2025 Author: Howard Calhoun | [email protected]. Last modified: 2025-01-24 13:10
At the present stage of industrial development, there are two main forms of organization of production systems, which cover production areas from ballpoint pens to passenger airliners. Depending on the type of products, production volumes, the complexity of the technology and a number of other indicators of the enterprise system, stationary or in-line methods of manufacturing or repairing products are used.
Difference of methods
The main difference between these two forms lies in the processes of moving objects or subjects of repair when performing specified technological algorithms. With the stationary method, an object (electric motor, car, etc.) is rigidly fixed in one position during the full production cycle. Workers perform the necessary set of stages according to production needs.
With in-line methods of organizing production, on the contrary, workers are rigidly fixed in space, and the manufacturing object(repair) moves between positions with selected production parameters. This maximizes productivity and reduces downtime.
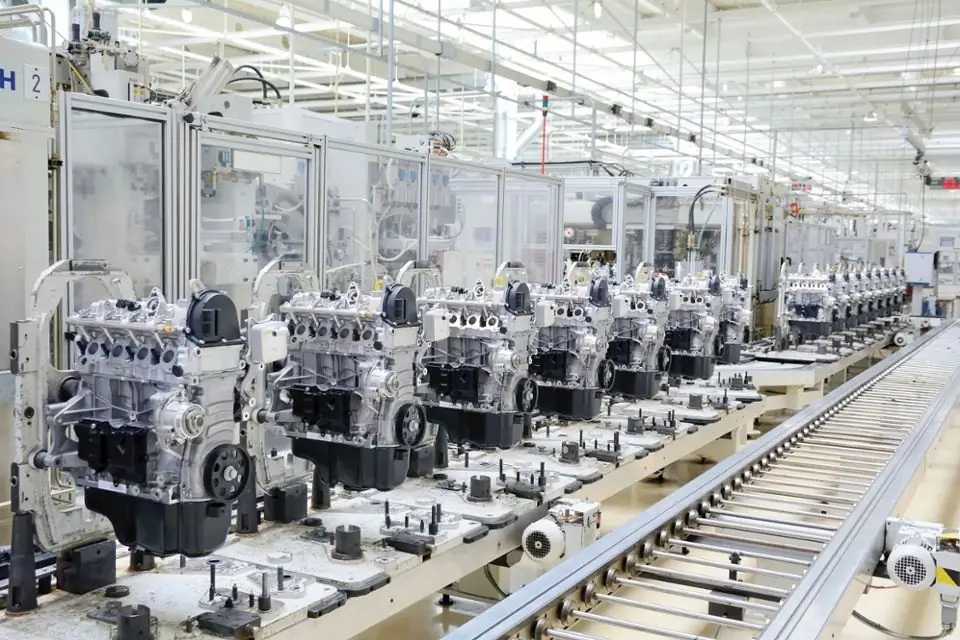
Development history
The development of branch industrial systems is determined by mass production enterprises, which, due to high volumes and rates of production, use the most advanced technologies and approaches. It is not surprising that the first cases of mass application of in-line methods of organizing production were recorded in the US automotive industry at the beginning of the 20th century. The industrialist Henry Ford is rightly called the father of the in-line forms of organization. After all, it was with his ideas that the introduction of the principles of a new production paradigm began.
