2025 Author: Howard Calhoun | [email protected]. Last modified: 2025-01-24 13:10
Iron ore is obtained in the usual way: open pit or underground mining and subsequent transport for initial preparation, where the material is crushed, washed and processed.
The ore is poured into a blast furnace and blasted with hot air and heat, which turns it into molten iron. It is then removed from the bottom of the furnace into molds known as pigs, where it is cooled to produce pig iron. It is turned into wrought iron or processed into steel in several ways.
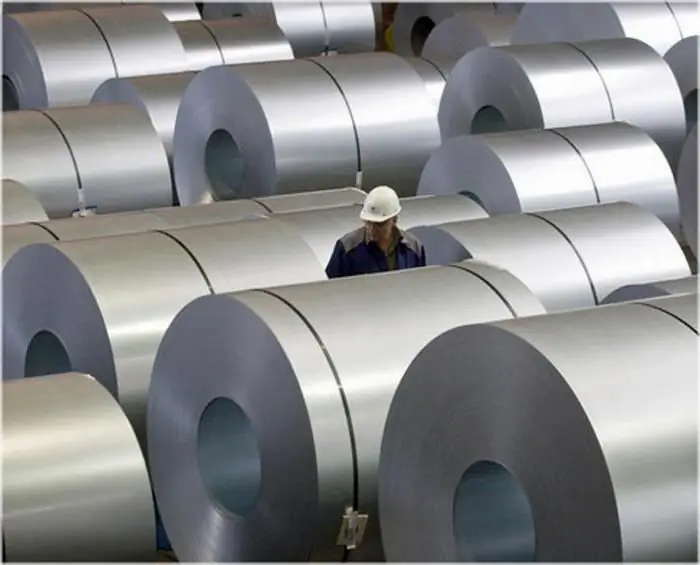
What is steel?
In the beginning there was iron. It is one of the most common metals in the earth's crust. It can be found almost everywhere, in combination with many other elements, in the form of ore. In Europe, the beginning of work with iron dates back to 1700 BC
In 1786, French scientists Berthollet, Monge and Vandermonde accurately determined that the difference between iron, cast iron and steel is due to different carbon content. Nevertheless, steel, made from iron, quickly became the most important metal of the Industrial Revolution. At the beginning of the 20th century, world steel production was 28million tons - this is six times more than in 1880. By the beginning of World War I, its production was 85 million tons. For several decades, it has practically replaced iron.
Carbon content affects the characteristics of the metal. There are two main types of steel: alloyed and unalloyed. Steel alloy refers to chemical elements other than carbon added to iron. Thus, an alloy of 17% chromium and 8% nickel is used to create stainless steel.
Currently, there are more than 3000 cataloged brands (chemical compositions), not counting those created to meet individual needs. All contribute to making steel the most suitable material for the challenges of the future.
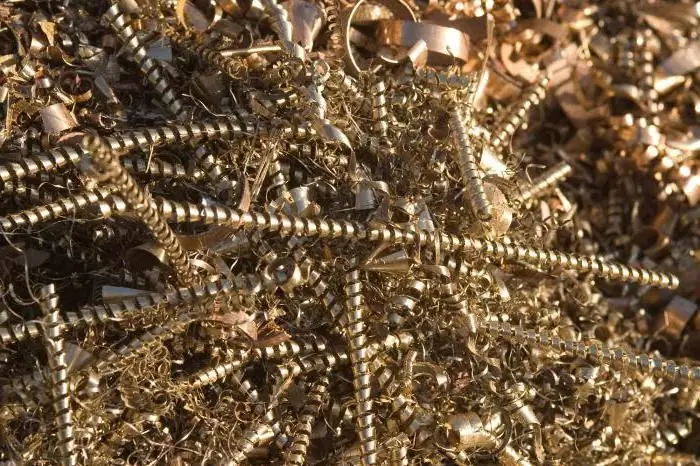
Steelmaking raw materials: primary and secondary
Smelting this metal using many components is the most common mining method. Charge materials can be both primary and secondary. The main composition of the charge, as a rule, is 55% pig iron and 45% of the remaining scrap metal. Ferroalloys, converted cast iron and commercially pure metals are used as the main element of the alloy, as a rule, all types of ferrous metal are classified as secondary.
Iron ore is the most important and basic raw material in the iron and steel industry. It takes about 1.5 tons of this material to produce a ton of pig iron. About 450 tons of coke are used to produce one ton of pig iron. Many ironworkseven charcoal is used.
