2025 Author: Howard Calhoun | [email protected]. Last modified: 2025-01-24 13:10
Today, people actively use plastic containers. For the manufacture of such products with a very different and complex shape, a vacuum forming machine is used. Goods made on such machines are actively used not only in everyday life, but also in food, light industry, and the automotive sector.
How the device works
How does a vacuum forming machine work? At the heart of its operation, as the name implies, is the technological process of vacuum forming. It allows you to give the workpiece the desired shape.
The essence of the work is as follows:
- A billet made of plastic, which has previously undergone high-temperature heating, is placed in a special vacuum chamber, which is located above the matrix, with the necessary shape of the product.
- After that, the vacuum forming machine pressurizes the chamber by pumping out the air.
- Due to this impact, the workpiece takes the form of the existing die.
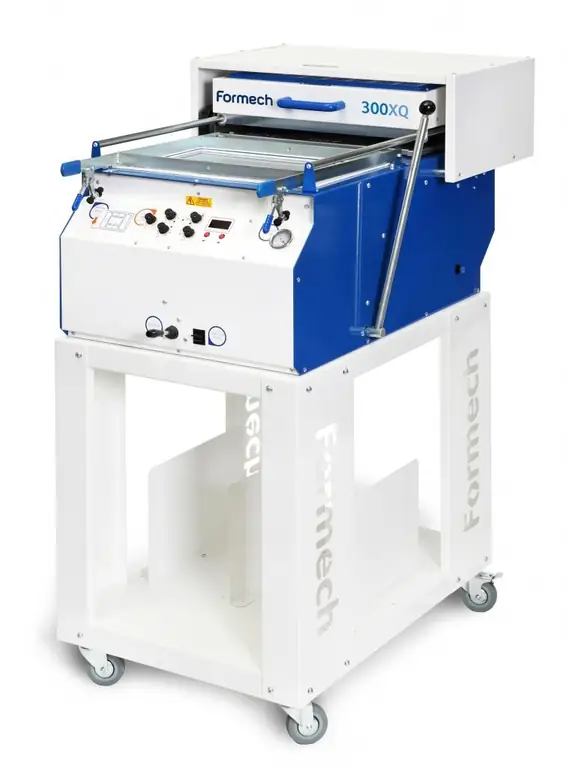
Main types of machines
Today, all vacuum forming machines can be divided into three types. The main factor for dividing into different groups is the size of the manufactured parts. According to this principle, the following types are distinguished:
- large-sized machines used for the production of large-scale goods on a large scale;
- medium-sized devices are used for the production of medium-sized goods and one-off products on an industrial scale;
- small-scale equipment is used for the production of small batches of plastic goods and one-off products.
It is worth noting here that all machines can also be divided into two categories - automatic and semi-automatic. If everything is clear with the first type of aggregate, then for the second category, the processes of excavation and loading of material are carried out manually.
Different types of vacuum forming machines are capable of developing different pressure, temperature and other technical characteristics. Depending on these indicators, the devices are able to work with blanks made of materials such as ABS, PMMA, PVC, acrylic and other materials.
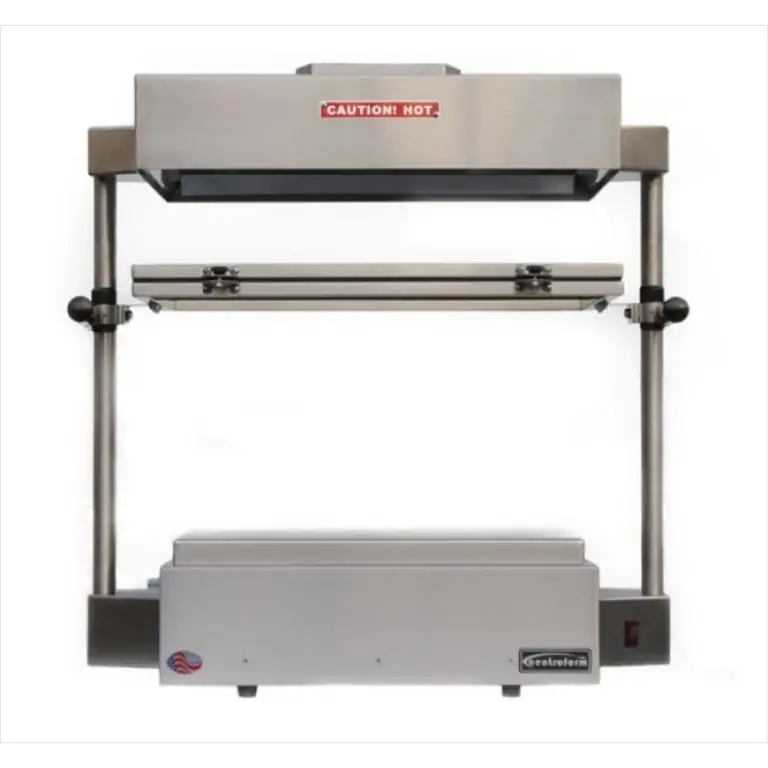
Korst car
Vacuum forming machines have almost the same working principle. The main difference lies in its technical characteristics. They must correspond to the purposes for which the device was developed. EquipmentKorst company is intended for the production of various body parts, trays, racks, other forms for various purposes, etc. All products are widely used in various industrial fields.
