2025 Author: Howard Calhoun | [email protected]. Last modified: 2025-06-01 07:12
Welding technologies are used in various branches of human activity. Its versatility has made gas-shielded welding an integral part of any production.
This variety makes it easy to connect metals with a thickness of 1 mm to several centimeters in any position in space. Welding in a protective atmosphere is gradually replacing traditional electrode welding.
The essence of the welding process in shielding gases
The welding process is used to create a permanent connection between different metals. It is achieved by heating the connected elements to a temperature close to the melting point. Heating takes place with the help of an electric arc, which has a combustion temperature of 7,000 to 18,000 °C. This allows you to heat the metal being welded and form a weld pool, which is filled withmolten electrode.
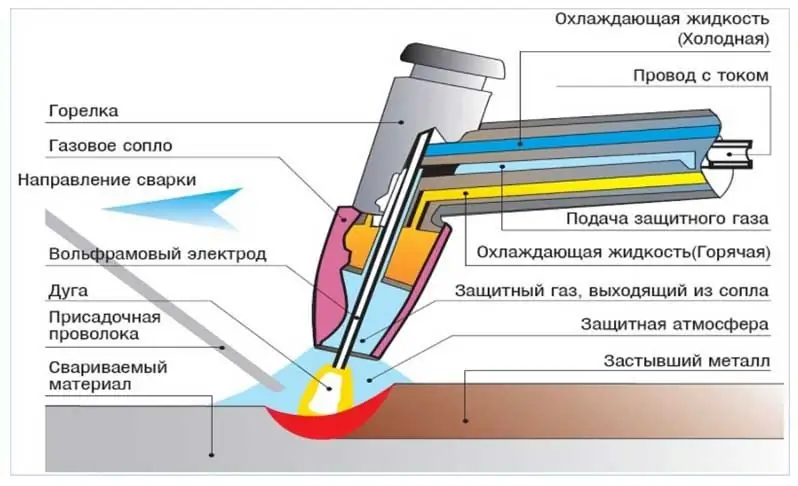
In order for the electric arc to burn stably, and also so that the air does not affect welding, protective gas is supplied to the combustion zone, which creates a dome that prevents oxidation.
Gas-shielded welding is used where simple welding with a coated electrode does not work. This is a compound of metals such as:
- copper;
- bronze;
- titanium;
- molybdenum;
- chrome and others
Modern automatic production uses mechanized welding in shielding gases. With its help, not only non-ferrous metals are brewed, but also ferrous ones (varieties of steel).
Method advantages
This type of welding has many advantages.
- Allows welding of non-ferrous metals. The complexity of their welding lies in the fact that they have a low melting point with high oxidization, which contaminates the welding zone with oxides and makes it difficult to obtain a high-quality seam.
- High temperature heating. This makes it possible to localize the welding zone within small limits. As a result, the welded metal does not change its mechanical properties due to overheating.
- High performance. Welding in a shielding gas environment makes it possible to automate the process through the use of wire wound on a coil and its automatic feeding.
- No slag. No time is wasted deleting it.
Disadvantages of shielded welding
To the disadvantages of this specieswelding can be attributed to the bulkiness of the equipment. In addition to the welding machine itself, the kit includes gas cylinders, reducers, gas fittings.
