped vessel, provided with an inner lining and a tap hole for the release of smelting products. In the upper part of the structure, a hole with a neck is provided for supplying lance, scrap, molten iron, alloying mixtures and gas removal. The tonnage varies from 50 to 400 tons. Sheet or welded medium steel is used as materials for the manufacture of the structure.about 50-70 mm thick. A typical device of an oxygen converter provides for the possibility of detaching the bottom - these are modifications with bottom purge with gas-air mixtures. Among the auxiliary and functional elements of the unit, one can single out an electric motor, a pipeline infrastructure for circulating oxygen flows, thrust bearings, a damper platform and a support frame for mounting the structure.
Support rings and trunnion
The converter is located on roller bearings, which are fixed on the frame. The design may be stationary, but this is rare. Usually, at the design stages, the possibility of transporting or moving the unit in certain conditions is determined. It is for these functions that the equipment in the form of support rings and pins is responsible. The group of bearings provides the possibility of torsion of the equipment around the axis of the trunnions. Previous models of converters assumed the combination of the carrier equipment and the body of the melting equipment, but due to exposure to high temperatures and deformation of auxiliary materials, this design solution was replaced by a more complex, but reliable and durable scheme of interaction between the functional unit and the vessel.
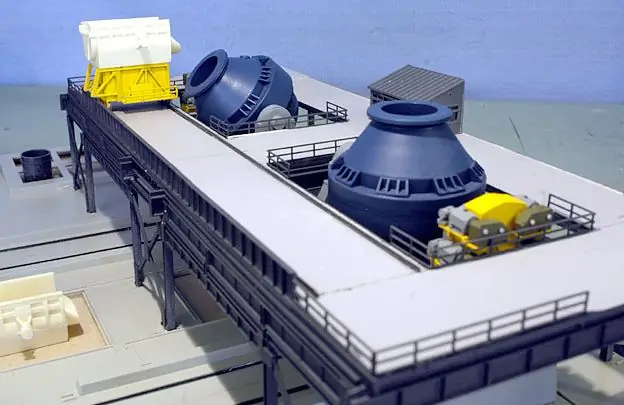
Modern oxygen converter, in particular, is provided with a separate support ring, into the structure of which trunnions and a fixed casing are also introduced. The technological gap between the casing and the support base prevents negative temperature effects on the sensitive elements of suspensions and mobile mechanisms. The fixing system of the converter itself is implemented due to the stops. The support ring itself is a carrier, formed by two half-rings and trunnion plates fixed at the docking points.
Swivel mechanism
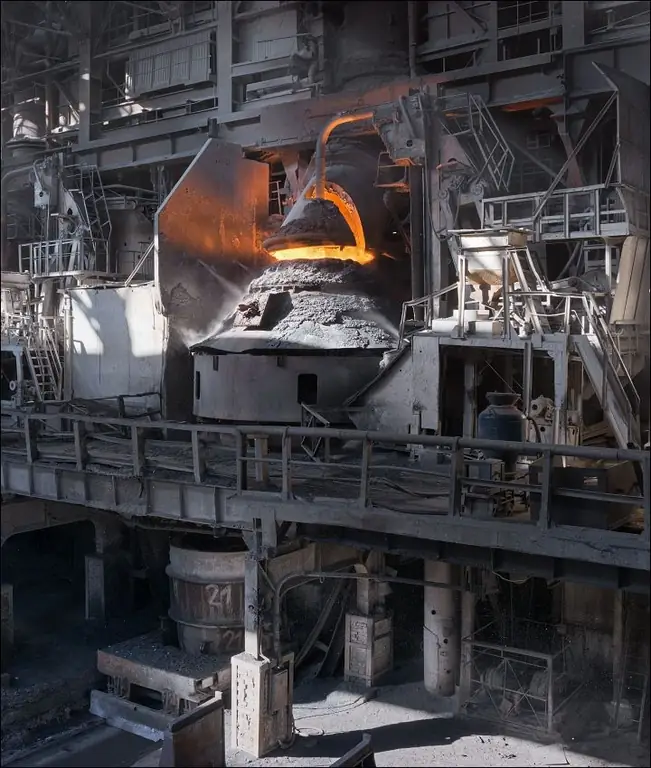
Electric actuator allows converter to rotate 360°. The average rotation speed is 0.1-1 m/min. By itself, this function is not always required - depending on the organization of technological operations during the workflow. For example, a turn may be required to orient the neck directly to the point of supplying scrap, pouring iron, draining steel, etc. The functionality of the turning mechanism may be different. There are both one-way and two-way systems. As a rule, oxygen converters with a carrying capacity of up to 200 tons assume a turn in one direction only. This is due to the fact that in such designs less torque is required when tilting the neck. To eliminate the consumption of excess energy during the operation of heavy-duty equipment, it is provided with a two-way rotation mechanism, which compensates for the cost of manipulating the neck. The structure of the torsion system includes a gearbox, an electric motor and a spindle. This is the traditional layout of a stationary drive mounted on a concrete screed. More technological hinged mechanisms are fixed on the trunnion and driven by a driven gear with a system of bearings, which are also activated by electric motors through a shaft system.
