2025 Author: Howard Calhoun | [email protected]. Last modified: 2025-01-24 13:10
Oil refineries receive products from well deposits as feedstock. Basically, these are oil and gas resources that are extracted in the form of an emulsion with impurities and mineral s alts. Without pre-treatment, such mixtures can harm process equipment even at the early stages of raw material processing, so oil dehydration and desalination methods are used, which can be compared with filtration in terms of effects.
General principles of dewatering and des alting technologies
A mixture of oil and associated impurities, as a rule, is formed from several types of liquids, which may include solid particles. In the simplest emulsions, the water component is mixed with crude oil in thin drops along the molecular structure. It should be noted that the processes of dehydration and des alting of oil can be associated not only with natural pollution and dilution of the targetproduct in the well and during production. The technology of airlift operation of wells provides for the intentional dilution of the resource in order to extract it to the surface under downhole pressure. Air or hydrocarbon gases can act as active lifting media, so further oil refining is a mandatory technological measure for resource preparation. Another thing is that the low oxygen content in the airlift technique facilitates the process of separation of raw materials.
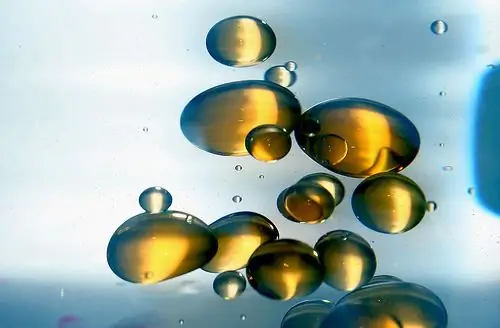
The most common application of oil refining technologies involves the separation of s alt and water at the molecular level. In particular, the simplest technologies for oil desalination include the effect of an electrostatic field created by electrodes with transformer power supply at a voltage of 12-25 kV. The electrostatic field causes the water molecules to move, collide and stick together. As the liquid volume accumulates, it becomes possible to settle it with subsequent separation from the oil phase. This is one of the general principles of operation of dehydration and desalination methods, but technologies involving the addition of various active components that speed up and optimize separation processes are also widely used.
Crude oil and its characteristics
Crude produced oil also contains natural emulsifiers with dispersed impurities and mineralized chlorides. In some cases, depending on the well development technology, gas components can also be preserved - volatile andinorganic. All these components are active and can be considered as mandatory for conservation or undesirable - their status is determined by the requirements for the final product and at the stages of processing determines the list of acceptable methods for dehydrating and des alting oil, which will also affect the choice of equipment for oil refineries. That is, even some of the useful components can harm technological units, therefore, at certain stages of processing, they are also excluded, and then reintroduced.
The process of dehydration is considered one of the basic ones. It is implemented by destroying the water-oil medium with the addition of demulsifiers, which, during adsorption at the phase separation boundary, separate the liquid droplets in the oil. As an active component, a composition should be used, which in itself will be easily separated from the target product. For example, demulsifiers used for dehydration and des alting of oil do not affect the properties of the raw material being purified and do not react with water. These are synthesized compounds that are also inert to equipment and environmentally friendly. Demulsifiers from the oil-soluble group are easily mixed with oil-containing emulsions and at the same time are poorly washed out with water. There are also organic non-electrolyte demulsifiers, the features of which include a dissolving function relative to oil emulsifiers. As a result of chemical action, the viscosity of the raw material also decreases.