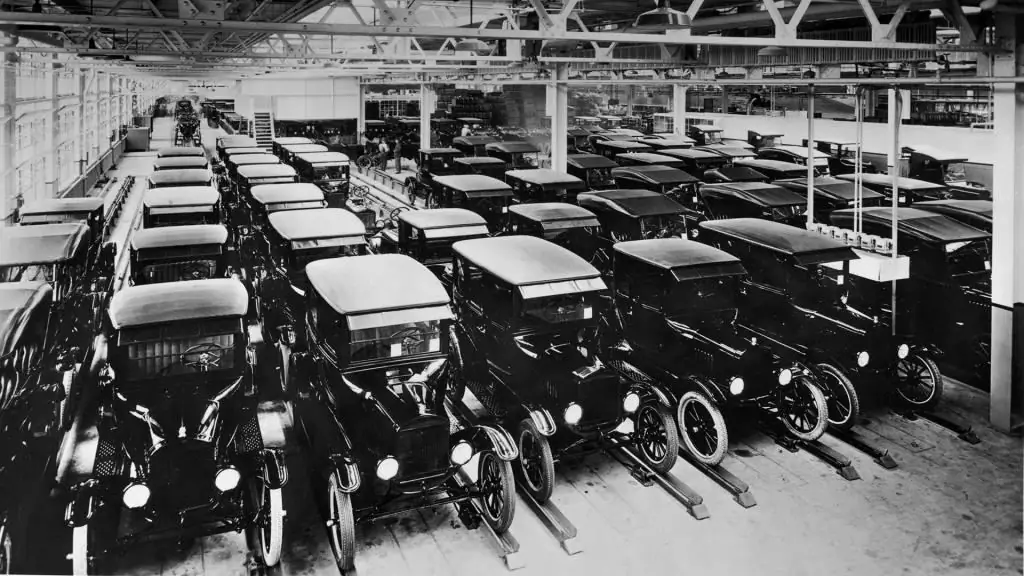
Prerequisites for Creation
The flow method of organizing production assumes a feasibility study. Therefore, at the initial stages, it is necessary to analyze production to meet the conditions for the transition to a more complex form of organization. These include:
- possibility of full loading of technological equipment, which is determined by a sufficient number of homogeneous products;
- detailed technology differentiation;
- long-term binding of operations in time and space;
- specialization in a limited number of operations with their maximum machineization;
- possibility to create a production flow (sequential placement of positions), which makes it possible to obtain optimalproduct flow patterns;
- use of a single time parameter (production rhythm);
- possibility of using transport parties (parallelism and concentration of production);
- availability of special transport for moving products.
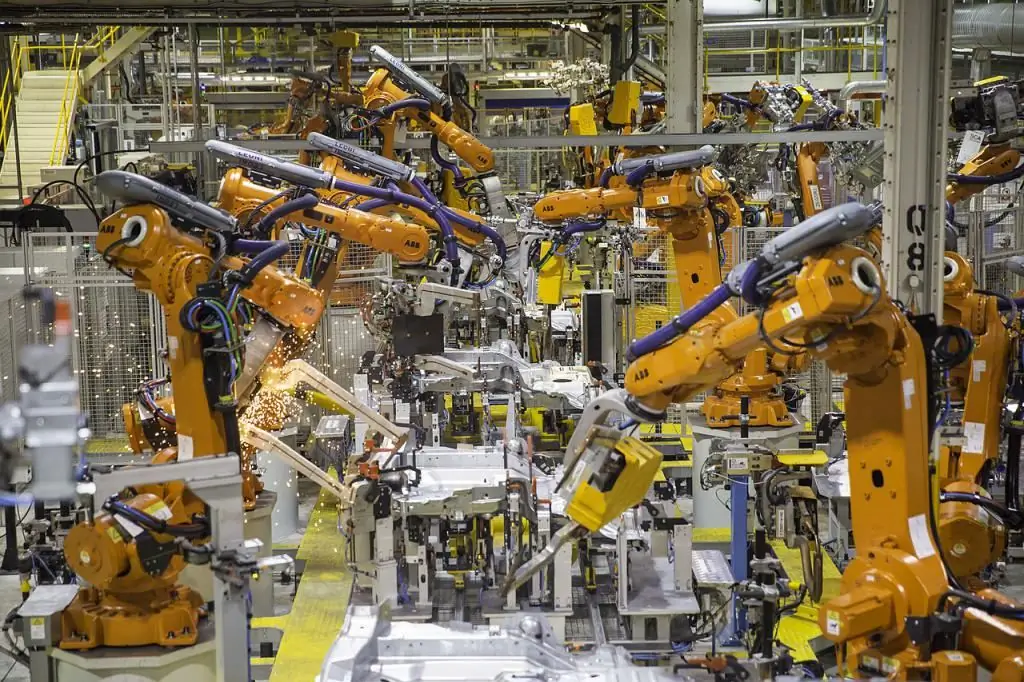
Positive implementation dynamics
Characteristic advantages of in-line production methods:
- use of high performance equipment (special);
- mechanization of transport technology units,
- rational use of system resources.
