2025 Author: Howard Calhoun | [email protected]. Last modified: 2025-01-24 13:10
During the drilling process, special solutions are used to flush out cuttings and products from the development of local rock. This operation is necessary to increase the efficiency of the mechanical impact of the drilling rig and to clear the bottom hole. Washing out is carried out using cement slurries, which are prepared using special technologies.
Purpose of drilling fluids
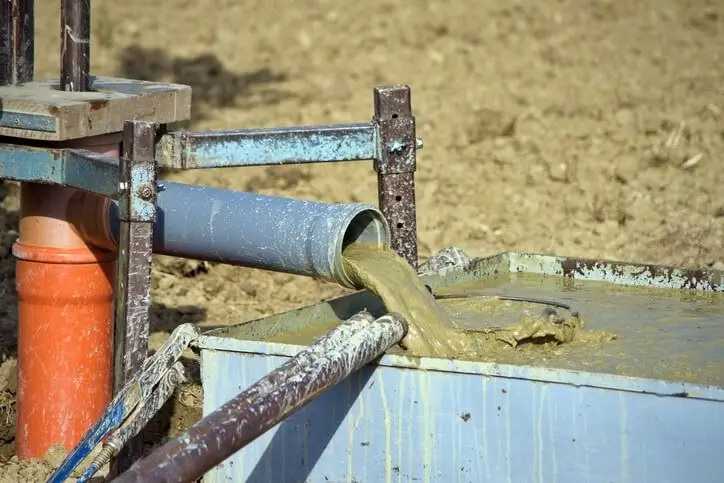
The circulation of water in the well contributes to the cleaning of the hole, which helps the drilling and completion processes. Provided that an active compound with additional performance properties is used, a number of other effects can be expected, among which are the following:
- Formation of a filter cake on the walls of an open hole. As a result, unstable deposits, clay rocks and loose layers are strengthened.
- Pore pressure is counteracted.
- The downhole power plant and the bit are transmittedadditional hydraulic power.
- Drilling and cement slurries transport the developed rock and, after circulation is completed, keep this mass in suspension.
- The risks of complications, differential sticking, oil and gas shows and loss of the well are prevented.
- Cavings and screes are prevented.
- Provides a lubricating effect on drilling equipment.
- Provides tool cooling and lubrication.
The basis for the composition of the cement mixture
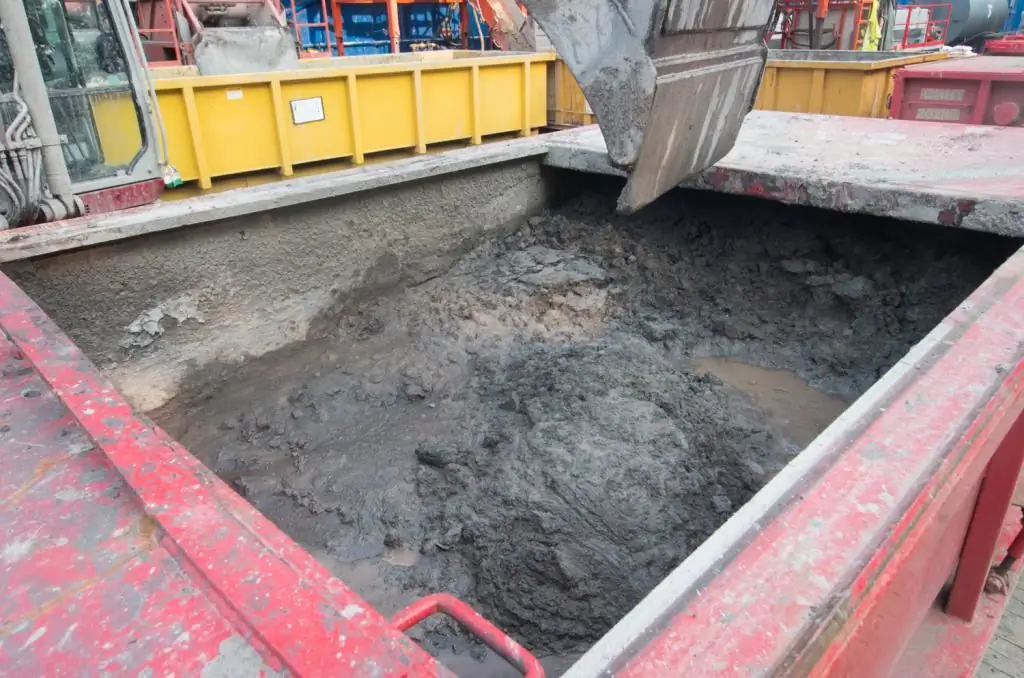
To create drilling fluids, plastic and fine clays with minimal sand inclusions are used, which, together with water, can form a viscous suspension with a long settling period. When developing gas and oil wells, experts recommend using alkaline types of montmorillonite clays, as well as clay powders. In addition, the composition of the cement slurry includes industrial water, hydrogels and s alt components. Modern mixtures include invert emulsion, lime-bitumen bases and polymer components. The ratio between the ingredients and their specific set depends on the effect to be achieved and the conditions for using the solution. In any case, undesirable components include impurities like gypsum and soluble minerals, which reduce the stability of viscous clay raw materials.
