2025 Author: Howard Calhoun | [email protected]. Last modified: 2025-01-24 13:10
Welding in automatic or semi-automatic mode often takes place using such a consumable item as flux-cored wire. One of its main advantages is the ability to save gas, which would be spent on preventing oxidation.
Wire description
The most common use of flux-cored wire is when it is necessary to work with metals such as copper, titanium and aluminum. Another feature concerns the welding seam. It turns out to be very even and quite durable. Most often, the main component is a granular flux. Although this is not always the case, there are cases when oxide, s alt components are used. Also, in some cases, a combined type of s alt oxide base is used.
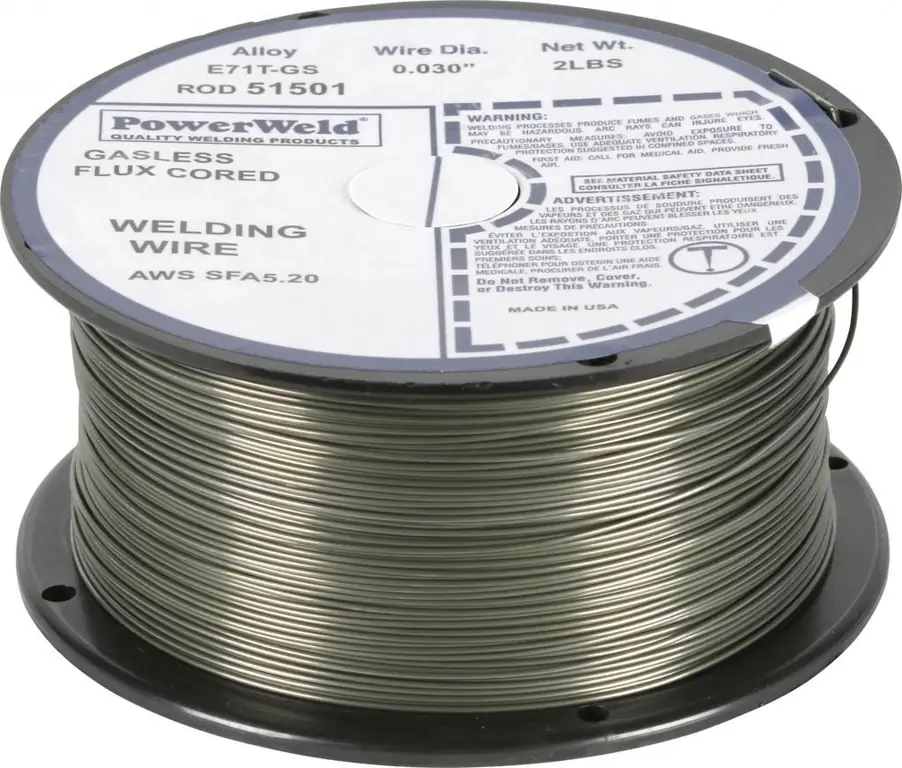
Key Benefits
It's worth starting with the fact that flux-cored wire has a high degree of melting. This allows it to be used for working with refractory materials. In addition, during operation, a high welding speed is ensured,and the working arc is characterized by stability and softness. The arc also burns evenly, which is why the seam turns out to be even. One of the rather significant advantages is that after welding with flux-cored wire, it is enough to simply remove the slag coating from the weld.
In addition to the above positive qualities, there are many others:
- good welding area protection;
- high speed of work is accompanied by efficiency;
- melting can be carried out to a sufficiently large depth, and there is no splash during operation;
- during operation no harmful volatile substances are released;
- you can control the amount of oxygen contained in the weld;
- The use of flux-cored wire welding technology helps to optimize the weld structure.
It is worth noting that the protection of the welding area is possible precisely due to the fact that the wire contains flux. Because of this, atmospheric gases do not reach the welding site, and therefore do not oxidize the welded material. It is worth noting that due to the presence of such a number of advantages, the flux wire for semi-automatic is used not only by amateurs for welding, but also by professionals.
