2025 Author: Howard Calhoun | [email protected]. Last modified: 2025-06-01 07:12
Copper and copper alloys have high electrical and thermal conductivity, can be machined, have good corrosion resistance, so they are actively used in many industries. But when it enters a certain environment, corrosion of copper and its alloys still manifests itself. What is it and how to protect products from damage, we will consider in this article.
What is corrosion
This is the destruction of metals as a result of exposure to the environment. In countries with a well-developed industry, the damage from corrosion is 4-5% of national income. Not only metals deteriorate, but also mechanisms and parts made from them, which leads to very high costs. Corroded pipelines often leak harmful chemicals, resulting in soil, water and air pollution. All this adversely affects people's he alth. Corrosion of copper is its spontaneous destruction under the influence of individual elements of the human environment. The cause of damage to the metal is instabilityit to individual substances in the air. The higher the temperature, the higher the corrosion rate.
Copper properties
Copper is the very first metal that man began to use. It is golden in color, and in the air it becomes covered with an oxide film and acquires a red-yellow color, which distinguishes it from other metals that have a gray tint. It is very plastic, has high thermal conductivity, is considered an excellent conductor, second only to silver. In weak hydrochloric acid, fresh and sea water, copper corrosion is negligible.
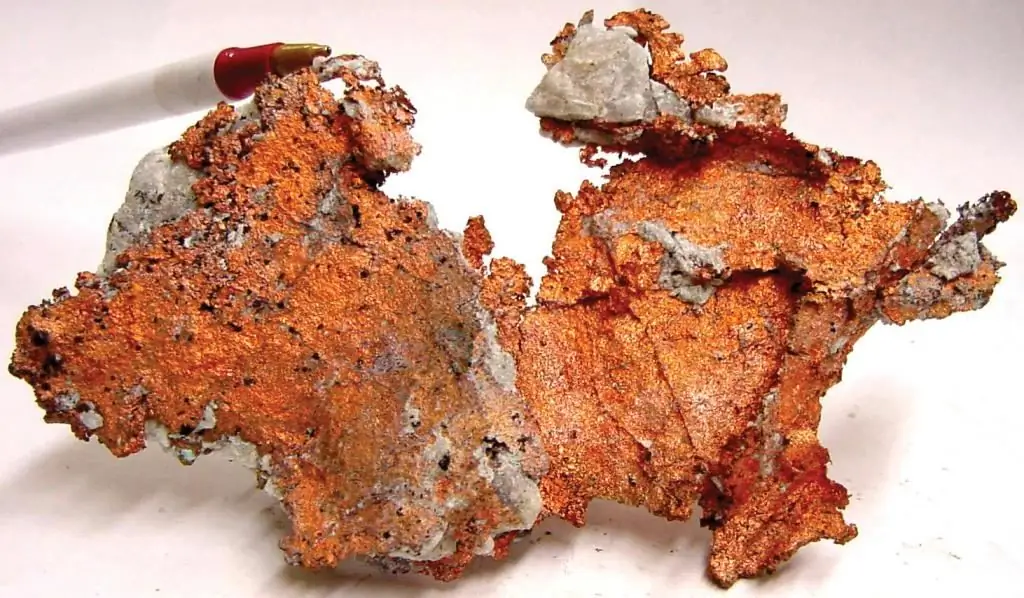
In the open air, the metal oxidizes with the formation of an oxide film that protects the metal. Over time, it darkens and becomes brown. The layer that covers copper is called patina. It changes its color from brownish to green and even black.
Electrochemical corrosion
This is the most common type of destruction of metal products. Electrochemical corrosion destroys machine parts, various structures located in the ground, water, atmosphere, lubricating and cooling liquids. This is damage to the surface of metals under the influence of an electric current, when, during a chemical reaction, electrons are released and transferred from cathodes to anodes. This is facilitated by the heterogeneous chemical structure of metals. When copper contacts iron, a galvanic cell appears in the electrolyte, where iron becomes the anode, and copper becomes the cathode, because iron in the series of voltages according to the periodic table is to the left of copper and is more active.