Rules for creating a solution
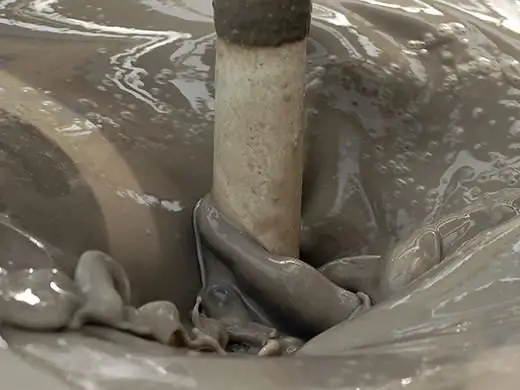
Cutting mixtures are prepared usingcement mixing units in accordance with the regulated regimes. Depending on the tasks set and the raw materials used, different technological solutions can be introduced into the cooking scheme. For example, if stale cement is used, then it is necessary to provide for its activation. The dry mixture is fed into the tank with stable operation of the water supply pump. The combination of liquid and dry components should be carried out under conditions of maintaining pressure at the level of 12-15 MPa. This is the optimal environment for the preparation of cement slurries in terms of mixing and setting of the structure. Next, you need to wait for the stabilization period of the mixture, for which a special mode is provided in the cement mixing machine.
Properties of cement mixtures
The technical and operational properties of drilling mixtures are determined by the selected recipe and in practice determine the quality of interaction with the materials of the well formations. The following cement slurry properties are taken into account:
- Water yield. Under conditions of pressure drops, the process of water separation from the active phase of the solution occurs. Depending on the parameters of the wellbore, the rate of fluid loss may be different, it is adjusted individually. For example, if it is planned to strengthen the structure, then the water loss of the solution should be close to zero.
- Sedimentation resistance. The process of separating water from the mortar, in which the cement mass moves down, and the liquid moves up.
- Thickening. It is determined by many factors, including the degree of grinding of the components of the solution and the presencetoughness materials. An increase in the proportion of water affects the stimulation of this property, and a third-party thermal effect affects the decrease.
- Grip. As a rule, technologists strive to improve this quality to the maximum in specific conditions. To do this, increase the temperature with pressure, as well as the isolation of the trunk in conditions of high moisture.
Modification of drilling fluid properties
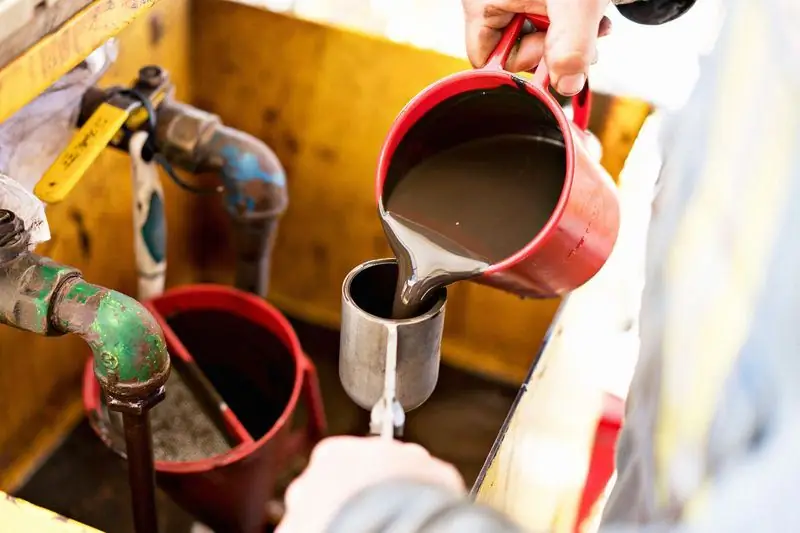
Correction of certain qualities is not always possible with conventional means and materials, therefore it is more expedient to use special additives and additives that effectively and pointwise change the desired properties. Among them, the following modifiers are noted:
- Sodium carbonate. Used to reduce setting time. With the help of this accelerator, quick-setting solutions are obtained, suitable for use at temperatures up to 55-65 ° С.
