2025 Author: Howard Calhoun | [email protected]. Last modified: 2025-01-24 13:10
In industry and in everyday life, metal parts are connected into a single structure by welding. This method is considered the most reliable and fairly cheap. Relatively not very complex equipment (welding machine, electrodes, protective equipment) makes it possible to create and repair many metal structures in a short time and with sufficiently reliable quality.
To create a durable metal product, a novice welder needs to thoroughly know the features and types of butt welds, as well as the technology of the work performed.
Weld joint definition
Welding of metals is their connection by melting the edges of the product and their subsequent crystallization during the cooling process. The welding process is accompanied by complex physical and chemical processes. These numerous factors must be taken into account by the welder during the performance of the work. Moreover, all these physical and chemical processes are interconnected in time and space.
During welding, there are several specific zones that characterize the welded joint:
- the place of fusion (weld pool), where there are molten grains of metal and electrode on the border of the base metal and the weld;
- weld formed after cooling and solidification of the weld pool;
- The heat-affected zone is defined by a piece of metal that has not melted, but has changed its composition and structure as a result of heating;
- base metal that can be welded without changing its properties.
Types of welded joints
Classify the connection of two metal parts according to their relative position relative to each other. The type of connection during welding is chosen by the welder, taking into account the characteristic features of the metal and the ability to achieve a high-quality result.
