2025 Author: Howard Calhoun | [email protected]. Last modified: 2025-01-24 13:10
There is a fairly large number of various rail defects. They all occur for different reasons. In total, there are four main types of deficiency, due to which a breakdown occurs. Poor track manufacturing and welding technology is the first cause of wear. The second reason is that the content of the path is too low. The material has such a parameter as contact fatigue strength, and if this parameter is not high enough, then the rails also become unusable. The last reason for the failure of these facilities is the impact of the rolling stock moving over them.
Causes of failure
During operation, rail defects and their likely occurrence are calculated based on several facts. First, an important factor is the amount of tonnage that has passed along the segment of the route. Secondly, the load on the axle of the rolling stock plays a role. The speed of trains can also affect the condition of the rails. Practice and observation show thatin the warm season, that is, in spring and summer, the number of broken tracks decreases. In autumn, this indicator slightly increases, and in winter it increases by 2-3 times, compared with the warm season. There is an explanation for this and it lies in the fact that at low temperatures the metal is characterized by increased brittleness. In other words, its impact strength is reduced to a minimum. The largest percentage of track failures due to rail defects occurs in March, if we talk about the European part of the country, and also in April, if it concerns the eastern and Siberian regions.
Flaw detectors are used to detect such problems. 96.5% of all identified problems can be identified using removable or portable devices. Another 2% are detected using car flaw detectors and another 1% using other models of this device. It is very important to note that there is a classification of rail defects and their description using numbers. This was done in order to be able to carry out a static accounting of rails.
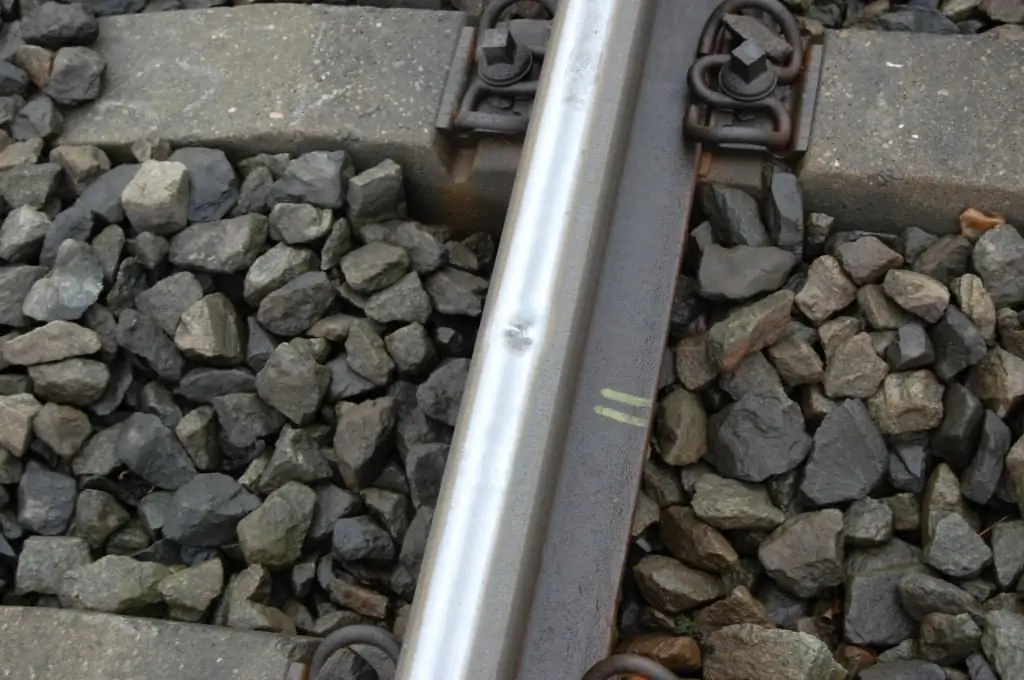
Classification
Any damage, breaks or defects in track sections are indicated using a unified system of numbers. The first two numbers are the main ones, and the third one is the auxiliary. The first number indicates the type of defect or damage to the rail. In addition, it also indicates the location of the problem on the railway section. The second digit describes the type of defect or describes the damage, taking into account the reason for which itappeared. The third auxiliary digit indicates the location of the defect or damage along the length of the rail. In more detail, rail defects and their classification are described by numbers from 1 to 9 for the first character.
