2025 Author: Howard Calhoun | [email protected]. Last modified: 2025-01-24 13:10
Humanity seeks to switch to alternative sources of electrical supply that will help keep the environment clean and reduce the cost of energy generation. Solar battery production is a modern industrial method. The power supply system includes solar receivers, batteries, controllers, inverters and other devices designed for specific functions.
The solar battery is the main element from which the accumulation and conversion of ray energy begins. In the modern world, there are many pitfalls for the consumer when choosing a panel, as the industry offers a large number of products combined under one name.
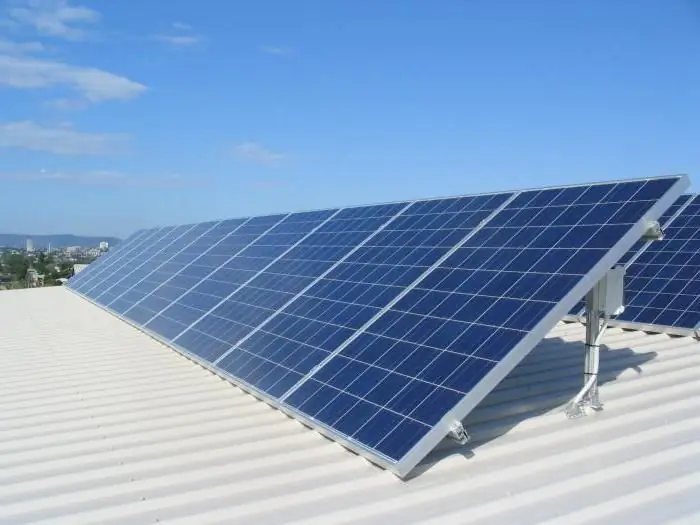
Silicon Solar Cells
These products are popular with today's consumers. Silicon is the basis for their manufacture. Its reserves in the depths are widespread, and production is relatively inexpensive. Silicon cells compare favorably in performance levels with other solar cells.
Types of elements
Silicon solar cells are manufactured in the following types:
- monocrystalline;
- polycrystalline;
- amorphous.
The above forms of devices differ in how the silicon atoms are arranged in the crystal. The main difference between the elements is the different indicator of the efficiency of the conversion of light energy, which for the first two types is approximately at the same level and exceeds the values for devices made of amorphous silicon.
Today's industry offers several models of solar light catchers. Their difference lies in the equipment used for the production of solar panels. The manufacturing technology and the type of starting material play a role.
Single crystal type
These elements consist of silicone cells fastened together. According to the method of the scientist Czochralski, absolutely pure silicon is produced, from which single crystals are made. The next process is cutting the frozen and hardened semi-finished product into plates with a thickness of 250 to 300 microns. Thin layers are saturated with a metal grid of electrodes. Despite the high cost of production, such elements are used quite widely due to the high conversion rate (17-22%).
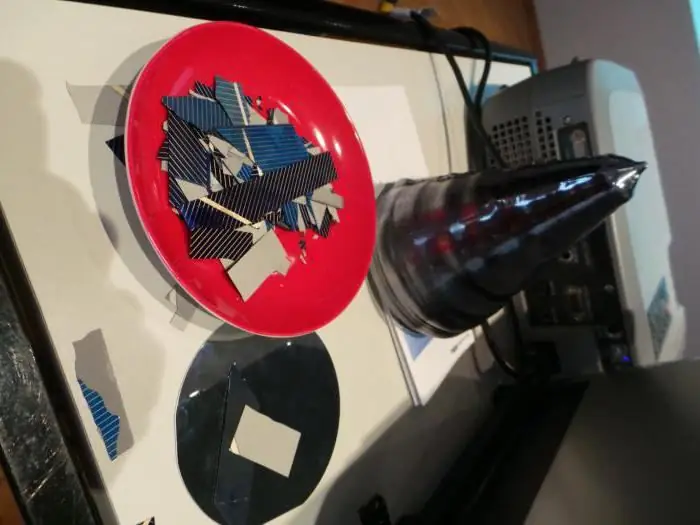
Production of polycrystalline elements
The technology for the production of solar cells from polycrystals is that the molten silicon mass is gradually cooled. The production does not require expensive equipment, therefore, the cost of obtaining silicon is reduced. Polycrystalline solar storages have a lower efficiency factor (11-18%), unlike monocrystalline ones. This is explained by the fact that during the cooling process, the mass of silicon is saturated with tiny granular bubbles, which leads to additional refraction of rays.
