2025 Author: Howard Calhoun | [email protected]. Last modified: 2025-01-24 13:10
Product cost is an important economic indicator. It is valued by every company. This allows you to determine the amount of costs that were determined by the enterprise in a certain period. The production cost deserves special attention. How this indicator is calculated and analyzed will be discussed below.
Definition
Full and production costs are the most important indicators that characterize the activities of the organization. They allow you to determine the profitability, as well as draw conclusions about the correctness of management decisions. The cost price is the costs that are formed at the enterprise in the course of its activities.
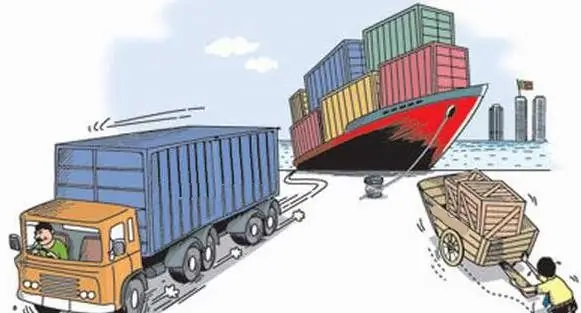
Each organization is engaged in the production of goods or the provision of services. In the course of its production activities, it spends certain resources. It can be raw materials, energy, labor of workers andetc. They are called production costs. These are all costs that are determined during the production of finished products from the moment raw materials enter the technological cycle and the final result is obtained.
Each company is interested in cost reduction. However, this process must be reasonable. As the cost decreases, the quality of the goods may decrease. The product obtained during the technological cycle must satisfy the requirements of buyers. Otherwise, they simply won't buy it. In this case, the company suffers losses, since it is not possible to achieve the desired amount of profit from the sale.
Today, when calculating the costs that a company has incurred in the course of its activities, such concepts as the total and production costs of products are used. They have several differences. The production cost reflects the costs that were caused directly by the production process. They are formed from the beginning of the technological cycle to the shipment of finished products to the warehouse. The full cost price also takes into account the costs that will be additionally incurred during the sale. In this case, the costs of packaging, advertising and transportation of products are added to the production cost.
Structure
To determine the production cost, you need to know its structure. Expenses are formed into separate groups according to certain criteria. The first category includes material costs. For a manufacturing enterprise, this is one of the largest cost groups.
Material costs include raw materials from whichfinished products are produced, as well as materials that are necessary for organizing the release. They are completely processed in the process of one technological cycle, changing their original form.
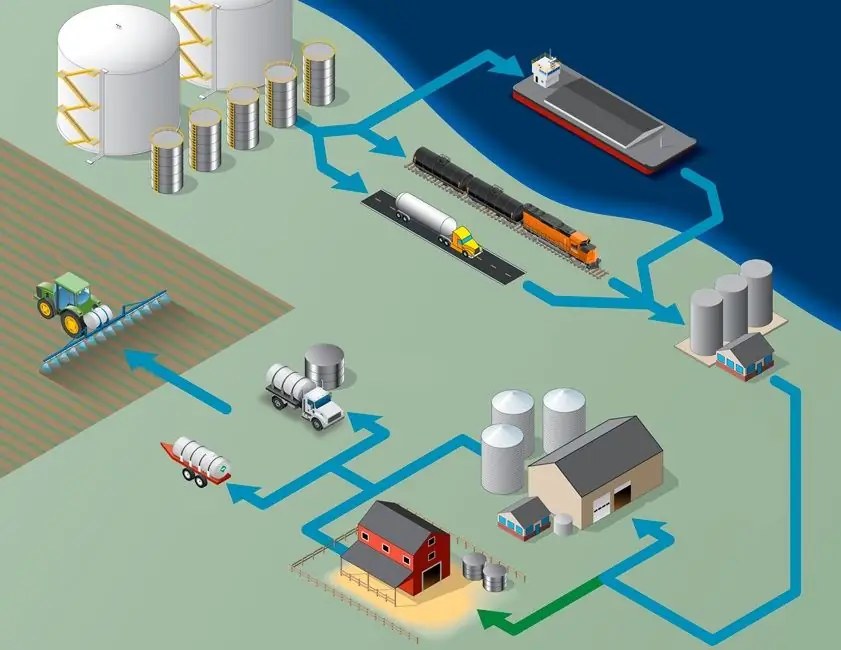
Also, material costs include energy costs. It can be electricity, gas and other similar resources. Another component of the production cost of the material group are consumables (for example, lubricants, fuel, etc.) and others.
