2025 Author: Howard Calhoun | [email protected]. Last modified: 2025-01-24 13:10
DKVR-20-13 is a vertical water tube steam boiler with a shielded combustion chamber. Its design also includes a boiling beam. These structural elements are carried out according to the "D" scheme. A distinctive feature of this scheme is the lateral location of the convective part of the device in relation to its combustion chamber.
Main indicators of the unit
It is worth starting with the technical characteristics of the DKVR-20-13. As noted earlier, this type of unit refers to steam boilers. Its steam capacity is 20 t/h. As for the type of fuel used for work, it is gas or liquid fuel. The excess or operating pressure of the coolant at the outlet of the boiler is 1.3 MPa. The outlet steam temperature is considered one of the main indicators. It can be equal to 194 degrees Celsius in the case of saturated steam or 250 degrees in the case of superheated. An important component is the temperature of the feed water - 100 degrees. Efficiency, according to calculations,is 92%. The consumption of fuel used is determined in kg / h and is 1470. The boiler belongs to large-sized installations, and its mass is 44634 kg.
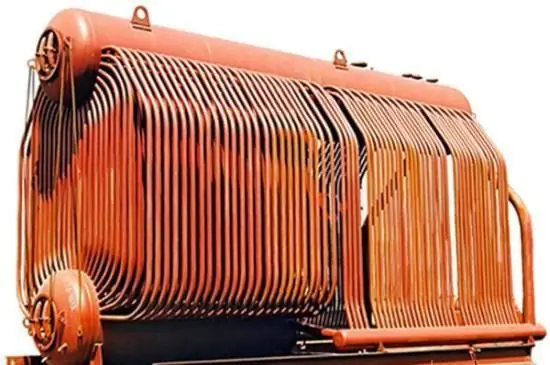
Description of the unit
The steam boiler DKVR-20-13 consists of several main structural elements: the upper short drum and the lower, shielded combustion chamber, which was mentioned earlier. Next, it is worth considering in more detail this unit and some of its parts.
The device DKVR-20-13 has a feature that the combustion chamber is divided into two parts: the furnace itself, as well as the afterburning chamber. This chamber is separated from the firebox by the rear screen of the boiler. Hot gases are supplied to the boiler tubes of the device by direct current and across the entire width of the beam. On the way they do not have any partitions. However, in case of additional installation of a superheater on the DKVR-20-13 boiler, some of these pipes may not be installed. The superheater itself will consist of a pair of packages. They will be located on different sides of the boiler. After working off, superheated steam from both packages will be discharged to a special collection manifold. The device of the DKVR-20-13 unit uses feed water, which will be supplied to the upper drum. Now about him.