- Bentonite. Increases the index of the initial mobility of the flushing solution, optimizing measures for its injection. This modifier is recommended for use with cement slurries whose density varies from 1.5 to 2.2 g/cm3.
- Gypsum cement suspensions. Improve the ability of the solution to water loss. The base becomes more resistant to dissolution in water. For flushing compositions, the use of suspensions is meaningless, however, in order to strengthen the trunk, it is quite acceptable.
- Cement-resin additives. A type of plasticizer with epoxy resins that are used for flushingwells with aquifer complications.
Types of drilling fluids
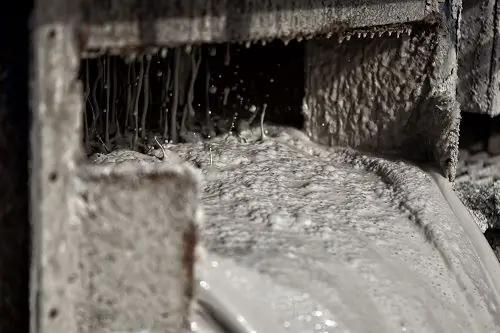
In practice, the following types of cement mixtures are usually distinguished:
- Drilling lignite. Alkaline based solution modified with lignites.
- Lime-bitumen mortar. Petroleum products are used as a basis - a combination of a dispersion medium from oil or diesel fuel, as well as bitumen and calcium oxide as a dispersed phase.
- Lightweight wash mix. It is a cement slurry reduced in mass with minimum density values. Used in the development of wells with low reservoir pressure.
- Polymer solution. The composition is based on water containing high-molecular linear polymers. Commonly used in hard rock drilling processes.
Check for compliance with GOST
According to GOST 26798.1-96, the parameters of drilling fluids are determined without taking into account the possible impacts that may occur during the operation of the material in real conditions with the connection of casing strings. For compliance with the standards, the thickening time of the mixture, density and viscosity are checked. At the same time, for different compositions, both technical indicators and the list of evaluation criteria may vary. So, to determine the properties of expansion and strength in the case of cement slurry, GOST 1581-96 is used, requiring that tests be carried out at an ambient temperature of about +30 ° C. In the process of solidificationcement stone mixtures in a limited volume, the strength indicators can be higher than when using a mass similar in composition when filling the well. Conversely, the permeability of the solution decreases.
Technology of cement mixture application
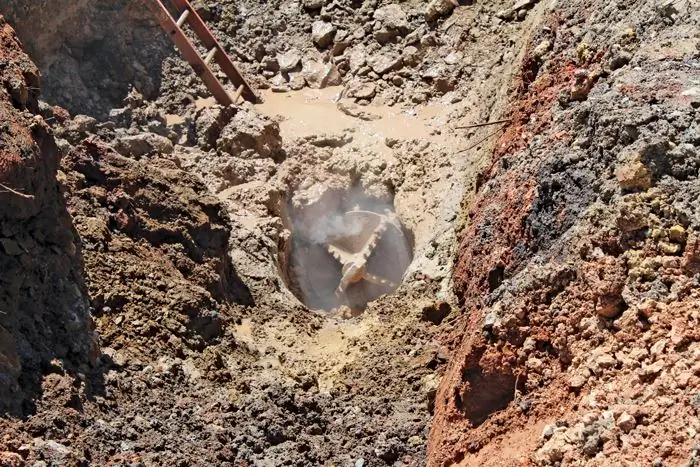
For the use of drilling fluids, special equipment is used to ensure the technical possibility of circulation operations. In the process of application, cement slurries perform the following technological cycle:
- The composition is mixed and stored in a special container.
