2025 Author: Howard Calhoun | [email protected]. Last modified: 2025-01-24 13:10
Even the ancient Egyptians in the ⅩⅠⅤ century BC used a mixture of olive oil and lime to lubricate the axles of wooden chariots. It was this composition that was the prototype of modern multicomponent greases, which are effectively used in many units of modern technology to reduce wear of rubbing parts.
In the modern world, every car owner is well aware that grease is one of the main components that effectively affects the safe and long-term operation of both simple and complex mechanisms with rubbing surfaces. Therefore, knowledge of the composition and range of lubricants is the key to their successful application.
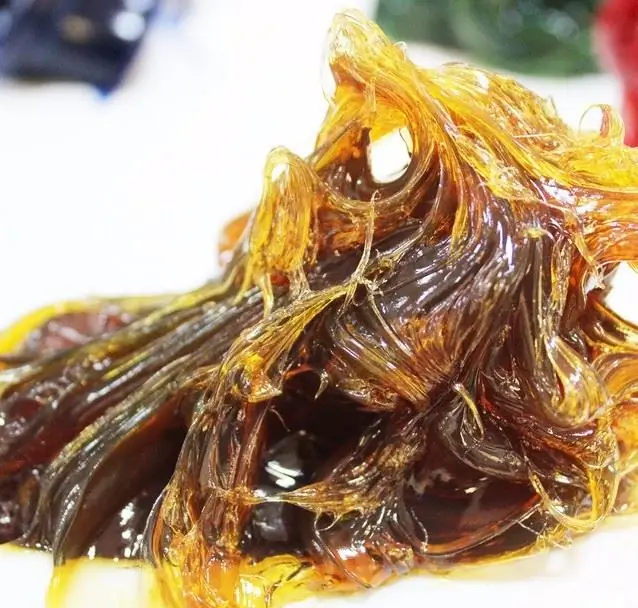
What is it made of
The most common type of lubricant is grease, which is a mixture of thickeners dissolved in a liquid medium. The most effective are three-component systems that contain liquidcomponent (70-90%), thickeners (10-15%) and various additives (1-15%).
As a liquid component, oils of synthetic and petroleum origin, as well as mixtures of these substances, are most often used. Synthetic oils are used for critical components of mechanisms operating in a wide range of contact loads and different temperatures. The oil component is less stable with temperature fluctuations. Liquid oil blends are designed to improve the application of greases and improve their performance.
Thickeners, which are taken as soap or solid hydrocarbons, create the necessary consistency of the product.
Improvement of the properties of greases is achieved by the introduction of additives in the form of additives and fillers. Each of the components performs its function.
Functional usage features
The effective operation of any brand of grease is determined not only by the operating conditions of the material itself, but also by the type of technical unit that it is designed to protect. There are many criteria according to which a lubricant is selected:
- Operating mode of the friction unit (variable or constant loads).
- Design features of the operated unit (size, type, nature of movement).
- Characteristic of the material with which the lubricant comes into contact.
- External conditions for the functioning of rubbing surfaces.
- Terms and possibility of replacing the protective coating.