The effectiveness of the proposed forms is based on the optimization of a number of production indicators (labor productivity, production program, duration of the production cycle, workshop areas and production costs).
The overall performance is affected by:
- reducing the share of physical labor (reducing the number of employees) at transport stages through the use of special tools (conveyors, transporters, roller conveyors);
- reducing employee downtime due to equipment changeovers, disproportionate loading and multiple capacity distribution;
- maximum specialization of jobs (several heterogeneous operations per employee);
- reducing the overall labor intensity of manufacturing as a result of the introduction of new technological regimes.
Types of mass production
The main element of in-line production is in-line (technological)line. It consists of technologically related specialized positions or jobs.
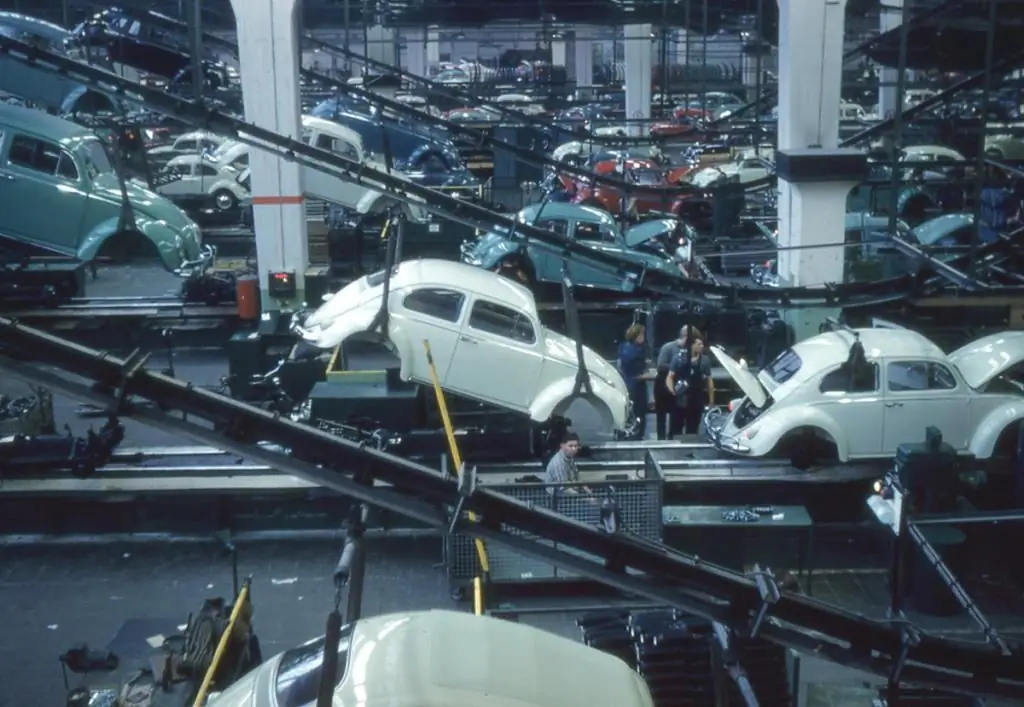
Production lines are classified according to a number of features:
- on the heterogeneity of products on the flow - on the line with homogeneous products and lines with products having different dimensions and structural elements;
- according to the structure of processes - continuous action in time (continuous) and periodic action;
- by type of rhythm - with a rigid (regulated) rhythm and with a changing (free) rhythm;
- for the transportation of products - with and without conveyor elements;
- by scale of use - at the level of the site (department), workshop (building), factory (several spans with a full production cycle);
- on mechanization and automation - non-mechanized (no movement in the case of large-sized products), with partial mechanization (movement with standard vehicles), with complex mechanization (use of a belt or chain conveyor), automated or automatic;
- by spatial configuration - rectilinear, ellipsoidal, etc.