Amorphous silicon elements
Products are classified as a special type, since their belonging to the silicon type comes from the name of the material used, and the production of solar cells is carried out using film device technology. The crystal in the manufacturing process gives way to silicon hydrogen or silon, a thin layer of which covers the substrate. Batteries have the lowest efficiency value, only up to 6%. Elements, despite a significant drawback, have a number of undeniable advantages that give them the right to stand in line with the above types:
- optics absorption value is two dozen times higher than that of monocrystalline and polycrystalline drives;
- has a minimum layer thickness of only 1 micron;
- cloudy weather does not affect light conversion work, unlike other species;
- due to its high bending strength, it can be used without problems in difficult places.
The three types of solar converters described above are complemented by hybrid products made from materials with dual properties. Such characteristics are achieved if microelements or nanoparticles are included in amorphous silicon. The resulting material is similar to polycrystalline silicon, but compares favorably with it by new technical features.indicators.
Raw material for the production of CdTe film-type solar cells
The choice of material is dictated by the need to reduce the cost of production and improve performance in work. The most commonly used light-absorbing cadmium telluride. In the 70s of the last century, CdTe was considered the main contender for space use, in modern industry it has found wide application in solar energy.
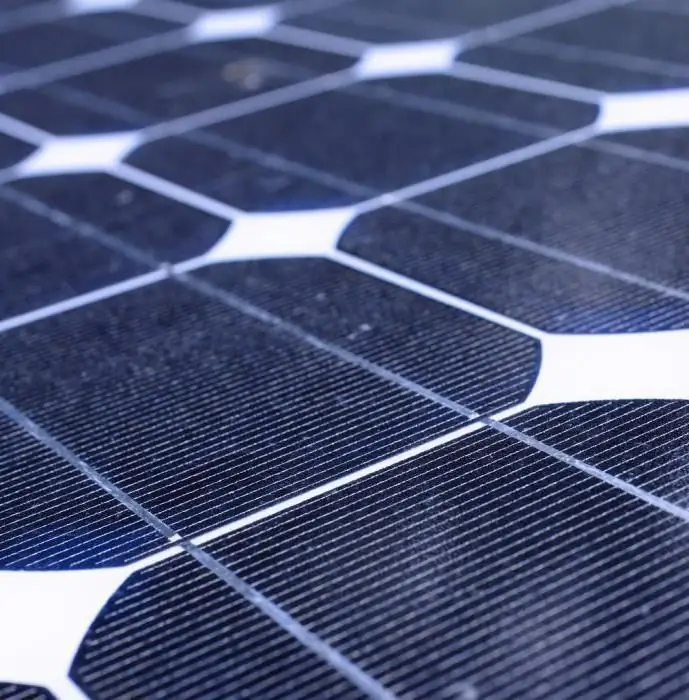
This material is classified as a cumulative poison, so the debate on its harmfulness does not subside. Research by scientists has established the fact that the level of harmful substances entering the atmosphere is acceptable and does not harm the environment. The efficiency level is only 11%, but the cost of converted electricity from such cells is 20-30% lower than from silicon-type devices.
Ray accumulators made of selenium, copper and indium
Semiconductors in the device are copper, selenium and indium, sometimes it is allowed to replace the latter with gallium. This is due to the high demand for indium for the production of flat-type monitors. Therefore, this substitution option was chosen, since the materials have similar properties. But for the efficiency indicator, replacement plays a significant role, the production of a solar battery without gallium increases the efficiency of the device by 14%.
Polymer-based solar collectors
These elements are classified as young technologies, as they have recently appeared on the market. Organic semiconductors absorb lightto convert it into electrical energy. For production, fullerenes of the carbon group, polyphenylene, copper phthalocyanine, etc. are used. As a result, thin (100 nm) and flexible films are obtained, which in work give an efficiency coefficient of 5-7%. The value is small, but the production of flexible solar cells has several positive points:
- It doesn't cost much to make;
- the ability to install flexible batteries in bends where elasticity is of paramount importance;
- relative ease and affordability of installation;
- flexible batteries are environmentally friendly.
