2025 Author: Howard Calhoun | [email protected]. Last modified: 2025-01-24 13:10
Polymer cement mortar is one of the modifications of conventional sand-cement mortar. Polymers can also be added to mixtures that are used when laying plaster and other facing materials. Adding this substance to the composition helps to improve its characteristics.
General description and difference
A cement mortar made from conventional components, like other mortars in which a mineral substance acts as a binder, has a number of disadvantages. Among them, low tensile or flexural strength, low impact resistance, low percentage of deformation, low abrasion resistance, and poor adhesion to other building materials stand out. The list of disadvantages is quite large, which greatly limits the use of a conventional solution. In order to reduce the influence of these shortcomings as much as possible or even completely eliminate their influence, special polymers are introduced into the mixture as an additive from 2 to 30% of the total mass. Thus it is possibleto say that the composition of the polymer cement mortar differs from the usual one only by the presence of this very additive.
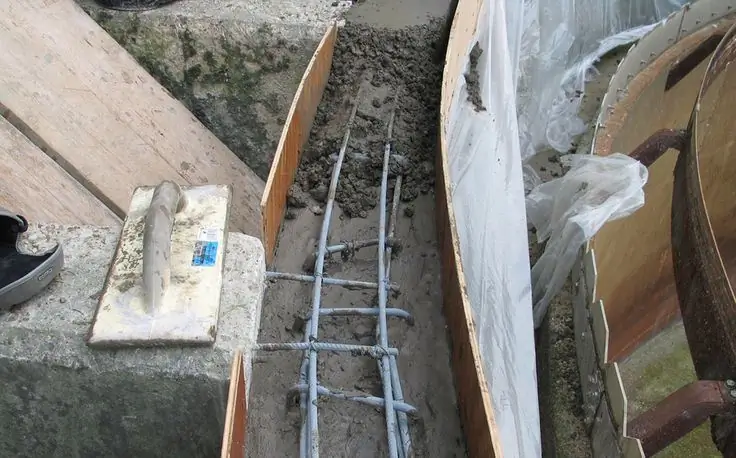
Introducing the polymer into the mixture
It is worth mentioning that the polymer, one way or another, is introduced into a large number of various mixtures. Most often, it is intended only to improve plasticization, as well as hydrophobization. In addition, the presence of such additives is less than 1% of the total mass. This is the main difference from a full-fledged polymer cement mortar. In them, the polymer seriously affects the composition, changing its physical and chemical properties, its structure, and also enters the solution as an independent element, and not an ordinary additive.
Polymer addition methods may vary. For example, you can add it in the form of an aqueous mixture. In such cases, usually its content in cement will be no more than 3-5% of the total mass. Much more commonly used method, which involves aqueous dispersions containing polymers. The difference is that in the dispersion the polymer does not dissolve in water, which means that its amount can be increased. Thus, it is possible to introduce into the cement mixture approximately 10-20% of the additive from the total mass of cement.
