2025 Author: Howard Calhoun | [email protected]. Last modified: 2025-01-24 13:10
The creation of any metal structure always implies a reliable and durable connection of individual components and parts into a single mechanical unit. Of course, the metal product can be produced as a monolithic, one-piece part, for example by casting. However, most often it is necessary to create an integral connection by the method of interatomic metal bonds, accompanied by high heating of the place where the parts are joined. Simply put, flash butt welding.
Equipment, methods and process technology are of interest to many beginner welders. This type of connection is widely used in the aerospace and automotive industries, as it allows you to create a strong and reliable welding seam.
Features of butt welding
Butt welding of various materials is one of the varieties of a strong connection under the influence of compressive force and electric current. That is, the parts connected during flash butt welding are simultaneously pressed against each other and heated by an electric arc.
If the space of the joinedparts to a plastic state (without melting), then this type of connection is called resistance welding. When the workpieces are heated to melting, the edges of the butt of welding joints are said to use the flashing method. Each of these methods is used in certain situations, which are evaluated by the welder, depending on the requirements for the quality and reliability of the connecting seam, as well as the equipment used.
The presence of defects in welds greatly impairs the quality of work performed. Therefore, in order to eliminate this trouble, it is necessary to pre-clean the contact surfaces from oxides, irregularities and dirt.
It should also be remembered that as the size of the joint surface increases, the strength and quality of the weld deteriorate significantly. This is due to the fact that a large area does not warm up well and contributes to the rapid formation of oxides, which negatively affect the quality of the welded joint.
Butt Joint Benefits
Any type of welding has its technological advantages and disadvantages. Butt welding, according to many welders, has a number of positive qualities that significantly distinguish it from other technologies.
The benefits of flash butt welding include:
- when using this method of reflow, there is no need to preheat the joint and prepare the edges of the joined parts;
- with the observance of welding technology, it is easy to obtain a strong and reliablea connection that can last several decades without accidents;
- maintains a high level of chemical homogeneity of the material after welding, which increases the strength of the joint;
- ease and simplicity of work do not require special knowledge even from a novice welder;
- the ability to perform the process of flash butt welding in a fully automatic mode;
- high speed of technological operations;
- versatility in the use of almost all materials.
All these advantages greatly outweigh the minor disadvantages of the butt welding process.
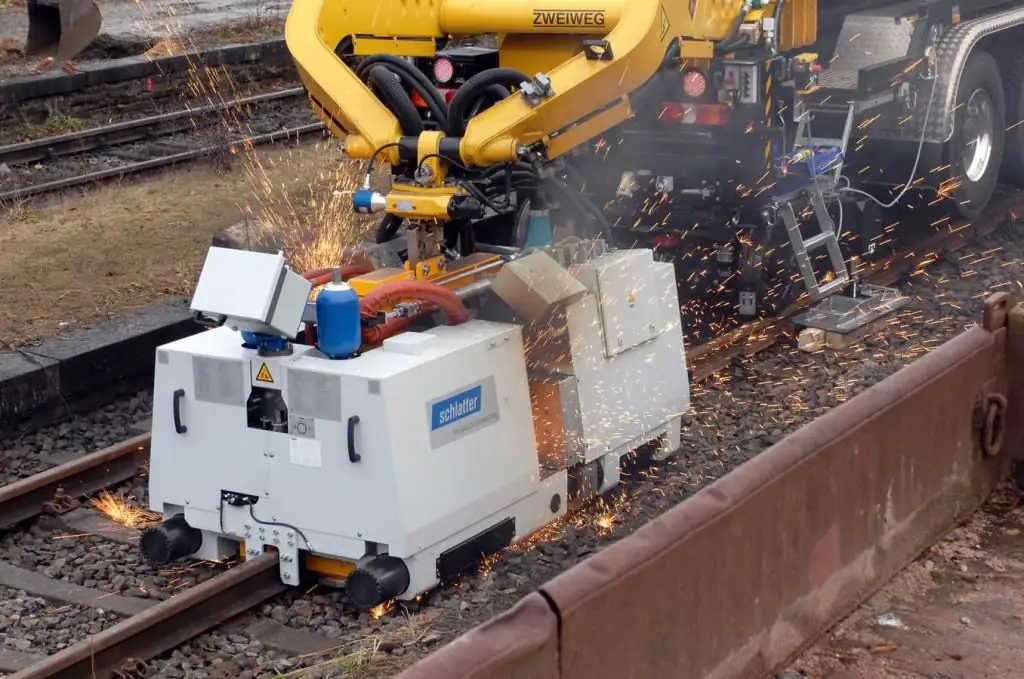
Disadvantages of welding
Some disadvantages of this type of welding include:
- high consumption of electrical energy;
- a rather high price of a resistance welding machine for home use, so it is best to do the butt joint manually by yourself;
- the need for strict adherence to the requirements for the size of the surface of the joined parts;
- difficulty in welding in high humidity conditions.