The flow method of organizing production characterizes the dynamics of the enterprise. The use of different variants of production lines creates a certain level of specialization of departments and affects the overall efficiency of the system.
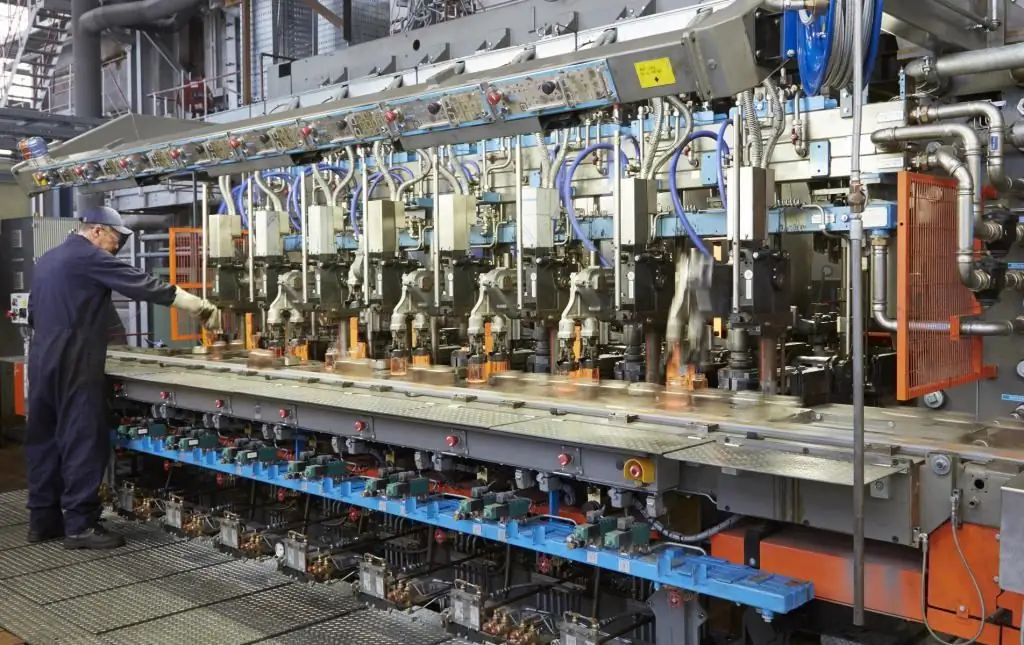
Features of flow system design
Note that the inline methodorganization determines the type of production. The introduction of a progressive machine model of the system in the presence of the required production volumes allows the enterprise to raise the bar of technological excellence.
The design basis for flow production is a rational scheme of functioning processes, which is based on several premises:
- Design prerequisites suggest the same type of structures, interchangeability of elements and their standardization.
- Technological allow the maximum separation of technology elements into component parts, which makes it possible to introduce deep mechanization of processes.
- Organizational conditions are based on a sufficient production program, full utilization of funds and a high level of specialization.
- Material are based on a progressive system of material support for the entire system (MRP, "Maximum-Minimum") and providing jobs (Kanban, FEED, etc.).
Standards for the flow method of organizing production
There are many options for the formation of production. The volumes of mechanization, spatial configuration, uniformity of structures are in fairly wide ranges. To create an efficient in-line system, a number of production guidelines, better known as in-line production parameters, are applied.
As a rule, they are classified into one of the following categories:
- parameters characterizing the work in time (measure, rhythm);
- parameters that determine the position in space (length, width, number of positions,workshop area, etc.);
- parameters that show the productivity of the production line (flow rate, productivity per unit time).
Scope of application
The most common flow methods of organizing production are used in mechanical engineering. The use at the enterprises of the automotive industry, railway transport, household electrical appliances is quite understandable from the point of view of product homogeneity, the possibility of creating transport parties, the detailing of technology and related factors. At the same time, the flow method of organizing production also characterizes the type of production.
