2025 Author: Howard Calhoun | [email protected]. Last modified: 2025-01-24 13:10
Polymers synthesized from products of oil, gas and coal processing can be used, among other things, for the manufacture of a special type of material - synthetic fiber. Such products are used in the production of yarn used for the manufacture of fabrics for various purposes. Nylon and polyester are examples of common types of this material.
Recently, scientists have developed several new types of synthetic fibers. All of these varieties have excellent performance characteristics and can be used very widely. For example, one of the most popular types of such material at the moment is inexpensive polypropylene fiber.
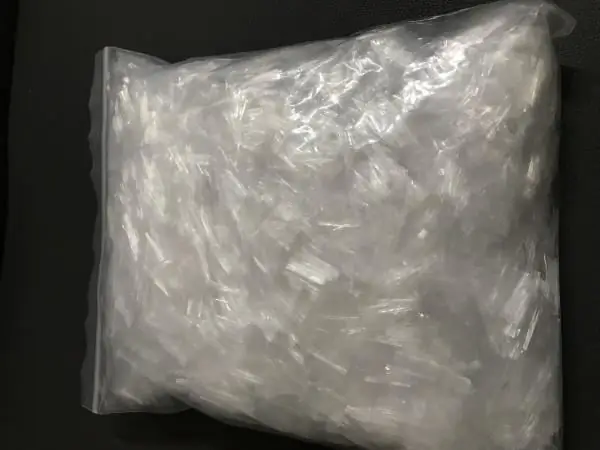
What is
This modern material belongs to the group of polyolefins - high-molecular hydrocarbons of the aliphatic series. This type of fiber is much more resistant to double bending and elastic than polyamide. The melting point of this material is 165 °C, ignition - 325-385 °C. Densitypolypropylene fiber is 900-910kg/m3.
What are the advantages and disadvantages
The advantages of this material, in addition to a sufficiently high degree of elasticity, include:
- resistance to acids, organic solvents, alkalis;
-
strength;
- excellent thermal insulation qualities.
The main disadvantage of polypropylene fiber is low light fastness. Under the influence of UV rays, such material begins to break down very quickly. Also, the disadvantage of synthetic fiber of this variety is not a very high degree of wear resistance. In addition, such material, unfortunately, does not lend itself well to surface staining.
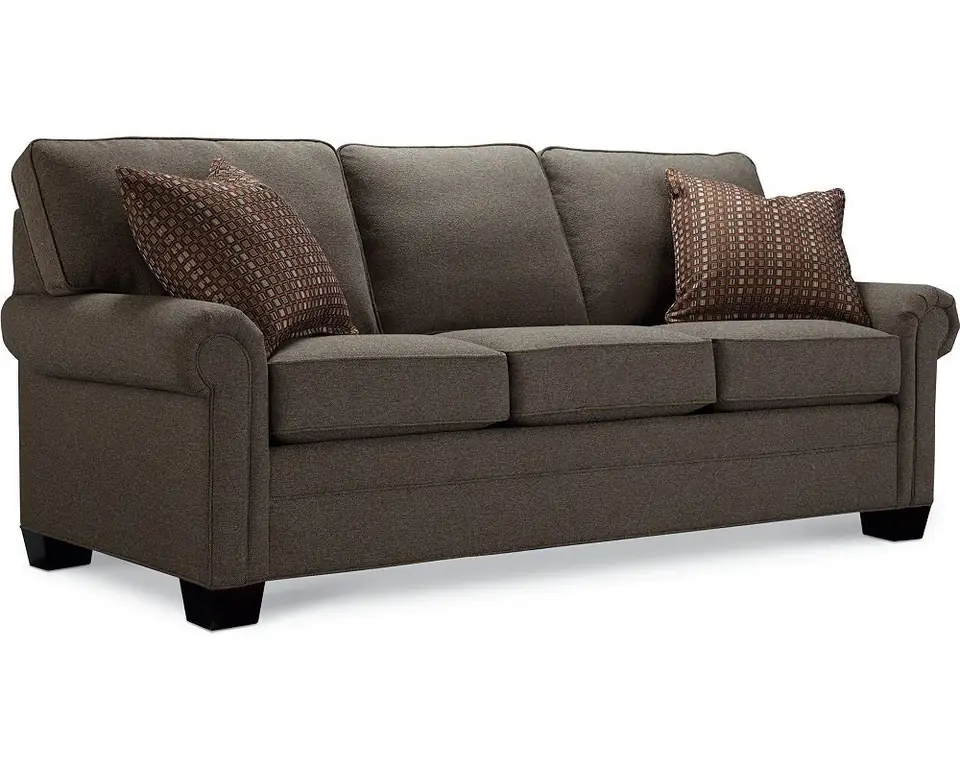
What is the composition of
This modern material is made, as its name suggests, from polypropylene. Also, special stabilizing substances can be added to the composition of such synthetic threads, designed to increase them:
- wear resistance;
- light fastness.
