2025 Author: Howard Calhoun | [email protected]. Last modified: 2025-01-24 13:10
A flaw detector is a specialist who detects defects, mechanical damage and defects in production. For example, a railcar depot flaw detector engineer checks train wheelsets for cracks and damage during operation.
For people of this profession, special measuring instruments are needed. Flaw detectorists working on railroad tracks detect defects in rails using flaw detection carts or wagons.
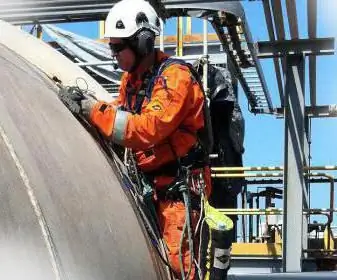
The profession of a flaw detectorist is the most important and responsible in metallurgical industries. Products manufactured at the factory are necessarily carefully checked by specialists for hidden defects that cannot be noticed without ultrasonic equipment.
What a flaw inspector should know
A flaw detection engineer is a rather difficult and responsible job. He is responsible for the quality of products manufactured at the plant, for the life and safety of passengers in the case of working in the rail transport industry. Not surprisingly, employers have a number of requirements for applicants for this position. Defectoscopistmust know the following:
- normative acts concerning labor safety and methodological acts of the state measurement system;
- types of possible defects, design features of the test object, potential danger during measurements;
- methodology and technical documentation for non-destructive testing;
- rules for selection and quality control of materials;
- types of defects, their classification, signs by which a defective part is detected.
Duty inspector
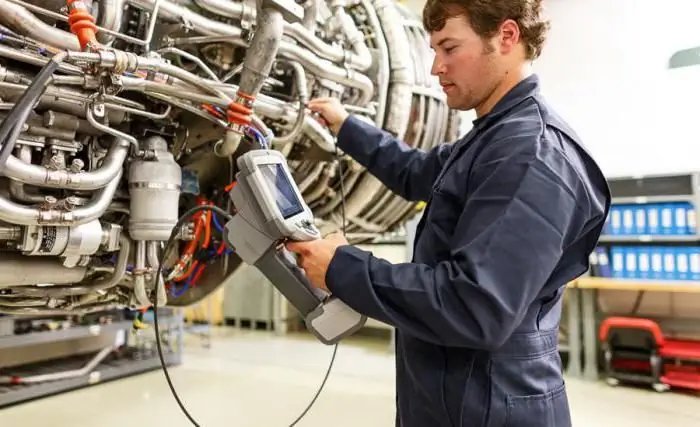
Many people ask the following question: "Who is a flaw detectorist? What does he do?" The flaw detection engineer has a number of job responsibilities in the workplace, which are listed below:
- carrying out work related to non-destructive testing and diagnostics of tested products;
- work planning and quality control during work;
- Checking the quality of measurements by subordinates;
- preparing a report on the quality of the test sample;
- ensuring the safety and performance of measuring equipment;
- monitoring simple and complex parts on stationary and mobile devices (flaw detectors);
- eddy current testing of cylindrical parts;
- setting, if necessary, flaw detectors of magnetic, ultrasonic and electromagnetic type;
- preparation of magnetic suspensions;
- checkparts for the presence of bundles, fixing the boundaries of the bundle in case of detection using a special device;
- keeping records of work performed.
Training
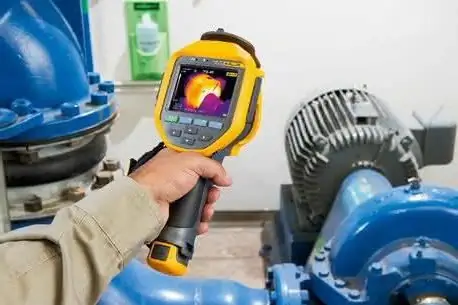
The position of flaw detector engineer is in high demand in our country. Qualified specialists in this field do not feel a lack of offers on the labor market. According to data received from the Ministry of Labor of Russia, in January 2016 the vacancy of a flaw detector (specialist in non-destructive testing) was included in the list of the most sought-after professions.