- If the first number is 1, it means that there was a chipping and peeling of the metal on the rolling surface of the rail head.
- If the number is 2, it means that transverse cracks in the rail head were found on the section of the track.
- The number 3 also indicates the presence of cracks in the rail head, but of a longitudinal type.
- The number 4 indicates that plastic changes have occurred, that is, crushing, vertical, lateral or uneven head wear.
- 5 are rail damage and defects affecting the neck.
- 6 is a failure or damage to the sole of the rails.
- 7 is a fairly strong deformation, since this figure indicates the occurrence of kinks along the entire section of the railway.
- If breaks occur in the vertical and horizontal plane, then the number 8 is assigned instead of the first.
- All other rail defects, damages, etc. that do not fall into any of the above categories are indicated by the number 9.
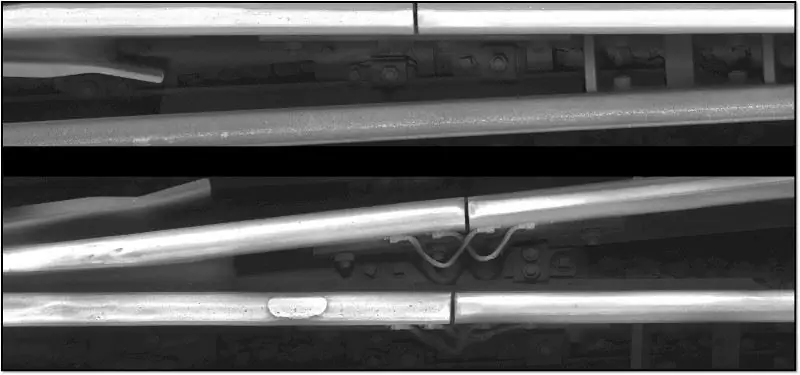
Determining the meaning of numbers
The second of the main digits for the rail defect code also has many values, more precisely, from 0 to 9.
- If the second digit is 0, then this means that the defect arose due to the fact that there were deviations from the technology when creating this section of the railwayproduction.
- The number 1 indicates that the metallurgical quality of the steel used to make the rails was insufficient. It is also possible that the strength of the steel was lower than needed for normal operation.
- 2 - indicates that errors were made during the processing of the ends, due to which the section of the path failed. In addition, it also includes some of the disadvantages that arise when processing rail profiles.
- 3 - these are defects in the rails of the railway track, which arose due to the fact that the requirements of the instructions for the current maintenance of the object were violated. It also includes damage caused by the fact that the principles of the technology for processing bolt holes in a smelter were violated.
- If the second number is 4, then this means that problems with the rails arose due to the specific impact on them from the rolling stock, for example, due to slipping. This also includes damage that occurs due to the fact that the rolling stock does not pass proper checks or driving modes are violated.
- The number 5 includes all damage caused by any mechanical impact from the side, for example, hitting a tool, hitting a rail against a rail, etc.
- Fairly common rail welding defects are caused by irregularities in the operation of the welding machine. They occur in welded joints and are numbered 6.
- 7 - problems associated with the operation of the rails at the joints.
- 8 - these are flaws that arise due to surfacing of rails, as well asdue to improper welding of the rail joints.
- All problems caused by corrosion are numbered 9.