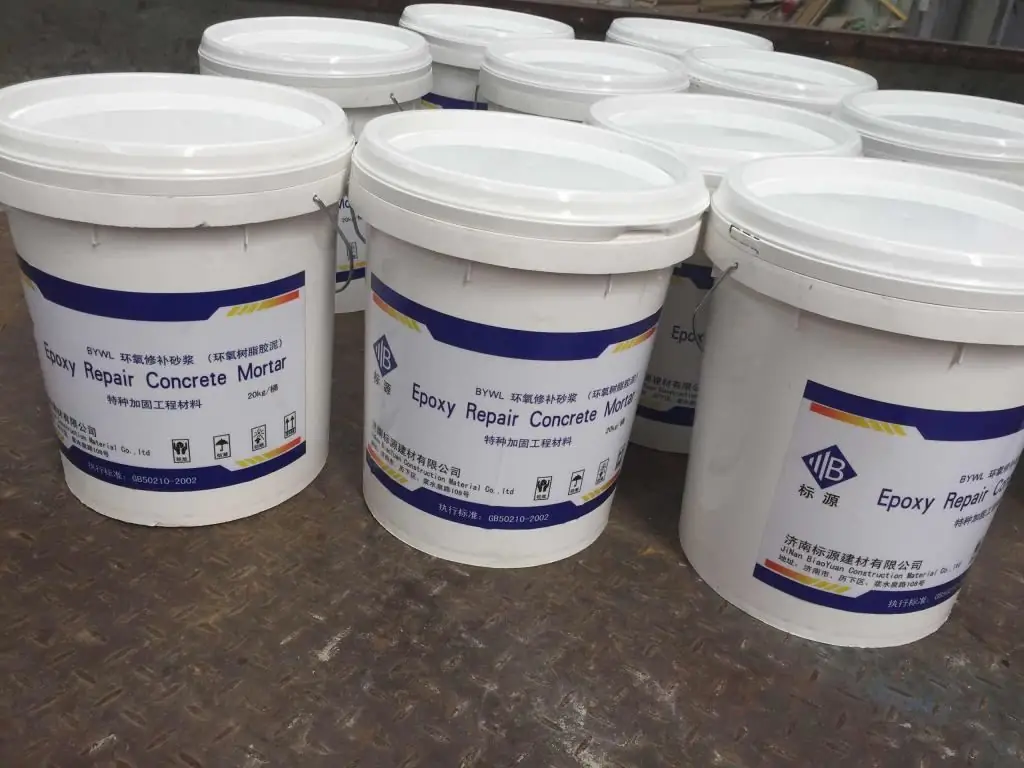
Additional items
It is worth noting that all the characteristics of the polymer cement mortar may be lost if, during the addition of the polymer dispersion, a process such as coagulation or curdling of the solution occurs. Most often, to avoid such negative consequences, variousstabilizers. As they are usually chosen surface-active substances (surfactants) - OP-7 or OP-U. It is also possible to replace them with a small group of electrolytes, for example, liquid glass. Only a polymer-cement mortar, which was mixed on the basis of a plasticized PVA dispersion, can do without the addition of a stabilizer.
However, the introduction of surfactants does not pass without a trace. Most often, these substances act as powerful foaming agents, and they are also able to involve air in the mortar mixture. If this happens, then the smallest air bubbles that were involved can reach up to 30% of the total mass of the solution.
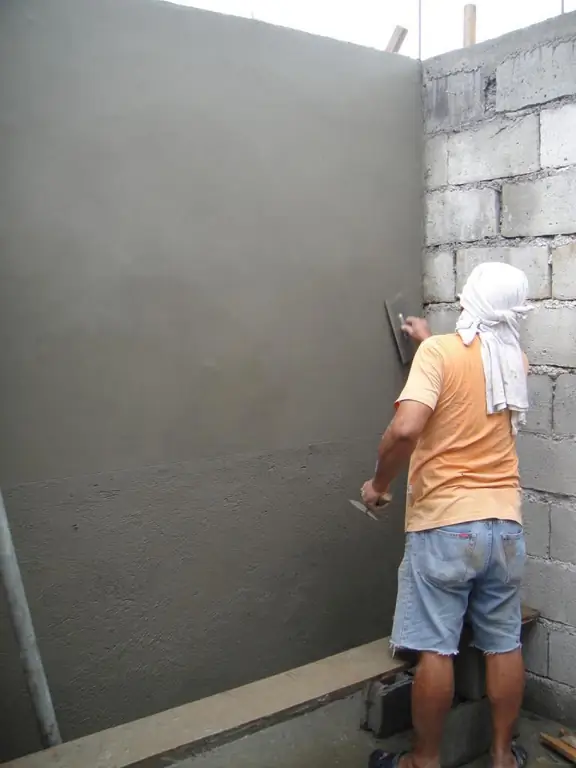
Change the properties of the solution
The presence of polymer additives in the solution helps to more evenly distribute the pores, as well as make their volume much smaller. An example can be given. In a conventional cement mortar, for example, pores can be up to 1 mm in diameter, and their main part differs by 0.2-0.5 mm in volume. If we are talking about a polymer-cement composition, then the maximum volume is reduced to 0.5 mm, and the largest amount, approximately 90-95%, will not be more than 0.2 mm at all.
