2025 Author: Howard Calhoun | [email protected]. Last modified: 2025-01-24 13:10
The introduction of plasma processing into the industry marked a technological breakthrough and a transition to a qualitatively new level of production. The scope of useful properties of plasma is very extensive. First of all, this is the production of electronic devices and semiconductor devices. Without plasma-chemical etching, modern high-performance personal computers would hardly see the light. But that's not all.
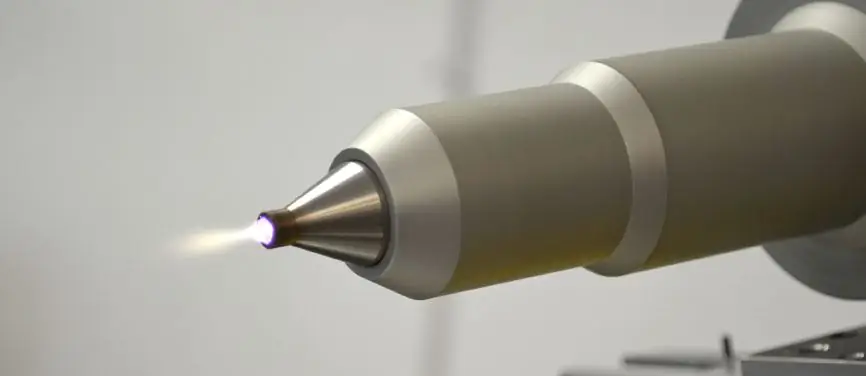
Ion-plasma processing is also used in optics and mechanical engineering for polishing products, applying protective coatings, diffusion saturation of the surface of metals and alloys, as well as for welding and cutting sheet steel. In this paper, the focus is on welding and cutting technologies using plasma.
General provisions
From school physics lessons everyone knows that matter can exist in four states: solid, liquid, gas, and plasma. Most questions arise when trying to represent the last state. But in fact, everything is not so difficult. Plasma is also a gas, only its molecules are, as they say, ionized (that is, separated from electrons). This state can be achievedin various ways: as a result of exposure to high temperatures, as well as as a result of electron bombardment of gas atoms in a vacuum.
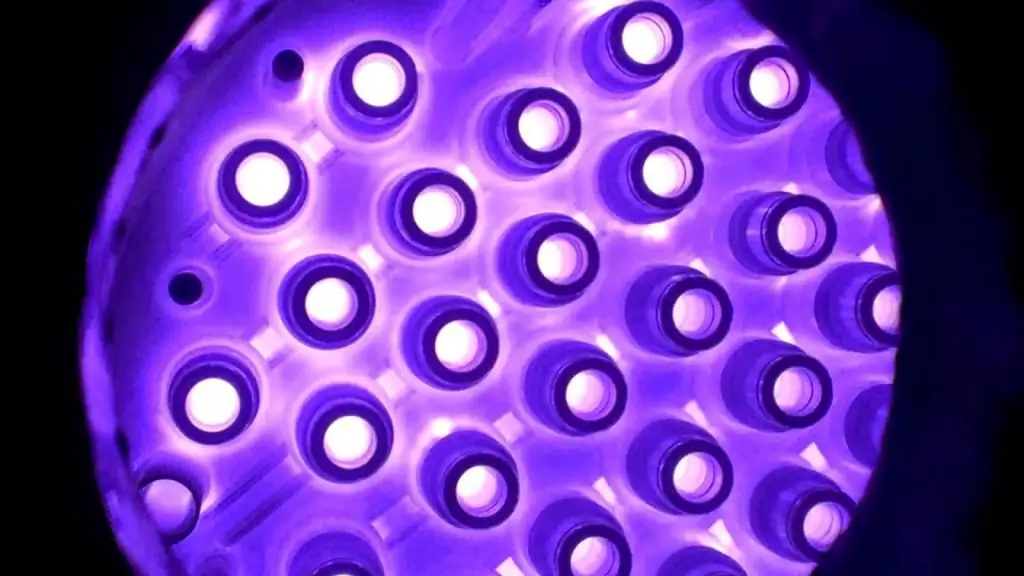
Such a plasma is called low-temperature. This physics of the process is used in the implementation of plasma deposition (etching, saturation) in a vacuum. By placing plasma particles in a magnetic field, they can be given directed motion. As practice has shown, such processing is more effective in a number of parameters of classical operations in mechanical engineering technology (saturation in powder media, flame cutting, pouring with chromium oxide-based paste, and so on).
