2025 Author: Howard Calhoun | [email protected]. Last modified: 2025-01-24 13:10
When it is necessary to securely fasten various solid joints together, soldering is most often chosen for this. This process is widespread in many industries. Home craftsmen also have to solder.
This operation helps out not only when the TV or computer is out of order, and to restore it is necessary to replace the burnt microcircuit or chip. With the help of this process, refrigeration equipment, industrial systems are restored. Soldering helps if you need to get a tight connection. In addition, some materials simply cannot be combined in any other way.
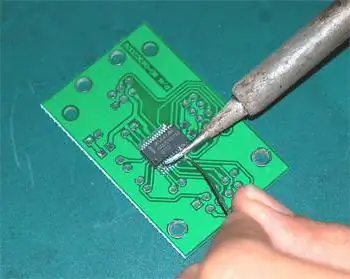
Aluminum, copper, brass cannot be joined by welding. In order to get a high-quality and reliable, as well as tight connection, you need to have not only good equipment and special skills, but also suitable consumables - solders and fluxes for soldering.
Solder alloys and flux types are selected depending on the materials with which you will have to work. For example, when working with aluminum productsa different flux is required than that suitable for copper or silver. Below we will look at the main characteristics of each of them and choose the best option for the job.
Solder Solder Key Features
Various metal alloys are used as it. There are also compositions based on pure metal. In order for a particular solder to be able to create high-quality connections, these materials must differ in some qualities.
Wettability
First of all, any kind of solder must have excellent wettability. Without this characteristic, the parts to be soldered simply will not be able to reliably contact each other. What is wettability? This is such an interesting phenomenon when the strength of bonds between particles of a solid and a liquid is higher than that of liquid molecules. If there is wettability, then the liquid will spread over the surface and get into all the cavities. So, if the solder for soldering does not wet, for example, copper, then it cannot be used with this metal. Pure lead is not used for soldering. Its wetting characteristics are very poor and cannot be counted on for a high quality joint.
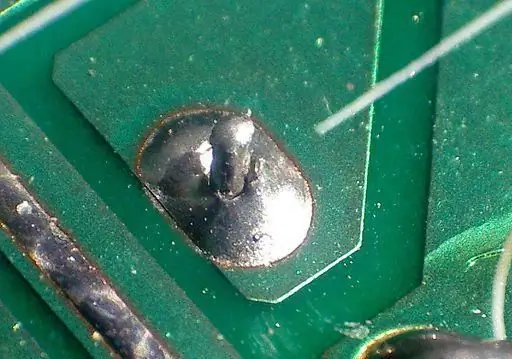
Melting point
Whatever the type of solder, the temperature at which it begins to melt must necessarily be lower than the melting of the soldered materials. It must also be higher than the operating temperatures of the parts.
When talking about the melting point, two points are meant. This is the value at which the fusible components will startthe melting process, and the minimum where the alloy will turn into a liquid. The difference between these two temperatures is called the crystallization range. If the soldering point is within this difference, then even small mechanical loads on the part can completely destroy the structure of the solder. In such a connection, high fragility and resistance will be noted. Remember the main thing: do not work on the joint in any way until the solder has completely crystallized.
Important properties of solders
Whatever the type and type of alloy, whatever material it is used with, it should not contain heavy metals or any other toxic substances above the established norm. The composition of the solder matches the material of the parts as closely as possible. Otherwise, you will not be able to get a reliable connection. Excessive fragility will be observed.
