2025 Author: Howard Calhoun | [email protected]. Last modified: 2025-01-24 13:10
Due to its lightness, ductility and resistance to corrosion, aluminum has become an indispensable material in many industries. Aviation aluminum is a group of alloys characterized by increased strength with the inclusion of magnesium, silicon, copper and manganese. Additional strength is given to the alloy with the help of the so-called. "aging effect" - a special method of hardening under the influence of an aggressive atmospheric environment for a long time. The alloy was invented at the beginning of the 20th century, called duralumin, now also known as "avial".
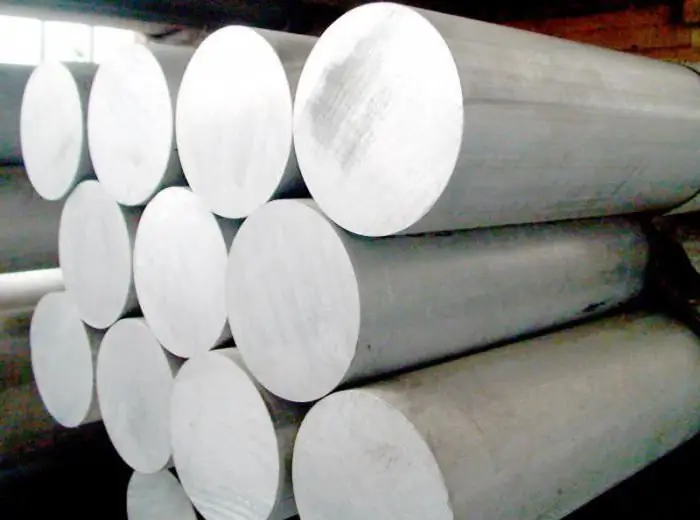
Definition. Historical excursion
The beginning of the history of aviation aluminum alloys is considered to be 1909. The German metallurgical engineer Alfred Wilm experimentally established that if an aluminum alloy with a slight addition of copper, manganese and magnesium after quenching at a temperature of 500 ° C and rapid cooling is maintained at a temperature of 20-25 degrees for 4-5 days, it gradually becomes harder and stronger without losing ductility. The procedure was called "aging" or "maturing". In the process of such hardening, copper atoms fillmany tiny zones at the grain boundaries. The diameter of the copper atom is smaller than that of aluminum, therefore, a compressive stress appears, as a result of which the strength of the material increases.
For the first time, the alloy was mastered at the German factories Dürener Metallwerken and received the trademark Dural, hence the name "duralumin". Subsequently, the American metallurgists R. Archer and V. Jafris improved the composition by changing the percentage, mainly of magnesium. The new alloy was named 2024, which is widely used in various modifications even now, and the entire family of alloys is called Avial. This alloy received the name "aviation aluminum" almost immediately after its discovery, since it completely replaced wood and metal in aircraft structures.
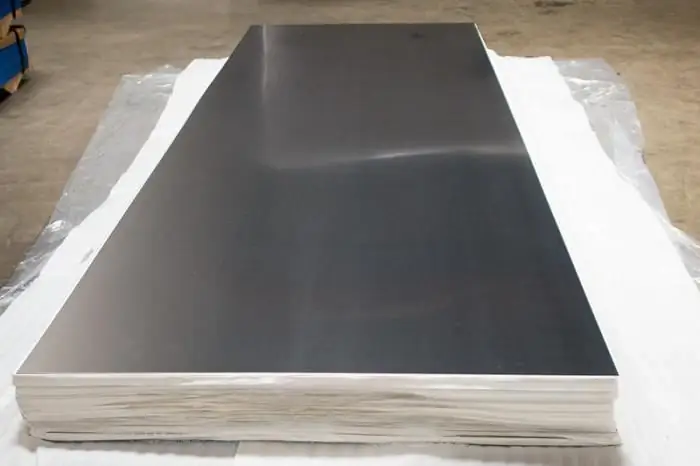
Main types and characteristics
There are three main groups:
- Aluminum-manganese (Al-Mn) and aluminum-magnesium (Al-Mg) families. The main characteristic is high corrosion resistance, barely inferior to pure aluminum. Such alloys lend themselves well to soldering and welding, but are poorly cut. Not hardened by heat treatment.
- Corrosion-resistant alloys of the aluminum-magnesium-silicon (Al-Mg-Si) system. They are hardened by heat treatment, namely, hardening at a temperature of 520 ° C, followed by rapid cooling with water and natural aging for about 10 days. A distinctive characteristic of this group of materials is their high corrosion resistance during operation under normal conditions and under stress.