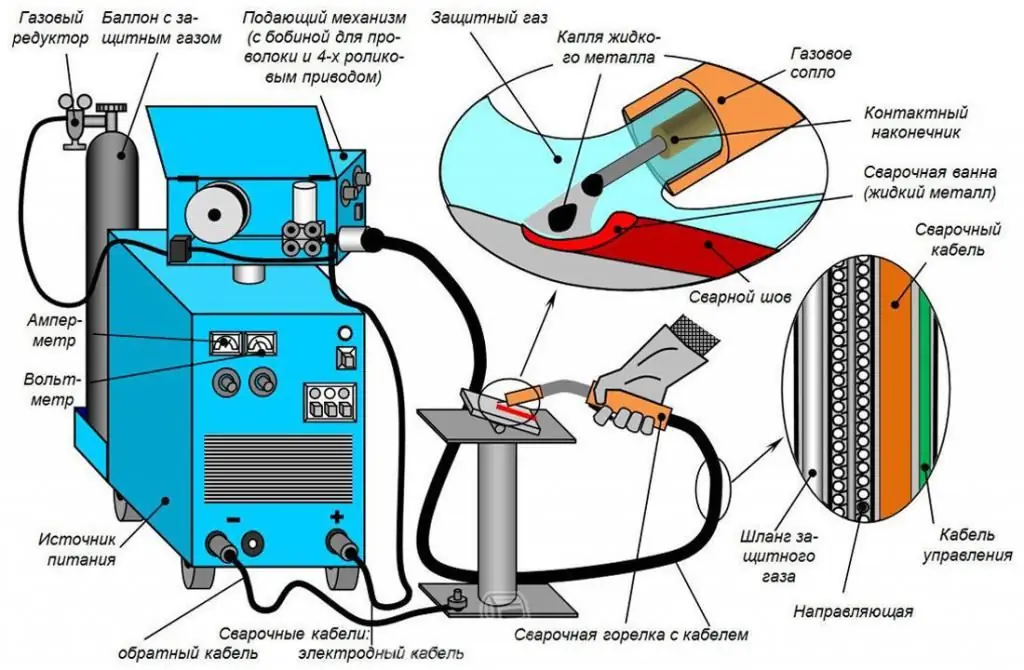
Consumables are more expensive than conventional arc welding.
In modern enterprises, the main criterion for economic feasibility is the time spent on production. They introduce automatic welding systems in shielding gases. Therefore, the high cost of materials is offset by high productivity.
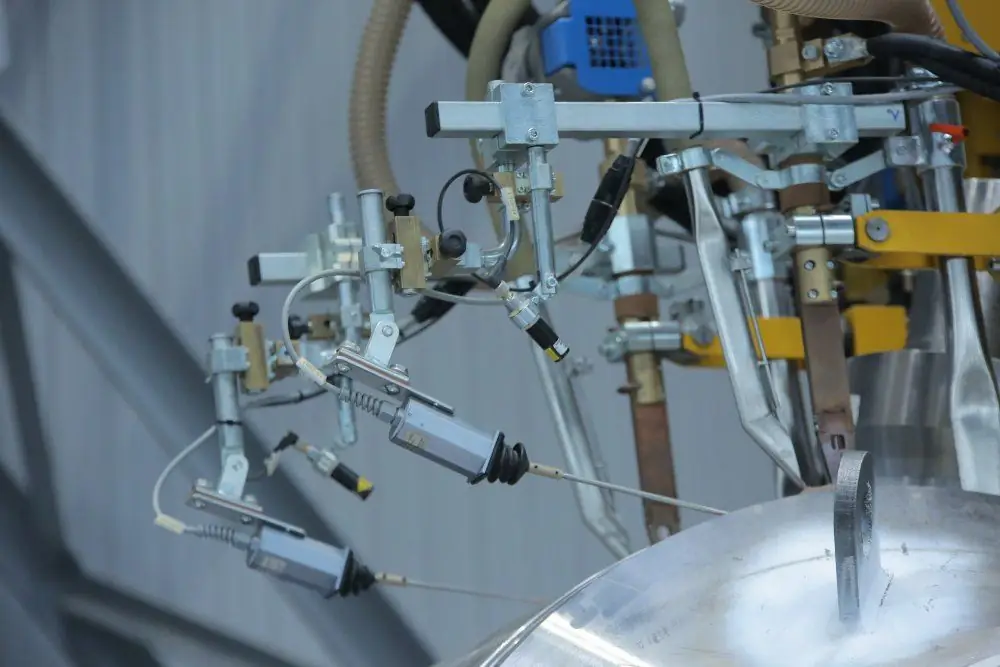
How strong are the welds
Welding metals creates a strong bond. It is much stronger than bolted or riveted joints. In addition, where it is necessary to create tightness, welding is indispensable. The main limitation in its application is the inability to withstand dynamic loads that vary both in magnitude and in the vector of impact. It is for this reason that rivets are used in aircraft construction instead of welded joints.