This vacuum forming machine can process materials with a thickness ranging from 0.05mm to 5mm. As for the dimensions of the finished product, it can reach several meters in length. For such equipment, it is enough to simply make a matrix with your own hands or buy it, since it is inexpensive. The use of VF machines allows you to use a huge range of raw materials, which at the same time is quite cheap.
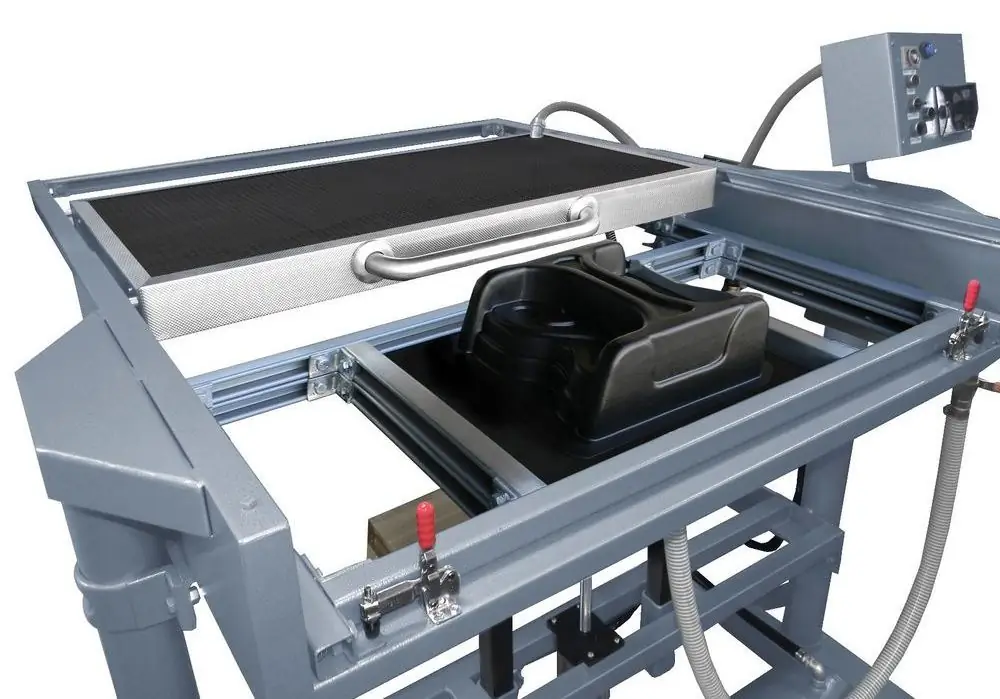
VF technical parameters
Model VF A550 has the following technical parameters:
- Firstly, it requires 3 x 380 V power supply at 50 Hz.
- Secondly, for proper operation, it is necessary to connect a pneumatic network with a pressure of 6 atm.
- Third, the weight of the equipment is 250 kg.
- Fourthly, for such devices, an important characteristic to consider is the air flow. For this model, it is 100 cubic meters. m per hour.
- Fifth, during operation, the device consumes 9 kW of power.
- Sixth, the maximum thickness of the produced film is 5mm. The working range itself is 0.2-5 mm.
- Seventh, the size of the surface of the table for packing finished products has dimensions of 550 x 400 mm.
- Eighth, the dimensions of the machine itselfare 700 x 1500 x 800 mm in width, height and length, respectively.
- Ninth, the maximum heating power of the unit is 7 kW.