Training as a flaw detector consists in acquiring knowledge regarding the principle of flaw detector operation, its main purpose, and machine control functions. Also, students will have to take courses on the topic "Basic concepts of electrical engineering".
After successfully completing the training, the flaw detector operator receives the following professional skills:
- Checking the quality of welding using magnetographic equipment.
- Fixing the level of magnetic permeability of austenitic steels depending on the amount of ferrite.
- Diagnosis and detection of surface defects, calculation of their coordinates and area.
- Diagnostics of used equipment, namely flaw detectors, depth gauges and transducers.
- Quality control of welds and rolled carbon low-alloy steel using an ultrasonic device.
Career Opportunities
To find out more about who it is -defectoscopist, will help understanding the possibility of climbing the career ladder for an employee working in this position. Citizens working in the profession of a defectoscopist, who have a professional education in this field and the 2nd category, can improve their qualifications in stages up to the 6th category. To do this, you must pass a medical examination and obtain a certificate that a person is fit for work, as well as complete a training course and pass qualifying exams.
Flaw detector equipment
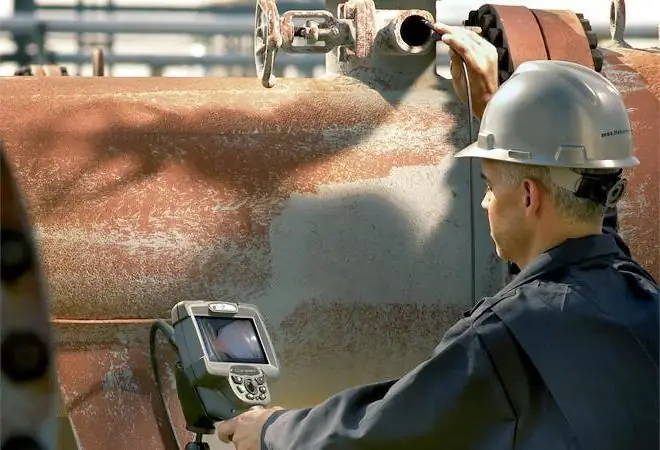
Many people are interested in the question: “Who is this - flaw detector? What functions does it perform? To answer this question, you should know what a flaw detector is.
The word "defectoscope" came to us from the ancient Greek and Latin languages, and in literal translation means "I observe a lack." This device is designed to detect defects in products made of various materials. In this case, the method of non-destructive testing is used. These defects include:
- Inhomogeneous part structure.
- Discontinuity.
- Deviation from given dimensions.
- Change in chemical composition.
- Corrosion damage.
Where flaw detectors are used
To answer the question: “Who is a flaw detectorist?” - you should know where the device is used to detect defects. Flaw detectors are needed to check transport, to control the production of machine-building plants, in the chemical industry, construction, energy, in scientificlaboratories and many other industries.
Defect detection equipment is used to control the quality of parts, blanks, welded, adhesive and solder joints. Some devices are able to check products that move at high speed, for example during pipe rolling. Also, some flaw detectors are able to work while moving at high speed, for example, wagons or carts equipped with the necessary equipment. Metallurgical enterprises often use flaw detectors capable of inspecting parts heated to high temperatures.
History of the flaw detector
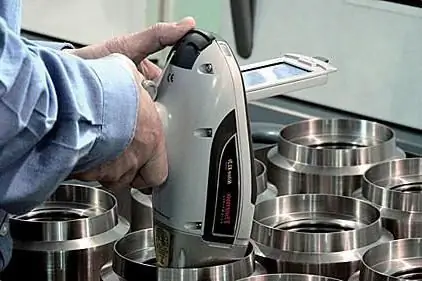
To understand who they are - flaw detectors and what they do, it is worth knowing a few historical facts about the history of the flaw detector. For the first time, the Curie brothers in 1880 noticed the reversible effect of piezoelectric pulses. This discovery made it possible to use quartz to convert electrical vibrations into sound.