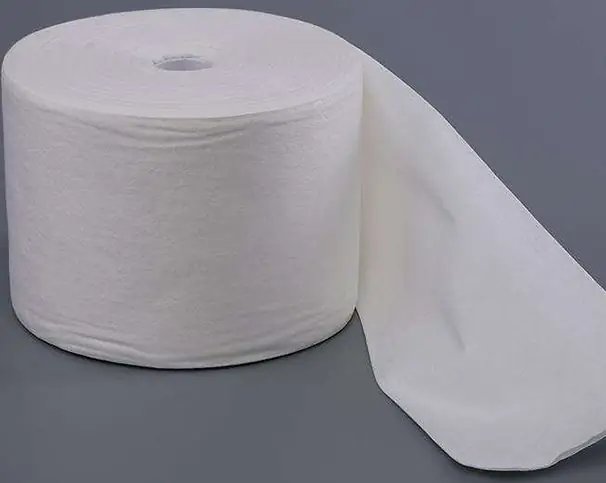
How it is made
Propylene is a cheap material, but very versatile in terms of physical and chemical properties. It is produced using rather complex structurally modern equipment. At the same time, there are two ways to stretch the polypropylene fiber itself:
- from solution;
- frommelt.
Made from mortar
This manufacturing method has a number of disadvantages. In industrial conditions, it is used, but quite rarely. Using this technique, the fibers are spun from concentrated solutions of propylene, which is known to be able to dissolve at high temperatures in many organic liquid formulations. It can be, for example, mineral oil or gasoline. When using this technology, a heated solution can be forced through a filter and narrow die holes by a special dosing pump:
- into the blower shaft towards the superheated steam;
- in a solution of butylene or propyl alcohol on any liquid.
In the latter case, thin polypropylene streams are blown with air before entering the liquid in an area of approximately 10 cm. In an alcohol mixture, they are freed from solvent residues.
When using the first manufacturing method, called dry, finished threads are first wound into bobbins. The material is then placed in washing baths with boiling water. This operation is also necessary to remove residual solvent.
Melt melt production
Using this production technique, polypropylene fiber is made on special spinning extrusion machines. The main design elements of such equipment are:
- screw extruder;
- spinning gear pump.
High viscosity polypropylene melt in suchthe machine is fed to the pump with the help of a worm, which allows to reduce its temperature. Next, the material is passed through a spinneret. The threads coming out of the last thread are evenly blown by the flow of a cooling agent (most often air with constant humidity and temperature).
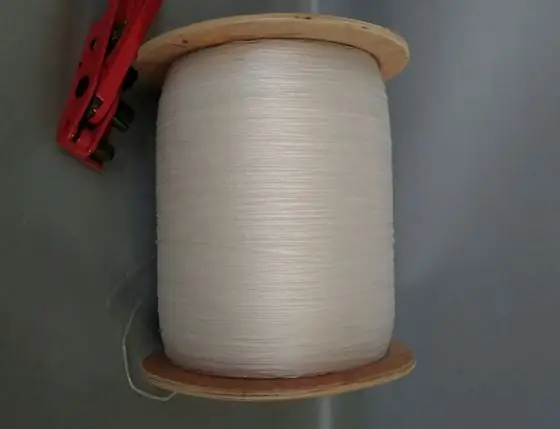
This method of manufacturing polypropylene fiber, in comparison with that described above, is primarily characterized by greater productivity. Therefore, it is he who is most often used when releasing such material.
Properties of polypropylene fiber
Among other things, the material of this variety has the following specifications:
- strength - 35-80 gs/tex;
- degree of elongation in wet and dry state (the indicator is the same) - 30-40%;
- density - 0.91 g/cm3;
- degree of frost resistance - up to -70 °С;
- hygroscopicity - 0.01-0.02%.
Products made from such material, in turn, have:
- lightweight;
- abrasion resistance;
- small rate of capillary rise of moisture;
- high speed drying.
The weight of the woven fabric of polypropylene fiber is so light that it does not sink in water. In terms of wear resistance, a fabric made from such threads, for example, is somewhat inferior to the same polyamide. But at the same time, it can still serve for a long time.
Among other things, materials made frompolypropylene fiber, are resistant to infection by fungus and microbes. Accordingly, they also have good hygienic properties. Polypropylene is also resistant to acids, alkalis and even aqua regia. Another indisputable advantage of fabrics made from this material is that they are not electrified and have dust and dirt-repellent properties.
Application of polypropylene fiber
30% of all polypropylene produced by modern industry is used today for the manufacture of fiber. This material is actually very popular. It can be used for production:
- durable fabrics;
- brushes (car) designed for street cleaning;
- shoes and bags;
- cement mortar;
- fishing nets;
- ropes, ropes, ribbons;
- carpet backings and bags.
