2025 Author: Howard Calhoun | [email protected]. Last modified: 2025-01-24 13:10
Omsk Oil Refinery is recognized as the best oil refinery in 2012 by WRA (World Association of Refiners). It is a subsidiary of Gazpromneft. The capacities of the enterprise allow producing 21.4 million tons of oil annually. The plant produces gasoline and diesel fuel, which comply with European standards 4 and 5. In 2013, the company's products were included in the hundred "Best Goods of Russia". The Omsk Refinery is carrying out a large-scale re-equipment and modernization, which mainly affects the systems for cleaning products from harmful and toxic impurities. At the same time, issues of increasing the degree of industrial safety, optimizing enterprise management, and treating industrial wastewater are being addressed. In 2013, the enterprise reached 95% of its capacity.
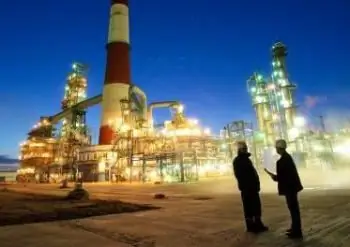
History of the enterprise
In order to provide the Kazakh SSR and the Urals with fuel and lubricants, in 1949 the leadership of the USSR decided to build a plant in Western Siberia. The Omsk site was rated as optimal. The raw material for processing wasbecome Bashkir oil. Design and construction lasted 6 years, and on September 5, 1955, the first furnace of the first refinery unit was launched. This day is still considered the birthday of the enterprise and is celebrated with corporate celebrations. For the first decade, the Omsk Oil Refinery processed only 3 million tons of Bashkir raw materials every year. But since 1964, Siberian oil has also been supplied to the enterprise. The Tyumen fields gave impetus to the development of refineries. At first it was delivered on tankers, but later the Ust-Balyk-Omsk pipeline was laid. This made the company a leader in the processing industry.
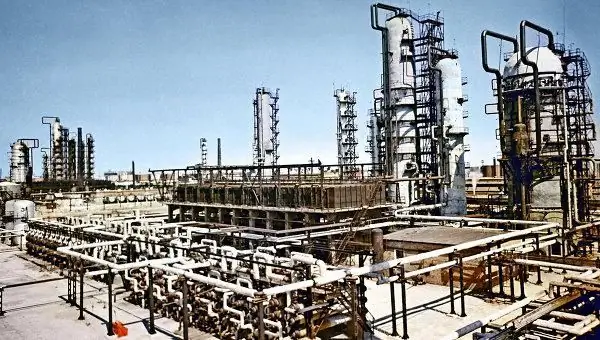
Development of refineries in Soviet times
At all stages of development, the enterprise mastered new capacities, introduced advanced technologies, and re-equipped. The development of the catalytic cracking system was a turning point, as it allowed the company to produce high-quality motor oils and significantly increase their production volumes. The Omsk Oil Refinery purchased, installed and put into operation an ELOU-AVT 6M unit, which could produce 6 million tons annually. Since that moment, the list of products has significantly expanded, and volumes have increased. Since 1983, the enterprise has been operating a complex producing aromatic hydrocarbons, which began to be purchased not only by domestic consumers, but also abroad.
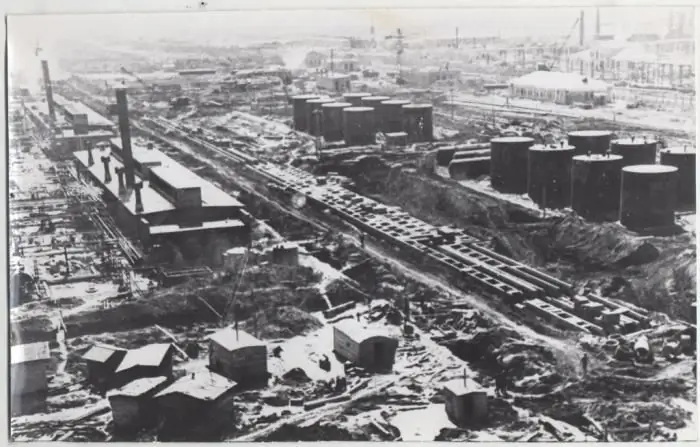
A new stage in the development of the Omsk Oil Refinery
In Perestroika, the enterprise, like all others, passed the stagereformation. OAO "Omsk Oil Refinery" was registered. There were difficult times in the 90s, but by the beginning of the 21st century, the enterprise began to work again in a normal mode. At the initiative of the Gazprom Neft corporation, the Omsk Oil Refinery became part of it. In 2001, a sulfuric acid alkylation unit was put into operation, and the plant switched to the production of unleaded gasoline exclusively. The Omsk Oil Refinery was also the first to produce Super-98 gasoline in the Russian Federation. The official website (onpz.gazprom-neft.ru) also reports that in the early 2000s, the reconstruction and modernization of the reforming unit was completed, which is capable of producing 1 million tons of products per year. In parallel, other equipment was being upgraded.
