2025 Author: Howard Calhoun | [email protected]. Last modified: 2025-01-24 13:10
Due to the advent of affordable electronic and insulating components in modern production, the field of application of induction heating is becoming ever wider. This technology is used not only in metallurgy, but also in the development of household appliances.
Principle of induction heating
The operation of the induction furnace is based on the transformer principle of energy exchange. The inductor is made of a copper tube, which is then twisted into a multi-turn coil. An alternating current is supplied to the primary circuit of the inductor, which leads to the formation of an alternating magnetic field around it. Under the influence of a magnetic field in the body placed inside the inductor, an electric field arises, which subsequently leads to the heating process. The power and, accordingly, the heat generated by the induction crucible melting furnace are directly dependent on the frequency of the alternating magnetic field. Therefore, the furnace needs high frequency currents to operate effectively.
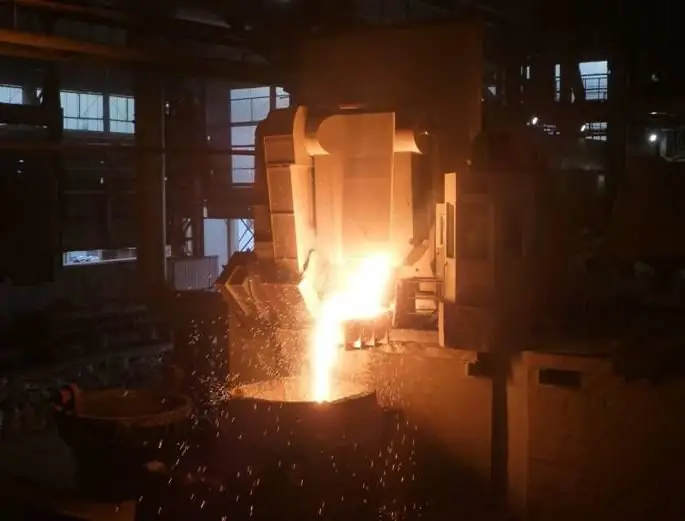
Application of induction furnaces
Inductionheating can be used to work with any material: metal, slag, gas, etc. The main advantage of its use is non-contact heat transfer. Also, induction heating allows you to achieve almost any heating rate - it all depends on the power of the generator that feeds the furnace. Heat losses during such heating are minimal. The maximum temperature to which an object can be heated in a furnace is limited only by the resistance of the refractory material. The process of non-contact heat transfer to the heated material makes it possible to produce heating in a vacuum environment.
According to the reviews of metallurgists, the scope of induction furnaces is somewhat limited due to the existing shortcomings. The disadvantages of the crucible furnace include:
- high price of electrical equipment;
- cold slags complicating the refining process;
- Reduced lining stability during temperature spikes between melts.
Scheme of crucible induction furnace
Induction crucible furnace has the following structure.
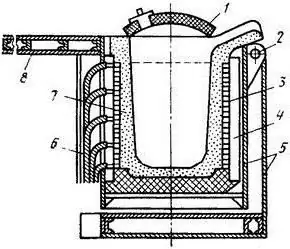
The main element of the furnace is the crucible (7), covered with a lid (1). The crucible is located inside the heating inductor (3), made in the form of a multi-turn coil. The coil is a copper tube, inside which, for the purpose of cooling, water constantly circulates. The magnetic flux from the inductor passes through the magnetic circuits (4), which are made of special transformer steel. The swivel assembly (2) is provided for tilting the oven during bottlingmolten liquid. The furnace is installed on a mello structure (5). Cooling is done with water cooling hoses (6). An auxiliary platform (8) is used to service the oven.
Also, the scheme of the crucible furnace includes a transformer, capacitors, a control unit and a gas pumping system. The crucible electric furnace is powered by currents with a frequency of 50 Hz.
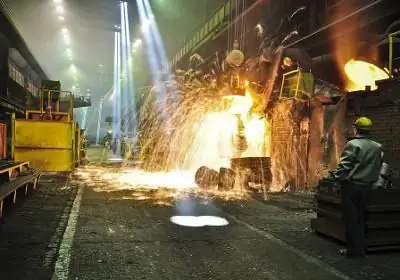
Features of internal structural elements
Most often the inductor is made from a round tube. But there are situations in which a round copper tube is not applicable. In certain cases, profiled elements are used to design an induction crucible furnace, due to which the leakage magnetic flux is reduced. The inductor tubes are isolated from each other with fiberglass impregnated with a special varnish. Protected turns are compressed by blocks made of dielectric material. The inductor and the crucible, placed inside the coil, are installed on a pallet made of refractory bricks or heat-resistant concrete. Under industrial conditions, the crucible manufacturing process takes place directly in the furnace. In this case, the inductor in the assembled state is installed on a pallet and insulated with asbestos. After that, the pallet is filled with refractory powder, which is compacted using a pneumatic unit. The gap between the template mounted on the bottom and the inductor is filled with refractory powders.