The second group of production costs includes labor costs. They are divided according to the category of employees of the company. Separately, the costs of wages for the main staff, specialists, employees of auxiliary departments, employees, junior staff are taken into account. This group of costs also includes contributions to insurance funds.
The third group of costs are the costs associated with the wear and tear of technological equipment. These are depreciation charges, which are also included in the cost price. These funds go to a special fund and are consumed when the equipment is significantly worn out. These funds are used to purchase new machines, units and other components of equipment.
There are also other costs. They are determined by the characteristics of the company's activities.
When is the calculation done?
The need to calculate the cost of production of a manufacturing enterprise may arise for various reasons. This procedure is carried out by any commercial organization, regardless of the scale of itsactivities. During analytical, economic studies of the performance of the enterprise, the calculation of the cost is carried out.
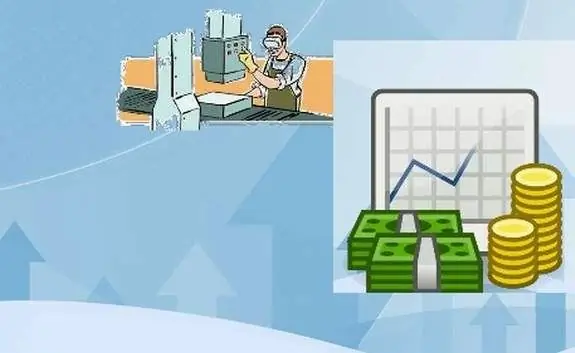
Often the need for such work arises in the process of finding reserves to reduce costs. This allows you to increase the profitability of production, the efficiency of the enterprise. Also, the cost is calculated in the process of pricing policy formation.
Similar work is also performed in the process of studying the effectiveness of management decisions and the company's production activities. This becomes especially relevant when new equipment is introduced into the technological cycle, after expanding the product range.
In the planning process, the cost calculation is also carried out. At the same time, it is possible to track the dynamics of changes in product prices and take timely actions to improve it.
The production cost of finished products is calculated during cost accounting, as well as in the process of studying the profitability of the organization's production activities. When analyzing profit, as well as the factors that influenced it in the reporting period, similar studies are also carried out.
Factors affecting the cost of production
Costs and production costs can vary greatly from organization to organization. Therefore, when calculating and analyzing, they compare the indicators in dynamics for several periods, as well as between similar competing enterprises in a particular industry.
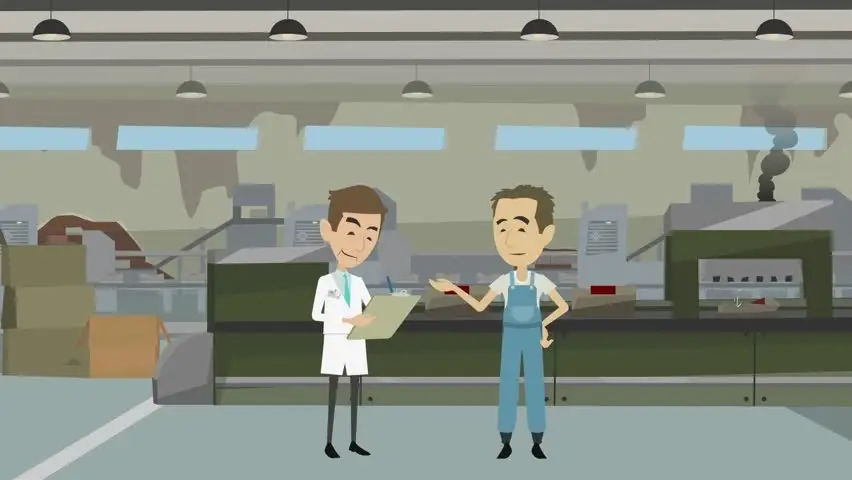
Certain factors can influence the cost price. This must be taken into account during the analysis of this indicator. First of all, the cost price is affected by the number of products manufactured by the enterprise. At the same time, the cost of a unit of finished products is taken into account both at retail and wholesale prices.
