2025 Author: Howard Calhoun | [email protected]. Last modified: 2025-01-24 13:10
Welding and surfacing technologies allow efficient restoration of metal parts, providing a high degree of reliability and durability of the product. This is confirmed by the practice of using these methods when performing repair operations in a variety of areas - from car repairs to the production of rolled metal. In the total amount of work on the repair of metal structures, the restoration of parts by welding and surfacing takes about 60-70%. The most common repair of steel cylinder blocks, motor shafts, crankcases, chain links, blades, etc.
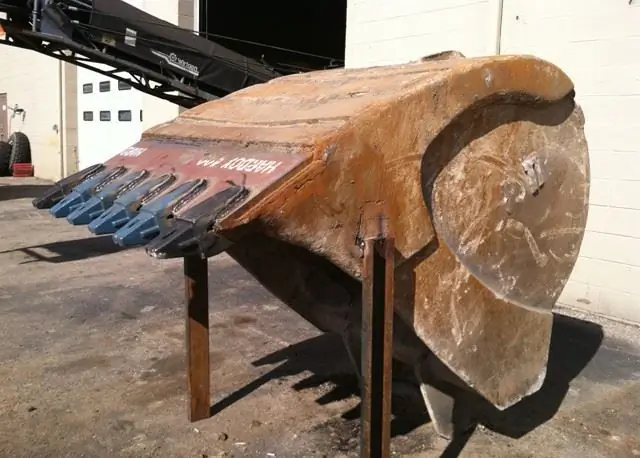
Welding and surfacing in repair and restoration work
Both methods are based on thermal treatment methods with different parametersoperation of the connected equipment. Welding is understood as the process of formation of interatomic bonds, which can be used to connect different elements of a part, close technological gaps and eliminate minor defects on the surface. The energy potential for the welding process is provided by general or local heating of the workpiece.
Typical operations of this kind include fixing additional or broken parts of plates, rims and bushings. In addition to the repair of products with simple geometric shapes, more complex restoration tasks are also possible, but as part of other technological operations. For example, thread restoration by welding will be supplemented by mechanical straightening and turning procedures. In addition, in such work, the requirements for overheating of an auxiliary tool such as dies, which are directly involved in thread correction, should be observed.
As for surfacing, this method involves applying an additional metal coating to the surface to be restored. The new technological layer can be useful when repairing worn parts or strengthening the surface in the area of friction.
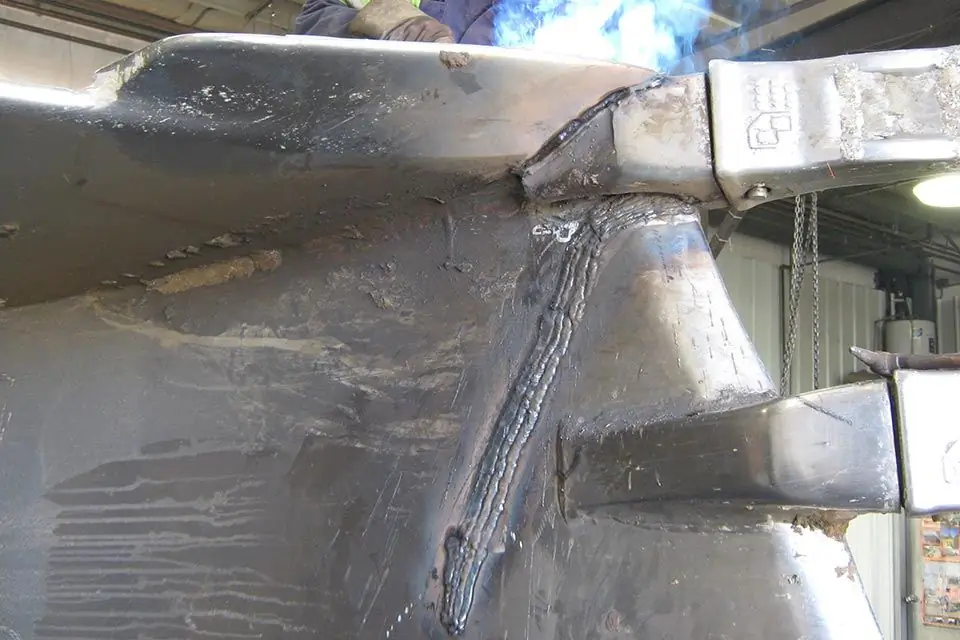
Applied equipment
When welding, a power source, equipment to hold the part and direct the arc are necessarily used. More often, a welding converter is used, which includes a motor with a DC generator from 70 to 800 A. Rectifiers with transformers can also be used.current and control gear. If we talk about consumables and auxiliary devices, then the restoration of parts by welding and surfacing is carried out with the connection of holding mouthpieces, electrodes and cooling systems. When surfacing, deforming heads with calipers and lifters are also used, which allow mounting on machine tools (lathes or screw-cutting). Special cutters are used to remove excess metal edges and layers.