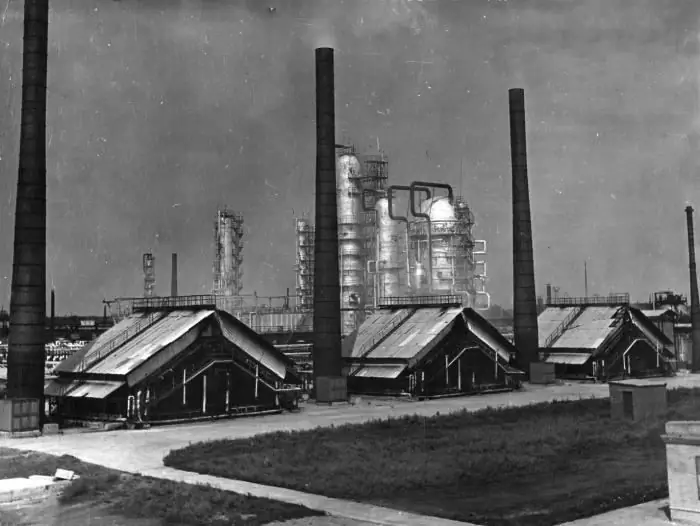
Leader in the processing industry forever
The Omsk Oil Refinery occupies the top positions in the list of Russian enterprises in terms of the output of light oil products and the depth of refinement of raw materials. The enterprise owns the largest set of technological processes for the production of diesel fuel, gasoline and aromatic hydrocarbons. In 2011, the billionth ton of crude oil was processed since the founding of the plant. The first enterprise in the Russian Federation to achieve such an indicator is the Omsk Oil Refinery. The refinery today produces about fifty items of products. These are gasoline for cars, fuel for rocket and diesel engines, fuel oil for furnaces, household gas, paraxylene, benzene, coke, toluene, bitumen, technical sulfur, benzene and other products.
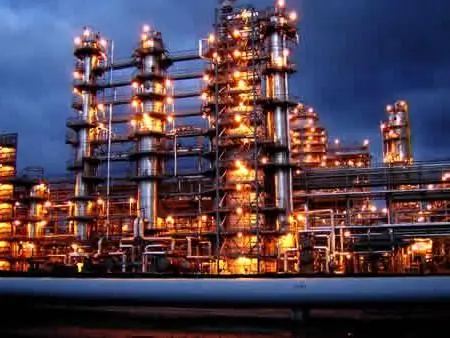
Fire at the plant
At the end of May 2010, disaster struck at the Omsk Oil Refinery. At half past six in the evening, a signal was received by the fire service panel - an explosion occurred in one of the sections of the technological furnace. A hole 10 meters in size was formed in the installation. A fire broke out at the enterprise, which was assigned the 3rd category. 25 fire brigades fought the fire, and after 2 hours it was completely extinguished. Two employees of the enterprise were injured, and the Omsk Oil Refinery suffered huge damage. Productivity dropped by 10%, but six months later the plant was running at full capacity again.
Activities to improve the environment
The Omsk Refinery is focused on the production of fuel of European environmental standards - this is not only an increase in product quality, but, ultimately, a reduction in emissions of harmful substances into the Earth's atmosphere. Among Russian enterprises, the leader in the production of environmentally friendly fuel is the Omsk Oil Refinery. The official website of the enterprise contains information that in 2016 the plant plans to begin construction of ultra-modern treatment facilities, which will allow to purify industrial effluents from waste by 99%, and industrial emissions into the atmosphere - by 90%. A 6-stage system of mechanical, physico-chemical, biological treatment using activated sludge will be equipped. Then coal and sand filters will come into play, and the final phase is ultraviolet disinfection. The building area will be 6 hectares. Thus, the entire complex will occupy a smaller area than the current one, but will be more efficient. The system will also cut the plant's water consumption in half.
