2025 Author: Howard Calhoun | [email protected]. Last modified: 2025-01-24 13:10
Welding operations with metals are mostly based on chemical-thermal melting processes. Depending on the tooling used, active consumables and, in general, the technical conditions for organizing the process, the characteristics of the resulting product also change. The main task of the welder is to form a strong seam that can withstand the loads that will also fall on the main structure. In this regard, electroslag welding is not the best solution today, since the classic electric arc effect allows you to form seams that are more profitable for further operation. However, the use of slag baths for the melt process provides many other advantages for which large enterprises use this technology.
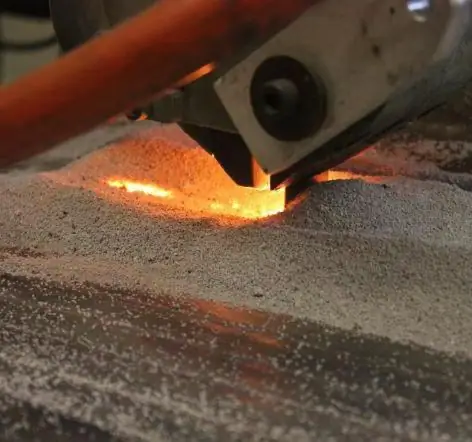
Essence of electroslag welding
The electroslag welding technique is based on the application of heat that is generated in the process of melting the material. The resulting thermal energy is the very factor that ensures the welding operation. The slag base is used as the material to be melted. The causative agent of the melt process is an electric current, thereforea special generator is used in the organization of the process. The peculiarities of the process include the fact that electroslag welding can be performed only under conditions of vertical placement of workpieces. Under the action of the generated heat, the liquid metal, which is formed during the melting of the electrode wires and the elements to be welded, fills the space between the parts. To keep the liquid bath of slag and metal from overflowing, sliders cooled by water are installed on different sides of the working bath. As the seam is welded, they rise and do not allow the working mass to flow out.
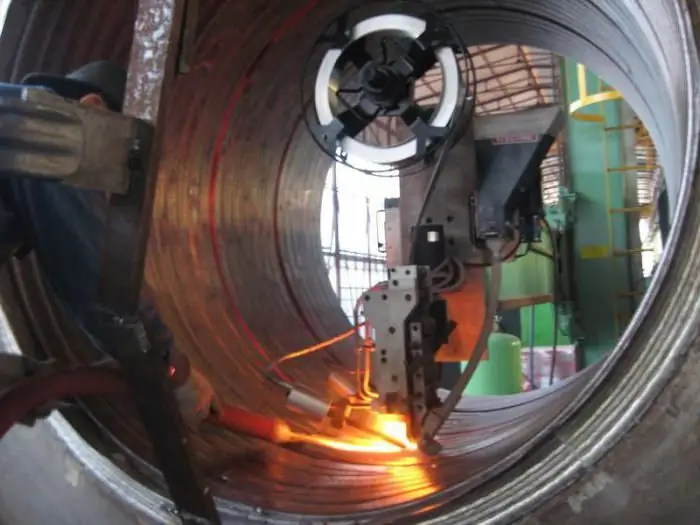
Technological process
The welding process begins with the excitation of an arc that will form between the parts and the electrode wires. The thermal energy of the arc melts the flux, after which the very slag pool is created, the level of which will rise. Due to the property of electrical conductivity, the fused flux begins to shunt the arc, stopping it from burning. In this case, the melting and heating of the flux continues due to the thermal effect, the source of which will be the current supplied to the liquid slag. That is, the technology of electroslag welding is based on the transfer of heat from slag, which not only releases energy under the influence of current, but can also directly transfer it to working parts.
The electrode and the target metal are connected to each other precisely through the slag bath. Next, a metal bath is formed. This may take different periods of time, depending onmaterial characteristics. The main point is that the metallic liquid base lies below the slag pool, but also requires the inclusion of mold sliders to contain leakage. To do this, use copper sliders cooled by water.
