2025 Author: Howard Calhoun | [email protected]. Last modified: 2025-01-24 13:10
Fretting corrosion is based on physical and chemical processes occurring at the molecular level. At the first stage, electrochemical destruction predominates. In the contact zone of metals (or metal with non-metal), oxides are formed, due to which mechanical wear is activated. These two processes are closely related and affect the strength characteristics of assemblies. The phenomenon of fretting has been studied by researchers for more than a century, but its prediction is still poorly developed.
Description
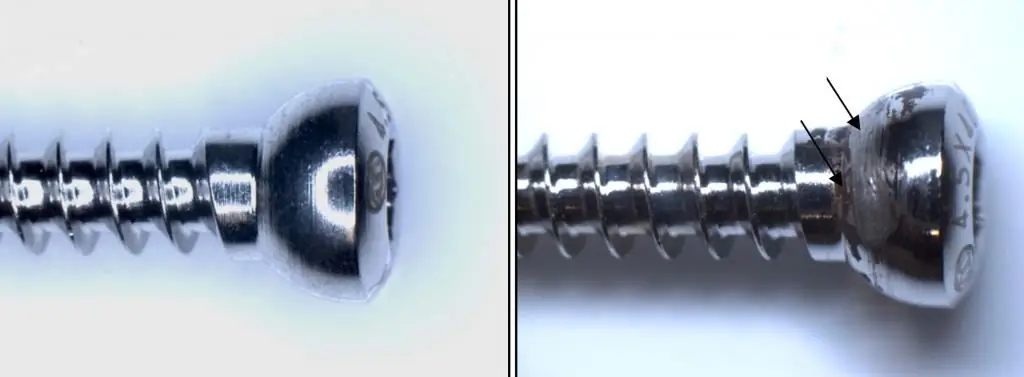
Fretting corrosion is one of the varieties of spontaneous destruction of the metal. This process occurs at the interface of tightly contacting metal-metal or metal-nonmetal pairs. Its characteristic feature is the presence of oscillatory movements of small amplitude. Fretting corrosion affects not only carbon steels, but also corrosion-resistant steels.
For the occurrence of this phenomenon, a cyclic amplitude of only 0.025 microns is sufficient. Its maximum value can be 200-300 microns. Externally, the destruction is manifested in the appearance of small ulcers, rubbing, tearing,colored spots, powdery deposits on the contact surface.
Oxide-like corrosion products of steel parts have a different color - from reddish to dark brown. It depends on the brand of material and operating conditions. They cannot leave the contact area due to the small amplitude of oscillations of the mutual movement of the surfaces, as a result of which their abrasive effect is enhanced.
The most negative consequence of this phenomenon is the fatigue failure of parts. The ability to perceive cyclic loads in the nodes is reduced up to 5 times.
Wear features
Fretting corrosion has the following differences from other types of wear and tear:
- Metal damage occurs in reciprocating motion.
- Localization of damage - only in the contact area of parts.
- Low travel speed in rubbing pair.
- The destruction of oxide films occurs mainly due to tangential (tangential) forces.
- Rupture of welding bridges during setting of surfaces leads to detachment of atoms and the appearance of fatigue cracks.
- Teared off metal particles quickly oxidize in air.
- Corrosion products are actively involved in the further wear process.
Causes and mechanism of the phenomenon
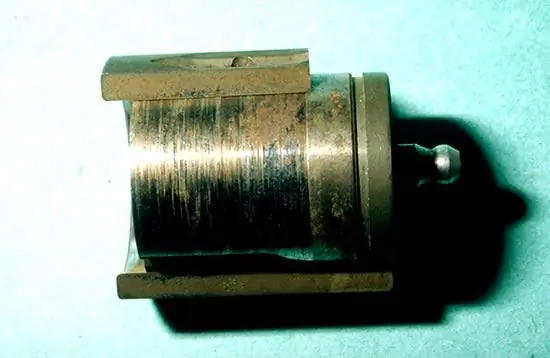
Simplistically, the process of fretting corrosion can be represented as follows:
- Move and deform surfaces.
- Metal oxidation.
- Destruction of oxidefilms.
- Discovery of pure metal.
- Its grip with the contact surface.
- Destruction of grasping bridges.
- Increased oxygen concentration in open areas.
- Repetition of the corrosion cycle, gradual increase in caverns.
As a result of the abrasive action of detached particles, the temperature in the contact zone also rises (in some cases up to 700 ° C). A white layer is formed, consisting of altered metal structures.
