2025 Author: Howard Calhoun | [email protected]. Last modified: 2025-01-24 13:10
Natural rubber has many analogues, and isoprene rubber is considered one of the most large-tonnage. The industry produces a wide variety of types of these products, differing both in properties and in the type of catalysts that were used - lithium, complex, and the like.

How rubber is made
Isoprene rubber is synthetic, it is stereoregular, and it is obtained by polymerization of isoprene placed in an inert solvent medium with a complex catalyst. This is done, for example, SKI-3. The polymerization of isoprene in solution must be continuous, for this there are batteries of four to six polymerizers that are cooled with brine.
The monomer in the mixture is concentrated to twelve - fifteen percent, then the degree of conversion will reach ninety-five percent, and the duration will be two to three hours at temperatures from zero to ten degrees Celsius. If it is necessary to obtain high molecular weight isoprene rubber, the purity of the reagents used in the polymerization is veryhigh degree.
Stabilizing and drying
To protect the polymer from oxidation, it must be stabilized with a mixture of phenylenediamine and neozone, which must be introduced into the polymerizate as a solution or aqueous suspension. In order to separate the isoprene rubber from the polymerizate as a crumb, the polymerizate must be mixed with steam and water, then add additives that prevent agglomeration (lumping). The solvent must then be distilled off. Now it is necessary to carry out the processes of degassing, separating the crumbs from water and drying in worm machines and belt dryers. At the end of this process, the production of isoprene rubber can be considered complete.
Now it will be briquetting on automatic plants under pressure. Brand SKI-3 - synthetic isoprene rubber, which is produced in briquettes of thirty kilograms each. The briquette is wrapped in polyethylene film and placed in a four-layer paper bag. This film is quite well processed simultaneously with the content, which is isoprene rubber, its properties with a mixing temperature quite allow polyethylene to soften and mix it with the main mass in a rubber mixer.
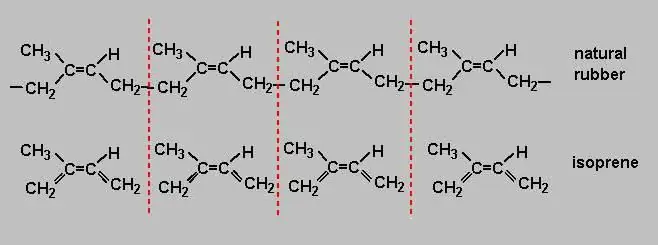
Structure
Each rubber that is produced by the industry has its own characteristics and properties inherent only to this variety. Some rubbers have good mechanical strength, others have good chemical resistance or gas impermeability, others have no fear of temperature changes, and so on. Propertiesindividual synthetic rubbers are superior to natural rubber in many ways and many times over. Only the elasticity of natural rubber has not yet been surpassed, and this is the most important property for products such as aircraft or car tires.
During operation, they always experience huge deformation - both stretching and compression, which causes intermolecular friction, heating and loss of quality. That is, the higher the elasticity of rubber, the more durable the product. It is for this reason that natural rubber has not yet gone out of use, and it is it that is used for the production of tires for high-speed and heavy-duty aircraft and cars. Natural rubber is a polymer of isoprene, which is why scientists are working so hard to make isoprene rubber an analogue of natural rubber.