Converter dimensions
During the design, the design parameters must be calculated based on what approximate volume of purge, excluding melt ejection, will be produced. In recent years, units have been developed that accept materials in volumes from 1 to 0.85 m3/t. The slope of the throat is also calculated, the angle of which averages from 20° to 35°. However, the practice of operating such structures shows that exceeding the slope of 26° degrades the quality of the lining. In depth, the dimensions of the converter are 1-2 m, but as the loading capacity increases, the height of the structure may also increase. Conventional converters up to 1 m deep can accept a load of no more than 50 tons. As for the diameter, it varies on average from 4 to 7 m. The thickness of the neck is 2-2.5 m.
BOF lining
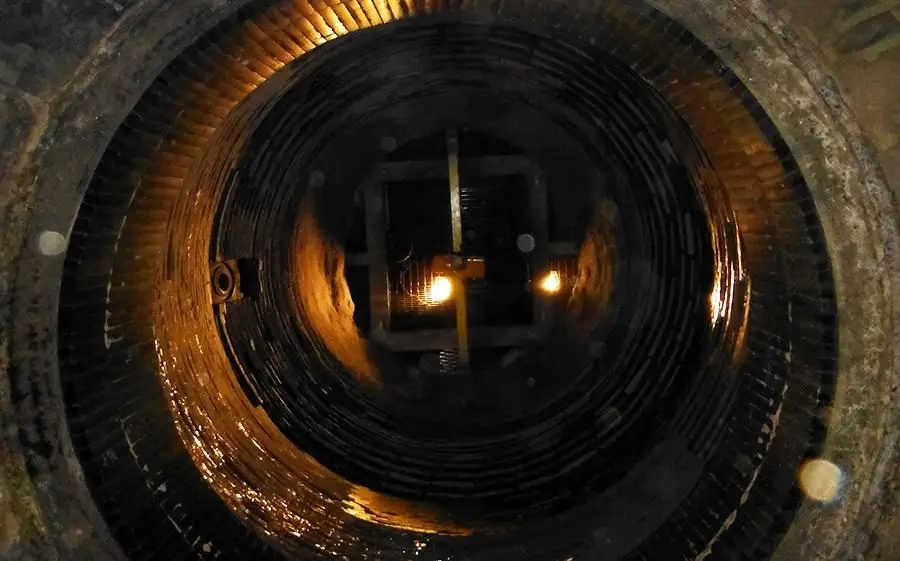
Mandatory technological procedure, during which the internal walls of the converter are provided with a protective layer. At the same time, it should be taken into account that, unlike most metallurgical furnaces, this design is subjected to much higher thermal loads, which also determines the features of the lining. This is a procedure involving the laying of two protective layers - functional and reinforcing. A layer of protective reinforcement with a thickness of 100-250 mm adjoins directly to the surface of the body. Its task is to reduce heat loss and prevent burnout of the upper layer. The material used is magnesite or magnesite-chromite brick, which can serve for years without renewal.
