2025 Author: Howard Calhoun | [email protected]. Last modified: 2025-01-24 13:10
Production of welding operations, regardless of the technology used, is associated with the need for a rather troublesome organization of the workflow. The master must prepare equipment, supplies, and also take care of safety. At the same time, it is necessary to take into account the cost of the event, since the financial support of such operations on a regular basis does not always justify the quality of the result obtained. In this regard, one of the most profitable is thermite welding, which is easy to perform, the availability of materials and, in some cases, allows you to achieve high strength joints.
Technology Features
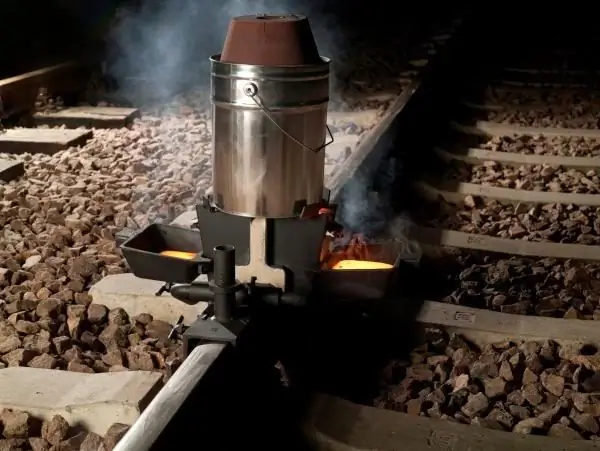
Thermite welding process is characterized by the use of special powder mixtures, which release a large amount of heat during combustion. As a rule, these are metal mixtures, which are called thermites. The traditional combination involves the use of two components - an igniting mass and a composition from which heat is released. Iron scale acts as an oxide, and thermite containing magnesium with aluminum is the main activator. In addition, technologyThermite welding allows the use of oxides of chromium, tungsten and nickel. Thanks to these powders, an increase in thermal effects is achieved. So, if a mixture of aluminum and magnesium provides heat of the order of 2500 ° C, then chrome compounds increase the temperature to 3500 ° C. The mixtures for the fuse also differ. The most common formulation for this task is a combination of magnesium, sodium, and barium peroxide. The peculiarities of burning thermite include the maintenance of active heat release even in contact with water. In other words, the mixture is almost impossible to extinguish by accidental exposure.
Varieties of thermite welding
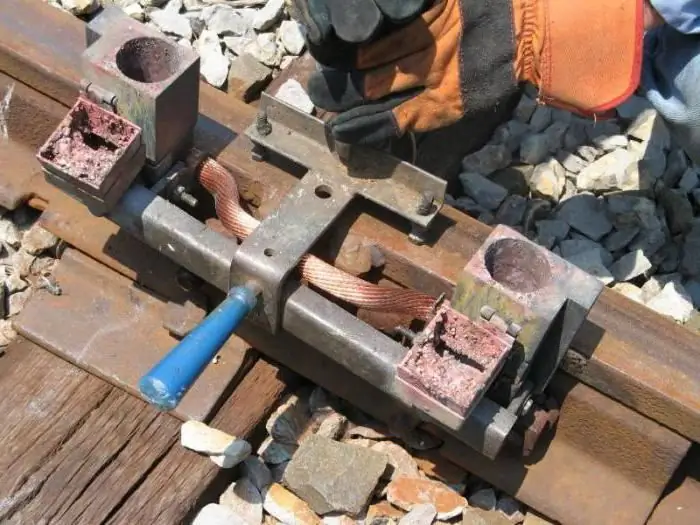
There are four main techniques for performing such welding - by intermediate casting, combined, butt and duplex. During the operation of intermediate casting, the powder mixture passes into the state of liquid metal, and this does not affect the initial characteristics of the thermite active substance. Typically, this technique is used for the installation of metal structures that are pre-attached in the desired position. Especially for work with lamellar products, cathode and drainage outlets, butt thermite welding is used, the mixture for which is pre-fired in a furnace. Combined technique involves a combination of the injection method and butt welding. That is, the master can perform the main work using liquid welding, and refine the edges using delicate butt welding. As for duplex, this methodprovides for the introduction of an additional stage, during which the melted gap of the structure is pressed.