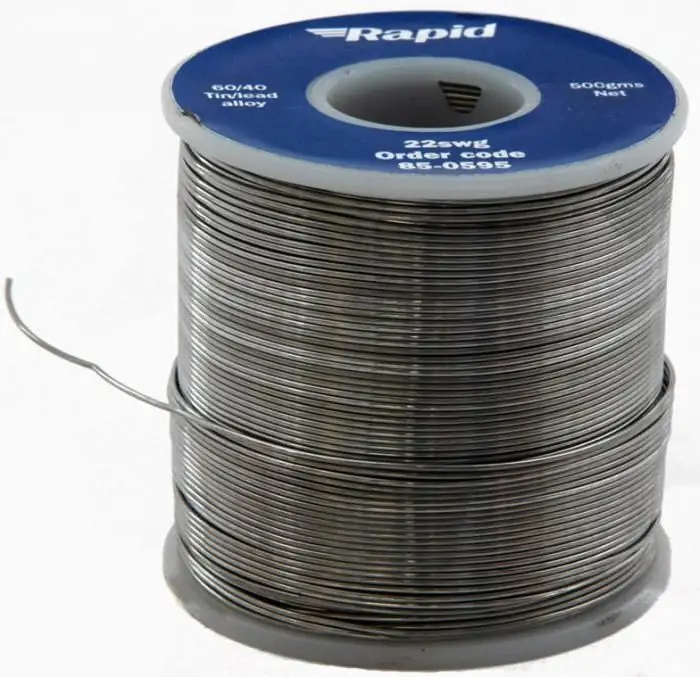
Any solder, regardless of type and purpose, must be thermally stable. Also solder for soldering must have electrical stability. The coefficients of thermal expansion and thermal conductivity should be taken into account. They should not differ significantly from the values that apply to soldered products.
Types of solders for soldering
All existing alloys for this operation are divided into soft, or fusible, where the melting point is up to 450 degrees Celsius, and hard. Here it significantly exceeds the above value.
Soft solders
Tin-lead alloys with different contents of components. In order to give the material the necessary characteristics, various additional ingredients can be added to the composition of the solder for soldering. For example, bismuth and cadmium are used to lower the melting point. The addition of antimony increases the strength of the brazed joint.
Alloys of lead and tin have a low melting point and low strength. They should not be used for parts whose operation implies a serious load. Also, these solders are not recommended if the operating temperatures of the parts will be above 100 ° C. If you have to solder loaded parts with soft solders, you should try to increase the contact area between the two products.
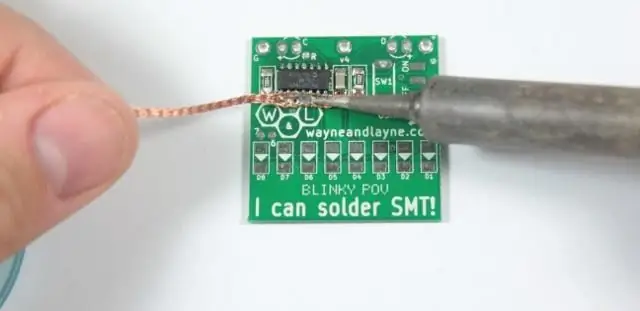
Among the most popular soft materials are POS-18, POS-30, POS-40, POS-61, POS-90. The numbers are here for a reason. This is the percentage of tin in the alloy. In industry, it is more often used in the production of electronics, instrumentation. In everyday life, they can connect a variety of parts: circuits of TVs, microwaves, electric kettles and other small appliances.
Assignment of soft solders
POS-90 is designed to work with parts, which will then be processed using galvanic technology. POS-61 can be used to repair high-precision equipment. Also, the alloy is ideal for joining parts of high responsibility from a variety of materials. POS-61 proved to be excellent as a solder for soldering copper and brass. Solder will come in when neededachieve strong connections with a high degree of electrical conductivity.
POS-40 are widely used for operations with irresponsible and inaccurate parts. In this case, the working area can be heated to high temperatures. POS-30 is suitable for soldering copper or brass, steel alloys and iron.
Solid
Among refractory alloys, only two groups are distinguished and widely used. These are mainly copper or silver alloys.
The first group includes solders made of copper and zinc. They are well suited for those connections that will only be affected by static loads. The brittleness of these alloys does not allow them to be used in assemblies that will experience shock or any vibration.