Depending on the placement of products in space, the connections are divided into the following types:
- butt joint;
- corner joint;
- T-bond;
- lap joint;
- end view.
Butt Fusion
The most common type of welding is the butt joint. With such welding, the two parts to be joined are located in the same plane, so the surface of one element is a continuation of the other.
Elements during butt welding are adjacent to each other end surfaces. The ends of the edges to be welded can be with or without a bevel. Moreover, without a bevel, the welding seam of metal sheets up to 4 mm thick is obtained with the highest quality. Double sided butt weldwithout beveling the ends of the metal allows you to achieve a good result with a thickness of parts up to 8 mm. To improve the quality of the connection, it is necessary to make a gap of up to two millimeters between the plates.
One-sided welding of parts with a thickness of 4 to 25 millimeters, it is desirable to perform with a preliminary bevel of the edges. The most popular among welders is the V-shaped bevel of the end surface. Sheets with a thickness of 12 mm or more are recommended to be welded in a double-sided X-cut.
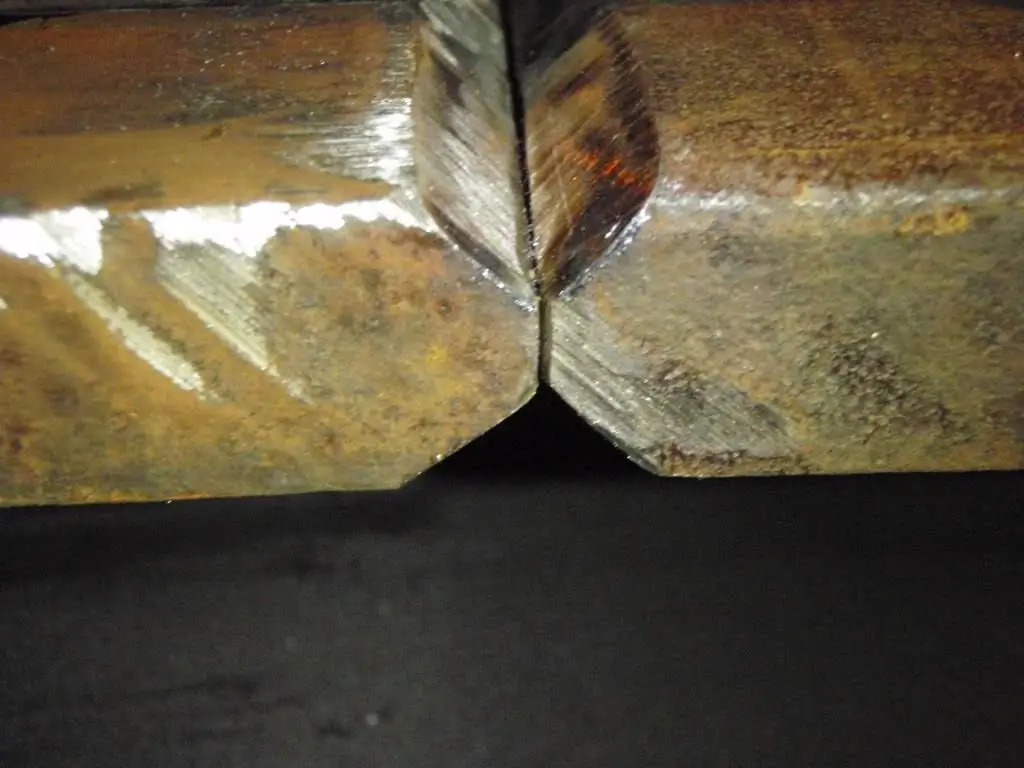
Classification by seam position
The quality of the weld depends on the position of the product in space. There are four main ways to make a butt joint of welds:
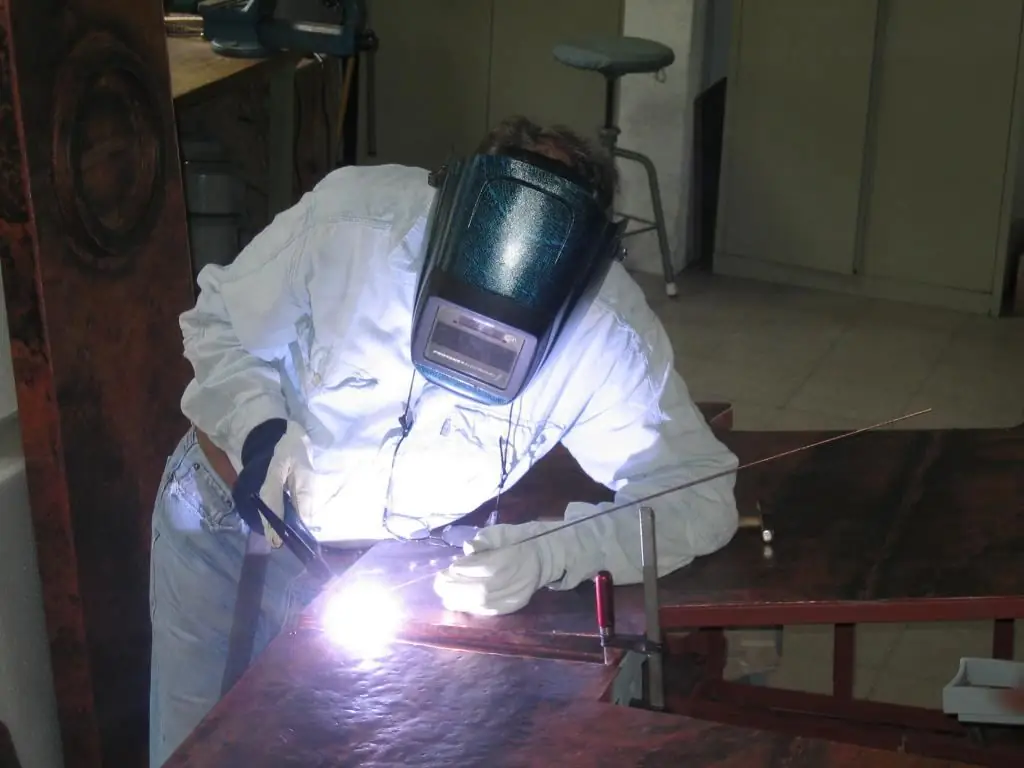
- The bottom connection method is used when the welder is located on top of the workpiece surfaces to be welded. This method is the most convenient, since the molten metal does not flow down or along the sides, but falls directly into the crater. In this case, slag and gas are removed from the weld pool without obstacles and freely exit to the surface.