The following main causes of fretting corrosion are identified:
- Low amplitude dynamic loads in fixed connections.
- Aggressive external environment.
- Temperature factor.
The nature of the corrosion process depends on what stage it is at. At the initial stage, the predominance of oxidative reactions due to electrochemical interaction was recorded. This process is slowed down by the use of chemical compositions that weaken the action of an aggressive environment. We will discuss what corrosion inhibitors are below.
The stressed state of the material has three components - the compressive force directed perpendicular to the contact surface, alternating shear stresses and friction force. Wear during fretting corrosion has the character of fatigue failure. Small cracks merge over time and pieces of metal break off.
Construction knots
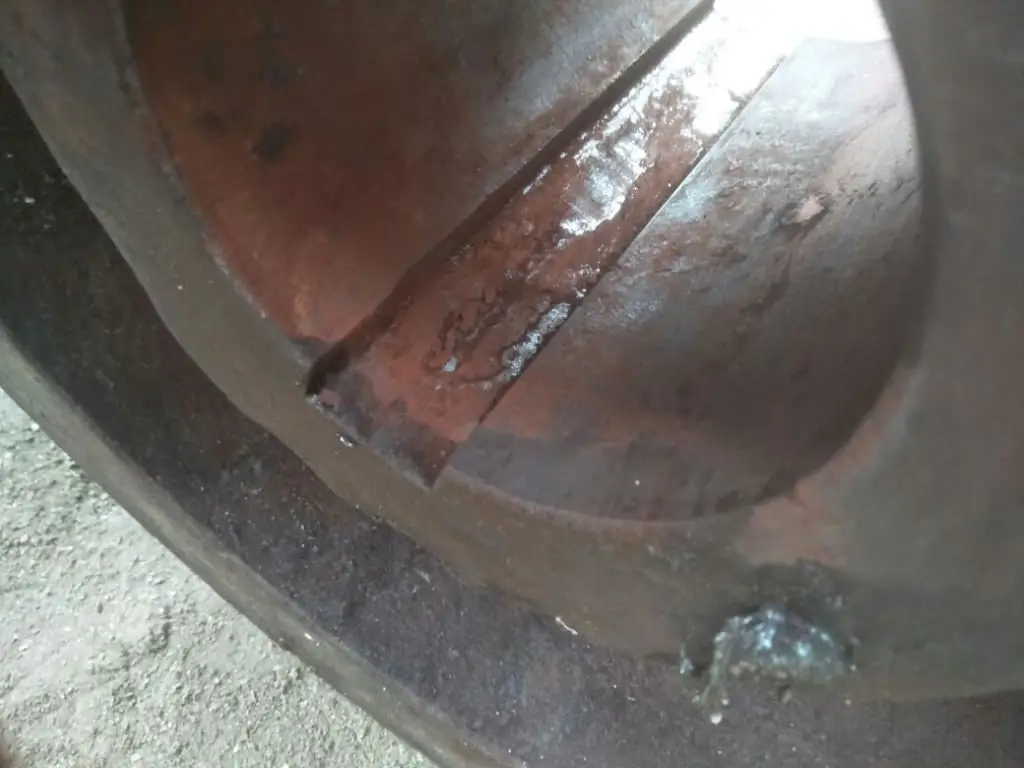
Fretting corrosion characteristic of assembly units,nominally immovable. Most often, the destruction of the metal is observed in the following types of joints:
- Bolted.
- Riveting.
- Slotted.
- Contact electrical.
- Castle.
- Toothed Hirths.
- Flanged.
- Squeeze fit (bearings, discs, wheels, shaft couplings, axles and wheel hubs).
- Spring bearing surfaces and others.
Fretting corrosion of bolted joints is caused by wear of the threaded part and the appearance of leaks in the gap. This is facilitated by a decrease in tightening during operation, self-unscrewing of joints due to vibration loads. However, an increase in the tightening torque is not a guarantee of a reduction in fretting corrosion, since in this case resistance welding of the surfaces may occur. As a result, the work of the threaded connection will occur in unfavorable conditions of tensile stresses.
Fracture intensity
The rate of fretting corrosion depends on several dozen factors. The most important ones are:
- Ambient atmosphere (corrosion proceeds faster in air). This phenomenon is also observed in vacuum, nitrogen and helium.
- Amplitude and frequency of oscillatory movements (friction speed). The relationship between fracture rate and amplitude is almost linear.
- Pressure (load) in the contact zone and other operating conditions. With a significant load, the depth of damage increases.