Applied equipment
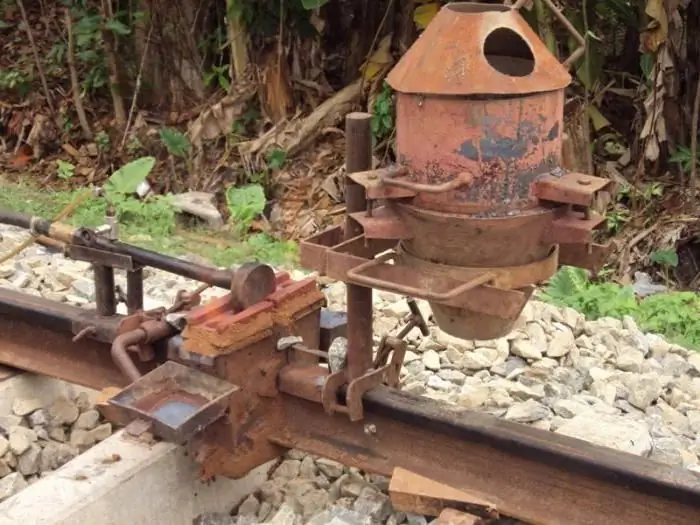
The basis of the equipment is a crucible, which provides the ability to work with termites, including draining and molten metal mass. This element can be made of ceramic or tungsten, depending on the requirements for temperature conditions. Casting molds are prepared separately. Special matrices allow you to work with a wide range of molten base. You should also prepare equipment for thermite welding in the form of clamping and fixing devices for massive structures, a special cutter and a technical pencil designed specifically for this type of operation. A special inverter torch and a thermometer may be required depending on the conditions of the work and the requirements for the result.
The practice of organizing work at home
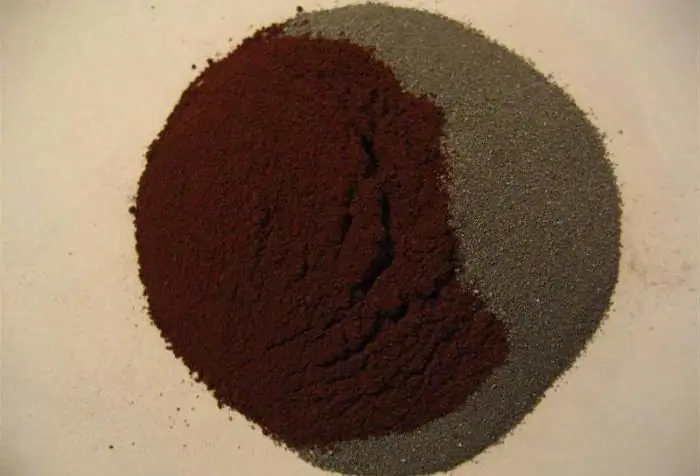
In the household, this type of welding saves those who cannot properly implement the electric arc method or fusion gas connection. Typically, in such cases, thermite is used with a minimum temperature of about 1300 ° C. This mode allows you to provide the simplest aluminum composition, due to which you can repair small cracks in a metal structure, carry out car mechanic operations or weld building reinforcement. Typically, thermite weldingat home is performed without special inverters. A thermite pencil will act as a working tool, with skillful handling of which you can achieve a strong connection.