- Horizontal seams are made on vertically arranged plates, while the electrode is guided from left to right or from right to left. The high-quality execution of a horizontal seam consists in strict control over the molten metal, preventing it from flowing down, therefore it is necessary to correctly select the electrode movement speed and current strength.
- Vertical method applied on partslocated vertically, while the seam of the butt joint is carried out from top to bottom or vice versa. The difficulty of such welding is that the molten metal flows down, thus violating the appearance and quality of the connection. Typically, welders try to avoid working in this position. Only experienced craftsmen resort to this method, relying on their theoretical and practical knowledge.
- With the overhead method, the parts to be welded are above the welder's head. When applying this method, you must strictly follow the technological process and safety rules, as the molten metal drips down.
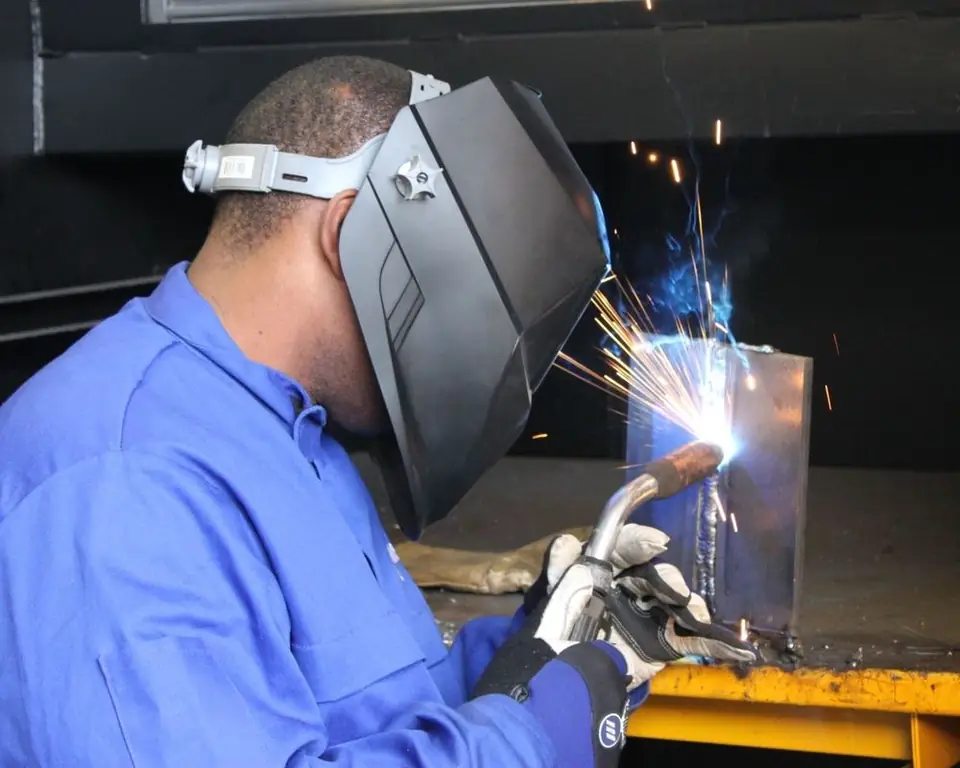
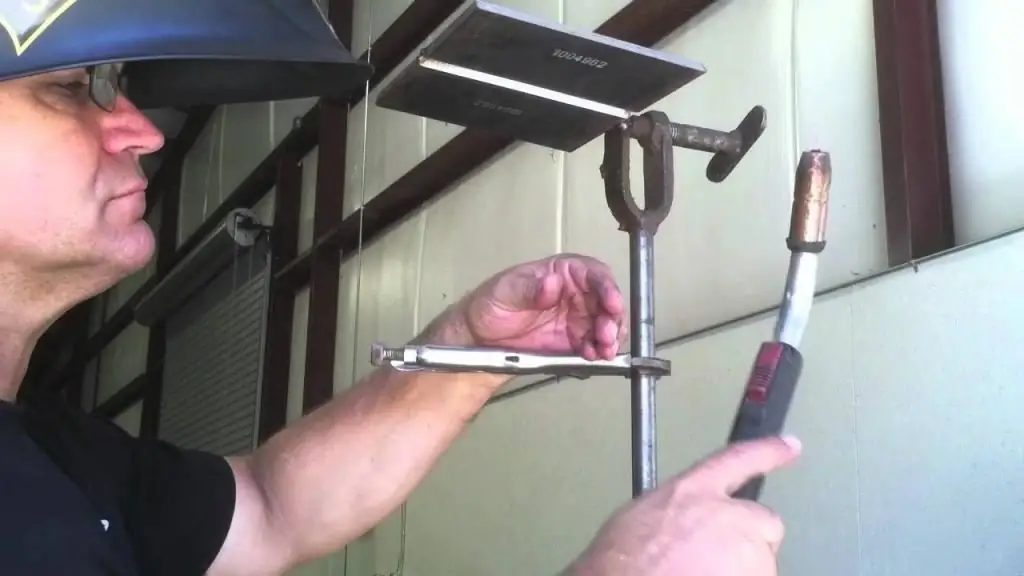
Organization of seams by type of welding
Butt joints can be classified according to the type of impact of welding equipment. It is the use of appropriate devices and devices that makes it possible to obtain the following types of seams:
- Manual electric arc welding promotes the creation of a weld using a special electrode and allows you to obtain reliable fastening of metal parts with a thickness of 0.1 to 100 mm.
- Arc welding using an inert gas allows you to get strong and aesthetic seams, since all welding processes take place under the protection of a gas cloud.
- Auto welding performs butt welding of metal in the inverter independent operation mode, here the welder controls the process after setting up the equipment.
- When gas welding, the formation of a weld occursdue to the high temperature of the burning gas mixture.