The indicator is affected by the number of stages that the production includes. Comparison of the cost price is made at the same point of the technological cycle. Therefore, you can only compare products of the same type, which are characterized by the same properties.
The cost indicator is affected by the amount of costs incurred during the production cycle. Also, this indicator is influenced by the method of analytical evaluation. Standard, planned and actual production costs can differ significantly.
At the same time, the price can be formed within one workshop, as well as within the entire production. In the second case, the general and target costs of the enterprise are added to the workshop costs incurred during the production of products. Therefore, at each level, the cost is considered separately.
Normative, process-by-process methodology
The actual manufacturing cost of a product can be calculated in many ways. This allows you to evaluate the indicator as efficiently as possible. Today, 4 costing methods are used. This is a normative, ostentatious, step-by-step and process-by-process approach. They have a number of differences.
Normative methodologyinvolves carrying out the calculation procedure in a certain sequence. First, the selling price of each unit of the group of goods is calculated. Then, the level of fluctuations that was recorded in the study period relative to production standards is taken into account.
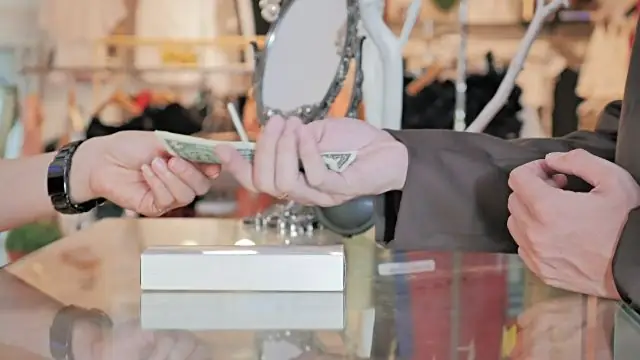
The next step is to determine the level of costs incurred during this time. This takes into account the established norms and deviations from them. This allows you to determine the causes of such discrepancies. After that, the calculation of the initial cost of production is carried out.
Actual production cost is suitable for enterprises that produce large batches of products in a short time. First, the company calculates all the costs that were incurred by it during the technological cycle. Next, the resulting figure is divided by the number of units of manufactured products. This allows you to determine the cost of one product.
To facilitate the control procedure, the calculation is carried out at different stages of production. This allows you to avoid mistakes. Negative factors can be identified directly at the stage of their occurrence.
Peredelnaya, ostentatious technique
The production cost of products can be calculated using the cross-cutting methodology. This approach is used by enterprises with different scales of production. These are representatives of such industries as agriculture, industry.
In the calculation process, the calculation of costs incurred during the execution of one order is carried out. After that, the result is divided either by the number of batches or by the number of homogeneous products.