Justification for the need for oil desalination
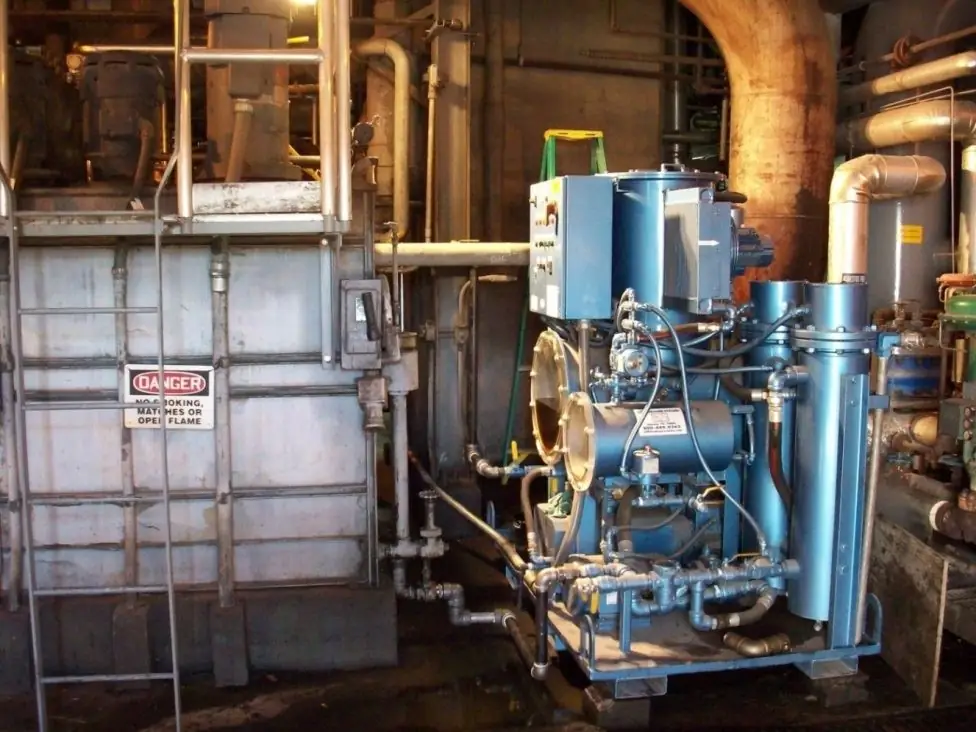
The utility of reducing the s alt concentration in crude oil goes far beyond the damage that corrosion processes cause to equipment. It should be taken into account that oil products with certain sets of physical and chemical properties established by strict regulations are used in production processes and in the supply of transport infrastructure. Therefore, oil desalination is, in principle, a completely rational procedure - another thing is that different technologies can be used to perform this task, not to mention differences in the degree of concentration reduction. For example, in areas where water conservation is planned, a two-stage desalination process can be introduced.
In what ways do s alt management approaches vary? It depends on the underlying technique. So, in electrical methods, the current parameters will matter, and in the framework of chemical treatment for dehydration and des alting of oil, a wide range of active substances are used, which initially affect the content of certain elements in different ways. Mostly these are the same chemicals from the general group of demulsifiers that are introduced into the emulsion under certain conditions. For example, to ensure dense mixing of a substance with oily raw materials, it must be directed upstream at a standard distance from the flush tank or separation zone.
Heating crude oil
One of the preparatory measures, the purpose of which is to create a sufficient temperature regime for the effective implementation of the desalination process. What is it for? Heating has two basic tasks:
- In conditions of high temperature, water particles move at a higher speed, which makes the process of merging molecules into a single structure more active. Accordingly, the process of desalination of oil increases, from which large water compounds are removed.
- Reducing the viscosity is also a consequence of temperature regulation. Viscosity as such indicates the ability of a fluid to resist flow. If this indicator decreases, then foreign components are more easily removed, since they are counteracted by a smaller force of the obstacle.
But what kind of temperature regime will be optimal for the oil emulsion in terms of a positive impact on further separation processes? A specific indicator is set taking into account the characteristics of a particular sample. For example, for light, low-viscosity emulsions, moderate average temperatures are used to prevent boiling of the oil phase, and for heavy hydrocarbon mixtures, it makes sense to increase the thermal effect bar. In most cases, the heating temperature from 100 to 120 °C is taken as the optimal mode for desalination. Mode up to 140 °C is considered elevated.

Chemical oil treatment
Processing or destruction of the emulsion structure in this way also requires special training. In particular, chemical methods of oil dehydration and des alting are carried out under the following physical conditions:
- Forto ensure contact between the oil component and the active substance, the interfacial film must be destroyed beforehand. This will make it possible to add the demulsifier necessary for the further process to the emulsion.
- Sufficient number of collisions of dispersed water particles must be provided for a certain period of time. In other words, by stirring or by rotating the content of the emulsion, the activity of destabilized water particles is artificially increased.
