2025 Author: Howard Calhoun | [email protected]. Last modified: 2025-06-01 07:12
The quality of the weld is determined not only by the ability of the master to organize the arc correctly, but also by the special protection of the working area from external influences. The main enemy on the way to creating a strong and durable metal connection is the natural air environment. Seam isolation from oxygen provides flux for welding, but not only this is its task. Different configurations of the composition of this additive with a combination of protective gas environment allow you to control the parameters of the seam joint in different ways.
Flux assignment
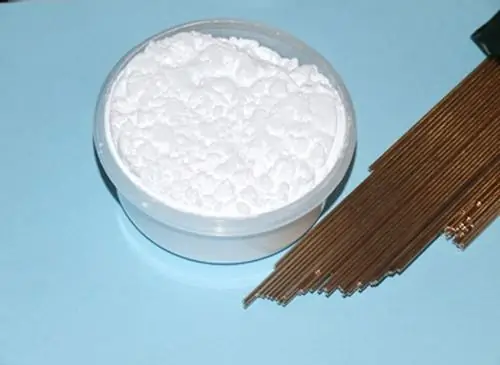
The welding consumable of this type is sent to the combustion zone and, depending on the characteristics of its melt, has a protective and modifying effect on the weld formation area. In particular, the material can perform the following functions:
- Creation of slag and gas insulation for the weld pool.
- Giving a welded jointcertain technical and physical properties.
- Maintaining arc stability.
- Transfer of electrode metal (or wire melt) to the welding zone.
- Removal of unwanted impurities in the slag layer.
If we talk about the compatibility of different fluxes for welding with metals, then the most common brands have the following purposes:
- FC-9 - low alloy steel carbon alloys.
- AN-18 - high alloy steel alloys.
- AN-47 - low- and medium-alloy steels, characterized by high strength characteristics.
- AN-60 - low alloy steels used in pipelines.
- ФЦ-7 - used when welding mild steel at high current.
- FC-17 - high-temperature face-centered iron.
- FC-19 - alloys with a high chromium content.
- ФЦ-22 - is used to make a fillet weld joint in work with alloyed carbon steels.
- 48-OF-6 - is used in welding techniques with the connection of high-alloy electrode wire.
Flux compositions
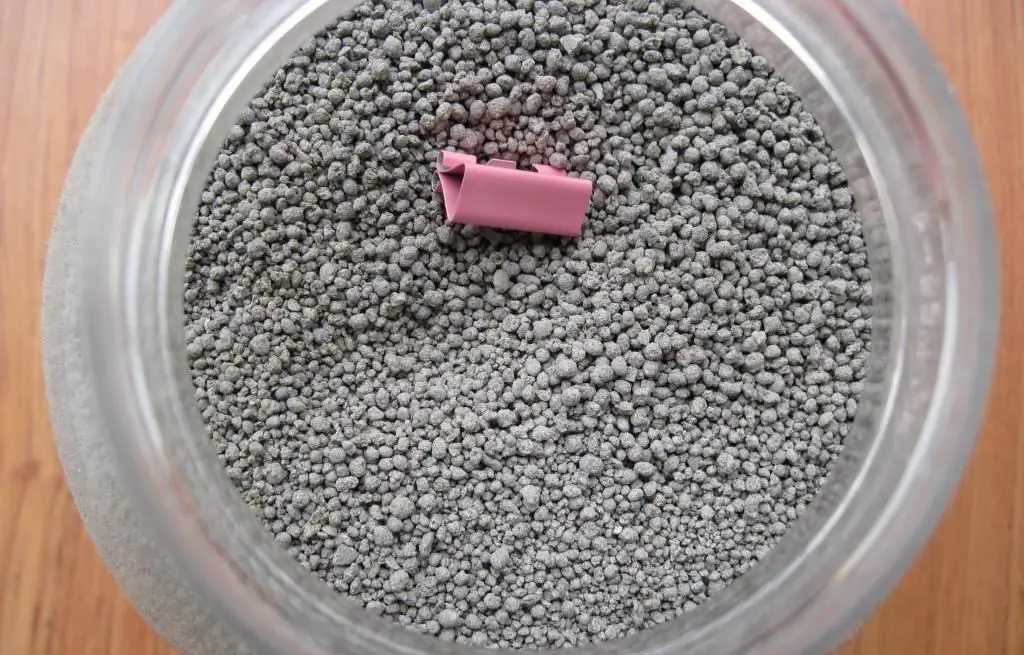
The flux itself, as a rule, is produced in the form of a granular powder with a fraction of about 0.2-4 mm. But the content and origin of this product can be very different and not always uniform. In this regard, the following types of flux for welding are distinguished:
- Oxide. Most of the content is metal oxides and about 10%accounts for the proportion of fluoride elements. This flux is used to work with low-alloy and fluorine steel alloys. Also, depending on the content, oxide flux compositions are divided into silicon-free, low-silicon and high-silicon.