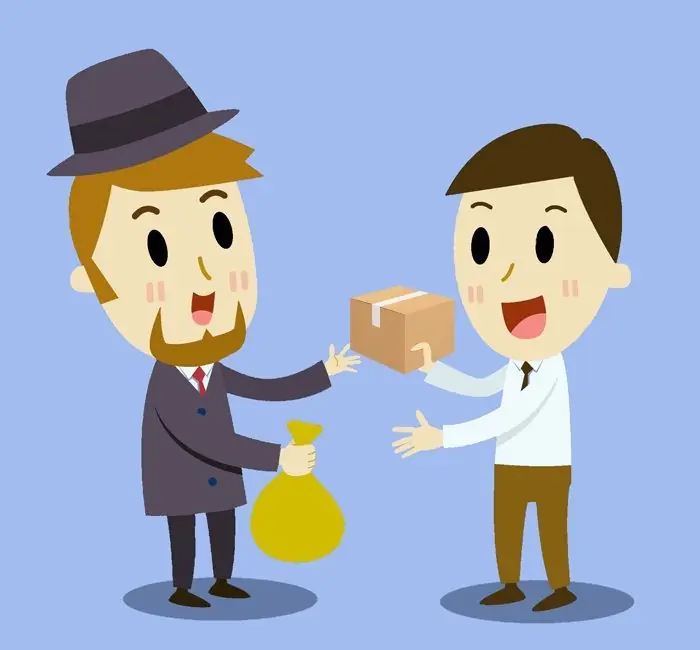
Show method is suitable for many enterprises to calculate the cost of production. First, all direct costs that have arisen in the course of the company's production activities are calculated. They are calculated for each individual order. Next, the amount of a unit of production for each batch of the same type of goods is determined. To do this, the total amount of all costs is divided by the number of finished products in the context of each specific order.
In this case, the production cost of production can be grouped according to different criteria. At the place of occurrence, costs can be production, shop, determined at sites or other structural divisions. Grouping can also be done by cost carriers. In this case, the cost price is calculated separately for each homogeneous type of goods.
By types of costing, costs can be taken into account according to economic indicators. This allows you to determine what factors influenced the increase in cost over time.
Calculation
Production cost of goods sold is calculated using a simple formula. To do this, you need to sum up all the costs that arose in the process of manufacturing products. In a simplified form, the formula looks like this:
PS=MZ + ZP + A + PR, where PS - production cost, MZ - material costs, ZP - staff wages; A - depreciation deductions; OL - other expenses.
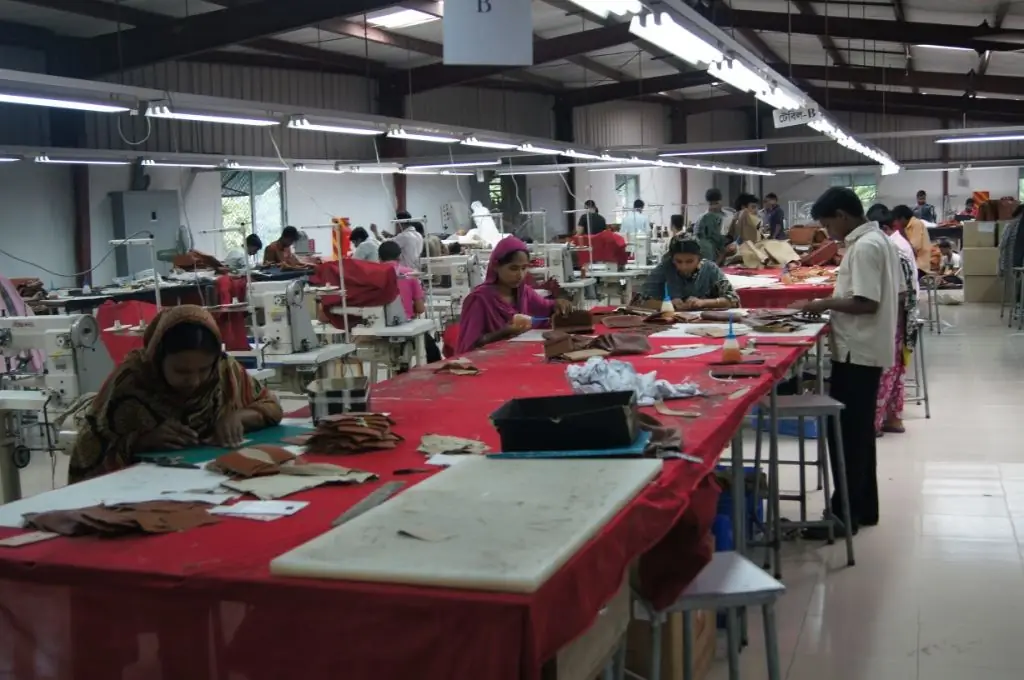
Other expenses may include general production and general industry costs, targeted financing. However, this is a very general formula. It may include other articles that are determined in the course of the production activities of the organization. Each item of expenditure is considered in dynamics. This allows you to determine what factors influenced the formation of the cost.
