2025 Author: Howard Calhoun | [email protected]. Last modified: 2025-01-24 13:10
High-strength plastics are increasingly being used in the construction and manufacturing sectors. They are superior to traditional hard materials due to their low weight, malleability and practicality. Yet metal persists in many industries as the most advantageous material in terms of combination of strength, rigidity and durability. At the same time, the use of a solid structure does not always justify itself. Increasingly, technologists are using metal spraying, which allows you to endow the workpiece with some of the properties of the most suitable alloy in terms of operation.
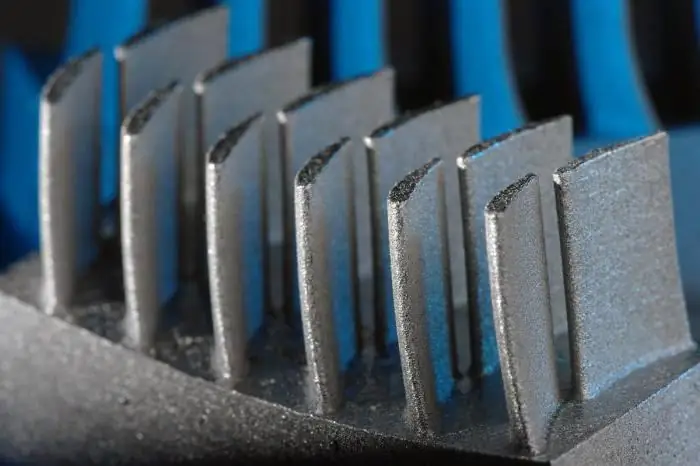
General information about metallization technologies
Among modern methods of surface metallization, galvanic deposition, as well as immersion in melts, is more often used. Traditional technology also includes vacuum sputtering, which has its own classifications depending on the active media used. One way or another, any deposition of metals involves processing the base of the material in order to obtain certain protective qualities. This can be the formation of an anti-corrosion layer, the restoration of a lost structure, or the repair of operational wear.
At the same time, the work surface itself ismost of the time it is heat treated. Before applying metal particles, it is melted by burners, inductors or by exposure to low-temperature plasma. Thus, a base with optimal physical and chemical qualities is prepared, on which metals are subsequently sprayed in the form of a powder. It is important to note that the same metal, glass, plastics or some types of wood and stones can act as the main material.
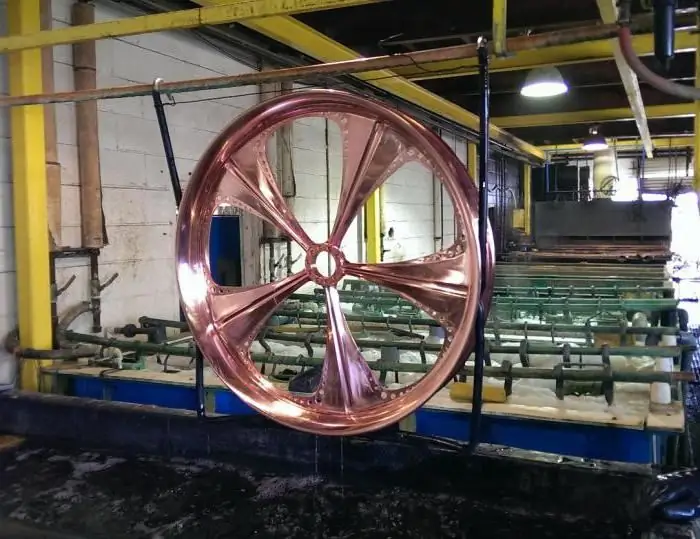
Chemical chromium plating method
Chemical reagents are used as an active component for the implementation of such a deposition. The classic composition includes chromium chloride, sodium, acetic acid, as well as water with a solution of caustic soda. The spraying process is carried out at a temperature of about 80 °C. Work begins with the preparation of the material. Typically, chromium plating is used to treat metal surfaces, in particular steel. Before the operation itself, the material is subjected to a primary coating with a copper layer. Next, chemical chromium plating is carried out by means of a sandblaster connected to a compressor unit. After the procedure is completed, the product is washed in clean water and dried.
Flame treatment method
If the previous technology provides for a thorough preparation of the base to be coated, in this case, special attention is paid to the metallization particles. Modern flame spraying can be carried out using polymer powder, wire orcord material. This mass is sent to the flame of an oxygen-propane or acetylene-oxygen burner, in which it is melted and transferred to the sprayed base by compressed air. Further, the composition cools down, forming a ready-to-use coating.