Types of butt welding
The welding process of the butt joint is based on the Joule-Lenz law. The process of interatomic bonds proceeds under the action of an electric current by means of strong compression applied to the contact surface of the product.
There are two types of butt welding:
- weldingresistance;
- flash welding.
In essence, both of these methods use the same technological electro-deformation process, but there are also special differences.
Resistance welding
The uniqueness of this method is that the process of joining parts proceeds without melting the base. In this case, the metal surface is subjected to severe plastic deformation. Structurally, the welding rods are connected to an electric current, and when they come into contact with the metal surface, a closed circuit is formed. At the point of contact, a high resistance appears, which provides a small heating. The rods, heated to a certain value, are tightly pressed against each other, and the current is turned off.
After the heated rods begin to harden, this is why this technology is called resistance welding. To avoid a defect in the weld, the surfaces of the products to be welded must be subjected to careful pre-treatment so that when the metal is bonded, there are no tiny particles of foreign origin.
Resistance welding is used to connect wire or pipes, and the materials can be different (steel and copper, cast iron and aluminum).
Reflow connection
A distinctive feature of flash butt welding is the supply of voltage to the transformer until the contact of the welded surfaces. In this case, the protruding microroughnesses of the surface are heated and crushed. Therefore, the electric current does not flow along a larger protrusion, but immediately alongthe entire plane of contact.
There are two types of flash butt welding:
- Continuous welding is characterized by the smooth movement of two parts of the product, clamped in special clamps of the welding unit, towards each other. Then a current is applied, and the parts are interlocked, contacting the entire plane. The parts are welded, after which a settling occurs at a certain value and the electric current is turned off.
- Intermittent melting occurs due to the alternation of the moments of sealing and weakening of the joints, while the electric current remains on. This back-and-forth movement closes the circuit up to the melting point of the material.
Surface requirements and cleaning technology
The surfaces of the materials to be joined in order to obtain a high-quality weld must meet certain requirements:
- The resistance value over the entire contact plane should be approximately equal.
- Resistance to electric current should be as low as possible.
- The planes of the two surfaces to be welded must match in level.
- Even appearance of the surface is the key to high-quality welding.