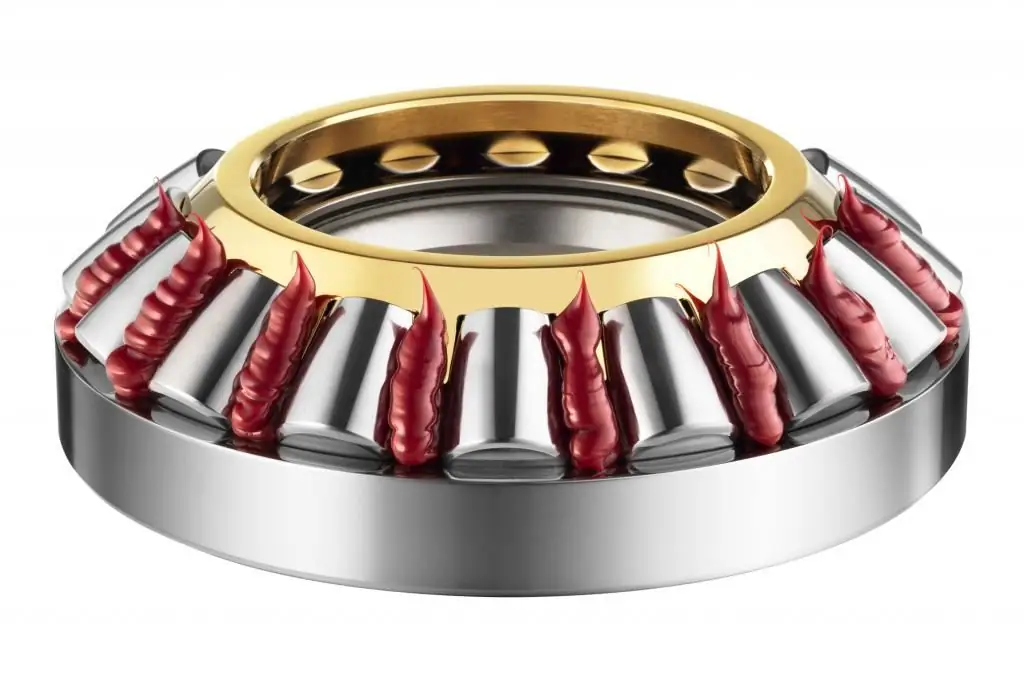
Based on these criteria, the main purpose of greases can be formulated:
- Reducing the force of friction between the mating elements of the mechanism.
- Reducing the noise and vibration of the unit during operation.
- Prevent wear of rubbing parts.
- Protection of metal surfaces from the harmful effects of the environment.
- Effective sealing of gaps between mating elements.
It is necessary to correctly determine which greases to use to perform several functions from the list that can ensure reliable operation of the mechanism. Why not everyone? Because there is no universal lubricant that can perform all these functions at the same time.
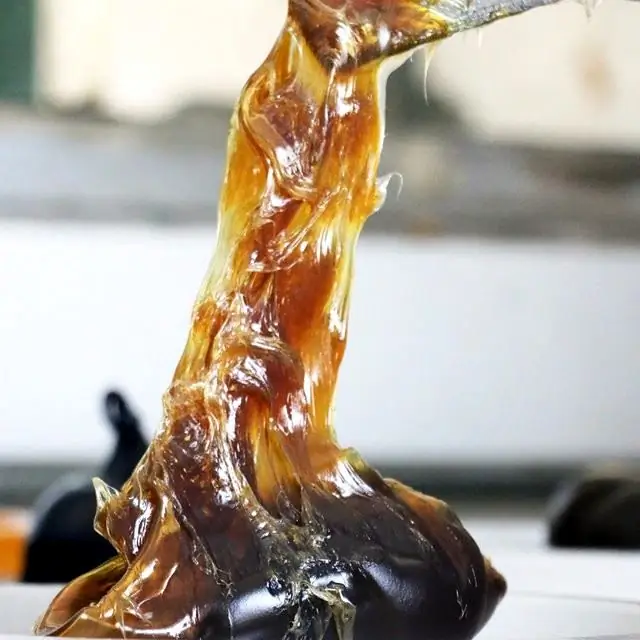
Requirements for lubricants
Grease is a tool to ensure the efficient and long-term operation of any unit with rubbing surfaces. The following requirements apply to such materials:
- The ability to maintain its properties under various temperature effects.
- Do not destroy the surface structure in contact with grease.
- Withstand various types of loads without changing its properties.
- No harmful effects on the human body and the environment.
- Economical operation and low material cost.
Also, lubricants may be subject torequirements of a particular nature, for example, in some mechanisms, the optical and dielectric properties of greases are very important.
Operation principle
Why is metallic soap added? It acts as a thickener, creating a container for oil. Soap in grease is like a sponge. It forms a lattice frame. In a simple sponge, it is foam rubber. With a large mechanical load or an increase in temperature, oil is squeezed out of this molecular structure. This action effectively reduces the friction force of the mating parts.