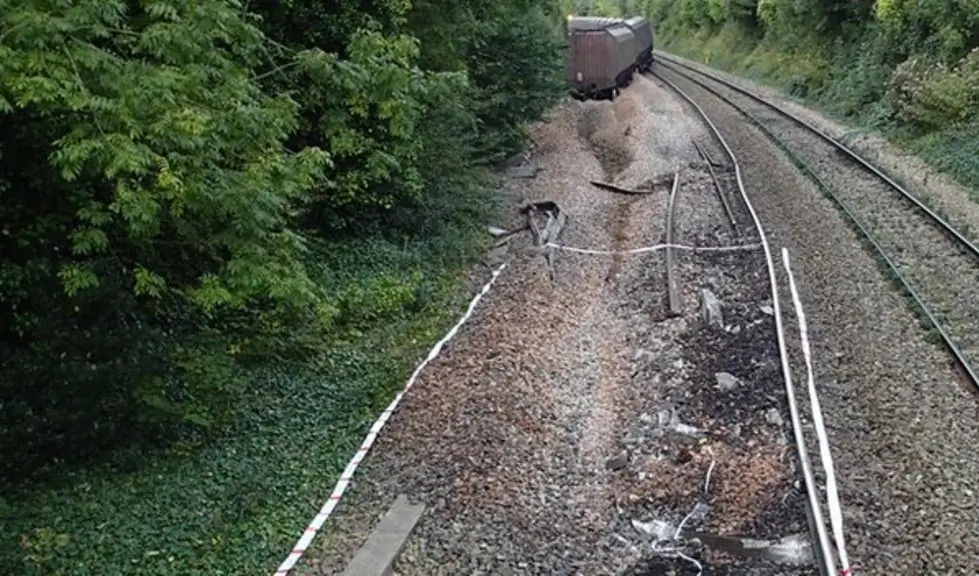
It is worth noting that the failure of a section of track due to broken rails is a consequence of the impact of several causes at the same time. Most often, it turns out that the lack of maintenance of the railway greatly accelerates the development of those flaws that were made during the assembly or welding of the structure. Because of this, it becomes difficult to determine the cause, since it is necessary to find exactly the main source of the breakdown. Defects in the rails of the railway track, or rather, their numbering also has a third digit.
- 0 indicates that the problem is present along the entire length of the rail.
- 1 means that the problem is at the joint, in several places. Perhaps the bolted joint is broken, which is located at a distance of at least 750 mm from the end of the rail. If we are talking about a welded joint, then at a distance of 200 mm symmetrically 100 mm on each side of the axis of the weld.
- 2 indicates that the problems are somewhere outside the joint. If we are talking about a bolted connection, then you need to look at a distance of 440 mm symmetrically 220 mm on each side of the axis of the weld in the rail foot.
Defects in rail welding and other damage are also divided into four categories, depending on the degree of their development. There is a degree of DP, D1, D2 and D3. The most dangerous are DP. This designation indicates that the damage has reached critical values or sizes. Such areas shouldbe replaced first. Defects that are classified as D1 and D2 will be fixed in accordance with the established procedure, which takes into account the intensity of the problem. Rails with defects related to category D3 are replaced only if the head of the track distance so decides. The decision is made on the basis of the data transmitted by the foreman after a scheduled inspection and taking into account the degree of development of the defect. As a result, it turns out that rail defect codes consist of three digits, as well as an indication of the degree of their development on the section.
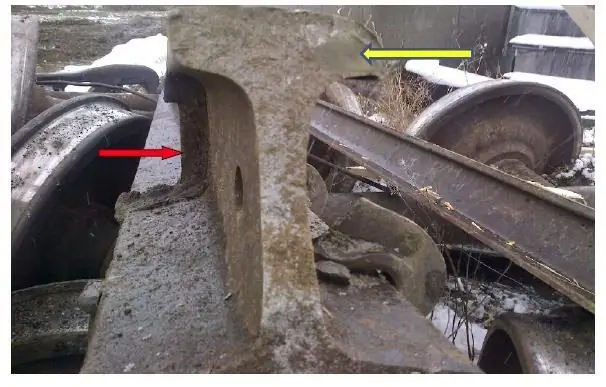
Flaw detection
Flaw detection is a procedure for identifying flaws in the structure of the railway using special flaw detection devices. It is worth noting that the rails go through this procedure several times. The first flaw detection is carried out at the rail rolling plant, when it is necessary to assess the quality of the finished work. The next verification process takes place already in operational conditions, that is, on the way. Additionally, verification is carried out in rail welding workshops, where the process of welding not only new ones, but also repair or welding of old structures is carried out.
