2025 Author: Howard Calhoun | [email protected]. Last modified: 2025-01-24 13:10
These devices are especially in demand today in the national economy. An industrial robot, which bears little resemblance to its prototype in the book Rise of the Robots by K. Chapek, does not at all feed revolutionary ideas. On the contrary, he conscientiously performs, and with great accuracy, both the main production processes (assembly, welding, painting) and auxiliary ones (loading and unloading, fixing the product during manufacture, moving).
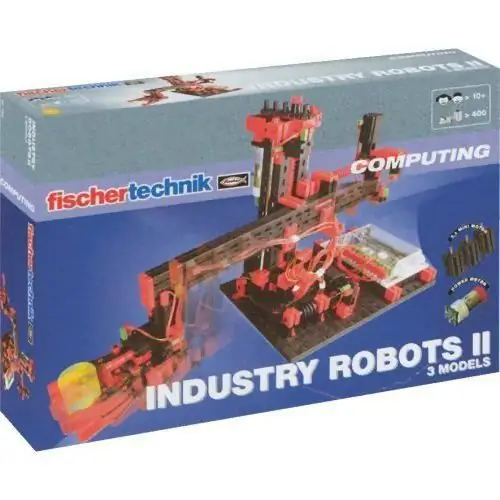
The use of such "smart" machines contributes to the effective solution of three major production problems:
- improving labor productivity;
- improve people's working conditions;
- optimize the use of human resources.
Industrial robots are the brainchild of large-scale production
Robots in production massively spread at the end of the 20th century due to a significant increase in industrial production. Large series of products have led to the need for the intensity and quality of such work, the performance of which exceeds the objective human capabilities. Instead of employing many thousands of skilled workers, modern technological factories operatenumerous high-performance automatic lines operating in intermittent or continuous cycles.
The leaders in the development of such technologies, declaring the widespread use of industrial robots, are Japan, the USA, Germany, Sweden and Switzerland. Modern industrial robots manufactured in the above countries are divided into two large groups. Their types are determined by belonging to two fundamentally different methods of management:
- automatic manipulators;
- devices remotely controlled by a human.
What are they used for?
The need for their creation began to be discussed at the beginning of the 20th century. However, at that time there was no element base for the implementation of the plan. Today, following the dictates of the times, robotic machines are used in most of the most technologically advanced industries.
Unfortunately, the re-equipment of entire industries with such "smart" machines is hampered by a lack of investment. Although the benefits of using them clearly exceed the initial monetary costs, because they allow us to talk not only and not so much about automation, but about profound changes in the sphere of production and labor.
The use of industrial robots has made it possible to more effectively perform work that is beyond human strength in terms of labor intensity and accuracy: loading / unloading, stacking, sorting, orientation of parts; moving blanks from one robot to another, and finished products to a warehouse; spot welding and seam welding; assembly of mechanical and electronic parts; cable laying; cuttingblanks along a complex contour.
Manipulator as part of an industrial robot
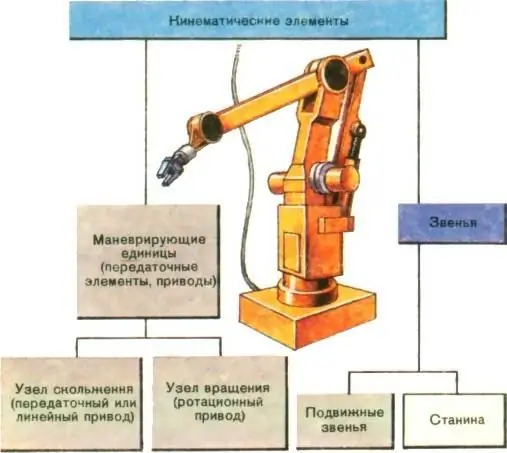
Functionally, such a “smart” machine consists of a reprogrammable ACS (automatic control system) and a working body (travel system and a mechanical manipulator). If the ACS is usually quite compact, visually hidden and does not immediately catch the eye, then the working body has such a characteristic appearance that an industrial robot is often called as follows: “robot-manipulator”.
By definition, a manipulator is a device that moves work surfaces and objects of labor in space. These devices consist of two types of links. The first provide a progressive movement. The second is angular displacement. Such standard links use either pneumatic or hydraulic (more powerful) drive for their movement.
The manipulator, created by analogy with the human hand, is equipped with a technological gripping device for working with parts. In various devices of this type, the direct grip was most often carried out by mechanical fingers. When working with flat surfaces, objects were captured using mechanical suction cups.