- Structural aluminum-copper-magnesium alloys (Al-Cu-Mg). Their basis is aluminum alloyed with copper, manganese and magnesium. By changing the proportions of alloying elements, aircraft-grade aluminum is obtained, the characteristics of which may differ.
Materials of the last group have good mechanical properties, but are highly susceptible to corrosion than the first and second families of alloys. The degree of susceptibility to corrosion depends on the type of surface treatment, which still needs to be protected by paint or anodizing. Corrosion resistance is partially increased by the introduction of manganese into the composition of the alloy.
In addition to the three main types of alloys, there are also forging alloys, heat-resistant, high-strength structural and other alloys with the properties necessary for a particular application.
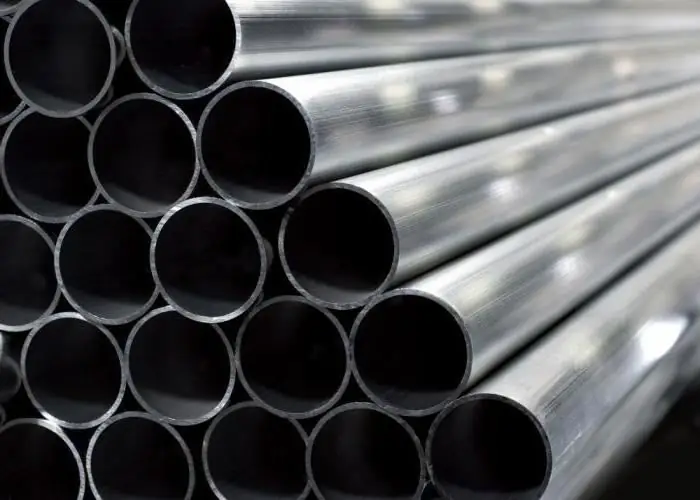
Marking of aviation alloys
In international standards, the first digit of the aviation aluminum marking indicates the main alloying elements of the alloy:
- 1000 - pure aluminium.
- 2000 - duralumins, alloys alloyed with copper. In a certain period - the most common aerospace alloy. Increasingly replaced by 7000 series alloys due to high susceptibility to stress corrosion cracking.
- 3000 - alloying element - manganese.
- 4000 - alloying element - silicon. Alloys are also known as silumins.
- 5000 - alloying element - magnesium.
- 6000 are the most ductile alloys. Alloying elements are magnesium and silicon. Can be heat-hardened to increase strength, but thisthe parameter is inferior to the 2000 and 7000 series.
- 7000 - thermally hardened alloys, the most durable aviation aluminum. The main alloying elements are zinc and magnesium.
The second digit of the marking is the serial number of the modification of the aluminum alloy after the original one - the number "0". The final two digits are the number of the alloy itself, information about its purity by impurities. If the alloy is experienced, a fifth “X” is added to the marking.
Today, the most common grades of aviation aluminum: 1100, 2014, 2017, 3003, 2024, 2219, 2025, 5052, 5056. Distinctive features of these alloys are: lightness, ductility, good strength, resistance to friction, corrosion and high loads. In the aircraft industry, the most widely used alloys are 6061 and 7075 aircraft aluminum.
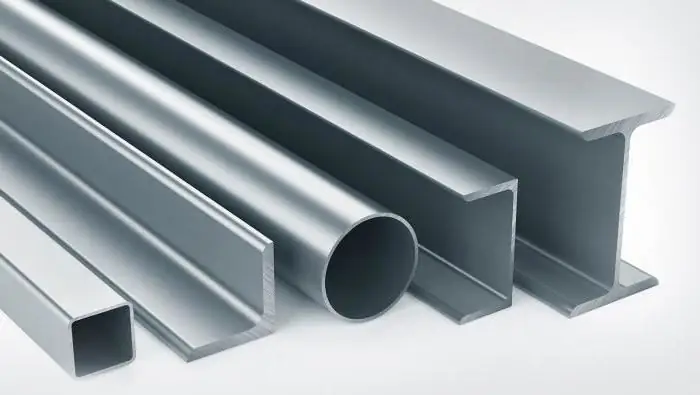
Composition
The main alloying elements of aviation aluminum are: copper, magnesium, silicon, manganese, zinc. The percentage of these elements by weight in the alloy is determined by such characteristics as strength, flexibility, resistance to mechanical stress, etc. The base of the alloy is aluminum, the main alloying elements are copper (2.2-5.2% by weight), magnesium (0. 2-2.7%) and manganese (0.2-1%).