The flaw detection procedure is intended primarily to identify those dangerous rail defects that are inside the structure, that is, they do not yet have flaws on the outside. This makes it possible to replace the damaged structure in a timely manner.
Types of problems
Currently, all kinds of defects, ways to eliminate them, the reasons for their occurrence,the means of their determination, etc., are presented in the "Regulatory and technical documentation NTD / TsP 2002". In addition, it is worth noting that there is also experimental documentation, as well as the classification of rail defects NTD / TsP 1-93, according to which all problem sections of the railway are divided into acutely defective (OD) and defective (D). It is the category of flaws D with the help of NTD / CPU 2002 that is divided into a large number of types, depending on the cause of occurrence, degree of distribution and location on the route section.
To sharply defective rails are those that pose a direct threat to the movement of the train, because due to the influence of a flaw, they can collapse right under the wheels of the train or cause the rolling stock to leave the track. If such a section is found, it must be immediately changed either to a new one or to an old one from a kilometer stock. If new defects in railway rails were discovered before the warranty period for their use expired, or if less tonnage was passed through them than indicated in the documentation, then a complaint is made against the metallurgical plant where they were manufactured. If the defect was detected at the welded joint also ahead of schedule, then the complaint is submitted to the rail welding plant.
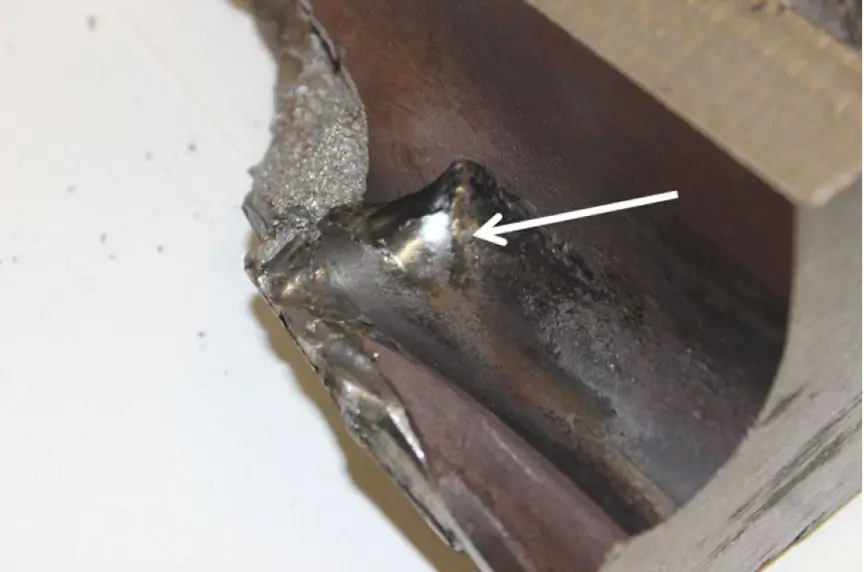
Defective rails include those sections of the track that, due to the long service life, began to become unusable. The formation of flaws in such areas is expected. However, they still have to ensure the safe passage of rolling stock. Although inIn some cases, a speed limit is introduced when passing such a segment of the path. The new edition of rail defects and their classification is presented precisely in the normative and technical document NTD / CPU 2002. The code values of possible problems were presented above.
Separation into sharply defective and defective areas
The documentation indicates the speed at which the train is allowed to move along a particular section of the track. If the degree of development of the defect belongs to the DP group, then the speed of movement is not more than 40 km / h until the moment of elimination. Category D1 allows a speed of no more than 70 km/h, D2 - no more than 100 km/h. Flaws belonging to group D3 do not create a restriction on the speed of movement of the rolling stock.
In addition, there is a set timeframe for replacing each group of defective rails. If no replacement occurs within the established period, the category is replaced by a higher one. In other words, DP3 goes to D2, D2 to D1, D1 to DP. Naturally, with each transition, the replacement deadlines become more stringent, and the speed limit for movement also increases, in accordance with the established norms.