- Hardness of base metal and protective coatings of parts, roughness of contactingsurfaces.
- Technological factors (method of obtaining the workpiece, residual stresses, machining accuracy and rigidity of the assembled assembly).
- Properties of oxide products resulting from wear.
- Temperature. In most cases, its negative values contribute to higher corrosivity. Positive temperatures favorably affect the performance of the unit only up to a certain critical value. When overheated, the rate of destruction increases.
- Abrasion resistance of wear products.
Methods of struggle
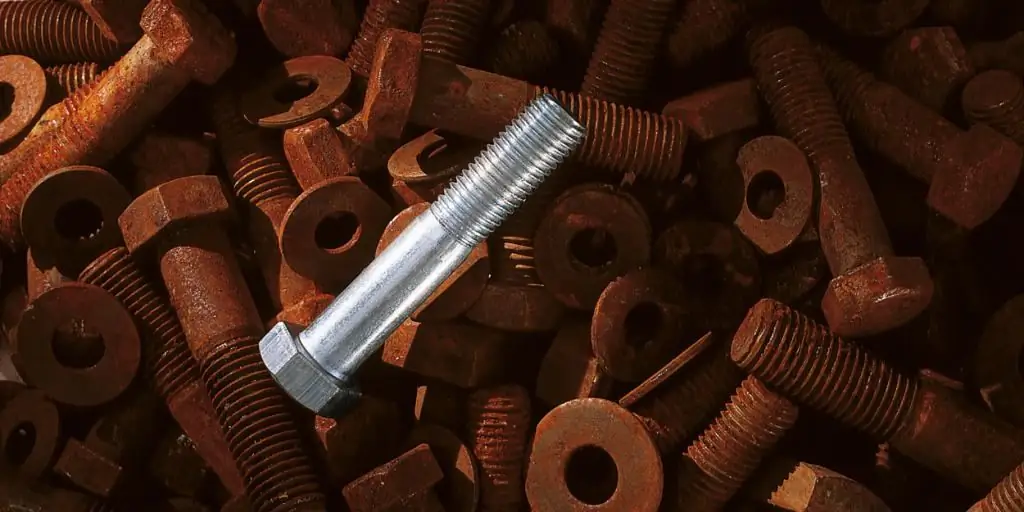
Ideal ways to deal with this phenomenon do not exist. To reduce it, the following measures are taken:
- Reducing relative displacement by increasing friction forces. Increasing roughness, pressure or changing the configuration of parts. The first method is the most effective if one of the elements is a non-metal. Friction can also be increased by electroplating with copper, tin or cadmium.
- If the elimination of vibration is impossible, then the reverse method is required - reducing the friction force by using phosphate, lead or indium coatings, as well as introducing lubricants. As part of the latter, it is recommended to use corrosion inhibitor additives. This method transfers the slide to an intermediate environment.
- Increasing the hardness of one of the parts (heat treatment, mechanical hardening). This measure reduces the mutual adhesionmating surfaces and reduce wear.
Oil and grease based lubricants effectively reduce contact wear. Most often, their consistent types are used - substances that, at a temperature of 25 ° C, are a thick, ointment-like material. Phosphate and anodic metal coatings contribute to its retention on surfaces.
What are corrosion inhibitors
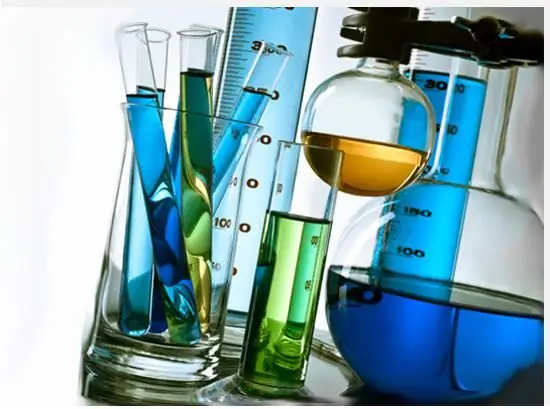
In case of material destruction by the type of fretting wear, contact type inhibitors are mainly used. They slow down corrosion in an aggressive environment, and the principle of their action is based on the formation of sparingly soluble compounds with metal ions.
Chromates, nitrites, benzoates, phosphates and other compounds are referred to as contact inhibitors. Filling the gap with plastic materials between the mating parts not only protects them from corrosion, but also promotes sealing. Contact inhibitors include compositions "Vital", SIM, M-1 and others. A list of inhibitors and recommendations for their use can be found in GOST 9.014-78.