This speaks in the most positive way, for example, when the plaster walls are completely leveled with a polymer cement mortar, where the pores could disrupt the overall structure. It is also worth adding here that those mixtures in which there is entrained air are characterized by greater plasticity, as well as better workability with a lower liquid content. As mentioned earlier, plasticization in such compoundsalso at a higher level. All this leads to the fact that when adding water it is very important to take into account the percentage of entrained air and the plasticization of the polymer cement solution.
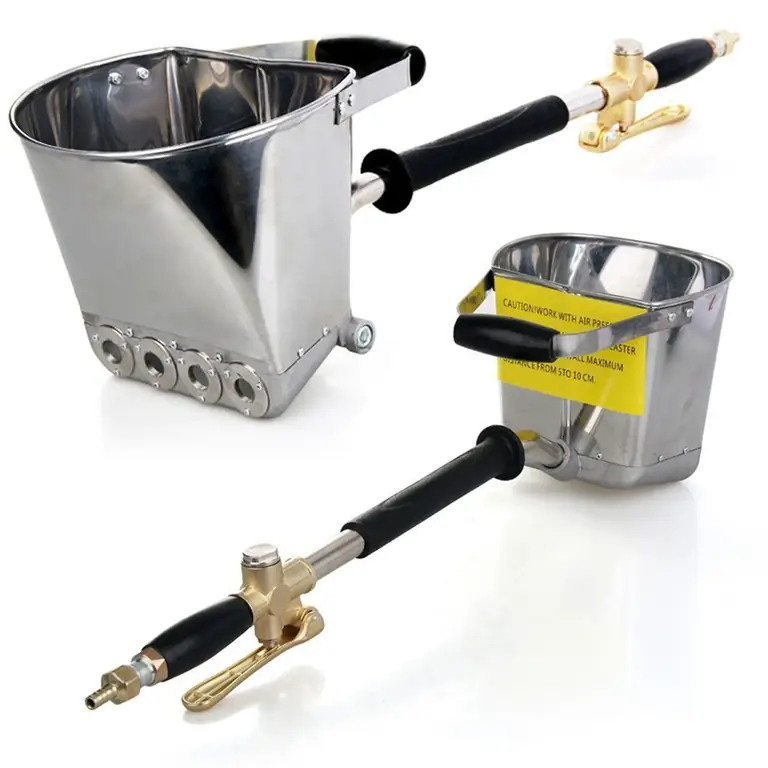
Adhesion properties
In such compositions, increased adhesion is observed, which is explained as follows. When applying the mixture, the polymer is concentrated at the interface and acts as a sticky base between the solution and the base. As for the adhesion itself, it directly depends on the type of added polymer, as well as on its concentration. Further, it should be said that this property manifests itself only when the solution is dried in air-dry conditions. Therefore, for example, plaster with a polymer-cement mortar applied to the walls will be an excellent basis for laying. If curing takes place in water, then the adhesion will not work as well, even with a huge concentration of polymer. This is due to the fact that stabilizers dissolve in water, and some additives are completely capable of changing their properties if they are in a liquid medium.
It can be added that a high level of adhesion affects not only improved adhesion to other materials, but also the mechanical characteristics of the mortar itself. This is especially noticeable under the resulting tensile and bending loads. For mixtures with additives, these figures are about 10 times higher than for conventional ones. This is due to the fact that the polymer layers bind the mineral components together. There is also such a characteristic as the modulus of elasticity, whichabout 10 times lower than normal. Thanks to this fact, we can safely say that the polymer composition is more deformable than the ordinary one.