Chemical pickling during production
The most expensive solar battery is a multicrystalline or monocrystalline silicon wafer. For the most rational use of silicon, pseudo-square figures are cut, the same shape allows you to tightly lay the plates in the future module. After the cutting process, microscopic layers of damaged surface remain on the surface, which are removed by etching and texturing to improve the reception of incident rays.
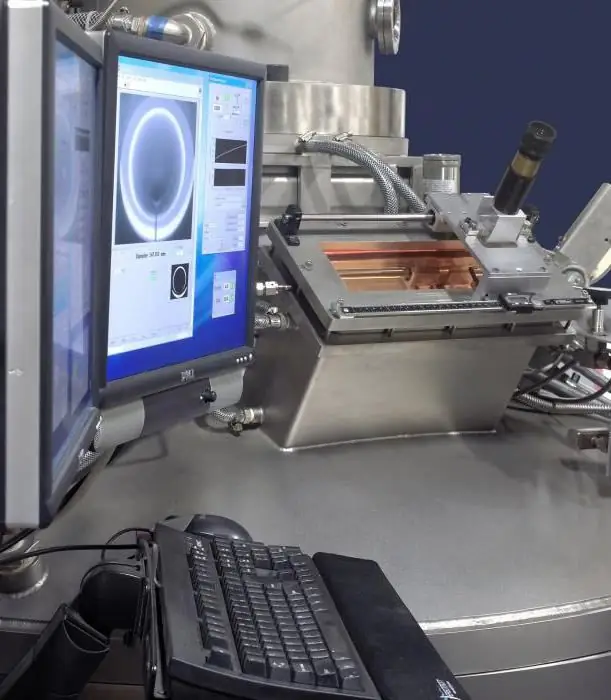
The surface treated in this way is a randomly located micropyramids, reflected from the edge of which, the light falls on the side surfaces of other protrusions. The loosening procedure reduces the reflectivity of the material by approximately 25%. The pickling process adopts a series of acidic and alkalineprocessing, but it is unacceptable to greatly reduce the layer thickness, since the plate does not withstand the following processing.
Semiconductors in solar cells
Solar cell production technology assumes that the main concept of solid electronics is p-n-junction. If the electronic conductivity of the n-type and the hole conductivity of the p-type are combined in one plate, then a p-n junction occurs at the point of contact between them. The main physical property of this definition is the ability to serve as a barrier and pass electricity in one direction. It is this effect that allows you to establish the full operation of solar cells.
As a result of phosphorus diffusion, an n-type layer is formed at the ends of the plate, which is based at the surface of the element at a depth of only 0.5 microns. The production of a solar battery provides for a shallow penetration of carriers of opposite signs, which arise under the action of light. Their path to the zone of influence of the p-n-junction must be short, otherwise they can extinguish each other when they meet, without generating any amount of electricity.
Use of plasma-chemical etching
The design of the solar battery has a front surface with an installed grating for current capture and a back side, which is a solid contact. During the diffusion phenomenon, an electrical short occurs between the two planes and is transmitted to the end.
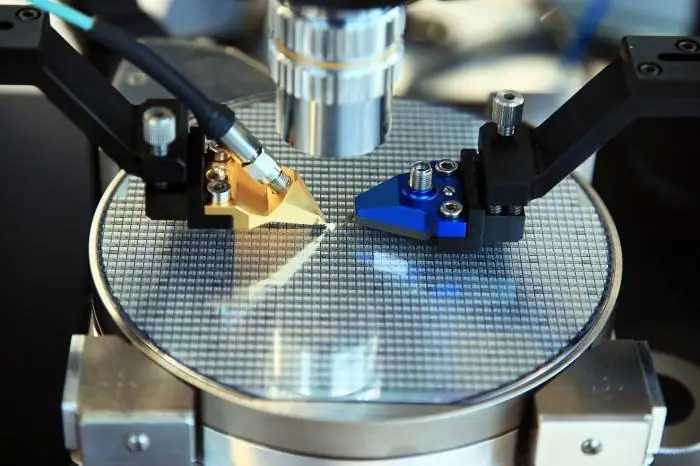
To remove the short circuit, equipment is used tosolar batteries, which allows you to do this with the help of plasma-chemical, chemical etching or mechanical, laser. The method of plasma-chemical influence is often used. Etching is performed simultaneously for a stack of silicon wafers stacked together. The outcome of the process depends on the duration of treatment, the composition of the agent, the size of the squares of the material, the direction of the ion flow jets and other factors.
