2025 Author: Howard Calhoun | [email protected]. Last modified: 2025-01-24 13:10
Tubular products based on polyvinyl chloride (PVC) are widely used today in a variety of areas and industries from the private sector to large oil and gas enterprises. But the process of their consolidation on the market was gradual, since the physical and technical properties of the polymer material are inferior to traditional metal counterparts in a number of criteria. Nevertheless, the modern production of PVC pipes, due to the introduction of advanced technologies, has significantly increased the performance of products in a wide range of evaluation parameters.
Raw material base for production
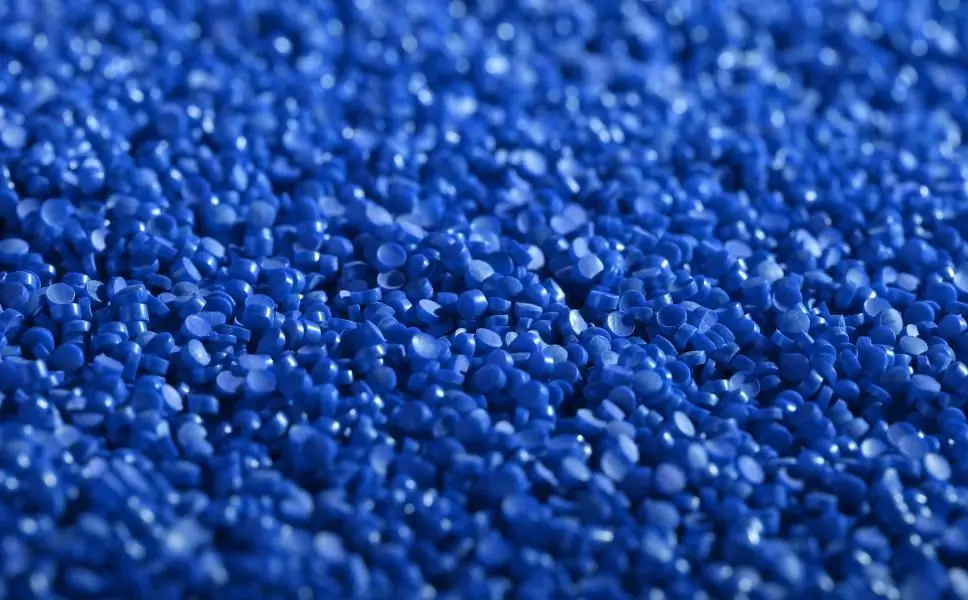
The quality of the final product is largely laid down at the stage of selecting the elements that will form the structural basis of the product. It is not always necessary to talk about the need to improve operational properties - for different segmentsapplications, some qualities are important and others are not obligatory. One way or another, the general group of consumables in the manufacture of plastic pipes is polymer raw materials, which are also diverse. Along with polyvinyl chloride, for example, polypropylene and polybutene can be used, but they are often labeled as PVC. For high quality pipes, granular polymers are used - for example, polypropylene copolymer. Derivatives from such raw materials are characterized by high mechanical resistance and are suitable for communications with high requirements for pressure loads. But also recycled raw materials in the form of chemical industry waste can provide decent production results if they are supplemented with fiberglass-based reinforcing inclusions.
PVC pipe technology
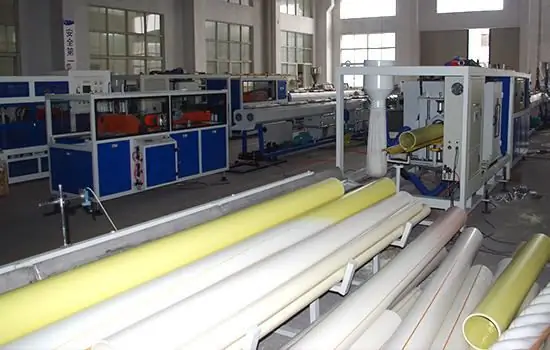
The most developed method is the extrusion method, which is also used in the manufacture of plastic bags. Its essence lies in the process of squeezing the plastic mass into a given shape under the standard temperature regime. In more detail, the PVC pipe production technology is as follows:
- Sorting and directing raw materials to the hopper of the extruder. The mass received in the processing compartment is crushed and melted under thermal influence.