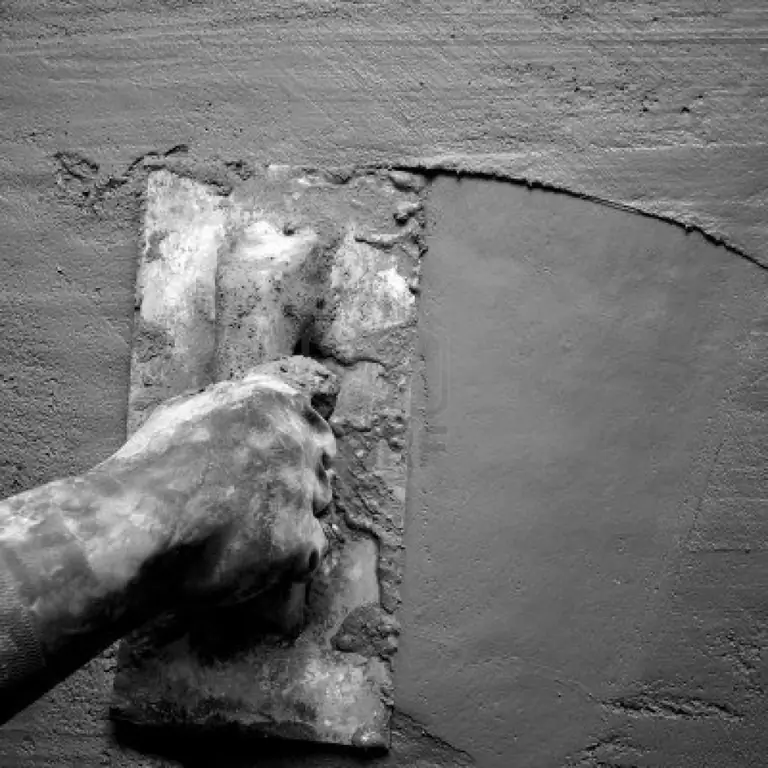
Shrinkage and other characteristics
If more than 7-10% of the polymer from the total mass of cement is introduced into the mixture, then more significant shrinkage will be observed during its hardening. However, since at the same time the deformability of the solution also increases greatly, in terms of such a characteristic as resistance to cracks, the mixture is in no way inferior to the usual one, and in some situations may even exceed it. Another difference in the parameters is the return of moisture. In a polymer solution, it passes more slowly, which has a positive effect on the hardening process, since there is no rapid drying, which can cause cracks.
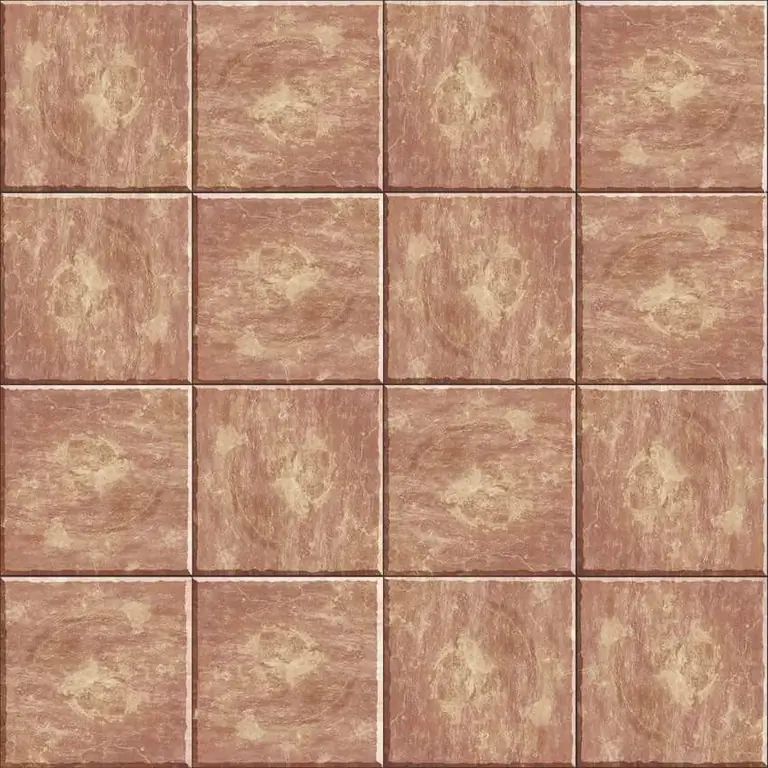
Interaction with other materials
What is polymer cement mortar used for? All of the above properties and characteristics of the material have led to the fact that it is excellent for fastening facing materials, as it can provide better fastening. A simple comparison can be made here between a conventional blend and a blend with a polymer additive. A mortar based on cement and sand creates maximum fastening strength by 7-9 days after facing, and by 28 days this figure will decrease by about 5-6 times. If it talks about a solution with an additive made of polymers, then the maximum fastening strength will be achieved a little later, on days 9-10, however, its absence in the future is not at allobserved. Thanks to this quality, such compositions have become the most widely used in cladding.