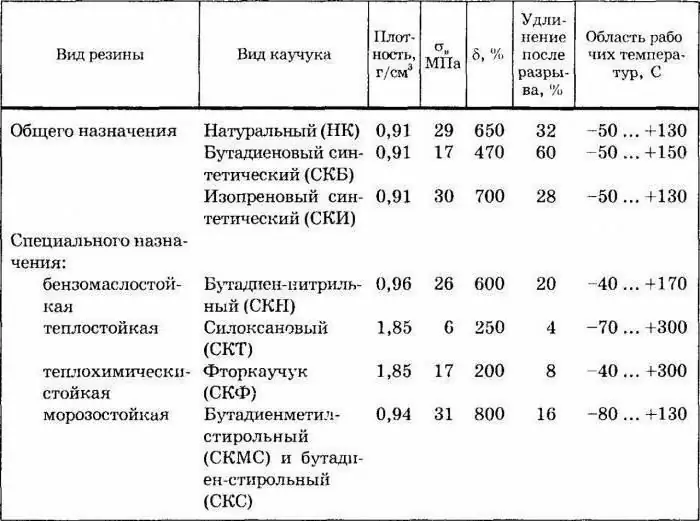
Formula
Resources for extracting natural rubber are very limited. Normal, naturally obtained rubber has the formula C5H8, as it turned out, it is absolutely identical to the molecular formula of isoprene, which is formed when rubber is heated, in its decomposition products. The challenge is to find a reasonably affordable way. And isoprene rubber is obtained during the polymerization reaction, and here it is important to correctly build the course of this reaction. Polymerization occurs as follows: nCH2 =C(CH3) - CH=CH2 -- (-CH2 - C(CH3)=CH - CH2)n.
The most promising method so far is the method of catalytic dehydrogenation of isopentane, which is released from petroleum gases. The starting material for isoprene production can also be pentane: CH3-CH2-CH2-CH 2-CH3, because when heated and with catalysts, it also turns into isopentane. There is also a polymerization method in which the reaction for obtaining isoprene rubber is built in such a way that rubber is obtained that is very similar in structure to natural rubber and, therefore, has the same excellent properties.
Isoprene
Isoprene is an unsaturated hydrocarbon belonging to the diene series. It is a volatile colorless liquid. The smell is very characteristic. Isoprene rubber is a natural monomer, since the remainder of its molecule is included in many other natural compounds - isoprenoids, terpenoids, and the like. Soluble in organic solvents. With ethyl alcohol, for example, it can be mixed in any ratio. But it does not dissolve well in water.
But it easily forms a structural unit of isoprene rubber during polymerization, due to which isoprene gutta-percha and rubbers are obtained. Also, isoprene can enter into various reactions during copolymerization. In industry, it is indispensable, since it is used to synthesize rubbers, medicines, and even some fragrant substances. In our country, the production of synthetic isoprene rubber has been developing for a long time, and accounts for approximately twenty-four percent of world production.
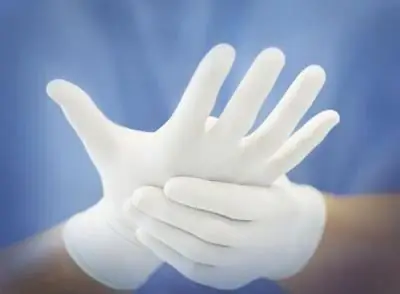
History
The first isoprene was obtained in 1860 by pyrolysis from natural rubber.pyrolysis is the thermal (at high temperatures) decomposition of many inorganic and organic compounds under conditions of lack of oxygen. Later, an isoprene lamp was invented - an electric one with a heated coil, with which turpentine oil was thermally decomposed in laboratories.
The Second World War brought a huge demand for isoprene rubbers, and therefore, isoprene was learned to be produced on an industrial scale by pyrolysis of limonene. Still, isoprene was too expensive for the mass production of synthetic rubbers. The situation changed when a way was found to obtain it from oil. Then technologies for the polymerization of isoprene began to develop rapidly.
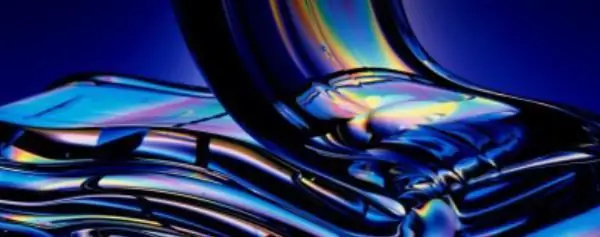
Role in the economy
The most important thing in planning the production of a product such as isoprene rubber is the right choice of location, because it will be necessary to deliver fractions of separation C5 to the destination from several enterprises at once, which carry out cracking. In second place in importance is the consideration in the plans for the disposal site of the remaining hydrocarbons from the C5. fraction.