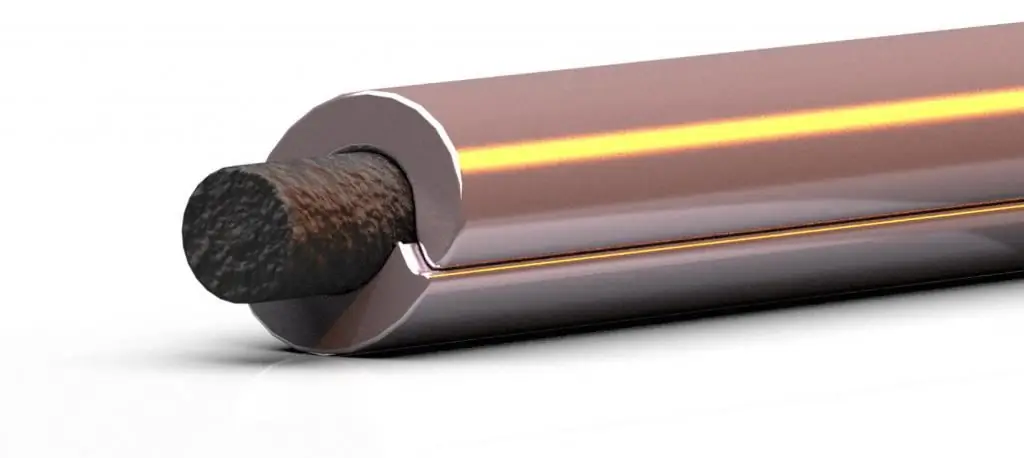
Main Applications
Most often, a welding machine that works using this type of wire is used to join materials such as non-ferrous metal, alloy steel and other high-alloy substances.
Depending on whetherwhat exactly is to be welded, the composition of the flux will change. For example, if it is necessary to weld together a material that belongs to the group of low-alloy steels, then oxide flux must be used. If you have to work with non-ferrous metal, then the flux-cored welding wire must have a s alt composition. For alloyed steel, a combined composition of oxide and s alts is used.
Besides, the other main parameter of the wire, the diameter, will also change. This indicator fluctuates in a fairly wide range, from 0.6 mm to 8 mm. Of course, the thicker the welding wire, the longer it will take for it to melt. And this will depend on the feed rate. Because of these factors, it turns out that if the thickness of the material is low or its composition is easy to weld, then using a thick wire is simply unprofitable.
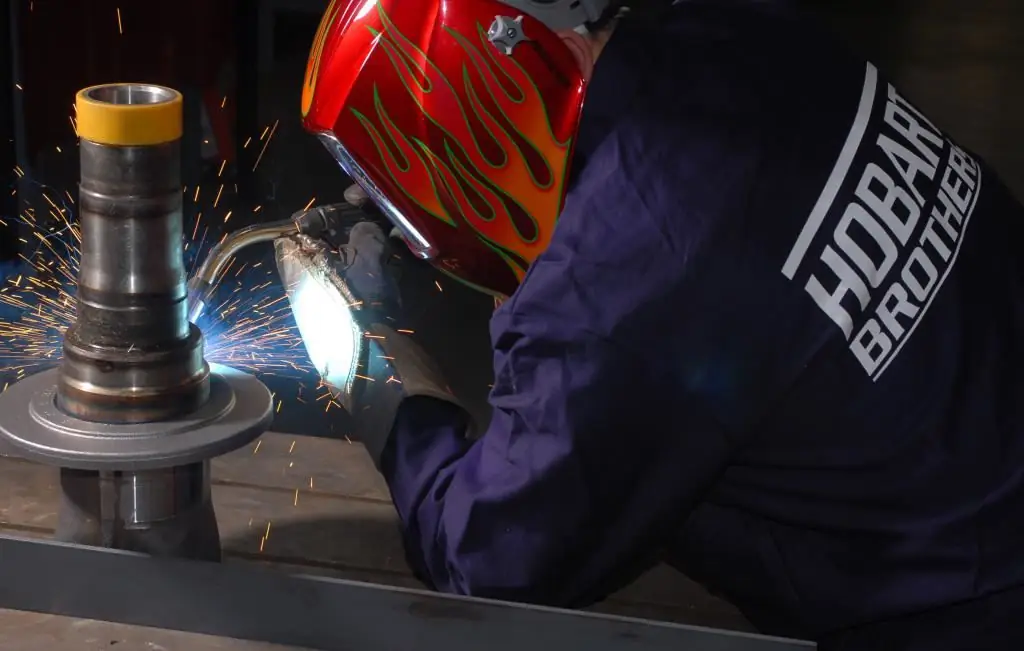
Select wire by diameter
As already described above, when welding with flux-cored wire, an element with a diameter of 0.6 to 8 mm is used. In addition to the feed rate, the speed of its melting also depends on this parameter. These several factors are very important and must be taken into account when choosing.