- The settling time has been maintained, during which large water particles will form a precipitate against the background of coagulation.
From this moment, you can start preparing the emulsion for the process of oil desalination by heating. All the positive properties of increasing the temperature of the oil phase operate with a chemical separation method, but it is important to take into account the limitations, since an excessive increase in temperature can lead to negative consequences. In some separation plants, when the temperature is incorrectly estimated, oil evaporates against the background of a decrease in the density of the substance and loss of volume. In order to prevent such effects, many enterprises use lower heating temperatures as a safety net. To compensate for the lack of thermal energy, a larger volume of demulsifier and equipment with higher power are used.
Electric dehydrators for oil desalination
In the simplest schemes for the implementation of electromechanical processes for separating s alt and water from an oil product, electric dehydrators are used. It's multifunctionalequipment that performs several phased tasks, including heating, electrical impact, separation and sump. Horizontal electric dehydrators for dehydration and des alting of oil are based on a tank in which one- or two-stage separation processes take place. Models with a heating function (thermoseparators) also contain a container at the heart of the design, but supplemented by an inlet heating section.
Electromechanical dehydrators are designed with coalescing units, electrostatic grids and the same heating equipment. A distinctive feature of this modification is the implementation of coalescing devices designed to work with phases in the liquid/liquid format. This type of electric dehydrator for oil desalination is used in the maintenance of problematic emulsions.
In the general technology of using electromechanical dehydrators, the final stage is the precipitation procedure. Within its framework, a separated oil flow is serviced, during the movement of which gas release is ensured and temperature indicators are normalized.
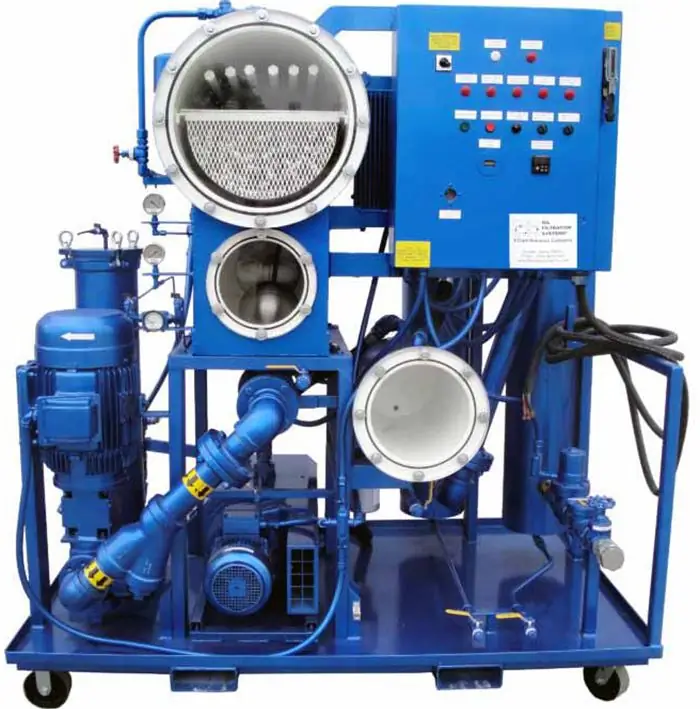
The principle of operation of the electric dehydrator
When a crude oil component enters an electric field, water molecules with a negative charge begin to move, taking on a pear-shaped droplet, facing the positive electrode. On the way to the latter, the drops collide and form a large fraction, ready for further precipitation and separation. The difficulty lies in the fact that one cycle of processing the emulsionwill not be enough to separate water and s alt. Although s alts naturally dissolve in the aquatic environment, they cannot be completely eliminated at high concentrations. For more efficient cleaning, fresh water can be additionally added to the mixture, which, over several cycles of electrical action, will wash out the s alt part. In addition to electrical treatment, the oil desalination unit with dehydrator performs sedimentation (settlement function). For this, optional equipment is used, which can have different shapes, dimensions and auxiliary process control tools.