Defects in rails and their new classification according to NTD/CP also define problems that turn a section of track into a state of severely defective or simply defective tracks. To OD belong such problems as:
- The occurrence of transverse, longitudinal or lateral cracks in the head of the rails. Most often, breakdowns belong to the second and third groups, and their codes are 20, 21, 24, 25.
- Cracking in bolt holes withcode 53, as well as cracks in the rail neck, regardless of size, as well as with codes 50, 55, 59 and 56.1.
- Occurrence of corrosion or local wear of rails with code 69 cracks that have arisen due to corrosion fatigue, chipping out of the sole of rails with codes 60, 64, 65, 66, as well as transverse fractures of rails.
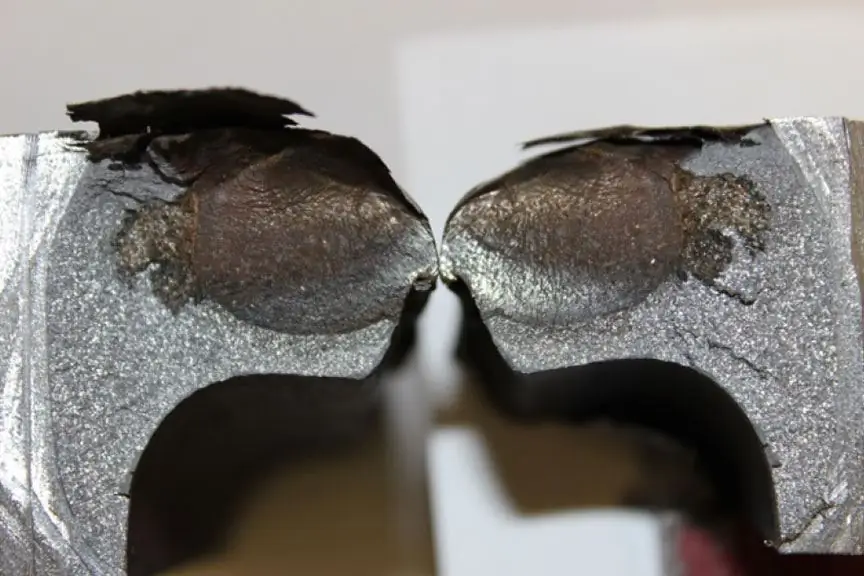
The occurrence of any of these new defects leads to the fact that even a new section of the railway goes into a state of ML and must be urgently replaced. There are several signs by which defective rails are identified in the receiving and departure tracks. These include:
- exceeding normalized reduced code 41+44, side code 44, or vertical rail head wear;
- chipping of metal, if the depth does not exceed 3 mm, and the length is 25 mm;
- presence of rolling stock slippage, undulating wear.
It is also worth adding that the largest percentage of the transition of normal rails to the defective category occurs due to the fact that there is a lack of contact fatigue strength of the material. Such problems of defects in rails and turnout elements, which are also installed on rails, are classified as codes 11 and 21. Also quite often the cause is problem 44, which means severe lateral wear of the rail head. Quite often there is corrosion of the sole of the rail - 69.
Especially dangerous defects and causes
First of all, when checking the rails, it is necessary to pay attention to those breakdowns that are caused by"fatigue" of the metal. They are considered the most dangerous. In more detail, it looks like this. The train wheel is in contact with the rail on a fairly small area during movement. It is through this small area that the huge amount of voltage that a moving train creates is transmitted. It is these contact stresses, especially if they occur in the immediate vicinity of the rail head, cause it to chip or lead to metal spalling. The more wheels pass through this area, the more the metal "gets tired". It is because of this that defects 11.1-2 are caused by such a problem as low contact strength of the material. To avoid this problem, or at least to make the rails withstand more movements, it is necessary to increase the strength of the raw material.
Delamination or spalling of metal can also be caused by the presence of hairlines, sunsets or captivity, which may appear on the surface of the rails during rolling.
