2025 Author: Howard Calhoun | [email protected]. Last modified: 2025-01-24 13:10
Corrosion is the destruction of the surface of materials as a result of actively passing redox processes. The destruction of the layers of the material leads to a decrease in strength, electrical conductivity, increased brittleness and inhibition of other properties of the metal.
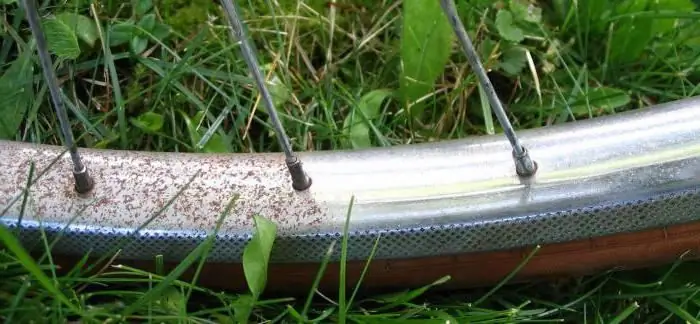
During the operation of metal products, they are exposed to various types of destructive effects, among which pitting corrosion stands out. She is the most dangerous and unpredictable.
Pitting
On the surface of metal products, you can often notice small depressions, dots of brown or brown color. Scientists call such points pitting, and the process of their appearance is called pitting corrosion. It occurs on the surface of materials that come into contact with sea water, solutions of various s alts, chemically aggressive environments and perceive other negative factors.
Pitting corrosion affects only passive metals and alloys, it develops mainly in the anti-corrosion layer or in places of various defects. "Point ulcers" can interfere with the work of variousproducts: from thin membranes and microcircuits to thick-walled aggregates. In addition, their appearance contributes to the formation of corrosion cracks, which significantly reduce the specified characteristics of the material.
Metal destruction scheme
To activate pitting corrosion, the presence of two reagents is necessary - activators and passivators. Anions of chlorine, bromine, iodine most often act as activators - they are found in most environments in which metal products are operated. They are adsorbed on the metal surface and form soluble complexes with its components.
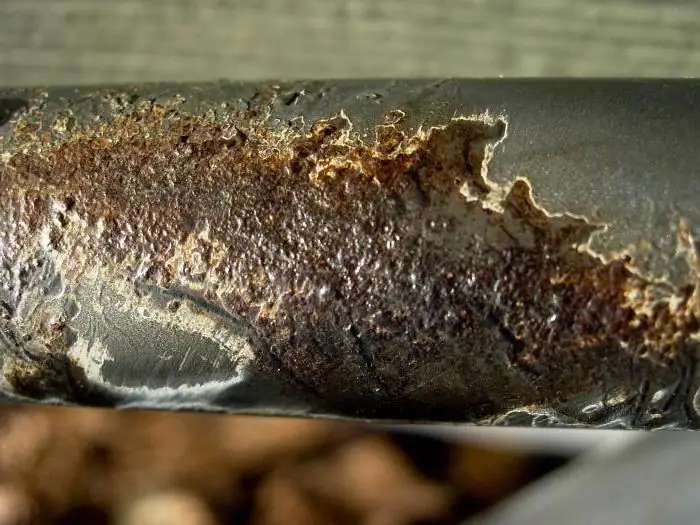
Water or a hydroxyl group most often acts as a passivator. The destruction process itself proceeds according to the following scheme:
- Activator ions are adsorbed on the surface of the protective (oxide) film.
- The process of replacing oxygen ions with process activator ions takes place.
- A large amount of soluble ions are formed, causing the film to break down.
As a result of this, a potential difference arises on the surface of the material, which leads to the appearance of local currents, and a violent anode process is activated. At the same time, activating ions move to the centers of destruction, due to which pitting corrosion progresses.
Varieties of pitting corrosion
The type of pitting corrosion varies depending on the environmental conditions, mainly temperature, acidity, chemical composition of substances. Under the influence of these factors, the shape changes,the size of the pits and their location. So, according to the size, point destruction is distinguished:
- microscopic - dot size less than 0.1 mm;
- regular - the diameter of the pits varies from 0.1 to 1 mm;
- ulcerative when formations exceed 1 mm in diameter.
