2025 Author: Howard Calhoun | [email protected]. Last modified: 2025-01-24 13:10
Inventory management is an important part of the company's current asset management policy. The main goal is to ensure the continuity of production processes and sales of products and at the same time minimize the total costs that go to servicing stocks. And this is where automation comes into play. The inventory management system at the enterprise helps us.
General information
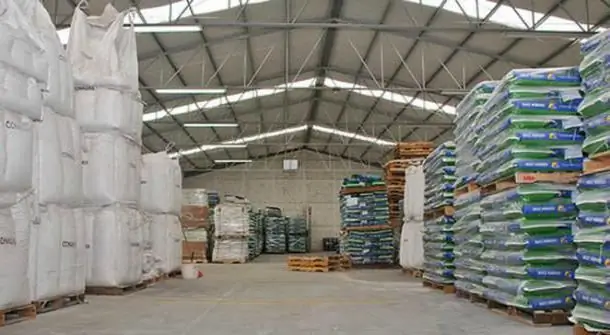
Inventories include not only materials and raw materials that are necessary for the production process, but also unfinished products and goods that can be sold. It is important to control their volume. Safety stocks should always be, because no one has yet canceled seasonal surges in consumer demand and interruptions in supply. And all this can negatively affect the financial result of the activity. Of course, it should be noted that this can also be attributed to reserves, but on the other hand, they ensure the stability and liquidity of the enterprise. If there is a shortage, then production will stop, sales volumes will fall, and such a situation may arise that you will have to buy a batch of raw materials or materials at an inflated price. As a result, the enterprisemiss out on potential profits. Also, due to the fact that inventories are liquid assets, their reduction will lead to a deterioration in the current regulatory state of the enterprise. But here it is necessary to adhere to the golden mean. So, an excess of stocks can lead to the fact that the cost of their storage will increase, you will have to overpay property tax. It is also possible to lose potential income due to the fact that financial resources will be frozen in raw materials. In addition, one should not lose sight of the fact that they are subject to moral aging and physical damage.
Approaches
Speaking about inventory management, it should be noted that the manager has a choice of three action plans regarding the formation of reserves. They differ in different levels of profitability and risks:
- Conservative approach. It focuses not only on meeting the entire existing need for raw materials, materials and semi-finished products. It also provides for the creation of large reserves in case of interruptions in the supply, deterioration in the conditions in which products are manufactured, there are delays associated with the collection of receivables, and the demand of buyers is activated. Using this approach negatively affects the level of profitability and positively affects the possible risk.
- Moderate approach. Provides for the creation of reserves for the most typical failures that may occur during the operation of the enterprise. The calculations in this case are based on data from previous years. In this case, the average level of profitability andrisks.
- Aggressive approach. In this case, a minimum level of stocks is provided (although they may be completely absent). If no failure occurs during the implementation of the operational process, then the enterprise will receive the best result of efficiency. But when problems arise, the company incurs significant financial losses. In this way, you can get the most profit, but there is also a significant risk of loss.
Governance model: factors
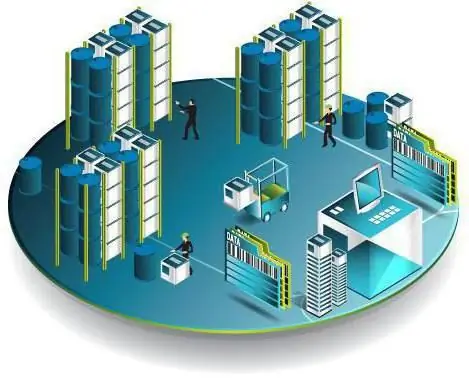
Everything that happened before was theoretical training. Now we will consider the development of an inventory management system for an enterprise. To do this, we need to take into account a number of factors:
- Conditions under which stocks are purchased (supply volumes, order frequency, incentives and discounts).
- Features of the sale of finished products (state of demand, reliability and development of the dealer network, changes in the level of sales).