If the manipulator had to work simultaneously with many similar workpieces, then the capture was carried out thanks to a special extensive design.
Instead of a gripper, a manipulator is often equipped with mobile welding equipment, a special technological spray gun, or simplyscrewdriver.
How the robot moves
Automata-robots usually adapt to two types of movement in space (although some of them can be called stationary). It depends on the conditions of a particular production. If it is necessary to ensure movement on a smooth surface, then it is implemented using a directional monorail. If it is required to work at different levels, "walking" systems with pneumatic suction cups are used. A moving robot is perfectly oriented both in spatial and angular coordinates. Modern positioning devices of such devices are unified, they consist of technological blocks and allow for high-precision movement of workpieces weighing from 250 to 4000 kg.
Design
The use of the automated machines in question precisely in multidisciplinary industries led to a certain unification of their main constituent blocks. Modern industrial robotic manipulators have in their design:
- the frame used to fasten the part-grabbing device (grab) - a kind of "hand" that actually performs the processing;
- grab with a guide (the latter determines the position of the "hand" in space);
- support devices that drive, convert and transmit energy in the form of torque on the axis (thanks to them, the industrial robot receives the potential for movement);
- monitoring and management system for the implementation of the programs assigned to it; acceptance of new programs; analysis of information coming from sensors, and, accordingly,transferring it to providing devices;
- positioning system of the working part, measuring positions and movements along the axes of manipulation.
The dawn of industrial robots
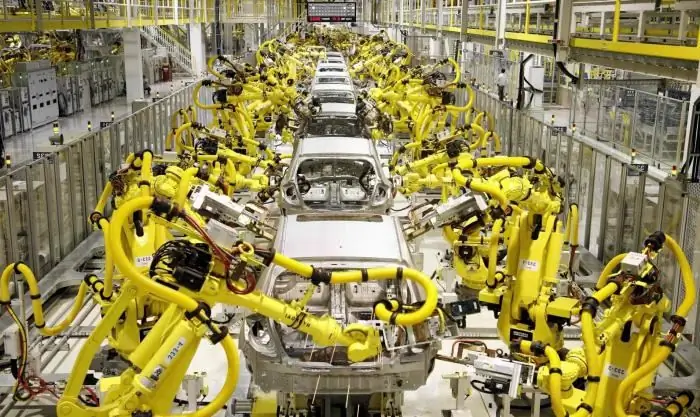
Let's go back to the recent past and remember how the history of the creation of industrial automatic machines began. The first robots appeared in the USA in 1962, and they were produced by Union Incorporated and Versatran. Although, to be precise, they nevertheless released the Unimate industrial robot, created by the American engineer D. Devol, who patented his own self-propelled guns programmed using punched cards. It was an obvious technical breakthrough: "smart" machines remembered the coordinates of the waypoints on their route and performed the work according to the program.
Unimate's first industrial robot was equipped with a pneumatically actuated two-finger gripper and a five degree of freedom hydraulically actuated arm. Its characteristics made it possible to move a 12 kg part with an accuracy of 1.25 mm.
Another Versatran robotic arm, made by the company of the same name, loaded and unloaded 1,200 bricks per hour into a kiln. He successfully replaced the work of people in an environment harmful to their he alth with a high temperature. The idea of its creation turned out to be very successful, and the design is so reliable that some machines of this brand continue to work in our time. And this despite the fact that their resource exceeded hundreds of thousands of hours.
Note that the first generation of industrial robots inin terms of value, it assumed 75% mechanics and 25% electronics. The readjustment of such devices required time and caused equipment downtime. To repurpose them to perform new work, the control program was replaced.
Second generation robot machines
It soon became clear: despite all the advantages, the machines of the first generation turned out to be imperfect … The second generation assumed more subtle control of industrial robots - adaptive. The very first devices required ordering the environment in which they worked. The latter circumstance often meant high additional costs. This was becoming critical for the development of mass production.
The new stage of progress was characterized by the development of many sensors. With their help, the robot received a quality called "feeling". He began to receive information about the external environment and, in accordance with it, choose the best course of action. For example, he acquired skills that allow him to take a part and bypass an obstacle with it. This action occurs due to the microprocessor processing of the received information, which further, entered into the variables of the control programs, is actually guided by the robots.
Types of basic production operations (welding, painting, assembly, various kinds of machining) are also subject to adaptation. That is, when performing each of them, multivariance is initiated to improve the quality of any kind of the above works.