Part preparation requirements
Both in welding and in the process of surfacing, the quality of the operation will be determined to a large extent by the initial state of the workpiece. The surfaces of the part must be cleaned of rust, scale, dirt and grease. Otherwise, the risk of retaining lack of penetration, cracks and slag inclusions increases. Particular attention should be paid to degreasing from factory and conservation oils. This procedure is performed in a hot solution, after which the product is washed and dried. Before restoring parts by welding, it is recommended to perform sandblasting, which improves the quality of the repair. For such tasks, abrasive processing methods are used with the connection of compressor equipment, grinding discs and cutters. Slight traces of corrosion damage can also be removed with manual metal brushes.
Which electrodes are used for recovery?
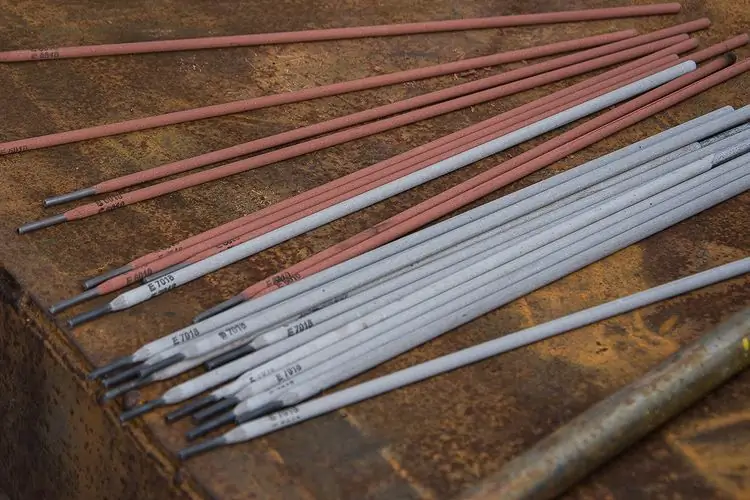
After preparing the main working equipment and the workpiece, you can proceed to the selection of electrodes. Selection depends on the type of metal, the nature of the defect andrequirements for the overlay layer. As a rule, in common cases of breaks and cracks, conventional welding electrodes with a tensile strength of about 4 MPa are used. To work with carbon steels, it is recommended to use consumables, the rods of which are made of wire grade Sv-08 with a thickness of 1.5-12 mm. Do not ignore the characteristics of the coating. A high stabilizing effect in the restoration of parts by welding and surfacing will be provided by chalk coating of the E-34 type electrode. It will contribute to a stable arc burning process, which will allow you to form a dense and even seam.
Non-standard electrode consumables like tape and tubular powder elements are also used today. Usually they are rolled metal strips up to 0.8 mm thick, the surface of which is filled with various powdered alloying mixtures based on ferromanganese, stalinite, etc. Such electrodes should be addressed if it is planned to endow the repaired area with additional operational properties.