The lining of the zone above the inductor is provided by refractory bricks. Collar and drain chute are also linedrefractory brick. The work of the induction crucible furnace takes place in the most difficult conditions, therefore, increased requirements are imposed on the quality of the heat-resistant materials used. The durability of the lining is affected by the composition of the refractory mass, the mode of operation and the applied frequency of the electric current. As a rule, the crucible withstands up to 100 melts, and then fails.

Design of exterior elements
The frame of the melting crucible furnace is the base to which all its elements are attached. On large industrial devices, the frame has the form of a solid casing. All parts of the frame must have high strength, due to the influence of the electromagnetic field of the inductor on them. The shell under certain conditions can be heated in the same way as the material in the furnace. To reduce heating, it is rational to make the frame from non-conductive materials. However, since dielectric materials are expensive, the frame material is usually steel. The steel structure is divided into several elements, which, in turn, are isolated from each other. Screens are used to reduce the electromagnetic field near the frame. A protective screen is installed between the inductor and the furnace body. The screen is cylindrical and made of aluminum or copper.
The swivel is an important design element. The main requirement for the turning mechanism is to provide an inclination for complete draining of the metal. Rotation mechanisms can be used different. Small ovens use manual or electricwinch. Industrial furnaces are tilted using a beam crane. Large capacity ovens can be equipped with a hydraulic tilt drive.
The lid, which covers the crucible melting furnace, serves to maintain the temperature inside the unit at a higher level. However, considering that it is possible to cover the furnace only after the charge is completely melted, the use of a cover is not mandatory.
Do-it-yourself oven making
Induction furnaces are widely used not only in industry, but also in everyday life. You can find schemes for a large number of home-made devices, but some of them, at best, simply will not work, and at worst, they will harm the he alth of their creator. Many fans warn about such consequences. In everyday life, the induction heating method is used in such devices:
- channel metal melting furnace;
- crucible induction furnace is the simplest to design, and therefore the most popular among enthusiasts, judging by the reviews;
- water heating boiler based on induction method;
- induction hobs that compete with popular gas stoves.
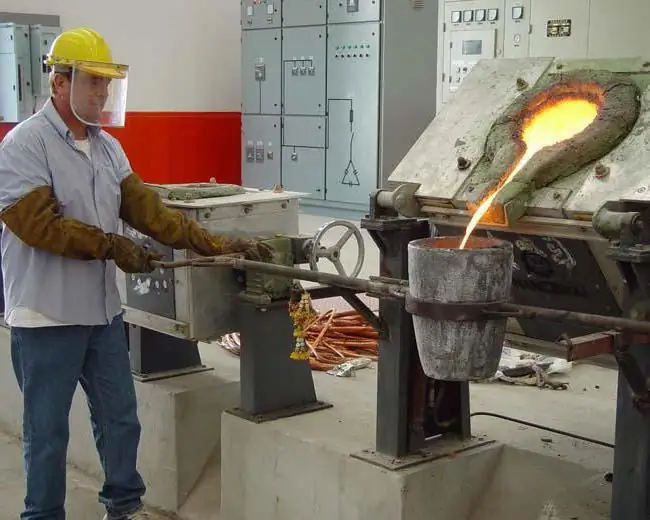
Duct oven
This type of furnace is used for producing high quality cast iron, as well as for melting duralumin and non-ferrous special alloys. A duct furnace with a power of up to 3 kW is made independently from a welding transformer, the frequency of which corresponds to the industrial one. This oven meltsa blank of bronze or copper weighing up to half a kilogram. The channel furnace also allows the duralumin to be remelted, but it must be taken into account that the “aging” process must follow the melting. The time of this process can be up to 2 weeks and depends on the composition of the alloy.
For the manufacture of the furnace, the primary winding of the welding transformer is left unchanged, and a ring-type crucible is placed in place of the secondary winding. The best material for the crucible of a small channel furnace is electroporcelain. Other options will not work due to low strength and dielectric losses. According to amateur metallurgists, the problem is that it is not possible to process electroporcelain on your own, and it is very unlikely to find a suitable element for sale. It is precisely because of the scarce crucible that the channel furnace has not found wide application among enthusiasts, although this type of furnace has an efficiency of more than 90%.
Crucible induction furnace
The self-made crucible furnace is used primarily in the purification of valuable metals. For example, having a radio connector made in the Soviet Union, you can extract a certain amount of gold from its contacts. Using external heating, this result cannot be achieved.
Besides gold mining, such a furnace is often used to evenly heat the metal, which is required for high-quality hardening. By changing the position of the part in the inductor and adjusting its power, it is possible to achieve the desired temperature in a specific area of the metal. It is important that the use of such a furnace will be quite budgetary, becausealmost all energy is directed to the process of heating the part.