- With a soldering iron it is possible to create brazed seams.
Weld profile
If you cut the butt joint, it is easy to determine the nature of the seam by its appearance:
- The concave weld is weakened, therefore it is mainly used for welding thin elements, for structures with a small dynamic load.
- Convex seams are considered reinforced, therefore they are widely used in structures with a large static load, the creation of such a seam requires an increased consumption of electrodes.
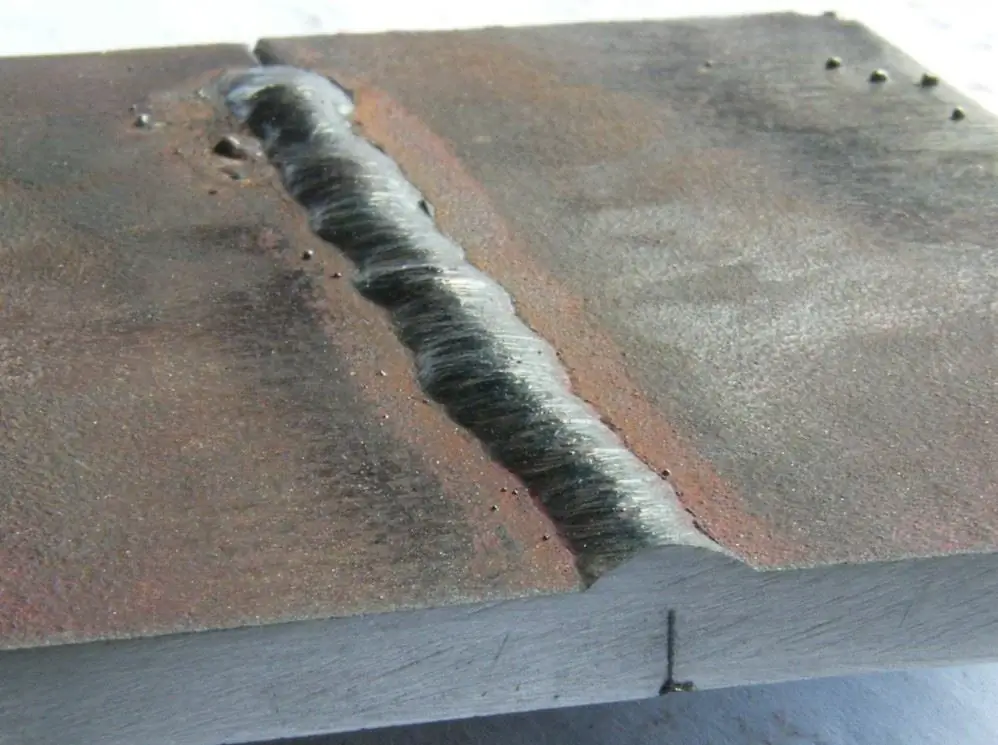
Normal welds are used for dynamic loads, in which case there is not much difference between the base metal and the height of the weld
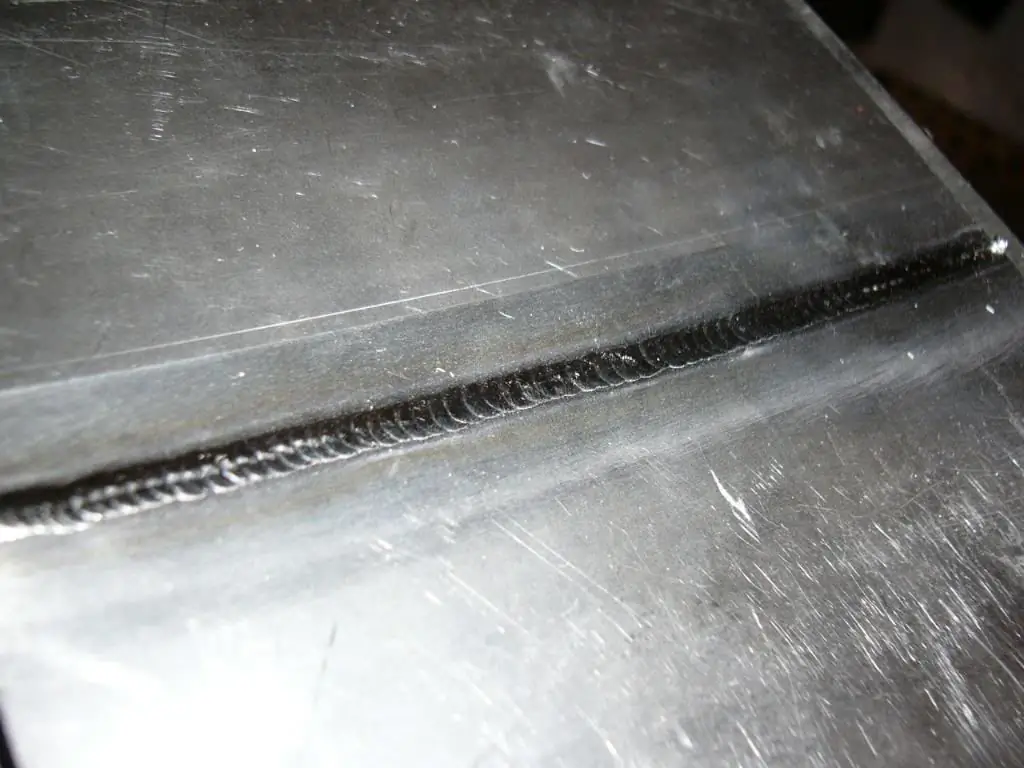
Types of seams by length
Another significant factor in obtaining a quality connection of two metals is the length of the weld. The calculation of butt joints takes into account the type and length of the weld.