Types of plasma treatment
Currently, plasma is actively used in almost all industries and the national economy: medicine, engineering, instrumentation, construction, science, and so on.
Pioneer in the use of plasma technology was instrumentation. The industrial application of plasma processing began with the use of the properties of ionized gas to spray all kinds of materials and apply them to linings, as well as to etch channels in order to obtain microcircuits. Depending on some features of the device of technological installations, plasma-chemical etching, ion-chemical, and ion-beam etching are distinguished.
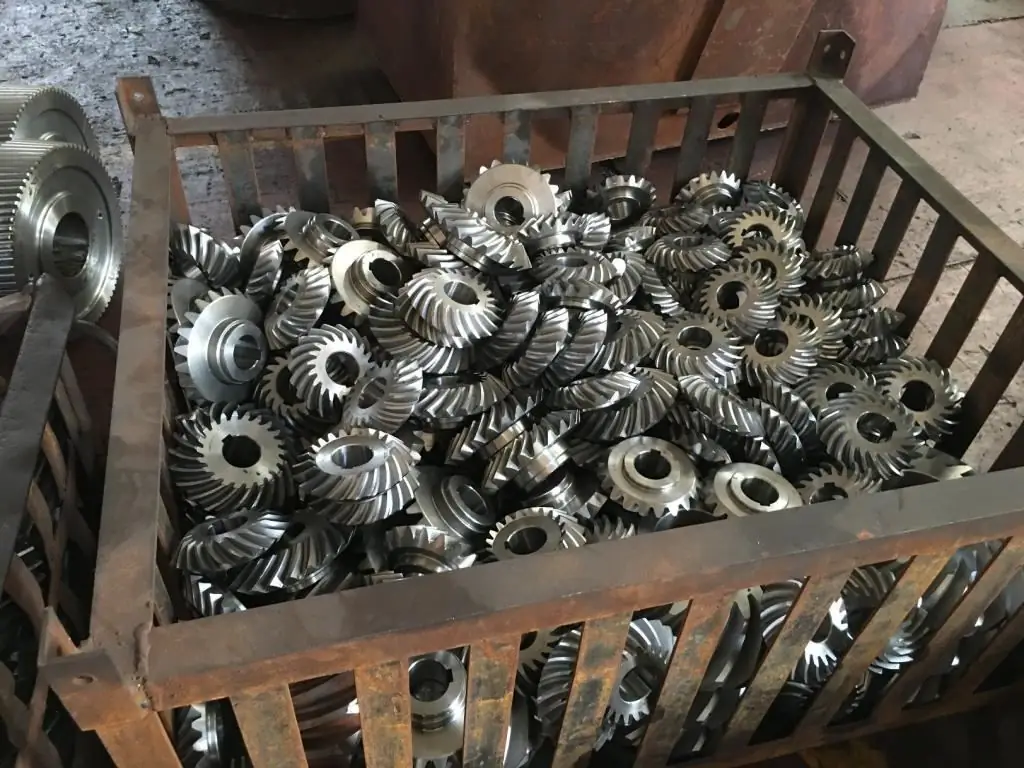
The development of plasma is an incredibly valuable contribution to the development of technology and the improvement, without exaggeration, of the quality of life of all mankind. With the passagetime, the field of application of gas ions has expanded. And today, plasma processing (in one form or another) is used to create materials with special properties (heat resistance, surface hardness, corrosion resistance, and so on), for effective metal cutting, for welding, for polishing surfaces and eliminating microroughness.
This list is not limited to the use of technologies based on the effect of plasma on the treated surface. Currently, the means and methods of plasma spraying are being actively developed using various materials and processing modes in order to achieve maximum mechanical and physical properties.
The Essence of Plasma Welding
Unlike installations of ion-plasma saturation and sputtering, in this case, plasma treatment is carried out using high-temperature plasma. The efficiency of this method is higher than when using traditional welding methods (flame, electric arc, submerged arc welding, and so on). As a working gas mixture, as a rule, ordinary atmospheric air under pressure is used. Thus, this technique is characterized by the absence of costs for consumable gases.
Advantages of plasma welding
Compared to traditional welding, using a plasma welding machine is safer. The reason is quite clear - the use of atmospheric oxygen under pressure as a working gas. Currently, safety in production is given very close attention by the ownersbusinesses, executives and regulators.
