2025 Author: Howard Calhoun | [email protected]. Last modified: 2025-01-24 13:10
The Labor Code of the Russian Federation provides for various documents that regulate the labor relations between an employee and an employer. With official employment, a person signs a number of documents with the employer, in particular, an employment contract and internal regulations. In some cases, the employer obliges the employee to read a document such as a job description.
Why only some? Because this document is not mentioned in the Labor Code of the Russian Federation, which means it is not mandatory. Nevertheless, thanks to this document, in a number of cases it is possible to establish the right relationships in the team and outline the scope of responsibility.
Requirements for the design of work instructions
Job description - a document that defines the rights, duties and functions of an employee in a particular position.
The job description isthe subject of personnel documentation. To compile unified forms of documentation, GOST is used, in accordance with the Decree of the State Standard of the Russian Federation dated 03.03.2003 No. 65-st.
Also, when issuing instructions, you need to use the Unified Tariff and Qualification Directory (ETKS). It specifies the requirements for individual positions and the duties of employees.
Since, after signing, the job description becomes a local act of the organization, it must not only be drawn up in accordance with GOST, but also contain the data of this company - abbreviations, abbreviations, professional vocabulary, etc.
In addition to the requirements for the design of job descriptions (indentation, font, etc.), GOST provides for the following sections:
- general requirements, indicating qualifications, specific skills and knowledge for the position;
- functions, fundamental tasks assigned to the department and terms of reference for a specific position;
- rights and obligations denoting the limit of responsibility;
- information about the relationship with other departments or institutions in the process of performing assigned tasks;
- powers, this section is provided for deputy heads.
- responsibility of the parties, expressed both in general phrases of disciplinary punishment for certain offenses, and in specific ones.
In addition, together with the listed sections, the work instruction contains the details of the enterprise.
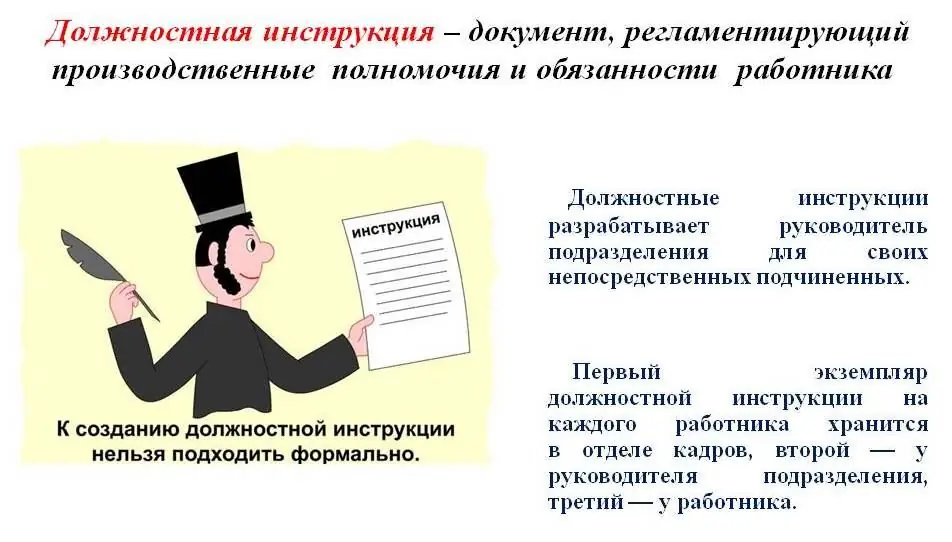
Consider today the requirements forof the job description of a toolmaker in production, we will denote the differences in work, knowledge and skills according to the qualification categories of the worker, according to ETKS.
The complexity, accuracy and quality of work determines the skill of the worker. That is, the more difficult the work, the higher his skill level. The degree of professionalism of employees is determined by the categories indicated in the ETCS.
Specifically for toolmakers, there are ranks from 2nd to
8th.
The tariff scale, which is interconnected with the categories of work, is involved in the calculation of the wages of the worker. The higher the skill level, the higher the hourly rate.
