2025 Author: Howard Calhoun | [email protected]. Last modified: 2025-01-24 13:10
What is tinned copper? Let's start with the fact that at present this metal is widely used in various industries. Among the distinctive features of the wire, which explain the demand for it, one can note its resistance to external influences: precipitation, temperature changes.
Also, copper wire compares favorably with other metals by its high thermal and electrical conductivity.
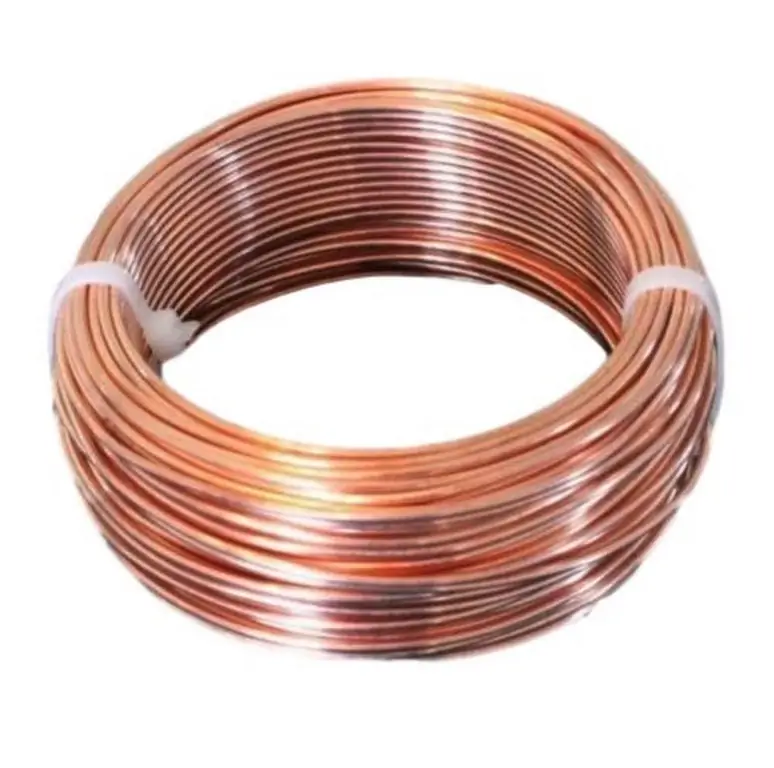
Distinguishing parameters
Tinned copper has high ductility and excellent machinability. It is this material that is used in electrical engineering for the manufacture of conductive conductors of copper cables, braids for military and civilian products.
Let's try to find out the difference between tinned and untinned copper. The first option is more protected from external influences, since the wire is covered with a layer of tin. This metal protects the metal thread from any manifestations of corrosion, giving the material increased tensile strength. Tinned copper will not break when bent.
Receive
Perform galvanized tinning. It makes it possible to apply a thin, even tin coating (from 1 to 20 microns) on copper. The thickness of the layer throughout the wire is the same, so there is no "double diameter" of the wire.
Tinned copper is currently available in two varieties:
- copper soft tinned wire (MML);
- solid tinned copper wire (MTL)
Features
The main distinguishing feature between them is the ability to bend. The diameter of tinned copper with aluminum can vary significantly. The most widely used wire, whose diameter is in the range of 0.02-9.42 mm.
To make it, use an ordinary copper wire on a coil, subjecting it to galvanic tinning. The material is passed through a tin bath containing molten tin. So that it does not enter into oxidation with atmospheric oxygen, the surface of the bath is covered with substances that are not able to pass air. In particular, charcoal can be such a substance.