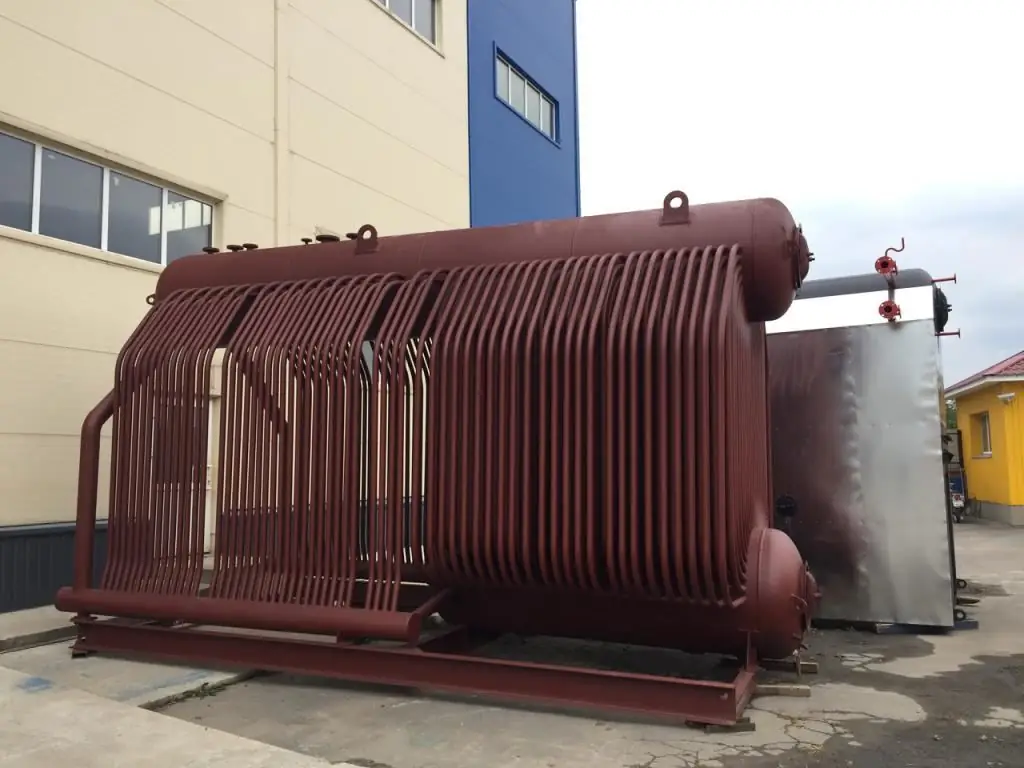
Boiler drum
The upper drum is subject to severe overheating, and therefore it must be cooled. To cool the walls of this structural element, a mixture of water andsteam that comes out of the tubes from both the side screens and from the front of the convective bundle.
The upper drum has an element called the upper generatrix. It usually contains such structural elements as safety valves, a steam valve or a valve, a valve for possible steam extraction for own needs (for blowing).
In the upper drum there is a water space through which the feed pipe passes. Separation devices pass in the space filled with steam.
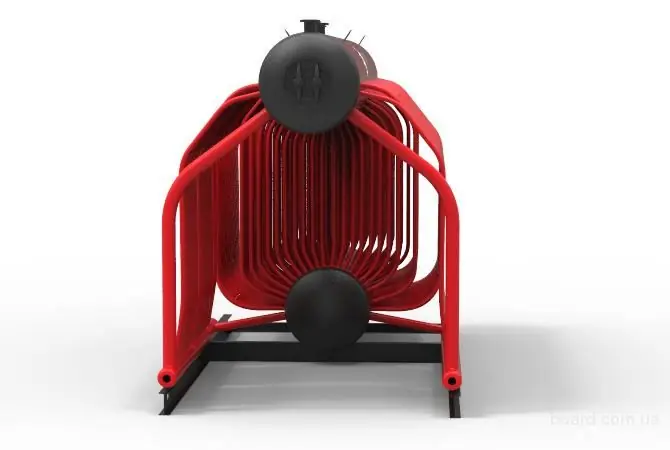
Distinguishing Features
When describing the DKVR-20-13, it should be noted that the design has certain distinctive features. Which distinguish this model from others, with a lower rate of steam production. Among them it is worth noting:
- The upper drum of the unit 20-13 is shorter, because of which it does not fall into the boiler furnace. At the same time, both the upper and lower drums are equal in length - 4500 mm. It is also worth adding that the presence of a shortened upper drum led to the absence of the need for its shotcrete, and also increased the reliability of the equipment as a whole.
- Due to the fact that the upper drum was reduced, and the amount of water and steam produced had to be left at the same level, it was decided to add two remote cyclones to the design. These elements generate about 20% of the total steam volume.
- The lower drum has also been slightly modified. It has been raised above zero to improve accessibility and convenience.during inspection and maintenance.
- The DKVR-20-13 boiler has a large number of screens. Two of them are located on the right side, two more on the left side, one front and one rear screen. In addition, each of them has two collectors in its composition. Thus, it turns out that the boiler is equipped with 12 collectors, six of which are located at the top, six at the bottom.