Although electric dehydrators are technologically complex and expensive equipment, they are increasingly used not only by large, but also by small refineries. This demand is explained by the following advantages of the units:
- Savings. As practice shows, both in terms of the cost of consumables and energy consumption, electric dehydrators are the most profitable solution for oil separation in their class.
- Ergonomics. This is a relatively new equipment, so its design was developed already in the first generations with an emphasis on modern forms of control with automation and electronic dispatch control panels.
- Processing quality. A well-thought-out construction system, coupled with a wide range of chemical catalysts, provides practically laboratory-quality oil treatment for a variety of technological processes in critical industries.
- High degree of reliability of technology. ATThe composition provides for protective devices with automation, which, according to the embedded algorithms, control technological operations with a slight risk of error. At the same time, personnel functions are reduced to a minimum, and in high-tech versions they are replaced by intelligent control systems.
Complex oil emulsion separation
If electric dehydrators are used specifically for the tasks of separating clean oil from water and s alts, then industrial separators in the complex implement the function of separating the emulsion into components. For example, when testing a well, it is necessary to obtain a general analysis of the hard layer in the bottomhole from the extracted sample. In these activities, oil desalination can be considered as an indirect task along with the determination of the concentration of iron or magnesium, but this does not reduce the usefulness of the separator. The fact is that in practice oil refineries themselves are interested not so much in the point withdrawal of s alt from the target product, but in its comprehensive preparation for further use. In this sense, the exclusion of solid impurities along with dehydration and des alting is only welcome.
High-performance separators also work with the provision of inlet-mud and gas sludge. Such installations are used for water desalination at oil treatment facilities for consuming enterprises with a final production cycle. That is, the output should be commercial pure oil, the characteristics of which allow it to be used as fuel or other materials. For example, a separator prepares oilan emulsion with characteristics that allow the production of bitumen, lubricants, synthetic rubber, etc. Such a high quality of oil is obtained by passing through several stages of processing, including scrubbers, coalescers, wash tanks, thermal separators and other functional units in different configurations.
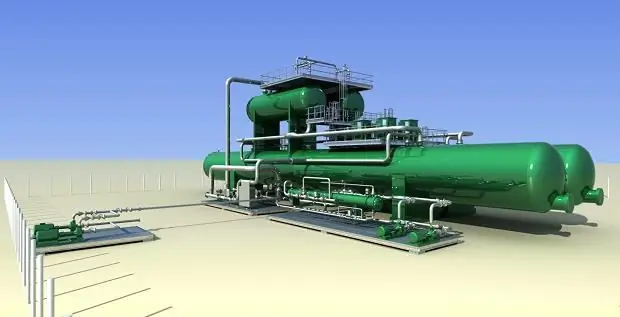
Deep desalination technology
Inadequate des alting of the oil emulsion also affects the state of the process equipment and the quality of the final product. Therefore, for demanding producers, processing plants produce products that have undergone deep separation. In this case, oil desalination equipment reduces the amount of s alts to 3-5 mg/l. How is such a result achieved? Different technologies can be used, but the combined electrothermochemical method is considered optimal.
It is possible to achieve high rates of deep separation with complex cleaning with the connection of diverse methods for removing s alts in the aquatic environment. In this case, intensive deposition in the washing liquid should be ensured with a strong electric current. As for the chemical method, it is also connected in the form of adding active demulsifiers.
Another way to ensure deep desalination is hydromechanical. In this case, chemical and electrical influences are not applied. Emphasis is placed on the gravitational function, which contributes to the natural exfoliation of the aquatic environment from oil. The desalination unit in this scheme is a cylindrical settling tank with a capacity of 100 - 150 m3. It provides for zones for separating fractions, in which liquids flow under pressure up to 1.5 MPa. The temperature regime from 120 to 140 °C is also maintained, which contributes to the processes of media separation.
AC-Direct field impact technology
This method is also called DC/AC field. That is, it is completely based on the electrical action provided by the rectifier in the transformer. Under direct current conditions, the electrostatic lattice acquires polarity (negative or positive), which contributes to the movement of water molecules in the direction of the electrode. As a result of the mutual attraction of molecules to each other, a water layer is formed, which is displayed according to the most convenient scheme.