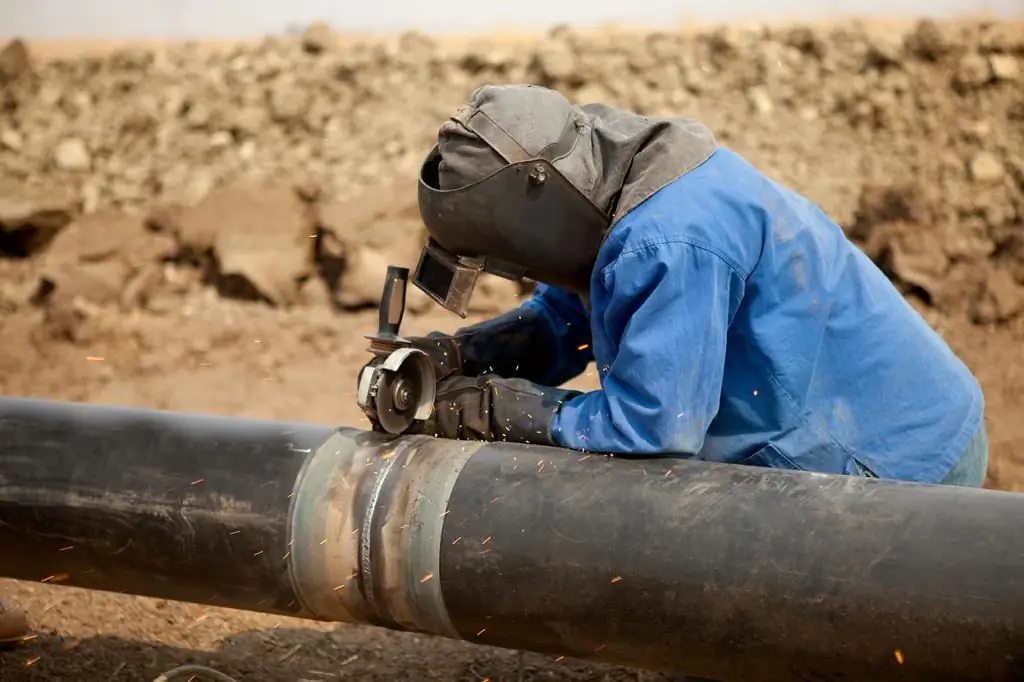
To meet these conditions, it is necessary to pre-prepare the surface. For this you need:
- Perform degreasing of the joint.
- Remove the oxide film over the entire contact plane.
- Perform joint neutralization.
- Dry the surface well.
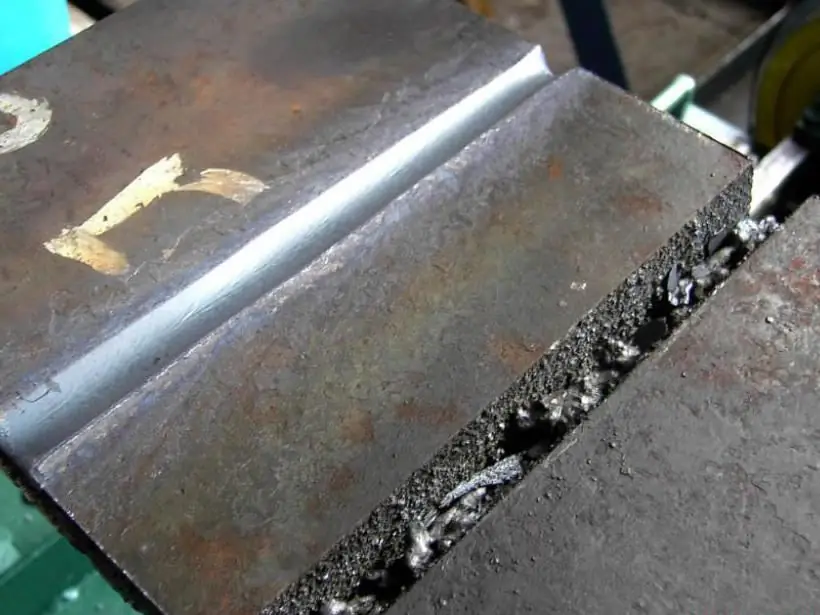
After cleaning, you need to visually check the readiness of the surfaces for welding.
Butt Welding Machines
With the help of special butt welding machines, polyethylene pipes are most often welded, since the material of these products is easily amenable to the butt type of the contact connection.
