2025 Author: Howard Calhoun | [email protected]. Last modified: 2025-01-24 13:10
When furnishing a home or making repairs to a home, you can lay the piping system yourself. If we are talking about steel communications, then you can use electric welding. As a result, it is possible to obtain a strong connection, which is obtained due to the occurrence of thermochemical processes, while using conductive electrodes.
Whatever welding works, they require experience and knowledge from the master, which are applied in the process. If you are just learning, then you can first get acquainted with the theoretical side of the issue. As with steel, polypropylene piping also requires appropriate welding equipment. However, practice shows that the latest technology is much easier than the one discussed in the article.
Preparation before work
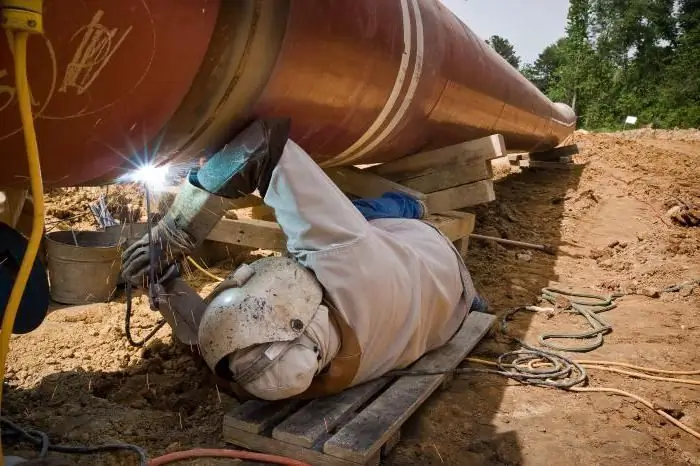
Pipeline welding begins with surface preparation. It is important to make sure that it is dry and even. The next step is to choose a power source. This affects the quality of education. It maybe compact inverters or heavy transformers. With their help, high voltage can be converted to low voltage in the secondary circuit.
For domestic work, electric welding will be the most preferred option. The transformer is easier to operate. It has the advantages expressed in non-failure operation and endurance. Inverter equipment has less impressive dimensions, in addition, it allows you to adjust the operating modes.
Varieties of welded joints
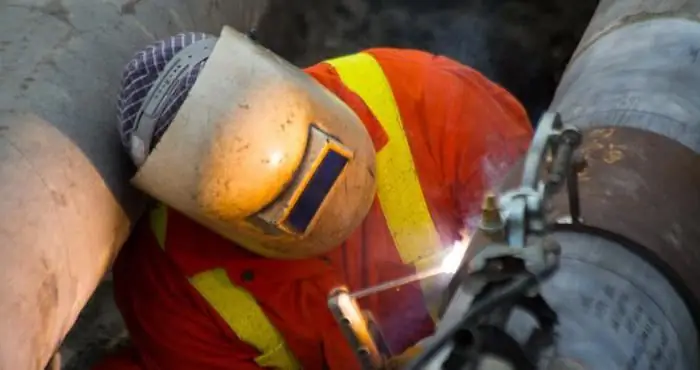
The following types of joints are used today in welding piping systems:
- butt;
- overlap;
- corner joint;
- T-joint.
In this case, the position of the seam can be vertical or horizontal, as well as ceiling or bottom. The lowest position is considered the most advantageous, therefore, if re-welding is possible, this method should be preferred. Welding of pipelines when laying communications usually involves the use of a butt joint. In this case, it is important to carry out the edges over the entire thickness. For thick-walled pipes, double seams are made - external and internal. To reduce the influx of metal from the inside, when performing work, the electrode must be held at an angle of 45 ° to the horizontal plane.