- S alt oxide. Such powders are also called mixed, since the filling can be equally formed by oxides and s alt compounds. This flux is used to process alloy steel.
- Saline. The presence of oxides is completely excluded, and fluorides and chlorides form the basis of the composition. The purpose of s alt flux is electroslag remelting and welding of active metals.
Flux technology
During the manufacturing process, the flux base (batch) undergoes several processing procedures, including smelting, granulation, molding and quality control. The raw material of the charge before the production process is segmented into small, medium and large. Each batch undergoes a thorough washing and drying, as the purity and accuracy in the parameters of the future flux are maintained from the outset. Then weighing, dosing and mixing with other technological components is performed. Smelting and granulation of flux for welding is carried out on special equipment - gas-flame or electric arc furnaces, pools for pouring cold water and metal pallets are used. At the final stages of processing, drying with sifting is performed. Flux that has passed inspection is packaged in special bags or boxes with refractory properties.
GOST requirements for flux
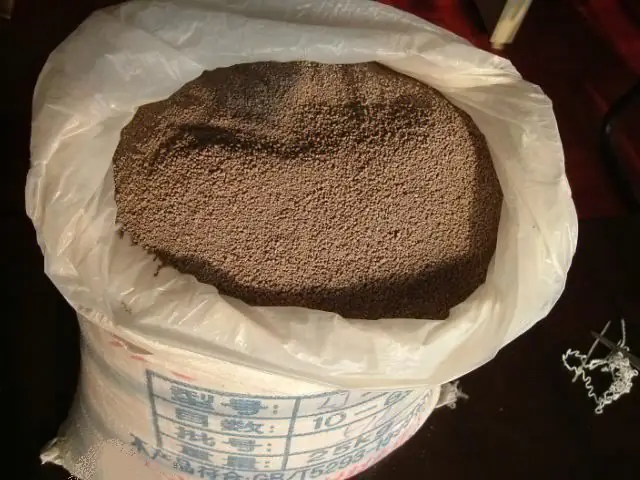
Regulatory requirements affect several areas of flux quality assessment, as well as regulate the safety rules for handling the material and methods for testing it. As for the main parameters, the following requirements are imposed on them:
- Excluded in flux powder grains larger than 1.6mm. The percentage of their content should not be more than 3% of the total mass.
- It is allowed to produce a flux with a fraction of up to 0.25 mm, if this condition was initially agreed with the consumer.
- Also, by agreement with the consumer, it is permissible to manufacture material with a grain fraction from 0.35 to 2.8 mm, but only in relation to the AN-348-A grade.
- The moisture content of fluxes, depending on the brand, should not exceed a coefficient from 0.05 to 0.1%.
As for safety requirements, personal protective measures are the main subject of GOST regulation. Submerged arc welding must be carried out in accordance with fire safety measures. Separately, the concentration of the flux powder used, which by default is considered chemically hazardous and harmful to production, should be controlled.