The top working layer has a thickness of about 500-700 mm and is replaced quite often as it wears out. At this stage, the BOF is treated with non-firing sand- or resin-bonded refractory compounds. The base material for this lining layer is dolomite with magnesite additives. The standard load calculation is based on a temperature effect of about 100-500 °C.
Shotcrete lining
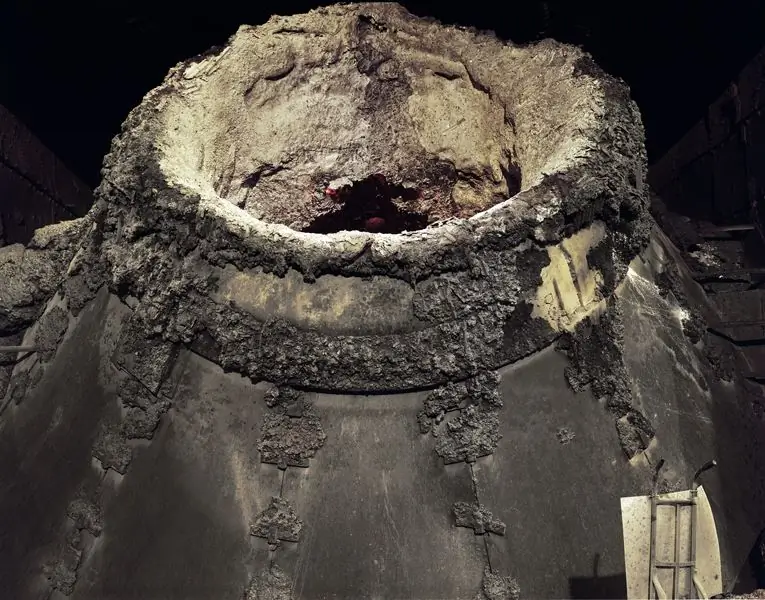
Under aggressive temperature and chemical influences, the internal surfaces of the converter structure quickly lose their qualities - again, this concerns the external wear of the working layer of thermal protection. Shotcrete lining is used as a repair operation. This is a hot reduction technology in which a refractory composition is laid with the help of special equipment. It is applied not in a continuous way, but pointwise on heavily worn areas of the base lining. The procedure is performed on special shotcrete machines that feed a water-cooled lance with a mass of coke dust and magnesite powder to the damaged area.
Smelting technologies
Traditionally, there are two approaches to the implementation of oxygen-converter melting - Bessemer and Thomas. However, modern methods differ from them by low nitrogen content in the furnace, which improves the quality of the work process. The technology is being carried out in the following stages:
- Loading scrap. About 25-27% of the total mass of the charge is loaded into the inclined converter by means of scoops.
- Fillingcast iron or steel alloy. Liquid metal at temperatures up to 1450 °C is poured into a tilted converter by ladles. The operation lasts no more than 3 minutes.
- Purge. In this part, the technology of steelmaking in oxygen converters allows different approaches in terms of supplying a gas-air mixture. The flow can be directed from above, below, bottom and combined ways, depending on the type of equipment design.
- Receiving samples. The temperature is measured, unwanted impurities are removed, and the analysis of the composition is expected. If its results meet the design requirements, the melt is released, and if not, adjustments are made.
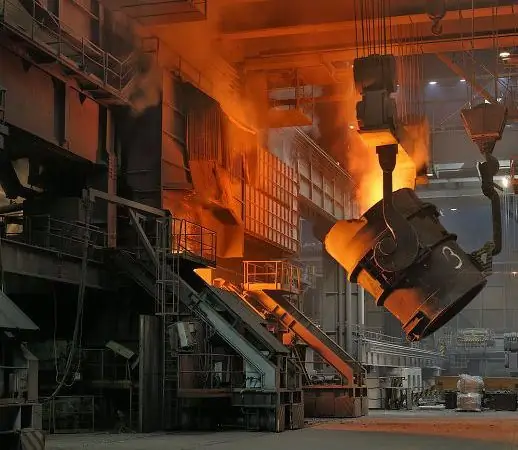
Pros and cons of technology
The method is valued for its high productivity, simple oxygen supply schemes, structural reliability and relatively low costs in general for the organization of the process. As for the disadvantages, they, in particular, include restrictions in terms of adding sludge and recyclables. The same scrap metal with other inclusions can be no more than 10%, and this does not allow to modify the structure of the smelting to the required extent. Also, blowing consumes a large amount of useful iron.