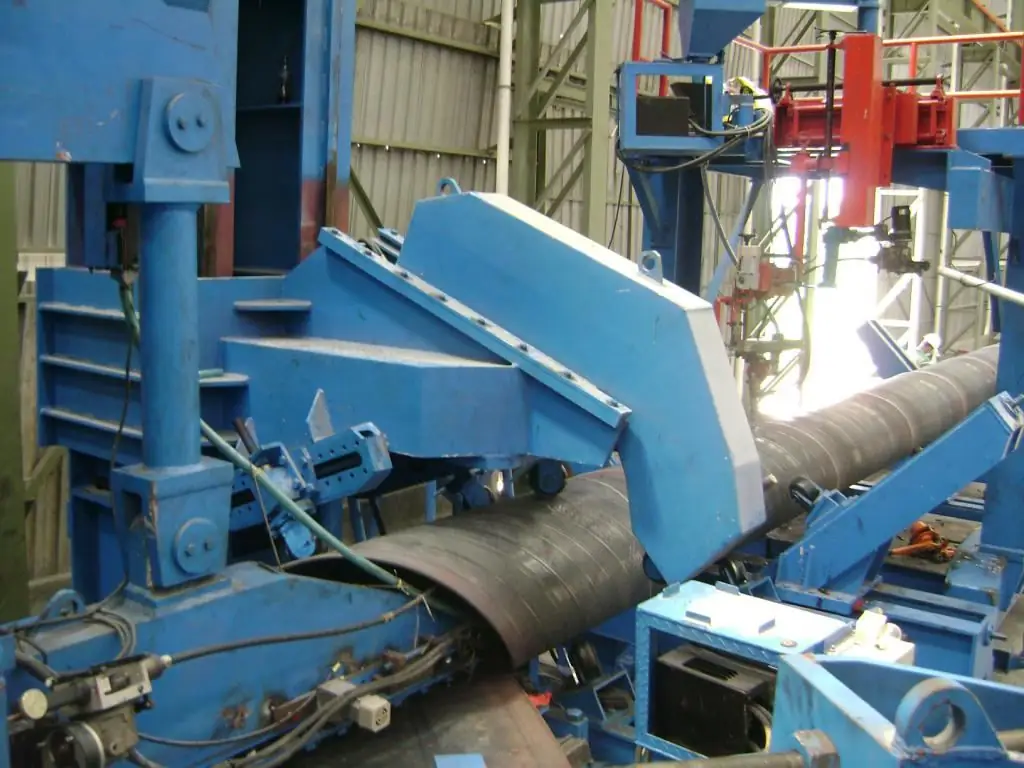
There are the following types of welding machines:
- mobile;
- stationary;
- pendant;
- universal;
- specialized.
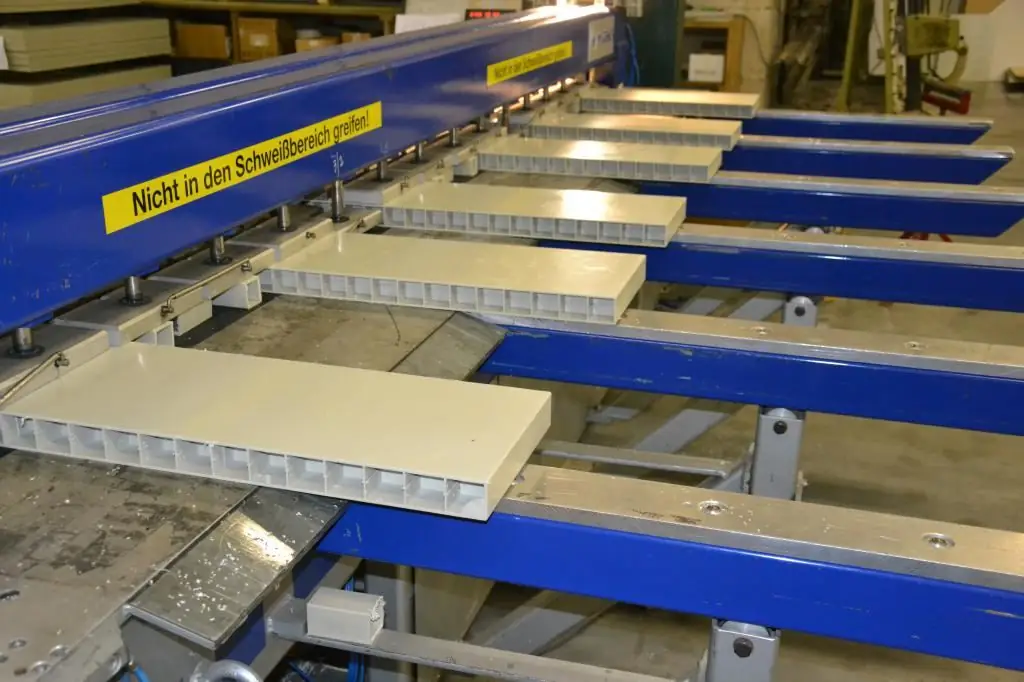
The design of any welding machine includes an electrical and mechanical assembly, as well as a water cooling system and a pneumatic workpiece feeder.
