2025 Author: Howard Calhoun | [email protected]. Last modified: 2025-01-24 13:10
Vacuum handling systems are widely used in various industries and construction. With the help of such devices, typical manipulations with various materials within the framework of logistics and production processes are reliably and safely performed. For quick and frequent high- altitude movement, a vacuum lifter is used, which can have various performance characteristics and designs.
General principle of operation of the lift
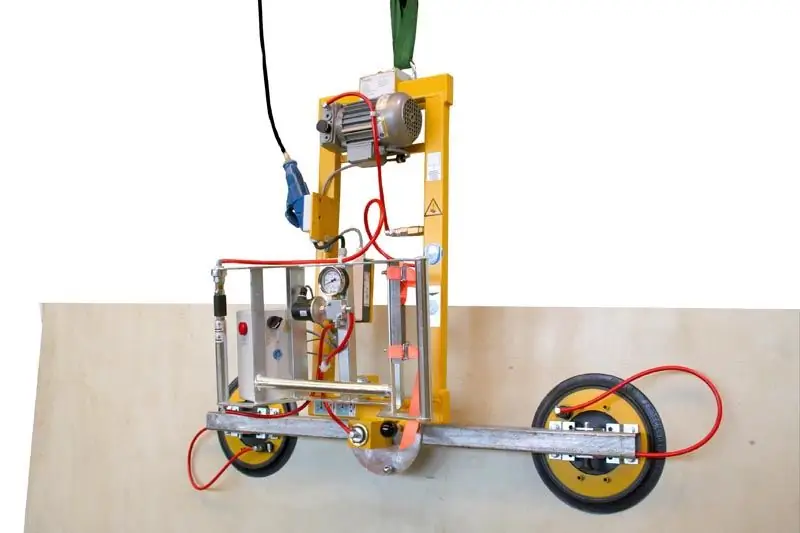
The device contains special vacuum suction cups in the design, due to which the capture of the target material is ensured. Next, the held object is moved along a given motion contour. The principle of vacuum gripping is ensured by the force of a special pump with a generator, which ensures vacuuming of the suction cup. Roughly speaking, under the action of pneumatic compression, a tight connection of the surface of the suction cup andtarget material with a certain load, sufficient to perform subsequent manipulations without breaking. Some modifications provide for the presence of a hook in the mechanical gripping system, which also allows parallel hooking of canisters, buckets, boxes and other objects with a suspension point.
Types of vacuum grippers
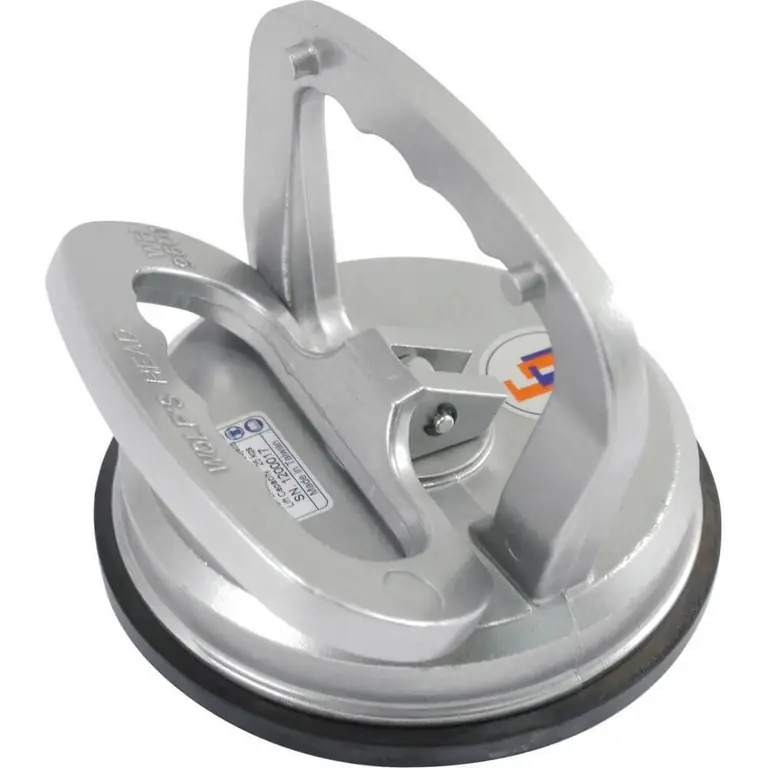
Since the conditions for performing gripping and moving operations can be different, the designs of working mechanisms also differ. We are talking about the base of the vacuum gripper, which is in direct contact with the surface of the object. The following varieties are distinguished:
- Single grapple is the simplest small-sized solution, ideal for handling boxes, cases, slabs, etc.
