2025 Author: Howard Calhoun | [email protected]. Last modified: 2025-01-24 13:10
A coordinate machine can have 3 or more axes. In the simplest case, this is a horizontal, vertical and rotational movement. 5-axis systems are the optimal solution, allowing the processing of most complex products. Tilt or swivel mechanisms can be added to existing axles for more specialized applications.
Assignment of multi-axis systems
The coordinate machine has independent axes that simultaneously orient the tool and the part relative to it. Additional axes include an anti-spindle assembly, table rotation, mechanisms for unloading and loading workpieces. Controlled by machine controllers.
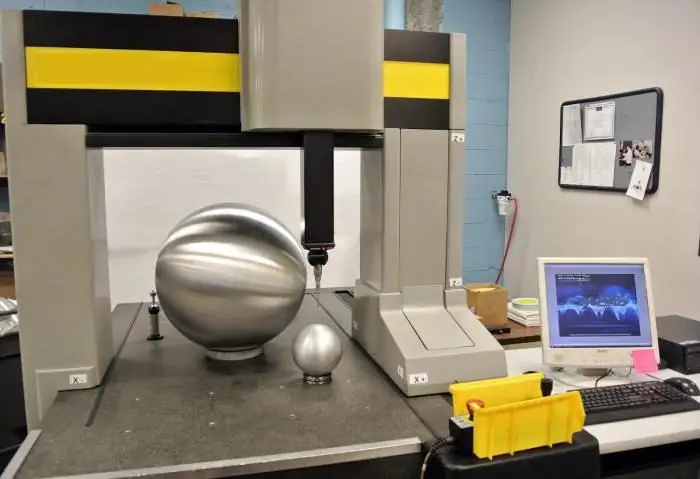
The coordinate machine has such a name due to the accuracy of making holes on the surface of the workpiece along any axis of the system. As a rule, the table moves in two coordinates, and the tool moves vertically in the third. Let's add the ability to rotate the part itself and change the inclined surface.
The coordinate machine is equipped with two additional axes that move the tool itself in a two-coordinate system, which allows you to perform even the most complex grooves and holes.
Classic symbols
All CNC machines try to produce with standard axis names. However, the manufacturer can change the letter designation at its discretion. It so happened that horizontal movement is associated with the Latin letter X, Y more often plays the role of a vertical projection, but on 5-coordinate systems this axis is the second direction of movement of the table.
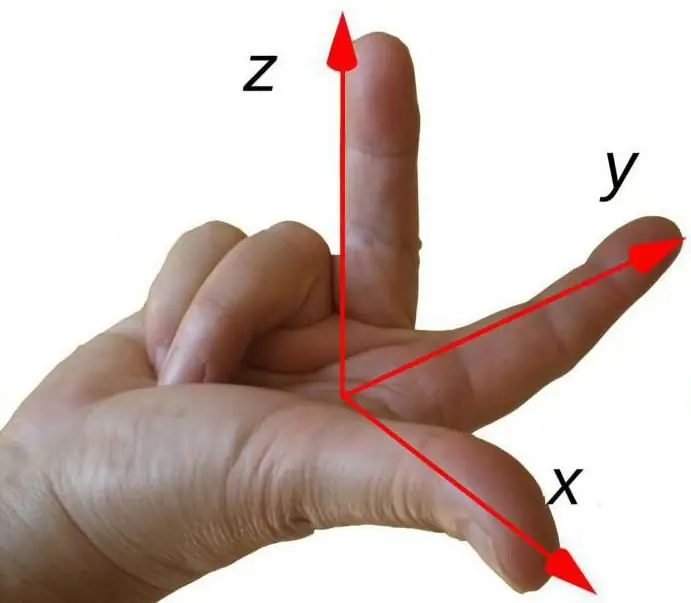
Moving vertically and in the direction of movement of the tool to the part is denoted by the Latin letter Z. Moreover, the increase in the position count occurs in the direction from the workpiece. C axis is more often referred to as rotational movement, more often this designation is used for cylindrical processing.