Fused and non-fused flux
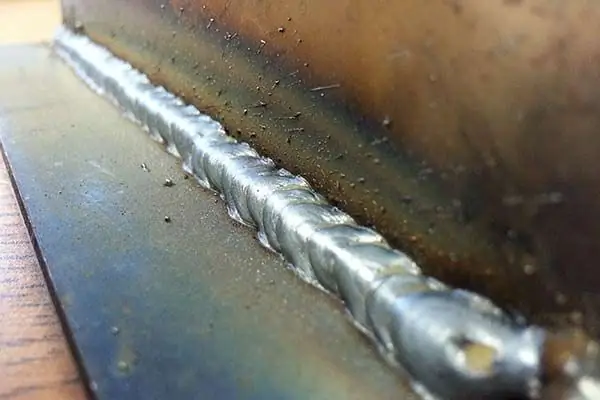
The content of fused powder is mainly formed by slag-forming components. They are produced as a result of the fusion of constituent elements, including quartz sand, manganese ore and chalk. By mixing them in certain proportions, followed by melting in furnaces, it is possible toget a modifier for a seam with a certain set of characteristics. More functional is submerged arc welding produced in an unmelted way. This is a mixture of granular and powder materials, which, in addition to the slag-forming base, also include alloying elements and deoxidizers. The absence of a melting operation makes it possible to introduce metal dust and ferroalloys into the flux, which will decipher the possibilities for improving joints.
Types of submerged arc welding
With the use of flux, both manual and automatic welding can be performed - the fundamental difference will depend on the selected equipment. Arc welding is performed in self-adjusting mode or supported by automatic voltage control. It is optimal to use inverter installations, supplemented by wire feed drums. Welding with flux without gas is also common, which by default acts as a protective environment from oxygen and nitrogen. How good is the technique that eliminates this barrier to negative impact factors? Firstly, if a suitable flux is selected, it will be able to perform the entire list of protective and auxiliary tasks in relation to the formed seam. Secondly, the absence of a gaseous medium facilitates the very organization of the process. No need to prepare a cylinder with an argon-carbon dioxide mixture, and also protect the welding area from excessive thermal exposure when using a torch.
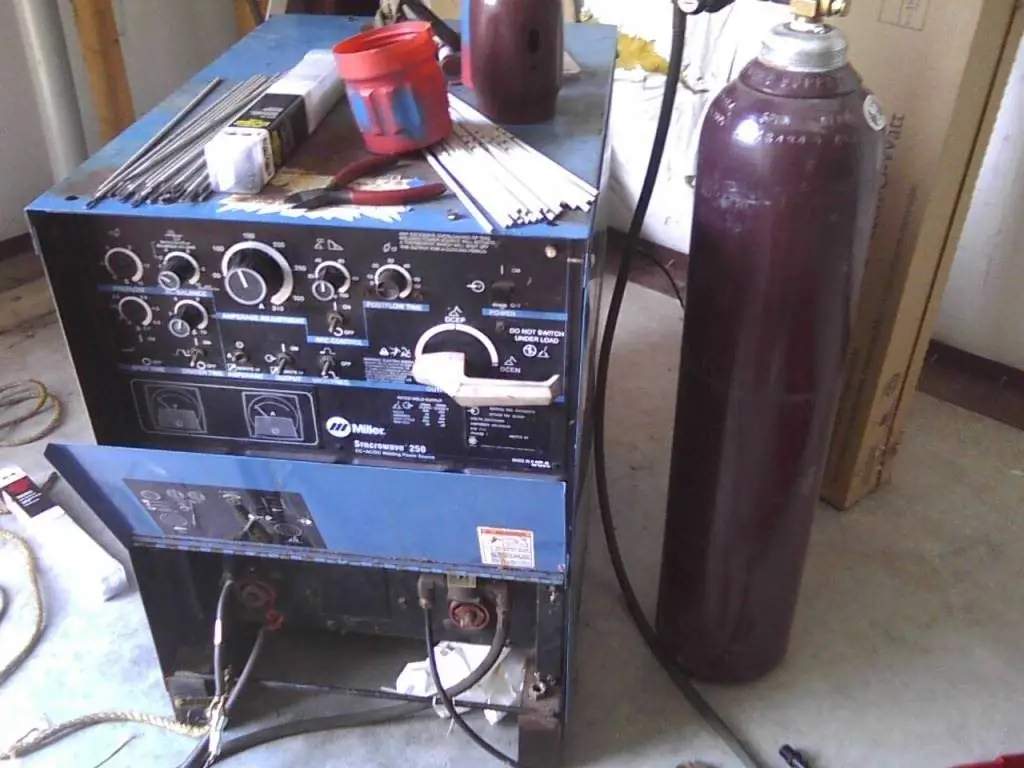
Flux technique
After ignition of the arc, the operator must maintain itbetween the end of the electrode and the workpiece under the flux layer. The powder is poured in a layer of 55-60 mm, after which the arc should be literally drowned in this mass until it melts. With an average flux weight, its static pressure on the metal can be about 8-9 g / cm2. This value is sufficient to eliminate unwanted mechanical effects on the weld pool. When using a wire for welding with flux, it is possible to achieve minimal melt spatter. This condition is met by ensuring stable contact of the melt zone with the consumable wire and flux, as well as by regulating the current strength. Protection from the gas side is also not required in this case, but power control will be especially important. As a rule, a combination of wire and flux is used when welding at a high current density, therefore, the machine must be selected taking into account the maintenance of a constant speed of guiding the electrode thread.