Application of anti-reflective coating
By applying a texture to the surface of an element, reflection is reduced to 11%. This means that a tenth of the rays are simply reflected from the surface and do not take part in the formation of electricity. In order to reduce such losses, a coating with deep penetration of light pulses is applied to the front side of the element, which does not reflect them back. Scientists, taking into account the laws of optics, determine the composition and thickness of the layer, so the production and installation of solar panels with such a coating reduces reflection by up to 2%.
Contact plating on the front side
The surface of the element is designed to absorb the greatest amount of radiation, it is this requirement that determines the dimensional and technical characteristics of the applied metal mesh. By choosing the design of the front side, engineers solve two opposing problems. The decrease in optical losses occurs with thinner lines and their location at a great distance from one another. The production of a solar battery with an increased grid size leads to the fact that some of the charges do not have time to reach contact and are lost.
Therefore, scientists have standardized the value of the distance and line thickness for each metal. Too thin strips open space on the surface of the element to absorb rays, but do not conduct a strong current. Modern methods of applying metallization consist of screen printing. As a material, silver-containing paste most justifies itself. Due to its use, the efficiency of the element rises by 15-17%.
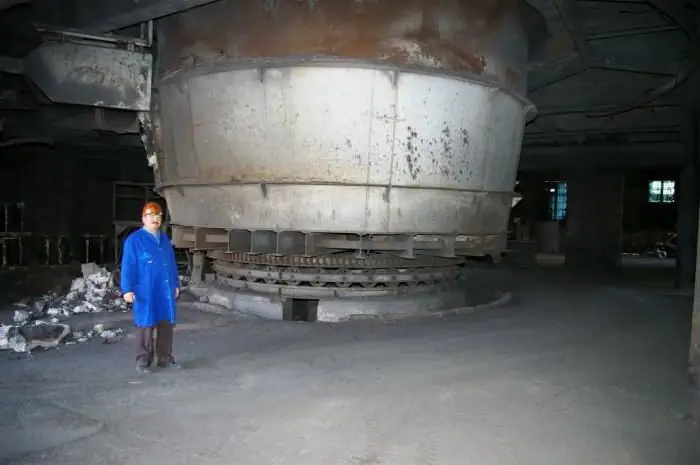
Metallization on the back of the device
Deposition of metal on the back of the device occurs in two ways, each of which performs its own work. A continuous thin layer over the entire surface, except for individual holes, is sprayed with aluminum, and the holes are filled with silver-containing paste, which plays a contact role. The solid aluminum layer serves as a kind of mirror device on the back side for free charges that can be lost in the dangling crystal bonds of the lattice. With such a coating, solar panels work 2% more in power. Consumer feedback says these items are more durable and less affected by cloudy weather.
Making solar panels with your own hands
Power sources from the sun, not everyone can order and install at home, as their cost today is quite high. Therefore, many craftsmen and craftsmen are mastering the production of solar panels at home.
You can buy sets of photocells for self-assembly on the Internet at various sites. Their costdepends on the number of plates used and power. For example, low power kits, from 63 to 76 W with 36 plates, cost 2350-2560 rubles. respectively. They also purchase work items rejected from production lines for any reason.
When choosing the type of photovoltaic converter, take into account the fact that polycrystalline cells are more resistant to cloudy weather and work more efficiently than monocrystalline ones, but have a shorter service life. Monocrystalline ones are more efficient in sunny weather and last much longer.
To organize the production of solar panels at home, you need to calculate the total load of all devices that will be powered by the future converter, and determine the power of the device. From this follows the number of photocells, while taking into account the angle of the panel. Some craftsmen provide for the possibility of changing the position of the accumulation plane depending on the height of the solstice, and in winter - on the thickness of the snow that has fallen.