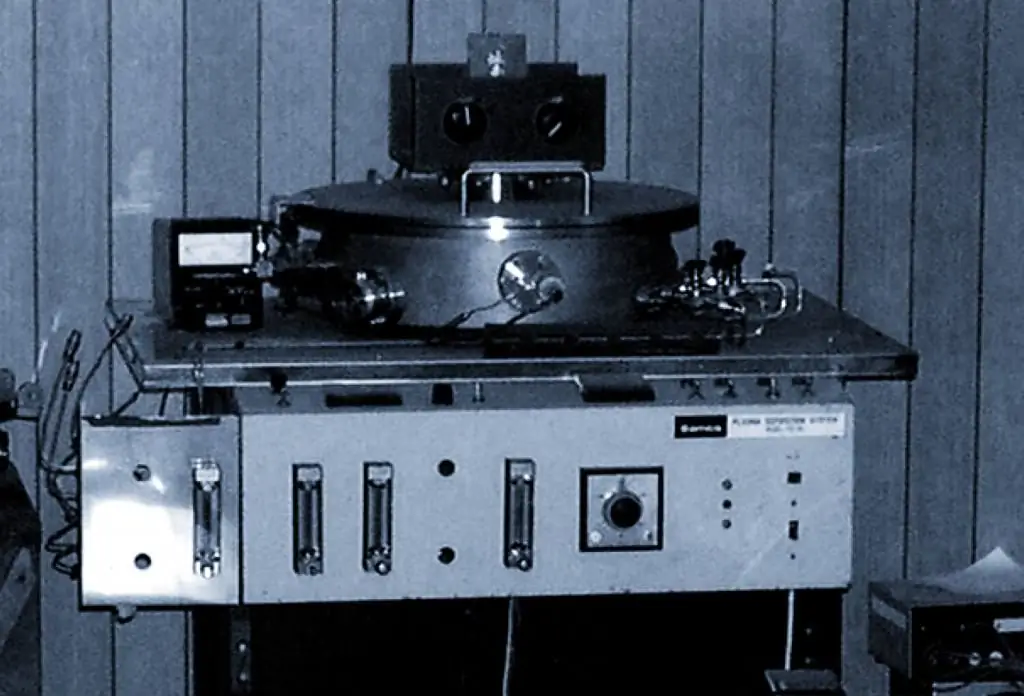
Another very important advantage is the high quality of the weld (minimum sagging, lack of penetration and other defects). Although, in order to learn how to skillfully use a plasma welding machine, many months of practice are needed. Only in this case, the weld and the joints as a whole will meet high standards.
This technology has a number of other advantages. Among them: high speed of the welding process (productivity increases), low consumption of energy resources (electricity), high connection accuracy, no deformation and warping.
Plasma cutting equipment
The process itself is very sensitive to the current sources used. Therefore, it is allowed to use only very high-quality and reliable transformers that demonstrate the constancy of the output voltage. Step-down transformers are used to convert high input voltage to low output voltage. The cost of such equipment is several times less than the cost of traditional converters for electric arc welding. They are also more economical.
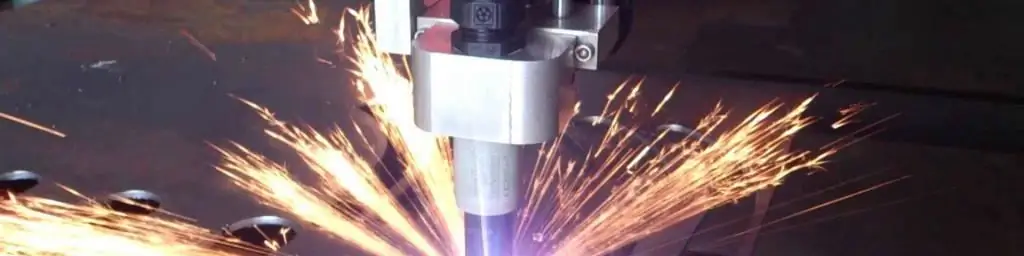
Plasma cutting equipment is easy to use. Therefore, if you have at least minimal experience and skills, you can do all the welding work yourself.
Plasma Welding Technology
Depending on the supply voltage, plasma welding is divided into micro welding, welding intomedium and high current. The process itself is based on the action of a directed flow of high-temperature plasma on an electron and on the surfaces to be welded. The electrode melts, resulting in a permanent welding joint.