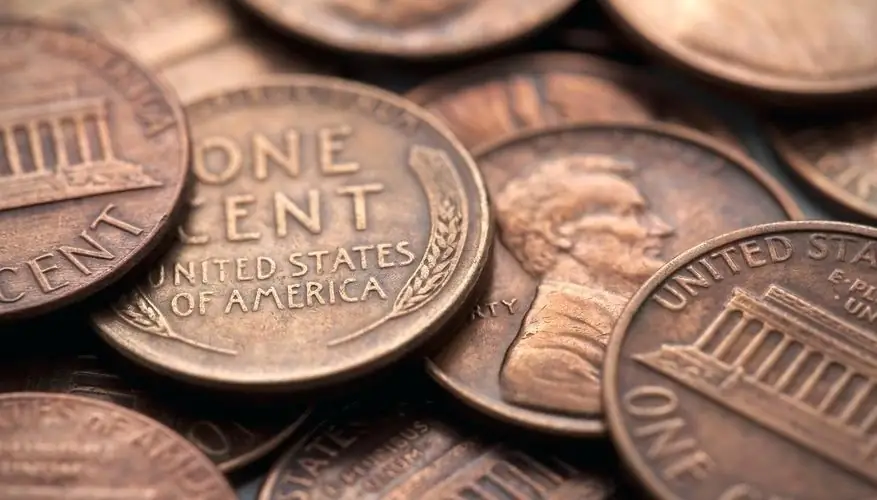
In a pair of iron with copper, iron corrosion occurs faster than copper. This is because when iron is destroyed, electrons from it pass to copper, which remains protected until the entire layer of iron is completely destroyed. This property is often used to protect parts and mechanisms.
Effect of impurities on the deterioration of metals
It is known that pure metals practically do not corrode. But in practice, all materials contain some amount of impurities. How do they affect the safety during operation of products? Assume that there is a part made of two metals. Consider how the corrosion of copper with aluminum occurs. When exposed to air, its surface is covered with a thin film of water. It should be noted that water decomposes into hydrogen ions and hydroxide ions, and carbon dioxide dissolved in water forms carbonic acid. It turns out that copper and aluminum, immersed in a solution, create a galvanic cell. Moreover, aluminum is the anode, copper is the cathode (aluminum is to the left of copper in the voltage series).
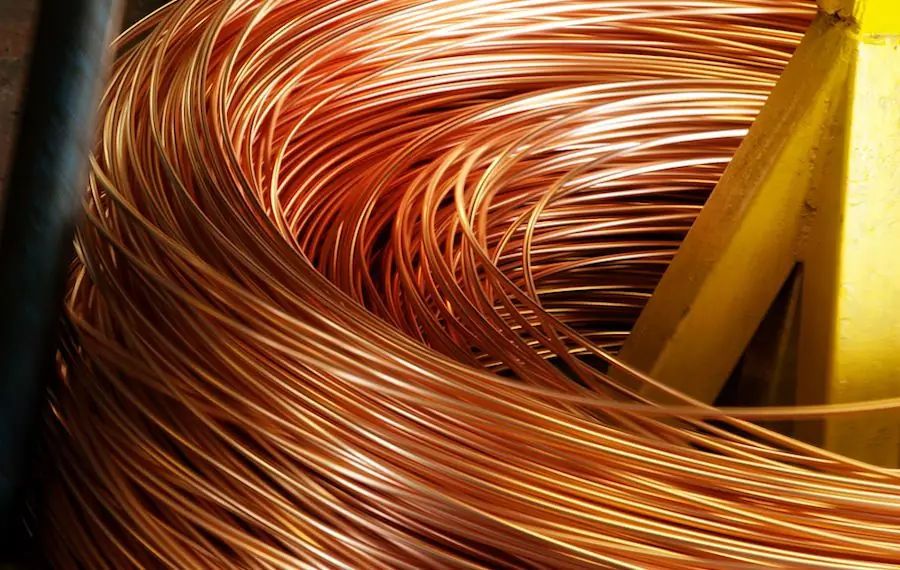
Aluminum ions enter the solution, and excess electrons pass to copper, discharging hydrogen ions near its surface. Aluminum ions and hydroxide tones combine and deposit on the aluminum surface as a white substance, causing corrosion.