- Pumping equipment starts pumping fluid from the tank to the well through the drill string.
- The mixture is sent through pipes to the bottom of the wellbore, where the bit of the drilling rig develops the next layer of rock.
- The mud returns to the surface, carrying rock particles separated by the chisel.
- The mass rises along the annulus, passing between the drill pipe and the walls of the well.
- On the surface, the operation of filtering and cleaning the solution from sludge is performed. To do this, use a vibrating sieve.
Conclusion
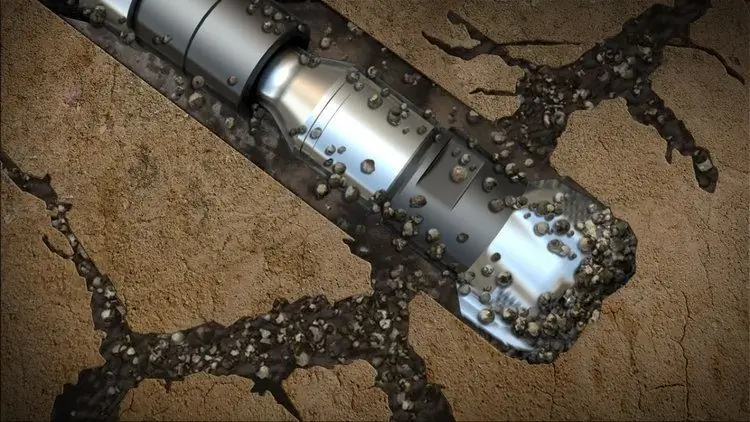
Cement mixtures are a necessary consumable in the development and construction of wells. However, their improper use, along with positive effects, can also lead to negative consequences. In particular, errors in the manufacture of cement slurry in the future may result in rock falls and evendrilling equipment damage. Therefore, a flushing project is initially drawn up, the composition of which is carefully calculated. In general, it is necessary to determine what will be the volume of dry components, water, the total amount of the mixture, the characteristics of the cementing units, etc.
Recommended:
Industrial marker: description, composition, rules, application and purpose
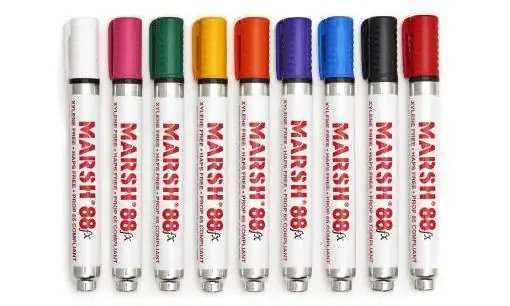
Industrial marker - a writing tool for applying information on a variety of surfaces. In this case, the surface can be wood, glass, stone, metal, leather, painted materials and even rust. The requirements for such a marker are very specific
Polymer cement mortar: composition, technical characteristics, compliance with GOST requirements, purpose and application
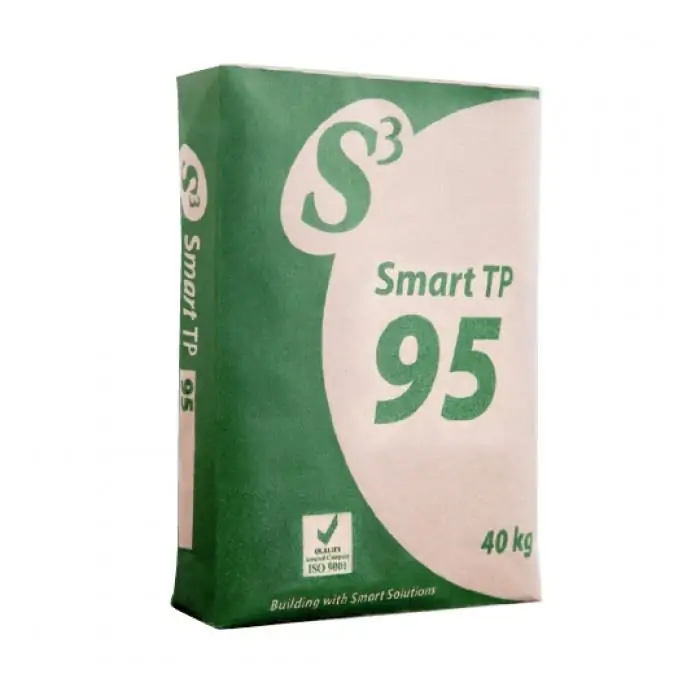
