2025 Author: Howard Calhoun | [email protected]. Last modified: 2025-01-24 13:10
Each year, about a quarter of all the metal produced in the world is lost due to the development and occurrence of corrosion processes. The costs associated with the repair and replacement of equipment and communications of chemical industries often exceed the cost of materials required for their manufacture by several times. Corrosion is called the spontaneous destruction of metals and various alloys under the influence of the environment. However, you can protect yourself from these processes. There are various ways to protect against corrosion, as well as types of exposure. In the chemical industry, the most common types of corrosion are gas, atmospheric and electrochemical.
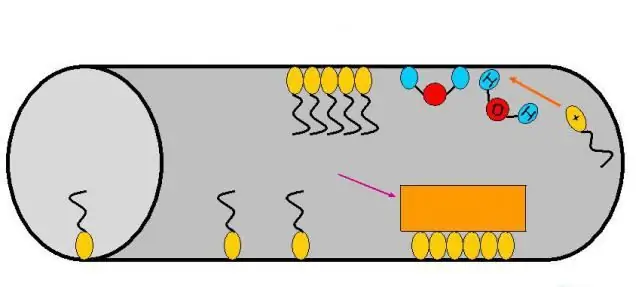
Out of the situation
The choice of a method of struggle in this case depends not only on the characteristics of the metal itself, but also on its operating conditions. Methods of protection against corrosion are selected in accordance with certain factors, however, even here a number of difficulties often arise. A particular problem is associated with the choice of an option for a multi-component environment withparameters that change during the process. This is quite common in the chemical industry. Corrosion protection methods used in practice are divided according to the nature of their impact on the environment and metal.
Environmental impact
Even in the Middle Ages, special substances became known, which were introduced in relatively small quantities, which made it possible to reduce the aggressiveness of the corrosive environment. For these purposes, it was customary to use oils, resins and starch. Over the past period, more and more new corrosion inhibitors have appeared. At the moment, only in Russia, you can count dozens of their manufacturers. Metal corrosion inhibitors are quite widespread due to their affordable cost. They are most effective in systems where there is a constant or low volume of corrosive environment, such as tanks, tanks, cooling systems, steam boilers and other chemical plants.
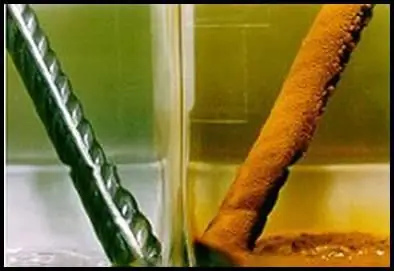
Properties
Corrosion inhibitors can be organic or inorganic in nature. They can protect against exposure to liquid media or gas exposure. Corrosion inhibitors in the oil industry in most cases are associated with inhibition of anodic and cathodic processes of electrochemical damage, the formation of passivating and protective films. You can consider the essence of this.
Anode corrosion inhibitors act on the basis of passivation of the anodic areas of the corroding metal surface, which was the reason for the appearance of the name passivators. As such, it is traditionaloxidizing agents of inorganic origin are used: nitrates, chromates and molybdates. They are easily reduced on cathode surfaces, which makes them similar to depolarizers, reducing the rate of anodic transition into a solution containing corrosive metal ions.
Anode moderators are also some compounds that are not characterized by the presence of oxidizing properties: polyphosphates, phosphates, sodium benzoate, silicates. Their action as inhibitors is manifested only in the presence of oxygen, which plays the role of a passivator. These substances lead to the adsorption of oxygen on metal surfaces. In addition, they cause inhibition of the anodic dissolution process due to the formation of protective films, which consist of hardly soluble products of the interaction of the inhibitor and metal ions passing into solution.
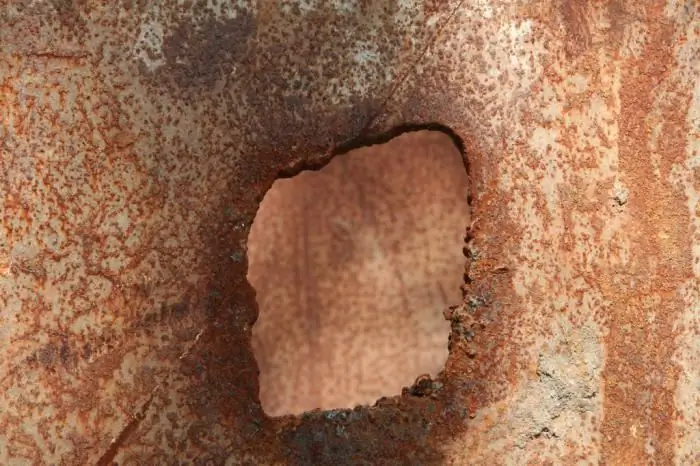
Features
Anode corrosion inhibitors of metals are usually classified as hazardous, because under certain conditions they turn from moderators into initiators of a destructive process. To avoid this, it is necessary that the density of the corrosion current be higher than that at which absolute passivation of the anode sections is formed. The concentration of the passivator should not fall below a certain value, otherwise passivation may not occur, or it will be incomplete. The latter option is fraught with great danger, because it causes a reduction in the anode surface, an increase in the depth and speed of metal destruction bysmall areas.