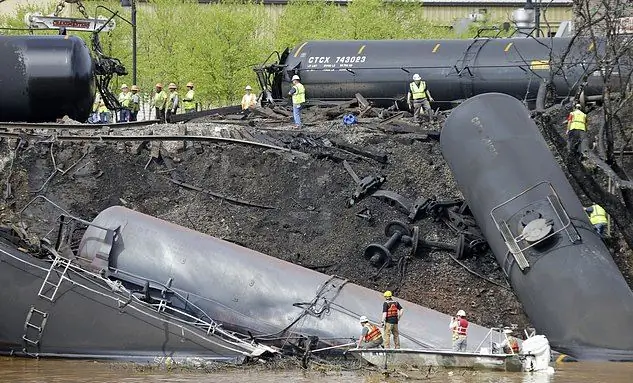
Such groups of rail defects as 20.1-2 and 21.1-2 are considered very dangerous. As for the second group of flaws, they quite often appear in the form of internal cracks in the head or external cracks that appear in the area of the fillet in the head. If such a problem occurs, then the rail may subsequently break under the weight of a moving train into many small pieces. Naturally, this will lead to an accident and, most likely, the train will go off the track. As for the problems with code 20.1-2, theyarise in the head itself, and the main reason for their appearance is the shortcomings in manufacturing technology.
Railway defects due to poor inspection
It is worth noting that on October 23, 2014, the classification of rail defects 2499 NTD / CPU was approved. This document entered into force on September 1, 2015, and the document itself contains 140 pages. In addition, a new instruction on the maintenance of tracks 2288 was also adopted. This document entered into force on 2017-01-03.
Such flaws as 11.1-2 and 21.1-2 are also quite often due to the fact that road foremen poorly monitor the condition of the rails. If in the first period of operation an incorrect rail underslope occurs, then the main stress will shift from the center of the section to the edge where the head is located, which, of course, will lead to its rapid wear. The frequency of occurrence of defects also increases significantly if there is a violation of the smoothness of the rail threads. Further, it is important to note that the process of the growth of the appearance of these problems is strongly associated not only with improper maintenance of the tracks, but also with violations in the care of the rolling part of the train itself. If chipped, sliders and other flaws appear on the wheels of the car, then this greatly affects the fatigue strength of the metal and its development.
Besides the head, problems often occur in the neck of the rails - cracks in the area of the bolt holes, the main problem. Most often, a crack originates in the contour of a bolted connection, and then leaves at a slope of 45 degrees to the horizon. An effective means of combating such cracksis the quality content of the joints. In other words, it is necessary to tighten the bolts as tightly as possible, to prevent sagging of the rails or their subsidence. Cracks in the neck also often appear in places where the head of the rail passes into the sole. The main reason for the appearance of such a defect is an incorrectly selected rail underslope.
As for the sole itself, here most often there are not only cracks, but also punctures, hairlines. All this leads to a break in the railway tracks, to the appearance of longitudinal cracks, and accelerates the process of corrosion. The best way to deal with many sole defects is to install a resilient pad that is placed directly under the rail sole.
Location of defects and their names
Currently, there are quite large tables that indicate the main rail defects that can occur. They also indicate the place where this or that damage occurs, the problem code is precisely indicated. Such tables look like this.
Problem description | Location of damage on rails | Defect code |
Due to the violation of rail manufacturing technology, a problem such as cracks or chipping of metal on the head rolling surface may occur | In and out of the joint | Depending on the location, the code can be 10.1 or 10.2 respectively |
Cracks or chipping can also occur on the side of the head oron the fillet. They arise from the inside under the influence of a large number of non-metallic accumulations | In and out of the joint | As in the previous case, the code can be 11.1 or 11.2 depending on the location of the damage |
Metal chipping may occur on the tread surface. The reason for this is that the dynamic effect in the joints of the bolts increases | In the junction | this damage code is 13.1 |
Metal spalling may occur on the tread surface of the head in the area of the welded joint after the amount of tonnage passed under warranty has expired | Defect of rail welds | Flaw code 16.3 and 16.4 |
Similar problem with metal spalling but before the guaranteed tonnage has been passed over the rails | Weld joint | Defect 17.3 and 17.4 |
It is possible that transverse cracks in the head may occur under the influence of thermomechanical effects from slipping or skidding, for example | Occurs both inside and outside the seam | 24.1 and 24.2 |
Due to a violation of welding technology or a violation in the processing of welds, transverse cracks in the head may occur. It is important to add that this can lead to rail failure immediately after the warranty tonnage is missed | Weld joint | 26.3 and 26.4 |
If the same problem occurs as in the previous case, but before it was skippedguaranteed tonnage, then the problem is transferred to another category | Weld joint remains as location | Error code changes to 27.3 and 27.4 |
If the rail manufacturing technology is violated, longitudinal or transverse cracks may form in the rail heads. | This happens both in the joint and outside the joint | Damage code 30.1 or 30.2 |
Determination of railway defects
Today, the only method that allows you to detect new defects in railway rails at an early stage and prevent it is the ultrasonic method.