- Already in the molten form, the polymer structure is squeezed out through a nozzle of a certain format. At this stage, future dimensional parameters and the overall configuration of the pipe device are laid.
- Immediately after moldingthe workpiece is sent to the cooling zone.
- Under the influence of high pressure, individual pipe characteristics are corrected, calibrated and final shaped.
- Cutting, packing and marking. The nature of this stage is determined by the requirements for the form of delivery.
Extruder device
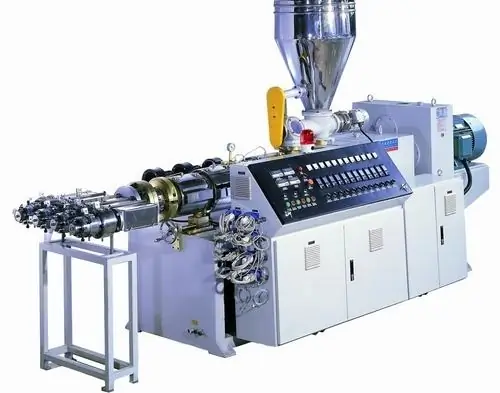
This is far from the only functional unit of production support, but its role in the manufacture of finished products is decisive. Pipe manufacturing plants use extruders to continuously process raw materials into a single melt, followed by product formation. The loaded raw material goes through several technological operations - from the hopper to the hot cylinder for heating and the screw. The most common single screw plastic extruders are based on a single frame with a vertical gearbox. An asynchronous electric motor is usually used as a power supply source, driving the auger through a shaft. The whole process is controlled by the operator through the remote control. Modern installations are also provided with automation that controls the operations of plastic feeding, heating and extrusion, so the functions of the operating personnel can be reduced to general control.
Complete complete production line
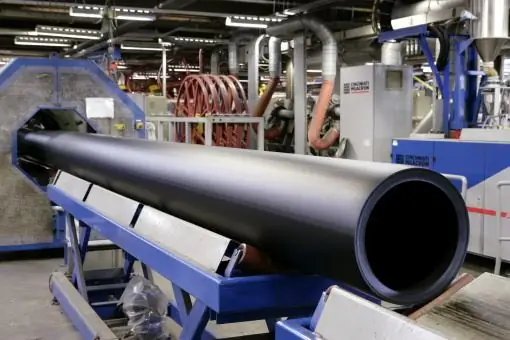
On the basis of extruder machines, manufacturers of industrial equipment are trying to create multifunctional lines that support the full range of technological operations. But since it is fundamental toSince this concept is structural optimization and the minimum cost of equipment, the disadvantages of such a solution are also obvious in the form of low productivity, and sometimes functional limitations. A full-fledged plastic pipe production line includes several modules, among which the following can be distinguished:
- Machine for direct production of plastic pipes. Includes the same extruder, as well as a conveyor belt, a heat gun, an automatic polymer pellet mixer, a vacuum forming unit, an accumulator, a cooling system.
- Device for cutting pipes. Usually cutters support the ability to work with adjustable parameters in accordance with the specification.
- Feeding system. A transport unit that transports raw materials and finished products between process areas.
- Loader stacker. Units that perform the functions of automatic storage of finished and cut pipes.
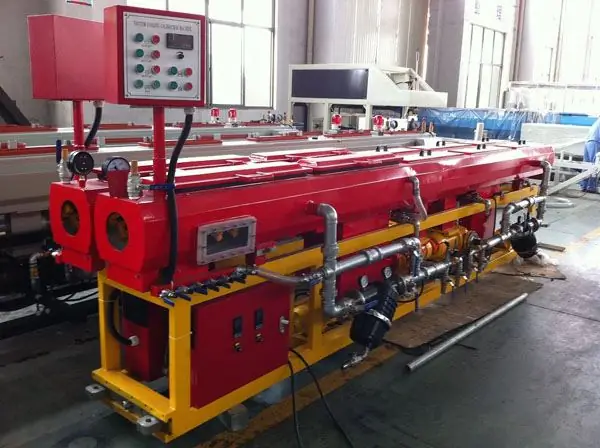
By-products of production
In large industries, chlorine, hydrogen and caustic soda are inevitably released as a result of the electrolysis operation. However, today this is not a problem, since waste is sent directly from the places of production of PVC pipes either to disposal sites or to recycling centers. In the second case, for example, hydrogen can be used in pyrolysis processes, which can be organized at the same polymer industry plants.