The strength of the weld depends on the materials used, compliance with the technology and the correct preparation of the edges to be welded.
Varieties of used equipment
Gas shielded welding has two varieties:
- Non-consumable electrode. The electric arc is created by a tungsten rod that does not melt in the process. Material to fill the weld pool is fed manually in the form of a piece of wire.
- Consumable electrode. Here the electric arc is createdautomatically fed wire, which receives an electric current. This wire melts and fills the weld pool, forming a seam.
Depending on this, gas shielded welding equipment is divided into two types:
- Welding transformers and inverters equipped with tungsten tip torch.
- Semi-automatic welding. Now this type of equipment is the most widely used. With their help, you can weld the whole range of metals. They are mobile and have great performance. Semi-automatic welding in a shielding gas environment is used both in garages and private households, as well as in serious enterprises.
- Laser-arc welding. This is a type of hybrid equipment, where in addition to the welding arc from the tungsten electrode, deep melting is created by the laser beam. In this case, a device is used that combines laser optics and a tungsten-tipped torch.
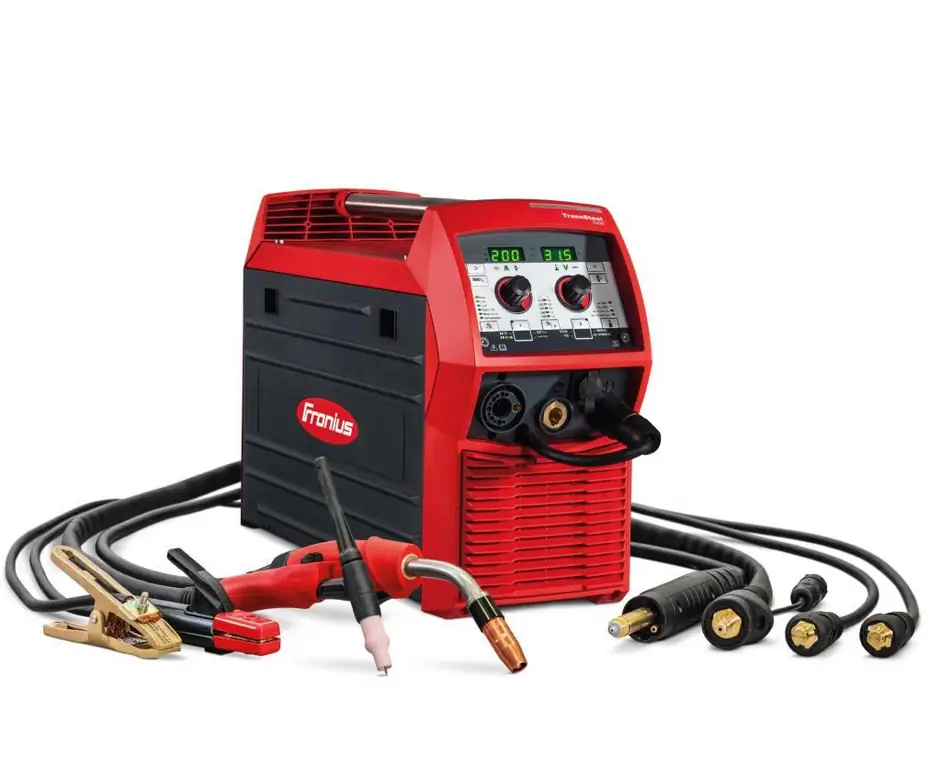
Which gases are used
There are several types of gases used, which can be divided into 3 groups: inert, active and combined.