Application of technology
The combination of pluses and minuses ultimately determined the nature of the use of converters. In particular, metallurgical plants produce low-alloy, carbon and alloy steel of high quality, sufficient for the use of the material in heavy industry and construction. Receiving steels inoxygen converter is alloyed and improved individual properties, which expands the scope of the final product. Pipes, wire, rails, hardware, hardware, etc. are made from the resulting raw materials. The technology is also widely used in non-ferrous metallurgy, where blister copper is obtained with sufficient blowing.
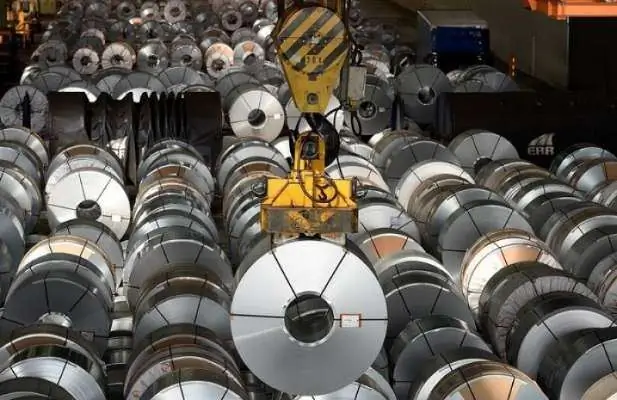
Conclusion
Smelting in converter facilities is considered a morally obsolete technique, but it continues to be used due to the optimal combination of productivity and financial costs for the process. To a large extent, the demand for technology is also facilitated by the structural advantages of the equipment used. The same possibility of direct loading of metal scrap, charge, sludge and other wastes, albeit to a limited extent, expands the possibilities for modifying the alloy. Another thing is that for the full-fledged operation of large-sized converters with the ability to turn, the organization of an appropriate room at the enterprise is required. Therefore, smelting with oxygen purge in large volumes is carried out mainly by large companies.
Recommended:
Oxygen sleeve: description, GOST, types and diameter