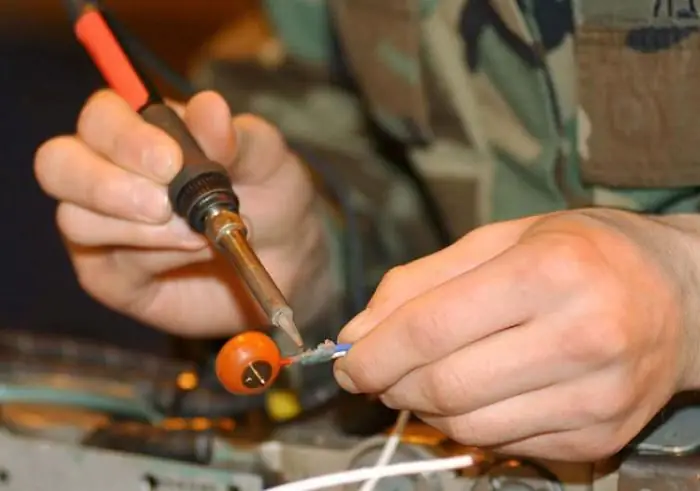
Copper solders or zinc-based solders include PMC-36 and PMC-54. The first is the ideal solder for soldering brass and any other copper connections. The second is suitable for working on copper parts, bronze or steel.
If you need to connect two steel parts together, then you can use pure copper, brass grades L-62, L-62, L-68. These brass-based solders allow you to create stronger and more ductile joints. Copper alloys do not have these characteristics.
Silver alloys are considered the highest quality. The composition may also contain zinc and copper. PSr-70 - solder for soldering copper, for working with brass or silver parts. This element is suitable if the junction must conduct electricity. PSr-65 is used in the production of jewelry,fittings, water pipes. PSR-45 is necessary for connecting those parts that operate under vibration and shock loads.
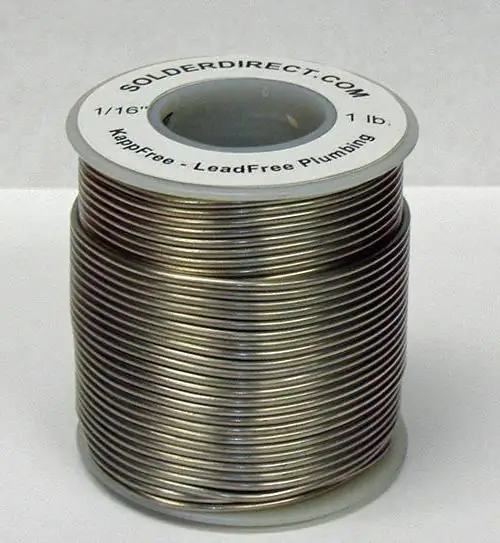
Other species
There are other, less popular solders. Often they are used for rare metals or for work in special conditions. For example, nickel-based compounds are designed for products that operate at elevated temperatures. They also solder stainless steel alloys. Gold-based solders are used to work with vacuum tubes. Suitable solders are also available for magnesium.
Issue form
Soldering materials and compounds come in a variety of forms. So, it can be wire, thin foil, tablets, powder. In addition, solder is available in the form of a paste or granules. The shape determines how the solder will be delivered to the work area.
Features of aluminum soldering
The connection of aluminum parts by soldering is used in industry and in everyday life. For example, the frames of modern bicycles are made of aluminum alloys - in the process of extreme riding, they often break. The question arises: what kind of solder to choose?
It is believed that soldering aluminum is a very complex process. But in fact, this is true if materials for stainless steel or brass, steel, copper are used in the process. The reason for this is the oxide film. It is she who does not provide the required level of wettability, and the base metal does not dissolve.
How to solder aluminum and alloys based on it
In order for the work to be carried out at the proper level,solder for soldering aluminum should contain silicon, aluminum, as well as copper, zinc and silver. Today on sale you can find compositions where all these components are in different ratios.