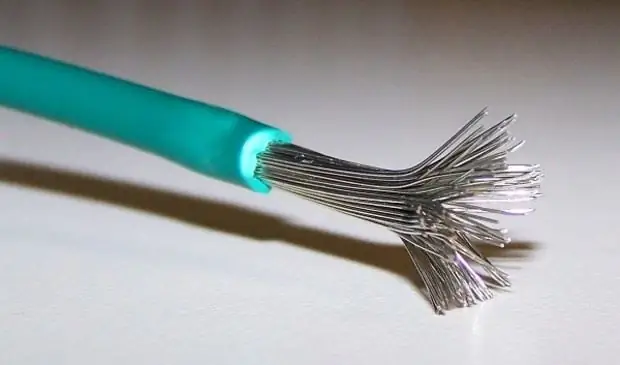
Steps
In order to understand what tinned copper means, let's take a closer look at the main stages of the ongoing process. First, the copper wire, which is mounted on a special feeder, is cleaned. The essence of the process is passing through special rubbing brushes moistened with a solution of zinc chloride (this s alt is obtained by reacting granulated zinc with hydrochloric acid).
Next, the wire is lowered intotinning bath, where tin is located in molten form, as a result, tinned copper is obtained. The photo of the finished product shows the uniformity of the applied layer.
It is important at this stage to prevent the appearance of "sagging" on the wire, as they lead to rejection of the lot due to deviations from the declared diameter.
At the next stage of creating tinned wire, the material is passed through rubber brushes (their diameter should not exceed 0.14 mm) or through a drawing mechanism with diamond discs. A similar procedure is required to give the wire surface a perfect uniformity.
Then the material is cooled by passing through a container of cold water. The cooled wire is re-passed through the drawing mechanism with diamond discs, getting rid of the remaining "sagging".
The final moment is the wire feed to the receiving mechanism. Here it is fixed on a special coil. Having gone through the entire chain, the wire is absolutely ready for sale or for the subsequent creation of a cable of different sections. Before the tinned wire goes to consumers, it has to go through the control procedure. Its essence is to carry out several operations that will prove its compliance with TU 16-505.850-75.
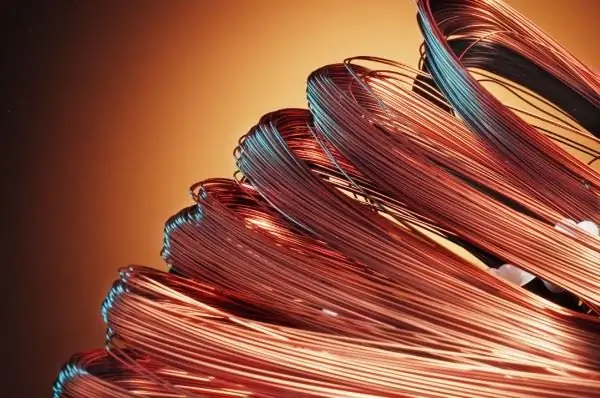
Features of soldering iron
The essence of tinning is to cover the copper part with a thin layer of tin, which protects the product from corrosive processes. Soldering iron maintenance has some distinctive features.
First, it is important to prepare the work surface. takenew soldering iron, sharpen the tip of the device. To do this, the sting is pulled out, armed with a soldering iron or an electric machine, at an angle of up to 400, then sharpening is carried out. If the soldering iron is being prepared to work with small radio components, it must be conical.
Pros recommend that the width of a sharp wedge is not less than a millimeter. If the shape of the sting proposed by the manufacturer suits the consumer, you can skip this step. Since the soldering iron rod is coated at the factory with a patina - greenish copper oxide, it is important to remove the coating with abrasive material (sandpaper) before tinning. Next, the tip is returned to the device, the soldering iron is connected to the electrical network. You need to wait for the surface of the sting to warm up evenly, and then proceed to tinning.
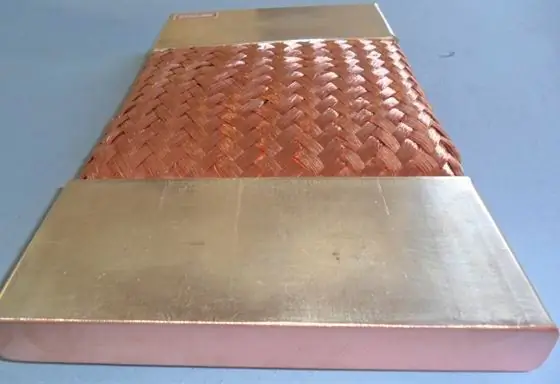
Technology
During operation, copper and its alloys are capable of forming oxides with atmospheric oxygen. To prevent such situations, copper is tinned with tin. To perform such a procedure at home, you will need solder, a soldering iron, rosin or flux. In order to properly tin the copper wire, it is important to warm up the soldering iron with high quality. The conductor is pre-cleaned of insulation, removed (depending on needs) insulation. When working with stranded wire, twist it before tinning.