- Round grip is a special mechanism for working with rough materials. For example, such heads are supplied with vacuum lifters for metal, stone slabs and wood products that have undergone rough abrasive processing.
- Double grip is a system that is used when working with objects that require holding at several points. In particular, if it is planned to move boxes that are glued, connected or insecurely joined in another way by weight.
- Multifunctional grip is the most complex design of the retention mechanism, which assumes the simultaneous operation of four or more fixation heads. This is the best vacuum lifter for glass and other fragile materials, which are presented in largepanels. In this case, holding at several points of load is required, which eliminates the risk of breakage and damage to products under their own weight.
Crane mechanisms in the lift system
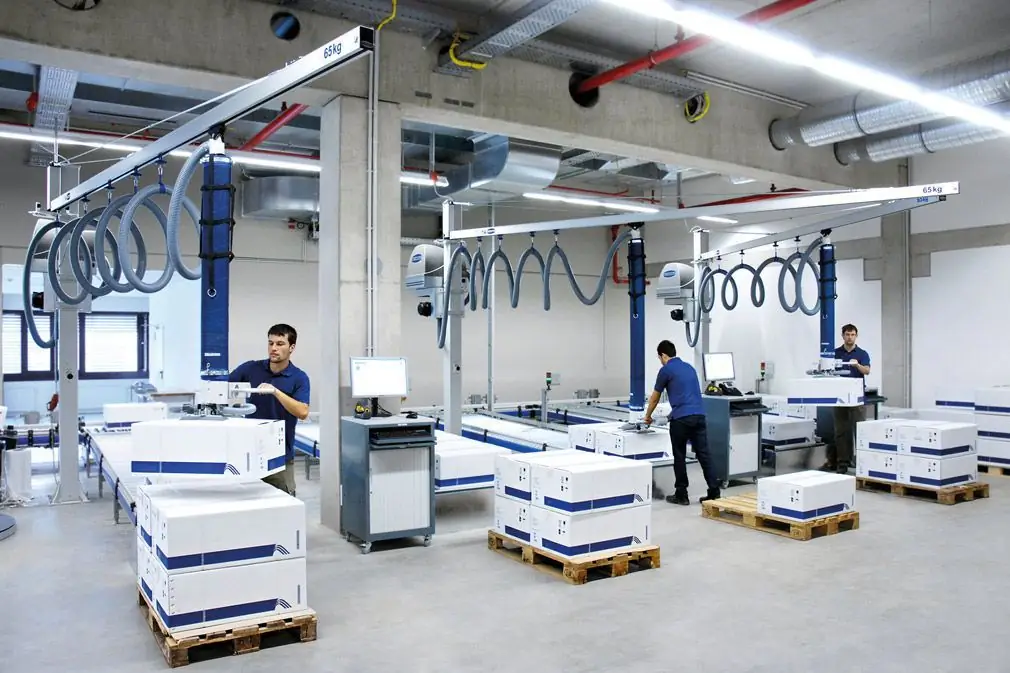
Capture the target is only half the battle. Further, its direct movement is required, for which the crane-manipulator is responsible. Its construction is usually made of steel or aluminum (anodized alloy) beams and profiles, which are designed for specific applications. The basis of the crane is a carrier or suspension base. In the first case, this is a floor vertical column, which is securely fixed and, if necessary, insured with reinforcing elements. In the case of a hinged system, the design of a rail ceiling manipulator is implemented. The vacuum lifter moves along predetermined routes within the working area on rigid suspension mounts, for example, in the form of a chain hoist. The force for the movement of such a transport trolley creates a power supply with its own energy supply.
Communication hose device
Generator, crane and vacuum grippers are interconnected by a lifting element. It directly connects the mobile hoist and suction cup devices. The lifting element acts both as a bearing part and as a full-fledged functional organ that provides power and coordinates the movement of the working mechanism. In the vacuum hose lifter, it is presented in the form of a spring balancer with long handles, which provide directgrip direction. The surfaces of the lifting arm are additionally protected by covers that prevent mechanical, thermal and chemical damage to the critical communication circuit.