- Characteristic nuances of the production process (features of the technology of creation, duration of preparation and direct provision of products).
- Costs incurred while holding inventory (freezing funds, possible spoilage, storage costs).
The inventory management system in an enterprise can be built on several specific methods. Each of them has its own specific features.
Wilson Model
Used to ensure that inventory management in the logistics system is optimized to the maximum. She may beused to answer questions such as: what stocks should be; what volume of materials and raw materials is needed per unit of time; optimal supply. In addition to them, there are other provisions that need to be addressed. According to the Wilson model, it is possible to make sure by mathematical means that the enterprise is interested in ordering raw materials, materials and goods in as large lots as possible. In this case, the cost of transport costs, registration and the like will be minimized. And this will directly affect the profitability of the enterprise. It also allows you to select the minimum allowable standard level of stocks, which will avoid high operating costs that go to the storage of raw materials, materials and semi-finished products. What are the parameters of the inventory management system in this case? To fully use the model, you need to know:
- That it can only be applied to one kind of goods. At the same time, its quantity must be continuously measured.
- The level of demand for a particular good that is constant over time.
- Products are produced in batches.
- Orders come in a separate delivery, which entails additional costs.
- Inventory runs out continuously.
- Shipping and order costs are constants (or you need to average). Moreover, in this case, transport, operating and other expenses are implied.
- Does not cover cases with additional deliveries of goods and discounts for large volume orders.
What is used in practice?
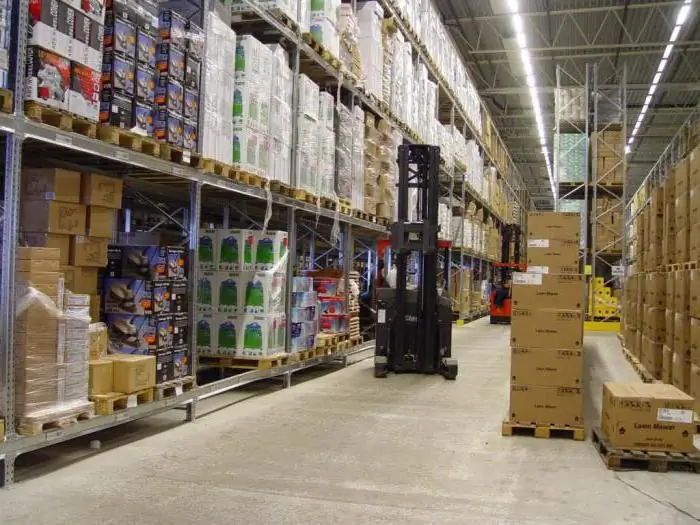
What are the main inventory management systems? What are their features? Let's look at this with an example. And the ABC inventory control system will act as the object under study. It is based on a volume-cost analysis, which divides all types of stocks into certain groups, depending on the amount of sales and the profit received. In many cases, it may turn out that 70-80% of all sales fall on 10-20% of products. This is the Pareto principle in action. In such cases, the inventory management system suggests focusing on the most important products and goods, as well as managing them effectively so as not to spend extra money on less important areas. Within the framework of the system, the cost, volume and frequency of spending, the consequences of a shortage of certain raw materials, and the like are of great importance. The division is carried out into different categories. Let's take a look at them.
Classification of categories of the ABC system
There are three of them:
- Category A. This includes the most expensive types of stocks that have a long cycle of use. They require constant monitoring, as there will be serious financial consequences if they are not available. The Wilson model described above is used to determine the optimal time to import them. Specific inventory items are generally very limited and require weekly inspections.
- CategoryB. This includes inventory items in the matter of ensuring the continuity of the operational process and the formation of the final financial result. As a rule, stocks from this group are controlled only once a month.
- Category C. The ABC Inventory Management System includes here all inventories that have a low cost and that do not play a significant role in shaping the final financial result. The volume of purchases in this case will be quite large. Inventory control is carried out, as a rule, no more than once a quarter.