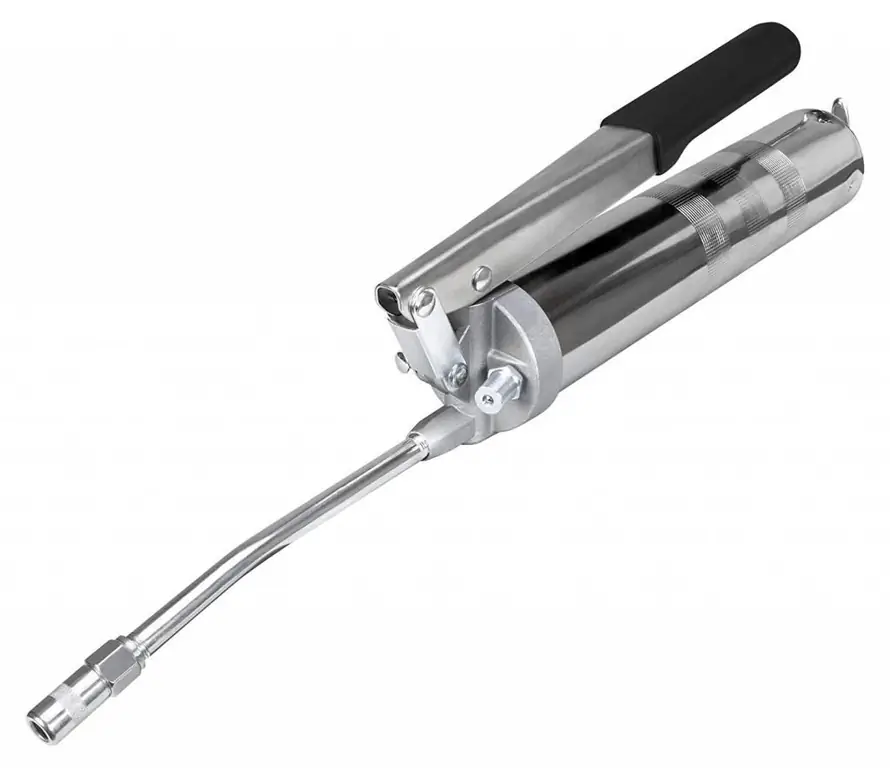
Relieving the load helps restore the lubricant to a plastic state that prevents the oil from spreading and also keeps it on an inclined and vertical surface.
Pros and cons
Qualitative definition of grease can be characterized by its advantages in comparison with liquid lubricants. Its main advantages include:
- Increased lubrication coefficient increases the wear resistance of rubbing surfaces.
- Better corrosion protection.
- High coefficient of adhesion allows grease to be held securely in vertical and inclined planes.
- Increased sealing properties protect mating assemblies from foreign debris and moisture.
- Higher operating temperature range.
- Long grease life increases the economics of grease application.
Alongwith the advantages of a plastic material, there are several disadvantages of using it:
- Slows down the cooling of rubbing surfaces.
- Soap lubricants have poor chemical resistance.
- The ability to retain foreign inclusions significantly increases the wear rate of mating nodes.
- Difficulty delivering lubricant directly to rubbing surfaces.
Basic Features
Of great importance during the operation of any mechanical unit is the correct choice of lubricant. That is why it is necessary to know well the main characteristics of greases, which largely depend on the substances that make up their composition, as well as on the operating conditions of the equipment.
The main properties of plastic materials can be divided into several groups, characterized by the following indicators:
- Strength.
- Viscosity.
- Stability.
Strength
All brands of greases are characterized by a special indicator - tensile strength. This coefficient indicates the value of the minimum load at which the destruction of the molecular framework occurs and the material is deformed by shear.
If the load of friction surfaces exceeds the tensile strength, then the lubricant begins to spread. This can lead to serious deformation of the nodes and even to accidents (if we talk about cars). When the load is reduced, the lubricant returns to an elastic state, due to which it is effectively retained even on verticalsurfaces.
The strength is affected by the following factors:
- Type of thickener and its concentration.
- Properties and composition of the liquid component of the material.
- Concentration and composition of fillers.
- Mode and method of making grease.
The tensile strength index is significantly affected by the temperature in the node. When choosing a lubricant, consider the minimum force that must be applied to move the mating surfaces.