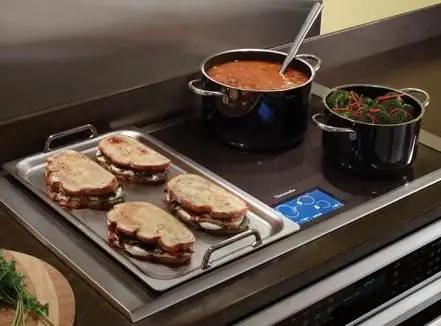
Induction boilers
Induction water heating boilers have every chance of replacing conventional boilers in the future. Users consider the high price to be a disadvantage of such a water heater, but at the same time, systematizing numerous reviews, several advantages can be distinguished:
- Reliability. The boiler does not have an electric coil, which is the weak link of a conventional boiler.
- Efficiency almost 100%.
- Safety. Electricity access to the boiler body is impossible due to the design features.
- The device does not need special grounding.
- Resistant to power surges.
- Does not scale.
- Durability. The boiler is able to work without maintenance for about 30 years.
Homemade hot water boiler
The basis of such a water heater is a power transformer with a power of up to 1.5 kW, the primary winding of which is designed for a voltage of 220 V. A transformer from a tube color TV is perfect. The secondary winding should be removed, and the number of turns of the primary should be increased.
Craftsmen advise and warn: the use of such a home-made device is unsafe, so the transformer should be grounded, and the device itself should be connected through a high-speed RCD.
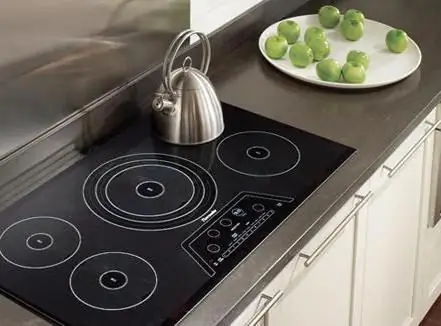
Inductor in the kitchen
Induction cooking hobs are no longercause surprise and are widely used in everyday life. The operation of the device is based on the same principles as that of an induction furnace, with the only difference that the secondary winding is the metal bottom of the cookware.
The use of such plates became possible due to the appearance in the production of a dielectric, which, in addition to fulfilling the task of isolating the inductor, must also have strength and hygienic characteristics. A material that satisfies all the requirements has appeared relatively recently, and its cost is a significant part of the total price of the plate.
Users unanimously claim: self-production of an induction cooker does not make sense for two reasons. First, cooking on such a hob requires fine tuning for each type of food. For the necessary adjustment of all electrical parameters during the cooking process, a microcontroller is required. The second reason is the price of the electronic parts that make up the stove. In total, all the elements will cost much more than the cost of an already finished device.