Plasma cutting
Plasma cutting is a process in which a metal is cut into its component parts by a directed stream of high-temperature plasma. This technology provides a perfectly even cut line. After a plasma cutter, the need for additional processing of the contour of products (whether sheet material or pipe products) is eliminated.
The process can be carried out both with a manual cutter and with a plasma cutting machine for cutting sheet steel. Plasma is formed when an electric arc is applied to the working gas flow. As a result of significant local heating, ionization occurs (separation of negatively charged electrons from positively charged atoms).
Plasma cutting applications
The jet of high-temperature plasma has a very high energy. Its temperature is so high that it literally evaporates many metals and alloys with ease. This technology is mainly used for cutting steel sheets, sheets of aluminum, bronze, brass and even titanium. Moreover, the thickness of the sheet can be very different. This will not affect the quality of the cut line - it will be perfectly smooth and even, without streaks.
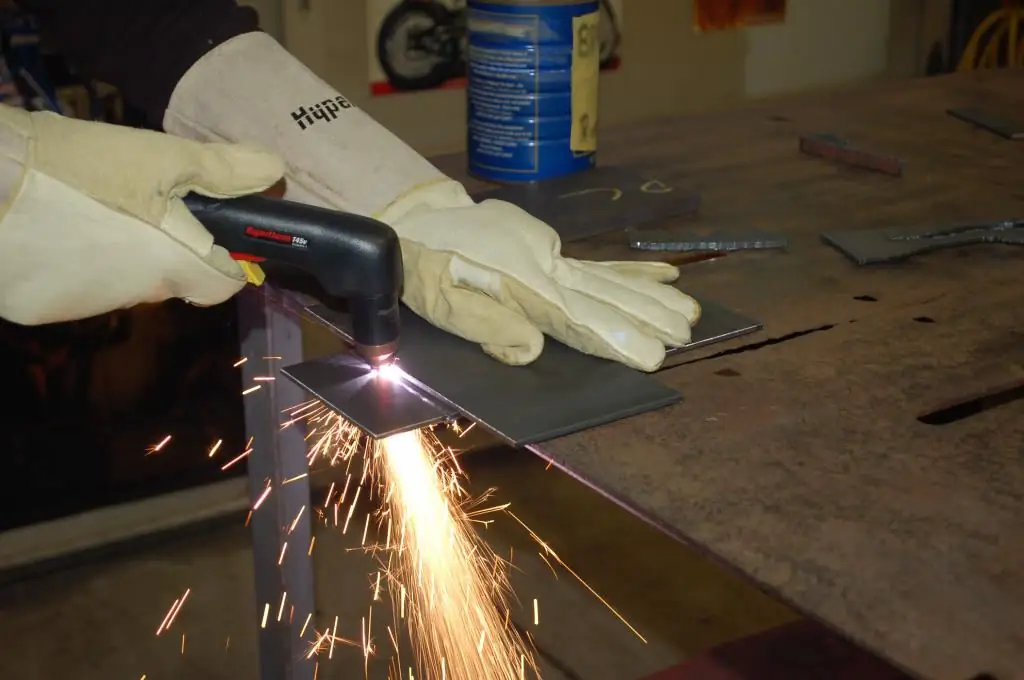
However, it should be noted that in order to obtain high-quality and evencut when working with thick-walled material, you must use a plasma cutting machine. The power of a handheld torch will not be enough to cut metal with a thickness of 5 to 30 millimeters.
Gas cutting or plasma cutting?
What type of cutting and cutting of metal should be preferred? Which is better: oxy-fuel cutting or plasma cutting technology? The second option is perhaps more versatile, as it is suitable for almost any material (even those prone to oxidation at elevated temperatures). In addition, plasma cutting is carried out using ordinary atmospheric air, which means that it does not require the purchase of expensive consumables. And the cut line is perfectly even and does not require refinement. All this in combination significantly reduces the cost of the product and makes products more competitive.
Plasma cutting materials
It should be taken into account the fact that the maximum allowable thickness of the processed metal or alloy depends on the material itself or its grade. Based on many years of production experience and laboratory research experience, experts give the following recommendations on the thickness of the processed materials: cast iron - no more than nine centimeters, steel (regardless of the chemical composition and the presence of alloying elements) - no more than five centimeters, copper and alloys based on it - no more than eight centimeters, aluminum and its alloys - no more than 12 centimeters.