By the beginning of the nineties of the twentieth century, Western Europe produced about eighty-five thousand tons of C5 dienes, of which forty-four thousand tons was dimerized cyclopentadiene and twenty-three thousand tons was isoprene. The rest - about fifteen thousand tons - were piperylenes. Ten years later, the world production of isoprene had risen to 850,000 tons per year.
Properties
Under standard conditions, isoprene, as already mentioned, is a volatile colorless liquid, almost insoluble in water, but miscible in any ratio with diethyl alcohol, standard, benzene, acetone. Isoprene is able to form azeotropic mixtures with a wide variety of organic solvents. When considering the data of spectroscopic studies, it can be seen that already at fifty degrees Celsius, most of the isoprene molecules take on a stable s-trans conformation, only fifteen percent of the molecules are in the s-cis conformation. The energy difference between these states is 6.3 kJ.
The chemical properties of isoprene present it as a typical conjugated diene, which enters into substitution, addition, complexation, cyclization, telomerization reactions. Active in reaction with electrophiles and dienophiles.
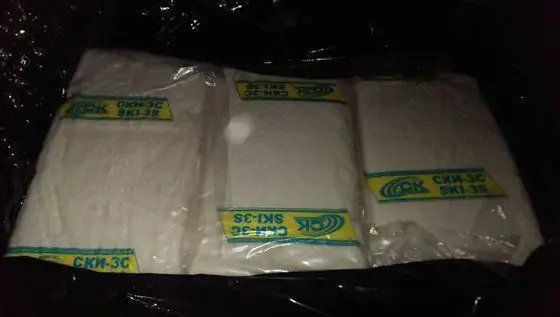
Application
The main part of the isoprene currently produced is used in the synthesis of isoprene rubber, similar in structure and properties to natural rubber. It is used especially widely for the production of tires. There is also another isoprene polymerization product, polyisoprene, which is used much less because it has the properties of gutta-percha. It is used to make, for example, insulation for wires and golf balls. Isoprene rubber is used to make all kinds of rubber products that combine natural and other synthetic rubbers.
For example, to reduce stickiness, are addedbutadiene-methylstyrene rubbers, in addition, fatigue endurance increases if the deformations are repeated. Nitrites add ozone resistance and resistance to heat aging. Thus, observing a set of technical properties, isoprene rubbers perfectly manifest themselves when using conveyor belts, suction or pressure hoses, when lining machine shafts, in the production of footwear, medical and other products.
Environmental hazard
Isoprene is highly explosive and flammable. In high concentrations in the body, it can lead to paralysis and death. This mainly occurs at atmospheric saturation, and therefore metabolism takes place in the respiratory system, when isoprene is converted to epoxides and diols.
Forty milligrams per cubic meter is considered a high concentration - this is the maximum dose. Small concentrations of isoprene in the air can have a narcotic effect on a person, cause irritation of the eyes, skin, respiratory tract and mucous membranes.
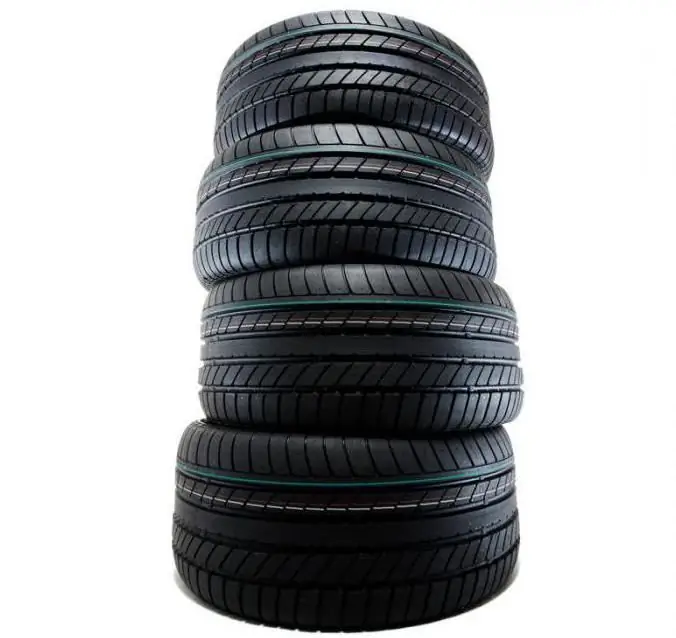
Biology
Modern scientists have discovered that isoprene fumes emit almost all plants into the atmosphere. The global amount of phytogenic isoprene is approximately estimated at (180-450).1012 grams of carbon per year. This process is accelerated if the air temperature approaches thirty degrees Celsius, and also if the intensity of solar radiation is high, while photosynthesis is already fully saturated. Isoprene biosynthesis inhibited by fosmidomycin and compounds of the wholea number of statins. Why plants do this is not fully understood. Perhaps the isoprene gives them extra resistance to overheating. In addition, it is a radical scavenger, which means it can protect plants from reactive oxygen species and ozone.