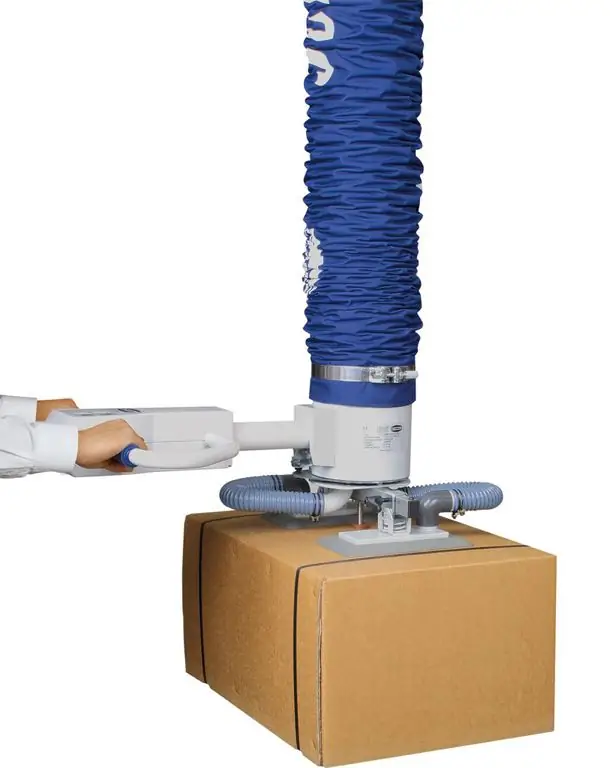
Operation of the control system
The processes of capture and movement in the complex are controlled by the operator through a special console. The simplest button modules allow you to perform the basic operations of the pneumatic system and crane equipment, and in more advanced versions, the mechanisms also support auxiliary functions:
- Pneumatic air savings.
- Turn.
- Long hold in place.
- Adjust travel speed.
Automatic vacuum lifter can work according to a given algorithm in the mode of cyclic repetition of operations without direct participation of the operator. In addition, the latest systems use the wireless principle of communication, which eliminates the need for laying current-carrying bars to the control panel.
Hardware highlights
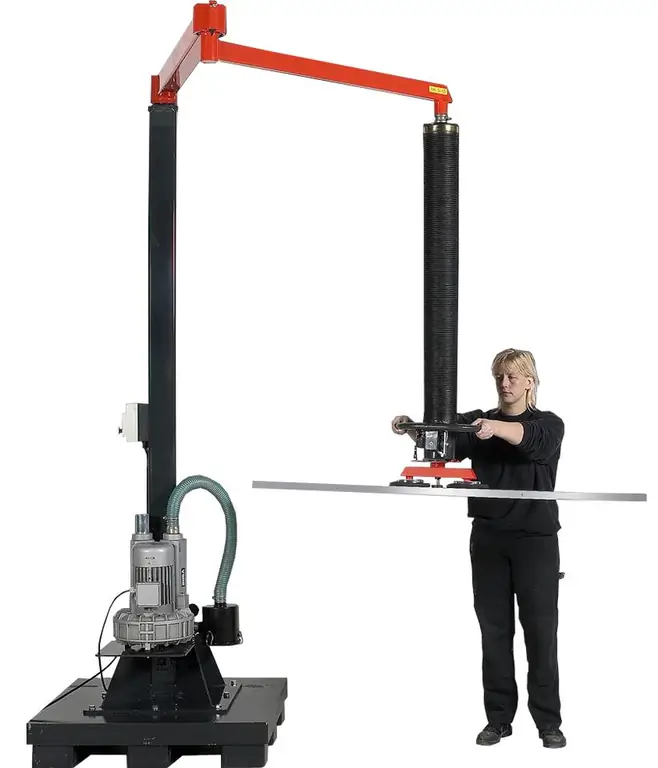
Among the main technical and operational parameters of this equipment are the following:
- Capacity - from 35 to 350 kg.
- Turn angle - from 90° to 180°.
- Drive operating voltage - 220V single-phase mains are typically used.
- Lift Height - Usually limited by the level of the top of the crane and can reach 2.5-3.5 m depending on the model.
- The speed of movement of the vacuum lifter - the maximum average is 45-60 m / min., but in modern models, as already noted, the ability to adjust this parameter is supported.