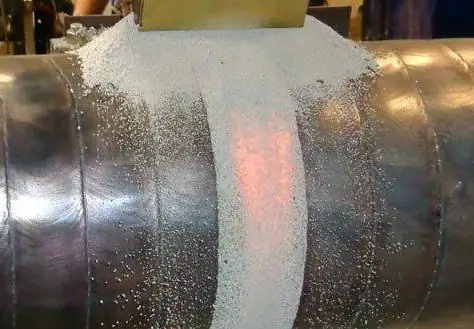
Varieties of welding
Approaches to this method differ according to the type of electrode used. For example, the classical scheme involves the use of electrode wire, which, as it melts, is fed into the slag bath. With this approach, the master must also impart reciprocating horizontal movements to the electrodes, which ensures uniform heating of the parts to be welded throughout the entire thickness.
Another method involves the use of electrodes with a large cross section or plates. In this case, the electrode will occupy most of the space formed by the gap between the workpieces. The use of plates is also common. With such a scheme, electroslag welding is performed with the expectation of dimensional correspondence of the active elements to the details. In any case, their shape should be similar to the workpieces being welded. The plates are fixedly fixed in the gap and, depending on the state of the slag bath, can be fed to the work area as the operation is performed.
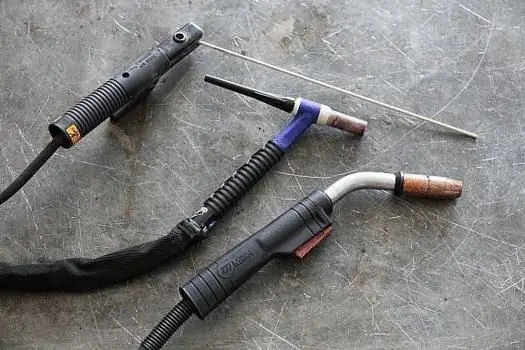
Welding equipment
As with traditional electric arc verification, in this case a special apparatus is used. To determine its features, it should be noted that the electroslagThe technique, unlike other common welding technologies, can be implemented at a current density of 0.1 A/mm2, which is hundreds of times less than with the same arc method. To accomplish this task, automata that meet several conditions are used. First of all, the technique must provide a gap between the different edges of the bath. The second condition is expressed in the fact that the equipment for electroslag welding must allow the vertical formation of the welded seam. And the last significant condition is that welding must be performed in one approach. Wire feed rollers, current-carrying mouthpiece, sliders with slats and water-cooling tubes are also available as accessories.
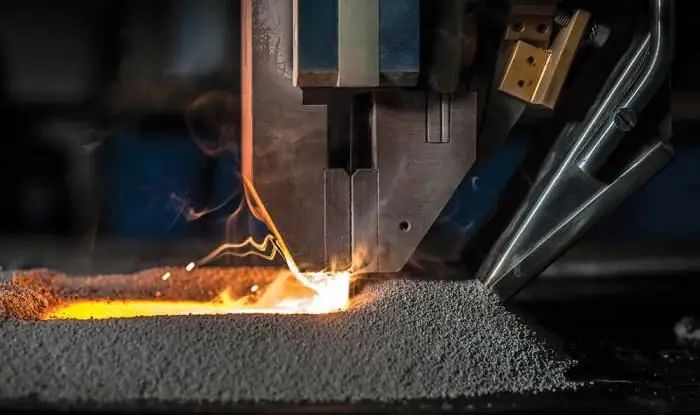
Welding consumables
The active basis for such welding is the mentioned electrodes, which can have several fixed axes. The feed to the slag bath is provided at a constant speed. In addition to slag and electrodes, a consumable mouthpiece can also be used. Depending on the requirements for the result obtained, the operator can control the consumables in such a way that the process will be carried out with varying degrees of intensity - a correction for manipulations with the same electrodes in order to increase heating is also made taking into account the type of metal. In general, from the point of view of complexity for the master, the most difficult process is electroslag welding with the contact principle of action. Usually, the contact-slag technique is used in cases where it is necessary to weldrods to a flat surface.
Advantages of Technology
One of the main advantages of the method is the possibility of welding without the need for preliminary separation of the edges, since the process is implemented with a gap between the working parts of up to 3 cm. savings on the organization of the event. The benefits will be felt even after the operation is completed. The fact is that welding of this type provides a symmetrical arrangement of the seam with respect to the axis. This factor eliminates the formation of angular deformations, which ultimately simplifies the installation of parts with their adjustment.