When choosing reliable solder, it is important to consider the following. The joint that was made with solder, which contains a lot of zinc, will have maximum resistance to corrosion and high strength.
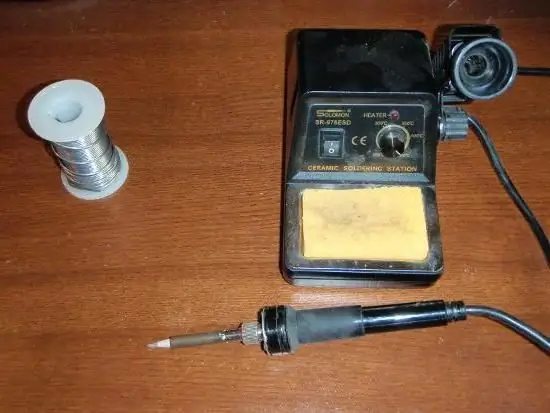
Also for aluminum, you can use compounds based on tin and lead. But it is important to prepare the work surface with high quality, clean it with a stainless steel brush and use active fluxes. But experts do not recommend using such an element.
Any solder for soldering aluminum high temperature. The most optimal, which allow you to get a reliable connection, are aluminum-silicon and aluminum-copper-silicon.
How to solder copper?
As already noted above, it can work with most formulations. Both low-temperature fusible and hard solders can be used. They also use compounds based on tin with lead, tin, silver, copper with silver and zinc.
If you need to repair a computer motherboard or repair a TV in the country, any fusible elements will do. If you need to solder fittings on pipes or repair a plumbing or refrigerator, then only hard solder for soldering copper will do. This is how you can get a quality result.
Stainless steel
If you need to connect stainless steel parts, thenprofessionals recommend using tin and lead rods. Materials with cadmium are also well suited. You can use low-melting alloys based on zinc. However, they should not be used together with carbon or low alloy steels. The best solder for soldering stainless steel is pure tin. Also, only tin is allowed if the soldering point will come into contact with food.
If the work will be carried out in a dry or furnace atmosphere, then silver with manganese, chromium-nickel solders or pure copper (and even better brass) should be used. When soldering in corrosive conditions, use silver tinoli with a small amount of nickel.
Steel brazing
Connecting two such parts is not difficult. Affordable and effective solder for soldering steel - POS-41. There is also POS-60 and others, you can even use pure tin. But zinc compositions are not suitable. Especially when it comes to carbon or low alloy materials.
Fluxes for soldering
In the process of operation, the flux plays no less a role than the solder. It is a chemical solvent and oxide scavenger. It also protects metals from oxidation and increases wetting.
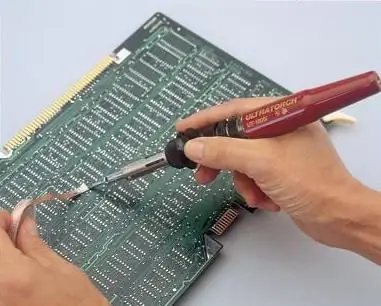
To work with elements based on lead and tin, hydrochloric acid, zinc chloride can be used as a flux. Also suitable is borax, ammonium chloride. These are active fluxes. Inactive substances include rosin, petroleum jelly, olive oil and many other substances.
For example, solutionshydrochloric acid can be used with soft solders. Zinc chloride is used with brass, copper, steel. Ammonia sleeps perfectly dilutes and dissolves fatty substances. For aluminum, a composition of tung oil, rosin, calcined zinc chloride is used. You can also use concentrated phosphoric acid.
So, we found out what solders exist, and which one is better to use in different cases.
Recommended:
Food stainless steel: GOST. How to identify food grade stainless steel? What is the difference between food stainless steel and technical stainless steel?