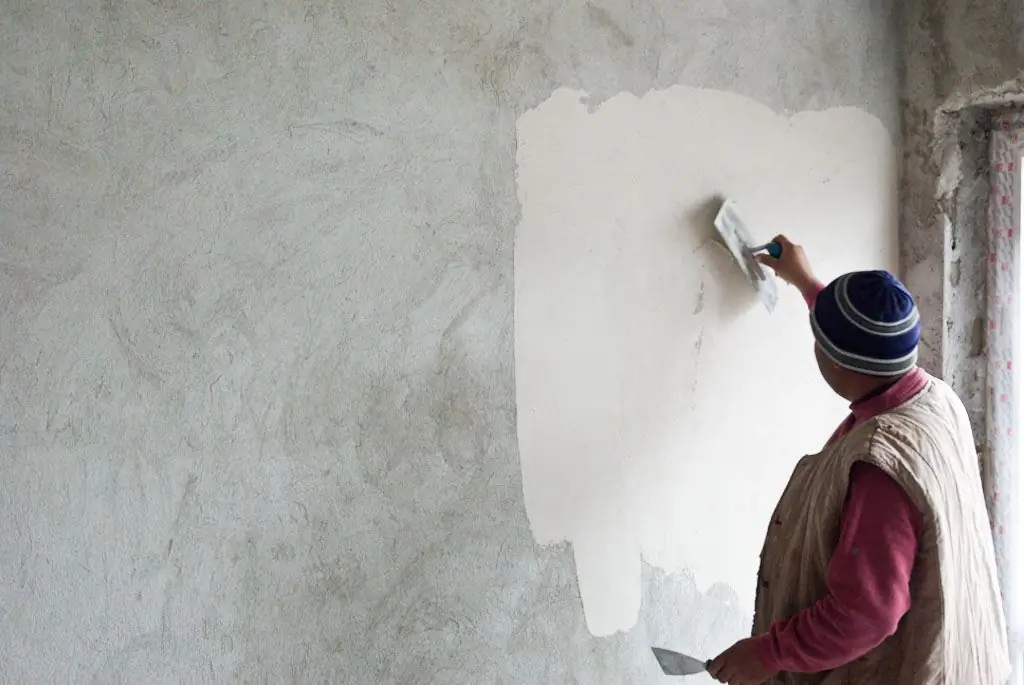
The best compositions for work and consumption
When modifying a conventional cement-sand mortar with plasticizers and polymers, a strong reduction in consumption can be achieved. The polymer cement mortar can be applied in the thinnest possible layers and at the same time be a high-quality base for the facing material. This is due to the fact that dispersion with polymers not only seriously increases plasticity, but also involves air from 8 to 12%.
To date, the most promising solution in this area is the one made on the basis of gypsum-cement-pozzolanic binder (GCPV), as well as aqueous dispersions of polymers. You can use such a composition both for outdoor work and for internal plastering. However, as practice has shown, it achieves the greatest effect when it is used in decorative solutions and mastic mixtures for processing building facades.
Composition Requirements
Today, there is a state document that regulates all the requirements that must be met during the operation of this kind of mixture. Previously, for a polymer cement mortar, GOST 28013-98 was not fully prepared. Its action extended only to ordinary mortars, without special additives. Instead of this and incomplete GOST, SP 82-101-98 was introduced, which extended to a more complete list of all mixtures. For example, the rulebook states thatspecial mixtures can be prepared only in special units - at mortar plants, if they are used in the construction of government buildings. In addition, only special dump trucks or mortar trucks should be used to deliver such building material. Another important requirement was that all constituent components must pass all the necessary tests for their suitability and quality before proceeding with their mixing.