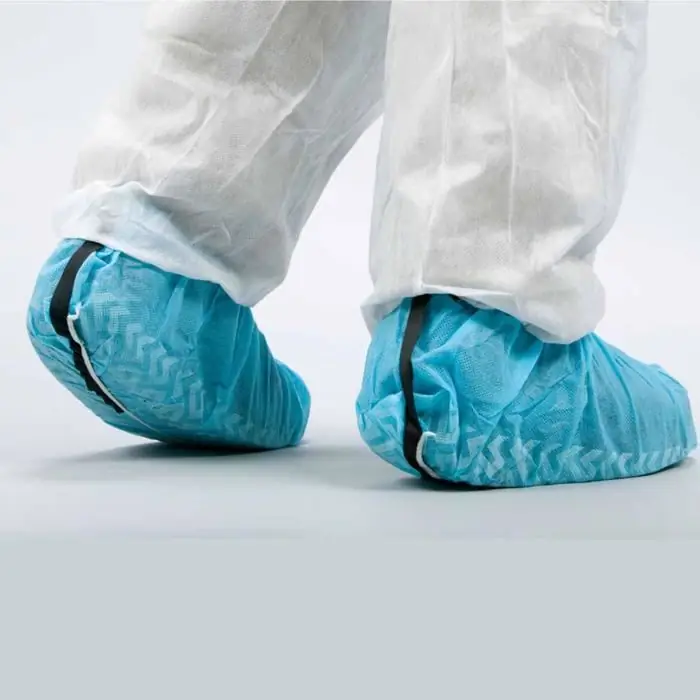
Clothes from this material, since it is difficult to dye and does not absorb moisture well, are rarely made. Basically, such threads are used for the production of technical fabrics. In addition to substrates, polypropylene fiber can be used to make:
- decorative fabric for furniture upholstery;
- finishing fabrics;
- surgical sutures and tissue;
- filter fabrics.
Polypropylene fiber car brushes costmore expensive than those made from bristles. But at the same time they are 10-20 times more durable. The strength of polypropylene bristles is 5 times higher than that of a fairly common polystyrene bristle. It is very rare to change brushes made with it.
Where else can it be used
In construction, polypropylene fiber is quite often used in the preparation of cement. Its use in this case makes it possible to achieve a uniform distribution of stresses over the entire mass of the material.
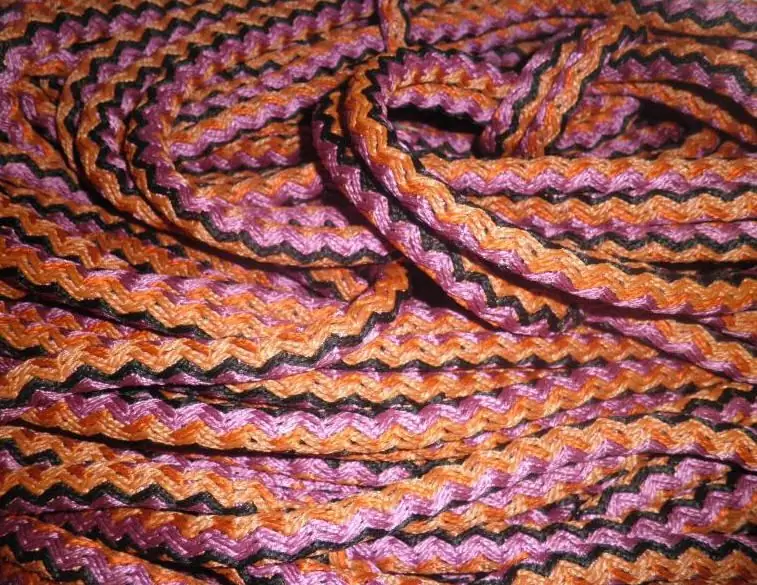
This material can also be used for the manufacture of fillers. Synthetic cotton is spun from polypropylene fiber. In the future, it is used for stuffing upholstered furniture. Also, a filler made of rigid thick polypropylene fibers is often used for the manufacture of knife stands. In this case, the thick "bristles" are simply inserted into a tall, narrow plastic box. Polypropylene fibers in these stands easily hold knives upright.