Additional axes are assigned according to the continuation of the alphabet. However, the rotation disk of the tool is assigned the letter A. The counter spindle is referred to as the letter E. Further names are chosen by the machine manufacturer according to their preferences.
Variety of axle options
Jig milling machine becomes more expensive with each added axis. Moving the tool itself along two coordinates gives great opportunities for cutting in hard-to-reach places. However, this must be justified in terms of technology.
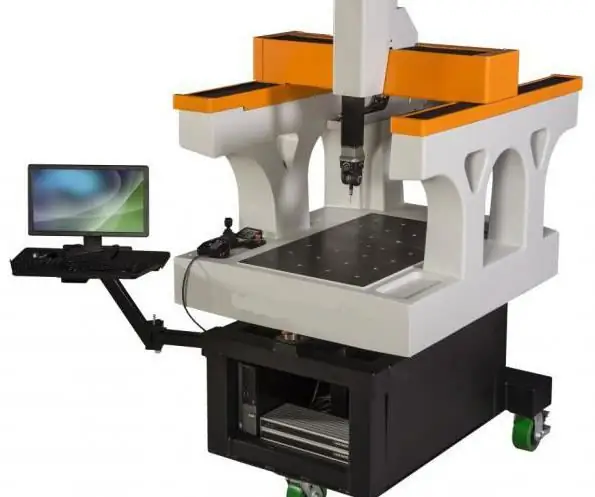
Often the addition of the rotation of the tool itself reduces the strength of the entire structure and such systems become less durable. The less kinematic connections are present, the more reliable it becomesmachine and it is capable of processing tougher materials. A more rational solution would be not to complement the rotation of the tool, but to choose models with a rotary table.
The last version of the machine rotates a larger unit, but this model will undoubtedly be more expensive. However, an important characteristic of the jig boring machine remains: structural rigidity and reliability. This parameter decreases when processing parts by weight exceeding the normal allowable parameters.
Multi-Axis Capabilities
Jig drilling machine allows you to get complex parts:
- Bosses, irregular holes.
- Shaped surfaces, body products.
- Gears, gears, impellers, rotors.
- Stiffening ribs are easily processed.
- Holes in any projection at different angles, grooves, threads.
- All complex parts requiring curved machining.
- In one cycle, the entire surface of the workpiece can be machined.
Recently, vacuum tables have been widely used to hold the workpiece by suction of air. Classic fasteners are no longer used, which reduces the time to remove and install a new workpiece.
Complete production process
The CNC milling machine works according to the standard algorithm. First, a model of the future part is created on paper or a personal computer. What follows is the transfer of dimensions and contours through the application into a machine-understood form of vector graphics. The programmer setsdirection of movement of the tool, inserts technological pauses. Selects the type of tool, processing speed, positioning accuracy of rotary axes.
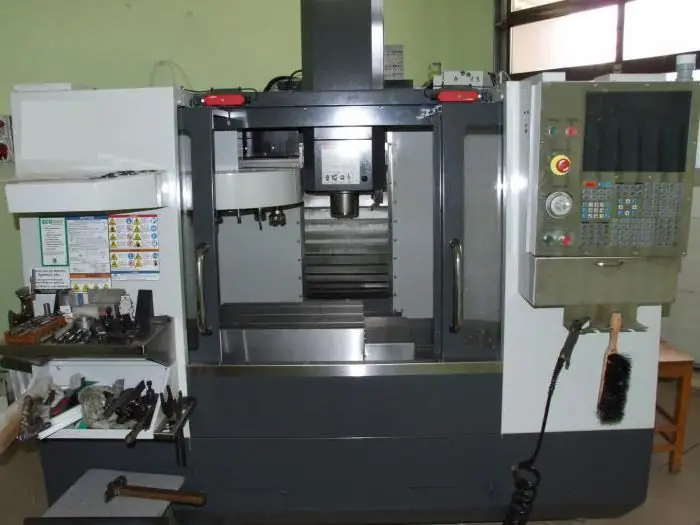
After converting the model into machine codes, the machine is ready to cut the part. But before that, debugging of the program follows. First, 3D-working out of movements and control of the result is carried out. Then, at a limited feed, the automation cycle is started without rotation of the main assembly - the spindle. If everything goes smoothly and without deviation of the trajectory of the movement, then the cutting of the part begins.