Requirements
It turns out that effective protection can be provided if the concentration of the anodic inhibitor is maintained above the maximum value in all areas of the product that is being protected. These substances are quite sensitive to the pH level of the medium. Chromates and nitrates are most commonly used in heat exchangers and to provide pipe surface protection.
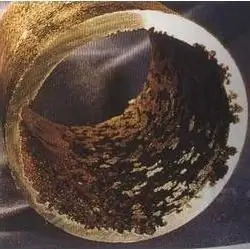
Cathode Inhibitors
In terms of protective action, these substances are less effective than anodic ones. Their action is based on the fact that local alkalization of the medium leads to the formation of insoluble products at the cathode sites, which isolate part of the surface from the solution. Such a substance can be, for example, calcium bicarbonate, which in an alkalized medium releases calcium carbonate in the form of a precipitate that is difficult to dissolve. The cathodic corrosion inhibitor, whose composition depends on the environment of use, does not lead to an increase in destructive processes even if the content is insufficient.
Varieties
In neutral media, inorganic substances often act as cathodic and anodic inhibitors, but in strongly acidic solutions they are not able to help. As moderators in the production of acids, organic substances are used, in which the molecules contain specific or polar groups, for example, amines, thiourea, aldehydes, carbonate s alts and phenols.
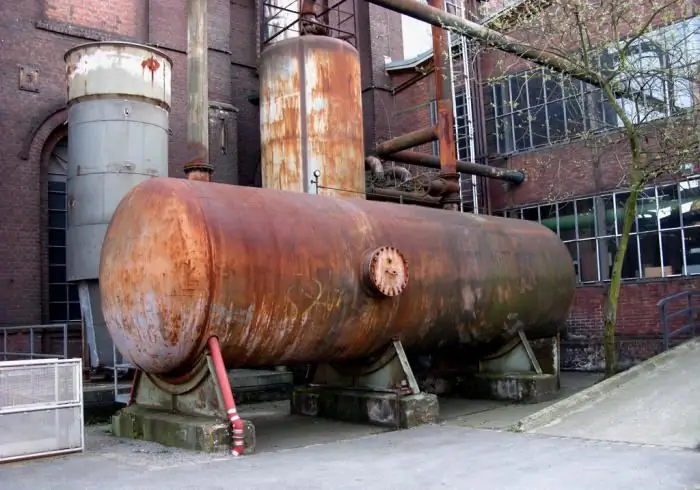
According to the mechanismThese corrosion inhibitors are distinguished by their adsorption character. After adsorption on the cathode or anode sites, they greatly hinder the discharge of hydrogen ions, as well as the metal ionization reaction. To a large extent, the protective effect is based on temperature, concentration, the type of acid anion, as well as the concentration of hydrogen ions. They are most often added in small quantities, because the protective effect of a number of organic inhibitors in high concentrations can even be dangerous.
For example, an organic compound called "Penta-522" is oil and water soluble. It is able to provide a degree of protection of more than 90% at a consumption of only 15-25 grams per ton. The corrosion inhibitor produced under the trademark "Amincor" is a product of esterification of carboxylic acids, which is non-volatile, does not have an unpleasant odor, and is non-toxic. Its dosage is determined only after establishing how corrosive the real environment is.
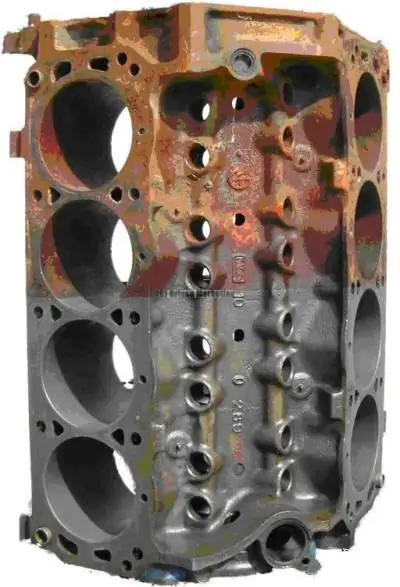
Impact on metal
This group of protection methods involves the use of a variety of coatings. These are paintwork, metal, rubber and other types. They are applied in different ways: spraying, galvanizing, gumming and others. You can consider each of them.