Recommended:
Yaya Oil Refinery. Yaya oil refinery (Kemerovo region)
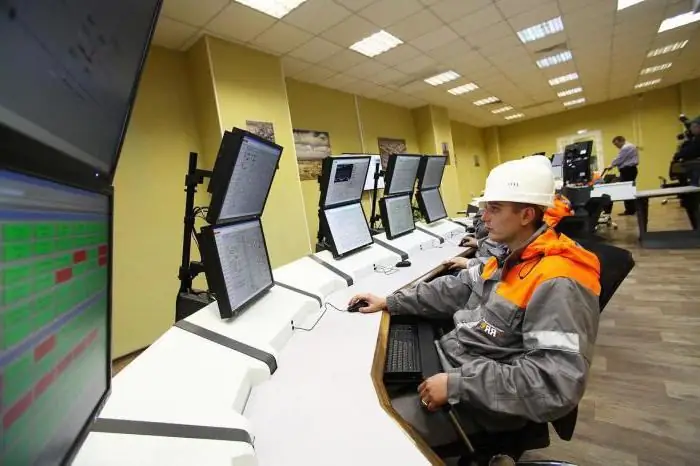
Yaya Oil Refinery "Severny Kuzbass" is the largest industrial enterprise built in the Kemerovo region in recent years. It is designed to reduce the acute shortage of fuel and lubricants in the Altai-Sayan region. The design processing capacity of the first stage is 3 million tons, the introduction of the second stage will double the output
Oil is a mineral. Oil deposits. Oil production
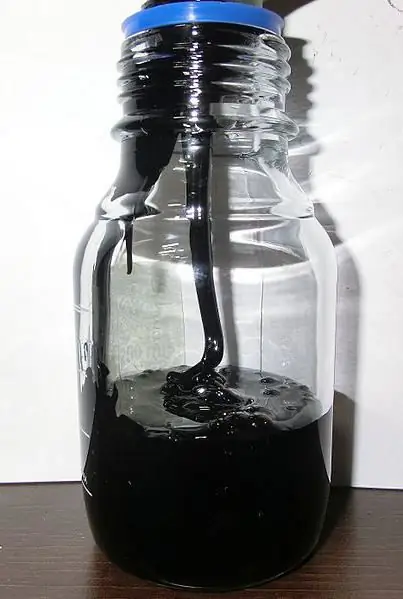
Oil is one of the world's most important minerals (hydrocarbon fuel). It is a raw material for the production of fuels, lubricants and other materials
JSC "Achinsk Oil Refinery of the Eastern Oil Company"
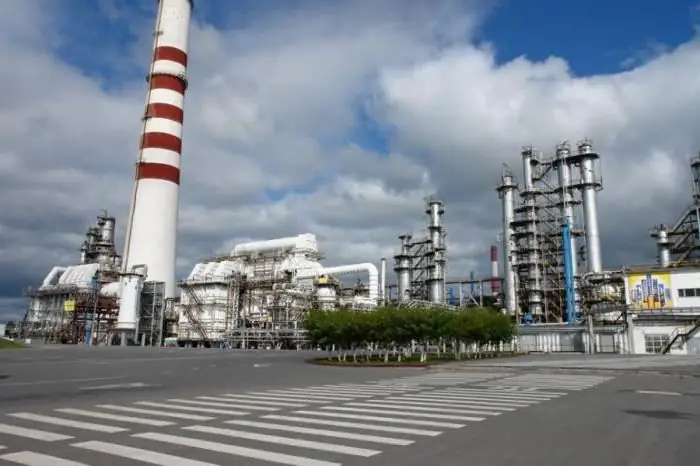
The Achinsk Oil Refinery of the Eastern Oil Company (AO ANPZ VNK) is the only large oil refinery in the Krasnoyarsk Territory. The plant's capacities allow processing about 7.5 million tons of crude oil annually
Syzran Refinery. Oil refining industry. Refinery
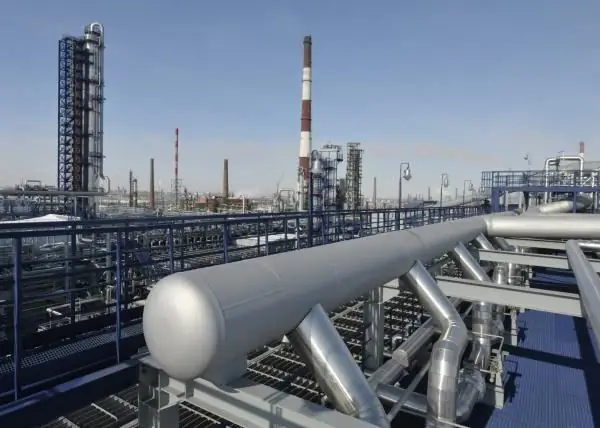
Oil is one of the most important assets of our country, since not only the financial position of our state, but also its energy security directly depends on the "black gold". One of the pillars of the domestic oil refining industry is the Syzran Refinery
How is oil produced? Where is oil produced? Oil price
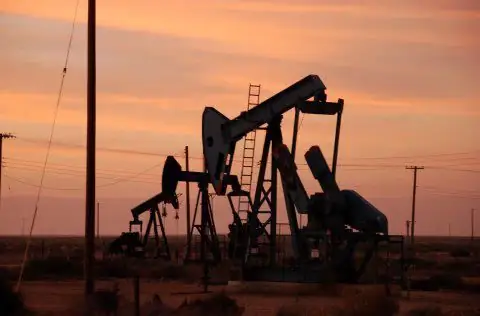
Currently, it is impossible to imagine the modern world without oil. It is the main source of fuel for various transport, raw materials for the production of various consumer goods, medicines and other things. How is oil produced?