What else is important to remember when preparing
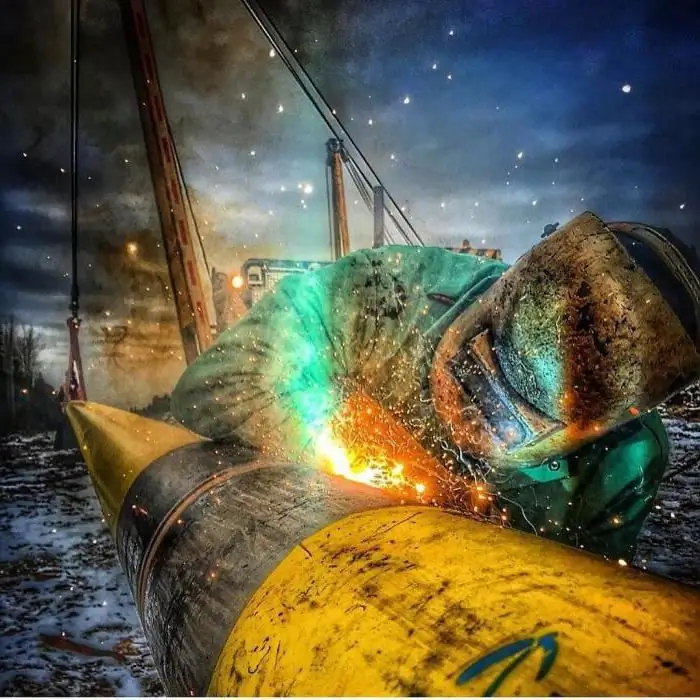
Before starting manual welding, preparations must be made. It is important to check the compliance of the pipes with the requirements. Productsmust correspond to the dimensions, they must not be deformed, they must not have defects. You need to make sure there is no difference in wall thickness.
The pipe material must match the chemical composition. Edges should be free of dirt and rust. The butt is measured, as is the angle of opening of the edge, as well as the amount of blunting. According to the standards, the amount of blunting can be equal to the limit from 2 to 2.5 mm. As for the bevel angle, it can be 70 °. If inconsistencies were identified, then it is necessary to carry out machining of the edges.
Installation of tacks

Welding process pipelines should involve the installation of tacks. They are an integral part of the seam, and an electrode is used for execution, which will be used when making the seam. If we are talking about pipes whose diameter does not exceed 300 mm, then 4 tacks are made, they should be distributed around the circumference as evenly as possible.
When you have to work with a pipe of a more impressive diameter, the tacks are located in increments of 250 mm. The recommended length of the tack is 50mm while its width is 4mm.
Features of electric welding
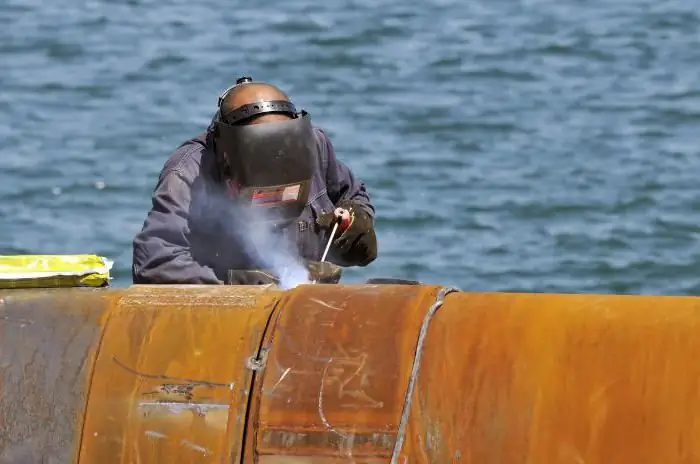
Welding of pipelines must be carried out according to a certain algorithm. It is important to pay special attention to the turning joints. If you have to cook in difficult conditions, then you should keep a small mirror on hand. If there is a need, then the endthe electrode must be bent, doing the work with the undamaged part.
A fairly common situation is welding at an angle of 30 ° to the surface of the product. The overlay of a seam at the same time is carried out on a circle. It can be single-layer at the joints of low-alloy steel products. Additional strength can be achieved by performing a second seam. The more impressive the wall of the pipe, the more passes should be made, there should be 2 or more.
Large-diameter pipes should be welded in a circle. Their connection is carried out up to half the seam. Then the sections are cleaned of slag and covered with the next seam at a distance of 1.5 cm from the previous one. It is necessary to complete the work by connecting the weld with a slight overlap. It is not recommended to carry out work without slag removal, as it will not work to achieve a good result.