Composition for flooring
The biggest difference between a conventional polymer-added mortar and one that should be used for flooring is that it has higher abrasion resistance and also does not generate dust during wear. Most often, PVA dispersions or styrene-butadiene latexes are used to compile such a base. If you add latex in an amount of 15-20%, then you can increase the resistance to abrasion by 4-5 times, if you add the same amount of PVA dispersion, you can only increase this parameter by 3 times.
If we conclude from all of the above, then we can say with confidence that the use of a conventional mixture is no longer so relevant. The presence of a variety of additives is fully justified, even if it slightly increases the cost of the mixture.
Recommended:
Cement slurry: properties, preparation rules, composition, compliance with GOST requirements, purpose and application
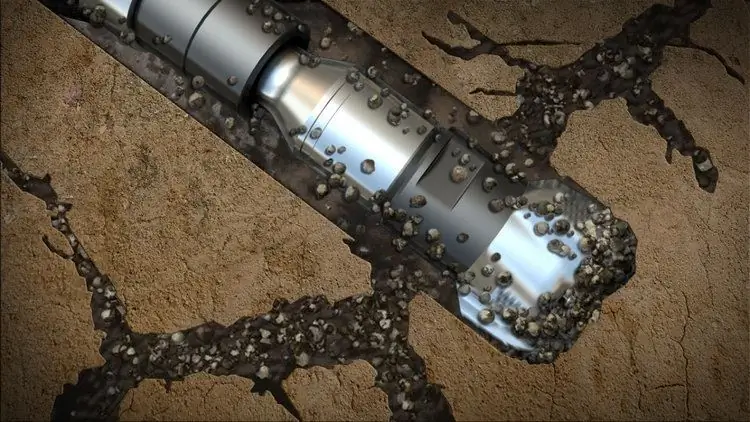
During the drilling process, special solutions are used to flush out cuttings and products from the development of local rock. This operation is necessary to increase the efficiency of the mechanical impact of the drilling rig and to clear the bottom hole. Washing out is carried out using cement slurries, which are prepared using special technologies
Coiled galvanized steel with a polymer coating: characteristics, purpose
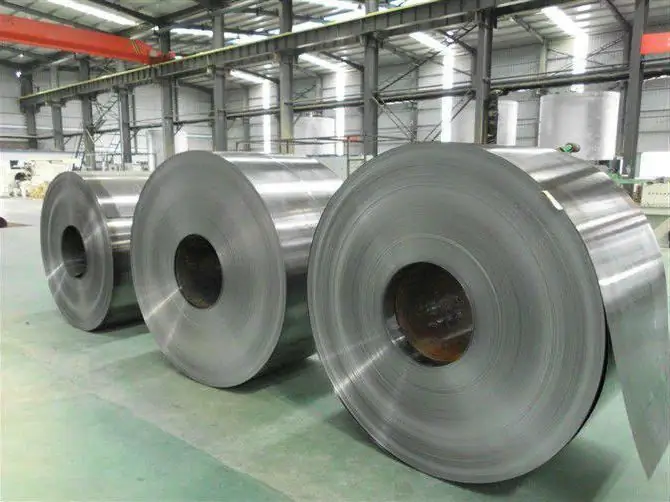