Manual arc welding and surfacing method
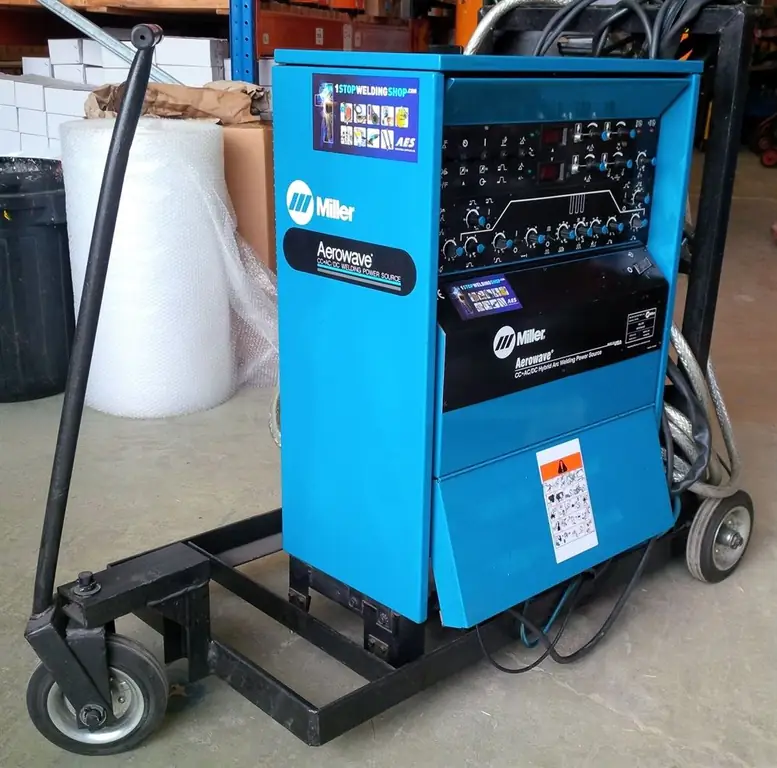
When repairing damaged welds, sealing cracks and sealing hermetic cases, you can use the manual method with graphite, carbon or tungsten electrodes. In the course of work, a bundle of rods with coating is taken and fastened with wire. The ends must be pre-welded and inserted into the prepared holder. During operation, the electrodes will form a so-called wandering arc with a wide field of action. Howthe larger the area of the damaged area, the larger the beam should be. The main difficulty of the welding process in this way lies in the need to connect a three-phase network, since the same surfacing with a beam of 5-6 electrodes must be carried out at an increased current. This method is used to repair parts made of alloyed and low-alloyed steels of medium and large thickness.
Automatic submerged arc welding method
The automatic process of surfacing is different in that the electrode supply with the movements of the arc itself along the working surface are completely mechanized. The flux, in turn, provides isolation of the target zone from the harmful effects of oxygen. The method is used to restore the surfaces of flat and cylindrical parts with a wear depth of up to 15 mm. As the size of the defect increases, several layers of hardfacing can be applied, but in this case it will be necessary to wait for the polymerization of each previous layer. This technology of restoring parts by welding and surfacing requires the connection of current sources in the form of a converter or rectifier with a screw-cutting lathe. A flux coating 1-4 mm thick is formed in the working area, after which an electrode wire with an arc is automatically guided. The main advantages of this method relative to manual welding include minimal loss of metal as a result of spatter. The manual method gives several times more cinders and waste.