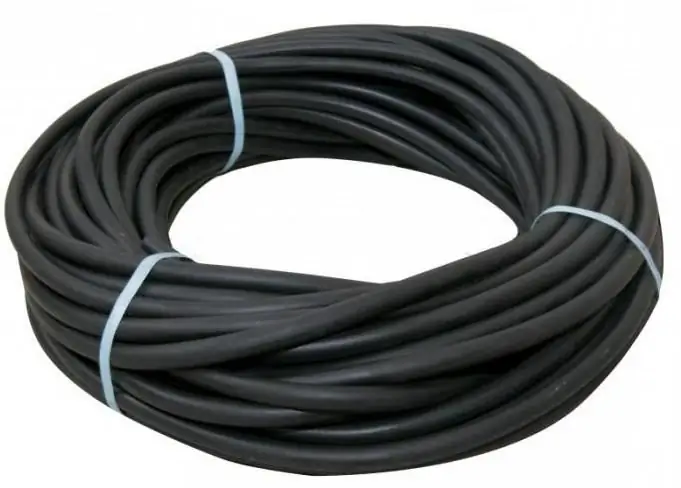
Currently, people are quite actively using various gas or oxygen for their own purposes. Since it is necessary to transport a gaseous substance in a completely sealed environment, hoses have been developed, which are called oxygen hoses
Oxygen cylinders. Proper refueling is the key to he alth and safety
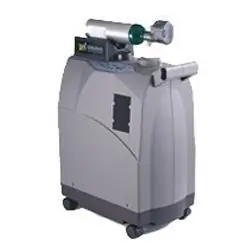
One of the most important and dangerous preparations for diving is the correct filling of oxygen cylinders. The article tells how to properly fill oxygen cylinders and why there are cases of explosion of oxygen cylinders
Oxygen hoses: description, dimensions, GOST and reviews
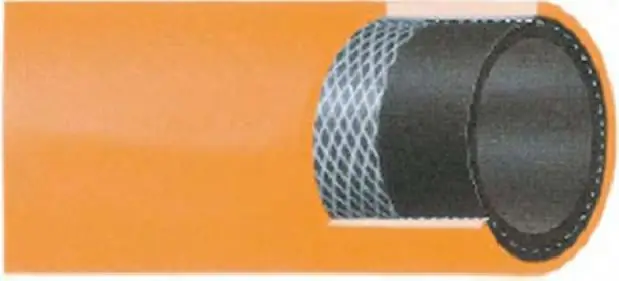
Currently, a lot of work is carried out using welding. For this reason, oxygen hoses have become quite a popular material, and besides, they are easy to transport
Welding converter: principle of operation
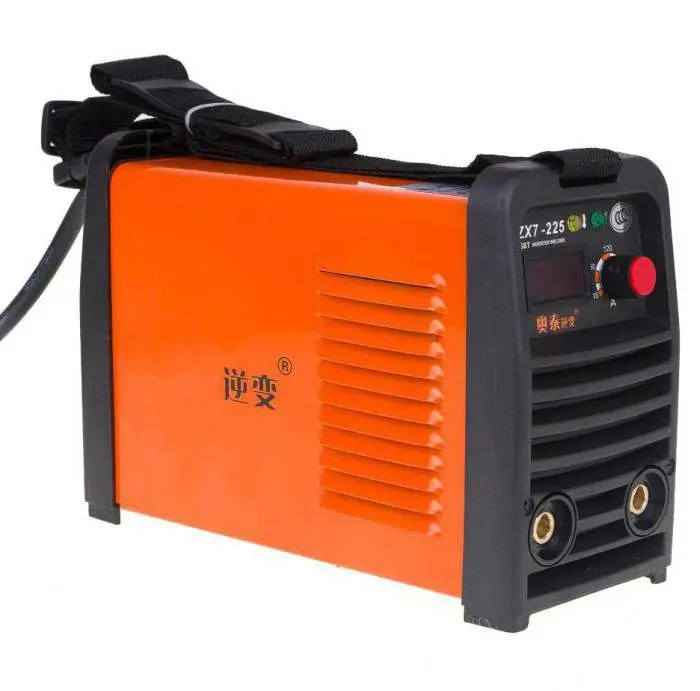
Currently, the process of welding to connect any structures is used quite actively. Experienced welders know that with direct current, the arc burns more stable than with alternating current, which means that the quality of the weld will be higher. The welding converter plays the role of a transformer that converts AC to DC
Vacuum metallization - technology description, device and reviews
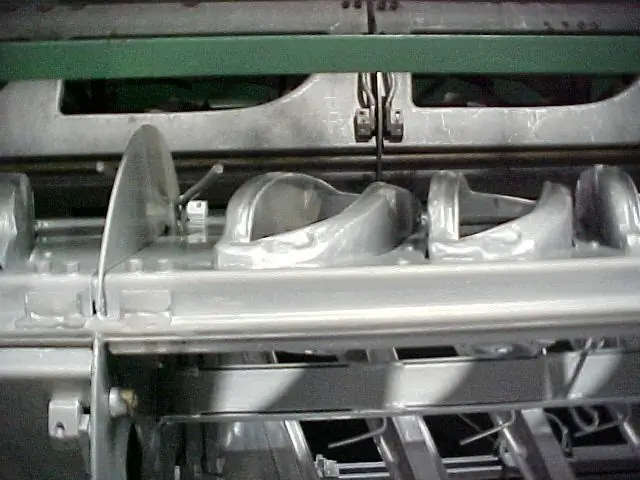
The article is devoted to vacuum metallization. The features of the technology, the device of the equipment used, reviews, etc. are considered