Industrial manipulators are mainly controlled by software. Control hardwarefunctions are industrial mini-computers PC/104 or MicroPC. Note that adaptive control is based on multivariant software. Moreover, the decision on the choice of the type of program operation is made by the robot based on information about the environment described by the detectors.
A characteristic feature of the functioning of the second generation robot is the preliminary presence of established modes of operation, each of which is activated at certain indicators obtained from the external environment.
The third generation of robots
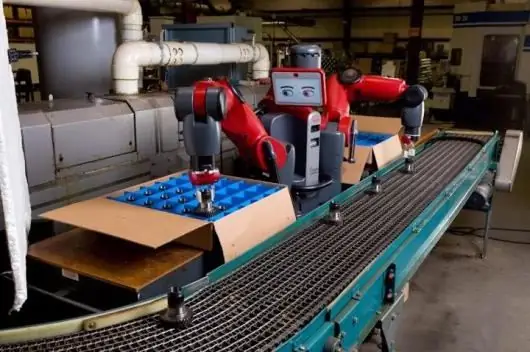
Automatic robots of the third generation are able to independently generate a program of their actions, depending on the task and the circumstances of the external environment. They do not have “cheat sheets”, i.e., painted technological actions for certain variants of the external environment. They have the ability to independently optimally build the algorithm of their work, as well as quickly implement it in practice. The cost of the electronics of such an industrial robot is ten times higher than its mechanical part.
The newest robot, capturing a part thanks to sensors, “knows” how well it did it. In addition, the gripping force itself (force feedback) is regulated depending on the fragility of the material of the part. Perhaps that is why the device of industrial robots of the new generation is called intelligent.
As you understand, the “brain” of such a device is its control system. The most promising is the regulation carried out according to the methods of artificialintelligence.
Intelligence for these machines is given by application software packages, programmable logic controllers, modeling tools. In production, industrial robots are networked, providing the proper level of interaction between the "man - machine" system. Also, tools have been developed to predict the functioning of such devices in the future thanks to the implemented software simulation, which allows you to choose the best options for action and network connection configurations.
The world's leading robot companies
Today, the use of industrial robots is provided by leading companies, including Japanese (Fanuc, Kawasaki, Motoman, OTC Daihen, Panasonic), American (KC Robots, Triton Manufacturing, Kaman Corporation), German (Kuka).
What are these firms famous for in the world? Fanuc's assets include the fastest delta robot M-1iA to date (such machines are usually used for packaging), the strongest of the serial robots - M-2000iA, ArcMate welding robots recognized worldwide.
Industrial robots manufactured by Kuka are no less in demand. These machines carry out processing, welding, assembly, packaging, palletizing, loading with German precision.
Also impressive is the product range of the Japanese-American company Motoman (Yaskawa), operating in the US market: 175 models of industrial robots, as well as more than 40 integrated solutions. Industrial robots used in production in the United States are mostly made by this industry-leadingcompany.
Most of the other firms we represent fill their niche by manufacturing a narrower range of specialized instruments. For example, Daihen and Panasonic produce welding robots.
Methods of organizing automated production
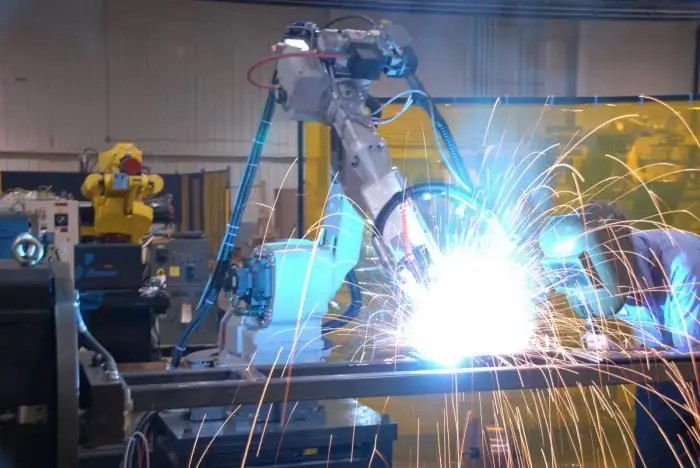
If we talk about the organization of automated production, then at first a rigid linear principle was implemented. However, at a sufficiently high speed of the production cycle, it has a significant drawback - downtime due to failures. As an alternative, rotary technology was invented. With such an organization of production, both the workpiece and the automated line itself (robots) move in a circle. Machines in this case can duplicate functions, and failures are practically excluded. However, in this case, speed is lost. The ideal process organization is a hybrid of the above two. It is called rotary conveyor.