Butt welding of polyethylene pipes is slightly different from joining metal products. Since the plastic material is not a conductor of electric current, the heating of the ends of the pipes is carried out by special heating elements. Otherwise, the technology of butt welding of polyethylene pipes is similar to the connection of other surfaces.
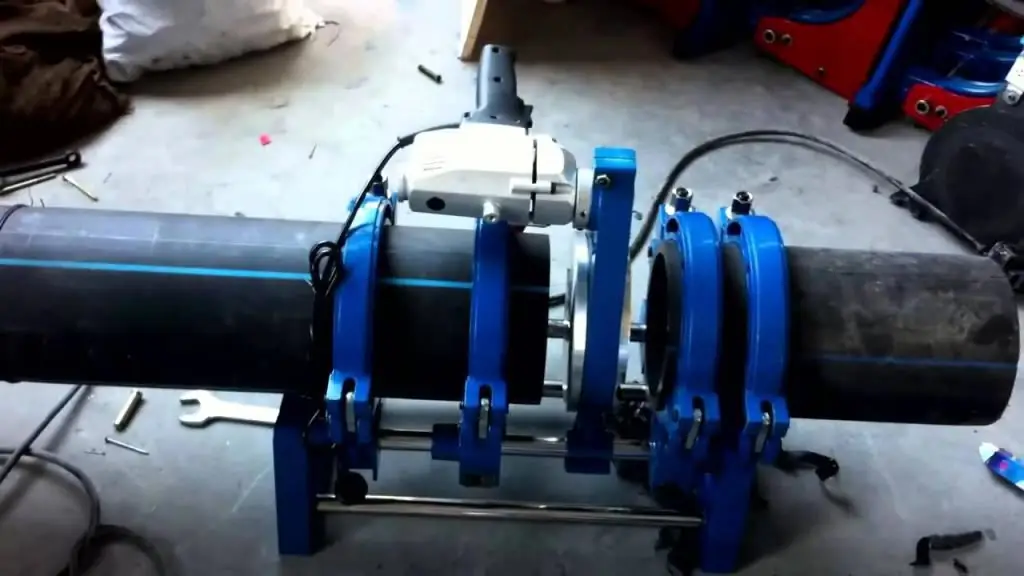
Manual butt welding
At home, the use of a contact welding machine is unprofitable, so pipes of small diameter can be welded manually. At the same time, in order to achieve a high-quality connection, it is necessary to gain experience in performing work through training.