Each indicator that is used in the calculation is estimated as a percentage of the total cost. The structure is influenced by the industry affiliation of the organization, other internal and external factors. This does not allow you to stick to the same cost level in different periods of time.
Example
To calculate the cost of production, we need to consider an example of this process. To do this, you need to take into account a number of data that are determined by the results of the company's production activities. For example, a company accounted for the following costs last month;
- raw materials and materials - 50 thousand rubles;
- remains of production resources - 0.9 thousand rubles;
- components, semi-finished products - 3 thousand rubles;
- energy, fuel - 6 thousand rubles;
- salary - 45 thousand rubles;
- prizes - 8 thousand rubles;
- Deductions to the Pension Fund - 13.78 thousand rubles;
- services of tool shops - 3, 3 thousand rubles;
- general production costs - 13.55 thousand rubles;
- general business expenses - 17.6 thousand rubles;
- fatalmarriage - 0.94 thousand rubles;
- shortages - 0.92 thousand rubles. (within the normal range) and 2.15 thousand rubles. (over the norm);
- work in progress - 24.6 thousand rubles.
First, material costs are determined: 50 - 0.9=49.1 thousand rubles. To the amount received, you need to add the cost of energy, semi-finished products: 49.1 + 3 + 6=58.1 thousand rubles.
Next, labor costs are determined: 45 + 8 + 13, 78 + 58, 1=124.88 thousand rubles. When the total amount is set, you need to add general production, general business costs to it: 3, 3 + 13, 55 + 17, 6 + 124, 88=159, 33 thousand rubles.
Shortage, which was established within the normal range, must be subtracted from the excess. The result obtained is added to the total amount: 2.15 - 0.92 + 159.33=160.56 thousand rubles.
Since the company has work in progress, it must be subtracted from the total cost for this period. This indicator will be taken into account in the next period: 160.56 - 24.6=135.96 thousand rubles. This is the sum of the production cost.
Unit cost analysis
Production cost of products requires proper analysis. This allows you to highlight existing problems and prevent their occurrence in the future. In the course of the analysis, an assessment of the unit cost of production is carried out. To do this, the indicator in monetary terms is divided by the number of goods produced. The calculation is carried out in wholesale prices.
The indicator is compared with the planned indicators. If there are deviations, determine the cause of such a phenomenon.
Alsoan assessment of the amount of costs by their types is carried out. Their structure is also analyzed. If any article has unreasonably increased, measures are taken to eliminate such a negative phenomenon. Further, the indicators are evaluated in dynamics. They are compared over several periods. At the same time, absolute (in thousand rubles) and relative deviation (in percent) are found. This allows you to set the growth rate.
The structure is also compared with the planned one. If there are deviations, the cause is determined, ways are found to solve such problems. The analysis is carried out once a year, quarter or monthly. The frequency is chosen in accordance with the peculiarity of the company's activities and its environment.
Methodological techniques
Production cost requires control by the governing bodies of the company. For this, different methods are used. Diagnostics and analysis are carried out in the context of a unit of production.
The selection of the best option for the release of certain products is being carried out, taking into account the needs of the market. It is also necessary to evaluate the cost effectiveness. To do this, they calculate how much profit falls on each ruble spent.
Each product group is compared to the previous year. Further, their cost is compared with the planned indicator. At the same time, the level of profitability of production is taken into account. Further, each group of products is evaluated in the context of costing items. This allows you to identify opportunities to improve the competitiveness of products.
To perform an analysis, examine the costing report data. Here is information about the costs in general for productiona certain type of product, as well as its individual parts, components. It is necessary to take into account the data that will be obtained in other areas of production. This will allow us to identify negative factors that are common to production and hinder its development.
Having considered the features of the production cost, you can calculate it and make an analysis regarding the result. This work is necessary to reduce costs and increase the competitiveness of finished products.