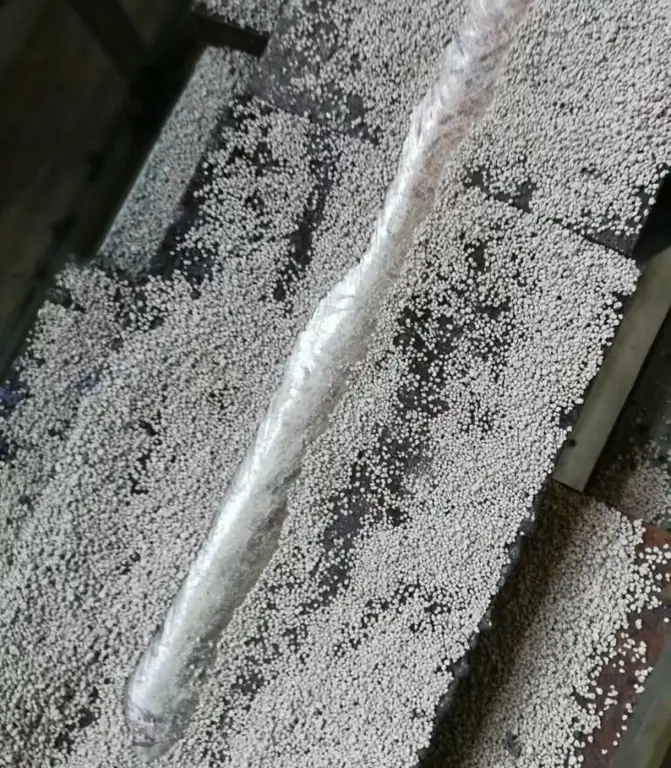
Pros of using flux
The use of flux certainly affects the formation of the seam in the best way, since the negative factors of the working process in open air conditions are minimized. The obvious benefits include reduced defects in the joint area, minimization of spatter and more efficient arc control with full auto control capabilities. What is also very important, the submerged arc welding area is always visible to the operator. This allows, if necessary, to make timely adjustments to the process, and in some cases even do without specialmasks.
Disadvantages of using flux
Weaknesses of this technology are caused by higher requirements for equipment, since more power is required to effectively melt the flux. Today, special modifications of devices for argon arc welding in a flux environment are produced, which have special equipment for its preparation and supply. It is logical that such models cost 15-20% more. Another disadvantage is associated with an increase in the melt zone. Although it can be controlled within certain limits, it is problematic to process small elements in such conditions.
Conclusion
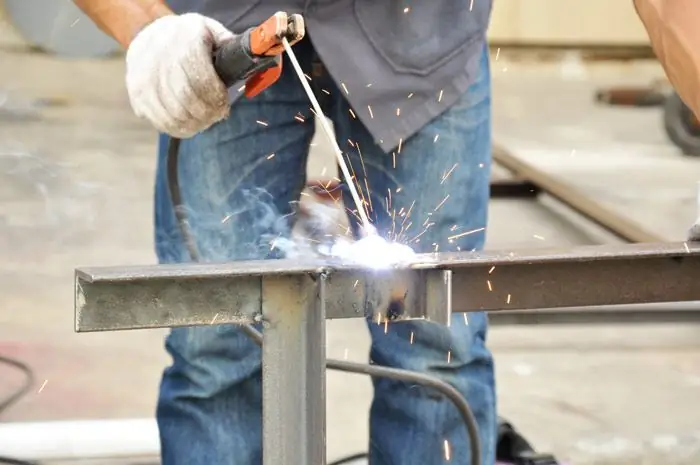
Flux as a consumable that improves the quality of the welding process, facilitates many production and construction activities of this spectrum. But even at home, it is often used in the country, in the garage or simply in repair operations. When choosing this material for your own needs, it is very important not to miscalculate the quality assessment. As noted by the same GOST, flux for welding should be supplied to the market in thick paper bags from 20 to 50 kg, indicating transport markings. By special order, small packaging can also be made, but special containers must be provided for this. Moreover, weighing should be carried out with a maximum error of 1% relative to the total tare weight.