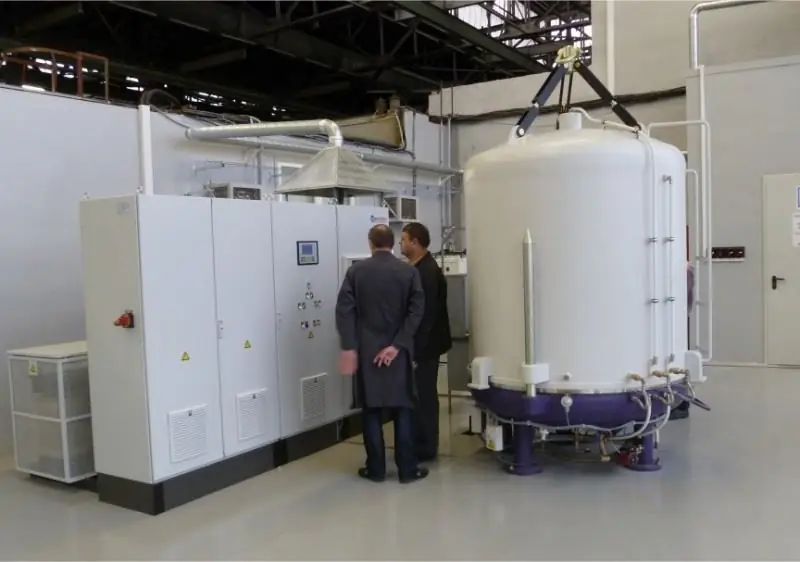
All listed values are typical for manualprocessing. An example of such a domestically produced unit is the Gorynych plasma apparatus. It is much cheaper than foreign analogues, while it is in no way inferior, and perhaps even superior to them in quality. A wide range of devices from this manufacturer is presented on the market, which are designed to perform various jobs (domestic welding, cutting and welding of metals of various thicknesses, inclusive). Thicker sheets can only be processed on high power machines.
Existing plasma cutting methods
All existing methods of plasma cutting can be divided into jet and arc. Moreover, it does not matter at all whether a hand cutter or a CNC plasma cutting and cutting machine is used. In the first case, all the necessary conditions for gas ionization are implemented in the cutter itself. Such a device can process almost any materials (metals and non-metals). In the second case, the material being processed must have electrical conductivity (otherwise, no electric arc will occur and gas ionization will occur).
In addition to differences in the way plasma is formed, plasma processing can also be classified according to the technological features of cutting into simple (without the use of auxiliary substances), processing with water and processing in a protective gas environment. The last two methods allow you to significantly increase the cutting speed and at the same time not be afraid of metal oxidation.
Recommended:
Meat processing enterprises, meat processing plants in Russia: rating, products
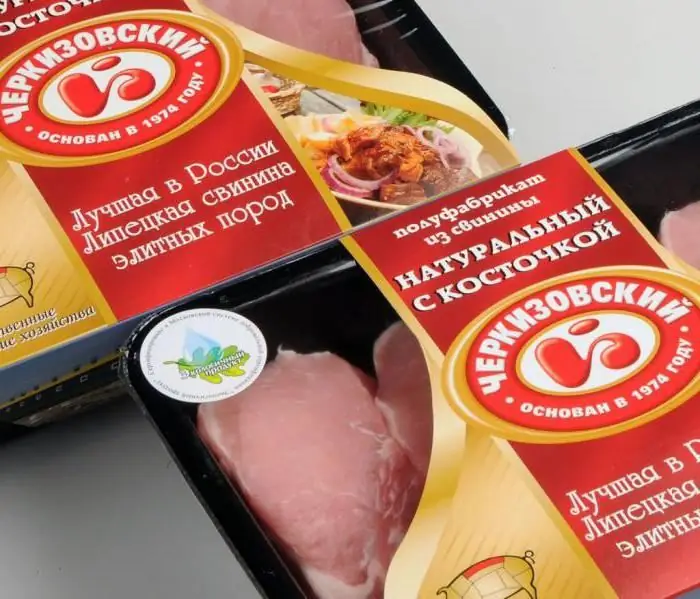
Today, a huge number of enterprises are engaged in meat processing. Moreover, some are known throughout the country, and some - only on the territory of their region. We offer to evaluate the most powerful meat processing enterprises in Russia in terms of productivity, which have the largest revenues and high turnover. Below is a list of such companies. It is based on consumer feedback