Recommended:
Fundamental market analysis. Technical and fundamental analysis
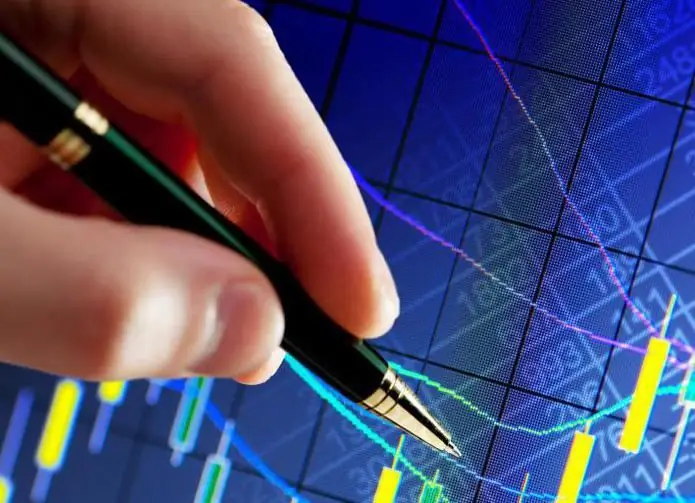
Fundamental analysis is a set of methods that allow predicting events in the market or in its segments under the influence of external factors and events
Analysis of the situation: options, features, stages and results of the analysis
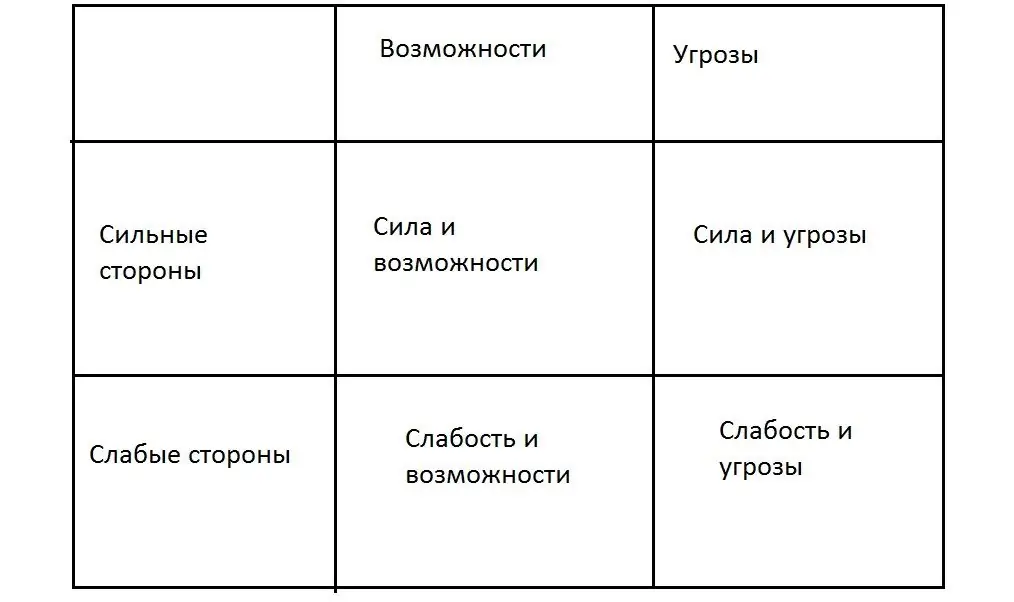
What is situation analysis? Who and when conducts it, the main stages of the analysis and assessment of the situation. Methods and tools used in the analysis of the situation. Why should it be carried out? What is the importance of the analysis of the situation for the work of the enterprise?