2 rank
The job description of a 2nd category toolmaker suggests that the employee must:
- process parts with a degree of accuracy of 12-14 qualifications;
- assemble and repair simple fixtures and tools;
- hardening simple tools;
- to produce and bring to the required parameters thermally untreated models for hardening in terms of accuracy - 12 qualifications;
- cut threads with taps and dies and check by gauge;
- make and carry out metalworking of tools and fixtures of medium complexity and put into practice special technological equipment and templates under the supervision of the work of a top-level toolmaker;
- know the principle of operation, technical characteristics and features of the use of lifting mechanisms;
Working to match the seconddischarge must:
- know the purpose and species diversity of locksmith and instrumentation tools and fixtures and operating rules;
- have knowledge of a unified system of tolerances and landings;
- have knowledge of the degree of accuracy and roughness parameters, as well as their designation on the drawings;
- clearly describe how drilling and lapping machines work;
- know how to set allowances for subsequent finishing, provided that the metal is deformed during heat treatment.
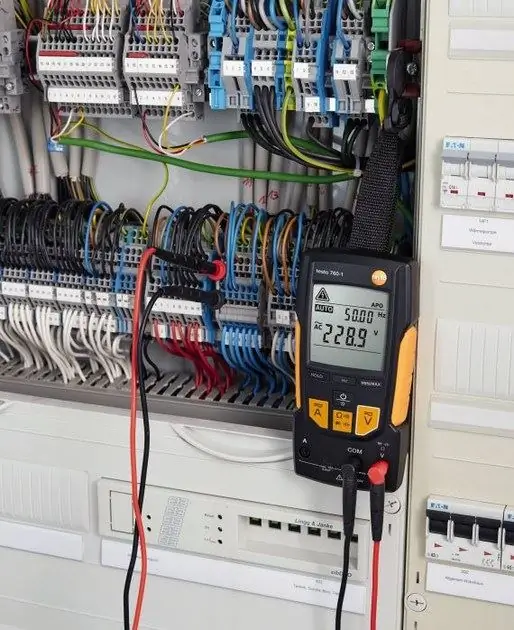
Requirements for 3rd category
The job description of a 3rd grade toolmaker describes the following work that an employee must be able to perform:
- make and restore tools and fixtures of medium complexity;
- produce tools of increased complexity and precision using special technical equipment and templates;
- carry out metalwork finishing of parts according to 8-11 qualifications using universal equipment;
- mark and draw curly details;
- to finish the tool and straighten the manufactured products;
- under the supervision of a toolmaker of a higher level, to make tools and fixtures of increased complexity.
To successfully achieve the tasks set, a toolmaker must have knowledge:
- about basic geometric and trigonometric dependencies and fundamentalstechnical drawing;
- about the design of used machine tools for metalworking, finishing and lapping type;
- how and under what conditions to use finishing materials;
- about the properties of steel of various grades;
- KIP, their device and operation;
- about the dependence of measurement accuracy on the temperature of the part;
- about methods of heat treatment of steel, taking into account its brand;
- about allowances for finishing, taking into account changes in the metal during heat treatment.
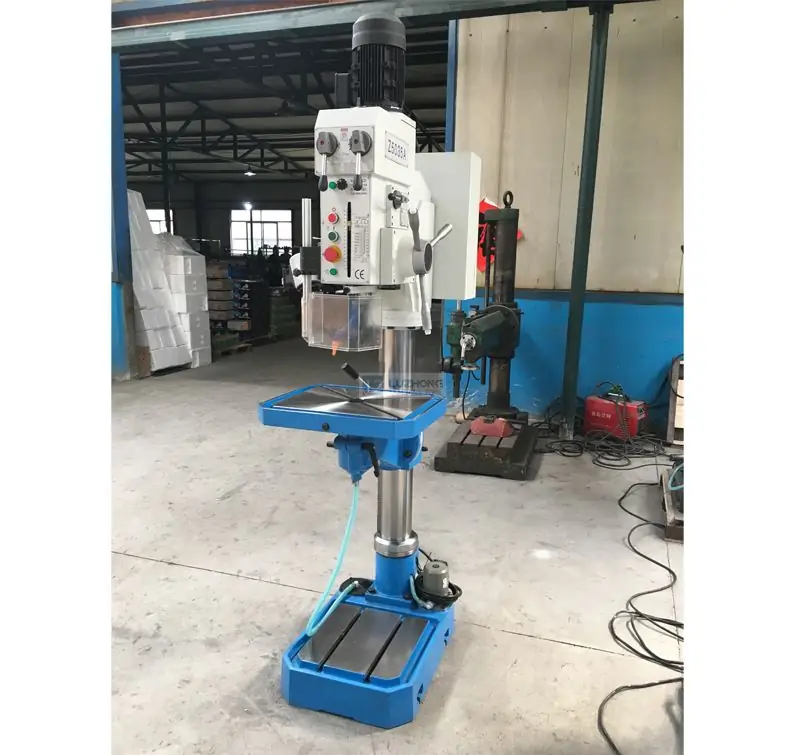
Getting 4 ranks
The job description of a 4-grade toolmaker predetermines the following types of work:
- the ability to make and repair tools and fixtures of increased complexity using modern special technological equipment;
- finish, lap and produce figured parts according to 7-10 grades with minimal surface roughness.