Russian PVC pipe manufacturers
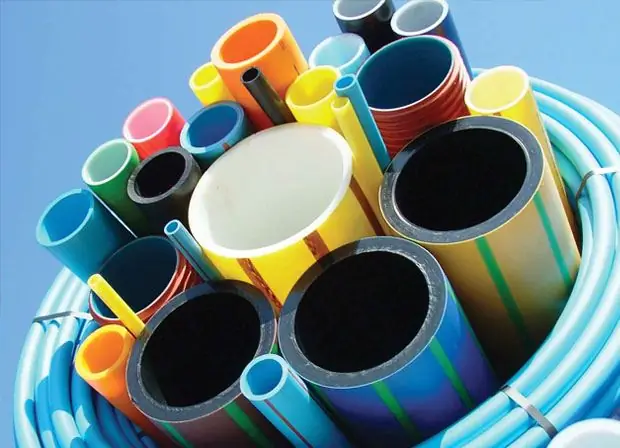
At the moment, Sayanskkhimplast holds the leading position in Russia in the PVC products manufacturing sector. The production capacity of this plant is about 340 thousand tons. The competition for this enterprise is the Bashkir Soda Company (BSC), the potential for manufacturing polymer products of which is 220 thousand tons. Among the specialized plants for the production of PVC pipes, PRO Aqua can be noted. This company is engaged in the development and direct production of components for pipes for various purposes - including sewer, water, gas, etc.
Industry outlook
The Russian petrochemical industry traditionally lags behind foreign participants in the global PVC products market in terms of technological development. However, experts expect an intensive rise in the development of enterprises in this segment in the near future, which is associated with an increase in demand for PVC pipes. The production facilities also do not stand still and are already being modernized in accordance with the new principles of manufacturing products. More modern devices are being introduced to ensure technological processes with plastic, automatic controls and, in general, the configuration of the logistics of plants in the chemical industry is changing.
Conclusion
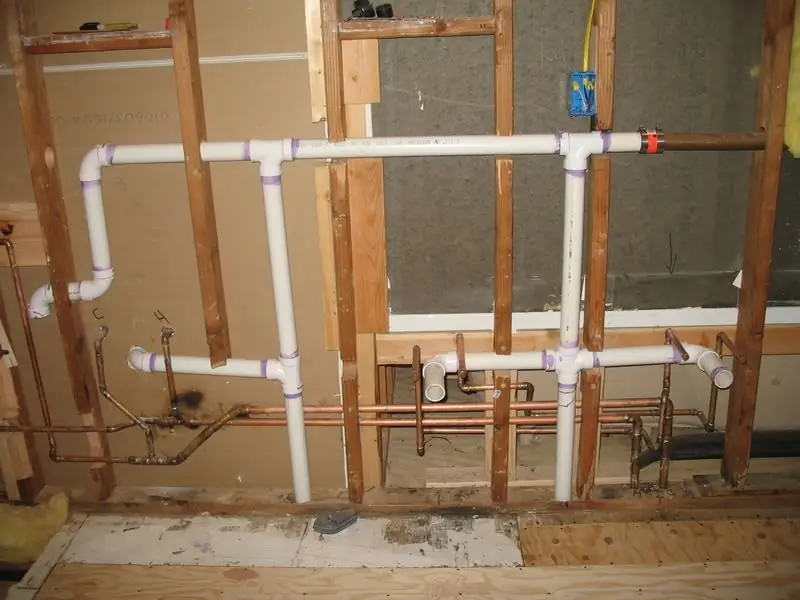
Obviously, much in the development of PVC pipe manufacturing technologies will depend on the market situation. Active dissemination of thisproducts in recent years is also not without barriers associated with the shortcomings of such products. Another thing is that the modern production of PVC pipes demonstrates an increase in their competitive advantages. Suffice it to note the breakthrough associated with the expansion of the scope of pipes with thermally insulated coatings. Also, quite recently it was impossible to use plastic pipelines for servicing gaseous media under high pressure, but today this restriction applies only to certain types of products.