Inert gases include: helium, argon. Helium is lighter than air, more expensive to produce, and less commonly used. But the arc in it picks up a higher temperature than in argon, so welding in a helium environment has a higher productivity. It is used for welding aluminum and magnesium alloys.
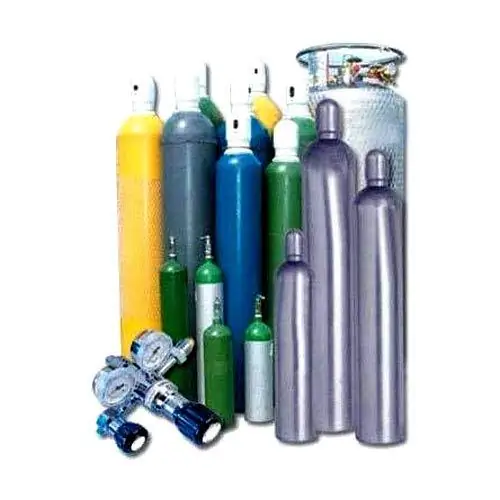
Argon has a widerapplication. It is used for welding critical parts, as well as rare and non-ferrous metals.
Nitrogen can be classified as conditionally inert gases. It is used only for welding copper and its alloys, in relation to which it is not active.
Active gases, although they protect the welding zone, nevertheless dissolve themselves in the weld metal, changing its composition. These include carbon dioxide and oxygen. CO2 is used for welding ferrous metals: low and medium carbon steels, cast iron, low alloy steels, etc.
Oxygen comes only mixed with inert gases.
Combinations of gas mixtures are used in different proportions to increase the stability of the welding process and improve the mechanical characteristics of the weld.
Consumables
For semi-automatic welding in a shielding gas environment, a wire rolled into coils is used. It has over 80 varieties. Its diameter is from 0.3 to 12 mm. The coils into which it is folded weigh from 1.5 to 40 kg. The wire is selected with the same composition as the parts to be welded.
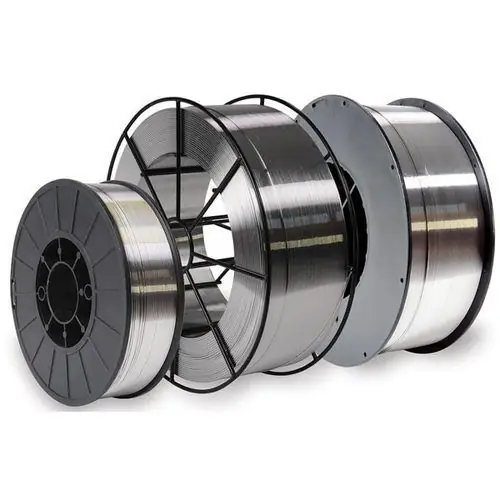
Non-consumable electrode can be either tungsten or carbon. The tungsten electrode is a wire with a diameter of 0.5-3 mm or rods with a diameter of 5-8 mm. The material for the additive is a wire with a diameter of 1.6-5 mm.
Preparation for welding work
Welding in a protective environment is performed mainly for welding critical parts. Therefore, the first requirement is a high qualification of the worker. To carry out suchworks are allowed welders of at least 5th grade, who have been trained and received a permit.
Before starting work, regardless of the certificate, the welder is forced to butt-weld a sample that will be tested for strength. GOST gas-shielded welding determines how much tensile force this sample must withstand.
The welding room should contain a minimum of dust. All types of work with its formation are prohibited (cutting, grinding, grinding work).
The indoor air should be warm and dry. For this, thermometers and hygrometers are installed. The temperature must be at least 16 °C.
Good lighting should provide an overview of the welding zone and allow timely detection of defects that occur in different welding modes in a shielding gas environment.
Drafts are not allowed in the room. The air flow speed should not exceed 0.5 m/s.
Tips & Tricks
To get a quality connection, you need to do some preparatory work.