In addition to the listed mandatory knowledge at grade 3, at grade 4, the employee must know:
- how to determine the quality of hardening and straightening of parts in processing;
- how to mark and draw a complex figure;
- how to prevent changes in the internal stress and structure of the metal during heat treatment.
Features of qualification of the 5th category
When signing the job description of a 5th grade toolmaker, an employee must be able to:
- - make, adjust,repair large complex and precise tools and fixtures, models with a large number of interconnected sizes, with an accuracy degree of 6-7 qualifications;
- finish, grind and produce parts with a high degree of accuracy (5 qualifications) and roughness Ra 0, 16-0, 02;
- test fixtures and dies when using. When receiving an impression, the accuracy of the shape and the relative position of the surfaces of the part is evaluated.
Additionally should know:
- structural features of complex tools and fixtures;
- types of calculations and geometric constructions.
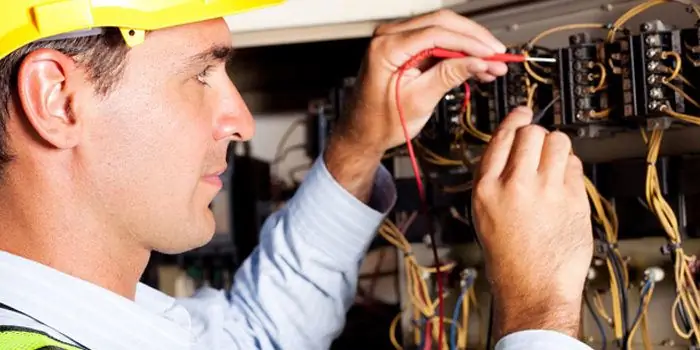
6 rank and conditions for its assignment
The job description of a 6th grade toolmaker authorizes him to:
- assembly, fine-tuning, finishing of precise and complex unique molds and experimental numbering machines;
- production of complex patterns, when the planes are located in different projections, according to 1-5 qualifications and roughness Ra 0, 04-0, 01;
- adjustment of optical instruments.
Getting rank 6, the worker must be competent in:
- designs, purposes and rules for the use of instrumentation;
- rational ways of using and repairing instrumentation with an accuracy of 1-5 qualifications;
- ways to increase the degree of roughness.
7 rank qualification
A 7th grade toolmaker must be able to independently process parts and products on universal machinesmetal-cutting type, and also have the skill of driving electric cars.
The job description of a 7th grade toolmaker additionally assumes knowledge of how to set up and check for accuracy of a complex machine.
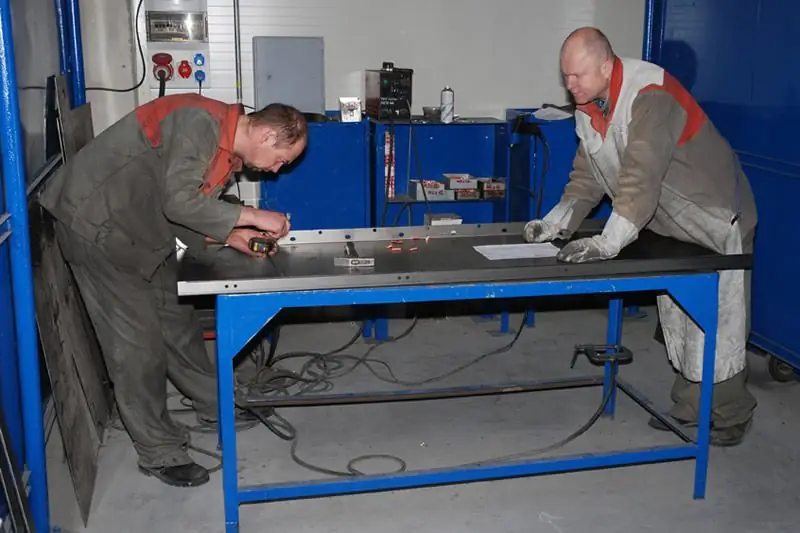
8 digit
To get the 8th category, a toolmaker needs to know how to adjust the working bodies of measuring instruments and auxiliary devices on a unique and experimental metal-cutting machine, machine, unit.