Industrial Operations Practice
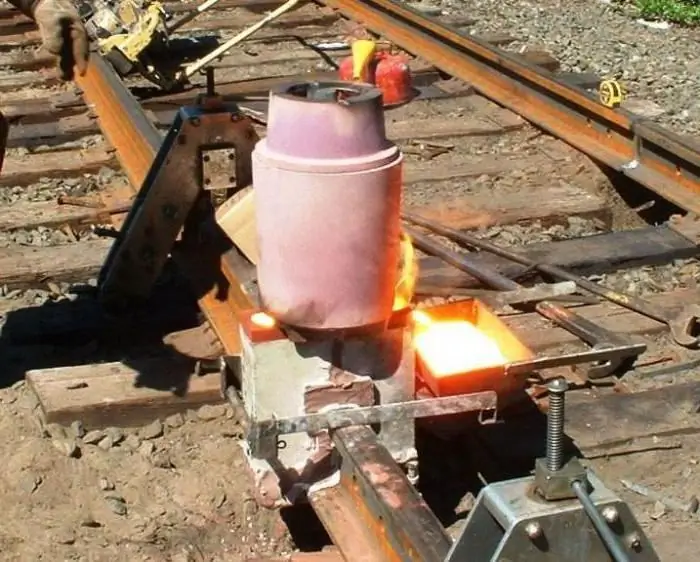
The industrial organization of the welding process using thermite mixtures has many significant differences. First of all, more efficient metal compositions with increased heat release are used. These are the same thermites with the inclusion of chromium, tungsten and other elements with an active combustion function. For the technical organization of the process, it is also necessary to use more powerful equipment, that is, specialists are not limited to one thermite pencil. For example, thermite welding in the electrical industry necessarily involves the use of inverters, thermostats and other equipment that allows you to track the parameters of the work process. The third distinguishing feature of welding in industrial sectors is the preparation of special holding equipment. Uses refractory molds to fill gaps, high-strength crucibles, holders and fixtures for various designs.
Features of wire welding
Thermite welding technology is optimal for working with electrical wiring. Moreover, this approach can be used both in industry and in everyday life. In the process of carrying out the work, an all-metal connection of the wiring ends is formed. It is important to note that in the place of thickeningwires in the welding area, the electrical resistance decreases relative to the rest of the material. For welding itself, a special thermite cartridge is used. In particular, it is used for thermite welding of wires made of aluminum and steel-aluminum. There are also special cartridges for working with copper wiring - they are made of mold.
Welding Safety
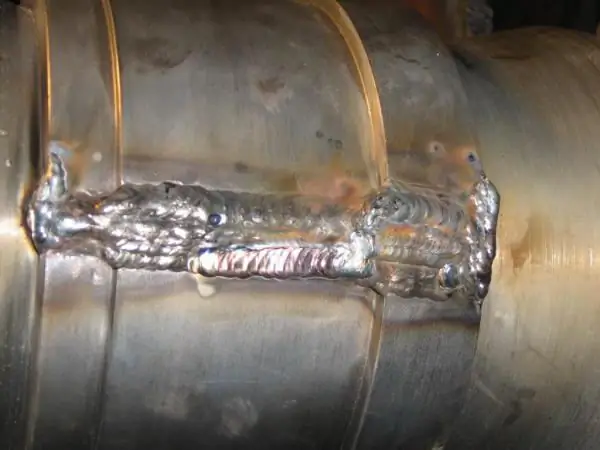
With all the simplicity of this welding method, it is precisely because of the specific chemical properties of thermite mixtures that quite strict safety rules are determined. First, there are special requirements for the storage of metal powders. It should be stored only in dry and heated rooms. Moreover, thermite welding does not allow the use of wet powders directly in the ignition process. Secondly, there are special requirements for the conditions of welding. The operation can only be performed at temperatures above 10 °C. Connections must be pre-cleaned and degreased.
Pros and cons of thermite welding
The advantages include the availability of materials, the ease of performing most operations and low energy consumption during the work process. In other words, this option is suitable for large-scale welding of massive building structures, and for minor household operations. As for the disadvantages, thermite welding brings a lot of difficulties in working with seamless joints. A businessin that directly during the operation, the master cannot fully monitor the quality of the formation of the gap and connection. As a result, in most cases it is not necessary to count on an even and clean reduction of parts of structures without significant deformations. But in terms of strength and durability, thermite compounds are considered one of the best.