Recommended:
Industrial marker: description, composition, rules, application and purpose
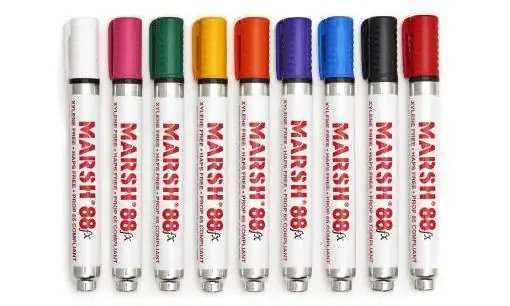
Industrial marker - a writing tool for applying information on a variety of surfaces. In this case, the surface can be wood, glass, stone, metal, leather, painted materials and even rust. The requirements for such a marker are very specific
Concentrated feed: purpose, composition, nutritional value, types and quality requirements
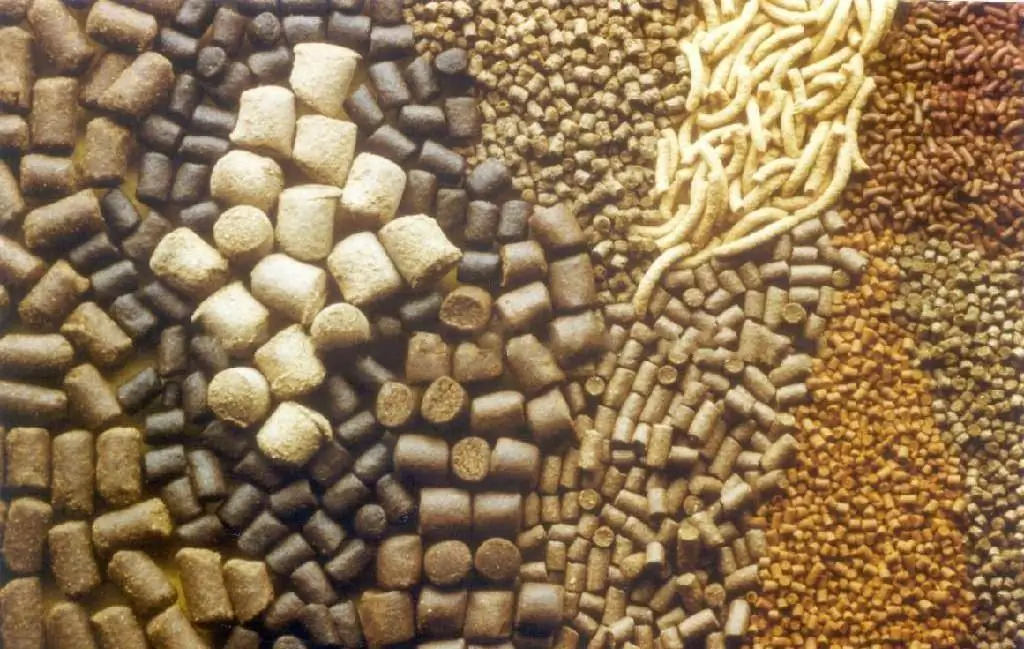
In addition to juicy and rough, concentrated feeds are also introduced into the diet of agricultural animals and poultry. There are only two main varieties of them - carbohydrate and protein
Cement slurry: properties, preparation rules, composition, compliance with GOST requirements, purpose and application
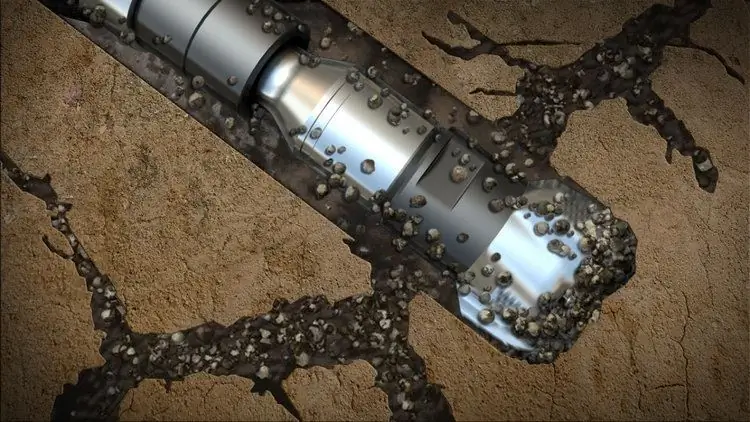