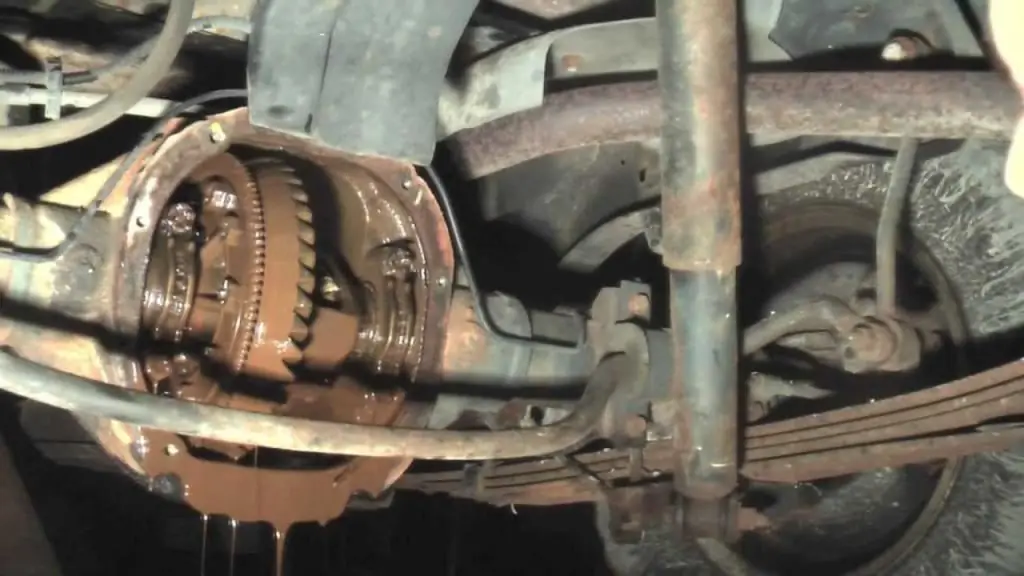
Viscosity
This indicator characterizes the action of grease directly at the point of friction after its transition to a liquid state. In lubricating liquid oils, viscosity is a constant value. In plastic ones, it directly depends on the speed of rotation of the node and on temperature, therefore this indicator is called effective viscosity.
Increasing movement speed will decrease this stat. If the temperature is constant, then it is expressed by the viscosity-speed characteristic. When the speed of movement of the rubbing surfaces remains constant, and the temperature changes, it is determined by the viscosity-temperature characteristic. An increase in temperature in the area of friction nodes significantly reduces the viscosity of the plastic bond.
Stability
This indicator means how much the material is able to maintain its properties over a certain period of time under the influence of external factors.
Depending on the type of external influence, the stability indicator can be divided intothe following groups:
- Mechanical stability refers to the ability to retain the properties of a grease after deformation. This is highly dependent on exposure time and intensity. Unstable type grease is not suitable for applications that are not very tight.
- Thermal stability refers to the ability of a grease to maintain its performance when briefly exposed to elevated temperatures. Its components can degrade into thickener and oil at various peak temperatures.
- Chemical stability characterizes the properties of a lubricant to withstand the harmful effects of various acids or alkalis. More often, this property indicates the resistance of a substance to oxidation by oxygen.
- Physical stability refers to the ability of a lubricant to evaporate or release its own liquid component without application of a load.
There are also many other grease properties:
- an indicator of the penetration of the composition into the material of rubbing surfaces;
- dropping point at which the first drop of a substance is released;
- anti-wear properties and others.
Classification
There are many parameters by which a standard classification of greases is made. Based on it, the choice of material for specific purposes is carried out.
By use, greases are divided into the following categories:
- Preservative - protect the metal surface during storage.
- Anti-friction - reducewear of rubbing parts.
- Rope - used to prevent wear of steel ropes.
- Sealing - used to seal valves and threaded connections.
According to the type of oil base, greases are divided into the following types:
- Based on refined petroleum products.
- Formulations using synthetic oils (synthetic).
- With vegetable oil.
- Oil blends.
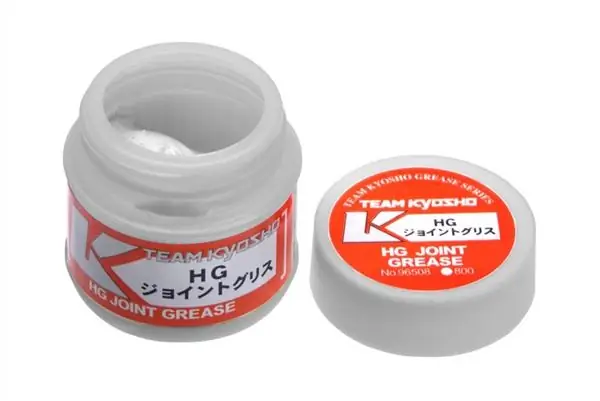
Classification of greases by type of thickener:
- Organic. They contain a thickener made of polymeric material.