Corrosion of copper in acid environments
Copper exhibits good resistance to corrosion in all conditions as it rarely displaces hydrogen because it is in the electrochemical voltage seriesstands near precious metals. The widespread use of copper in the chemical industry is due to its resistance to many aggressive organic media:
- nitrates and sulfides;
- phenolic resins;
- acetic, lactic, citric and oxalic acid;
- potassium and sodium hydroxides;
- weak solutions of sulfuric and hydrochloric acid.
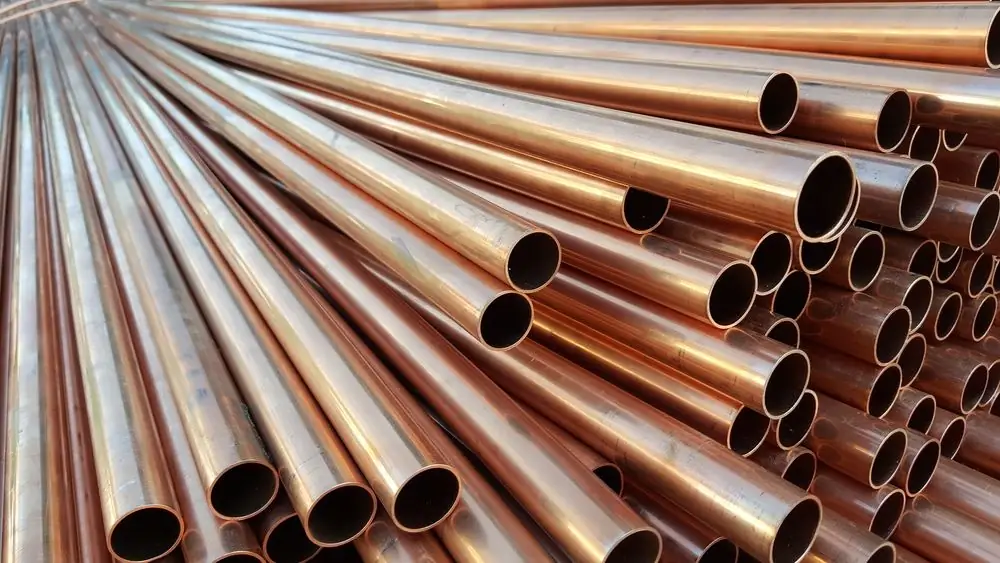
On the other hand, there is a strong destruction of copper in:
- acid solutions of chromium s alts;
- mineral acids - perchloric and nitric, and corrosion increases with increasing concentration.
- concentrated sulfuric acid, increasing with increasing temperature;
- ammonium hydroxide;
- oxidizing s alts.
Metal Preservation Methods
Practically all metals in a gaseous or liquid medium undergo surface destruction. The main way to protect copper from corrosion is to apply a protective layer to the surface of products, consisting of:
- Metal - a layer of metal is applied to the copper surface of the product, which is more resistant to corrosion. For example, brass, zinc, chromium and nickel are used as it. In this case, contact with the environment and oxidation will occur with the metal used for the coating. If the protective layer is partially damaged, then the base metal, copper, is destroyed.
- Non-metallic substances are inorganic coatings consisting of vitreous mass, cement mortar, or organic - paints, varnishes, bitumen.
- Chemicalfilms - protection is formed by a chemical method, creating compounds on the metal surface that reliably protect copper from corrosion. To do this, oxide, phosphate films are used or the surface of the alloys is saturated with nitrogen, organic substances, or treated with carbon, the compounds of which reliably preserve it.