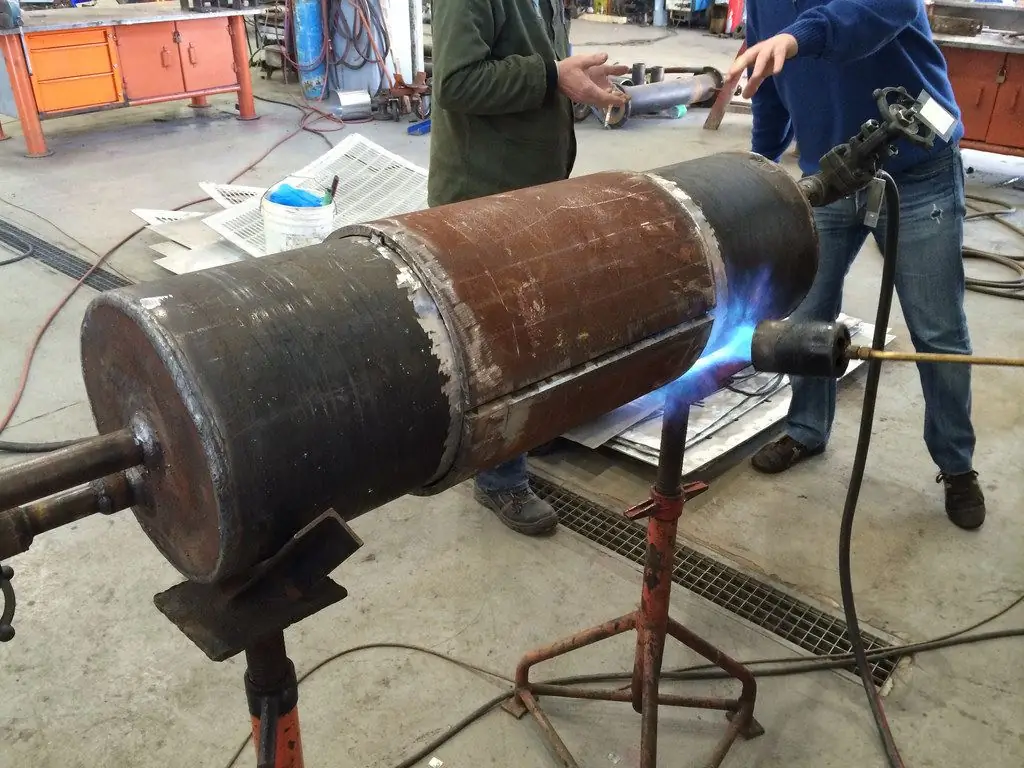
Technological steps of the manual butt welding process are as follows:
- Prepare the workspace according to safety requirements.
- Make a secure fixation of workpieces. Fastening can be done using special clamps, however, in domestic conditions, bricks or recesses in the ground are most often used. The main thing is that the parts remain motionless.
- Use sandpaper or a file to clean the surfaces to be welded.
- When heating a butt weld, pressure must be applied to the joint.
- The seam is cooled naturally - in air.
In case of strong wind outside, it is advisable to stop working to prevent dust or sand from entering the welding area. In rainy weather, work can be carried out under a special canopy.
Defects in butt joints
The long-term functioning of any mechanical device largely depends on the quality of visual control of the work performed. Therefore, every welder must know and be able to evaluate the main defects that can occur during the welding process.
The main defects of flash butt welding include:
- Lack of penetration of the weld, which manifests itself in a partial metallic bond. The most common cause of this defect is the presence ofthe junction of the oxide film, as well as weak heating of the ends of the parts.
- Cracks and delamination of the seam, which can occur when the material is rapidly cooled after welding.
- Fiber distortion in the weld area can also be caused by excessive upsetting.
- Pollution of the joint with various inclusions, large grains on the weld are structural defects. Such troubles arise when the seam is oxidized or overheated.
Butt resistance welding, according to experts, is a reliable and high-quality way of joining parts from different materials. Due to the ability to perform the process in automatic mode, it is widely used in industrial enterprises to connect complex components of many mechanical devices.