- Inorganic. Includes inorganic thickeners.
- Soapy. Soap is used as a thickener.
- Hydrocarbon. They contain a wax or ceresin thickener.
Marking
In accordance with the listed properties and compositions, lubricants are labeled. Previously, it was arbitrary, expressed by an alphabetic or numeric name, as well as by the name of the manufacturer. Later, the labeling process was standardized. Lubricants began to be designated by letters:
- The field of application is indicated by letters: U - universal, I - industrial, Zh - railway, P - rolling.
- Depending on the temperature of use, universal greases are marked with the letters: T - refractory, C - medium melting, H - low temperature.
- Specific propertiesare indicated by letters: Z - protective, V - moisture resistant, M - frost-resistant, K - rope.
For example, UNZ grease means that it is universal, low-temperature, protective.
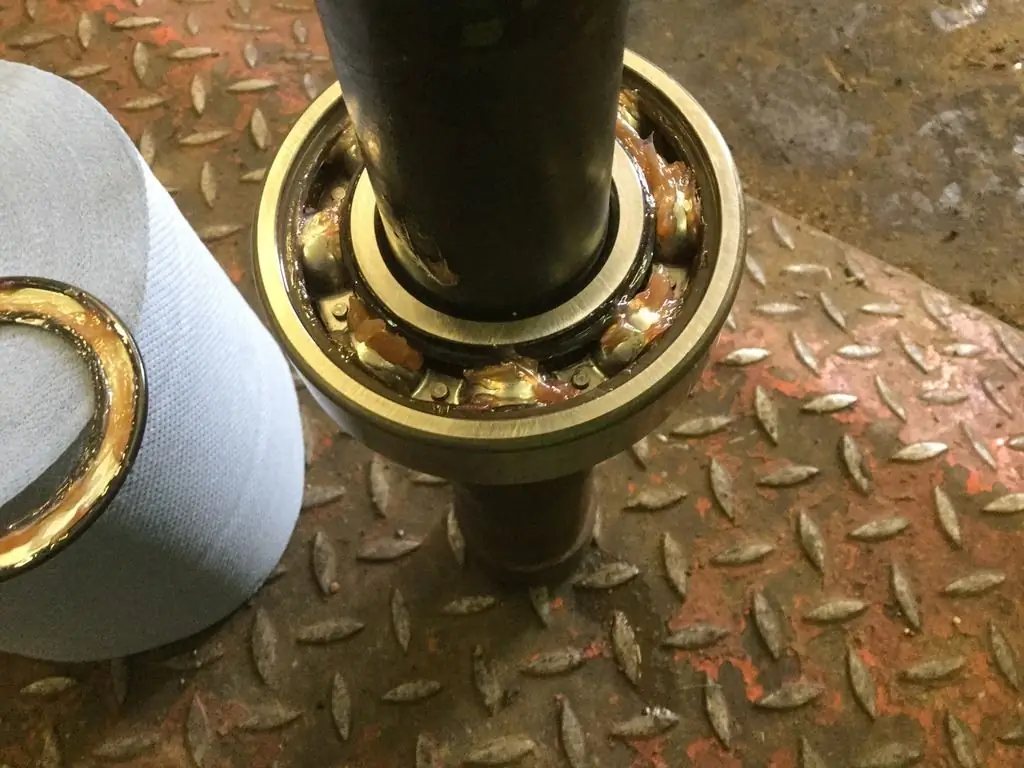
Remember that the effective performance of any mechanical equipment or assembly depends on the right lubricant. Its use will significantly reduce the friction force in the mating nodes and extend the life of the mechanical device.