Quality check
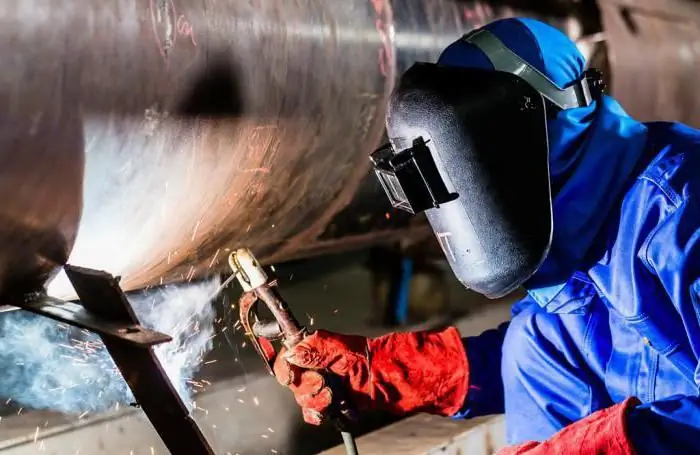
When welding pipelines, at the final stage you must make sure that the quality of the welds is perfect. Invisible cracks can be detected using a soapy solution, which is applied with a brush to the welded joints. Air is then introduced into the system. If there are unfinished seams or places, then you can notice them by the bubbles.
Turn welding method
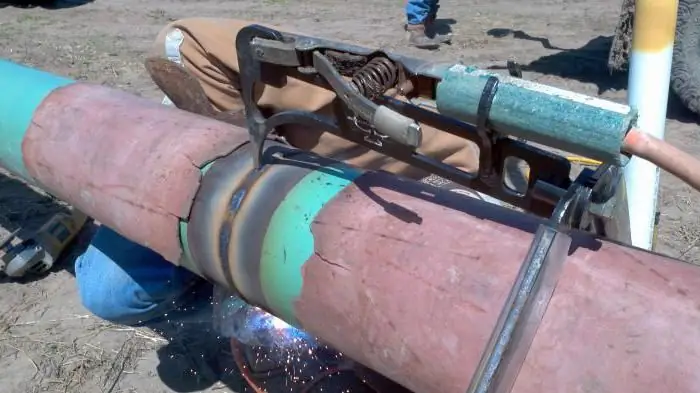
Welding of process pipelines usually involves the maximum number of welds made in the down position. This indicates that the rotation method can be used. If the pipe has a thicknesswalls up to 12 mm, then a triple seam can be made. The first layer is welded with an electrode, the thickness of the rod of which varies from 2 to 4 mm. All subsequent layers can be welded with electrodes of a larger diameter.
Initially, the joint should be divided into 4 parts. Welding is performed in the first and second sectors, which are located in the upper part of the pipe. Then the pipe turns, and the master has to make a joint along the third and fourth sectors. The pipe at the next stage should be turned again and boiled 1 and 2 sectors. When repeating the turn, the second layer is applied in sectors 3 and 4. The last layer should be applied in one direction, while the pipe should turn all the time.
Automatic welding
The pipeline welding process can be carried out in large-scale production, where high productivity is important. Under such conditions, manual welding will be laborious, so welding machines are used for work. All processes will take place automatically.
Welding is carried out by welding wire, which is unwound from the coil and fed into the work area. Protective gases are also automatically supplied to the working area. If the work cannot be automated, semi-automatic welding is used.
Alternative Welding Methods
Welding and installation of pipelines can be carried out using gas welding. This method involves heating the edges to the melting temperature. At the same time, the filler rod is melted, as well as the metal used to fill the seam. As a resultit is possible to get a sufficiently strong seam that will have a protruding bead.
Gas welding is carried out using a mixture of oxygen and acetylene. The main tools are a torch and a cutter. The body of the first has two channels through which gases are supplied to the mixing chamber. The master at the same time regulates the gas supply when welding different materials.
Welding of steel pipelines can also be carried out using the induction method. This technology involves heating the elements with eddy currents. The edges are connected by pressure rollers. This type of welding is used in manufacturing and engineering.
Recommendations for choosing electrodes
When welding pipelines, GOST 16037-80 must be observed. They also spelled out the features of the choice of electrodes. The latter are metal rods made of welding wire. Its thickness can vary from 2 to 5 mm. The surface is covered with a coating, which is applied in a thick or thin layer. In the latter case, the mass of the coating varies from 1 to 2% of the mass of the rod. If we are talking about a thick layer, then its mass can vary from 20 to 30%.
The main task of coating is the formation of slag, which has the form of a non-metallic alloy of less weight compared to metal. Slag floats to the top during welding, creating a protective coating. After connecting the pipelines by welding, the slag must be knocked down. Once the crust becomes brittle, it can be removed fairly easily.