Water is an important raw material for the iron and steel industry. It is mainly used for coke quenching, blast furnace cooling, coal furnace door steam production, hydraulic equipment operation and waste water disposal. It takes about 4 tons of air to produce a ton of steel. The flux is used in the blast furnace to extract contaminants from smelter ore. Limestone and dolomite combine with the extracted impurities to form slag.
Both blast and steel furnaces lined with refractories. They are used for facing furnaces for iron ore smelting. Silicon dioxide or sand is used for molding. Non-ferrous metals are used to produce steel of various grades: aluminum, chromium, cob alt, copper, lead, manganese, molybdenum, nickel, tin, tungsten, zinc, vanadium, etc. Among all these ferroalloys, manganese is widely used in steelmaking.
Iron waste from dismantled factory structures, machinery, old vehicles, etc. is recycled and widely used in the industry.
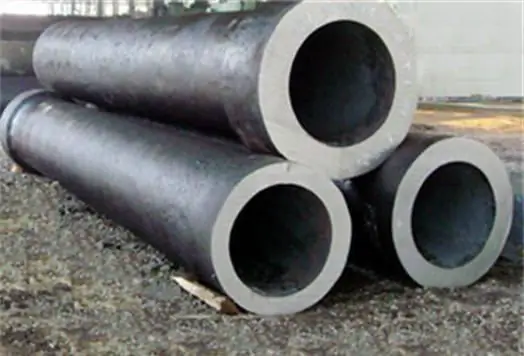
Iron for steel
Steel smelting with cast iron is much more common than with other materials. Cast iron is a term that usually refers to gray iron, however it is also identified with a large group of ferroalloys. Carbon makes up about 2.1 to 4 wt% while silicon makes up typically 1 to 3 wt% in the alloy.
Iron and steel smelting takes place at a temperaturemelting point between 1150 and 1200 degrees, which is about 300 degrees lower than the melting point of pure iron. Cast iron also exhibits good fluidity, excellent machinability, resistance to deformation, oxidation and casting.
Steel is also an alloy of iron with a variable carbon content. The carbon content of steel is 0.2 to 2.1 mass%, and it is the most economical alloying material for iron. Smelting steel from cast iron is useful for a variety of engineering and structural purposes.
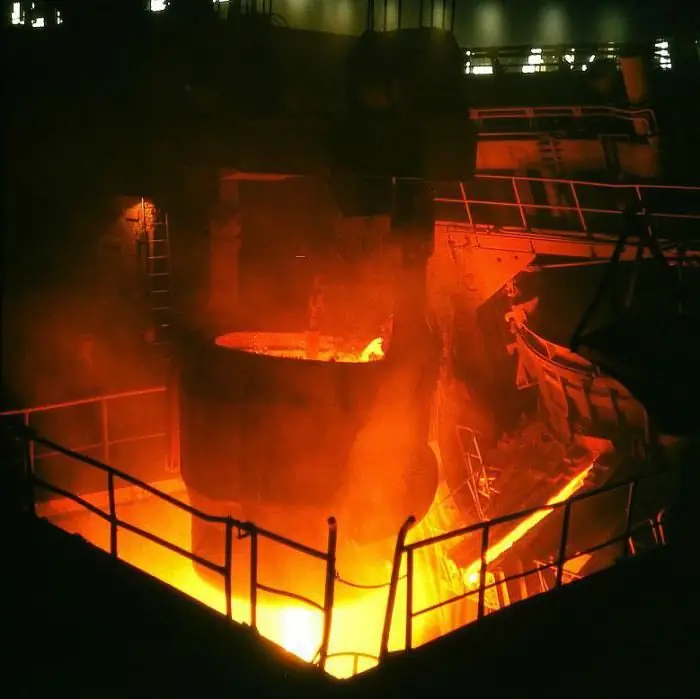
Iron ore for steel
The process of making steel begins with the processing of iron ore. The rock containing iron ore is crushed. Ore is mined using magnetic rollers. Fine-grained iron ore is processed into coarse-grained lumps for use in a blast furnace. Coal is refined in a coke oven to produce an almost pure form of carbon. The mixture of iron ore and coal is then heated to produce molten iron, or pig iron, from which steel is made.
In the main oxygen furnace, molten iron ore is the main raw material and is mixed with various amounts of scrap steel and alloys to produce various grades of steel. In an electric arc furnace, recycled steel scrap is melted directly into new steel. About 12% of steel is made from recycled material.