The job description of a 8th grade toolmaker obliges him to know all the above theoretical and practical aspects of activity, to actively use them at work.
It should be noted that in order to receive 7th and 8th grade, you must have an education in the profession of a technician. These ranks are assigned during work in the experimental, preparatory and experimental workshops.
Based on the above characteristics of the work, the required knowledge and skills, job responsibilities are drawn up. When reading the instructions, you need to refer to the ETKS, namely, to the recommendations for this type of profession.
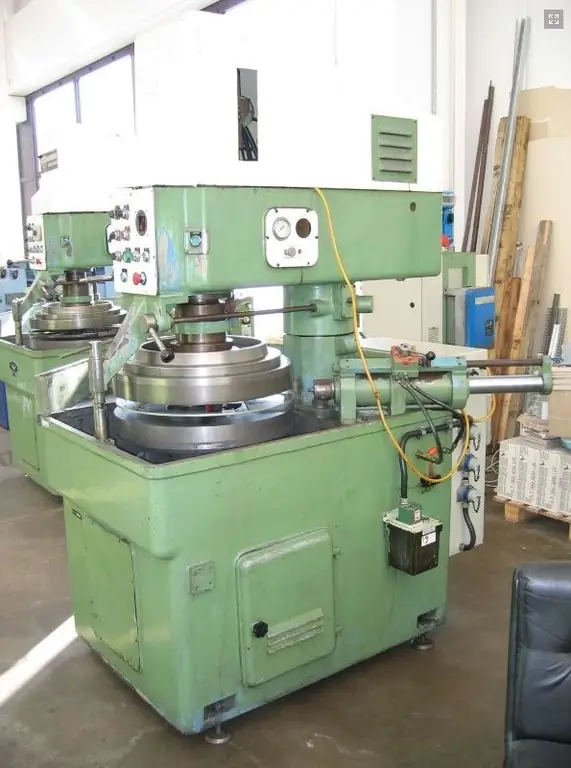
Mold Toolmaker
Press molds are used to create products of various sizes and shapes from metal, plastic and other materials. The job description of a toolmaker for repairing molds indicates the necessary knowledge of the device,the design and features of molds, the ability to disassemble molds, repair them, and also put into practice knowledge about their rational operation.
Sources for developing job descriptions:
- information about the organizational structure and management structure of the enterprise;
- statutory documents of the firm;
- ETKS;
- Regulations on the structural unit;
- classification directory of positions.

Making changes to CI
Sometimes the responsibilities for any position are narrowed or expanded. In this case, a change order is issued. You can also issue an additional agreement to a specific job description.
Moreover, if the content of the instruction is planned to be radically changed, a new instruction is created in the new edition.