Recommended:
Cattle fascioliasis: causes, symptoms, diagnosis, treatment and prevention
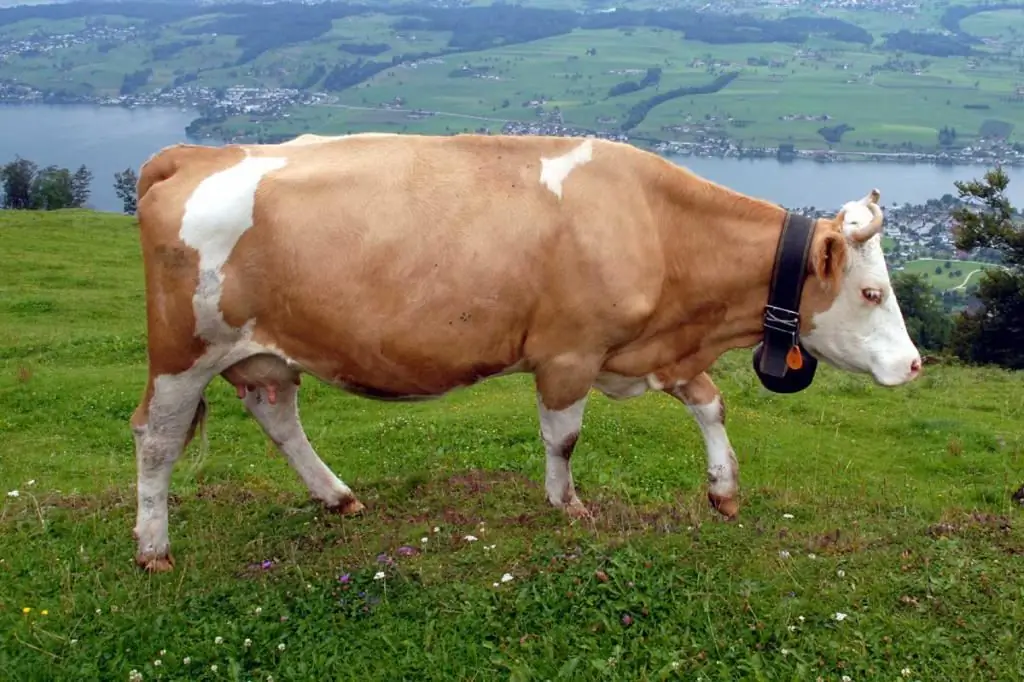
Cattle fascioliasis is a disease that can bring great material damage to the farm. In an infected cow, milk yield drops, weight decreases, and reproductive function is impaired. To protect livestock, it is necessary to carry out anthelmintic treatment in a timely manner and carefully approach the choice of pastures
Corrosion of aluminum and its alloys. Methods for combating and protecting aluminum from corrosion
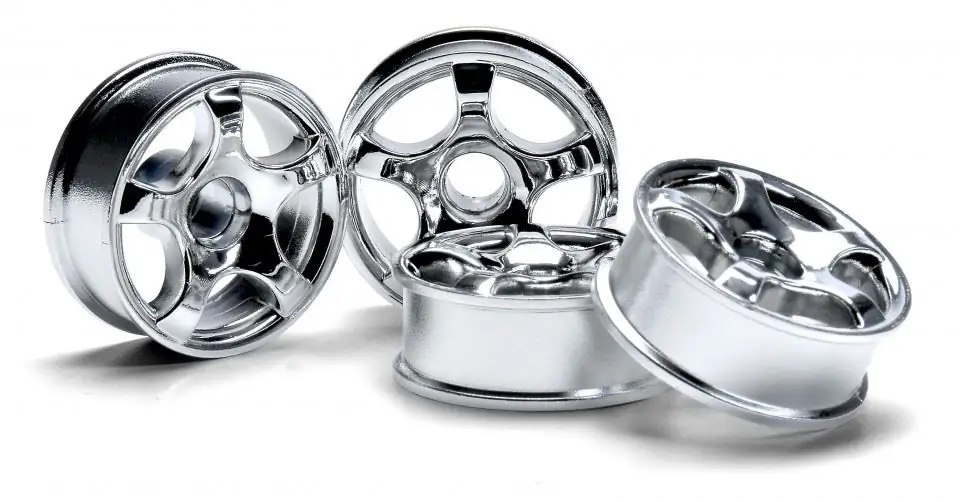
Aluminium, unlike iron and steel, is quite resistant to corrosion. This metal is protected from rust by a dense oxide film formed on its surface. However, in the case of destruction of the latter, the chemical activity of aluminum greatly increases
Pitting corrosion: causes. Methods for protecting metals from corrosion
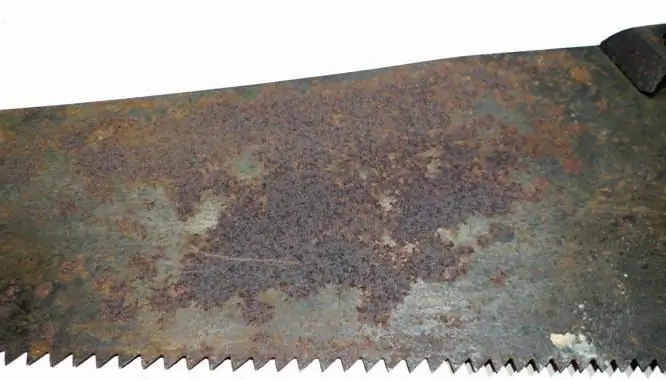
During the operation of metal products, they are exposed to various types of destructive effects, among which pitting corrosion stands out as the most dangerous and unpredictable