However, flow technology is a certain approach to the organization, management and functioning of various processes. Therefore, the application of flow principles is possible in any systems that have the above prerequisites. Consider the use of flow technologies on the example of the construction industry.
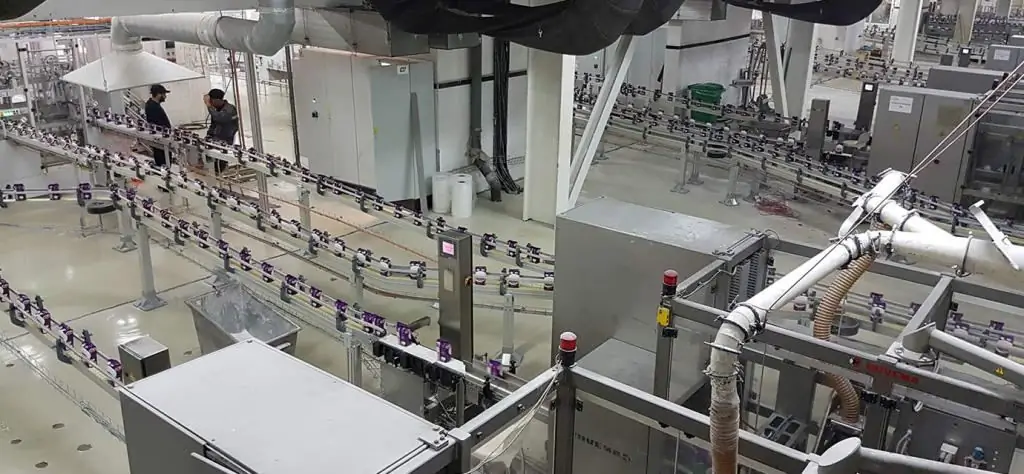
Features of use in construction
The construction of various objects is the same production process as the manufacture of industrial goods. In both the first and second cases, we deal only with different products (manufactured household appliances, built a house) and technologies (assembling a power supply, building a foundation).
The purpose of construction is the objects (buildings, structures) accepted for operation, obtained on the basis of the implementation of a complex of processes at the construction site. During construction, serial and parallel types are used.production cycles. In-line production was not bypassed either.
The flow method of organizing construction production consists in dividing the construction process into a number of stages - laying the foundation of a residential building, installing floors, internal work that work teams perform on the basis of the general rhythm of the production process. At the same time, they strive to create work areas with the complexity of equal multiplicity. Production processes of different content are carried out in parallel, which saves resources and reduces the cycle time.
The parameters of the flow method of organizing construction production characterize the features of the flow based on the accounting and analysis of technological, spatial and temporal characteristics. These include the flow structure, scope of work, labor intensity, flow step, cyclicity module, etc.
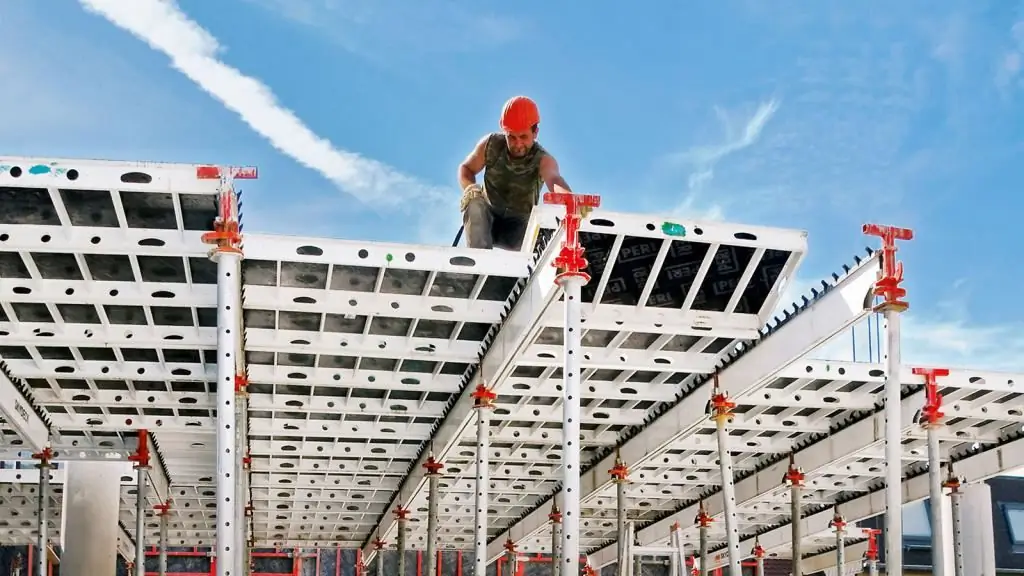
In closing
The analysis shows that the use of in-line methods of organizing production is a necessary condition for the formation of a high-tech modern enterprise. In-line technologies can be applied to a variety of manufacturing activities, ensuring high standards of productivity and product quality.