Recommended:
Tinned copper: concept, composition, manufacture, characteristics and application
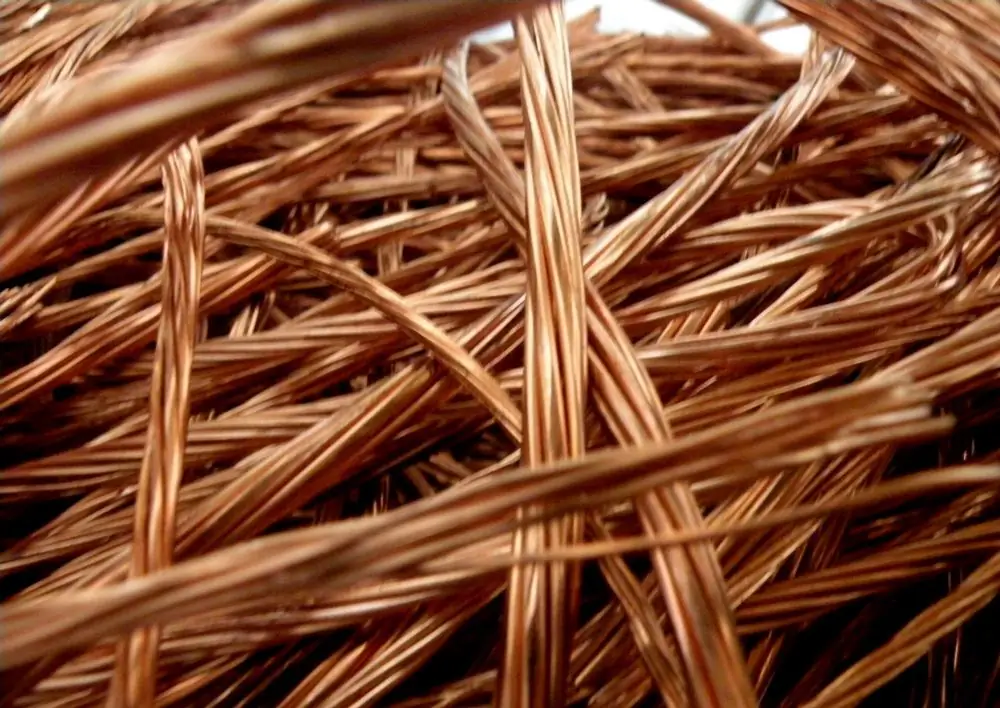
Tinning means to cover metal products with a thin layer of tin, which in turn prevents the process of oxidation of metal surfaces. But if we take into account the maintenance of the soldering iron, then the process is slightly different
Reinforced concrete is Concept, definition, production, composition and application
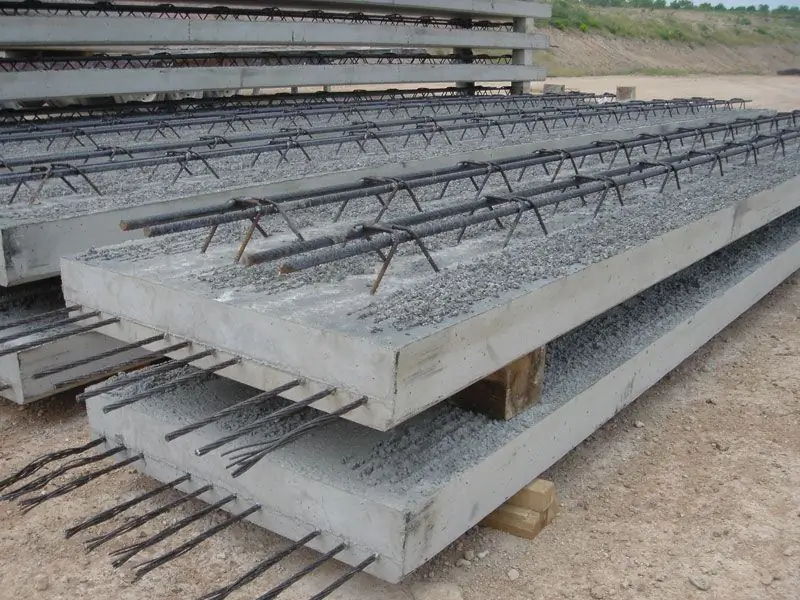
One of the most popular building materials is reinforced concrete. These are durable slabs that are used during the construction of high-rise buildings. The material is able to withstand significant loads. It is not subject to the destructive influence of external adverse factors. Features of reinforced concrete, its production technology and application will be discussed in detail in the article
"Grad": MLRS firing range. Firing range "Grad" and "Hurricane"
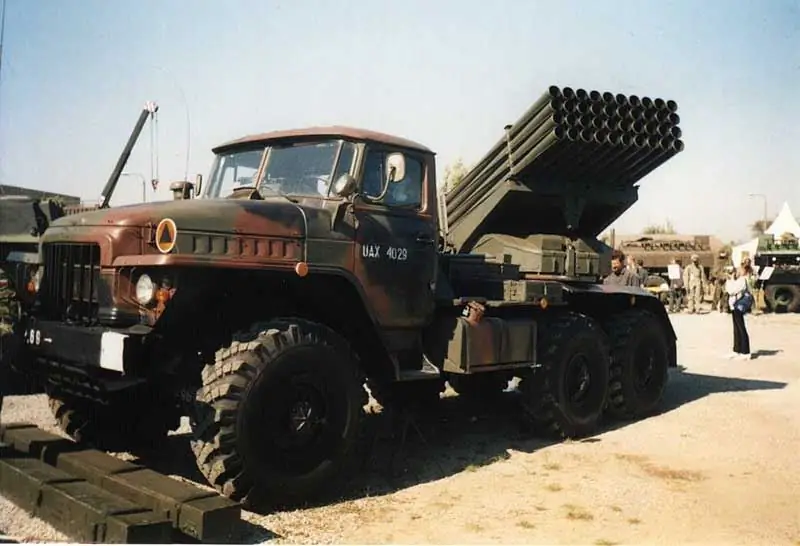