Recommended:
Steel smelting: technology, methods, raw materials
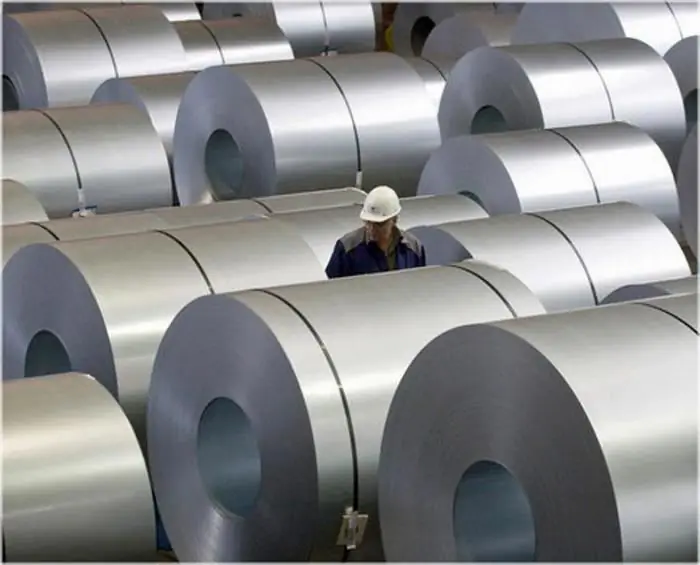
Iron ore is obtained in the usual way: open or underground mining and subsequent transportation for initial preparation, where the material is crushed, washed and processed
Clothing industry as a branch of light industry. Technologies, equipment and raw materials for the clothing industry
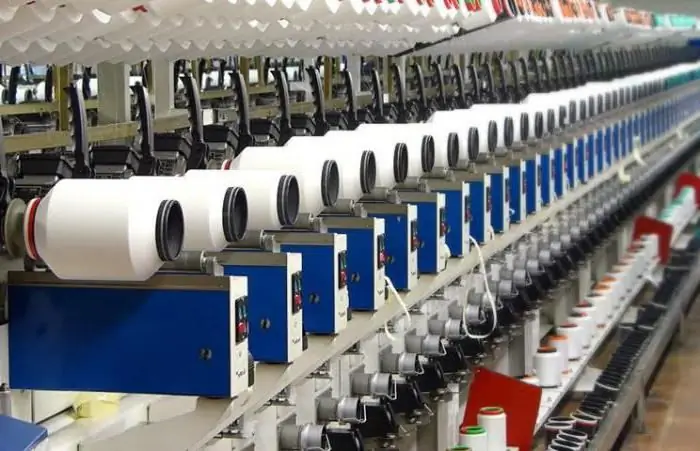
The article is devoted to the clothing industry. The technologies used in this industry, equipment, raw materials, etc. are considered
Raw materials are the basis of production
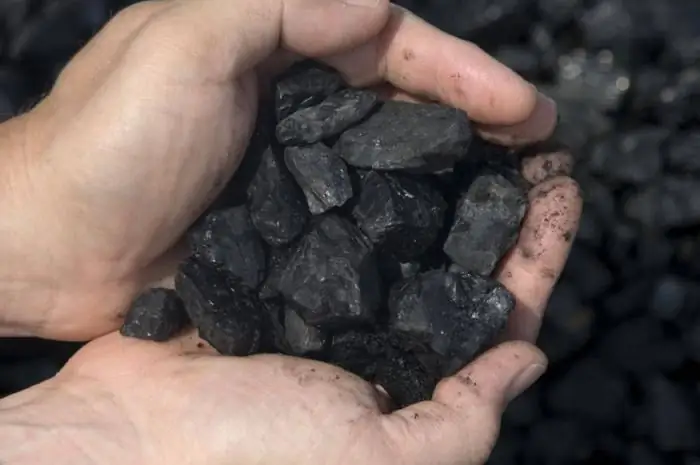
Raw material is a material intended for further processing in production. In fact, it is with him that the release of any product begins
Kvass production: necessary equipment, raw materials and recipes
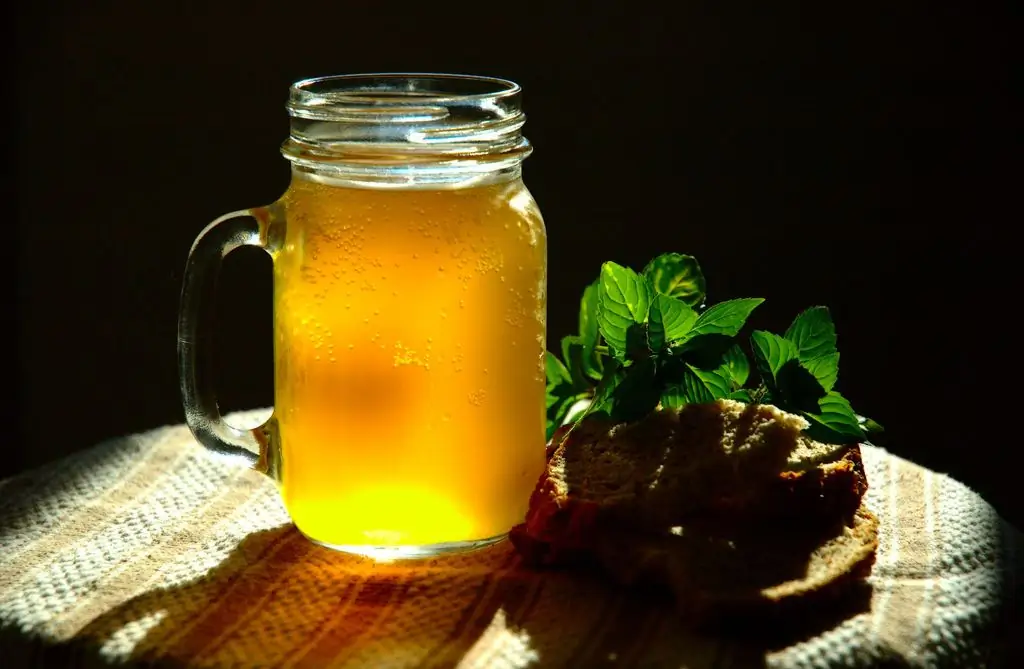