- Another design feature that affects the side screens is their division into two blocks. The first block is considered to be the side screens for the first stage of evaporation, respectively, the second block is the second stage of evaporation. In addition, the second block is usually located in front of the convective beam, and the screens are usually counted from the front of the boiler.
- The last design feature is L-shaped side pipes for screens. Their installation is carried out according to the following principles. For example, the first pipe for the right side screen will have its lower end welded to the lower right header and its upper end welded to the upper left screen header. The first pipe for the left screen will be attached in the same way. Further cross-connection in this way results in the combustion chamber being completely shielded.
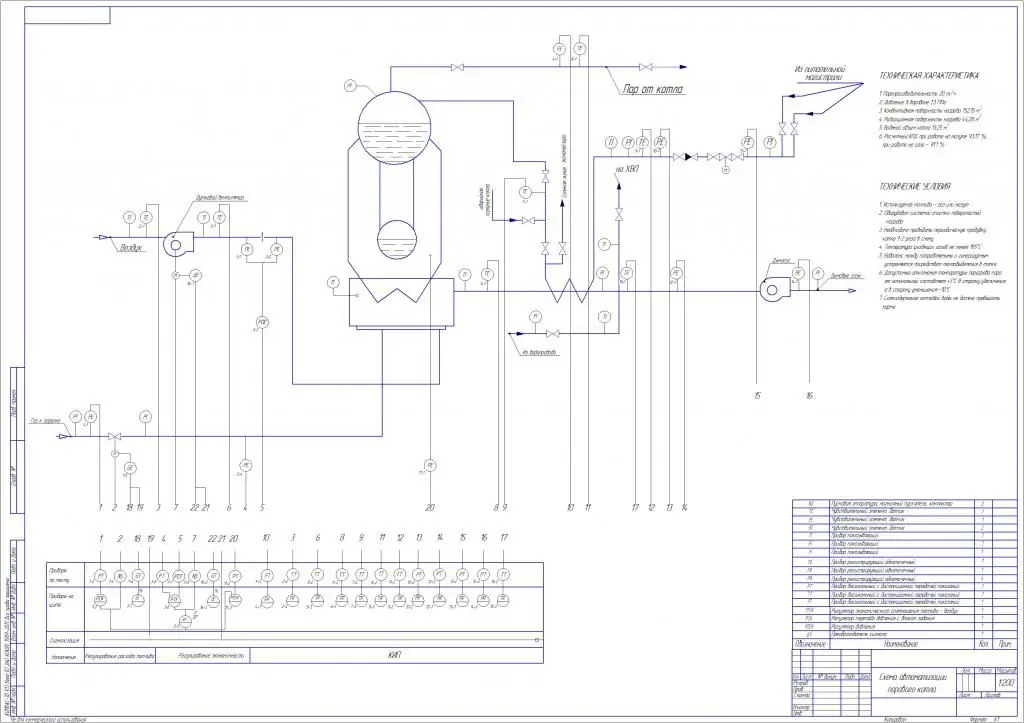
And in the end, we can add that the convective beam has no partitions in its design.
Common Aggregate Problems
Repair of boilers should be trusted only to professionals. Among the most commonproblems that can be detected, scale formation is highlighted. This defect will be characterized by a decrease in the heat output of the boiler, as well as a decrease in its overall performance indicator. Among other common causes of breakdowns, incorrect maintenance or non-compliance with the rule of these works stands out. Often the cause can be an error at the design stage of the system or installation of the unit itself.
In any case, the repair of this type of boiler is very expensive. To avoid the need for this work, diagnostics of all parts and the system as a whole should be carried out as often as possible. In addition, preventive cleaning work should be carried out to avoid scale formation.