Recommended:
Argon welding: equipment and work technology
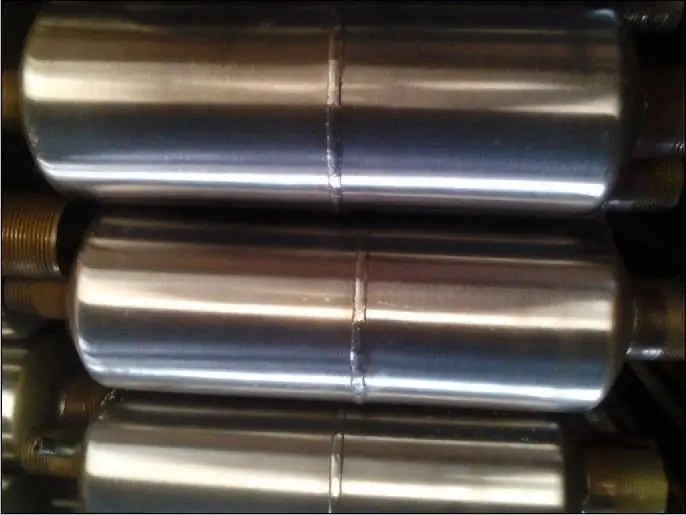
Argon welding method (TIG system) is mainly used to work with thin-walled workpieces with a thickness of no more than 6 mm. According to the execution configuration and types of metal available for maintenance, this technology can be called universal. The limitations of the scope of argon welding are determined only by its low efficiency in working with large volumes. The technique focuses on high accuracy of the operation, but with large resources
Thermite welding: technology. The practice of thermite welding in everyday life and in the electrical industry
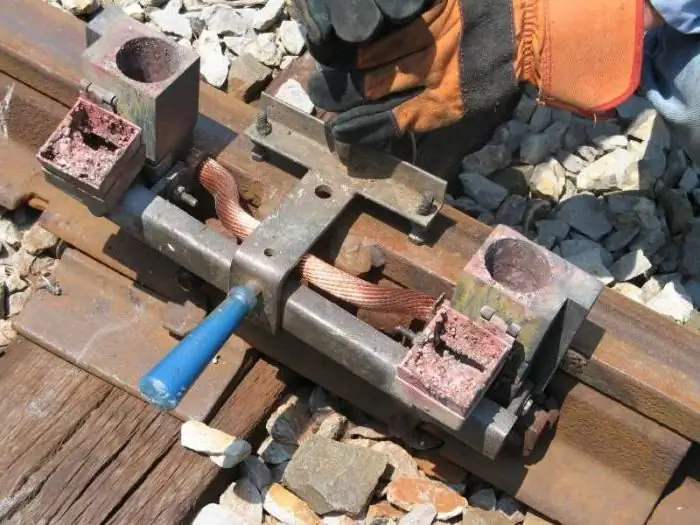
The article is devoted to thermite welding technology. The features of this method, the equipment used, the nuances of use, etc. are considered
Welding of copper and its alloys: methods, technologies and equipment
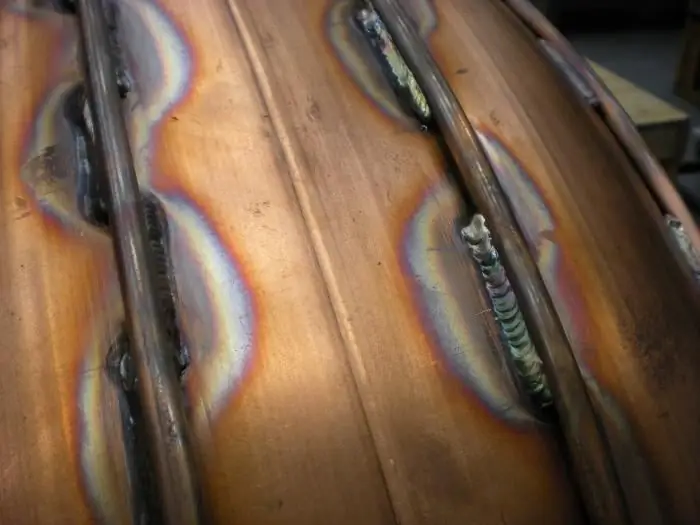
Copper and its alloys are used in various sectors of the economy. This metal is in demand due to its physicochemical properties, which also complicate the processing of its structure. In particular, the welding of copper requires the creation of special conditions, although the process is based on fairly common thermal treatment technologies