The complexity of using an electrical installation for dehydration and des alting of oil lies in the fact that the process of coalescence of the aquatic environment involves the risks of a short circuit. This is due to the fact that negative and positive electrodes can contact each other due to the bridges formed during the movement of water particles. This negative factor is eliminated by a triode thyristor, but only in the form of a partial reduction in the probability of a short circuit. In the processing of heavy oil fractions, AC-Direct technology is not allowed or limited for other reasons. In such media, even under thermal exposure, the activity of water molecules is not so active, which in principle reduces the intensity and overall quality of the process.separation.
One way or another, the method of electrical action itself has an advantage over other methods as the most practical, easy to use and undemanding in terms of technical organization. Difficulties are caused only by the requirements for ensuring process safety, which is expressed in the need to use safety blocks, short circuit prevention units, voltage stabilizers, etc.
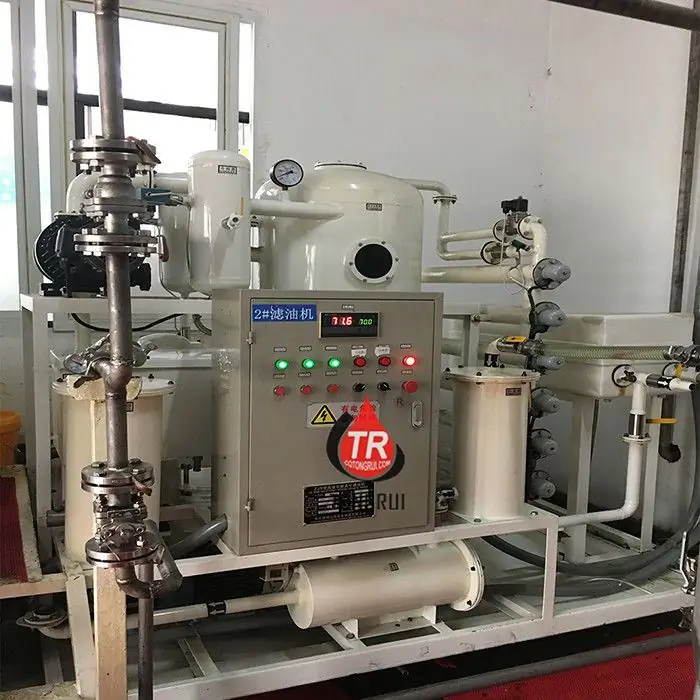
Additional functionality of des alters
Because oil refineries and refineries usually combine oil refining with a range of other process steps, separation equipment is also provided with a range of ancillary features, including:
- Control and measuring functions. Both mandatory and secondary optional measuring instruments are used. For example, pressure gauges, hydrostatic devices, multimeters, dosimeters, etc. In chemical oil desalination plants, special devices are also used to determine the type and amount of demulsifiers.
- Flushing and cleaning operations. The function refers to self-service systems - after pumping out the processed oil, the flushing of the tank and channels that ensure the transportation of the emulsion is activated.
- Power management tools. In electrical installations, as already mentioned, a change in current parameters affects the quality of oil desalination processes, so the correction of the power supply source can be considered asregulatory function. For this, special control panels are used, connected to ammeters, voltmeters and a current converter.
Complete Desalination Plant
At large oil refineries, where cleaning and separation processes are carried out with raw materials moving in the stream, special units are used on flotation and centrifugal principles of operation. The capacities of the UPON in-line oil desalination unit allow processing up to 500 m3/h of raw material, providing a salinity level of up to 3 g/m3. However, to maintain high separation rates, adequate pressure in the oil supply circuit is necessary. For this, separate or built-in compressor units are used. Thus, the average pressure at the inlet to the processing line is 1.1-1.5 MPa.
Under the conditions of implementing a simplified scheme with one-stage mixing, the emulsion is preliminarily diluted with water, after which the mixture is sent to the mixing valve and enters the separation unit. Through the intake pipeline, the in-line oil desalination unit distributes the prepared solution along the entire length of the separation vessel, which makes it possible to effectively separate the fractions. During mechanical separation, electrostatic action can also occur. At the final stage, already purified oil is released into the common circulation channel with direction to the next technological stage of processing or temporary storage. It should be noted that the quality of in-line desalination is rather low due to the exclusion of the functionsump, however, in some areas, the requirements for high performance in the preparation of an oil product put the speed of processing in the first place.