The article talks about grades of food grade stainless steel. Read how to distinguish food stainless steel from technical
Corrosion resistant steel. Steel grades: GOST. Stainless steel - price
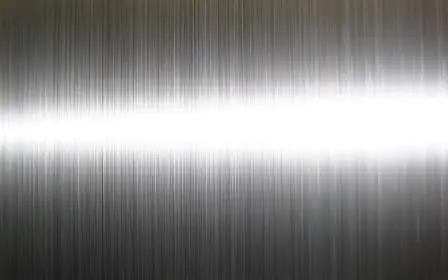
Why metal materials break down. What are corrosion-resistant steels and alloys. Chemical composition and classification according to the type of stainless steel microstructure. Factors affecting pricing. Steel grade designation system (GOST requirements). Application area
Steel: composition, properties, types and applications. Composition of stainless steel
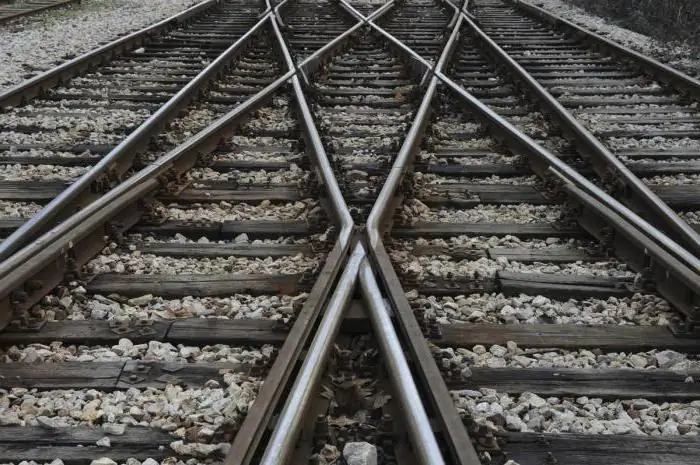
Today, steel is used in the vast majority of industries. However, not everyone knows that the composition of steel, its properties, types and applications are very different from the production process of this product
Duralumin is a high-strength aluminum-based alloy with additions of copper, magnesium and manganese: properties, production and application
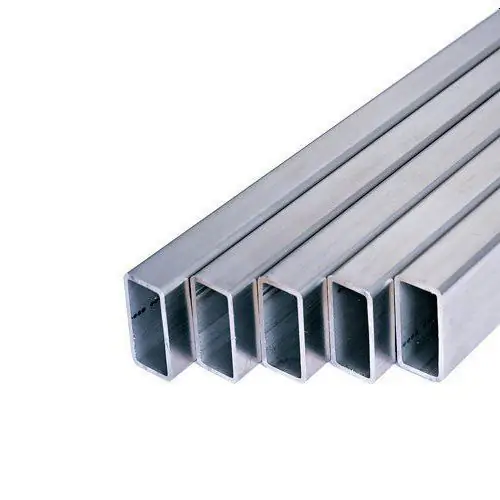
What is duralumin? What are the features of duralumin alloy? Technical and quality indicators of the alloy. A variety of products from this metal and their scope
440 steel - stainless steel. Steel 440: characteristics
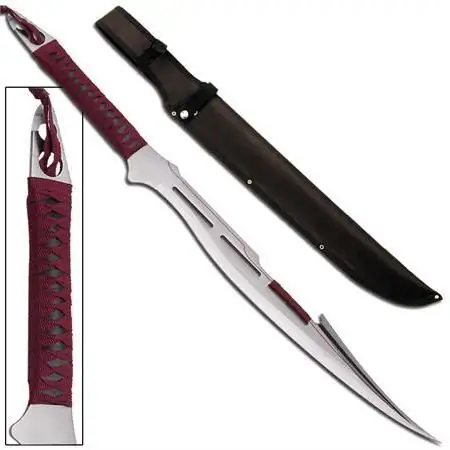
Many people know 440 steel. It has established itself as a reliable, anti-corrosion, time-tested hard material, which is most often used for the manufacture of knives for various purposes. What is the secret of this alloy? What are its chemical, physical characteristics and applications?