Depending on the location, pitting corrosion can be open or closed. In the first case, it is almost impossible to detect traces of destruction - it is necessary to use special devices. This type of corrosion very often leads to breakdowns.
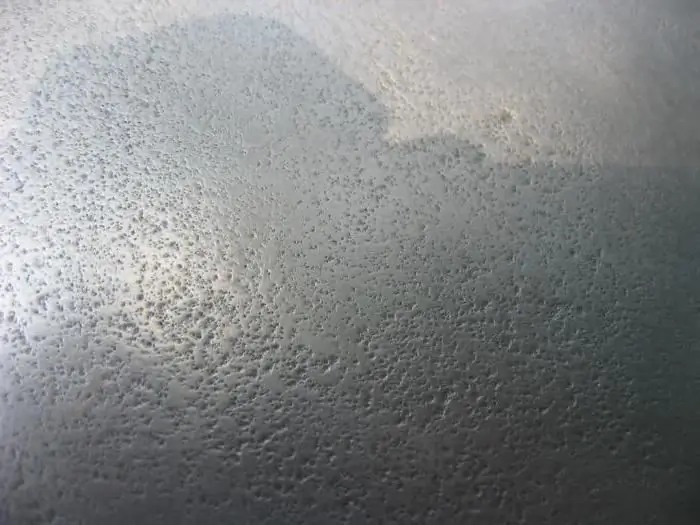
Exposed rust visible to the naked eye. Often pittings merge into a single formation. In this case, the destruction of the material does not occur in depth, but in width, which causes defects of large area.
Shape of pits
The shape of the pitting depends on the voids inside the crystal lattice, which are formed at the first stages of the corrosion process. The most common formations of irregular shape - they occur on the surface of stainless, low-alloy and carbon steels, aluminum, chromium, nickel alloys, iron.
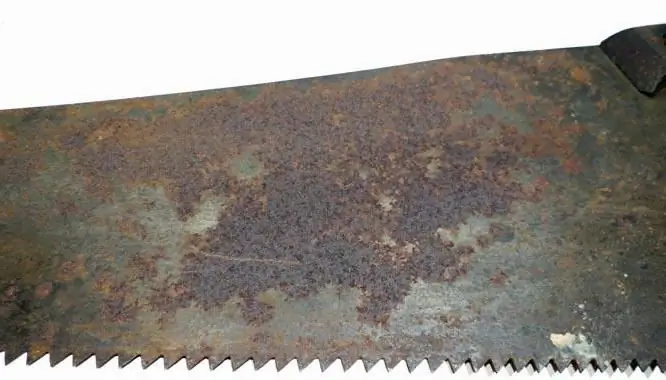
Hemispherical ulcers are formed as a result of isotropic dissolution. This process is similar to electropolishing. This partly explains the shiny bottom of the semicircular recesses. The most susceptible to such destruction are titanium, aluminum, nickel and cob alt products, as well as tantalum structures. Approximately the same appearancepitting corrosion of stainless steels.
In addition, pittings can be polyhedral and faceted. The "ulcers" of the latter type very often combine with each other, which leads to large hemispherical fractures.
Reasons for appearance
The main causes of pitting corrosion are violation of production technology and mechanical impact on the material. As a result of violation of the casting technology, various microinclusions appear in the metal, which violate its structure. The most common inclusion can be called mill scale.
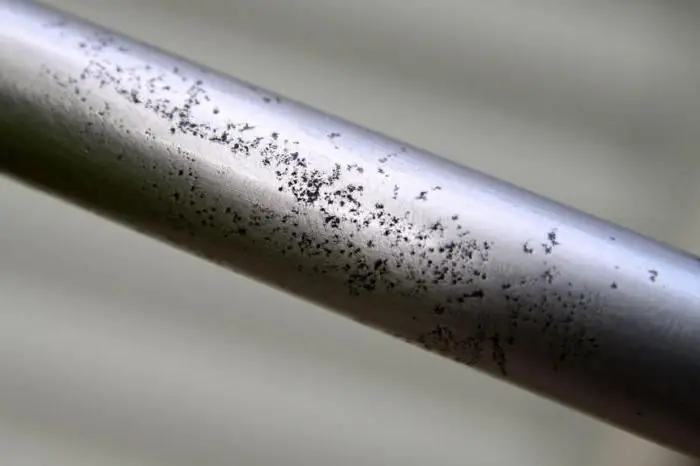
Due to mechanical impact, very often pitting corrosion begins to develop on the surface of products. The reasons for this lie in the destruction of the upper protective film, the violation of the internal structure, and the emergence of grain boundaries on the surface. The most common activating factor can be called a dynamic impact, which leads to the appearance of microcracks.