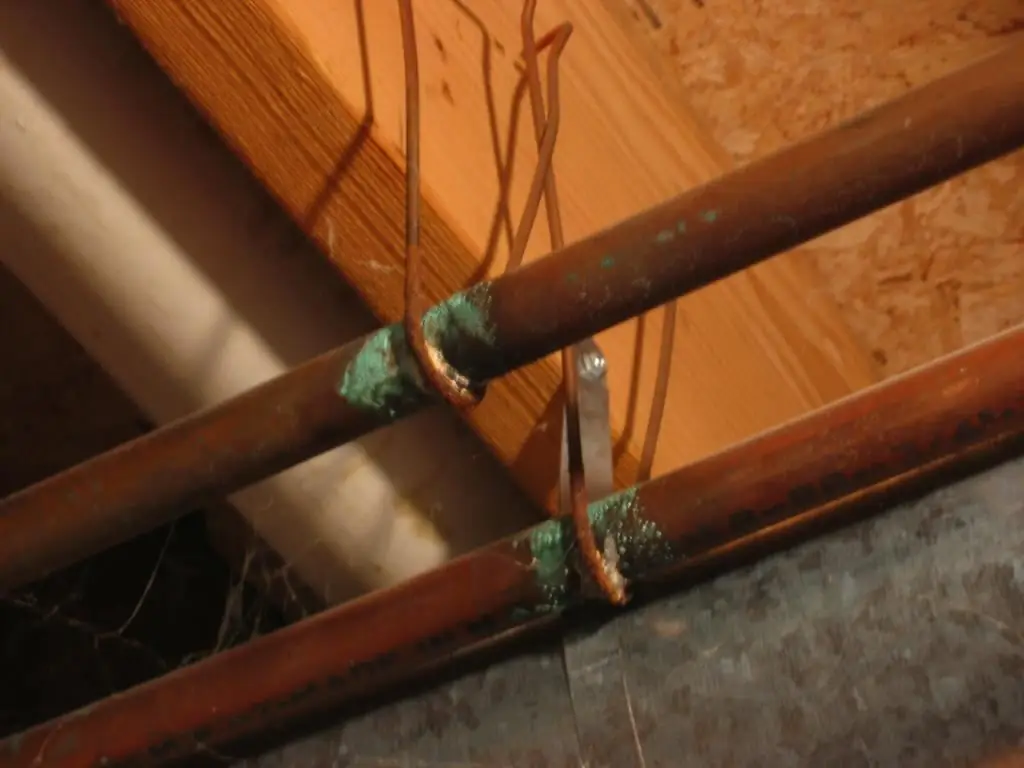
In addition, an alloying component is introduced into the composition of copper alloys, which enhances the anti-corrosion properties, or the composition of the environment is changed, removing impurities from it and introducing inhibitors that slow down the reaction.
Conclusion
Copper is not a chemically active element, because of this, its destruction is very slow in almost any environment. Therefore, it is widely used in many sectors of the national economy. For example, metal is very stable in clean fresh and sea water. But as the oxygen content increases or the water flow speeds up, the corrosion resistance decreases.
Recommended:
Corrosion of aluminum and its alloys. Methods for combating and protecting aluminum from corrosion
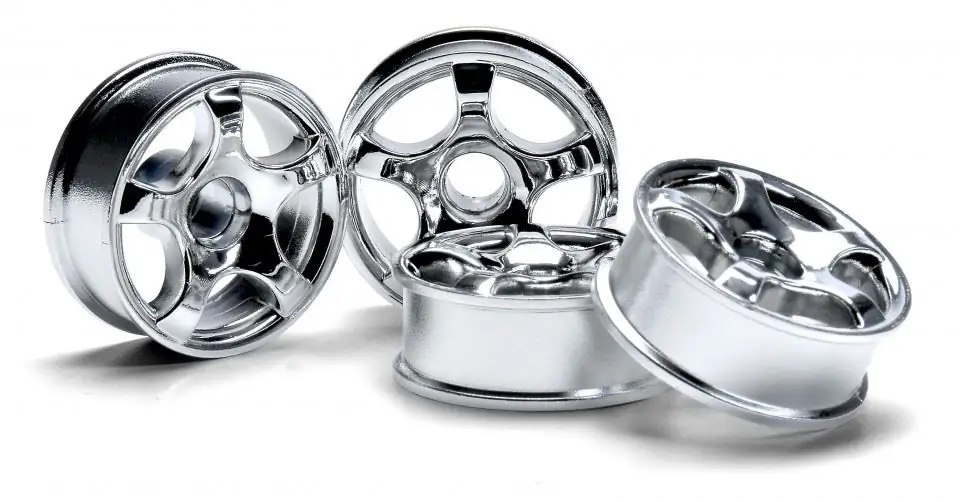
Aluminium, unlike iron and steel, is quite resistant to corrosion. This metal is protected from rust by a dense oxide film formed on its surface. However, in the case of destruction of the latter, the chemical activity of aluminum greatly increases
Pitting corrosion: causes. Methods for protecting metals from corrosion
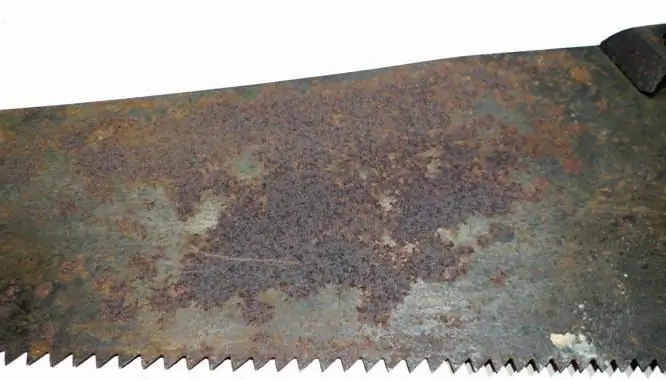
During the operation of metal products, they are exposed to various types of destructive effects, among which pitting corrosion stands out as the most dangerous and unpredictable