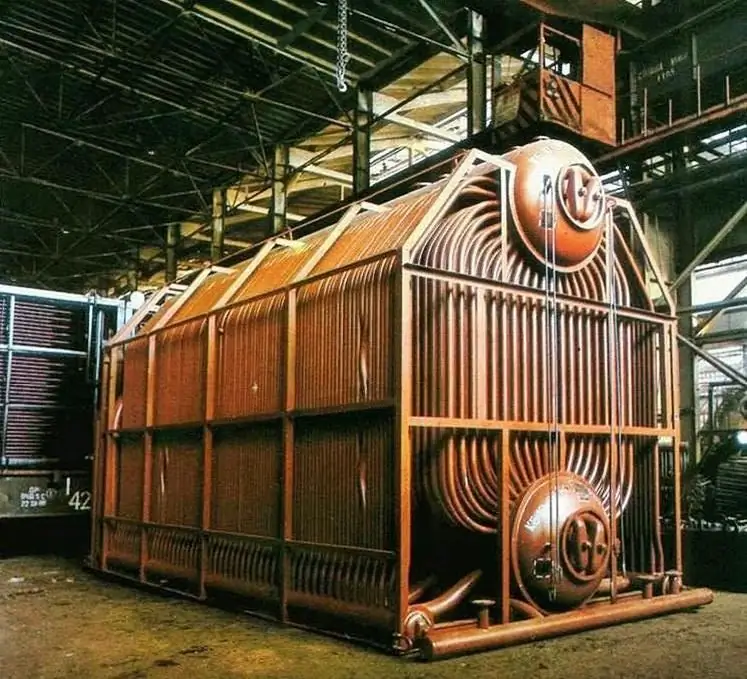
Bricking. Features
During the installation of the DKVR-20-13 boiler, brickwork is an obligatory part. At the same time, the thickness of the walls for it should be 510 mm - this is the thickness of two bricks. All walls should have this thickness except for the back. Here, reduction to a thickness of 1.5 bricks or 380 mm is allowed. In addition, the rear wall is usually covered on the outside with a layer of plaster 20 mm thick. This is done in order to reduce the number of suction cups.
Such brickwork is considered heavy, and therefore it is made of red brick. Fireclay bricks are also used here, with which they lay out the walls facing the furnace. Their thickness should be 125 mm.
The walls of the afterburner must be 250 mm thick. It is necessary to make a partition between the beam pipes. Both of thesethe structural elements of the lining must be made of fireclay bricks.
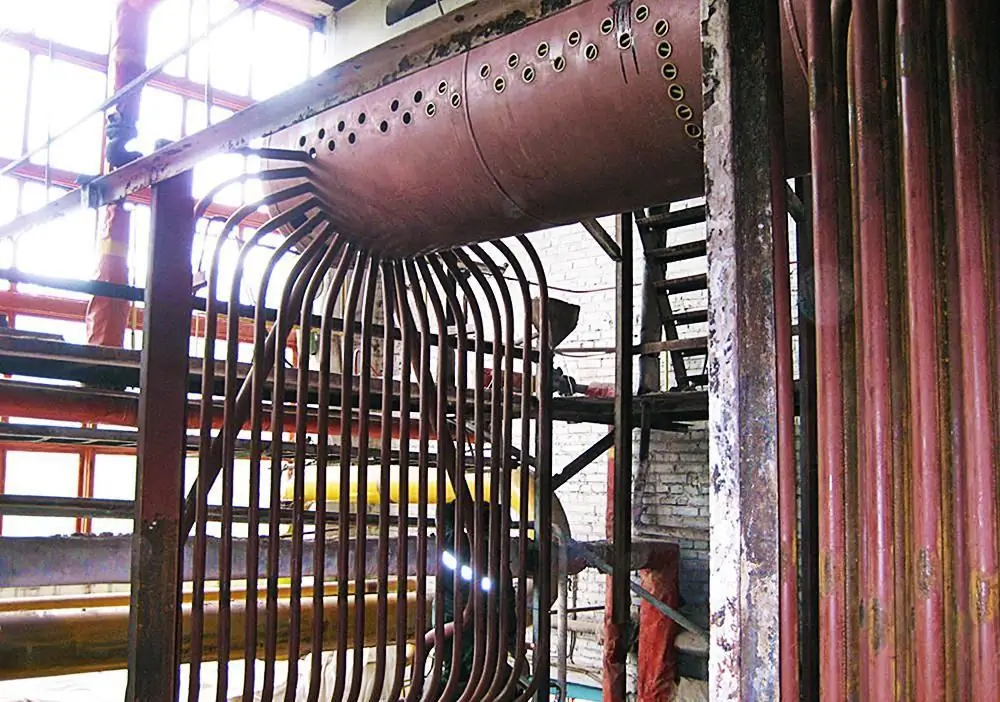
Front screen operation
The operation manual for the DKVR-20-13 boiler is attached to each unit and contains all the necessary instructions for using the unit, caring for it and carrying out maintenance. However, the operation of some parts should be studied in more detail.