Let's say that in order to get the highest possible even seam, it is necessary that the wire be long. For example, if it is necessary to weld a sufficiently refractory material together, and the seam must be strong and thick, then the thickness of the electrode must be taken large. If it is necessary to carry out work with sufficiently softmetals in terms of welding, there is no need to use thick wire.
If the diameter was chosen correctly and all the rules for the work were observed, then welding with a flux-cored wire without gas can provide a high quality weld, a high margin of safety and create a connection that will be resistant to atmospheric influences. These three factors make it possible to use structures connected in this way even in places with extreme conditions, for example, in a zone with increased pressure.
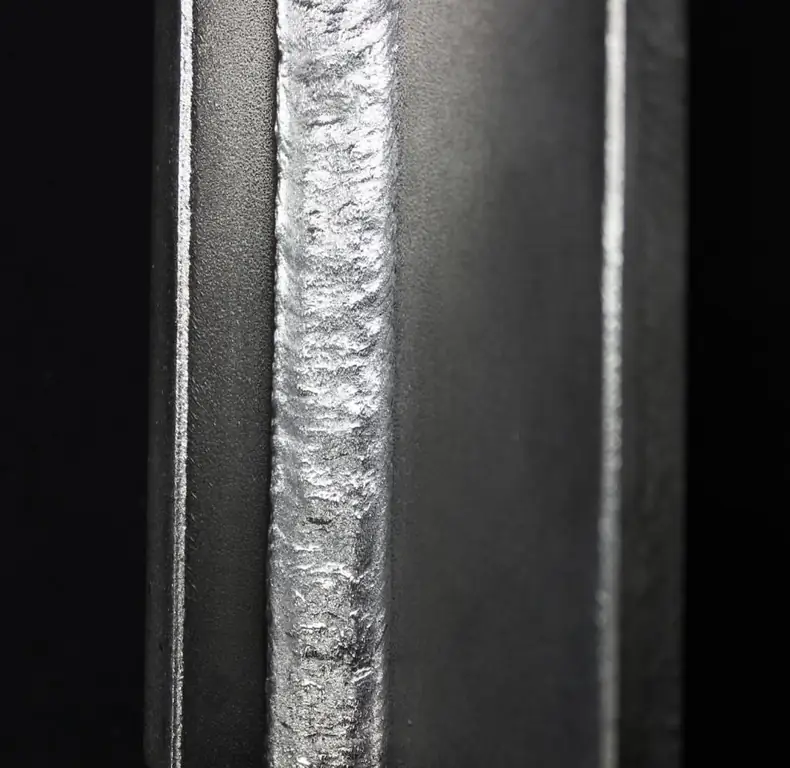
Flaws
Despite the large number of advantages, like any other thing, the wire has its negative qualities.
Firstly, the cost of this type of element is quite high, which means that welding with flux-cored wire is not always profitable in terms of cost or cost. Secondly, finding such an electrode on sale is much more difficult than any other. Thirdly, it also happens that even with the help of a flux material it is not possible to solve the problem of poor weldability of the material and you have to spend money on additional measures, which further increases the cost of the process.
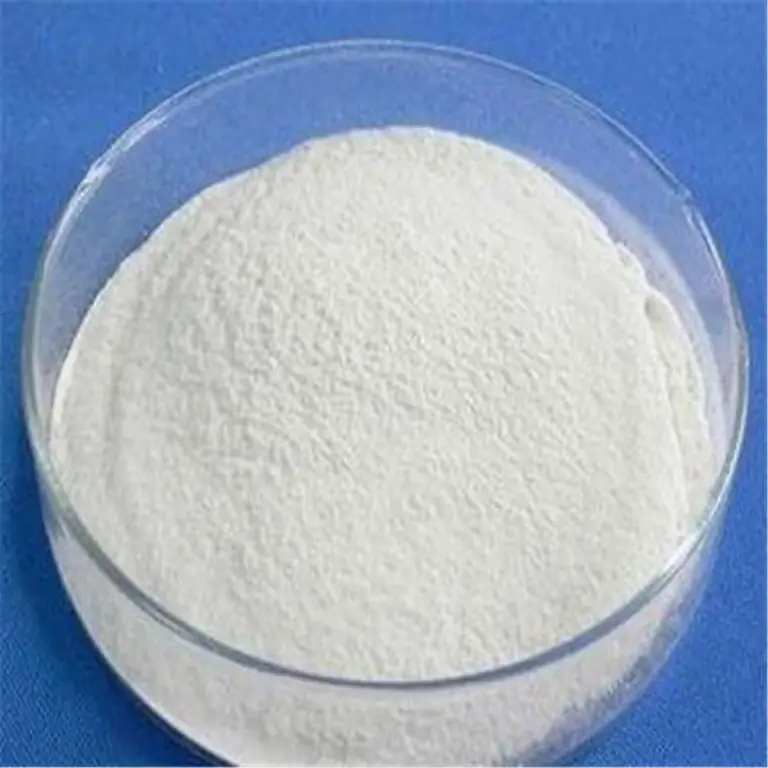
Types of wire
Today it is important to consider not only the thickness and diameter, but also what needs to be worked with.