Rolled steel is one of the most common types of rolled metal. To make a successful purchase of this material, you should know several important features
Flux for welding: purpose, types of welding, flux composition, rules of use, GOST requirements, pros and cons of application
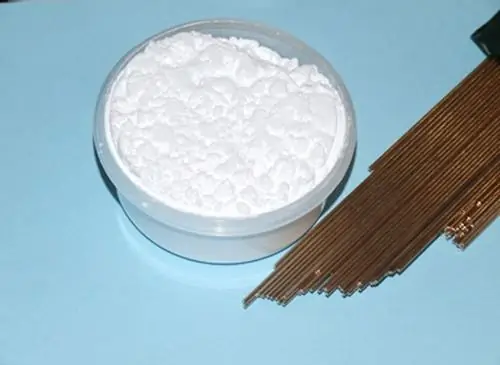
The quality of the weld is determined not only by the ability of the master to organize the arc correctly, but also by the special protection of the working area from external influences. The main enemy on the way to creating a strong and durable metal connection is the natural air environment. The weld is isolated from oxygen by a flux for welding, but this is not only its task
Ripstop fabric: what is it, composition, characteristics, purpose and application
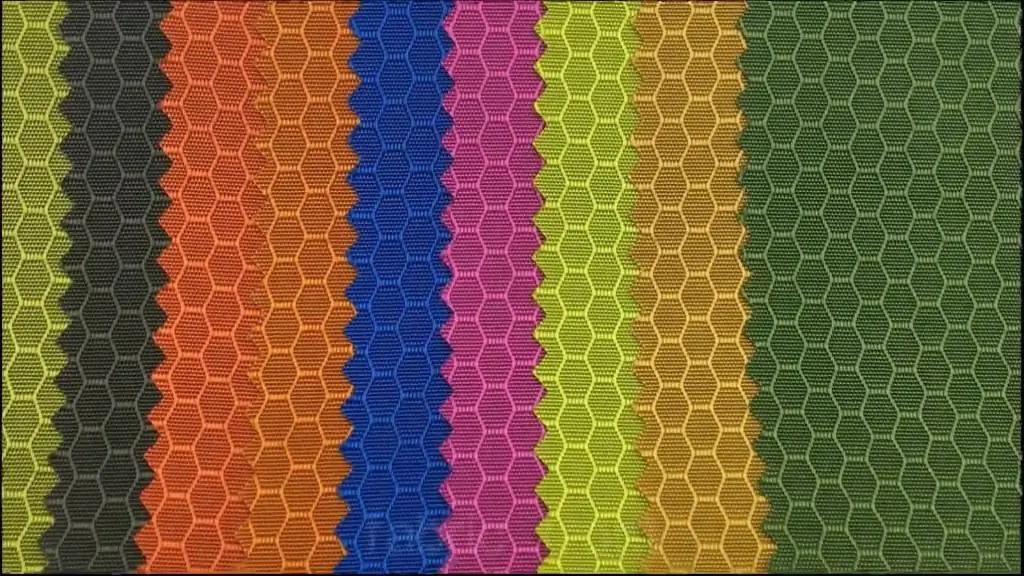
When asked if it is a ripstop fabric, the answer is usually about a durable material. However, the name unites a whole category of very durable materials that are produced using a special technology. It comes from the English phrase (rip - tear, stop - cessation)
Concrete mix: properties, composition, types, grades of concrete, characteristics, compliance with GOST standards and application
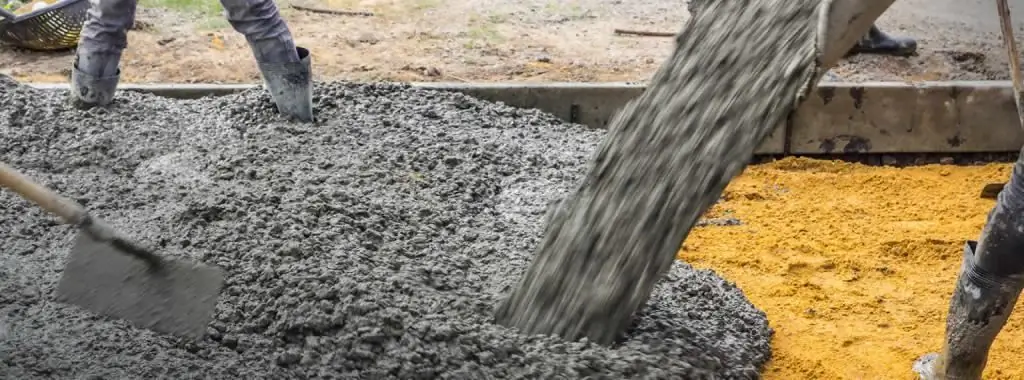
Among the main properties of the concrete mixture, which is also called hydrotechnical concrete, it is necessary to highlight the increased water resistance. Buildings are being built from this material to be used in swampy areas or in regions that are prone to flooding