Water circulates around the circuit in the front screen. The lower collector of this screen belongs to the first evaporation stage. It is fed with water from the upper drum through two bypass pipes. During operation of the unit, not all water evaporates. Unevaporated liquid will also enter this collector from the upper drum. There are four special downpipes for this. Further, there are riser pipes in the structure, through which from the lower collector, the liquid will move upwards. It will heat up, turning into a steam-water mixture, after which it will be fed into the upper manifold.
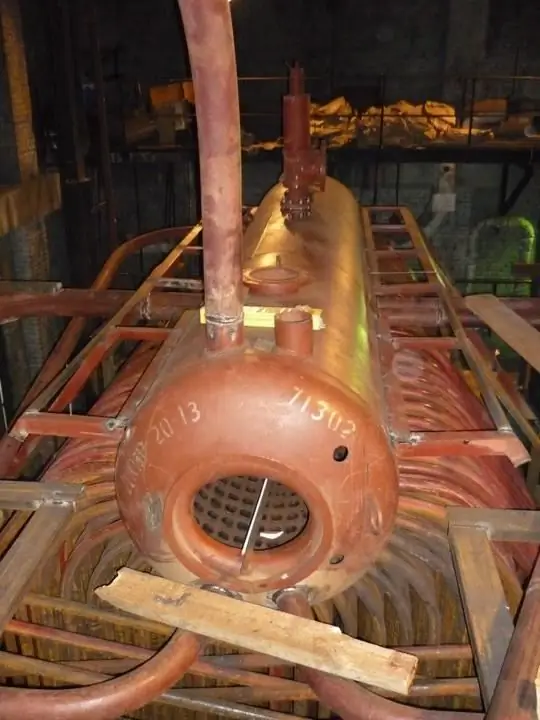
Moving gases
After the combustion of the fuel, gases will be formed that move into the afterburner. A superheater is usually installed at the end of such a chamber. Since the design of this particular boiler does not provide for the presence of partitions in front of the beam, these exhaust gases will pass through it, giving off their heat. After that, they will be removed from the boiler along its entire width of the rear wall. After that, there is a special gas duct through which gases will be delivered toeconomizer.
Changes in design
As noted earlier, data has been produced since 1961. The peculiarity was that they were originally intended for burning solid fuels, such as hard and brown coal or anthracite. However, after that, the fuel balance was changed in the country and it was necessary to switch to burning liquid and gas fuels. It did not make any special changes to the design.
It is important to note here that after switching to such types of fuel, a forced operation mode from nominal to 140% was allowed. This led to a strong increase in emergency situations. Their bulk consisted in the failure of the s alt compartment and cyclones.
Water heating mode
At the end it is worth adding that the boiler can be operated in hot water mode. This allows you to reduce fuel consumption during operation, increase the productivity of the unit, reduce the cost of resources for the unit's own needs, and reduce the cost of preparing the liquid.