Inventory valuation
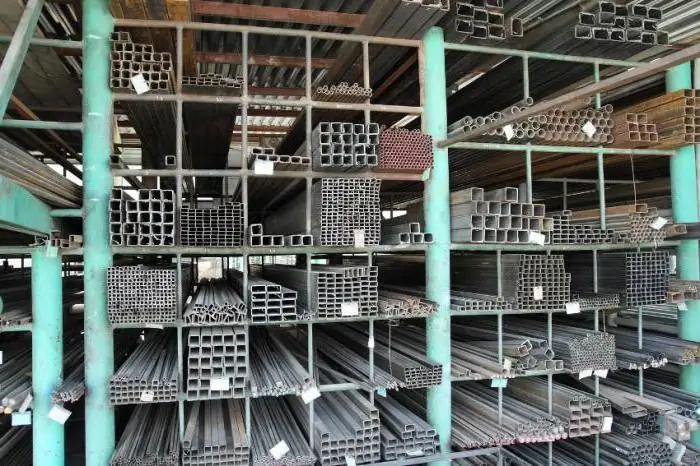
In practice, the following methods can be used for this purpose:
- LIFO. In this case, the effect of inflation is smoothed out when profit is formed. This method is suitable if it is necessary to have an objective assessment of the result. The positive side is that it allows you to reduce the amount of property tax.
- FIFO. Positively affects liquidity, reduces costs and increases profits.
Summarize
What is the inventory management system? This is a full-fledged set of measures that are aimed at creating and replenishing stocks, as well as organizing continuous monitoring and operational planning of supplies. Feedback plays a big role here, or rather, how it is implemented. The best result is when management representatives can quickly receiveall the necessary data, make decisions and implement them. For this, automation tools are widely used. To explain the device, you can work with a three-level model.
Implementation
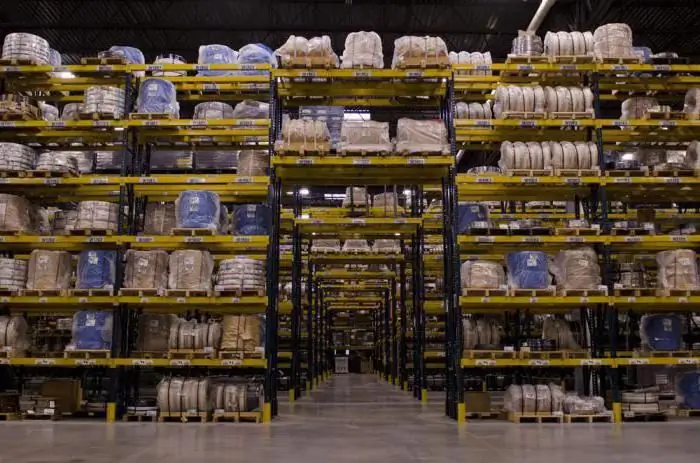
At the first level, information about the material stock of the inventory management system is formed thanks to warehouse programs and databases. Thanks to them, you can get all the information about the movement of raw materials, materials and semi-finished products, as well as information about loading or shipping something. The second level of the system is formed from different inventory management models. They use all the necessary mathematical apparatus, which allows them to assess the current state of stocks and develop recommendations for effective management. At the third level, a financial management model is used, as well as software-implemented restrictions, which allow you to control the financial condition of stocks. In this case, the economic efficiency of the decisions being made is evaluated, sources for the purchase of raw materials and materials are determined. In addition, this model deals with the overall financial strategy of inventory management. The availability of software implementation and automation tools can significantly increase the level of efficiency and ultimately save on the staff of economic workers.