Features of battery lifts
A less common version of the vacuum gripping and moving system, featuring complete autonomy during the workflow. The presence of rechargeable batteries in the design eliminates the need to connect 12 V electric cables, which also determines the specifics of the equipment application. Such models are used as mobile forklifts in the construction industry to move various materials with flat surfaces. For example, a vacuum panel lifter for cladding can be used both manually and mechanized. Under conditions of complete autonomy, a structure with captured building materials is carried by two workers, and under conditions of mechanization, special equipment with a drive performs the same task. The difference is only in the levels of power supply from the battery - in complex mode or partially (only the capture device is supplied).
Conclusion
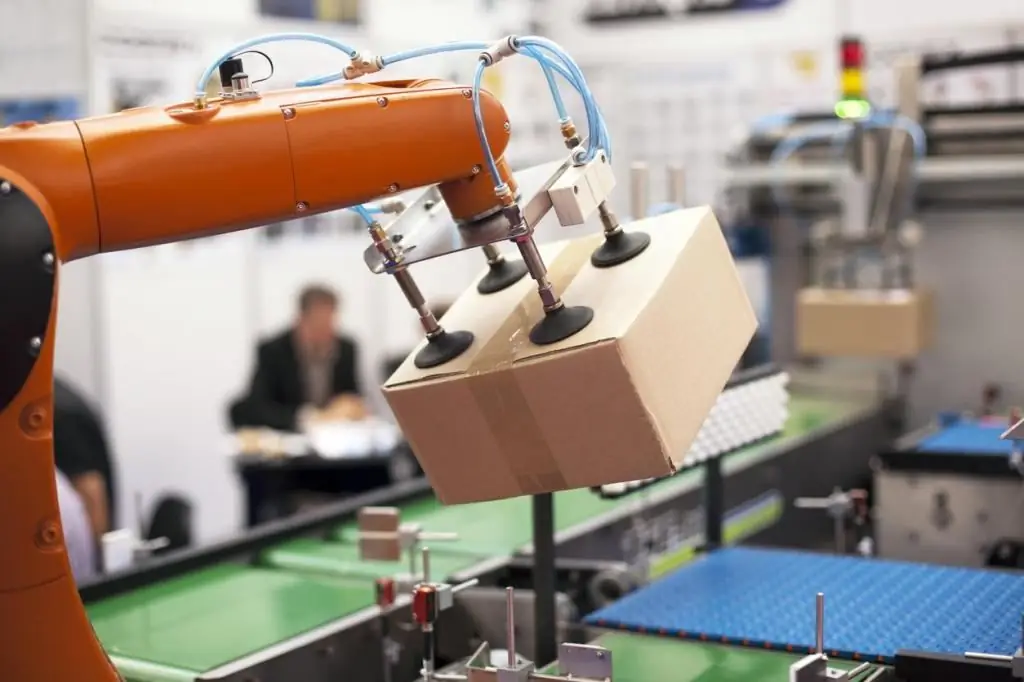
Vacuum lifting equipment exemplifies the combination of technology, functionality and economy. To a large extent, the combination of such contradictory properties became possible due to the principle of operation of the pneumatic gripper mechanism, which consumes a minimum of energy, but at the same time effectively performs its task. At the same time, a number of technicalstructural difficulties in organizing the operation of a vacuum lifter as a stationary equipment in production. To achieve high performance indicators, it is necessary to create an appropriate infrastructure with a power drive, a structural base for manipulators and auxiliary control units. However, these shortcomings are becoming a thing of the past as technological development and general optimization of vacuum-pneumatic mechanisms.