Conclusion
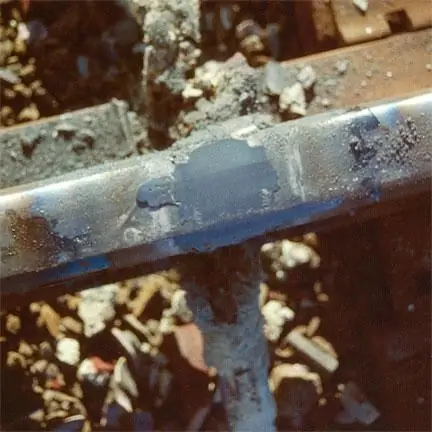
Manufacturers of welding equipment mainly improve cutting equipment, giving high performance to the thermal impact tool. This approach to the development of devices justifies itself, but the operation of equipment with increased power naturally requires large investments in energy supply. As the practice of thermite welding in everyday life shows, the use of metal powder mixtures based on aluminum and magnesium in terms of cutting force gives the same effect as alternative methods. Another thing is that the maintenance of these same mixtures also requires considerable trouble and expense. But these inconveniences are compensated by the versatility of the technology. The presence in the economy of a full range of metal powders from aluminum to tungsten will allow you to create a variety of mixtures suitable for joining railway sleepers and for fine work with wires.
Recommended:
Life and he alth insurance. Voluntary life and he alth insurance. Compulsory life and he alth insurance
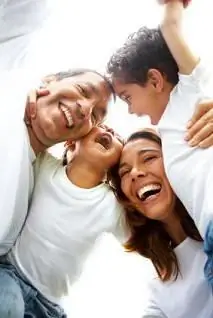
To insure the life and he alth of citizens of the Russian Federation, the state allocates multi-billion sums. But far from all of this money is being used for its intended purpose. This is due to the fact that people are not aware of their rights in financial, pension and insurance matters
Thermal battery: types and use in everyday life
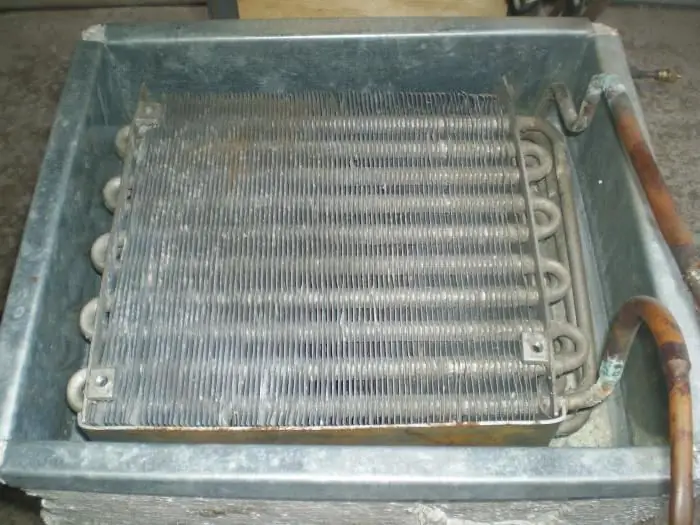