For example, with regard to steel, you cannot use the same wire with the same parameters for any material, since they can be from different groups, for example, by the level of alloying of the composition. BesidesThere is also such a material as stainless steel. As for copper welding, it is necessary to use a consumable with a diameter of 0.8 mm, which is specially created for use with copper parts. Such a wire will help improve the quality of the seam when welding at normal temperatures.
As for the main specifications and their meanings, they are as follows:
- ultimate strength is 480-580 MPa;
- yield strength from 400 to 490 MPa;
- relative elongation ranges from 22 to 27%;
- as a protective gas, if necessary, carbon dioxide can be used.
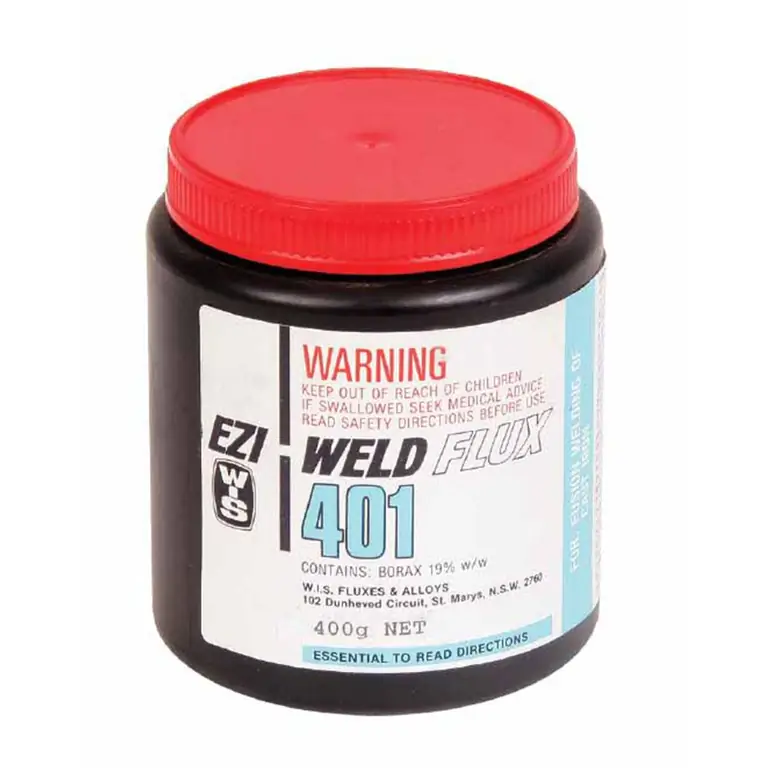
Powder material
Today, flux-cored wire is also actively used. It is a tube inside which is placed a welding flux containing metal powder as an additive. It also has its own characteristics and can be used for different purposes, but in practice it is usually used only for welding low alloy steel or for not very strong carbon steel.
There are several basic requirements for working with such a consumable.
Firstly, the powder flux must provide a stable arc, as well as the ease with which it will appear. Secondly, during melting, there should be no spattering of the material and uniformity of melting. Naturally, it is necessary that the end result, that is, the seam, does not have flaws. During welding, slag will form on the coating, which aftercooling should be easy to peel off the surface.