The first flaw detector was created thanks to D. Lachinov at the end of 1880. Its main purpose is to detect a break in the electrical circuit.
But more modern flaw detectors, working thanks to echo-pulse signals, were assembled in 1943 by two companies almost simultaneously: the American Sperry Products and the British Kelvin & Hughes.
Recommended:
What kind of profession is a logistician?
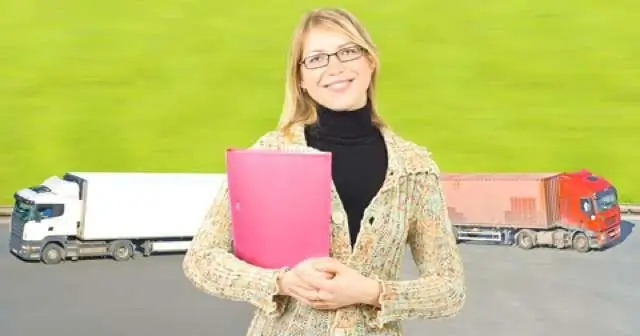
The profession of a logistician is directly related to the commodity market. Transport logistics includes everything related to the movement of products (from the place of production to the point of storage and delivery of products to the final point). The mechanism of delivery of goods must be carefully debugged. This is necessary in order for the goods to get to the place of sale on time and make a profit
Estimator - what kind of profession is this? Where to study and work?
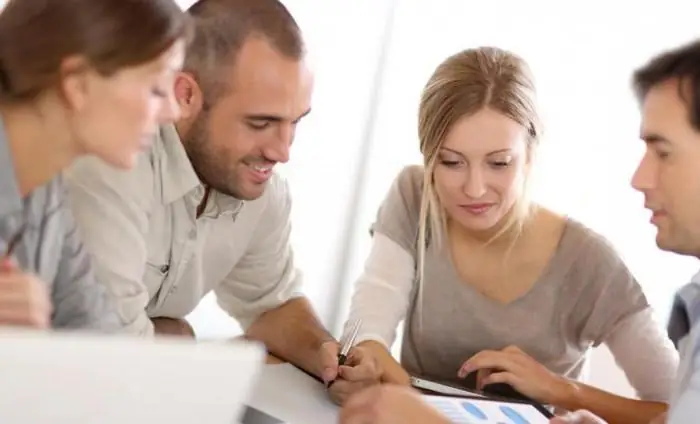
The ability to make estimates requires a lot of experience and knowledge. After all, such documentation reflects the cost of construction, shows the available costs for materials, the profit of the project. In addition, you can reduce costs or increase profitability. It turns out that the estimator is a specialist who combines knowledge about construction, finance and knows how to put them into practice in a quality manner