Electrodes today are produced with differenttypes of coatings, the latter of which are designed to solve specific problems. For example, cellulose coating is used to weld pipelines of impressive diameter. With the help of such electrodes, it is possible to create circular and vertical seams.
On sale you can also find electrodes with a rutile coating, which is easily ignited and forms a highly brittle slag crust. With the help of such electrodes, it is possible to create marketable seams, corner seams, install tacks and weld root seams. This allows you to get connections with a beautiful appearance.
Pipeline welding technology may involve the use of rutile-acid coated electrodes. This material is characterized by ease of peeling, and the consumption of electrodes is low, which allows saving. The rutile-cellulose coating is suitable for seaming in any position, which can be directed upwards, which is the most difficult.
High viscosity seam can be obtained with basic electrode coating. As a result, it is possible to form joints that do not crack. The material is excellent for working with thick-walled pipes and products that will be operated in difficult conditions.
Repair by welding
You can repair pipelines by welding. To do this, the defective area must be cleaned mechanically. Can be cleaned with sandblasting, abrasive wheels, grinders and disc wire brushes.
Repair by welding involves surfacing on defective areas. Damagemay be caused by corrosion, the surface may be scratched, burred and notched. In order to clarify the wall thickness, it is necessary to carry out measuring and visual control. Additional physical methods that will not be destructive are acceptable.
Defects with a depth of 0.2 mm can be removed by grinding. The norms for welding pipelines in this case require the use of a manual method using electrodes with the main type of coating. For welding the first filling seam, it is recommended to use electrodes with a diameter of up to 3.2 mm. For facing and filling joints, the electrode diameter can vary from 3 to 4 mm.
The technological process of pipeline welding involves the annealing of electrodes. It is acceptable to use electrodes calcined in stationary conditions. At the same time, they must be delivered to the place of production in sealed containers. Storage of electrodes in accordance with state standards should be carried out in heated dry rooms, the temperature of which does not fall below +15 °C.
The defective area must be heated with electric heating devices before welding. You can use the induction method, which ensures uniform heating. Use of gas torches or heaters is admissible. Welding can be done using the inverter method. Surfacing is carried out on direct current of reverse polarity.
The arc is ignited at the edges of the sample of the defective area. Welding of filling layersrectilinear or round shape is carried out by a narrow roller. The scheme used is counter-symmetric. The direction of movement in each next seam should be oncoming. The width of the filling first layers can vary from 4 to 6 mm. All subsequent layers have a width of 8 to 10 mm.
Conclusion
If you have the appropriate equipment, you can weld the pipeline systems yourself. However, it is important to choose the right electrodes, while taking into account the properties of the materials that underlie the pipes. For example, in order to join carbon steel pipes, you should stock up on welding consumables with a basic or rutile coating.
If the seams are made on galvanized steel pipes, then electrodes should be prepared for welding galvanized pipes. The main feature of welding when working with galvanized pipes is the boiling point of zinc. It is lower than that which is true for steel. This indicates that the zinc coating will evaporate when heated.
Recommended:
Gas pipeline to China. Project and scheme of a gas pipeline to China
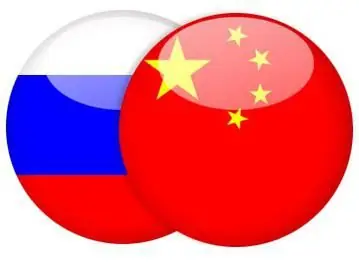
Russia and China have signed a long-awaited gas contract. To whom is it beneficial? Will the fact of its signing affect the geopolitical situation?