Recommended:
Essence and concept of organization. Form of ownership of the organization. Organization life cycle
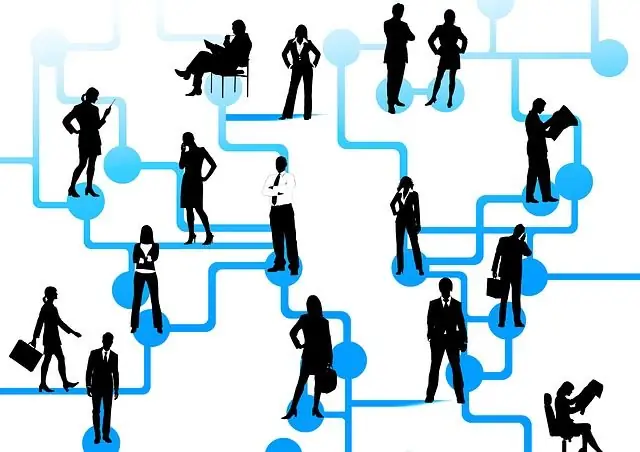
Human society consists of many organizations that can be called associations of people pursuing certain goals. They have a number of differences. However, they all have a number of common characteristics. The essence and concept of organization will be discussed in the article
Hoskold method, Ring method, Inwood method - ways to recover investment capital
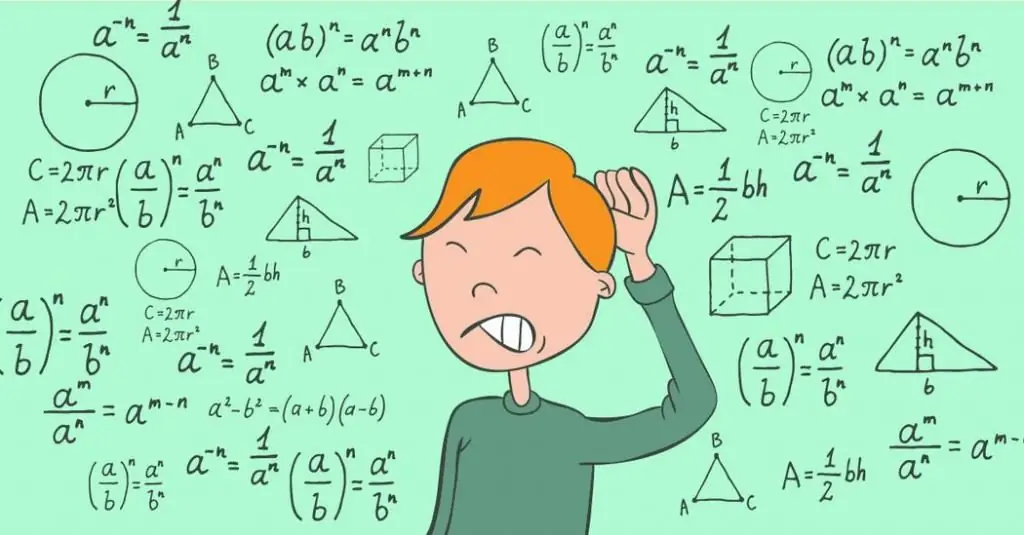
When a person invests his own money in an income-generating object, he expects not only to receive profit from the invested capital, but also to fully repay it. This can be done through resale or by obtaining such profits that not only bring interest, but also gradually return investments
The difference between a commercial organization and a non-profit organization: legal forms, characteristics, main goals of activity
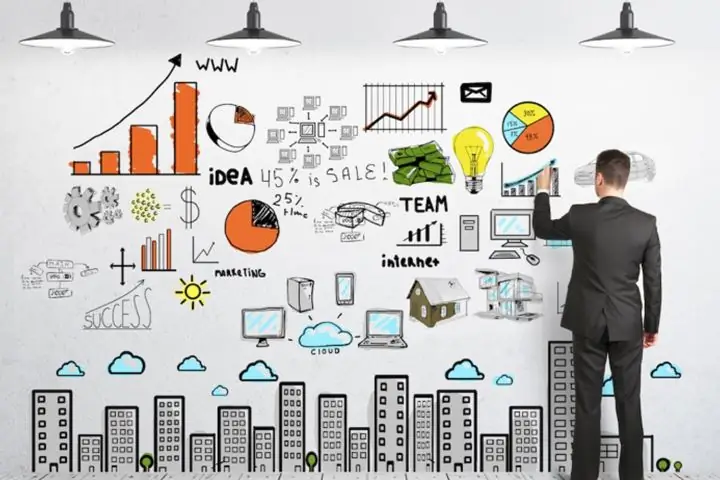