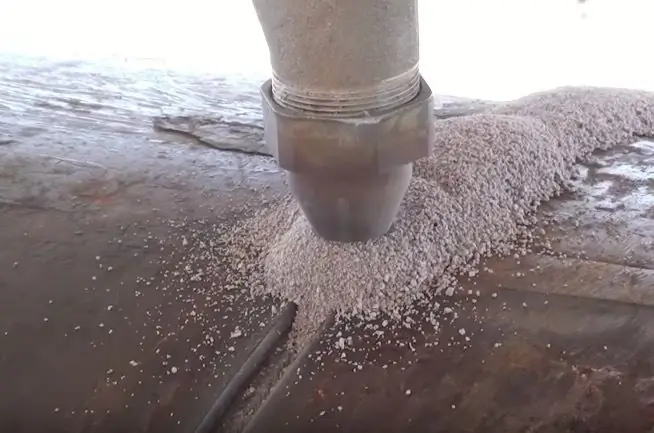
Vibro-arc surfacing method
In this case, fusible electrodes are used, which in the processburning arcs vibrate with short circuits. The operations of supplying and moving consumables are also automated. Despite the external complexity of the process, the method is quite simple and does not require the use of special equipment. Moreover, in the long run, one can expect the exclusion of deformation of the part with the preservation of hardness without heat treatment. However, there are also limitations. So, vibration methods for restoring parts by welding and surfacing are suitable for workpieces with a diameter of at least 8 mm or a thickness of 0.5 to 3.5 mm. Theoretically, vibro-arc surfacing can be performed in various protective environments with gas or flux, but in practice liquid insulation is more often used - for example, soda ash solution.
Welding and surfacing in gas protective environments
This method involves the preparation of a special cylinder with a compressed gas mixture. Argon and carbon dioxide gases can be used, directed to the welding zone under high pressure. The task of the mixture is also reduced to the protective function of isolating the workpiece from the negative effects of nitrogen and oxygen in the air. The highest quality joints by welding in gaseous media are obtained using tungsten electrodes with a separate input of filler materials into the working area. Surfacing is carried out under direct current with reverse polarity. The process can be mechanized if an electrode wire is used, but gas-electric burners are usually handled manually.
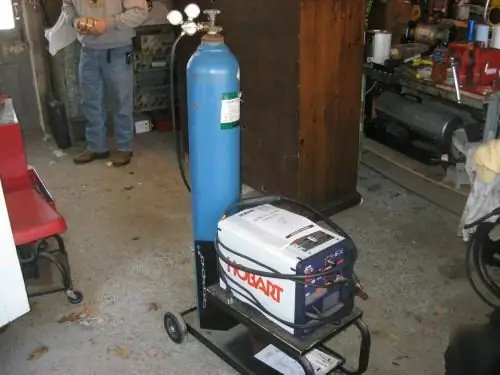
Semi-automatic welding and surfacing methods
Optimal method for working with aluminum and various non-ferrous alloys. Thanks to the flexible setting of equipment parameters and the possibility of using different protective environments, the operator can obtain a high-quality seam on a workpiece up to 12 mm thick at a low current strength. The semi-automatic method of restoring parts by welding is performed using tungsten electrodes with a thickness of 0.8-6 mm. The voltage in this case can vary from 20 to 25 V, and the current strength is within 120 A.
Alternative Pressure Recovery Technology
In addition to thermal methods of welding and surfacing, a wide group of contact or cold methods of changing the structure of metal blanks is also used. In particular, the restoration of parts by welding under pressure is carried out using mechanical units with punches. In the process of plastic deformation, a welded joint with certain parameters is formed at the contact points. The configuration of the deforming effect will depend on the characteristics of the punch and the compression technique.

Conclusion
Today, there are no more effective ways to correct defects in a metal structure than welding and surfacing. Another thing is that in these segments there is an active development of various methods for implementing the technology in practice. The most promising direction can be called the restoration of parts by welding and surfacing on automated equipment. Mechanization of repair operations increases the productivity of the process, itsergonomics and safety level for the welder. In parallel, methods of high-precision argon-arc welding with the connection of gas protective environments are also being developed. It is too early to talk about full automation in this direction, but in terms of the quality of the result, this area is advanced.