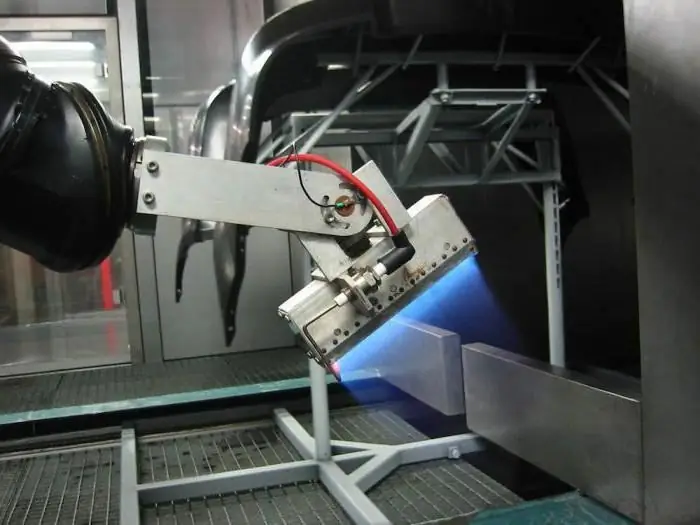
With the help of this technique, it is possible to endow materials with anti-corrosion resistance and mechanical strength. The active material can process aluminum, nickel, zinc, iron and copper alloys. In particular, flame spraying is used to improve the performance of plain bearings, insulating coatings, electrical parts, etc. In addition, the technology is used in interior and architectural design to provide structures with decorative properties.
Vacuum deposition method
In this case, we are talking about a group of methods that involve the formation of thin films in a vacuum under the influence of direct vapor condensation. The technology is implemented in different ways, including through thermal action, evaporation by electron and laser beams. Vacuum deposition is used to improve the technical qualities of parts, equipment and tools. For example, such processing allows the formation of special "working" coatings that can improve electrical conductivity, insulating properties, wear resistance and corrosion protection.
The technology is also used to create decorative coatings. In this case, the technique can be used in operations that require high precision. For example, vacuumsputtering is used in the manufacture of gold-plated watches, to give an aesthetic appearance to eyeglass frames, etc.
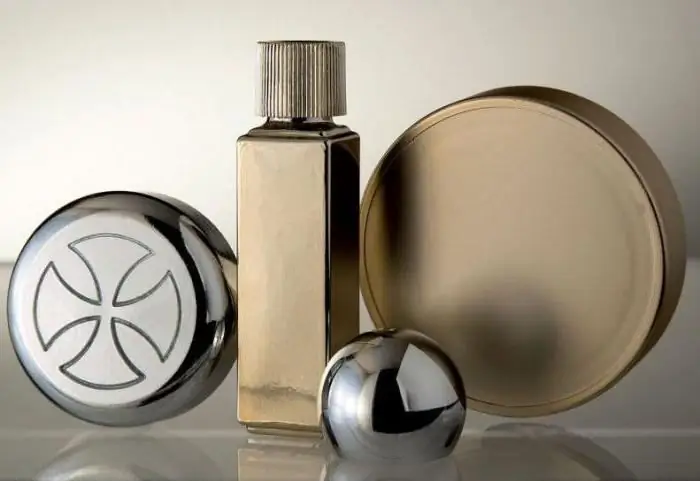
Applied equipment
Most often used for spraying apparatus equipped with a supersonic nozzle. A small electric heater powered by compressed air is also used. A feature of the latest model is the possibility of bringing the temperature up to 600 °C. Until recently, the use of standard devices, reminiscent of the principle of operation of pneumatic pistols, was complicated by the fact that the particles wore out the nozzles of the tool. Modern equipment, thanks to which metal spraying is carried out, uses the principle of a spray gun. This means that at the moment the working gaseous medium passes through the jet supply channel, the flow velocity increases as the pipe narrows. At the same time, the static pressure also decreases. This principle of operation reduces wear and increases the working life of the devices.
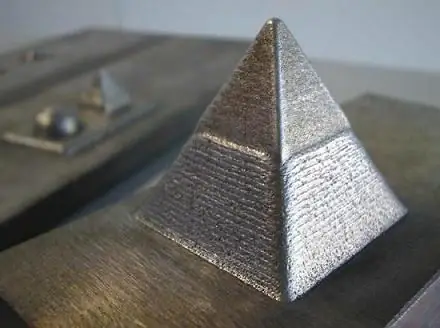
Conclusion
In order to reduce the cost of technological operations to protect the metal from external influences, highly specialized, but less effective means are often used. At the same time, metal spraying also helps to save money, the price of which is on average 8-10 thousand rubles. for the detail. Financial feasibility is due to the fact that such coatings can provide several functional qualities at once. For example, by processing a metal component of a roof structure, you can obtain suchproperties such as anti-corrosion, resistance to precipitation, mechanical protection. There are also special metallized coatings that can protect the part from aggressive chemical and thermal influences.