This non-destructive testing method can detect damage in metal rails using ultrasonic pulses. This method is used in many industries where there is work with metal, but it is most popular at railway stations, where it is most important to monitor the quality of the tracks. Ultrasonic flaw detection will allow workers to quickly and accurately identify hidden damage, while not influencing or destroying the object of study.
This method of detecting rail defects has several undeniable advantages.
First, and most important, is the absence of any damage or any other marks left on the test specimen, i.e. new defects. Secondly, the cost of such equipment is quite low, and the reliability of the data obtained as a result of its use is very high. Moreover, it is important enough thatsuch a device allows you to search for new rail defects at any time of the year, which is especially important.
Ultrasonic method of detecting defects allows you to find even the slightest damage in any metal products and joints. For this reason, they are also actively used to inspect turnouts and structural welds. Using ultrasonic equipment, the following damage can be determined: the occurrence of violations in the homogeneity of the structure; check the places damaged by corrosion; check whether or not the chemical composition of the rail corresponds to the one stated in the documents.
Recommended:
Reserves of banks and their formation. Required bank reserves and their norm
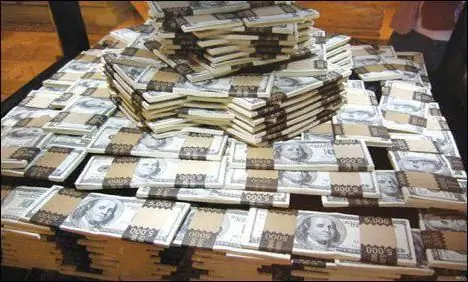
Bank reserves ensure the availability of funds for the uninterrupted fulfillment of payment obligations regarding the return of deposits to depositors and settlements with other financial institutions. In other words, they act as a guarantee
Main types and types of business plans, their classification, structure and application in practice
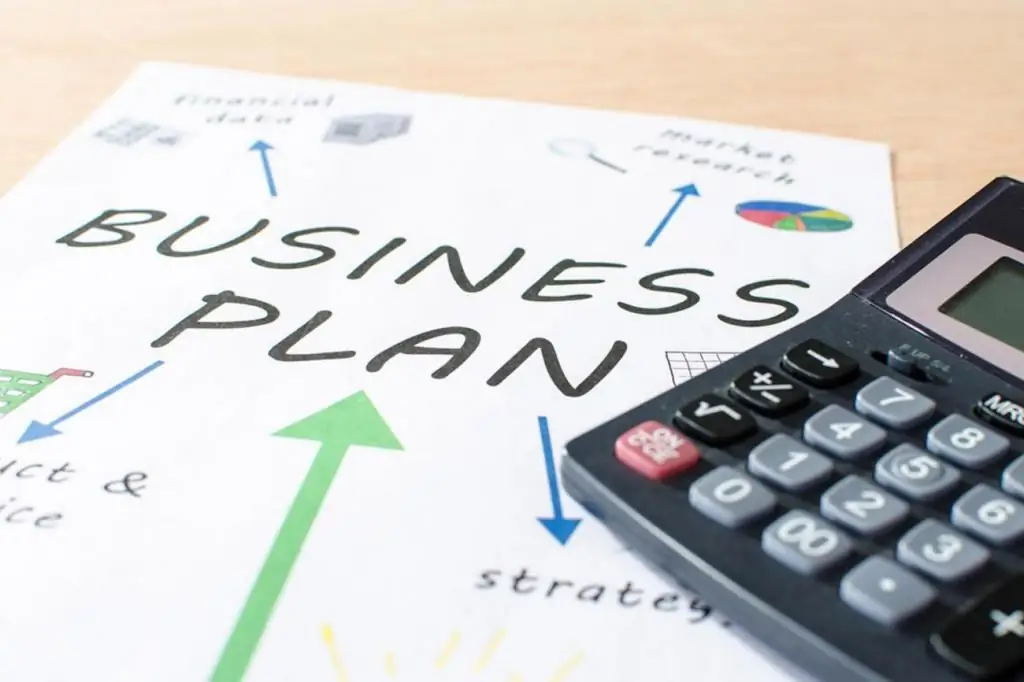
Each business plan is unique, because it is developed for certain specific conditions. But you need to familiarize yourself with the features of various types of business plans in order to understand their key features. Experts recommend doing this before compiling your own similar document
Defect scopist - who is it and what kind of profession?