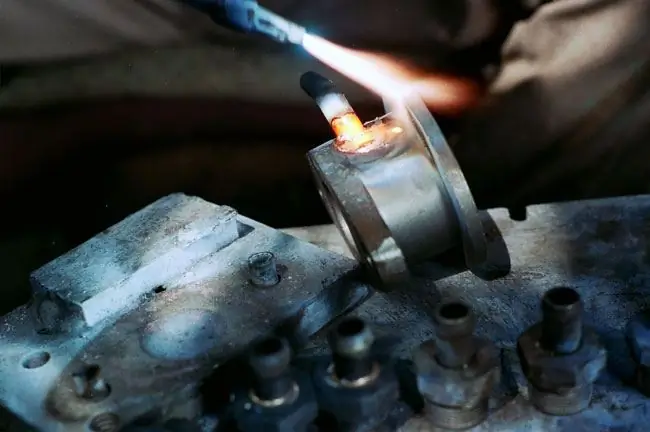
Types of wire for powder welding
Further it is worth saying that there are different ways to use and protect from external influences. According to these two criteria, flux-cored wire is divided into gas-shielded and self-shielded.
As for the first type, it is used in cases where it is necessary to work in automatic or semi-automatic mode, and low-alloy steel or low-carbon steel acts as the processed material. During operation, carbon dioxide and sometimes its mixture with argon are also used. If you choose the right flux powder, you can improve some welding parameters. For example, you can increase the speed of vertical welding or improve the bond strength of hard-to-weld steel.
As for the use of this welding technology, it is relevant mainly for creating overlaps, as well as at the corners of structures or at joints. As mentioned earlier, it can be used both in automatic welding mode and in semi-automatic mode.
Self-protective type of wire
Feature of self-shielded wire is that it is made in the form of an electrode that is "turned" inside out. The peculiarity of the application lies in the fact that welding with such a consumable can be used at a wide variety of and even extreme temperatures. In addition, it is allowed to carry out work in strong gusts of wind and other similar weather conditions.
Worth highlighting a few morethe benefits of a self-shielding flux-cored wire.
- allows welding in any position;
- since the arc in this case is an open type, that is, the ability to slowly move the metal being processed;
- wire is coated with a special substance that increases pressure resistance;
- it is possible to control the chemical composition, which means that you can get a certain composition of the slag if necessary.
Powder Welding Benefits and Reviews
As for the advantages that powder welding has, these are all points regarding open methods and semi-automatic. In other words, there is no such problem as in the case of shielding gas flow, which can be blown away by strong winds.
If we talk about the main advantage of welding with wires from this category, then this is the absence of the need for lengthy preparatory work.
Reviews about flux wire and working with it are quite good, but there are also bad ones. The bottom line is that for a small amount of work, the wire fits perfectly and it costs less than a gas bottle. However, in the event that it will be necessary to cook a lot, then constantly buying such a consumable will be very expensive, this is the main problem. It is worth buying wire if you do not need to cook too much.