- Properly cut the edges of the elements to be welded. The penetration and filling of the weld pool with metal depends on this.
- Thoroughly clean the surface to be welded from dirt, rust.
- Adjust shielding gas pressure. If the pressure is high, there will be excessive cooling of the welding zone. Low pressure will cause pores to form in the weld.
- Choose the optimal current strength. It is selected based on the thickness of the metal to be welded. The wire feed is adjusted according to the amperage.
- To receiveA high-quality seam burner must be periodically cleaned of scale. If this is not done, then gradually the scale will reduce the internal diameter of the burner, and the shielding gas will be supplied to the combustion zone with the wrong torch. Also, the scale will make it difficult to feed the wire. Silicone can be used to reduce the formation of soot on the burner. They lubricate the inside of the burner. Very handy aerosol cans for welding.
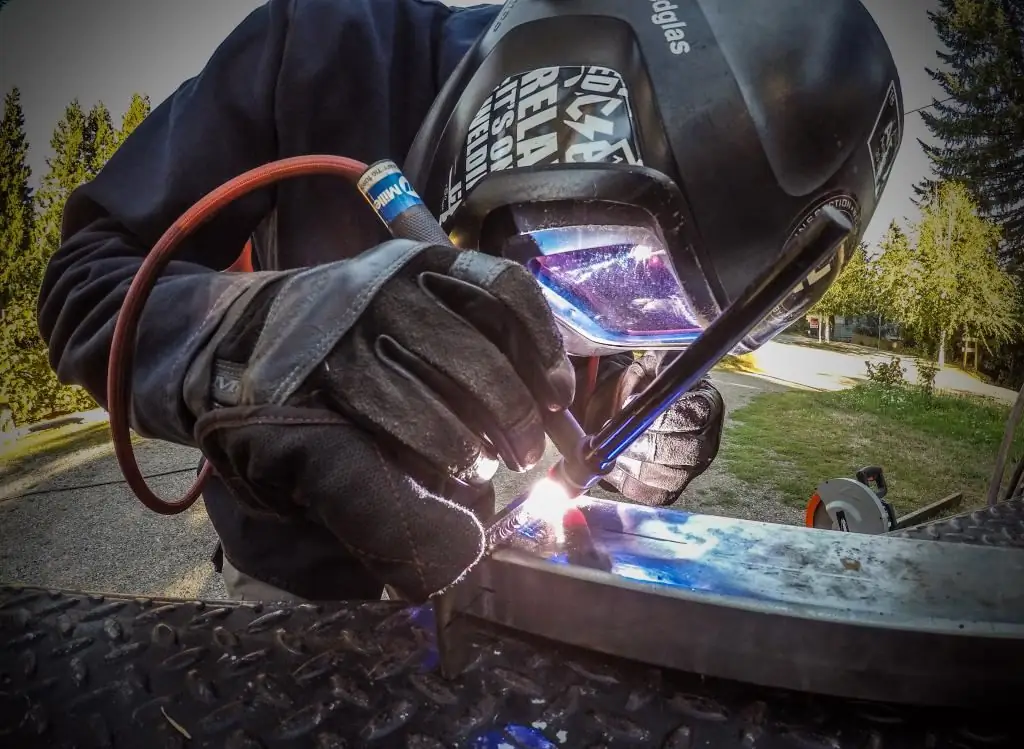
Gas-shielded welding is a responsible process that largely depends on the human factor. Compliance with safety measures, the use of protective equipment will help not only to perform the work efficiently, but also to maintain he alth.