Recommended:
Ferrous metals: deposits, storage. Metallurgy of ferrous metals
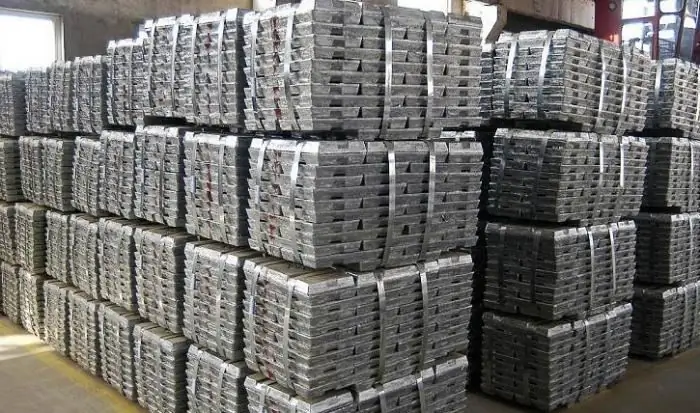
Metals are materials that never lose their relevance. They are widely used in household and industry
Slaughter of cattle at meat processing plants: rules, technology, methods and methods
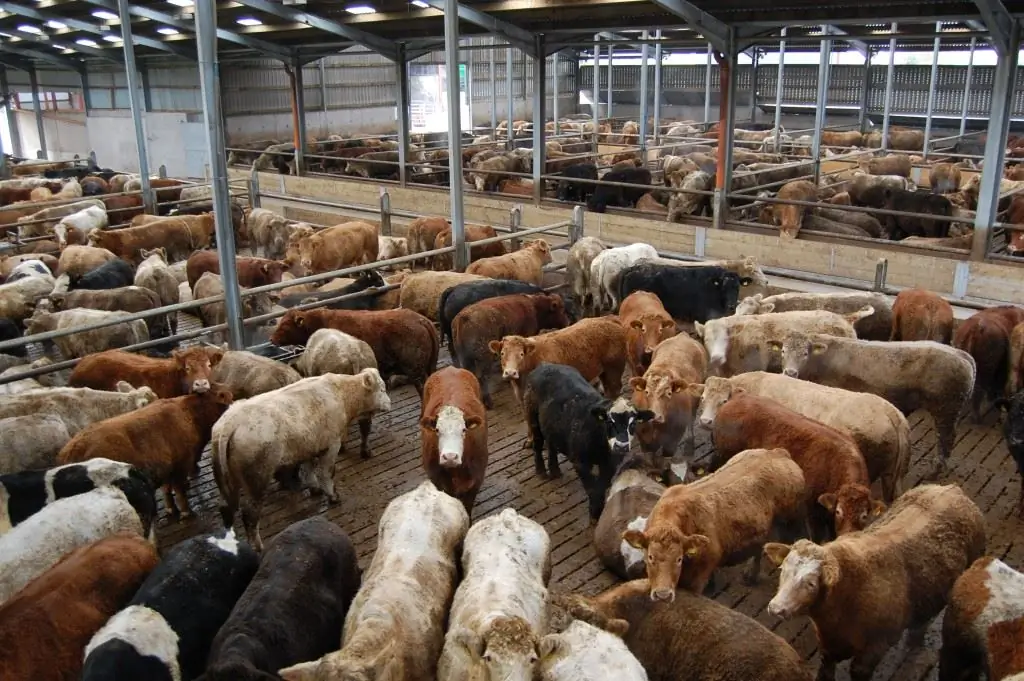
Providing the consumer basket with meat products directly depends on the slaughter and processing of cattle. Delicious beef and veal dishes are largely the merit of livestock breeders who know how to properly slaughter bulls and cows. There are various technologies, methods and methods for slaughtering cattle, which make it possible to obtain high quality meat products
Precious metals quotes at Sberbank. Precious metals (Sberbank): prices
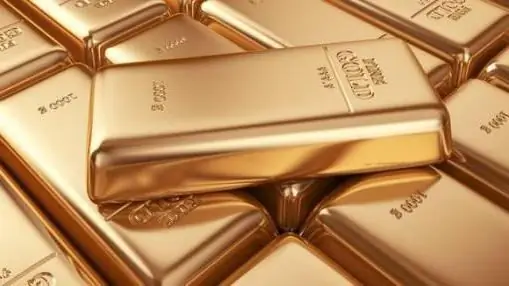
One of the most profitable investments is the purchase of precious metals such as gold, silver, platinum, palladium. This has been the case for many years and remains so today. In times of economic crisis, this option is even more relevant