Corrosion of copper and its alloys: causes and solutions
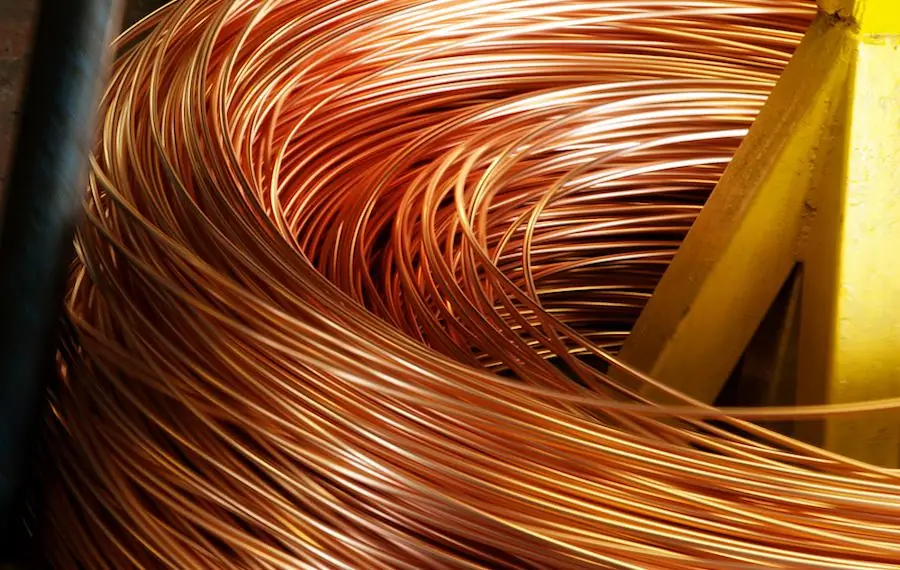
Copper and copper alloys have high electrical and thermal conductivity, can be machined, have good corrosion resistance, so they are actively used in many industries. But when it enters a certain environment, corrosion of copper and its alloys still manifests itself. What is it and how to protect products from damage, we will consider in this article
Corrosion and erosion of metals: causes and methods of protection
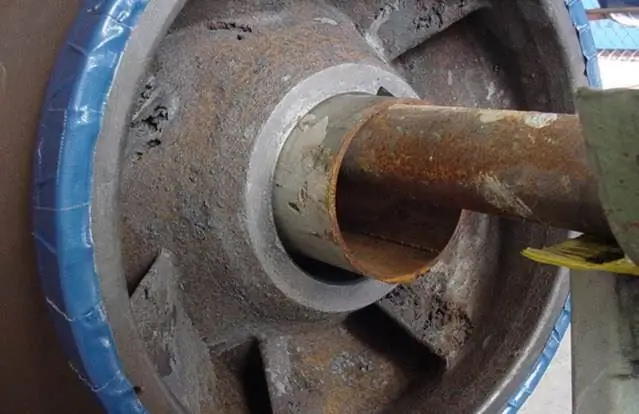
Chemical, mechanical and electrical external influences often occur in metal product operating environments. As a result, with improper maintenance of such elements, as well as ignoring safety standards, there may be risks of deformation and damage to structures and parts. This is due to the emerging processes of corrosion and erosion of metals, which in the long term contribute to the complete destruction of the structure of the product