By length, joints are classified as continuous or intermittent:
- Solid welds do not have gaps free from welding along the entire length of the connection of two metal surfaces. This type of welding allows you to get the most high-quality and durable connection of any structures. The disadvantage of continuous electrode guidance is a large consumption of material and slow work.
- Intermittent wayit is used in the case when it is not required to create a particularly strong connection. Such seams are most often made of a certain length with a strict synchronous interval. Intermittent welding can be staggered or chain track.
Welding Safety Precautions
The welding process is accompanied by a number of factors that can affect the safety of human he alth. The main damaging factors are considered to be the presence of radiation that affects the eyesight, the detrimental effect of the emitted gas, as well as the effect of molten metal.
Therefore, at all modern enterprises, special attention is paid to the protective clothing of the welder:
- canvas suit;
- boots or boots with closed laces;
- welder mask or goggles;
- respirator protecting respiratory organs;
- canvas mittens.
All items must be clean, free of oily liquid stains.
For a beginner welder to acquire welding skills, it is better to start with simple products, since the reliability and strength of any metal structure depends on a quality connection. Proper execution of the welding process is the main guarantee of quality work.
Recommended:
Welding seams: types of seams and joints
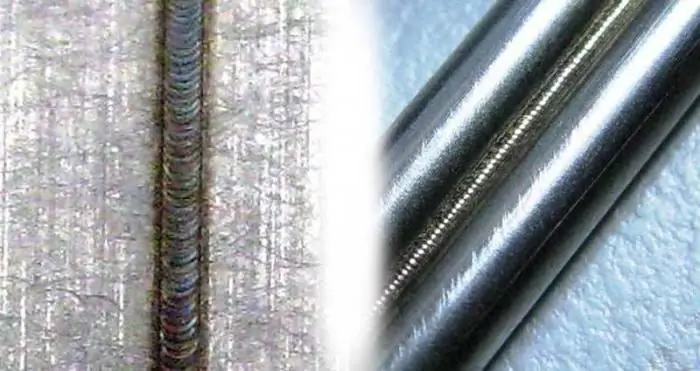
In the process of welding, various connections are obtained. Welding seams are able to connect not only metals, but also other dissimilar materials. They are classified according to several criteria: method of execution, spatial position, length, etc
Ultrasonic testing of welded joints, methods and technology of testing
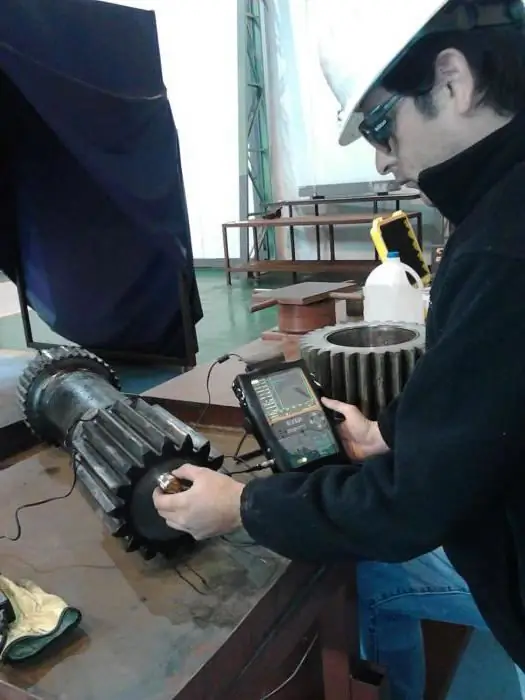
Ultrasonic testing - advanced technology for the study of welding joints and seams. It will be discussed in this article
Wood shavings: types, production technology and application features

Wood shavings as an industrial, packaging and decorative material. Types and characteristics of chips, differences from chips and sawdust. Application in the country, in animal husbandry, in construction, as a heater, decorative element and filler when packing gifts and fragile items
Butt welding: equipment, methods and process technology
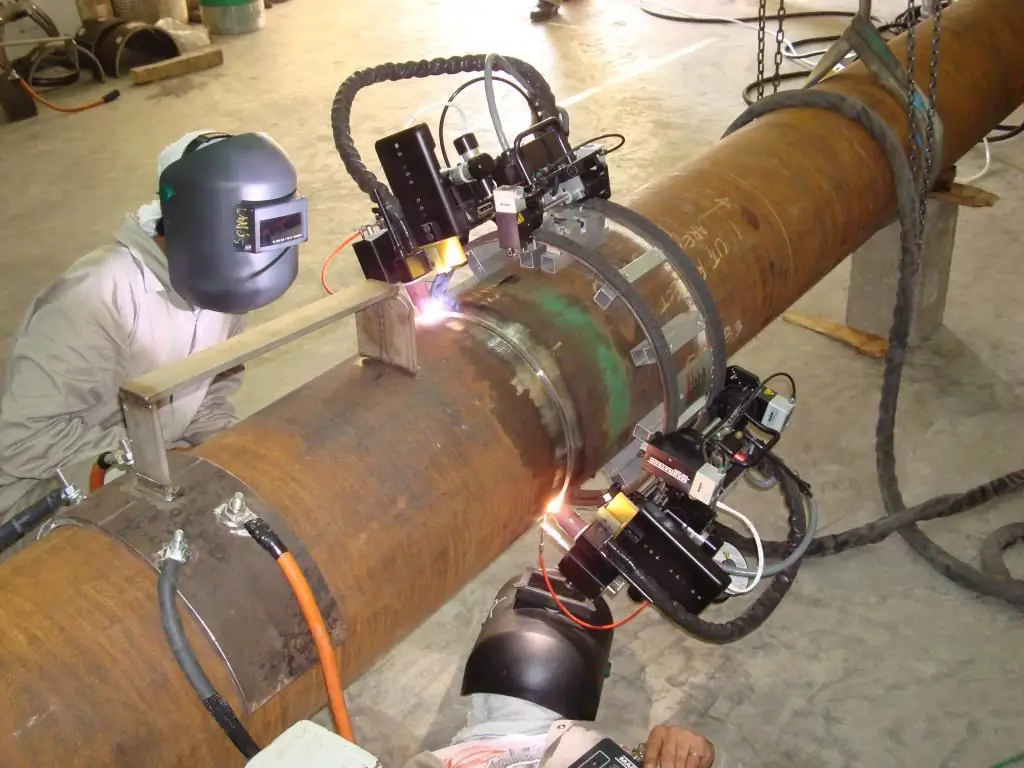
Features of flash butt welding. Types of butt welding joints, as well as equipment, methods and technology for carrying out the butt welding process. Welding seam defects arising from flash butt welding, as well as the reasons for their formation
Non-destructive testing of welded joints: equipment, GOST
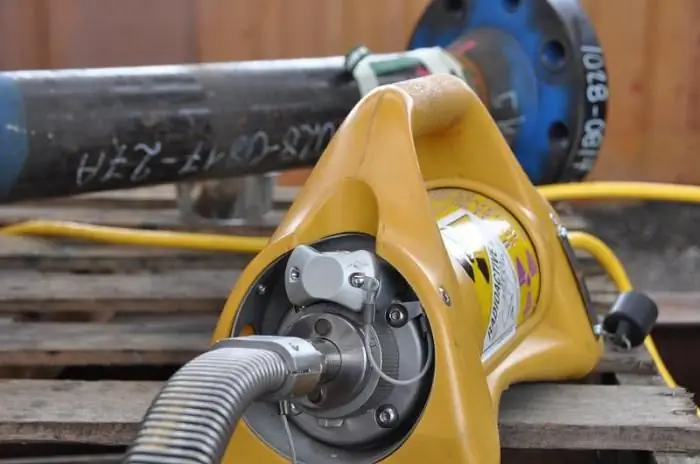
The article is devoted to methods of non-destructive testing of welded joints. The methods of control allowed by GOST and the equipment used are described