Then they cover the copper core with rosin, heat it all over with a soldering iron. Tin is taken on the heated tip, it is distributed over the entire section of the wire, pre-treated with rosin.
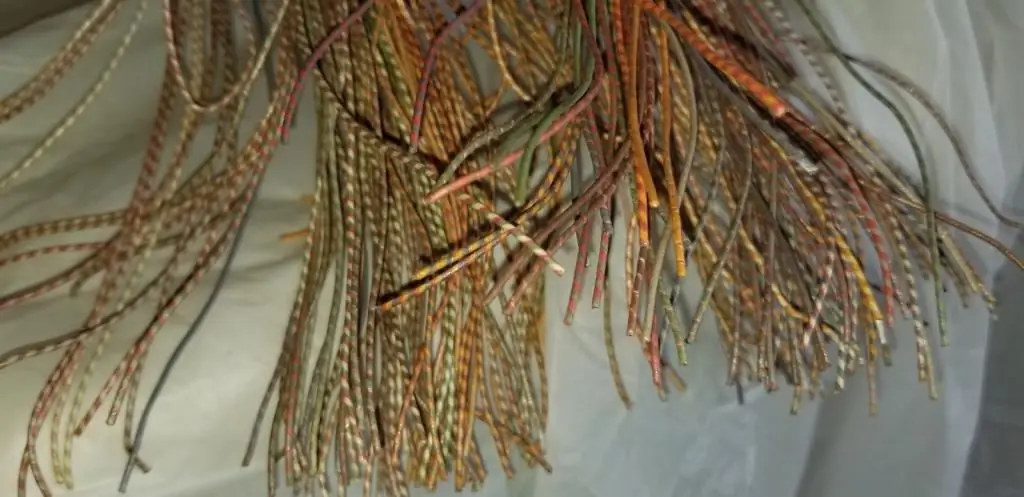
In headphones, due to mechanical stress, low-current conductors often break. Since they have a small diameter, a slightly different technology is used for tinning. Take a soldering iron with a thin tip, rosin, solder wire. First solder broken wires, then proceed to solder a new wire. The wires are covered with a layer of varnish (to provide insulation), so it is first removed with a heated soldering iron and rosin. Then covered with a layer of tin, which greatly simplifies subsequent soldering.
Recommended:
CVG steel: composition, application and characteristics
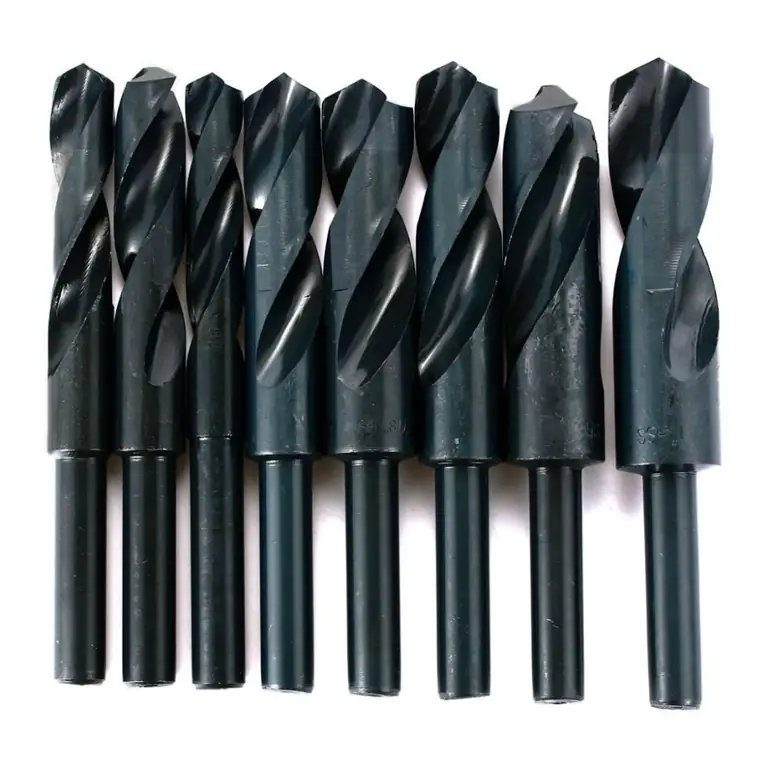