The profession of a film and theater actor: a description of the profession, pros and cons
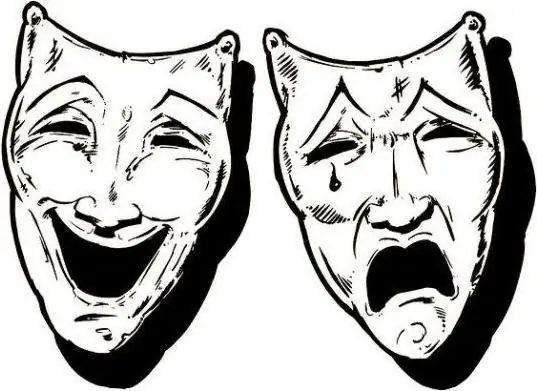
Today, many want to be involved in the art of acting, because under certain conditions a person can realize himself in it, eventually gaining fame, recognition and immense popularity
Defects of rails and their classification. Rail defect designation structure
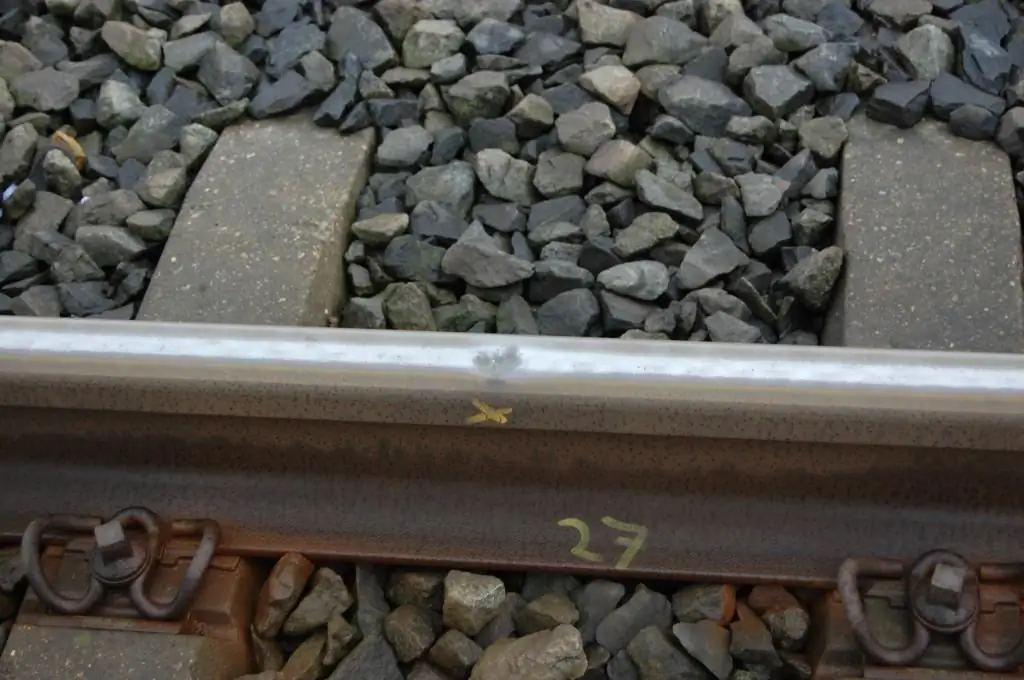
Currently, people are actively using the railway. Delivery of various types of cargo by this route is the main type of transportation. However, due to the large weight of the trains themselves, as well as the cargo they carry, there is a strong pressure on the rails. Defects in these objects are a fairly common occurrence, which must be eliminated immediately
Re altor - what kind of profession is this? The subtleties of the profession of a re altor
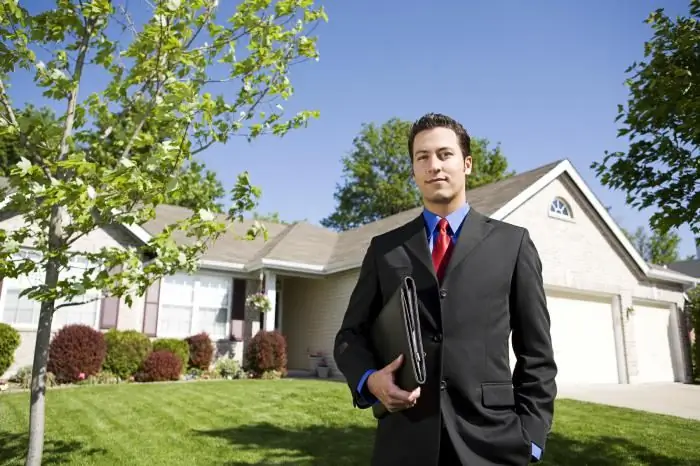
People involved in real estate transactions often have the question: "What is a re altor?" This is a specialist who provides intermediary services in this area (purchase, rent, sale). He brings together buyers and sellers to conclude deals, and then receives a reward for his services in the form of a percentage of the total amount