Heat-resistant alloys. Special steels and alloys. Production and use of heat-resistant alloys
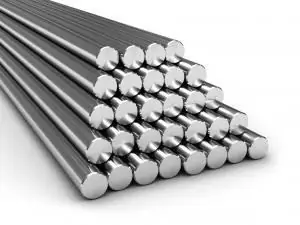
Modern industry cannot be imagined without such material as steel. We encounter it at almost every turn. By introducing various chemical elements into its composition, it is possible to significantly improve the mechanical and operational properties
Corrosion and erosion of metals: causes and methods of protection
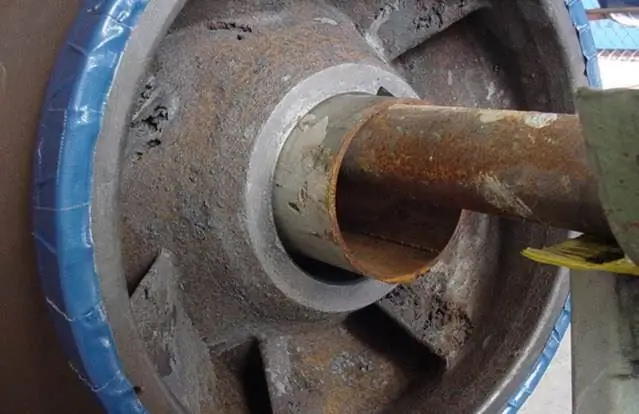
Chemical, mechanical and electrical external influences often occur in metal product operating environments. As a result, with improper maintenance of such elements, as well as ignoring safety standards, there may be risks of deformation and damage to structures and parts. This is due to the emerging processes of corrosion and erosion of metals, which in the long term contribute to the complete destruction of the structure of the product
Welding of copper and its alloys: methods, technologies and equipment
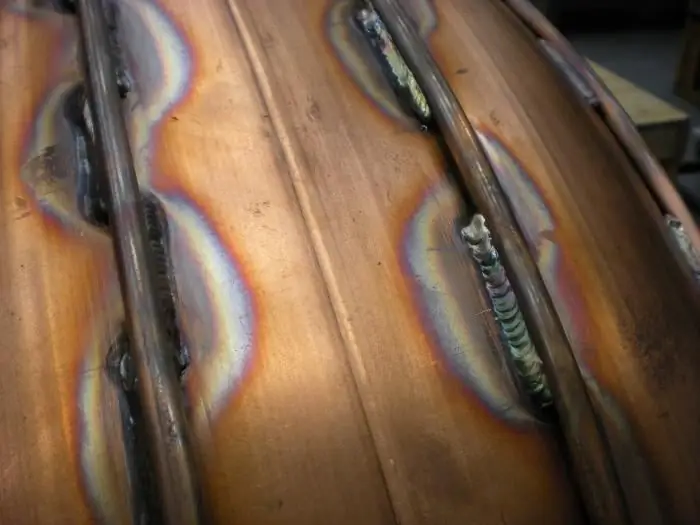
Copper and its alloys are used in various sectors of the economy. This metal is in demand due to its physicochemical properties, which also complicate the processing of its structure. In particular, the welding of copper requires the creation of special conditions, although the process is based on fairly common thermal treatment technologies