Recommended:
Welding in shielding gas: modes, technology, application, GOST
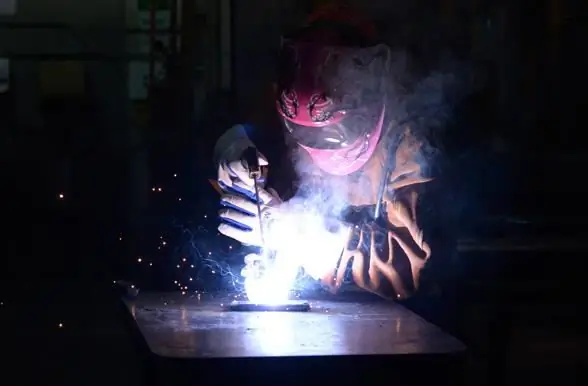
The article is devoted to the technology of welding in protective gas environments. The features of the working process, regulatory requirements for the technical operation, possible welding modes, the influence of gaseous media on the quality of weld formation, etc. are considered
Growing mushrooms in greenhouses: technology, characteristics of work, necessary conditions and expert advice
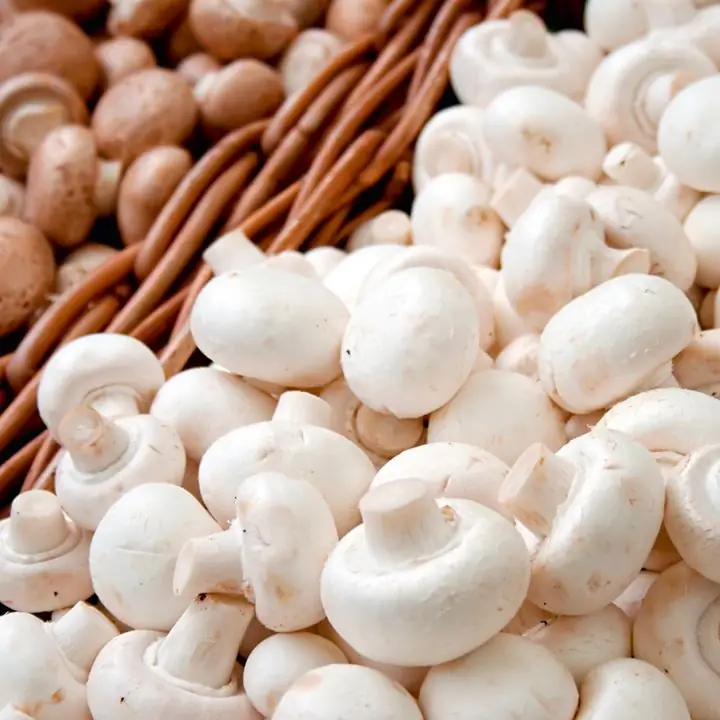
Growing mushrooms in greenhouses is a great way to get a clean crop for yourself or to sell. It cannot be said that the technology of this process is too complicated, but a lot of work will have to be invested
How to cook cast iron by electric welding: work technology and necessary materials
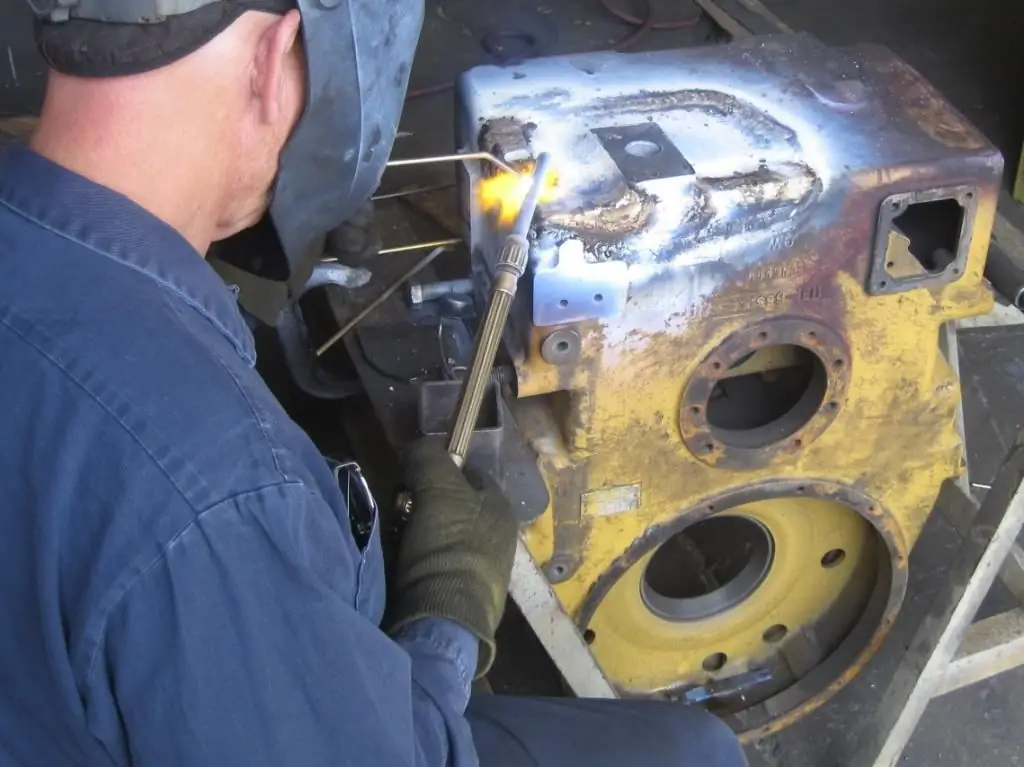
The main composition and types of cast iron. Difficulties and features of welding cast iron products. Cast iron welding methods. Preparatory operations before welding. How to cook cast iron by electric welding in a cold and hot way, as well as gas equipment. Features of the electrodes used for welding cast iron. Safety measures during welding