It should be remembered that no CNC machine can physically be protected from the ignorant. At best, manufacturers provide soft safety clutches against mechanical damage. But even such a small breakdown can lead to a long downtime of the equipment. Therefore, all figures entered into the processing program must be meaningful and calculated. They act similarly when adding correctors for tool wear and backlash compensation.
Tools for creating programs and exporting to the machine
A coordinate machine, like a conventional one, has an internal memory and a set of standard interfaces that allow you to “fill in” control programs via connectors: USB, COM, Flash-card, Ethernet, wireless methods. All of the above methods of recording programs are options and add a burden to the cost of the equipment. In the simplest case, the machine can be controlled through an old PC using the installed control board and the correspondingapplications. This implementation is the most accessible, but to organize the correct operation of all nodes, considerable knowledge in the field of machine tool building is required.
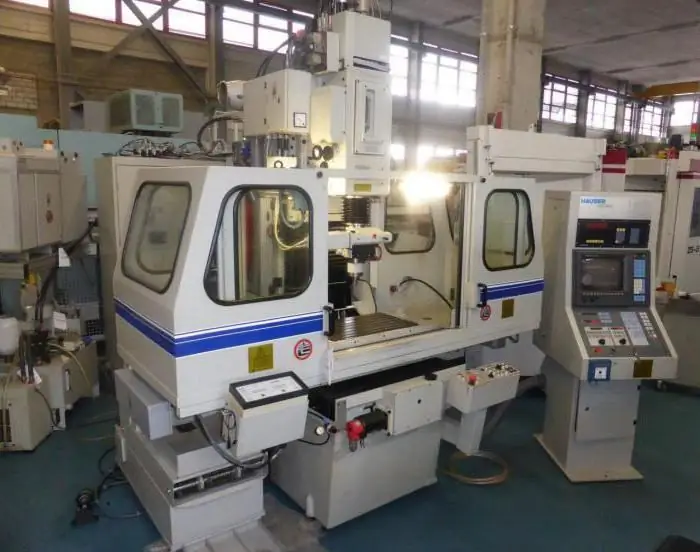
CAD/CAM applications are used to create control codes. Their choice is huge, there are also free options from leading manufacturers of machine tools. However, in the serial production of parts, a whole team of workers is required, consisting of a designer, programmer, adjusting technologist and repairman. As practice has shown, one person will not be able to simultaneously engage in an automated cycle and make improvements to the current processing process. With the help of applications, this possibility has partially arisen, but so far there is no universal means that excludes human participation in the calculations of the parameters of the final product.
Technological shutdown
Pauses in the processing of the part are required to remove the accumulated coolant and chips from the cutting zone, to control the parameters and externally inspect the integrity of the tool. They are also needed for intensive processing, when it takes time to cool the heated parts of the workpiece.