Recommended:
Job description of the sales floor controller: duties, job description and requirements
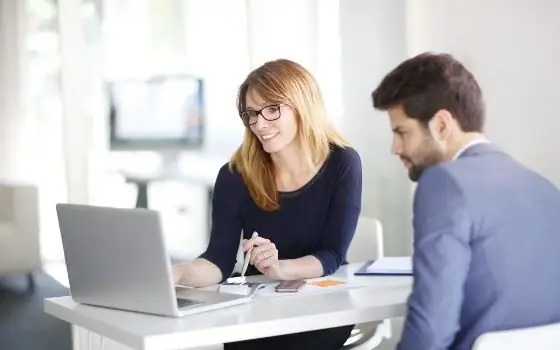
There are hundreds of different professions, and the sales floor controller is one of them. This profession can hardly be called prestigious. They don’t dream about it, starting from the school bench. But it is one of the basic ones. The work of its representatives is not so noticeable and obvious, but it is beneficial for society. Let's learn more about the job responsibilities of a sales floor controller and other features of this profession
Job description of a psychologist - duties, job description and requirements
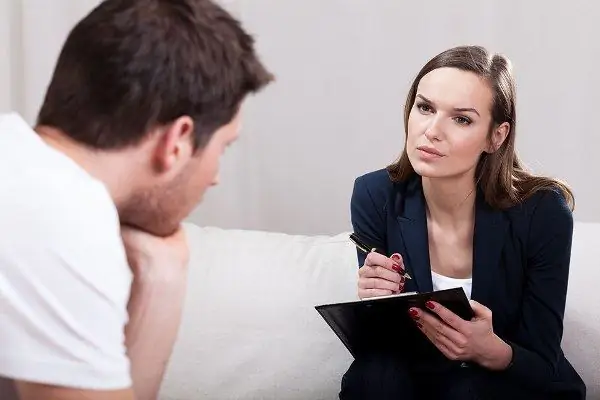
Not every person knows the duties of a psychologist. Many have a hard time imagining what this specialist does. What are the requirements for it in various organizations. What rights does a psychologist have? Who is suitable for this profession
Operational and maintenance personnel: duties and job description
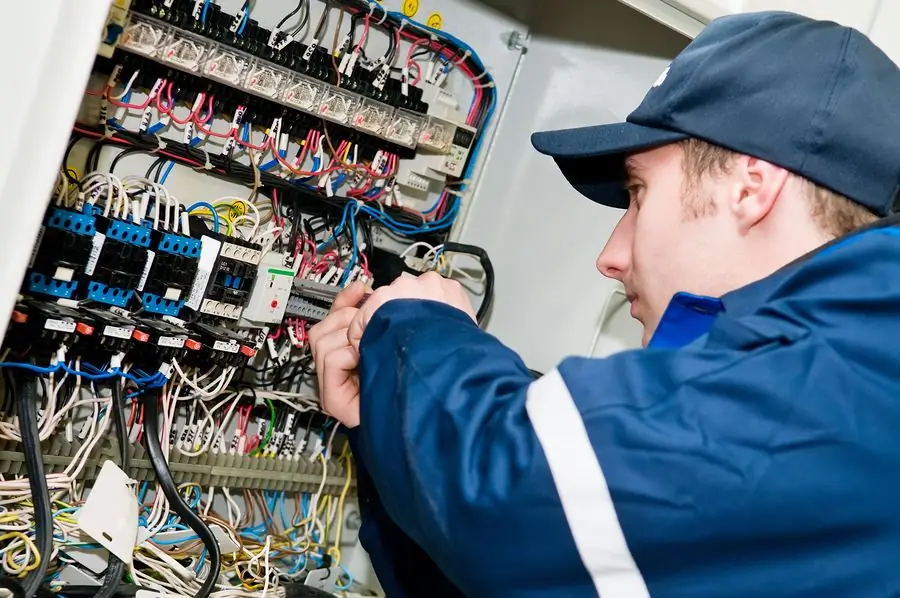
Who is the operational and maintenance personnel? Who belongs to this category and what are the responsibilities of the staff? What is duplication of operational and maintenance personnel, the essence and timing of the passage
What are the duties of a security guard? Job duties and responsibilities of a security guard
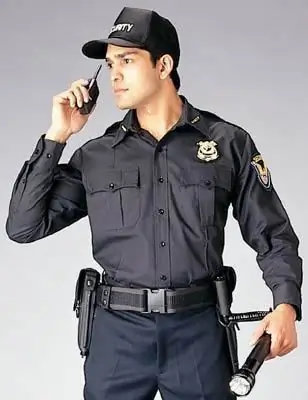
The profession of a security guard is quite popular today. And all because more and more stores and shopping centers are opening these days, in which it is necessary to ensure the safety of both employees and customers, as well as goods and money, at the proper level. In addition, factories, various municipal institutions and a host of other facilities are constantly in need of security guards. We offer today to find out in detail what is included in the duties of a security guard
Job description plumber 4, 5 or 6 category. What are the job responsibilities of a plumber?
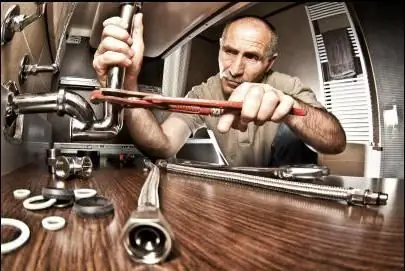
Plumber is a very common profession today. All the features of this work will be discussed in this article