Recommended:
Equipment for gold mining: types, characteristics and working conditions
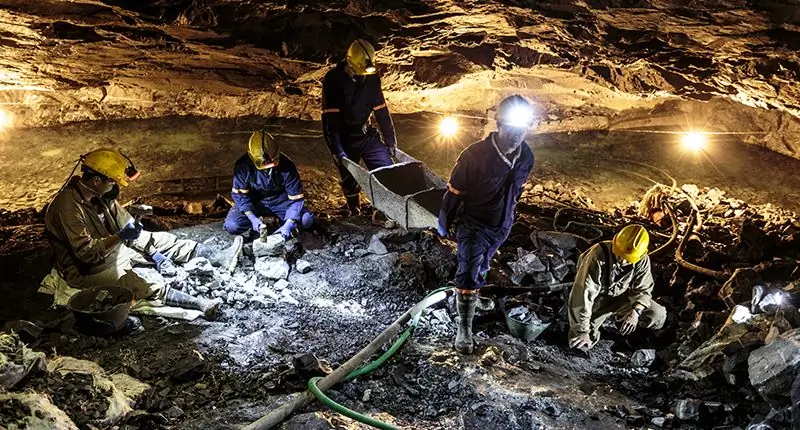
The main amateur and professional types of equipment for gold mining. The use of trays and "lazybones" on the rivers. Description of industrial equipment and the process of gold mining with its help. Dredges for gold miners. Application and possibilities of modern metal detectors. Use of hand blowers. Equipment from the company "Dipsis"
Container type diesel generator set: types, specifications, working principle and application
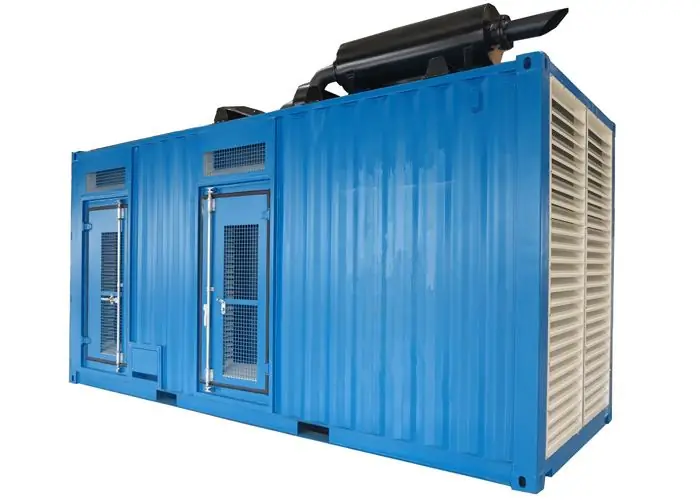
Description of the general design of DGS and the principle of their operation. Classification of installations by mobility. What are container-type diesel generator sets for? Description of containers and equipment, characteristics. Features of FGWilson diesel generator sets. How are DGUs installed? Main rules of operation. Options for additional equipment on request. Locomotive installations
The difference between a branch and a representative office: definition, concept, characteristics, features and working conditions
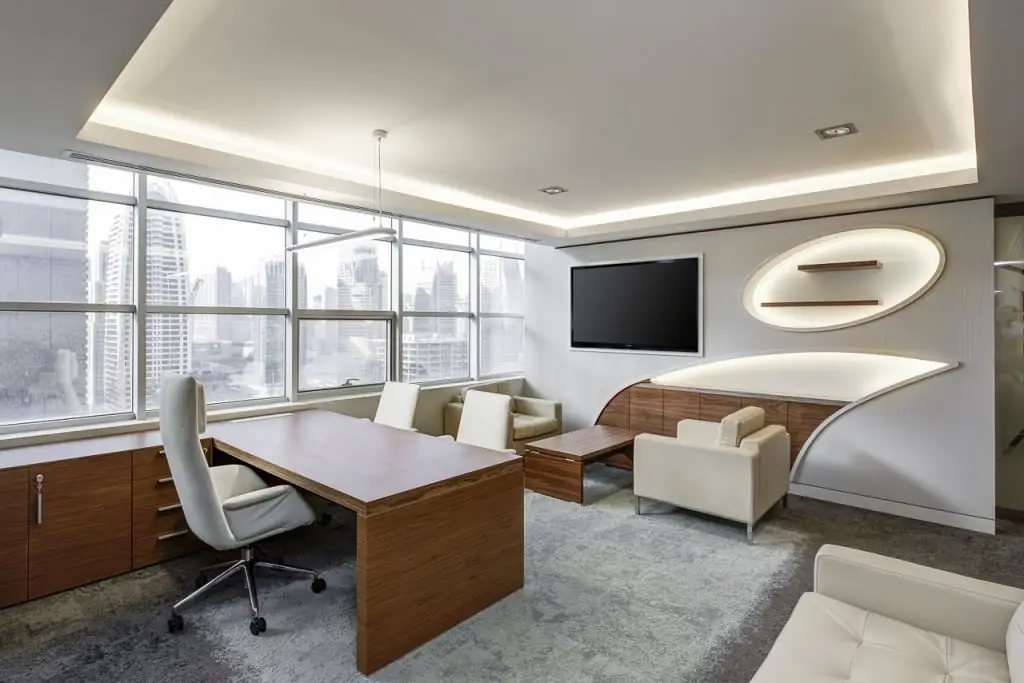