If we consider all these benefits in aggregate from the point of view of increasing efficiency, then on average this figure increases by 2-2.5%.
Based on the above, we can draw the following conclusion. These units were good units for their time, but now technology allows the manufacture and operation of better equipment.
Recommended:
Diamond boring machine: types, device, operating principle and operating conditions
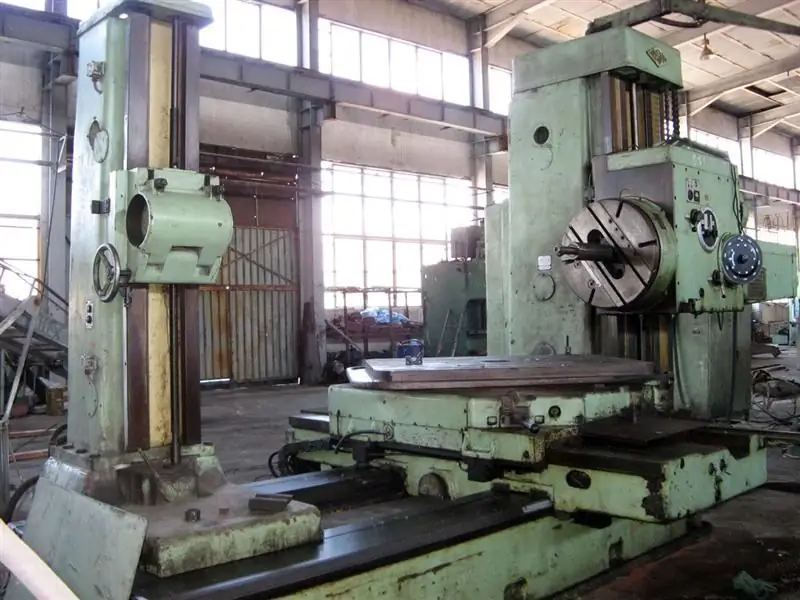
The combination of a complex cutting direction configuration and solid-state working equipment allows diamond boring equipment to perform extremely delicate and critical metalworking operations. Such units are trusted with the operations of creating shaped surfaces, hole correction, dressing of ends, etc. At the same time, the diamond boring machine is universal in terms of application possibilities in various fields. It is used not only in specialized industries, but also in private workshops
Duration of the operating cycle. What is an operating cycle?
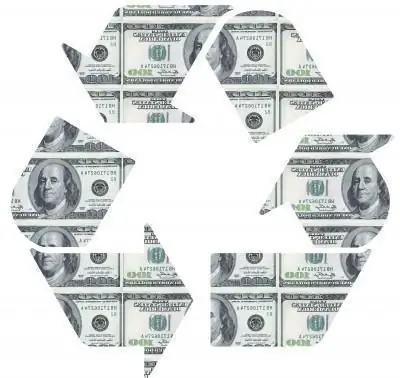