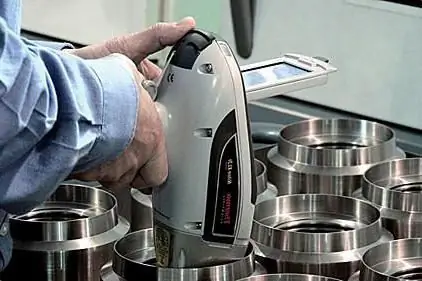
Profession flaw detectorist: who is it and what does it do. Work as a flaw detectorist, is the profession in demand? Where do flaw detector engineers work? Vacancies of a defectoscopist in the labor market
Organizational structure of Russian Railways. Scheme of the management structure of Russian Railways. Structure of Russian Railways and its divisions
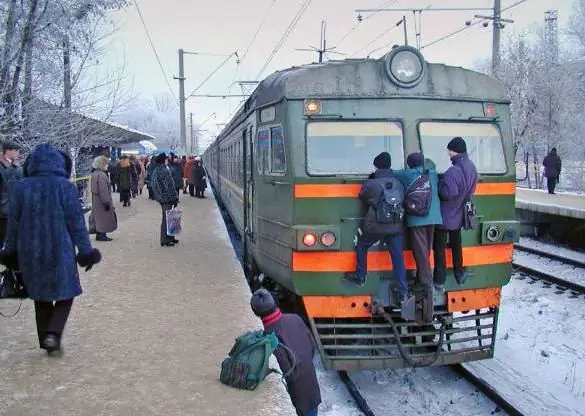
The structure of Russian Railways, in addition to the management apparatus, includes various dependent divisions, representative offices in other countries, as well as branches and subsidiaries. The head office of the company is located at: Moscow, st. New Basmannaya d 2
Graphic designation of the ruble. International designation of the ruble
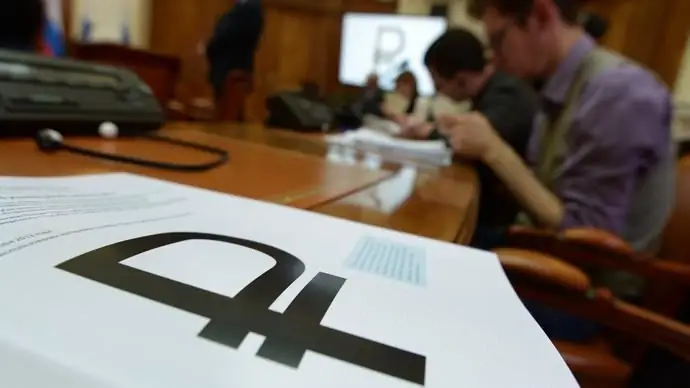
The graphic designation of the ruble has the format of the Cyrillic letter "R", which is crossed out at the bottom of the leg. This symbol, developed over the course of 6 years, embodies the reliability of the Russian currency