Industrial robot as an element of flexible automatic production
Modern "smart" devices are quickly reconfigured, highly productive and independently perform work using their equipment, processing materials and workpieces. Depending on the specifics of use, they can function both within the framework of one program, and by varying their work, i.e., choosing the right one from a fixed number of provided programs.
Industrial robot is a constituent element of flexible automated production (generally accepted abbreviation - GAP). Lastalso includes:
- computer-aided design system;
- complex of automated control of technological equipment of production;
- industrial robotic arms;
- Automatic production transport;
- loading/unloading and placement devices;
- manufacturing process control systems;
- automatic production control.
More about the practice of using robots
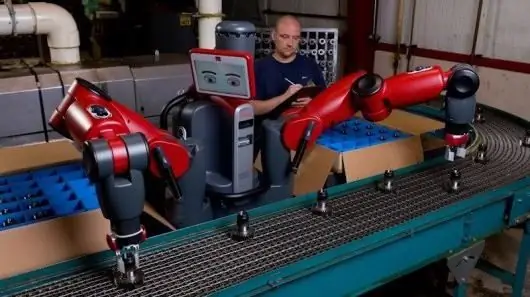
Real industrial applications are modern robots. Their types are different, and they provide high productivity in strategically important areas of industry. In particular, the modern German economy owes much of its growing potential to their application. In what industries do these "iron workers" work? In metalworking, they function in almost all processes: casting, welding, forging, providing the highest level of work quality.
As an industry with extreme conditions for human labor (meaning high temperatures and pollution), casting is largely robotized. Machines from Kuka are assembled even in foundries.
The food industry also received equipment for production purposes from Kuka. "Food robots" (photos are presented in the article) for the most part replace people in areas with special conditions. Widespread in the production of machines that provide a microclimate in heated rooms withtemperature not exceeding 30 degrees Celsius. Stainless steel robots masterfully process meat, participate in the production of dairy products, and, of course, stack and pack products in an optimal way.
It is difficult to overestimate the contribution of such devices to the automotive industry. According to experts, the most powerful and productive machines today are precisely the "Cook" robots. Photos of such devices that carry out the entire range of auto assembly operations are impressive. At the same time, it is really time to talk about automated production.
Processing of plastics, production of plastic, manufacturing of the most complex parts from various materials is provided by robots in production in a polluted environment that is really harmful to human he alth.
Another important area of application for "Cook" aggregates is woodworking. Moreover, the described devices provide both the fulfillment of individual orders and the establishment of large-scale mass production at all stages - from primary processing and sawing to milling, drilling, grinding.
Prices
Currently, robots manufactured by Kuka and Fanuc are in demand in the Russian and CIS markets. Their prices range from 25,000 to 800,000 rubles. Such an impressive difference is explained by the existence of various models: standard low-capacity (5-15 kg), special (solving special tasks), specialized (working in a non-standard environment), large-capacity (up to 4000 tons).
Conclusions
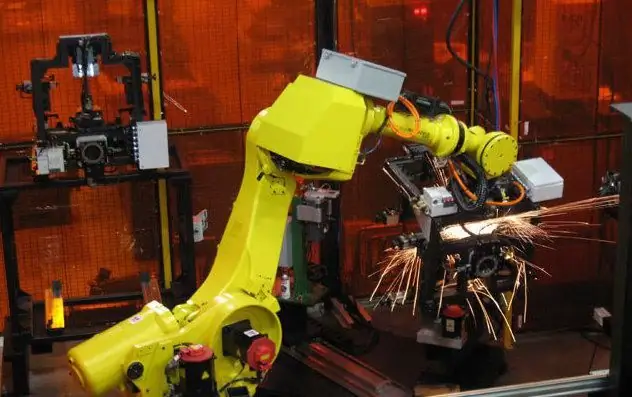
It has to be acknowledged that the potential of industrial robots is still not fully exploited. At the same time, thanks to the efforts of specialists, modern technologies make it possible to implement ever more daring ideas.
The need to increase the productivity of the world economy and maximize the share of intellectual human labor serve as powerful incentives for the development of more and more new types and modifications of industrial robots.