The firing range of the Grad and Hurricane makes it possible to carry out tasks to defeat enemy equipment and manpower, both in open areas and in natural shelters. The salvo of the launcher will also cover lightly armored vehicles, as well as mortar and artillery crews in places of concentration. These products of the domestic military industry will be discussed in the article
What are the best lithium greases? Features, benefits, application examples
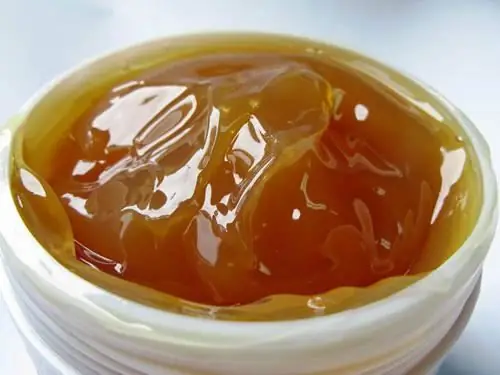
The modern lubricants market is a wide range of various products, however, most motorists most often use lithium greases. This is due to the fact that such compositions are versatile and can be used in different areas
Firing range of 120 mm mortar. mortar firing range
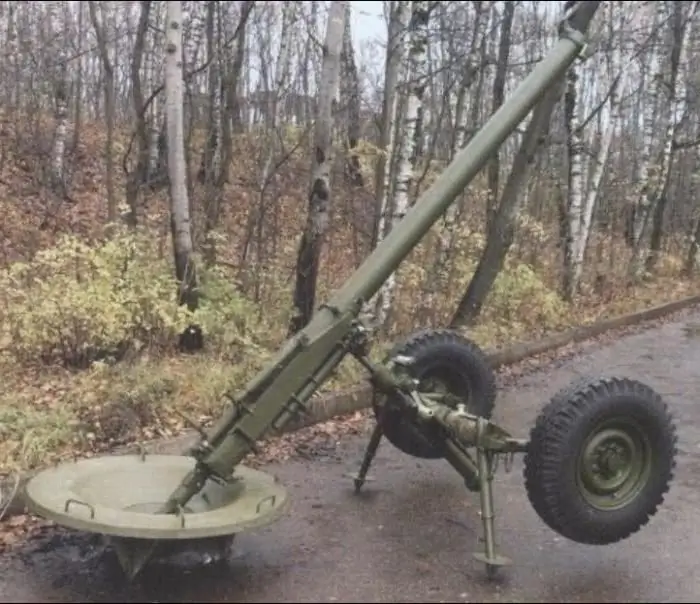
At the dawn of the 20th century, it was time for change in the organization of military operations. While the belligerents dug in, dug multi-way trenches and fenced off with barbed wire, all the power from the use of firearms, from rifles to machine guns, and powerful gun fire could not inflict much damage on the fighters