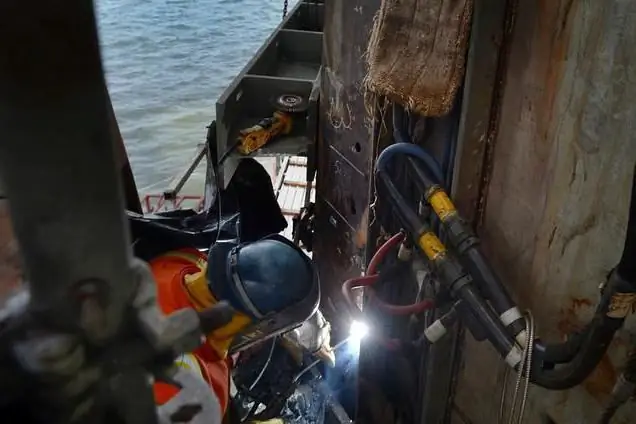
Application areas
The possibilities of using this technique are determined precisely by its shortcomings. This method is not practical for most typical welding applications. Most often, the technology is used in construction and industrial environments. For example, the manufacture of massive frames, the installation of turbine equipment, the installation of thick-walled drums and boiler units are just some of the common operations in which electroslag welding is used. The use of this method in production allows the assembly of large-sized structures. The fundamental difference between electroslag technology and other methods of reducing metal elements is the assumption of the possibility of replacing forged or cast massive parts with welded counterparts made from small castings orforgings.
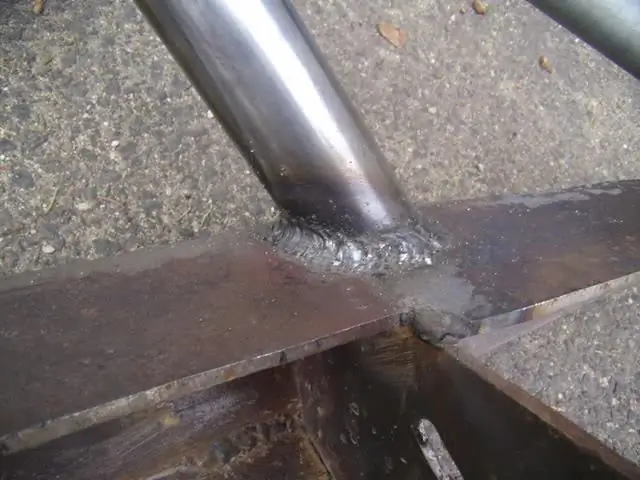
Conclusion
For a variety of reasons, even in the target areas of this technology, its application is not always allowed. The limitations are mainly related to technological shortcomings that make the use of the method impractical. For example, electroslag welding will be inefficient if it is planned to be used on a site where materials that are sensitive to thermal effects are also present. That is, for economic reasons and the quality of the resulting joint, the technology justifies itself, but another nuance arises. Such welding is characterized by a large zone of thermal influence, respectively, in work with a stationary arrangement of parts, all materials adjacent to them will also be subjected to strong temperature effects.