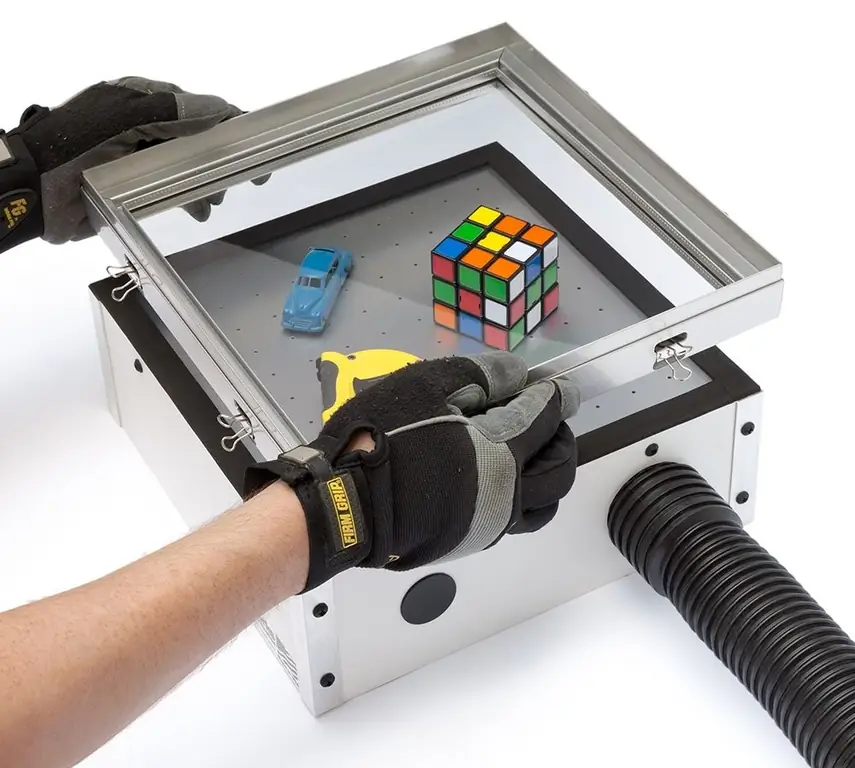
As for the heating zones, they are equipped with infrared elements made in Germany. Temperature control in such zones is carried out using seven-storey power controllers. The evacuation process is carried out by a vacuum pump, and the subsequent blowing by a fan.
DIY vacuum forming machine
In some cases, you can make such equipment with your own hands. The main limitation is that on a home-made machine it will be possible to produce plastic products with a wall thickness of no more than 4 mm. Such a machine will allow you to easily produce small-scale products or single containers, etc. The future vacuum forming machine operator will need the following production kit:
- metal profile pipes and plywood sheets;
- compressor and several electric heaters for heating;
- self-tapping screws for fastening;
- asbestos cardboard;
- quality stainless steel sheet;
- vacuum table;
- you will also need an automatic relay, on / off buttons, LED.
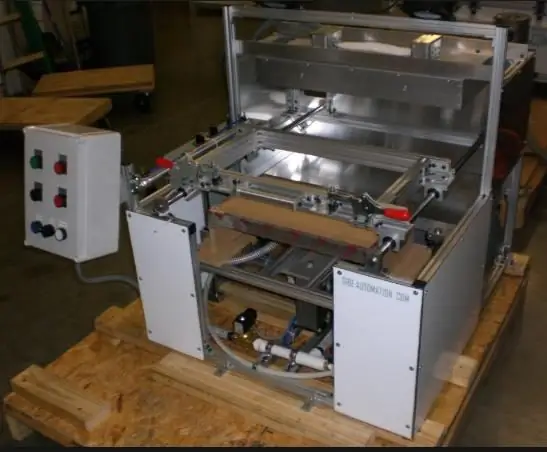
Assembly process
The assembly of such equipment should be carried out in the following sequence:
- To begin with, a clamping frame is made. For this, a prepared metal profile is used.pipe.
- Next, you need to make a plywood box. In addition, you need to assemble a sealed box in which the compressor will be located. A perforated forming table must be installed on top of it.
- The next step is to assemble the stainless steel box to house the heating elements. A workpiece will have to be located on top of this box, this must be borne in mind during installation.
- After that, you should proceed to the installation of relays and switches.
- The last step is the connection between one part of the clamping frame and the molding table.
Based on the foregoing, several conclusions can be drawn. Firstly, a vacuum forming machine is a fairly functional equipment capable of manufacturing most plastic products. Secondly, all products are used in various industries, even in food. Thirdly, if necessary, it is possible to assemble such a structure at home. However, such units consume a huge amount of energy and are very powerful, and therefore the wiring must be appropriate.