Scientists also suggest that the synthesis of isoprene causes a constant consumption of NADPH and ATP molecules, which the plant produces during photosynthesis. Hence, the release of isoprene prevents photo-oxidative degradation and re-reduction if the illumination is excessive. The disadvantage of this defense mechanism may be one: the carbon, which is extracted with such difficulty in the process of photosynthesis, is spent on the release of isoprene. Scientists did not stop at plants and found out that the human body can also produce diene hydrocarbons, and isoprene is the most common among them.
Recommended:
Synthetic fibers. Synthetic polyamide fiber
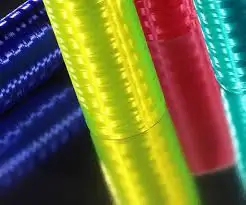
Synthetic fibers began to be produced industrially in 1938. At the moment, there are already several dozen of them. All of them have in common that the starting material for them is low molecular weight compounds that are converted into polymers through chemical synthesis. By dissolving or melting the resulting polymers, a spinning or spinning solution is prepared. Fibers are formed from a solution or melt, and they are only then subjected to finishing
Synthetic accounts. Synthetic and analytical accounts, the relationship between accounts and balance
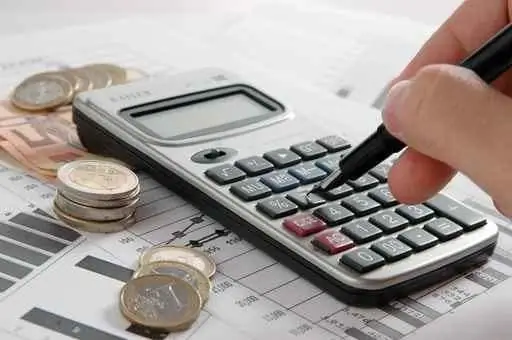