Technology of electric arc welding of metals
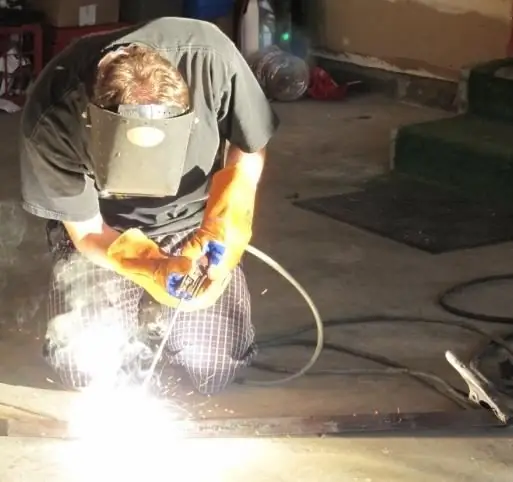
The impact of an electric arc on the structure of a material is one of the oldest ways to obtain a strong connection between metal workpieces. The first technological approaches to this welding method had a lot of disadvantages associated with the porosity of the weld and the formation of cracks in the working area. To date, manufacturers of equipment and auxiliary devices have significantly optimized the method of electric arc welding, expanding the scope of its use
Butt welding: equipment, methods and process technology
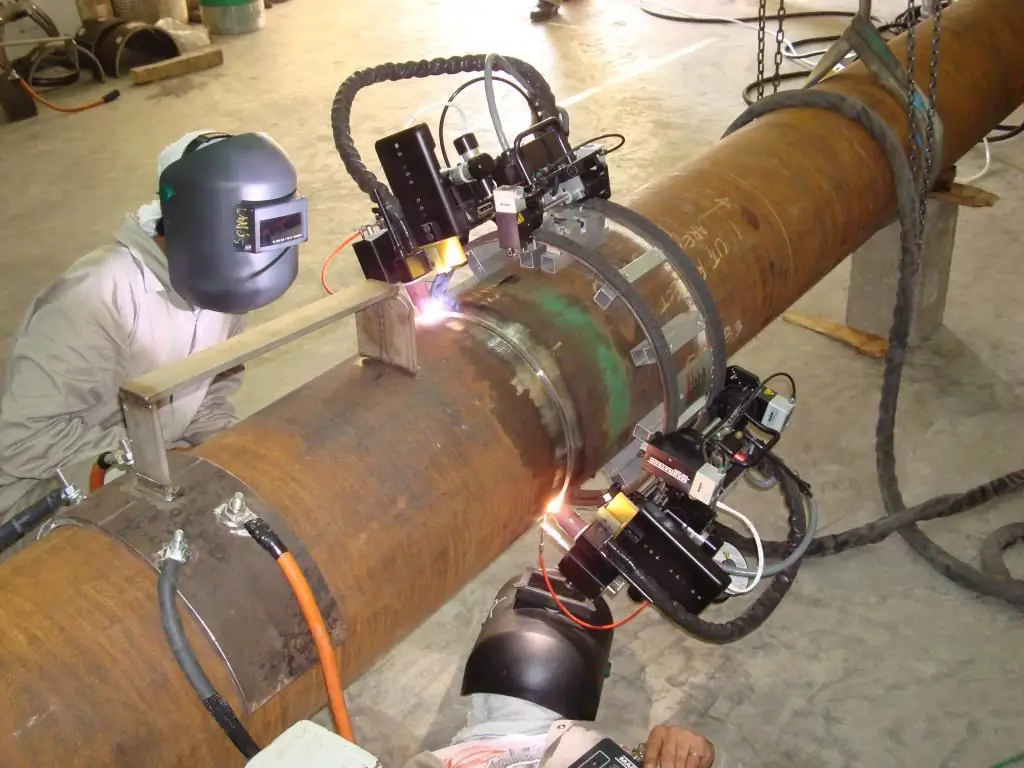
Features of flash butt welding. Types of butt welding joints, as well as equipment, methods and technology for carrying out the butt welding process. Welding seam defects arising from flash butt welding, as well as the reasons for their formation