Recommended:
Japanese Brands: Products, Brand Names, Top Best Brands and Famous Japanese Quality
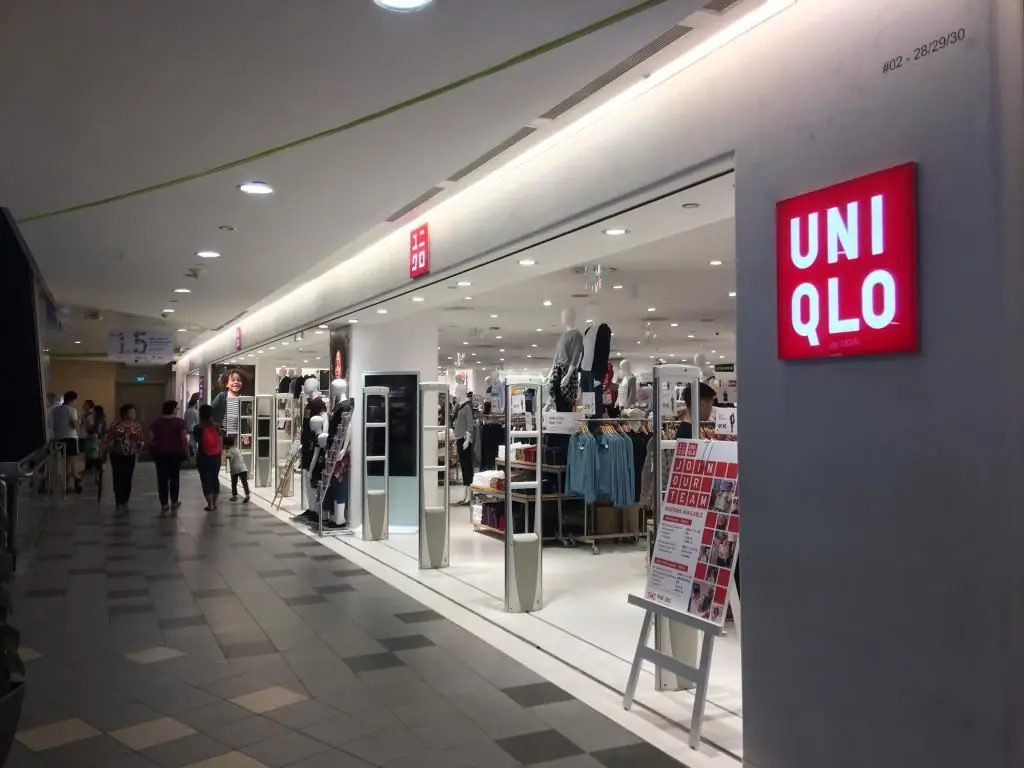
Every kind of goods is produced in Japan. Given the huge number of manufacturers, it is often difficult for the buyer to decide on the choice of products. Everyone knows what Japanese brands of cars and household appliances exist. But this country also produces excellent clothes, perfumes, and cosmetics. We offer a rating of brands of these products
Vacuum lifter: characteristics and working principle
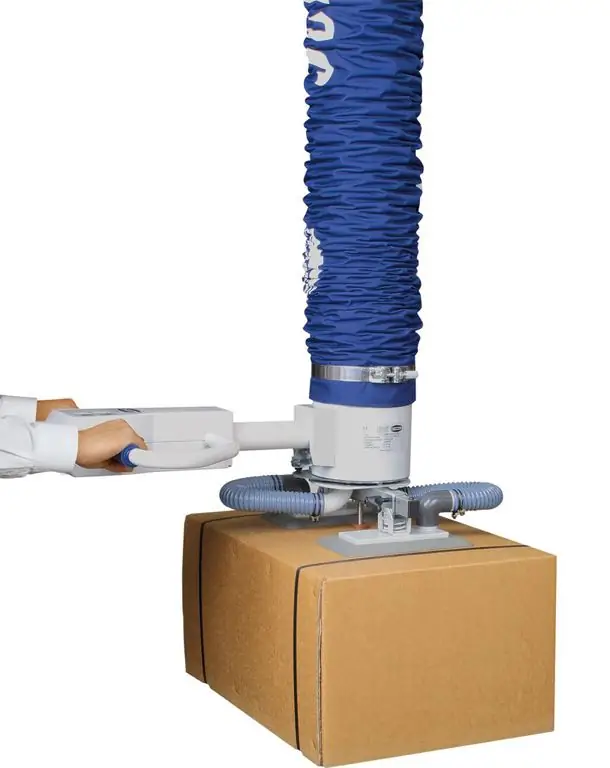
Vacuum handling systems are widely used in various industries and construction. With the help of such devices, typical manipulations with various materials within the framework of logistics and production processes are reliably and safely performed. For quick and frequent high- altitude movement, a vacuum lifter is used, which can have various performance characteristics and design
Container type diesel generator set: types, specifications, working principle and application
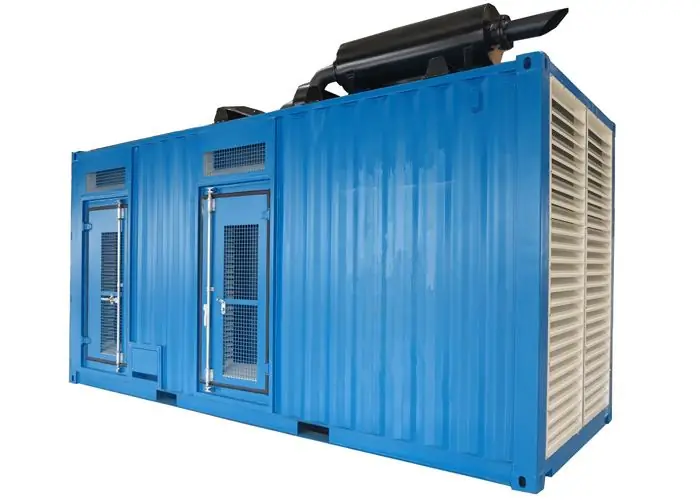