Gumming is commonly understood as corrosion protection through rubber coatings, which is often required in the chlorine industry. Rubber compounds have increased chemical resistance and provide reliable protection of containers, baths, as well as other chemical equipment from exposure toaggressive media and corrosion. Gumming is cold, as well as hot, which is carried out by the method of vulcanization of epoxy and fluoroplastic mixtures.
It is important not only to choose correctly, but also to apply a corrosion inhibitor. Manufacturers usually give fairly clear instructions about this. At the moment, in addition to galvanic deposition, the method of high-speed deposition has become quite widespread. With its help, a fairly wide range of tasks is solved. Powder materials can be applied to obtain coatings with various properties.
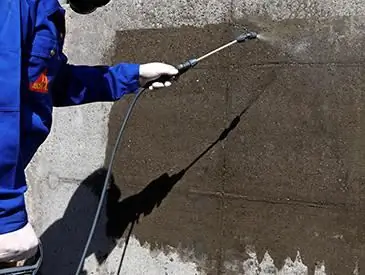
Protecting equipment
Issues related to the protection of chemical equipment are quite specific, and therefore require very careful study. The choice of material for obtaining a high-quality coating requires an analysis of the state of the surface, the composition of the environment, operating conditions, the degree of aggressiveness, temperature conditions, and so on. Sometimes, in “lower environments”, there is a critical parameter that makes it difficult to choose the type of coverage, for example, steaming even once every few months a propane tank. That is why each aggressive environment requires the selection of such a film former and such coating components that are characterized by resistance to the reagent.
Minority opinion
Specialists say that it is impossible to compare gas-thermal spraying methods with each other, and even more so to say that one of them is better than the other. Each of them has certain advantages and disadvantages, and the resultingcoatings have different properties, which indicates their ability to solve some of their tasks. The optimal composition by which corrosion inhibitors should be characterized, as well as the method of their application, are selected depending on the specific case.
At the enterprises of the chemical industry, this method is used most often in the process of current repairs. Even if acid corrosion inhibitors are used, the metal surface must first be properly prepared. This is the only way to guarantee a high-quality coverage. Blasting can be used prior to direct application of the paint material to ensure a sufficiently rough surface.