Auxiliary sludge treatment systems
Most dehydrator and separator plants default to a coarse filtration step with drainage of the slurry component. This procedure should not be confused with the removal of impurities, since sludge is a side effect of oil production and can harm the systems of fine purification of raw materials at the very first stages of processing. Therefore, heavy impurities are removed even before oil desalination processes. In this case, sludge is understood as sediments of rocks, sand and other coarse particles that got into the emulsion at different stages of the well operation of the field.
How is sludge cleaning done? Several removal processes are envisaged, but all of them are based on mechanical methods of filtration with drainage and washing. In industrial installations for dehydration and des alting of oil, a pressure blower of 4 bar or more is connected to these processes. In rare cases, the sludge is subjected to thermal and chemical treatment - this applies to special stable compounds, the drainage treatment of which is ineffective.
Conclusion
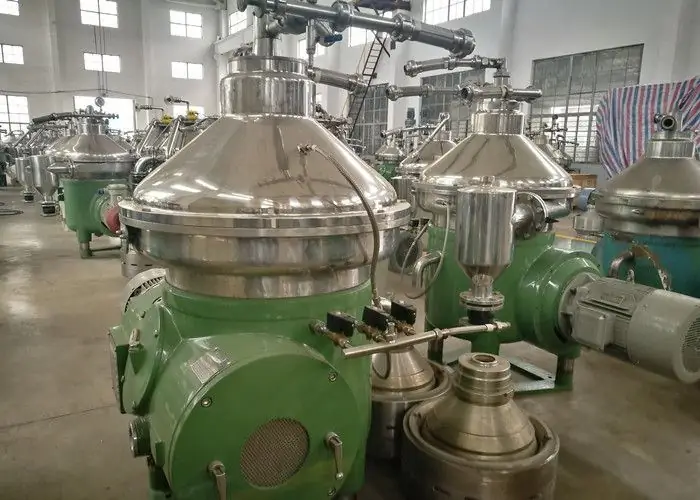
Problems of preparing oil for the main processes of technological processing for subsequent use in the manufacturing sector are solved by different means and methods. Dehydration and desalination technologies perform far from the most importantoperations of this spectrum, but it is impossible to do without them. Modern industry is trying to apply more optimized and energy efficient methods for solving separation problems, which is manifested in the connection of new high-tech installations. In particular, modern generations of oil dehydration and des alting apparatuses are actively developing towards increasing functionality and ergonomics. This is evidenced by the emergence of self-regulating transformers and high-precision measuring sensors, which allow you to keep under control all the main parameters of the cleaning process. The security systems are not neglected either. Both in chemical separation methods and in the use of electric dehydrators, insulating and protective means of protection are used both for the equipment itself and for operators involved in the technological processing of oil.