Meat: processing. Equipment for meat and poultry processing. Production, storage and processing of meat
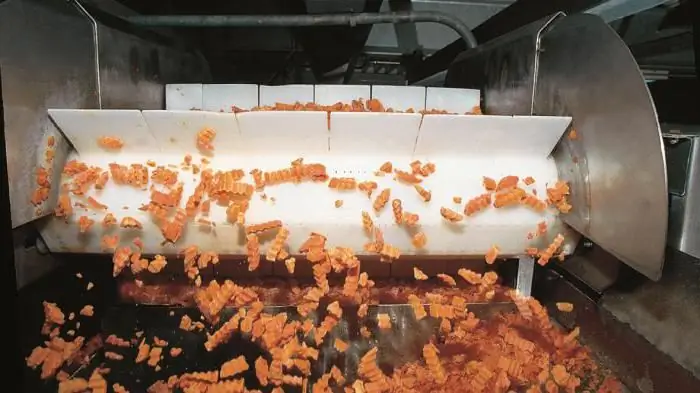
Information of state statistics show that the volume of meat, milk and poultry consumed by the population has significantly decreased in recent years. This is caused not only by the pricing policy of manufacturers, but also by the banal shortage of these products, the required volumes of which simply do not have time to produce. But meat, the processing of which is an extremely profitable business, is very important for human he alth
Amur Gas Processing Plant (Amur Gas Processing Plant) - the largest construction site in Russia
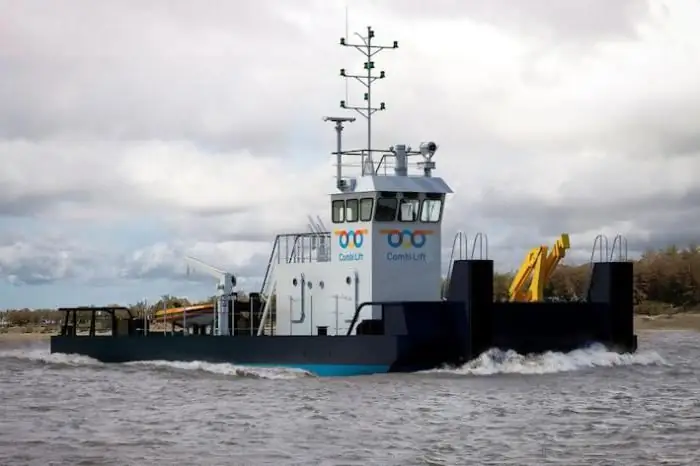
Amur GPP in 2017 is the largest construction project in Russia. After commissioning, this enterprise will supply the market with 60 million cubic meters of helium alone. Among other things, this plant is an important component of the grandiose project "Power of Siberia"
Materials released to production (posting). Accounting for the disposal of materials. accounting entries
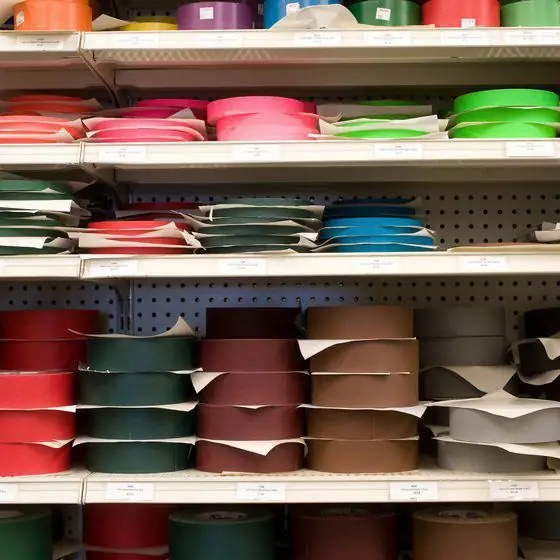
Most of all existing enterprises can not do without inventories used to produce products, provide services or perform work. Since inventories are the most liquid assets of the enterprise, their correct accounting is extremely important
Drilling is a type of mechanical processing of materials. drilling technology. Drilling equipment

Drilling is one of the types of material machining by cutting. This method uses a special cutting tool - a drill. With it, you can make a hole of different diameters, as well as depths. In addition, it is possible to create multifaceted holes with different cross sections