Studying metallurgy and all its subtleties, you involuntarily begin to experience an irresistible desire to get as much useful information as possible and spend as little time and effort as possible on it. In such a case, this article exists. It contains all the most important information related to CVG steel: deciphering the marking, studying the composition, the use of this alloy, as well as a brief excursion into substitute steels and foreign analogues. Everything you need in one place for everyone's convenience
Rip-stop fabric: what is it, composition, characteristics, weaving threads and application
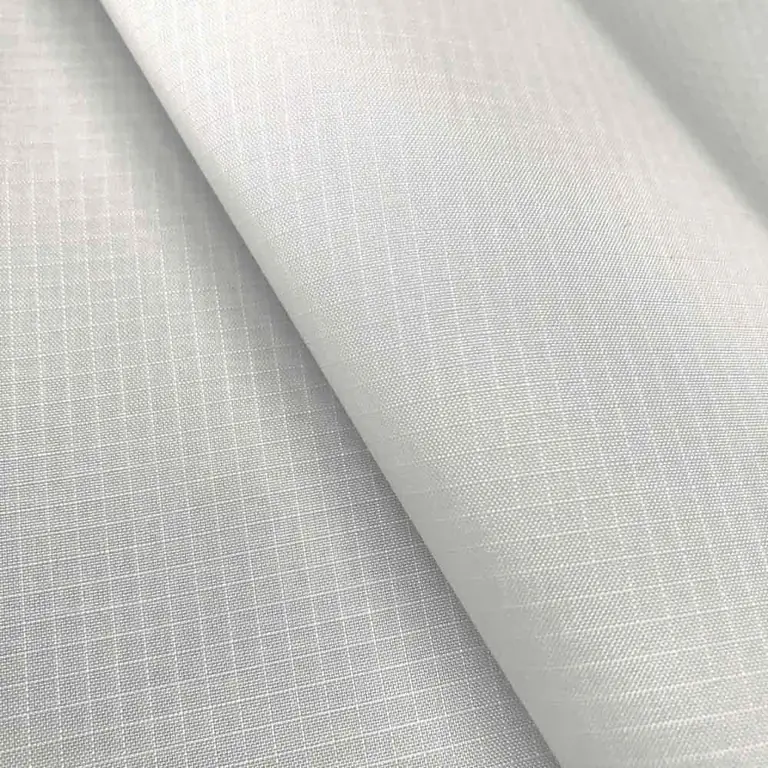
Rip-stop fabric - what is it? This is a high-strength material that has a combined weaving structure with reinforced yarn. It has many modifications. Rip-stop fabric is used for sewing all kinds of uniforms and things for recreation and sports, expeditions and hiking, fishing and hunting, overalls. Consider what composition it has, what properties it has
Electrolytic refining of copper: composition, formulas and reactions