How the cost of a service is calculated: an example of a calculation. Service cost
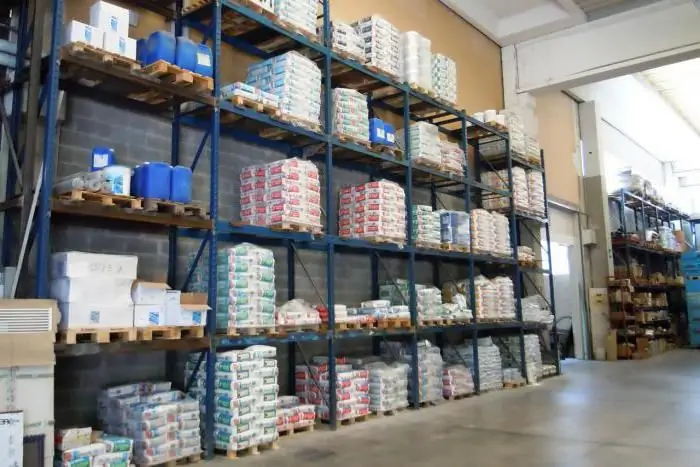
Description of the technology for compiling the cost calculation and listing the constituent data for the calculation. An example of calculating the cost of some public services
Analysis of the break-even of the enterprise. Break-even analysis of production
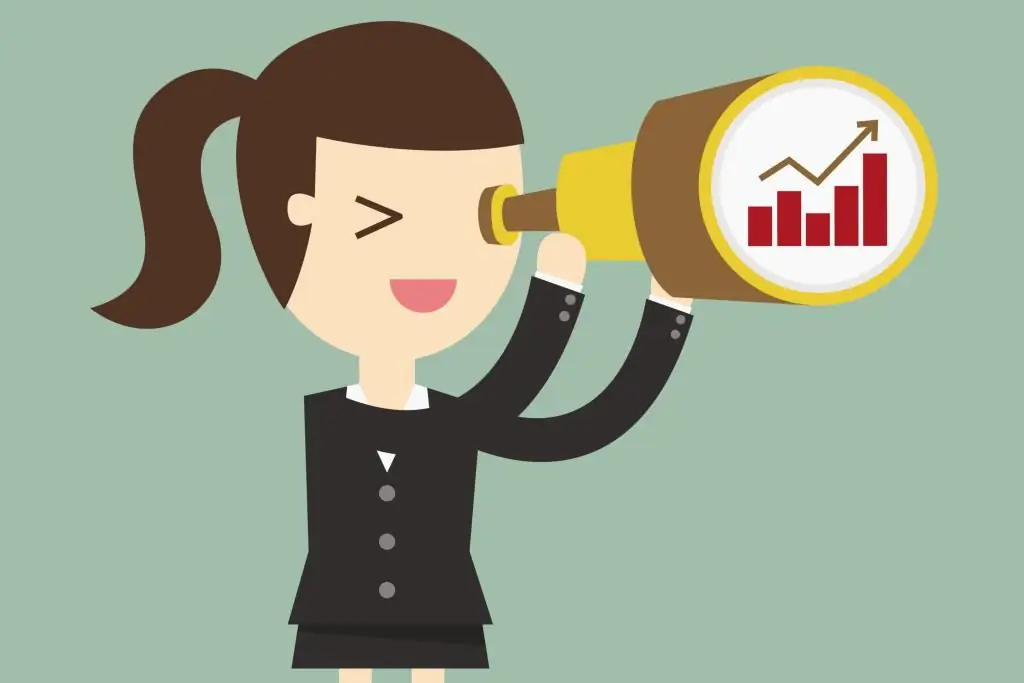
A break-even analysis is a process by which a business can decide how much to produce and sell finished products. This allows you to determine when you can cover an expense item
WACC is a measure of the cost of capital. Cost of Capital WACC: Examples and Calculation Formula
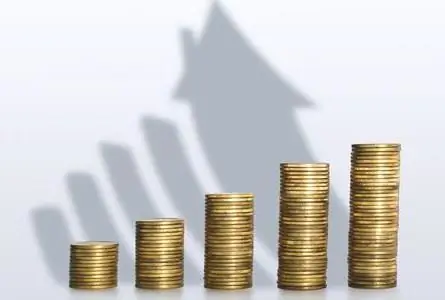
In the modern economic system, the property of any company has its own value. The control of this indicator is important for the choice of the organization's action strategy. WACC is a measure of the cost of capital. The formula of the indicator, as well as examples of its calculation will be presented in the article