Welding in a shielding gas environment: work technology, process description, execution technique, necessary materials and tools, step-by-step work instructions and expert advice
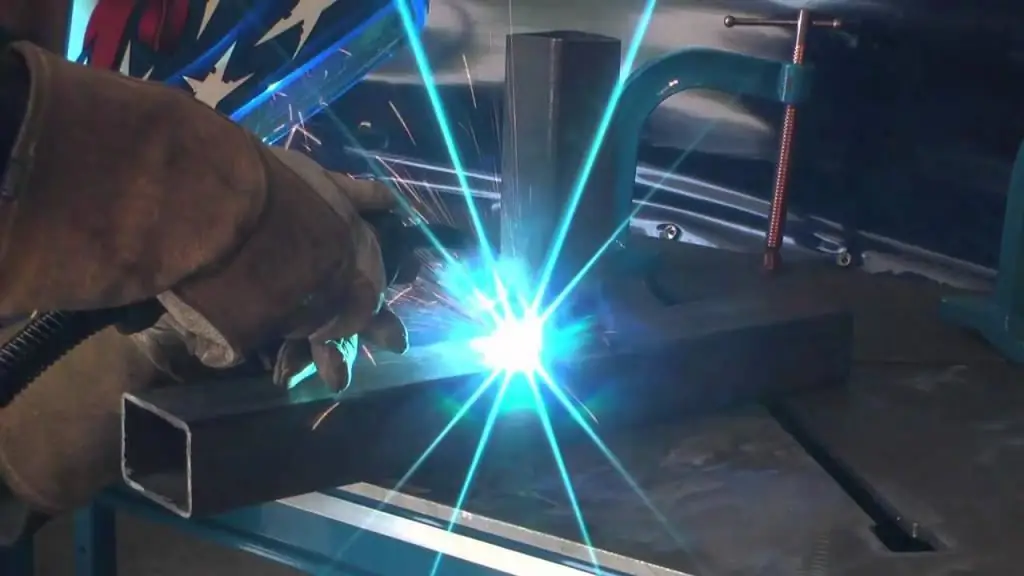
Welding technologies are used in various branches of human activity. Versatility has made welding in a protective gas environment an integral element of any production. This variety makes it easy to connect metals with a thickness of 1 mm to several centimeters in any position in space. Welding in a protective environment is gradually replacing traditional electrode welding
Restoration of parts by welding and surfacing: methods and methods of restoration, features, technological process
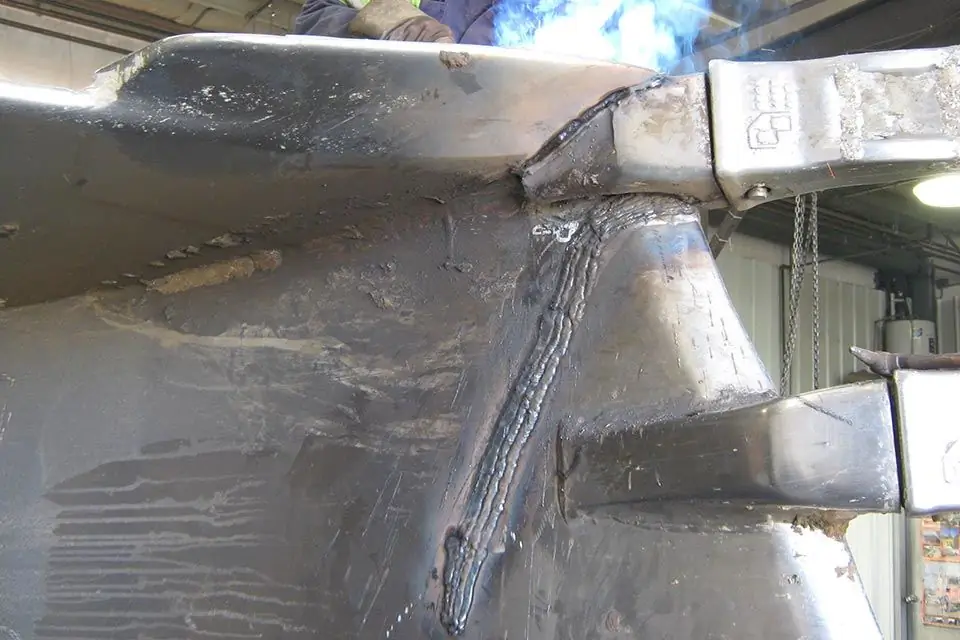
Welding and surfacing technologies allow efficient restoration of metal parts, providing a high degree of reliability and durability of the product. This is confirmed by the practice of using these methods when performing repair operations in a variety of areas - from car repairs to the production of rolled metal. In the total amount of work on the repair of metal structures, the restoration of parts by welding and surfacing takes about 60-70%