Recommended:
The main consumable for welding - welding wire
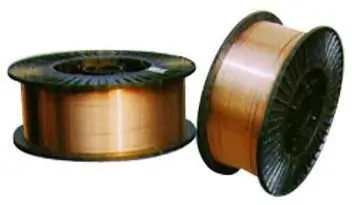
Welding wire is used in various welding operations, it is the main consumable material that acts as an electrode. Welding operations require extensive professional knowledge, a responsible approach to the choice of raw materials. For welding structures, it is unacceptable to use random wire of incomprehensible marking and unknown composition
Work permit for work in electrical installations. Rules for work in electrical installations. Work permit
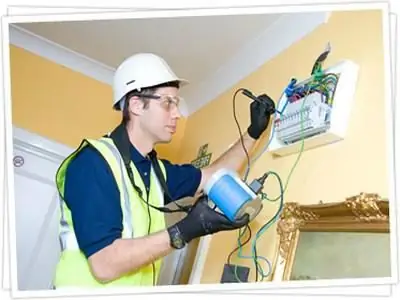
From August 2014, Law No. 328n comes into force. In accordance with it, a new edition of the "Rules on labor protection during the operation of electrical installations" is being introduced
Two-component polyurethane sealant: definition, creation, types and types, characteristics, properties and nuances of application
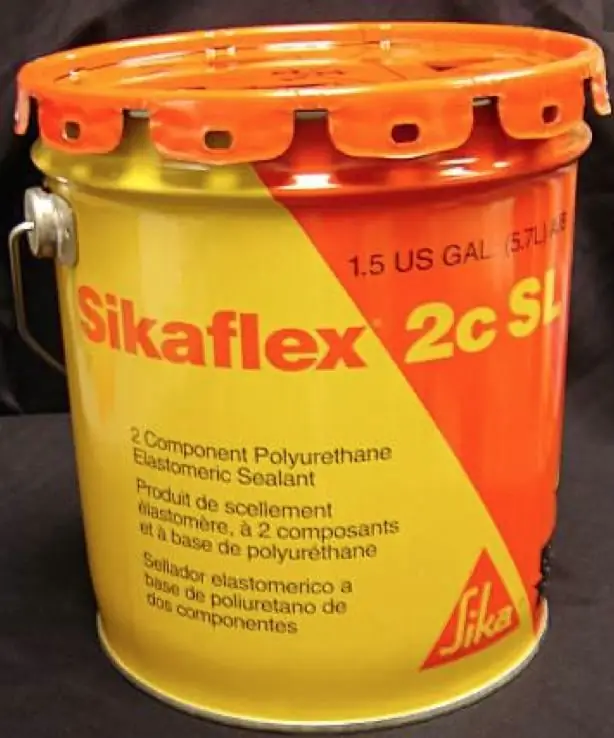
With long-term and high-quality sealing of seams and cracks, polyurethane two-component sealants have found their wide distribution. They have high deformation and elastic properties, therefore, they can be used as butt sealants in the field of repair and housing construction
Welding in a shielding gas environment: work technology, process description, execution technique, necessary materials and tools, step-by-step work instructions and expert advice
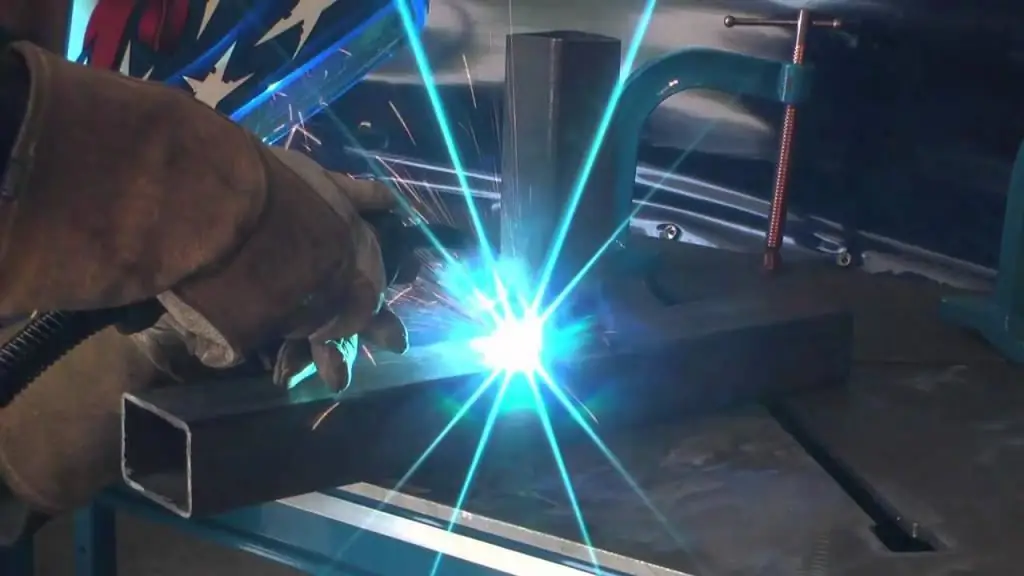
Welding technologies are used in various branches of human activity. Versatility has made welding in a protective gas environment an integral element of any production. This variety makes it easy to connect metals with a thickness of 1 mm to several centimeters in any position in space. Welding in a protective environment is gradually replacing traditional electrode welding
Flux for welding: purpose, types of welding, flux composition, rules of use, GOST requirements, pros and cons of application
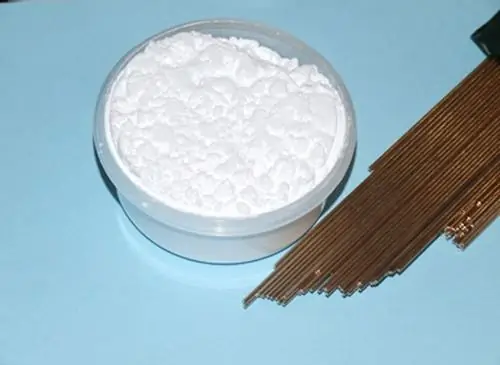
The quality of the weld is determined not only by the ability of the master to organize the arc correctly, but also by the special protection of the working area from external influences. The main enemy on the way to creating a strong and durable metal connection is the natural air environment. The weld is isolated from oxygen by a flux for welding, but this is not only its task