Many people often confuse the concepts of “branch” and “representative office” and use them in a synonymous connotation, but there is still a difference between these terms, which will be discussed in this article. You have probably heard such concepts as "separate subdivision", "branch", "representative office"… What is the difference? This information can be useful for any person, because you never know what will happen to you tomorrow. So, what is the difference between a branch and
Vacuum train: principle of operation, testing. Train of the future
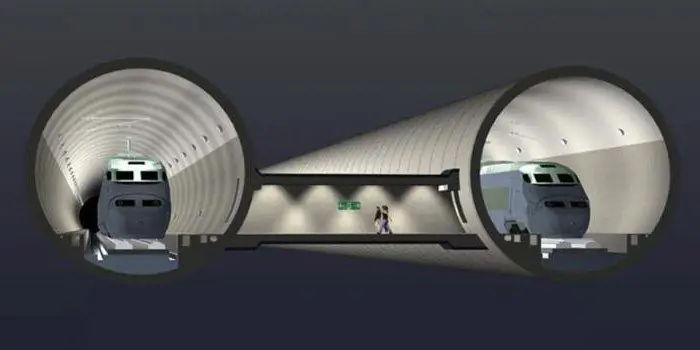
To increase the speed of any vehicle, it is necessary to suppress the friction force as much as possible. This is how spaceships fly into space, which can travel in space for a very long time without resistance. This same feature is at the heart of the project known as the "vacuum train"
Vacuum forming machine: brands, manufacturer, specifications, working principle and application
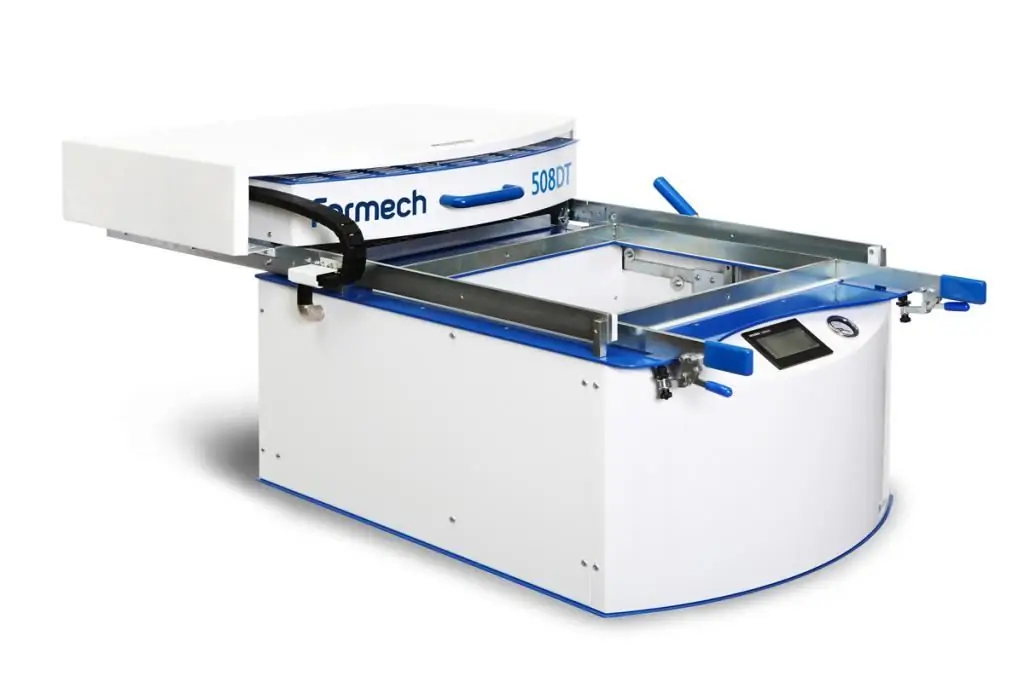
Today, people actively use plastic containers. For the manufacture of such products with a very different and complex shape, a vacuum forming machine is used. Goods made on such machines are actively used not only in everyday life, but also in food, light industry, and the automotive sector