A family of aviation alloys of aluminum with silicon (4-13% by weight) with a small content of other alloying elements - copper, manganese, magnesium, zinc, titanium, beryllium. Used to make complex parts, also known as silumin or cast aluminum alloy. aluminum-magnesium alloy family(1-13% mass) with other elements have high ductility and corrosion resistance.
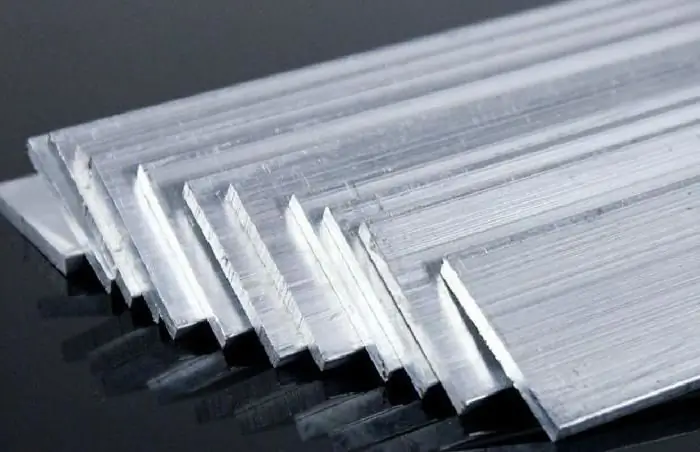
The role of copper in aircraft aluminum
The presence of copper in the composition of the aircraft alloy contributes to its hardening, but at the same time has a bad effect on its corrosion resistance. Dropping out at grain boundaries during the quenching process, copper makes the alloy susceptible to pitting, stress corrosion, and intergranular corrosion. Copper-rich areas are more galvanically cathodic than the surrounding aluminum matrix and therefore more vulnerable to galvanic corrosion. An increase in the copper content in the mass of the alloy up to 12% increases the strength properties due to dispersion strengthening during aging. With a copper content of more than 12%, the alloy becomes brittle.
Application areas
Aluminum alloys are the most sought after metal for sale. The light weight of aircraft-grade aluminum and its strength make this alloy a good choice for many industries from aircraft to household items (mobile phones, headphones, flashlights). Aluminum alloys are used in shipbuilding, automotive, construction, railway transport, and the nuclear industry.
Alloys with moderate copper content are widely demanded (2014, 2024 etc.). Profiles made of these alloys have high corrosion resistance, good machinability, and spot weldability. They are used to make critical structures for aircraft, heavy vehicles, military equipment.
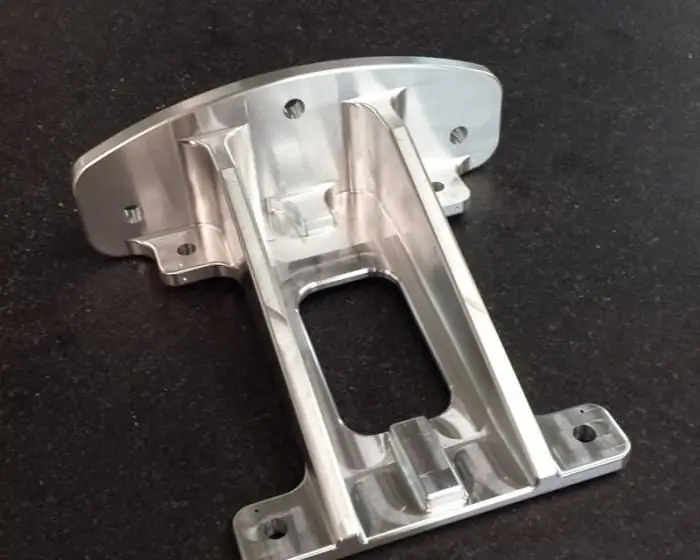
Aircraft-grade aluminum connection features
Welding of aviation alloys is carried out exclusively in a protective environment of inert gases. The preferred gases are: helium, argon or a mixture thereof. Helium has a higher thermal conductivity. This determines more favorable temperature indicators of the welding environment, which makes it possible to quite comfortably connect thick-walled structural elements. The use of a mixture of protective gases contributes to a more complete gas removal. In this case, the likelihood of pore formation in the weld is significantly reduced.
Aircraft applications
Aviation aluminum alloys were originally specially created for the construction of aviation equipment. Aircraft bodies, engine parts, chassis, fuel tanks, fasteners, etc. are made from them. Aviation aluminum parts are used in the interior of the cabin.