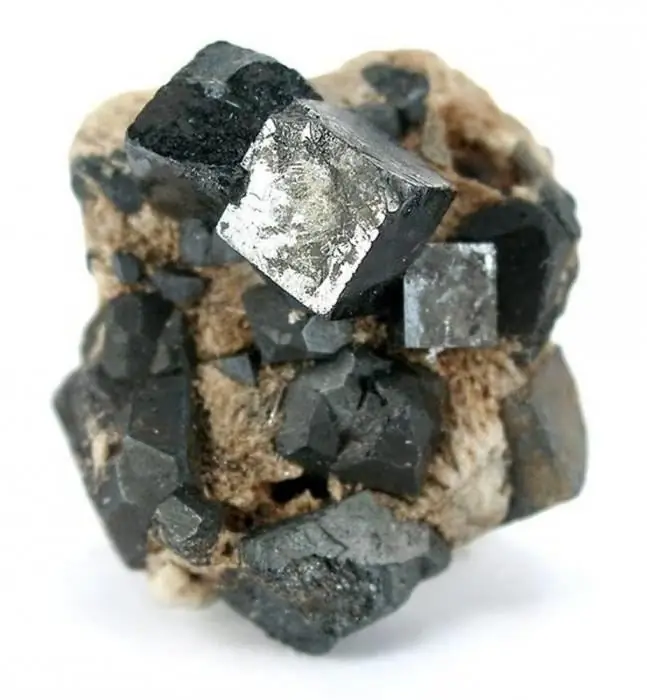
Different materials are used to make the case. Most often they put aluminum or stainless corners, use plywood, chipboard, etc. The transparent part is made of organic or ordinary glass. On sale there are photocells with already soldered conductors, it is preferable to buy such ones, since the assembly task is simplified. The plates are not stacked one on top of the other - the lower ones can give microcracks. Solder and flux are pre-applied. It is more convenient to solder the elements by placing them immediately on the working side. At the end, the extreme plates are welded to the tires (wider conductors), after which the "minus" and "plus" are output.
After the work done, the panel is tested and sealed. Foreign craftsmen use compounds for this, but for our craftsmen they are quite expensive. Homemade transducers are sealed with silicone, and the back side is coated with acrylic-based varnish.
In conclusion, it should be said that the reviews of the masters who made solar panels with their own hands are always positive. Once having spent money on the manufacture and installation of the converter, the family quickly pays for them and starts saving using free energy.
Recommended:
Production of felt boots: technology and equipment
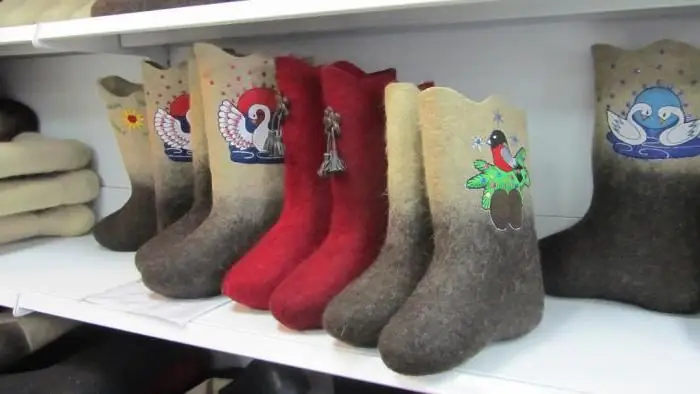
The production of felt boots has remained unchanged for several hundred years. The raw material is natural wool, which shrinks strongly during the manufacturing process, resulting in the best winter shoes for frosty and dry winters
Solar energy in Russia: technologies and prospects. Large solar power plants in Russia
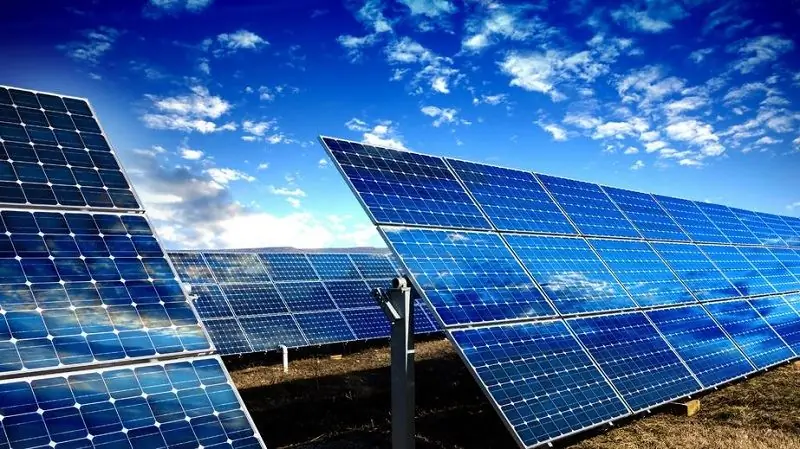