Induction cooker has the following positive qualities:
- lack, unlike microwave ovens, third-party radiation;
- the ability to program the stove to suit your cooking style;
- cooking dishes like caramel without overheating or burning;
- economy thanks to efficient use of heating energy.
Recommended:
Electric locomotive 2ES6: history of creation, description with photo, main characteristics, principle of operation, features of operation and repair
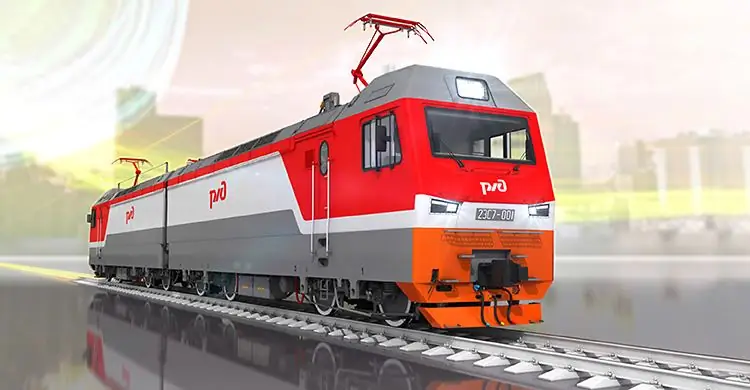
Today, communication between different cities, passenger transportation, delivery of goods is carried out in a variety of ways. One of these ways was the railroad. Electric locomotive 2ES6 is one of the types of transport that is currently actively used
Float level gauges: description, types, principle of operation and reviews
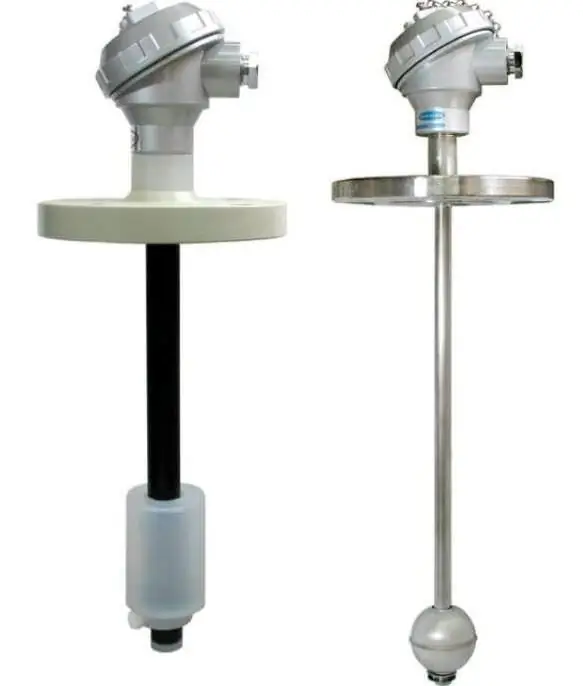
The article is devoted to float level gauges. The types of devices, the principle of operation, user reviews, etc. are considered
Low pressure heaters: definition, principle of operation, technical characteristics, classification, design, operation features, application in industry
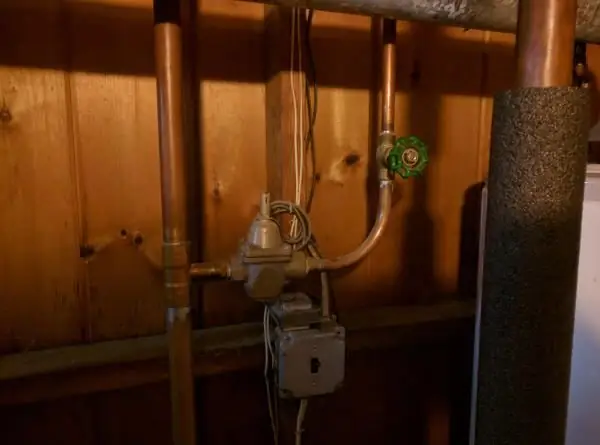
Low pressure heaters (LPH) are currently used quite actively. There are two main types that are produced by different assembly plants. Naturally, they also differ in their performance characteristics
Device, principle of operation and diagram of the rectifier diode bridge
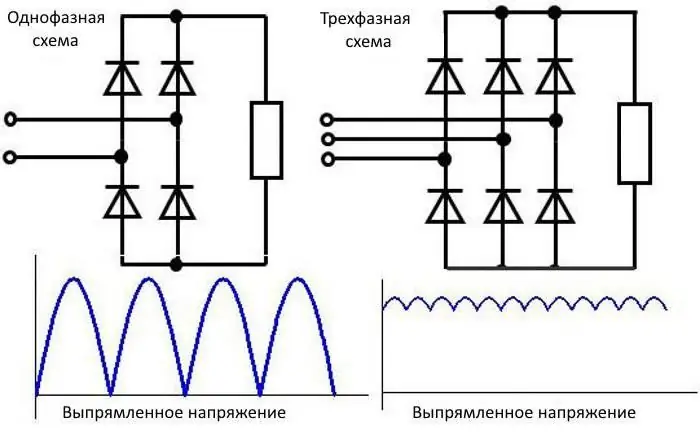
Alternating electric current is converted into a constant pulsating through the use of special electronic circuits - diode bridges. The rectifier diode bridge circuit is divided into 2 versions: single-phase and three-phase
Gas piston power plant: the principle of operation. Operation and maintenance of gas piston power plants
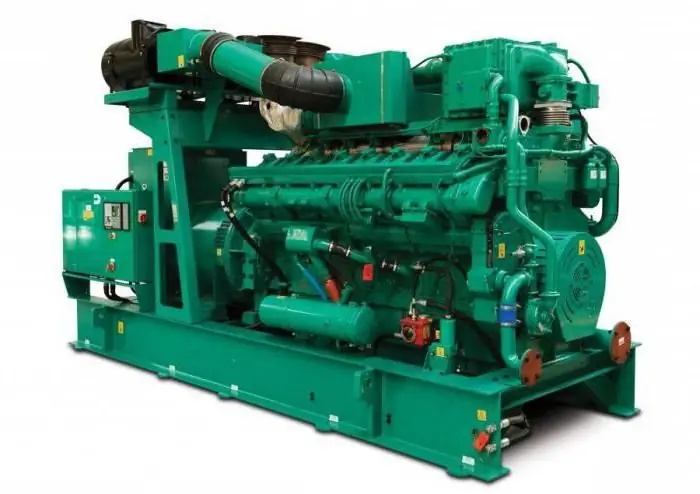
Gas piston power plant is used as a main or backup source of energy. The device requires access to any type of combustible gas to operate. Many GPES models can additionally generate heat for heating and cold for ventilation systems, warehouses, industrial facilities