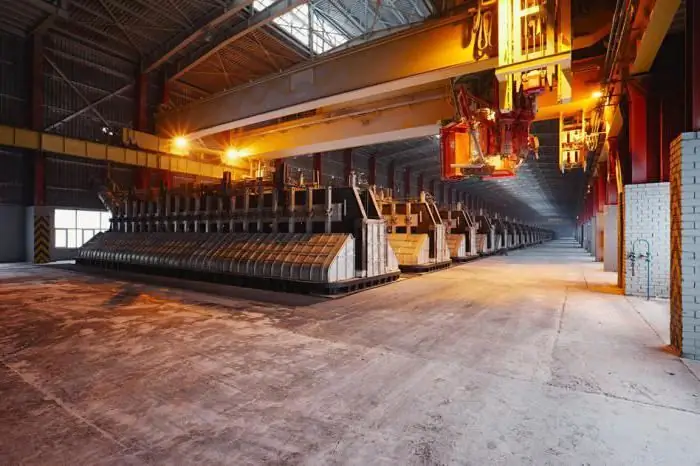
Smelting technology
Smelting is a process by which a metal is obtained either in the form of an element,either as a simple compound from its ore by heating above its melting point, usually in the presence of oxidizing agents such as air or reducing agents such as coke.
In steelmaking technology, the metal that is combined with oxygen, such as iron oxide, is heated to a high temperature, and the oxide is formed in combination with carbon in the fuel, which is released as carbon monoxide or carbon dioxide. Other impurities, collectively called veins, are removed by adding a stream with which they combine to form slag.
Modern steelmaking uses a reverberatory furnace. The concentrated ore and stream (usually limestone) are loaded at the top, while the molten matte (compound of copper, iron, sulfur, and slag) is drawn from the bottom. A second heat treatment in a converter furnace is necessary to remove iron from the matte finish.
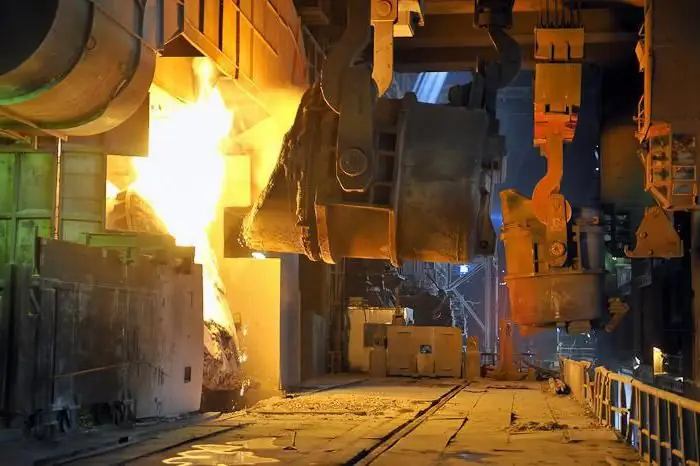
Oxygen-convector method
The BOF process is the world's leading steelmaking process. The world production of converter steel in 2003 amounted to 964.8 million tons or 63.3% of the total production. Converter production is a source of environmental pollution. The main problems of this are the reduction of emissions, discharges and reduction of waste. Their essence lies in the use of secondary energy and material resources.
Exothermic heat is generated by oxidation reactions during blowdown.
The main steelmaking process using our ownstocks:
- Molten iron (sometimes called hot metal) from a blast furnace is poured into a large refractory lined container called a ladle.
- The metal in the ladle is sent directly to the main steel production or pre-treatment stage.
- High purity oxygen at a pressure of 700-1000 kilopascals is injected at supersonic speed onto the surface of the iron bath through a water-cooled lance that is suspended in a vessel and held a few feet above the bath.
The pre-treatment decision depends on the quality of the hot metal and the desired final steel quality. The very first removable bottom converters that can be detached and repaired are still in use. The spears used for blowing have been changed. To prevent jamming of the lance during blowing, slotted collars with a long tapering copper tip were used. The tips of the tip, after combustion, burn off the CO formed when blown into CO2 and provide additional heat. Darts, refractory balls and slag detectors are used to remove slag.