During the drilling process, special solutions are used to flush out cuttings and products from the development of local rock. This operation is necessary to increase the efficiency of the mechanical impact of the drilling rig and to clear the bottom hole. Washing out is carried out using cement slurries, which are prepared using special technologies
Polymer cement mortar: composition, technical characteristics, compliance with GOST requirements, purpose and application
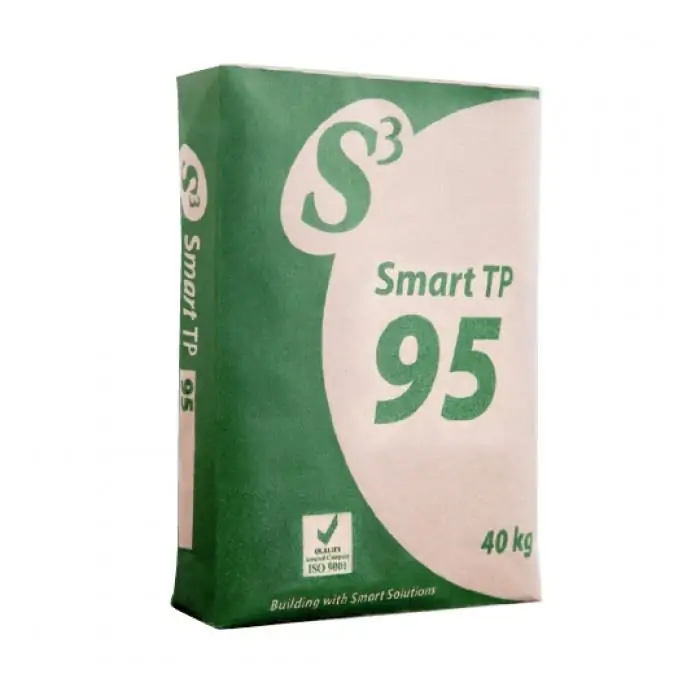
Polymer cement mortar is one of the modifications of conventional sand-cement mortar. Polymers can also be added to mixtures that are used when laying plaster and other facing materials. The addition of this substance to the composition helps to improve its characteristics
What is CAS: fertilizer composition, types, release form, purpose and instructions for use
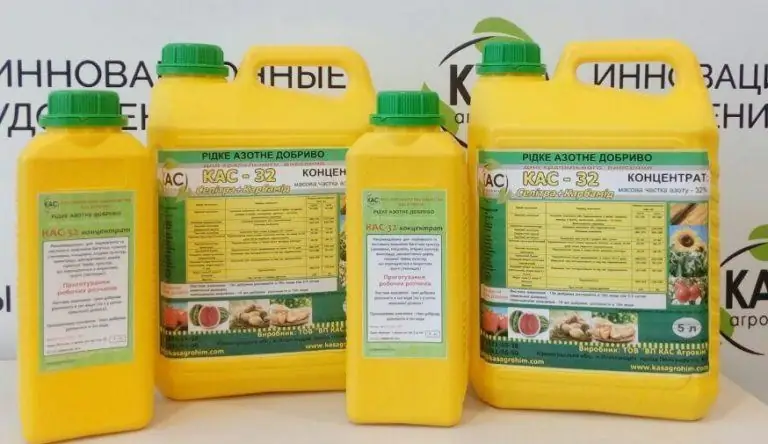
What is CAS? In order for garden and agricultural crops to develop well and give large yields, it is necessary, among other things, to use nitrogen fertilizers. The most popular type of such top dressing is CAS