Recommended:
Zirconium alloys: composition, properties, application
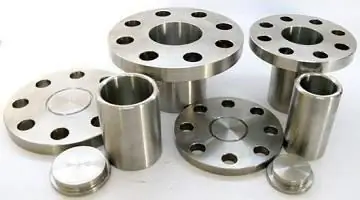
Currently, a material such as zirconium alloy has become quite widely used in some areas. Scientists identify a large number of advantages of this material
Cement slurry: properties, preparation rules, composition, compliance with GOST requirements, purpose and application
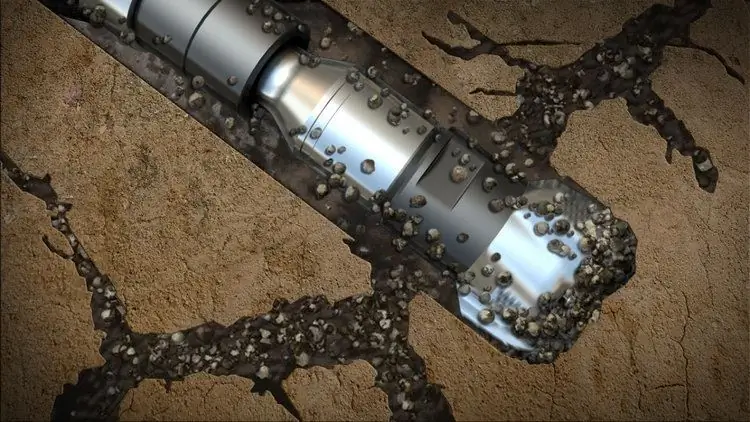
During the drilling process, special solutions are used to flush out cuttings and products from the development of local rock. This operation is necessary to increase the efficiency of the mechanical impact of the drilling rig and to clear the bottom hole. Washing out is carried out using cement slurries, which are prepared using special technologies
Types of cast iron, classification, composition, properties, marking and application
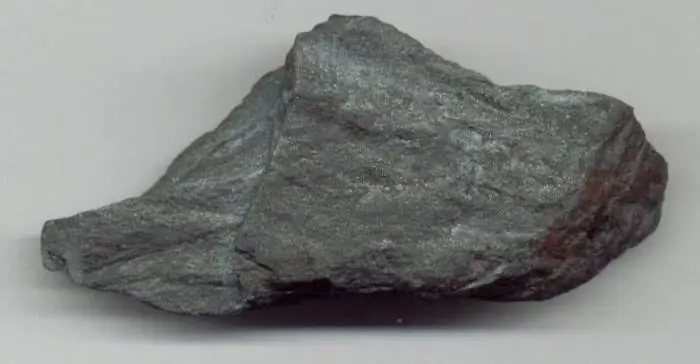
The types of cast iron that exist today allow a person to create many products. Therefore, we will talk about this material in more detail in this article
Natural fibers: origin and properties
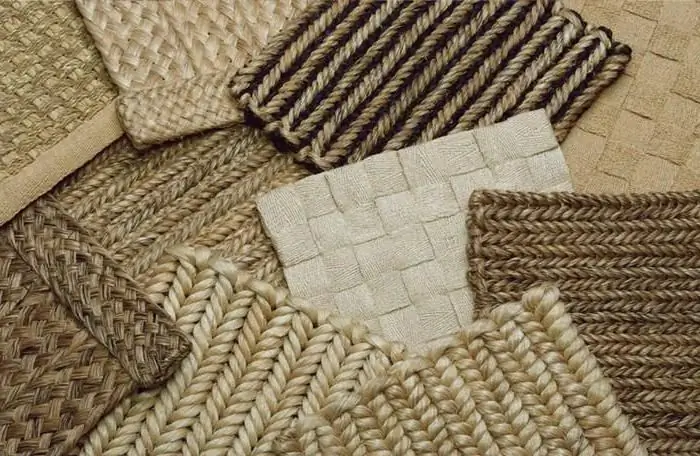
Natural fibers (cotton, linen and others) are the main raw material for the domestic textile industry. They are made from various natural products
Steel: composition, properties, types and applications. Composition of stainless steel
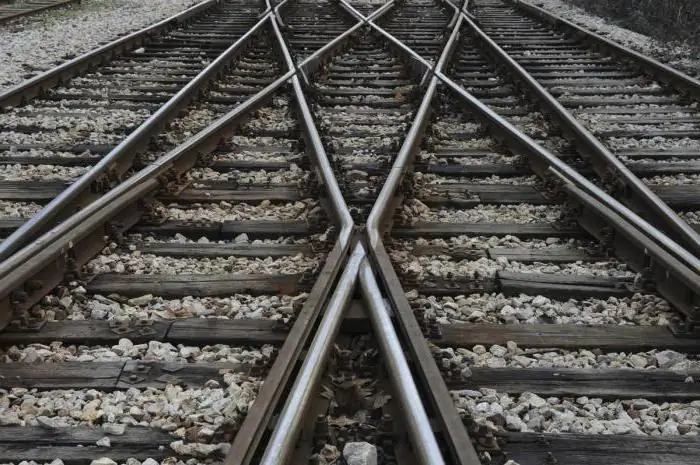
Today, steel is used in the vast majority of industries. However, not everyone knows that the composition of steel, its properties, types and applications are very different from the production process of this product