Description of the general design of DGS and the principle of their operation. Classification of installations by mobility. What are container-type diesel generator sets for? Description of containers and equipment, characteristics. Features of FGWilson diesel generator sets. How are DGUs installed? Main rules of operation. Options for additional equipment on request. Locomotive installations
Machine for metal processing: device, principle of operation, specifications
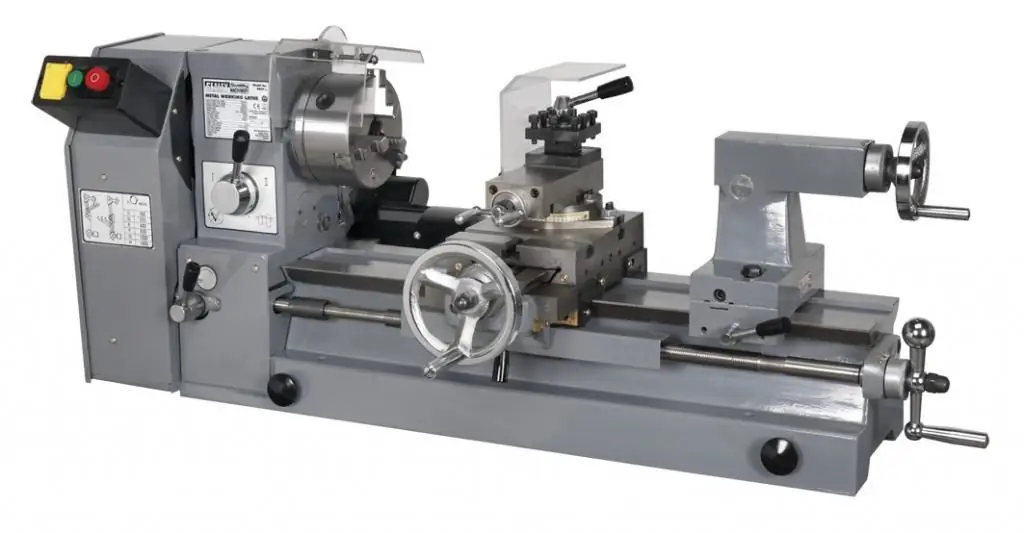
Metalworking machine is an equipment that today has many types, and is also the most widely used. Such a distribution of these units was due to the fact that today people produce a huge number of things from metal. And for successful work, raw materials must be processed correctly
Drilling machine "Caliber SS-16/550": description, specifications, manufacturer, reviews
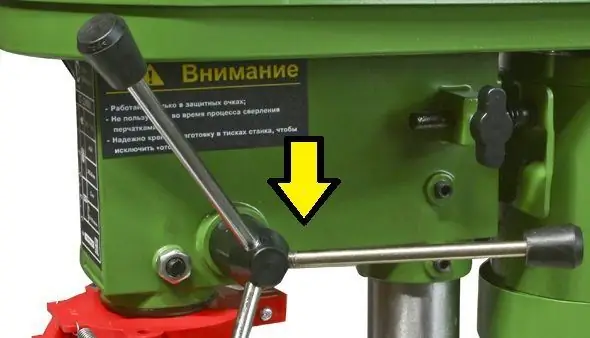
Drilling machine "Caliber SS-16/550": specifications, device, principle of operation, maintenance, photo. Drilling machine "Caliber SS-16/550": description, manufacturer, design features, operation, reviews