Polymer cement mortar is one of the modifications of conventional sand-cement mortar. Polymers can also be added to mixtures that are used when laying plaster and other facing materials. The addition of this substance to the composition helps to improve its characteristics
High-voltage tests: purpose, algorithm, test methods, standards, protocol and compliance with safety rules
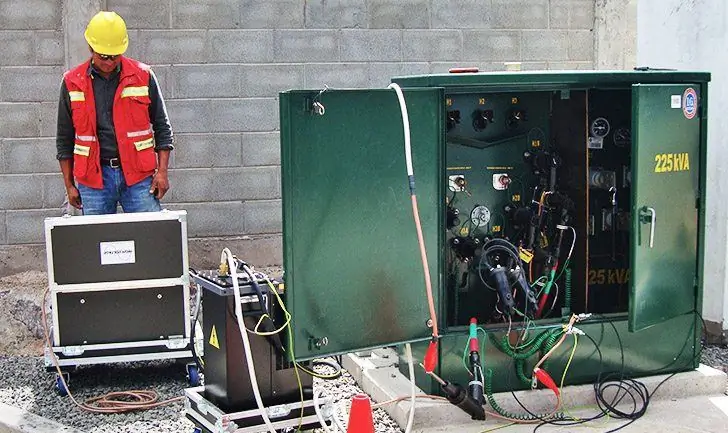
The operation of electrical equipment involves a number of high-voltage tests. They are very important for the correct operation of the devices. Their purpose. the algorithm for conducting, norms and compliance with safety rules are described in detail in this article
Flux for welding: purpose, types of welding, flux composition, rules of use, GOST requirements, pros and cons of application
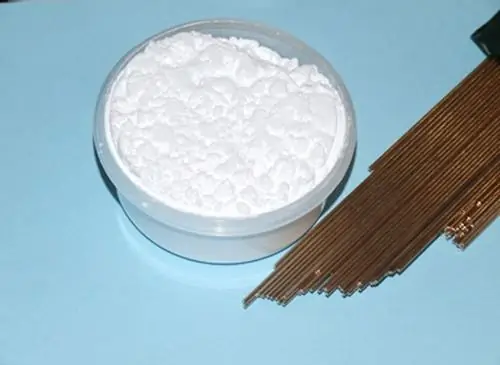
The quality of the weld is determined not only by the ability of the master to organize the arc correctly, but also by the special protection of the working area from external influences. The main enemy on the way to creating a strong and durable metal connection is the natural air environment. The weld is isolated from oxygen by a flux for welding, but this is not only its task
Concrete mix: properties, composition, types, grades of concrete, characteristics, compliance with GOST standards and application
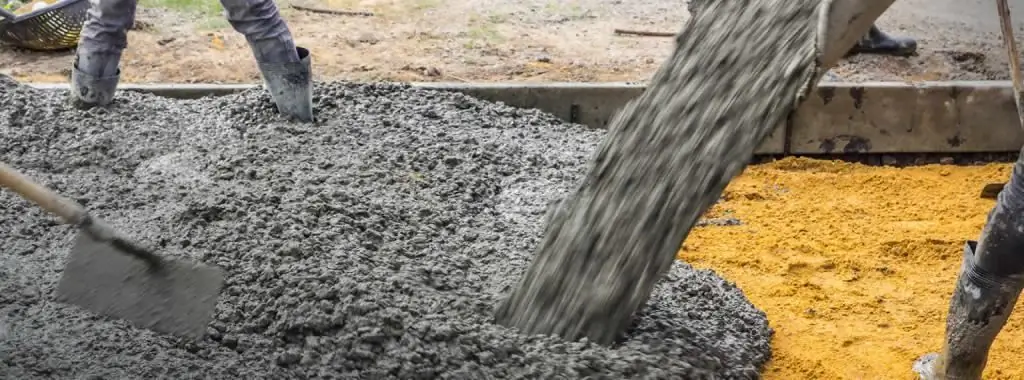
Among the main properties of the concrete mixture, which is also called hydrotechnical concrete, it is necessary to highlight the increased water resistance. Buildings are being built from this material to be used in swampy areas or in regions that are prone to flooding