Every year more and more new developments appear on the market, and there is a considerable choice. However, chemists should decide what will be more profitable - to carry out timely protection of equipment or a complete replacement of all structures.
Recommended:
Tread protection against corrosion. The main ways to protect pipelines from corrosion
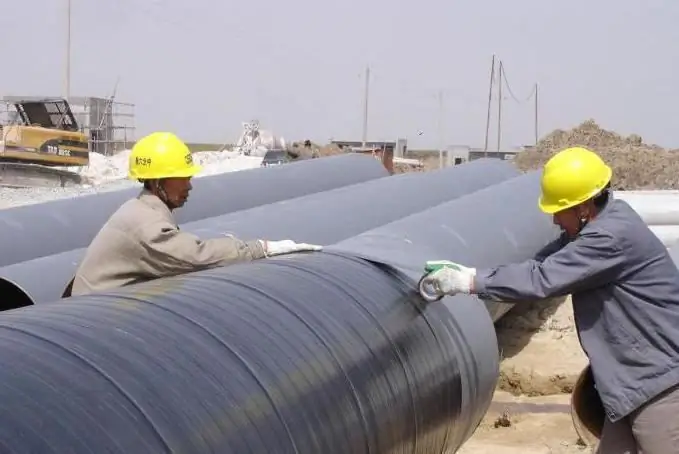
Protective corrosion protection is a universal solution when it is required to increase the resistance of metal surfaces to moisture and other external factors
Corrosion of aluminum and its alloys. Methods for combating and protecting aluminum from corrosion
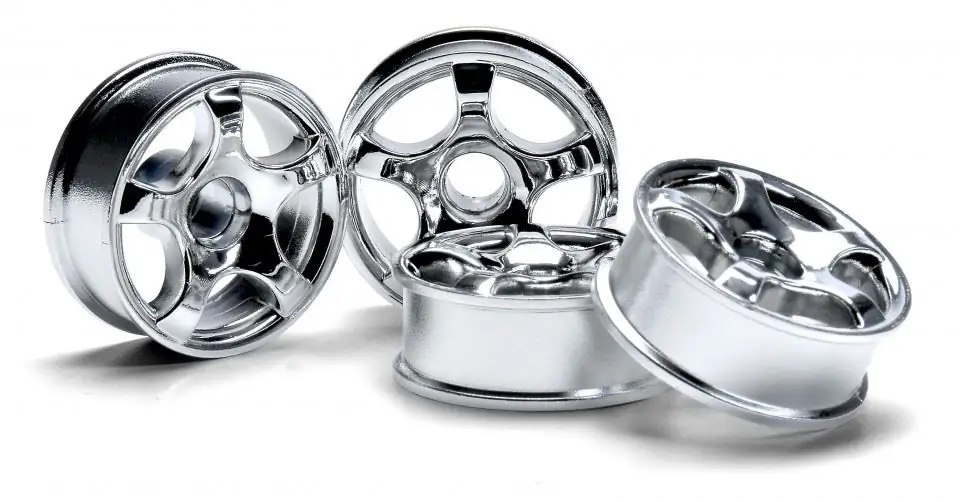
Aluminium, unlike iron and steel, is quite resistant to corrosion. This metal is protected from rust by a dense oxide film formed on its surface. However, in the case of destruction of the latter, the chemical activity of aluminum greatly increases
Pitting corrosion: causes. Methods for protecting metals from corrosion
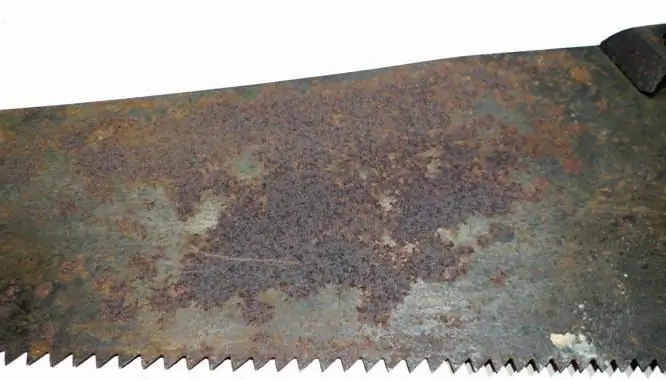
During the operation of metal products, they are exposed to various types of destructive effects, among which pitting corrosion stands out as the most dangerous and unpredictable
Corrosion and erosion of metals: causes and methods of protection
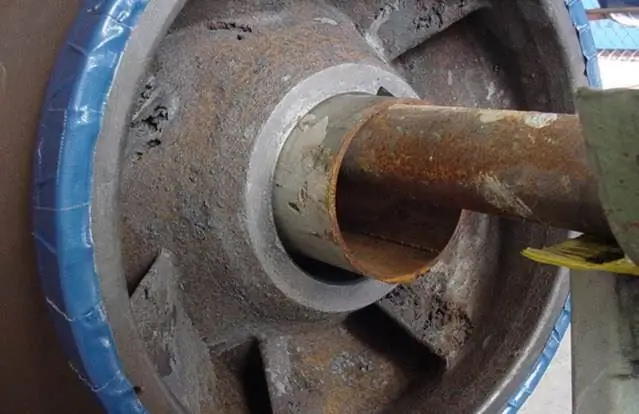
Chemical, mechanical and electrical external influences often occur in metal product operating environments. As a result, with improper maintenance of such elements, as well as ignoring safety standards, there may be risks of deformation and damage to structures and parts. This is due to the emerging processes of corrosion and erosion of metals, which in the long term contribute to the complete destruction of the structure of the product
Cataphoretic coating: description of the technology and its advantages. Corrosion protection methods
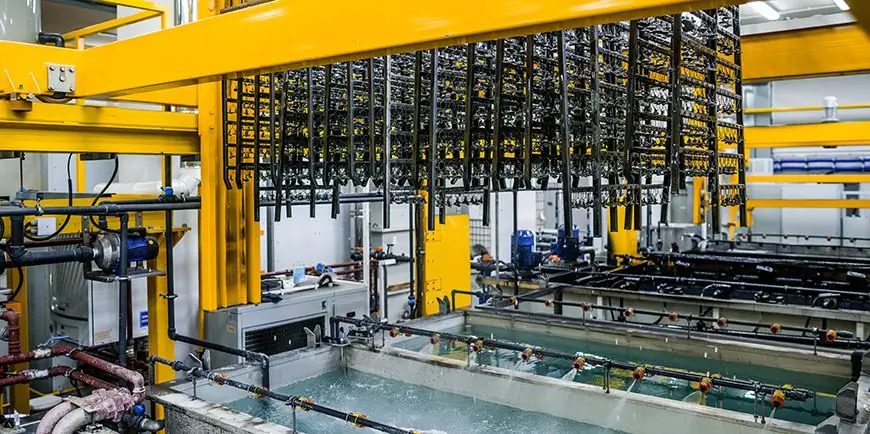
Techniques for applying external coatings represent the most extensive group of methods for the anti-corrosion protection of metal. Priming is often used in the protection of car bodies, which are subjected to various kinds of influences that contribute to the development of rust. One of the most effective methods of such protection is a cataphoretic coating, which simultaneously combines elements of physical and chemical insulation