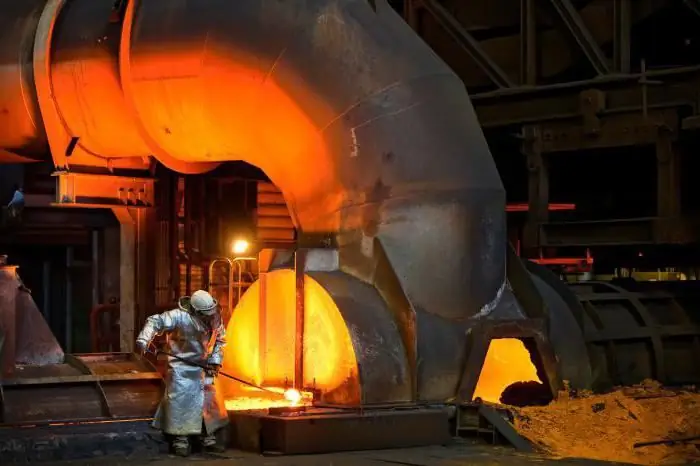
Oxygen-convector method: advantages and disadvantages
Does not require the cost of gas purification equipment, since dust formation, i.e. iron evaporation, is reduced by 3 times. Due to the decrease in the yield of iron, an increase in the yield of liquid steel by 1.5 - 2.5% is observed. The advantage is that the blowing intensity in this method increases, which givesthe ability to increase the performance of the converter by 18%. The quality of the steel is higher because the temperature in the purge zone is lower, which results in less nitrogen formation.
The shortcomings of this method of steel smelting led to a decrease in demand for consumption, as the level of oxygen consumption increases by 7% due to the high consumption of fuel combustion. There is an increased hydrogen content in the recycled metal, which is why it takes some time after the end of the process to carry out a purge with oxygen. Among all the methods, oxygen-converter has the highest slag formation, the reason is the inability to monitor the oxidation process inside the equipment.
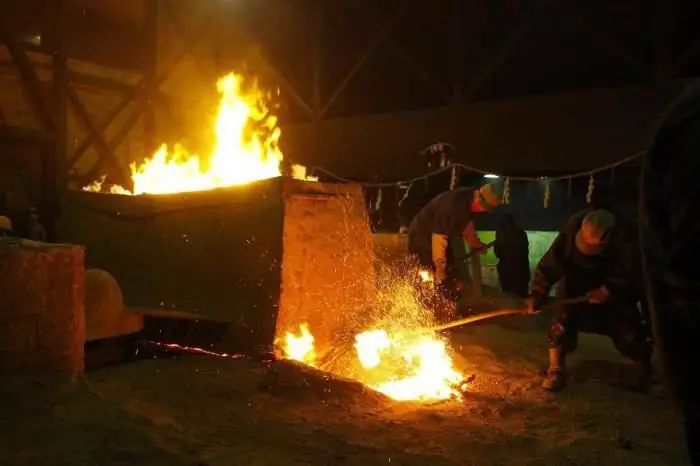
Open-hearth method
The open-hearth process for most of the 20th century was the main part of the processing of all steel made in the world. William Siemens, in the 1860s, sought a means of raising the temperature in a metallurgical furnace, resurrecting an old proposal to use the waste heat generated by the furnace. He heated the brick to a high temperature, then used the same path to introduce air into the kiln. The preheated air increased the temperature of the flame significantly.
Natural gas or atomized heavy oils are used as fuel; air and fuel are heated before combustion. The furnace is loaded with liquid pig iron and steel scrap along with iron ore, limestone, dolomite and fluxes.
The stove itself is made ofhighly refractory materials such as magnesite hearth bricks. Open hearth furnaces weigh up to 600 tons and are usually installed in groups, so that the massive auxiliary equipment needed to charge furnaces and process liquid steel can be effectively used.
Although the open hearth process has been almost completely replaced in most industrialized countries by the basic oxygen process and the electric arc furnace, it makes about 1/6 of all steel produced worldwide.
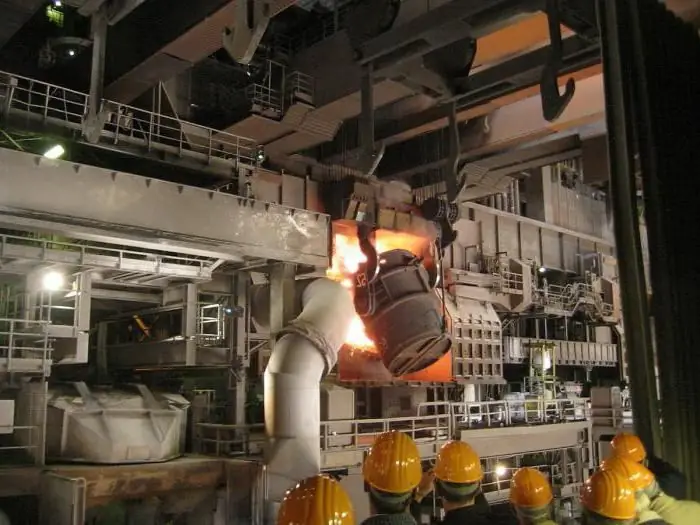
Advantages and disadvantages of this method
The advantages include ease of use and ease of production of alloy steel with various additives that give the material various specialized properties. The necessary additives and alloys are added immediately before the end of the smelting.