Features of the production and marketing of live kvass. Home or industrial production. The choice of premises and basic equipment, depending on the expected scale of the production of the drink. Technological process of production at the plant. Examples of recipes for home or small production
Production of polyurethane foam: technology, raw materials, equipment
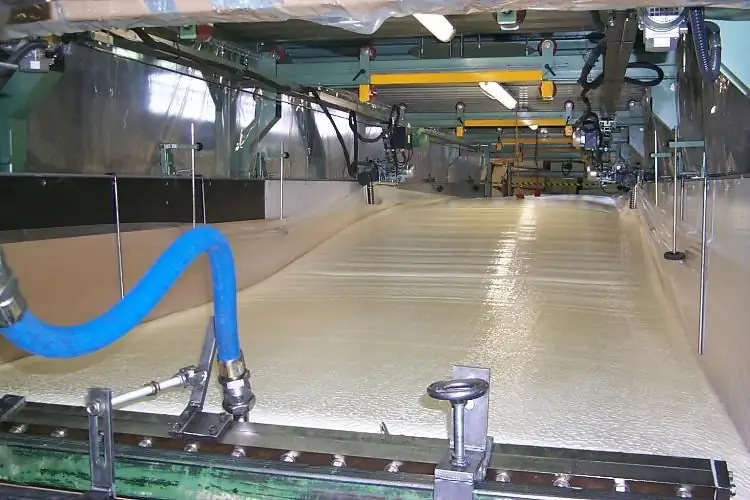
Mounting foam from the usual means of sealing window openings has long passed into the status of a full-fledged building material, which is widely used in a variety of types of work. The variety of applications of this product also determines the need for a differentiated approach to the technologies of its manufacture. However, the differences in foam production methods are more of a cosmetic nature, without affecting the basic technological processes