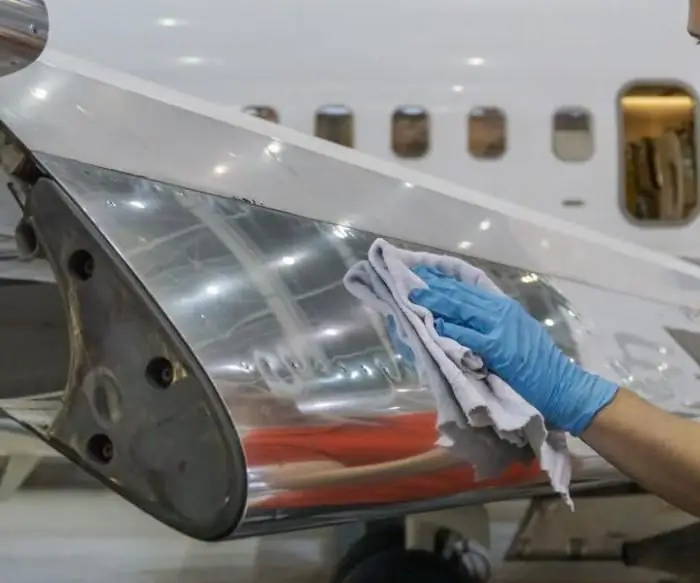
2xxx series aluminum alloys are used for the production of parts exposed to high temperatures. Parts of lightly loaded units, fuel, hydraulic and oil systems are made of 3xxx, 5xxx and 6xxx alloys. Alloy 7075 has received the widest application in the aircraft industry. Elements are made from it for operation under significant load, low temperatures with high resistance to corrosion. The basis of the alloy is aluminum, and the main alloying elements are magnesium, zinc and copper. Power profiles of aircraft structures, skin elements are made from it.
Recommended:
Aluminum self-adhesive tape: properties, types, characteristics
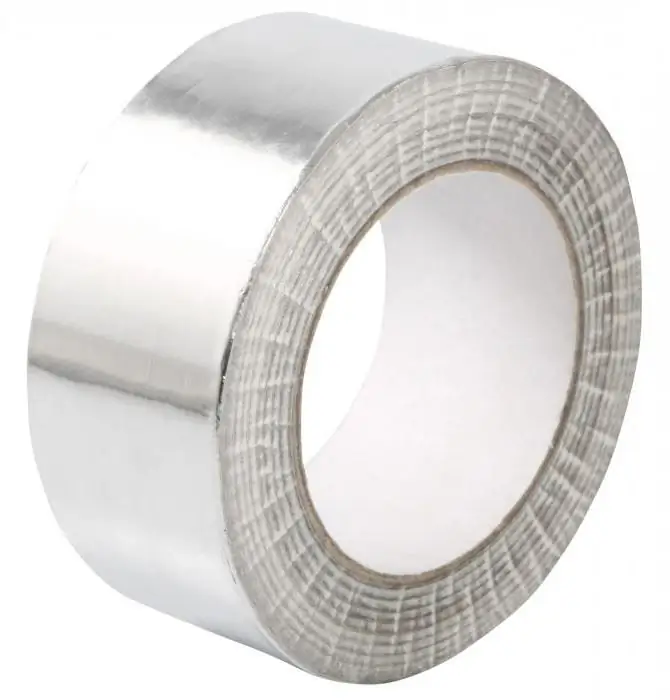
Aluminum self-adhesive tape is a universal material for technical purposes, which is used both in everyday life and in construction
Aluminum cable: description, types, characteristics
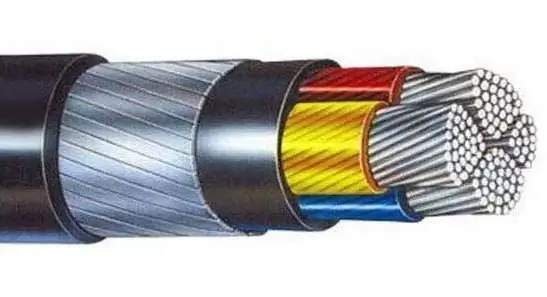
Currently, people are very actively using wires, cables, etc. The main purpose of these elements has become the transmission of electricity. In everyday life, aluminum cables are the most common type of steel