Pitting corrosion of metals develops faster on rough surfaces, as well as under the influence of aggressive environments - sea water, acid solutions.
Methods for protecting metal from pitting corrosion
To protect metal products from pitting corrosion, three main methods are used:
- Liquidation of closed systems using solutions of alkaline compounds, sulfates, chromates.
- Introduction into the composition of the material of components with high resistance to pitting rust - molybdenum,chromium, silicon.
- Using cathode and anode technology to create a protective layer.
All the presented methods of protecting metals from corrosion are applicable only in production, because they require high-tech equipment and large investments. In everyday life, it is impossible to completely eliminate the risk of pitting. It is only possible to weaken the influence of negatively acting factors through:
- anti-corrosion coatings;
- improving the operating conditions of products;
- reducing the level of acidity of the environment with which the material comes into contact.
But the most effective and affordable method is thorough polishing: by reducing the surface roughness, you simultaneously increase its anti-corrosion resistance. But for the best effect, it is better to use all methods of protecting metals from corrosion at the same time.
Recommended:
Corrosion of aluminum and its alloys. Methods for combating and protecting aluminum from corrosion
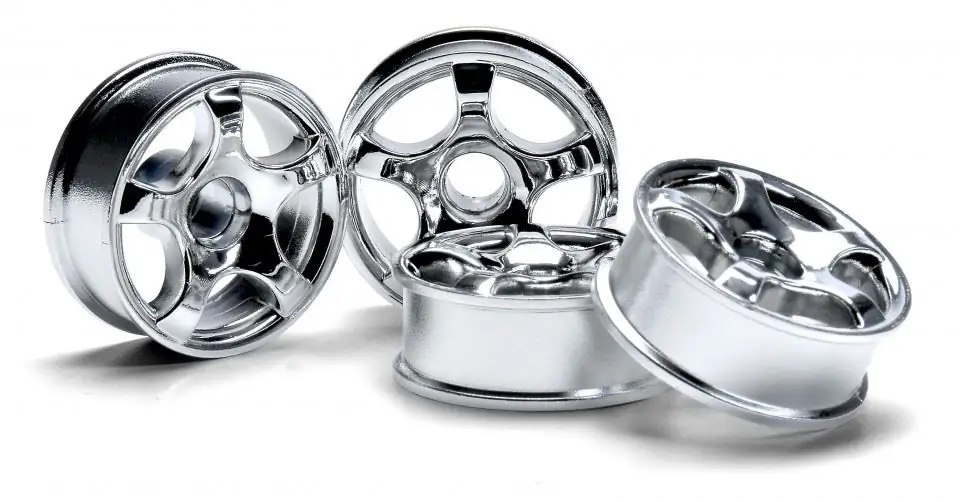
Aluminium, unlike iron and steel, is quite resistant to corrosion. This metal is protected from rust by a dense oxide film formed on its surface. However, in the case of destruction of the latter, the chemical activity of aluminum greatly increases