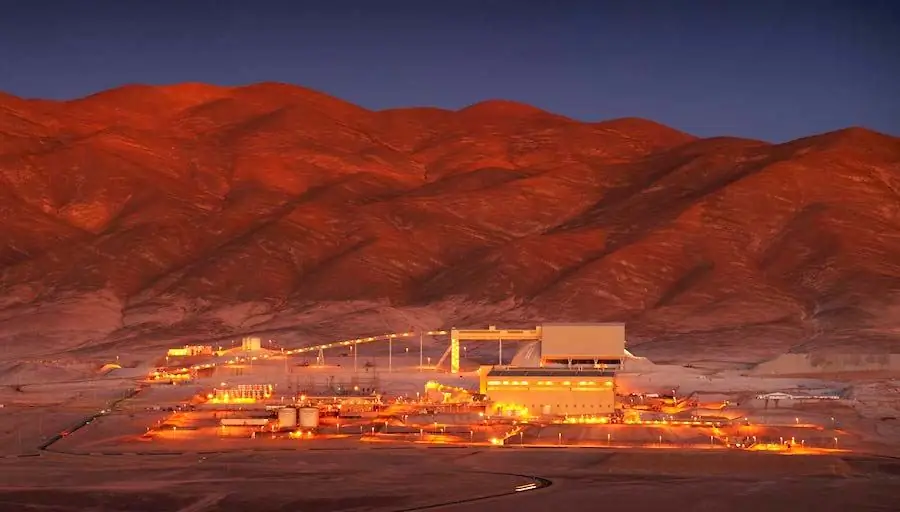
Copper is most commonly found in chalcopyrite and sulfide ores. Silicate, sulfate and carbonate ores also contain copper. Its low percentage in these ores makes it necessary to concentrate them prior to electrolysis. Methods used to concentrate copper ores include heating in a furnace or reacting them with sulfuric acid
Copper plate, foil, tape: production, characteristics, application
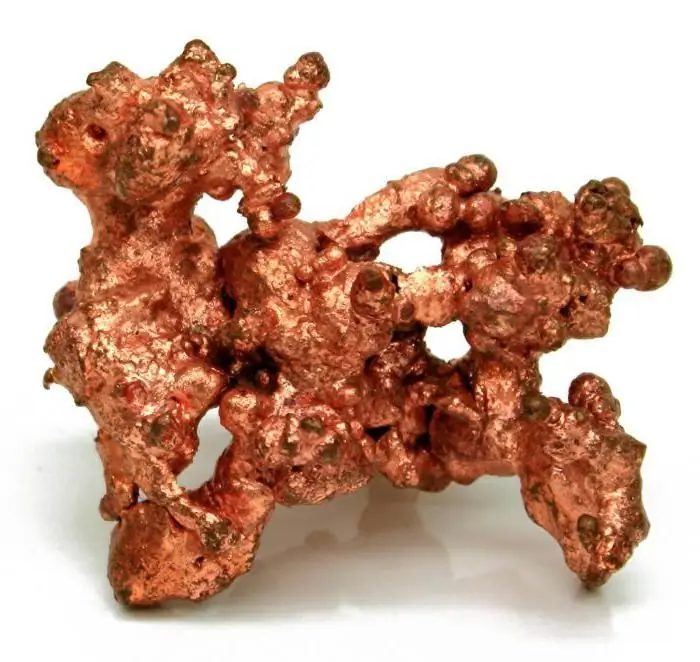
Copper is one of the most popular metals in the world today, it is used in many areas of production
Duralumin is a high-strength aluminum-based alloy with additions of copper, magnesium and manganese: properties, production and application
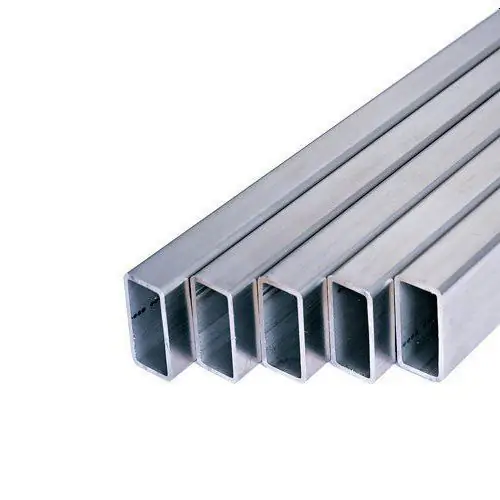
What is duralumin? What are the features of duralumin alloy? Technical and quality indicators of the alloy. A variety of products from this metal and their scope