Corrosion of aluminum and its alloys. Methods for combating and protecting aluminum from corrosion
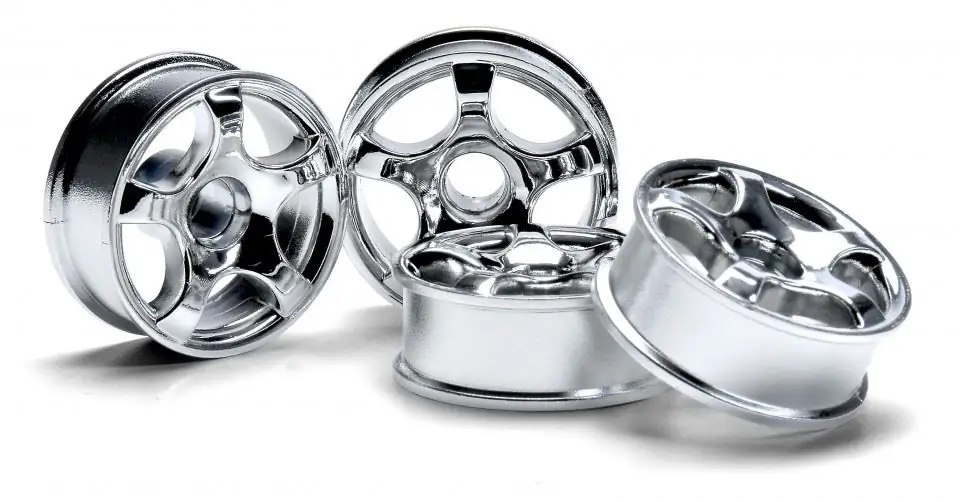
Aluminium, unlike iron and steel, is quite resistant to corrosion. This metal is protected from rust by a dense oxide film formed on its surface. However, in the case of destruction of the latter, the chemical activity of aluminum greatly increases
Characteristics of the Su-35. Su-35 aircraft: specifications, photo of the fighter. Comparative characteristics of the Su-35 and F-22
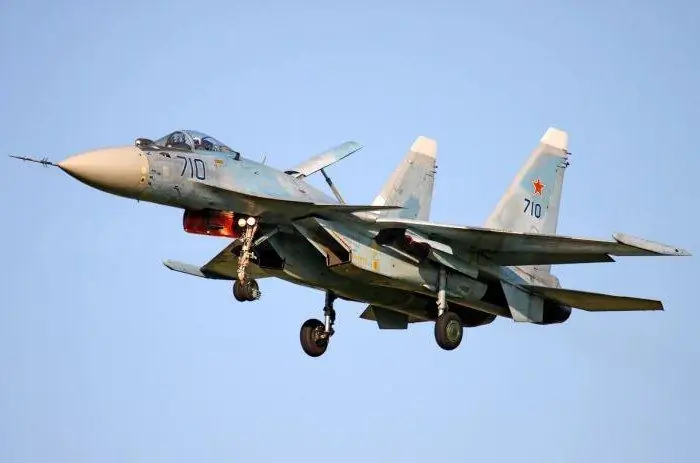
In 2003, the Sukhoi Design Bureau began the second in line modernization of the Su-27 fighter to create the Su-35 aircraft. The characteristics achieved in the process of modernization make it possible to call it a 4++ generation fighter, which means that its capabilities are as close as possible to the PAK FA fifth generation aircraft
Aviation gasoline: characteristics
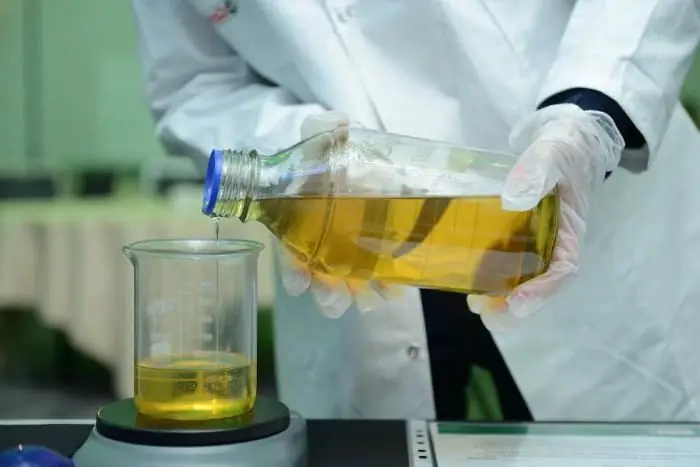
What is the difference between aviation gasoline and automobile? Brands of gasoline used in aviation. Specifications, production of fuel for aircraft