Improvements
The question is actively raised: how can the inventory management system be improved? First you need to make sure that the necessary information is available at any time.time. This is where cloud computing can help. They will allow you to receive data from an arbitrary point on the globe - if only there was an Internet. In addition, the most advanced inventory management systems have algorithms for calculating the consumption of raw materials and materials. Therefore, they can provide high-quality forecasts and recommendations when stocks need to be replenished. In this case, the individual's role is limited to placing orders and keeping the system running smoothly.
Create ACS
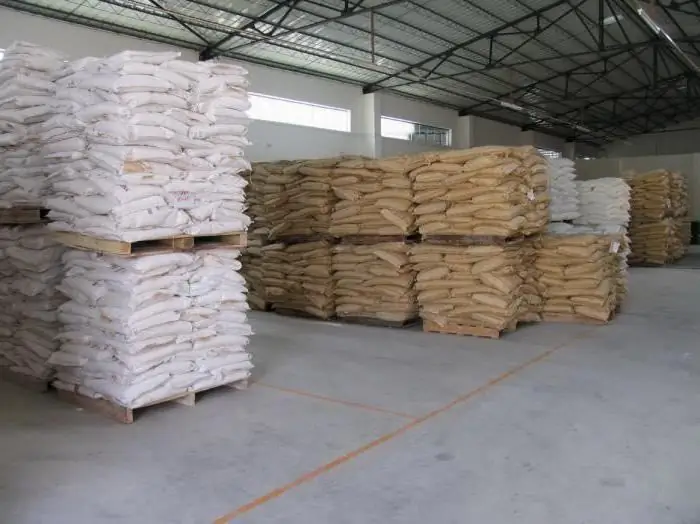
Let's say an automated control system is being created. In this case, the following factors will be of significant importance for the algorithm:
- Production capacity.
- The required amount of stocks for the normal functioning of the enterprise.
- The volume of production that is produced for certain periods of time (those are a day, a week, a month). In some cases, the year may even be taken as the basis.
- Inventory level at the time the system went online.
- Frequency of deliveries.
MRP
This is also a stock management system. We will consider it as an alternative to the previously mentioned ABC. There are two configurations: MRP-1 and MRP-2. In the first, information about the arrival, movement and consumption of stocks is processed and corrected. Replenishment and control strategies for each position are also provided. To solve management problems, there is a special order file that contains all the information. MRP-2 compares favorably with a wider range of functions. It includes production and financial planning, as well as logistics operations. Analysis of the inventory management system allows you to know where, what and how much.
Conclusion
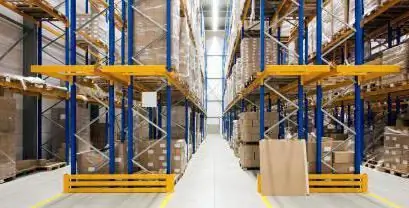
Inventory management system is necessary for every enterprise that plans to operate successfully for a long time. After all, it allows you to carry out the function of control and replenishment of reserves. A significant role as a structural element is played by automation tools. We can safely say that they will be gradually improved, and in the future we will be able to see this structural part of the enterprise as an autonomous system that only needs to be configured. She will be able to carry out activities on her own.