Welding of ultrasonic plastics, plastics, metals, polymeric materials, aluminum profiles. Ultrasonic welding: technology, harmful factors
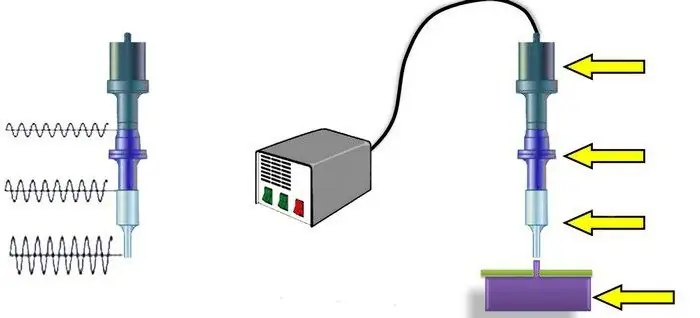
Ultrasonic welding of metals is a process during which a permanent joint is obtained in the solid phase. The formation of juvenile areas (in which bonds are formed) and the contact between them occur under the influence of a special tool
Laying a gas pipeline: methods, equipment, requirements. Gas pipeline security zone
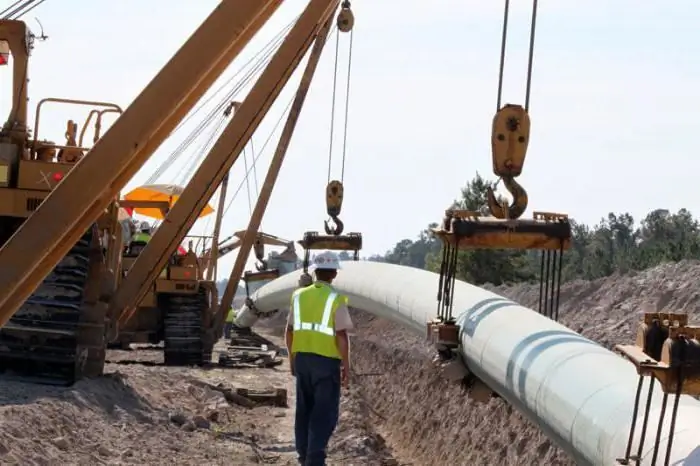
Laying of the gas pipeline can be done by underground and ground methods. When choosing equipment for such systems, safety standards should be followed. Actually, the laying of highways is carried out with strict observance of all the required technologies
Thermite welding: technology. The practice of thermite welding in everyday life and in the electrical industry
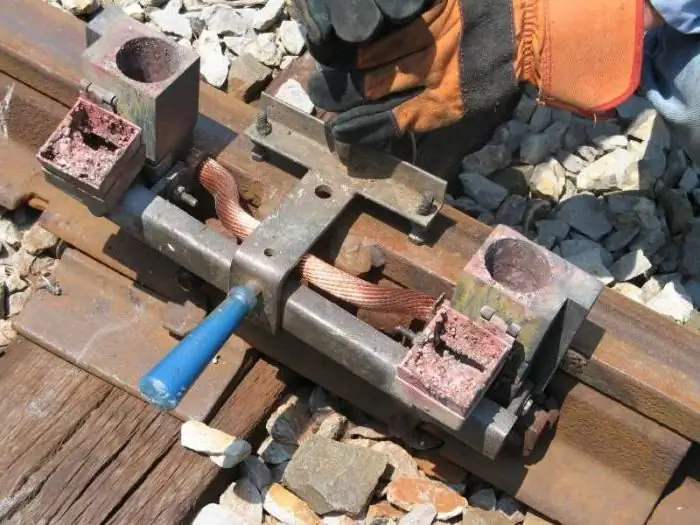
The article is devoted to thermite welding technology. The features of this method, the equipment used, the nuances of use, etc. are considered
Gas pipeline to Crimea. "Krasnodar Territory - Crimea" - the main gas pipeline with a length of 400 km
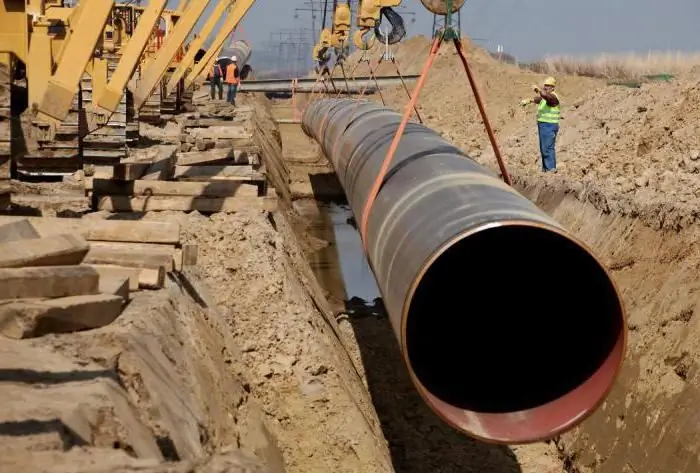
The gas pipeline to Crimea was commissioned in December 2016. Its construction took place at an accelerated pace in order to solve the main problem of the Crimean gas transportation system: the lack of own gas to fully supply the peninsula due to increased consumption