The basis for monitoring and analyzing the financial, economic, investment activities of an organization are accounting data. Their reliability and timeliness determine the relationship of the enterprise with regulatory authorities, partners and contractors, owners and founders
Polymers in our daily lives: synthetic rubber
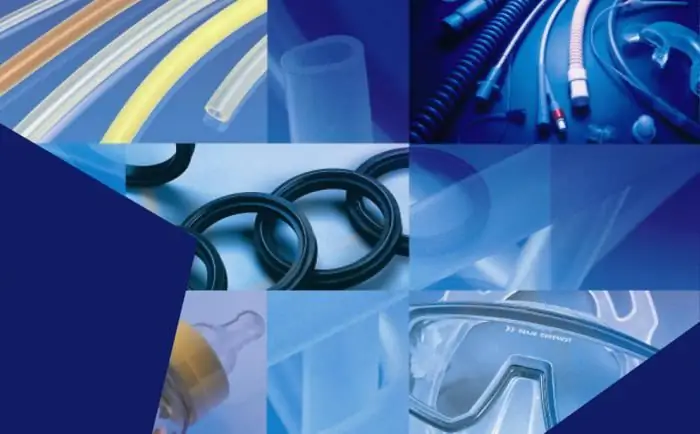
Synthetic rubber plays a very important role in human life. It is found in almost all sectors of our life: from dishes, toys to the automotive industry and rockets. There are two main categories: speci alty rubbers and general purpose rubbers. And each of these categories has its own unique uses
What is rubber: what is it made of, applications
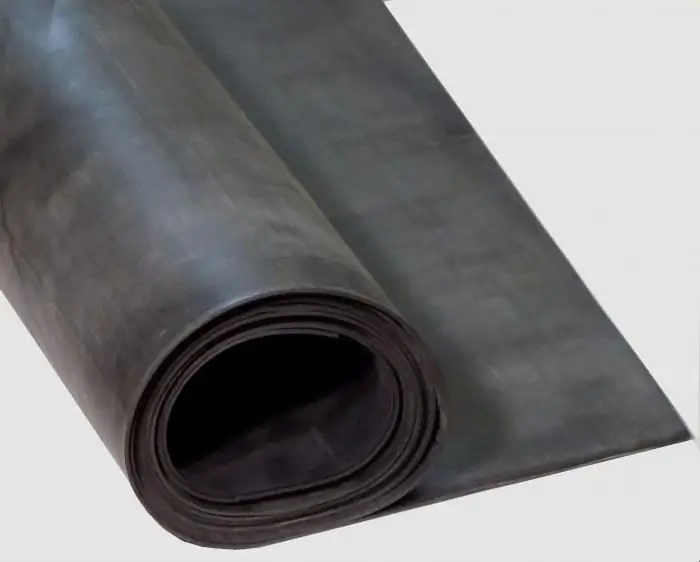
Rubber is a well-known material that is used in almost all spheres of human life. Medicine, agriculture, industry cannot do without this polymer. Many manufacturing processes also use rubber. What this material is made of and what are its features are described in the article
Krasnoyarsk synthetic rubber plant: production facilities, product overview
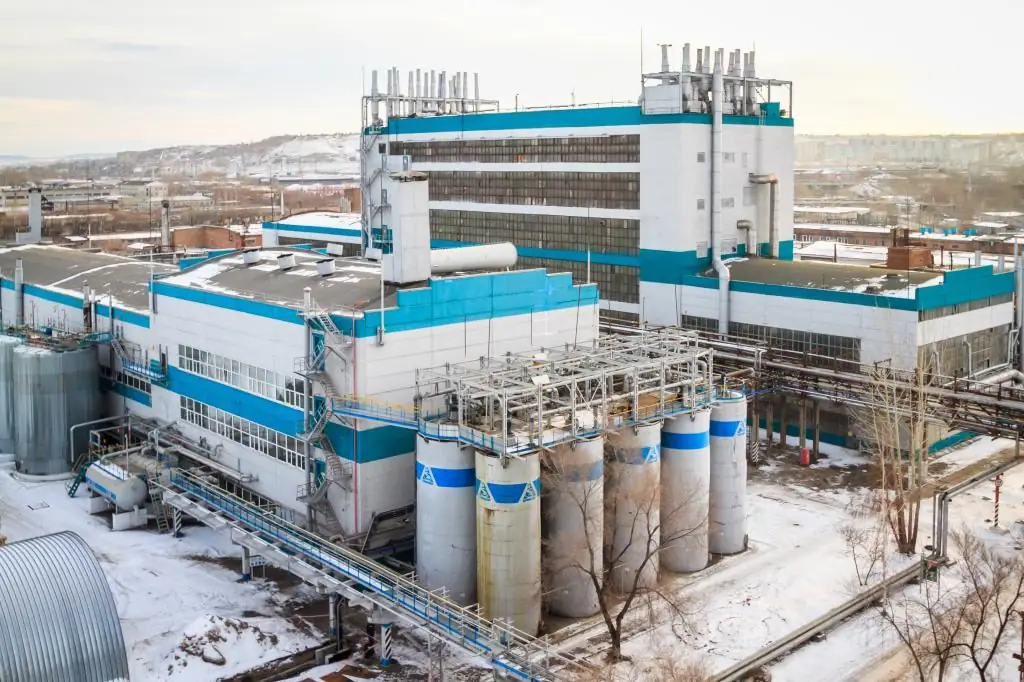
Krasnoyarsk Synthetic Rubber Plant has been producing products since 1947, deliveries are made to 35 countries of the world. The production is more than 42 thousand tons per year, the range includes 85 brands of rubber. The company is one of the ten world leaders in the industry