The company will not have problems with a lack of current assets if the management begins to strictly control the proportions between equity and debt capital, through which operations are financed
Bulldozer T 25: description, specifications, engine and operating features
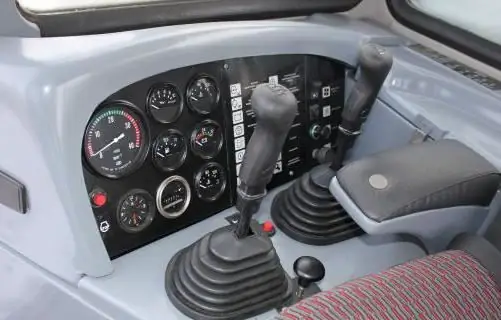
The T-25 bulldozer, produced by the Promtractor plant in Cheboksary, is characterized by increased cross-country ability and excellent technical characteristics. This model is used mainly by enterprises of the industrial and oil and gas complex
Maintenance of boiler rooms, repair and commissioning
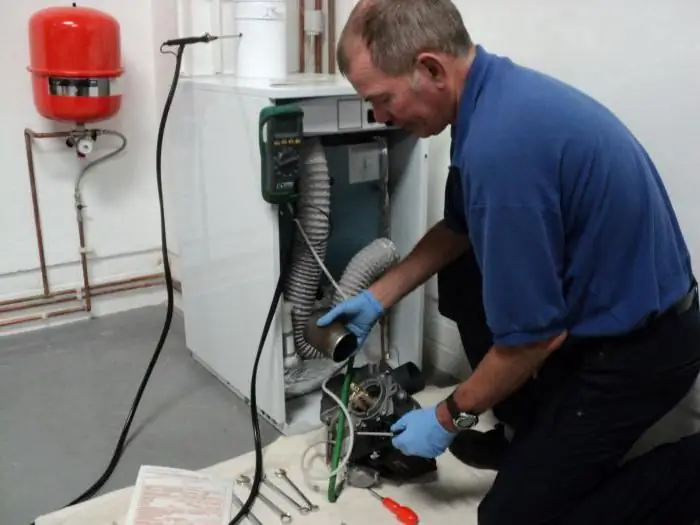
The article is devoted to the maintenance of boiler rooms. Considered the nuances of repair operations and commissioning
How to open a tailoring and repair shop: instructions and recommendations
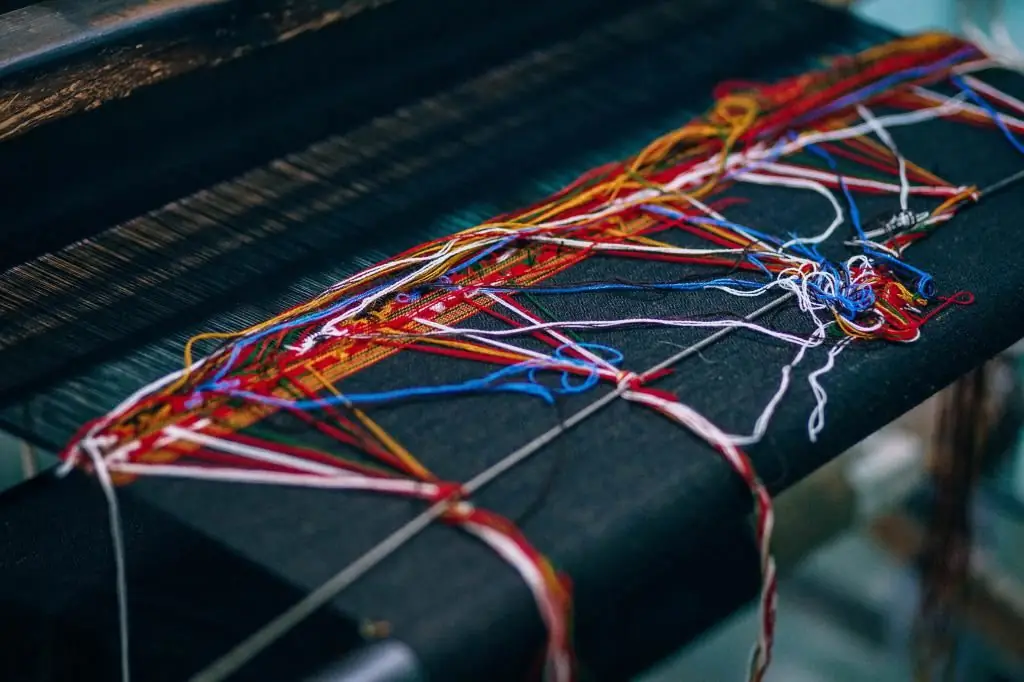
Repair and tailoring services are in demand in any city. Some businessmen are sure that starting such a business is easy, but, as practice shows, this is far from the case. This article discusses in detail the question of how to open an atelier