Recommended:
The main consumable for welding - welding wire
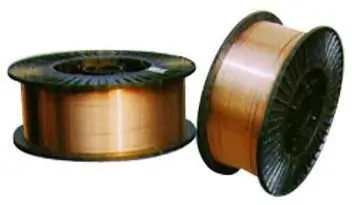
Welding wire is used in various welding operations, it is the main consumable material that acts as an electrode. Welding operations require extensive professional knowledge, a responsible approach to the choice of raw materials. For welding structures, it is unacceptable to use random wire of incomprehensible marking and unknown composition
Welding of ultrasonic plastics, plastics, metals, polymeric materials, aluminum profiles. Ultrasonic welding: technology, harmful factors
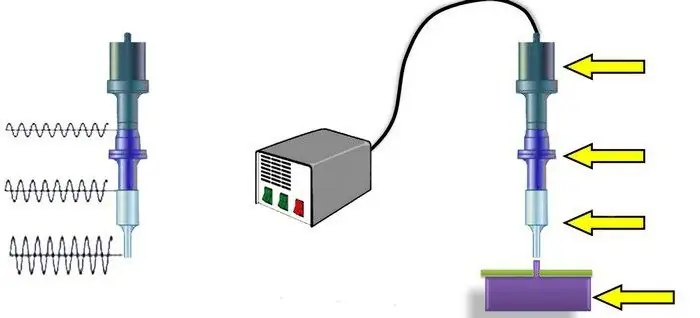
Ultrasonic welding of metals is a process during which a permanent joint is obtained in the solid phase. The formation of juvenile areas (in which bonds are formed) and the contact between them occur under the influence of a special tool
Thermite welding: technology. The practice of thermite welding in everyday life and in the electrical industry
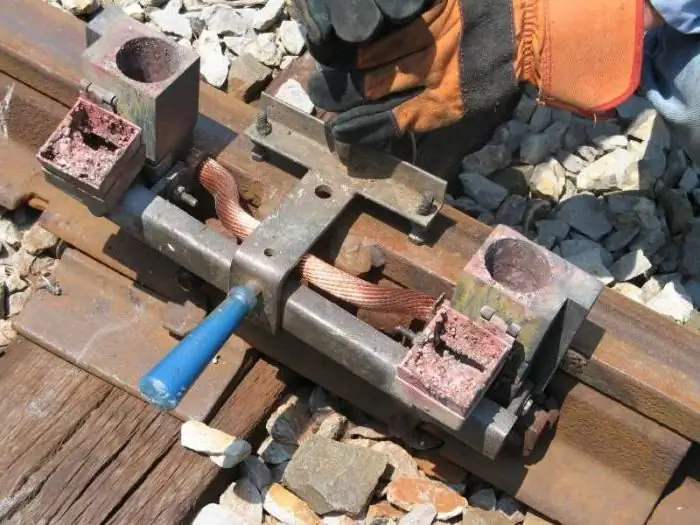
The article is devoted to thermite welding technology. The features of this method, the equipment used, the nuances of use, etc. are considered
Flux for welding: purpose, types of welding, flux composition, rules of use, GOST requirements, pros and cons of application
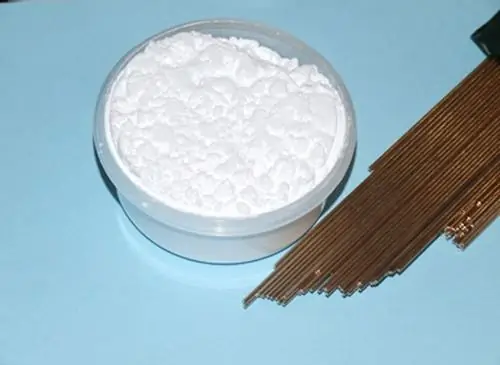
The quality of the weld is determined not only by the ability of the master to organize the arc correctly, but also by the special protection of the working area from external influences. The main enemy on the way to creating a strong and durable metal connection is the natural air environment. The weld is isolated from oxygen by a flux for welding, but this is not only its task
Sweet varieties of tomatoes: reviews. Sweet varieties of tomatoes for greenhouses
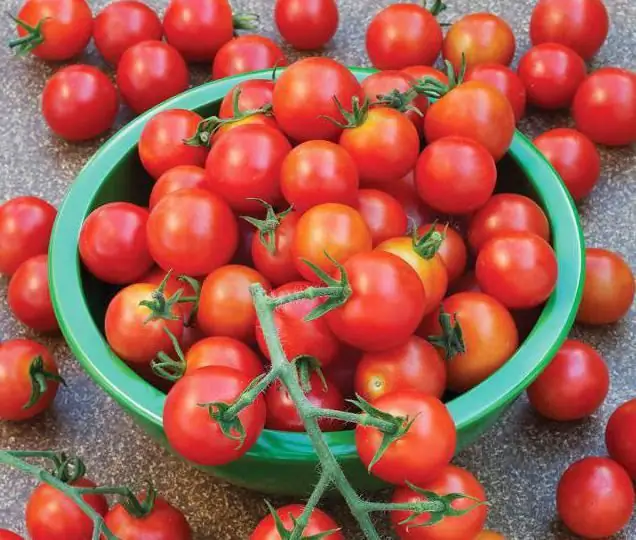
Gardeners plant various vegetables. Sweet varieties of tomato are considered one of the most sought-after varieties, as they are ideal for different occasions. More about them will be discussed in the article