Recommended:
Low-waste and waste-free technologies: definition, description, problems and principles
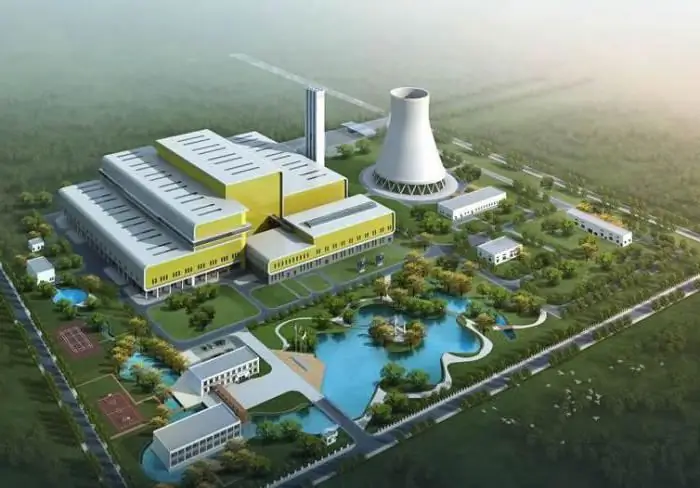
Problems of the harmful effects of industry on the environment have been worrying environmentalists for a long time. Along with modern means of organizing effective methods for the disposal of hazardous waste, options are being developed to minimize the initial damage to the environment
What is produced from oil? Oil refining technology
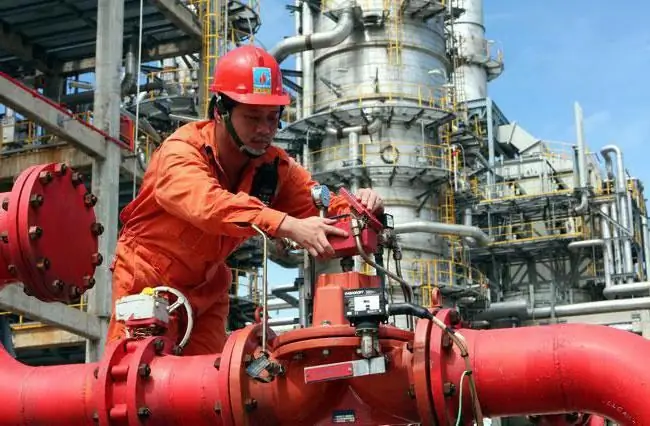
What is produced from oil: features, composition, types of products, photos. Oil refining technology: methods
Water desalination: methods and settings
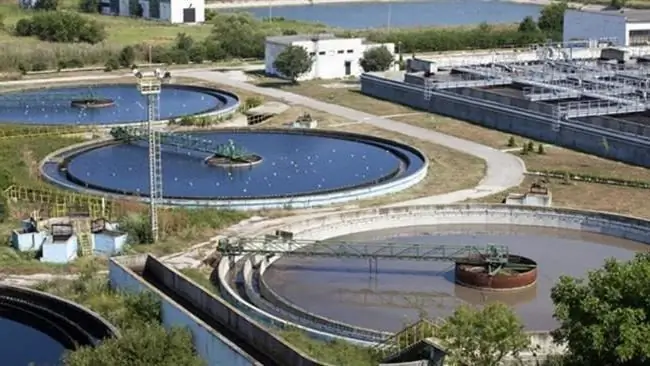
Demineralization of water is the removal of s alts from it. There are several methods by which you can desalinate the liquid completely or partially. Each of them has its own advantages and disadvantages
Oil is a mineral. Oil deposits. Oil production
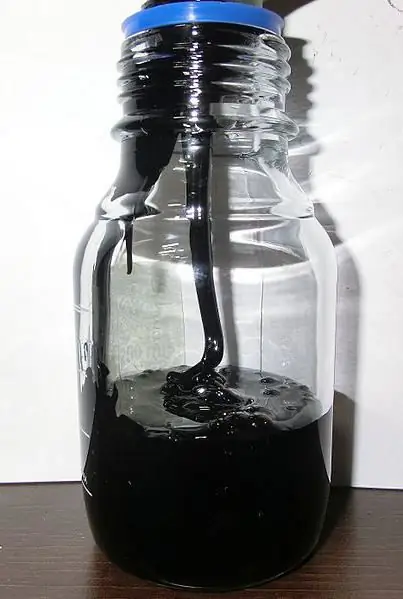
Oil is one of the world's most important minerals (hydrocarbon fuel). It is a raw material for the production of fuels, lubricants and other materials
How is oil produced? Where is oil produced? Oil price
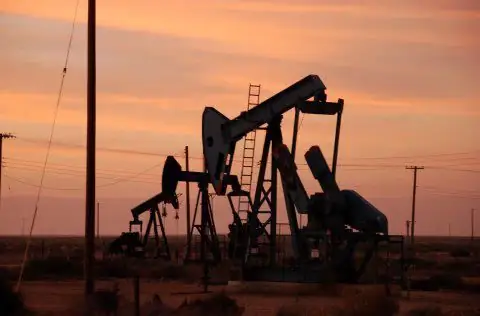
Currently, it is impossible to imagine the modern world without oil. It is the main source of fuel for various transport, raw materials for the production of various consumer goods, medicines and other things. How is oil produced?