Recommended:
Modern production. The structure of modern production. Problems of modern production

Developed industry and a high level of the country's economy are key factors influencing the we alth and well-being of its population. Such a state has great economic opportunities and potential. A significant component of the economy of many countries is the production
Gas production. Gas production methods. Gas production in Russia
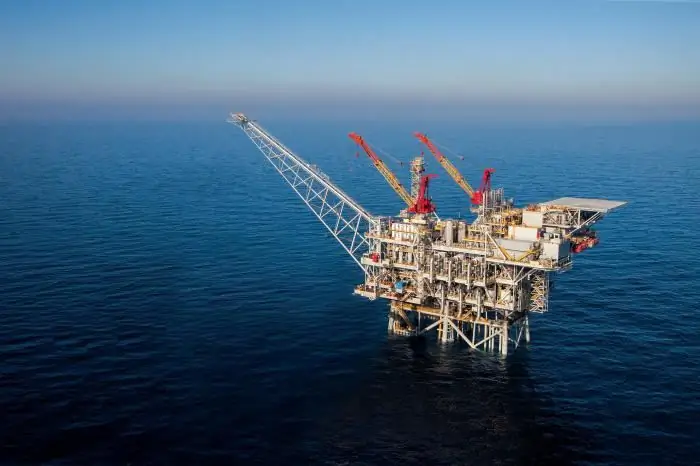
Natural gas is formed by mixing various gases in the earth's crust. In most cases, the depth of occurrence ranges from several hundred meters to a couple of kilometers. It is worth noting that gas can form at high temperatures and pressures. In this case, there is no access of oxygen to the place. To date, gas production has been implemented in several ways, each of which we will consider in this article. But let's talk about everything in order
German binary robot: reviews. How to remove German binary robot?
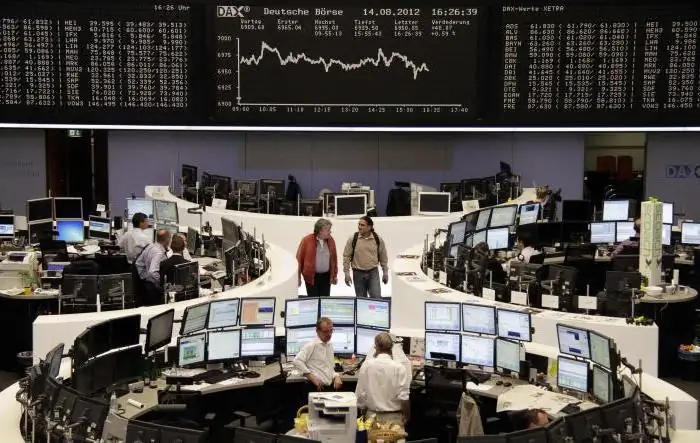
An article about an ad-supported browser extension - about a German binary robot. Feedback on how to remove the German binary robot
Industrial boilers: description, types, functions. Industrial expertise of boilers
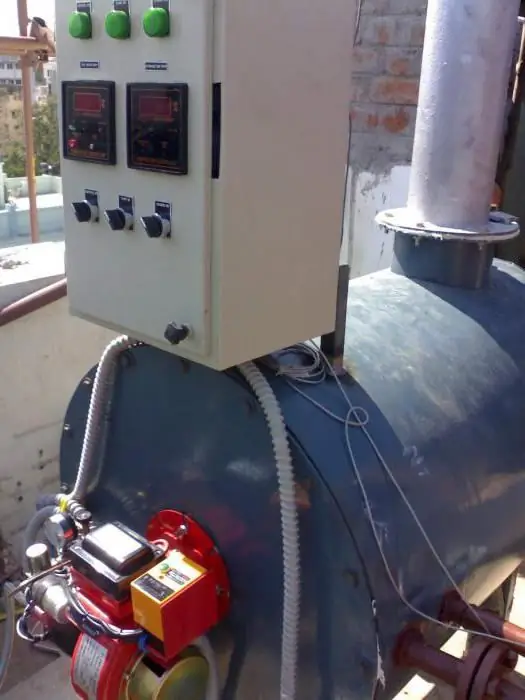
The article is devoted to industrial boilers. The varieties of such units, functions and nuances of the examination for the safety of equipment are considered
Industrial safety of hazardous industrial facilities: rules and requirements
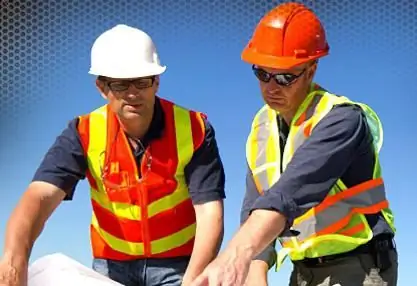
In modern production, unfortunately, there are accidents. However, there are special instructions, the observance of which helps to prevent disasters. Consider further the basic rules of industrial safety