The disadvantages include reduced efficiency compared to the oxygen-converter method. Also, the quality of the steel is lower compared to other metal smelting methods.
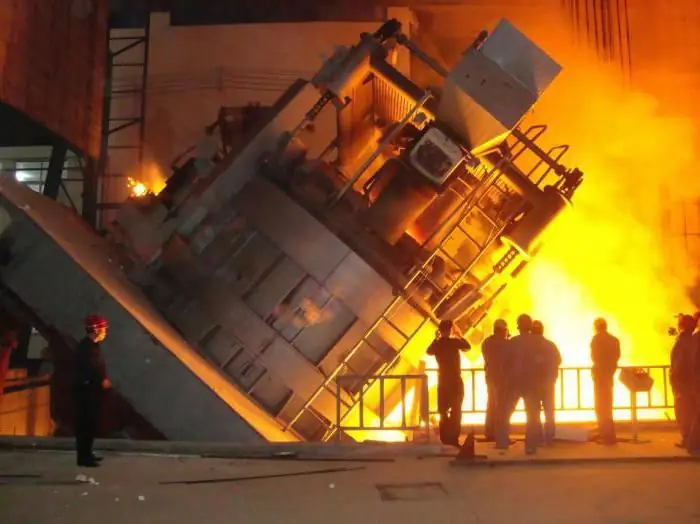
Electric steelmaking method
The modern method of smelting steel using our own reserves is a furnace that heats a charged material with an electric arc. Industrial arc furnaces range in size from small units with a capacity of about one ton (used in foundries for the production of iron products) to 400 tons units used in secondary metallurgy.
Arc furnaces,used in research laboratories may have a capacity of only a few tens of grams. Industrial electric arc furnace temperatures can reach up to 1800 °C (3,272 °F), while laboratory installations can exceed 3000 °C (5432 °F).
Arc furnaces differ from induction furnaces in that the charging material is directly exposed to an electric arc, and the current in the terminals passes through the charged material. The electric arc furnace is used for steel production, consists of a refractory lining, usually water-cooled, large size, covered with a retractable roof.
The oven is mainly divided into three sections:
- Shell consisting of side walls and lower steel bowl.
- The hearth consists of a refractory that pulls out the lower bowl.
- The refractory lined or water cooled roof can be made as a ball section or a truncated cone (conical section).
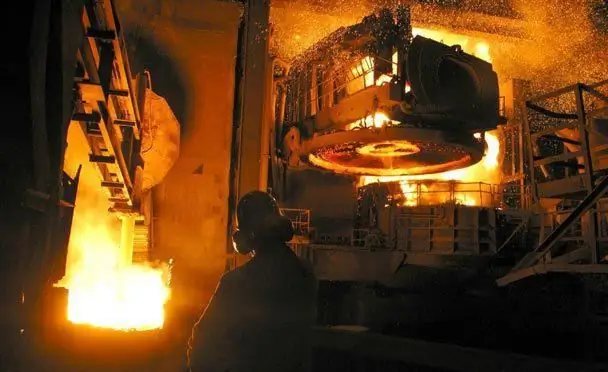
Advantages and disadvantages of the method
This method occupies a leading position in the field of steel production. The steel smelting method is used to create high-quality metal that is either completely devoid of, or contains a small amount of unwanted impurities such as sulfur, phosphorus and oxygen.
The main advantage of the method is the use of electricity for heating, so you can easily control the melting temperature and achieve an incredible rate of heating of the metal. Automated work will becomea pleasant addition to the excellent opportunity for high-quality processing of various scrap metal.
Disadvantages include high power consumption.
Recommended:
Food stainless steel: GOST. How to identify food grade stainless steel? What is the difference between food stainless steel and technical stainless steel?