Forge welding: description, work technology and necessary tools
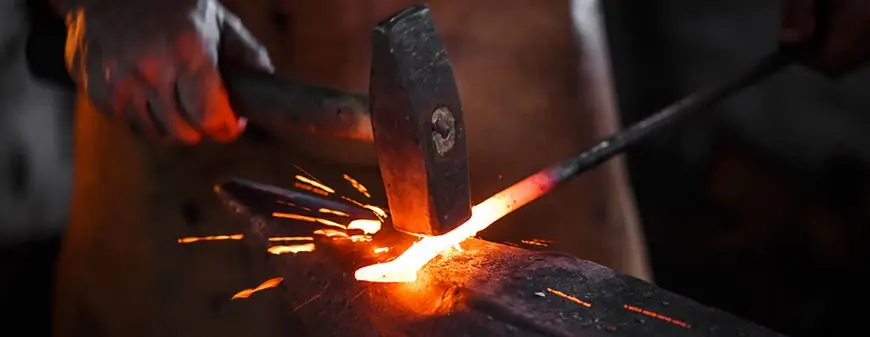
Forge welding is perhaps the oldest method of metal bonding. Blacksmithing was the only method of processing steel for several millennia, until in the 19th century specialists mastered the foundry industry. And in the 20th century, technological progress developed, as a result of which other progressive ways of connecting metals became available to mankind. Because of this, forging has lost its relevance
Arc welding in shielding gas: description of technology, modes, methods
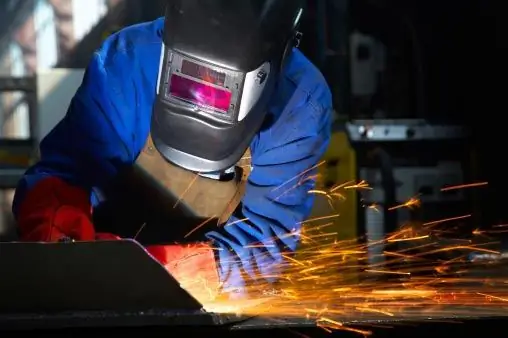
Gas shielded arc welding is a method that significantly improves the quality of the work result. This technology has a number of features. Before applying it, the master must familiarize himself with the basics of arc welding, which is carried out in a shielding gas environment. The features of this technology will be discussed in the article