The heat accumulator has become an indispensable device for many modern heating systems. With this addition, it is possible to ensure the accumulation of excess energy generated in the boiler and usually wasted. If we consider the models of heat accumulators, then most of them look like a steel tank, which has several upper and lower nozzles. The heat source is connected to the latter, while the consumers are connected to the former
Clothing industry as a branch of light industry. Technologies, equipment and raw materials for the clothing industry
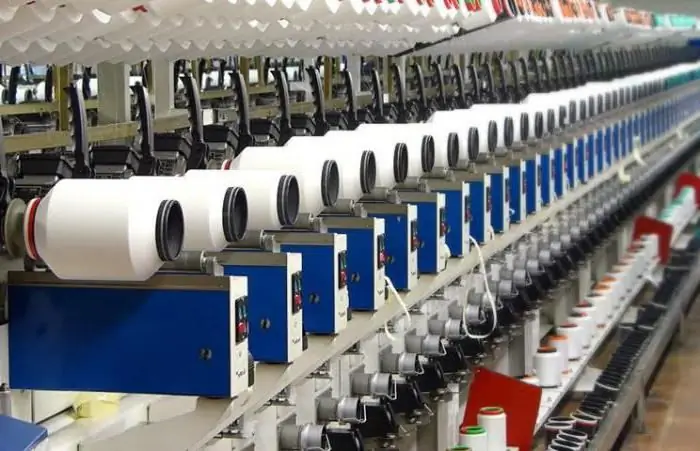
The article is devoted to the clothing industry. The technologies used in this industry, equipment, raw materials, etc. are considered
Dairy industry in Russia. Dairy industry enterprises: development and problems. Dairy and meat industry
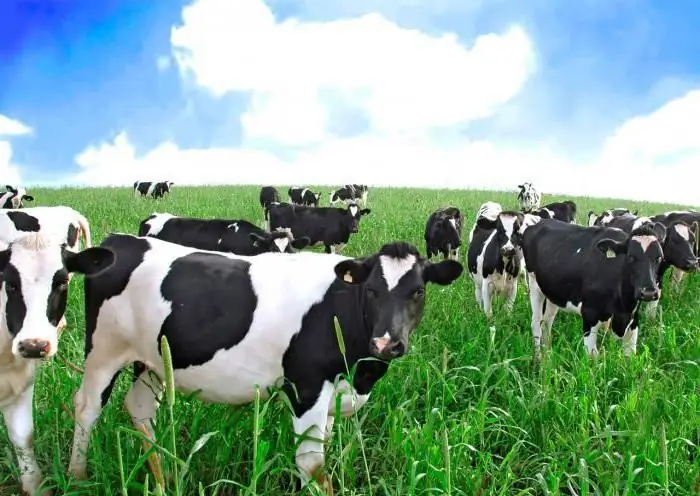
In the economy of any state, the role of the food industry is huge. Currently, there are about 25 thousand enterprises in this industry in our country. The share of the food industry in the volume of Russian production is more than 10%. The dairy industry is one of its branches
Polypropylene - what is it? Definition, technical characteristics of the material, application in industry and everyday life
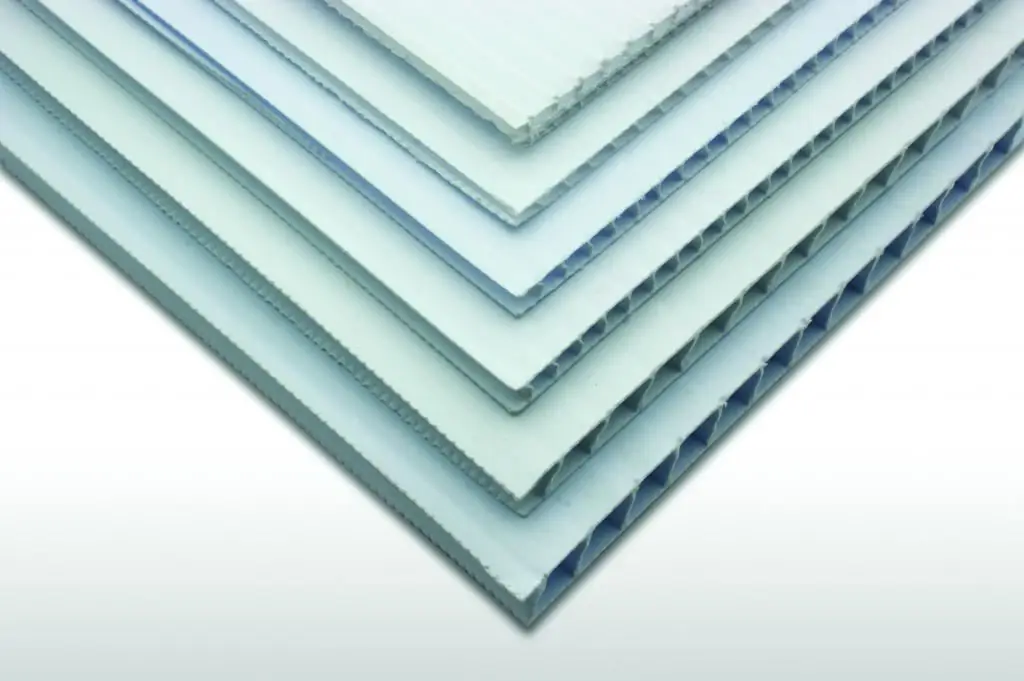
You can build a heating system with your own hands from polypropylene. The material is affordable and lightweight. Before starting work, it is necessary to designate the connection points and understand the installation method. For soldering pipes, products must be cut to size. The joints must be even and have a right angle. Sections are degreased, chips are removed from the surface after cutting