Recommended:
Inventory is Inventory accounting. Enterprise stocks
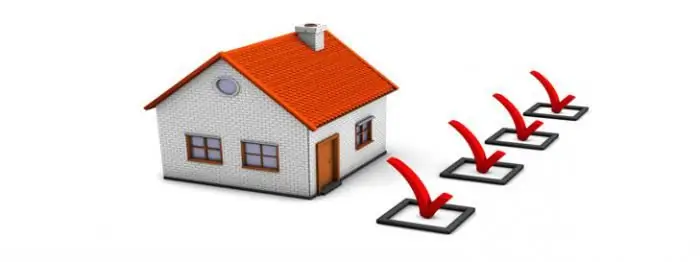
Stock is a form of material flow existence. On the way from the source of occurrence to the final consumer, it can accumulate in any area. That is why it is customary to distinguish between stocks of materials, raw materials, finished products and other things. It turns out that inventories are materials, raw materials, components, finished products, as well as other valuables that await personal or industrial consumption
Act of inventory of emission sources. Order on the inventory and the composition of the inventory commission
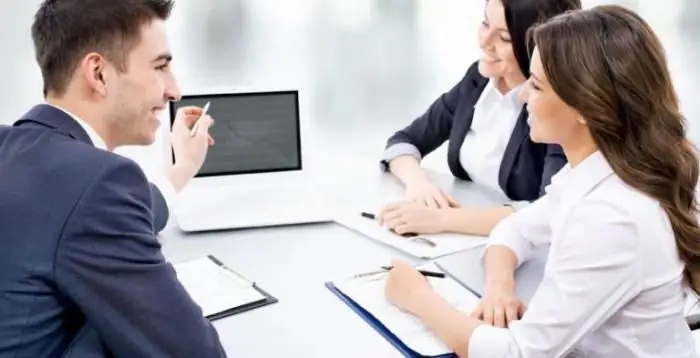
Inventory of waste emissions into the atmosphere is a set of activities that are carried out by nature users, including systematization of data on pollutant emissions, identification of their location, determination of emission indicators. Read more about how this process goes and how the act of inventory of emission sources is filled out, read on
Inventory in a pharmacy: procedure, documents, composition of the inventory commission
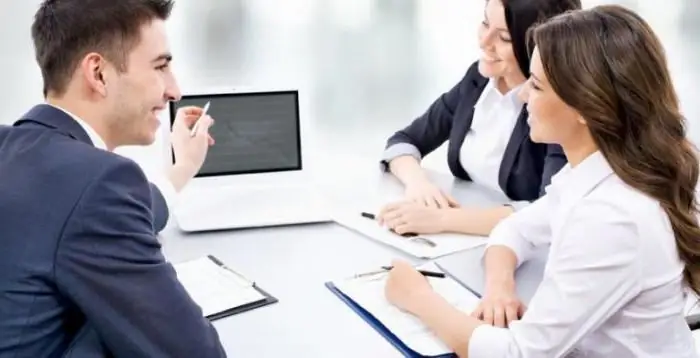
Inventory is the verification of a firm's inventory on a given date by comparing actual data with balance sheet information. This is the main way to control property values. Read more about how inventory is carried out and processed in a pharmacy, read on
Inventory - what is it? Goals, methods and types of inventory

Inventory is an inventory of property designed to identify discrepancies between the actual number of valuables and the information contained in the company's internal documentation. The article lists the main varieties of such a check. The procedure for conducting an inventory is given
Organization management is an enterprise management system
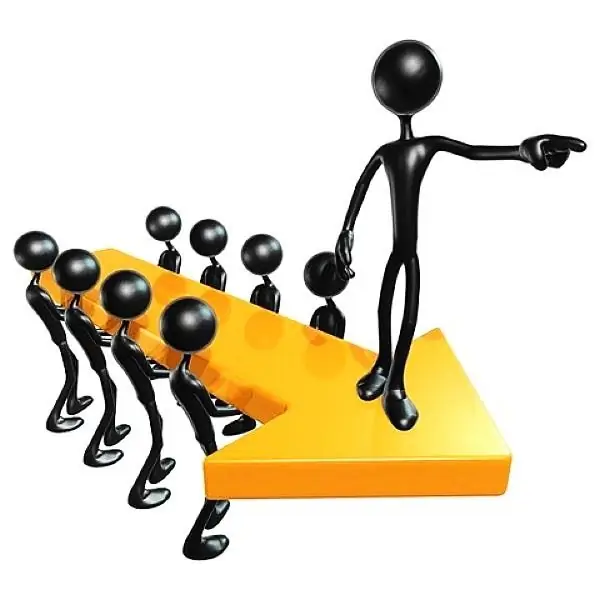
Management of an organization is the creation of a business model of an enterprise and the most effective management of it