Corrosion inhibitors. Corrosion protection methods
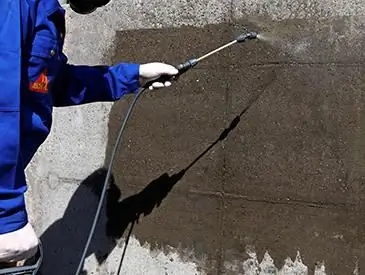
Each year, about a quarter of all the metal produced in the world is lost due to the development and occurrence of corrosion processes. The costs associated with the repair and replacement of equipment and communications of chemical industries are often many times higher than the cost of materials required for their manufacture
What is tinning? Methods for protecting metal from corrosion
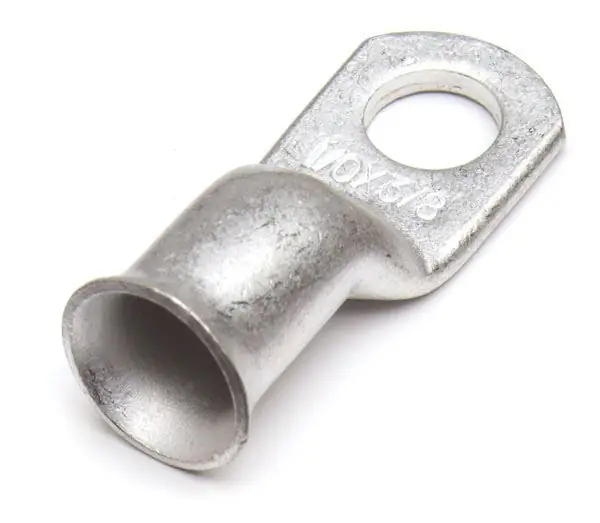
Tinning is widely used in industries such as aviation, radio engineering and electrical engineering. Products used for cooking and storing food are also subjected to this process. What is tinning, what is it used for and how this operation is carried out correctly, and we will consider in this article
Corrosion and erosion of metals: causes and methods of protection
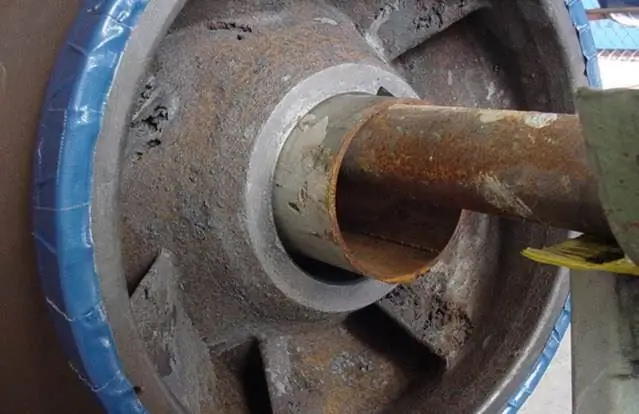
Chemical, mechanical and electrical external influences often occur in metal product operating environments. As a result, with improper maintenance of such elements, as well as ignoring safety standards, there may be risks of deformation and damage to structures and parts. This is due to the emerging processes of corrosion and erosion of metals, which in the long term contribute to the complete destruction of the structure of the product
Protection of the rights of the entrepreneur. Forms and methods of protecting the rights of entrepreneurs
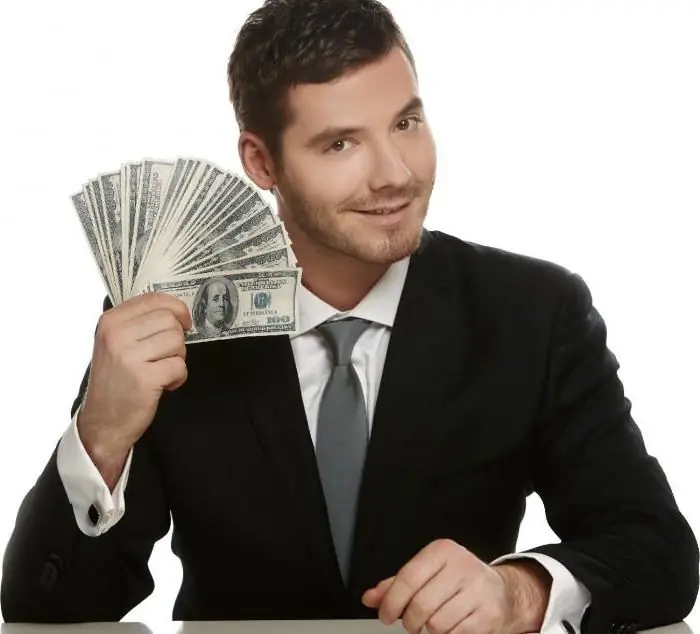
In our time, not all businessmen know how to protect the rights of an entrepreneur, but this is quite important information that can be repeatedly useful in the process of running their own business