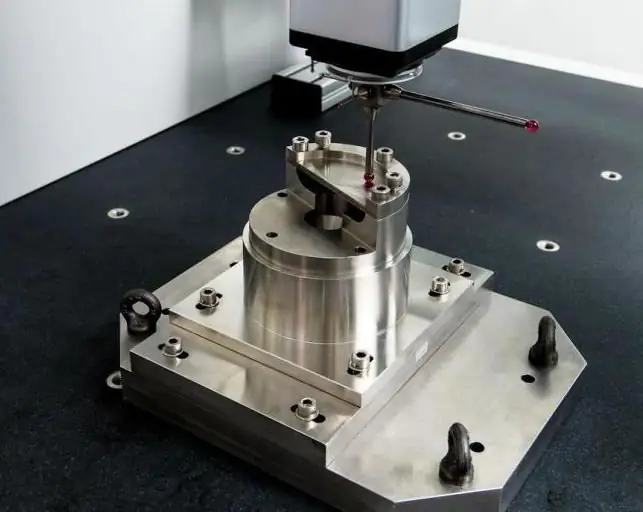
Automatic stop programmer contributes for operator confirmation of action. This is how the presence of an employee near the machine during operation is monitored. Additionally, a pause is introduced to control the reliability of the grippers during unloading or after loading the workpiece.
Scope of application
Multi-axis machines are in demand by almost anyonemanufacturer of metal products, furniture, plastics, unique products. The largest number of coordinate systems is in the automotive and aircraft industry, the space industry. Also, such machines can be seen at the sites for cutting sheet material.
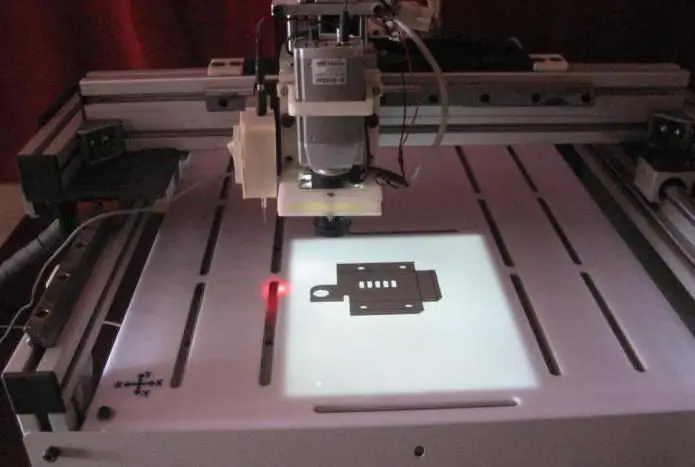
Vertical Multi-Axis Centers are mobile and easy to install on flat ground in a new location. Manufacturers are laying the possibility of upgrading equipment by adding axes, respectively, it is necessary to increase the memory, the number of inputs on the interface boards. From a 3-axis center, 5 or 6-axis systems can be easily obtained.
Varieties of cars
Multi-axis systems are used for more than just hole making and metalworking. Coordinate control can be implemented for the following purposes:
- A jig grinder is built on a similar principle.
- PCB printing system may have a similar structure.
- Automatic painting of cars and other parts.
- Filling forms with various materials is carried out according to the coordinate grid.
On the basis of a ready-made machine, there are many solutions for narrow tasks in production. Specialists of manufacturing companies are able to modify some models and provide them with robots, compresses to hold parts, or carry out a more complex project.