The article talks about grades of food grade stainless steel. Read how to distinguish food stainless steel from technical
Clothing industry as a branch of light industry. Technologies, equipment and raw materials for the clothing industry
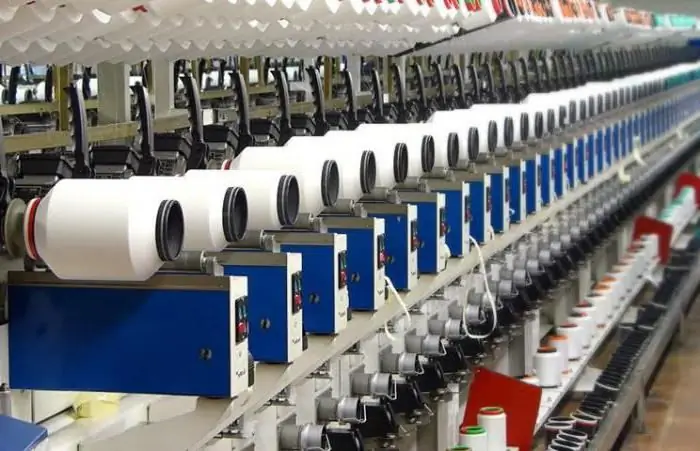
The article is devoted to the clothing industry. The technologies used in this industry, equipment, raw materials, etc. are considered
Obtaining alcohols: methods and raw materials
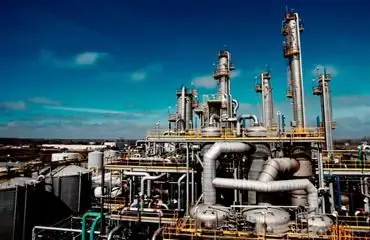
Obtaining alcohols is a rather complicated technological process. There are biochemical and chemical methods for obtaining alcohols. Obtaining methyl alcohol is carried out through the use of various technologies
Production of polyurethane foam: technology, raw materials, equipment
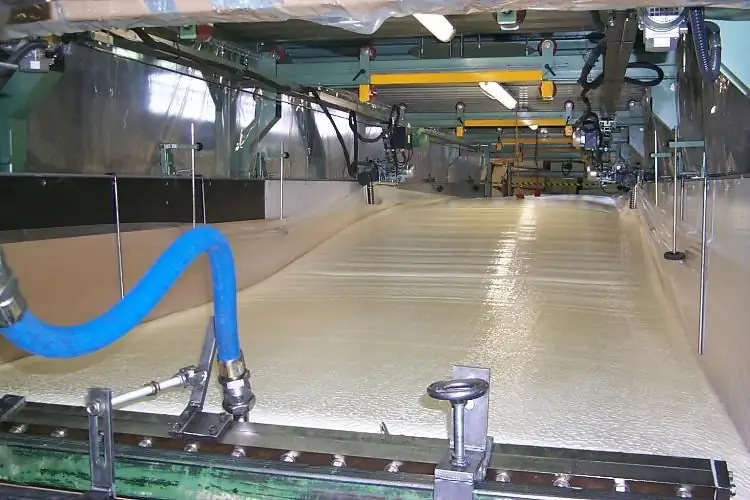
Mounting foam from the usual means of sealing window openings has long passed into the status of a full-fledged building material, which is widely used in a variety of types of work. The variety of applications of this product also determines the need for a differentiated approach to the technologies of its manufacture. However, the differences in foam production methods are more of a cosmetic nature, without affecting the basic technological processes
PVC pipe production: technology, raw materials and equipment
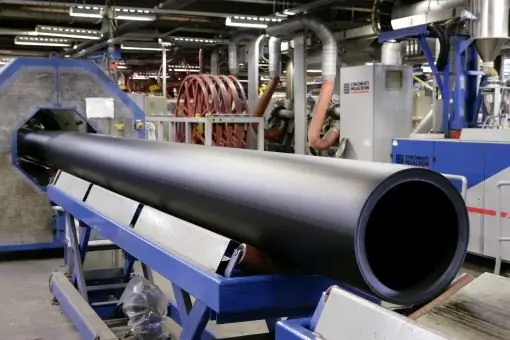
Tubular products based on polyvinyl chloride (PVC) are widely used today in a variety of areas and industries from the private sector to large oil and gas enterprises. But the process of their consolidation on the market was gradual, since the physical and technical properties of the polymer material are inferior to traditional metal counterparts in a number of criteria. However, the modern production of PVC pipes, due to the introduction of advanced technologies, has significantly increased the performance of products