For many years, humanity has been concerned about obtaining cheap energy from alternative renewable resources. Wind energy, ocean wave tides, geothermal waters - all this is being considered for additional electricity generation. The most promising renewable source is solar energy. Despite a number of shortcomings in this area, solar energy in Russia is gaining momentum
Mayonnaise production: equipment and technology
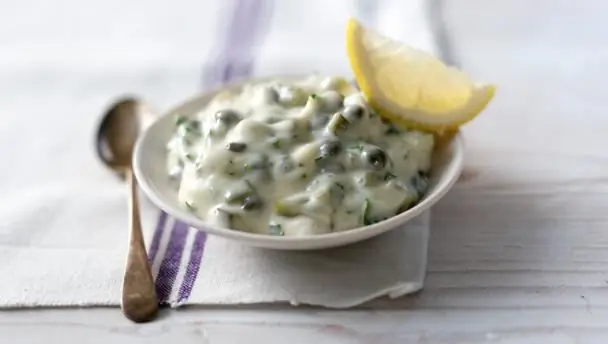
Mayonnaise is a cold emulsion used as a sauce or condiment. It is made by mixing egg yolks and butter, then flavored with various combinations of vinegar, mustard, herbs and spices. Mayonnaise is often used as the base for creamy salad dressings
Robot constructor on a solar battery. Reviews
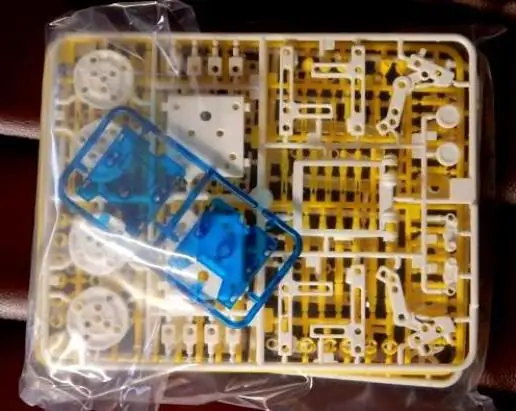
The solar-powered construction set is interesting for both children and adults. The big advantage of this toy is that it does not require batteries. It moves from the energy of the sun or a lamp. What do consumers think about this know-how? What difficulties do they face in assembling such robots?
PVC pipe production: technology, raw materials and equipment
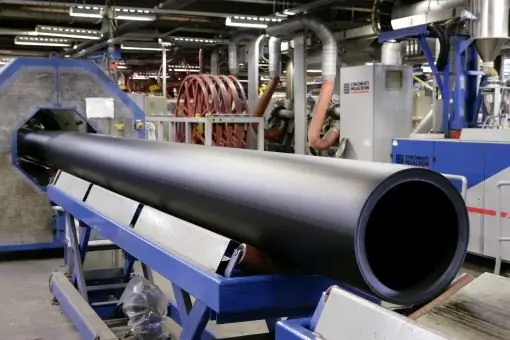
Tubular products based on polyvinyl chloride (PVC) are widely used today in a variety of areas and industries from the private sector to large oil and gas enterprises. But the process of their consolidation on the market was gradual, since the physical and technical properties of the polymer material are inferior to traditional metal counterparts in a number of criteria. However, the modern production of PVC pipes, due to the introduction of advanced technologies, has significantly increased the performance of products