Recommended:
Large-caliber machine guns of Russia and the world. Comparison of heavy machine guns

Even in the First World War, a fundamentally new and terrible weapon appeared on the battlefield. Large-caliber machine guns. In those years, there was no armor that could protect against them, and the shelters that were traditionally used by the infantry (made of earth and wood) generally made their way through with heavy bullets
RPK-16 machine gun: specifications. Kalashnikov light machine gun
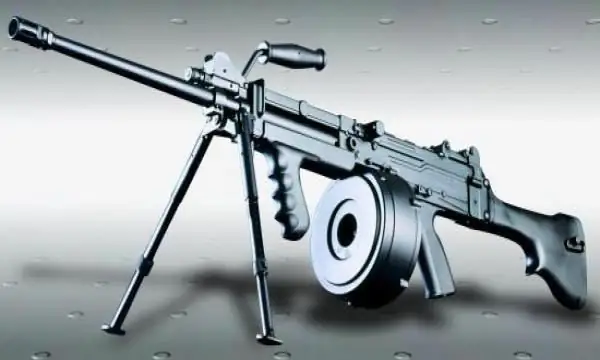
At the international presentation of weapons "Army-2016", held in September 2016, the RPK-16 machine gun, the brainchild of domestic gunsmiths, was demonstrated. It will be discussed in this article
KPVT, machine gun. Heavy machine gun Vladimirov KPV
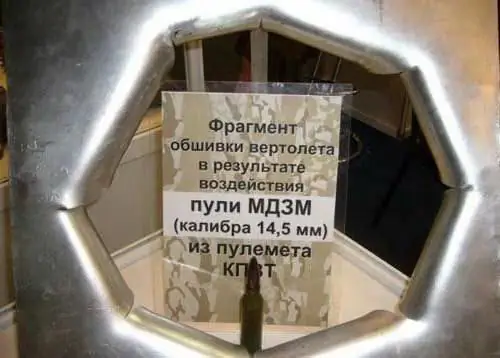
The idea of defeating aircraft and lightly armored vehicles led to the creation of heavy machine guns with a caliber of more than 12 mm. Such machine guns were already able to hit a lightly armored target, get a low-flying aircraft or helicopter, as well as shelters behind which there was infantry. According to the classification of small arms, the 14.5-mm KPVT machine gun is already adjacent to artillery weapons. And in design, heavy machine guns have much in common with automatic guns
Balancing machine: instructions for use. Balancing machine errors
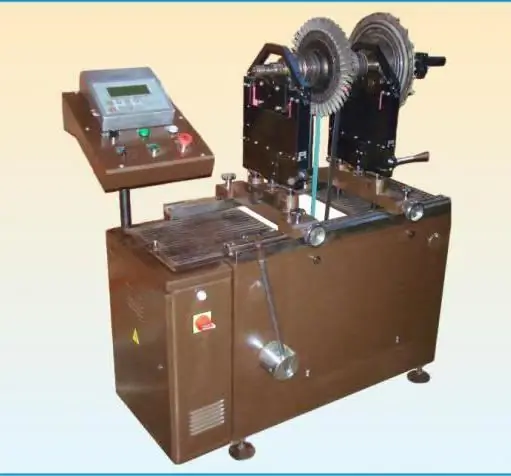
Balancing machine: characteristics, instructions, operation, features. Do-it-yourself balancing machine: recommendations, device. Balancing machine errors: description
Metal cutting machine. Plasma metal cutting machine
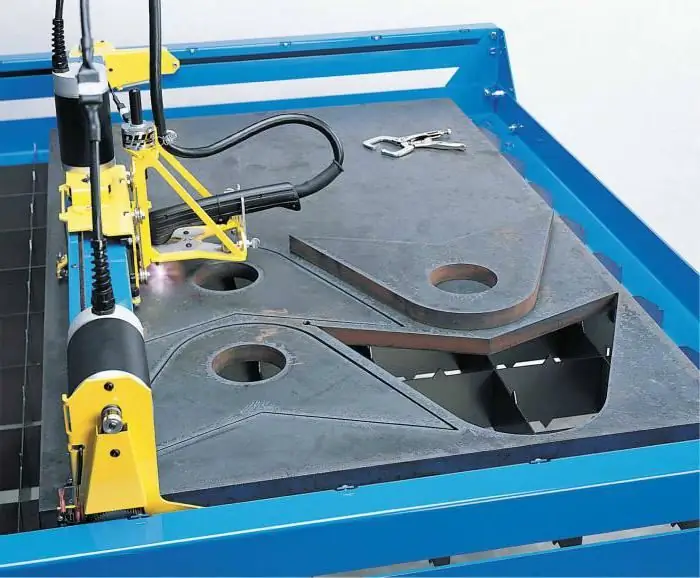
The article is devoted to the apparatus for cutting metal. The technology of plasma cutting, as well as the device and features of the equipment are considered