The main difference between commercial organizations and non-profit organizations is the following: the former work for profit, while the latter set themselves certain social goals. In a non-profit organization, profits must go in the direction of the purpose for which the organization was created
Material flow in logistics: overview, characteristics, types and schemes
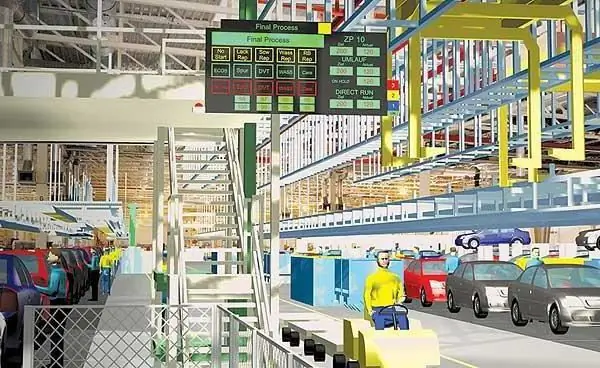
Types and classifications of material flows. Basic principles of their organization and management. Characteristics of material flows and their analysis
Regulations on the document flow of the organization. An example of workflow in an organization
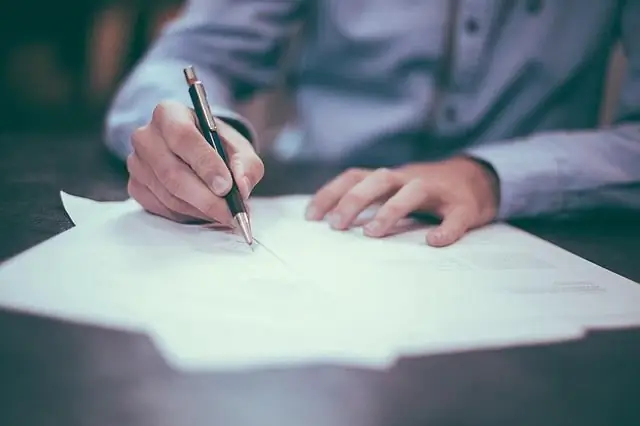
Documents are the pulse of an organization, and workflow is the life of an organization. The processes and logic of the movement of information in written and electronic form determine the level of development of the organization, its production, socio-economic achievements and position in society. Ultimately, this is an increase in profits and well-being of employees