Recommended:
Sheet stamping of parts: technologies and features of the process
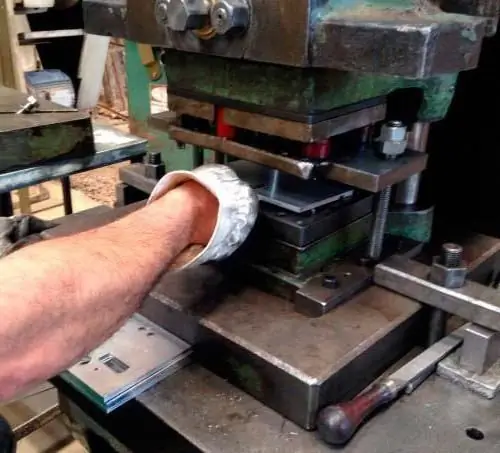
The article is devoted to sheet metal stamping. The features of this process, the advantages of the technology, the equipment used, etc. are considered
Inline production is Concept, definition, methods of organization and technological process
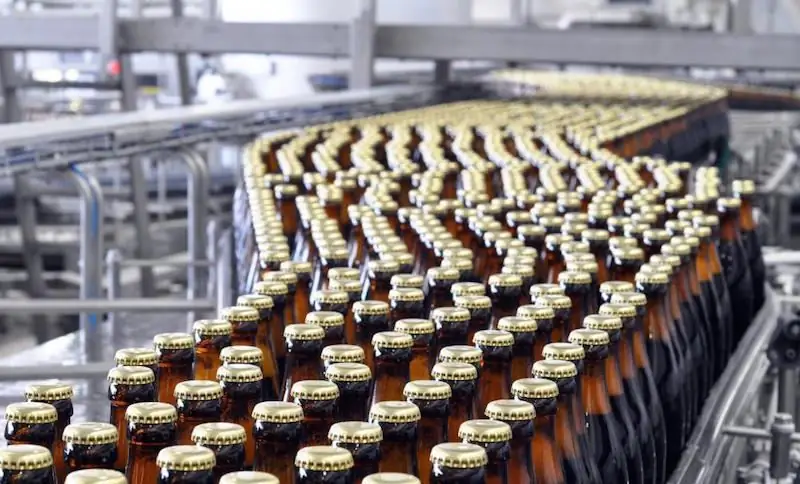
The production process is a complex technological action that can be organized in different ways and means. The work of an enterprise in the conditions of in-line production of products is today considered the most efficient, but at the same time demanding in terms of labor, organizational and material costs. In a general sense, in-line production is a format of production activity in which the principles of rhythm and repeatability of operations come to the fore
Chrome plating parts. Chrome parts in Moscow. Chrome parts in St. Petersburg
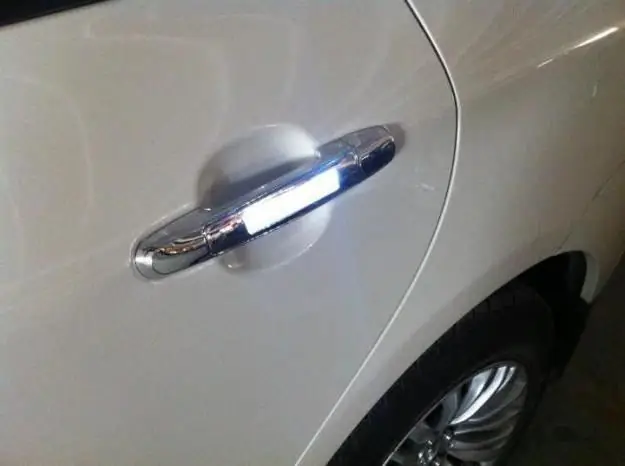
Chrome plating of parts is an opportunity to give them a new life and make them more reliable and of high quality in operation
Butt welding: equipment, methods and process technology
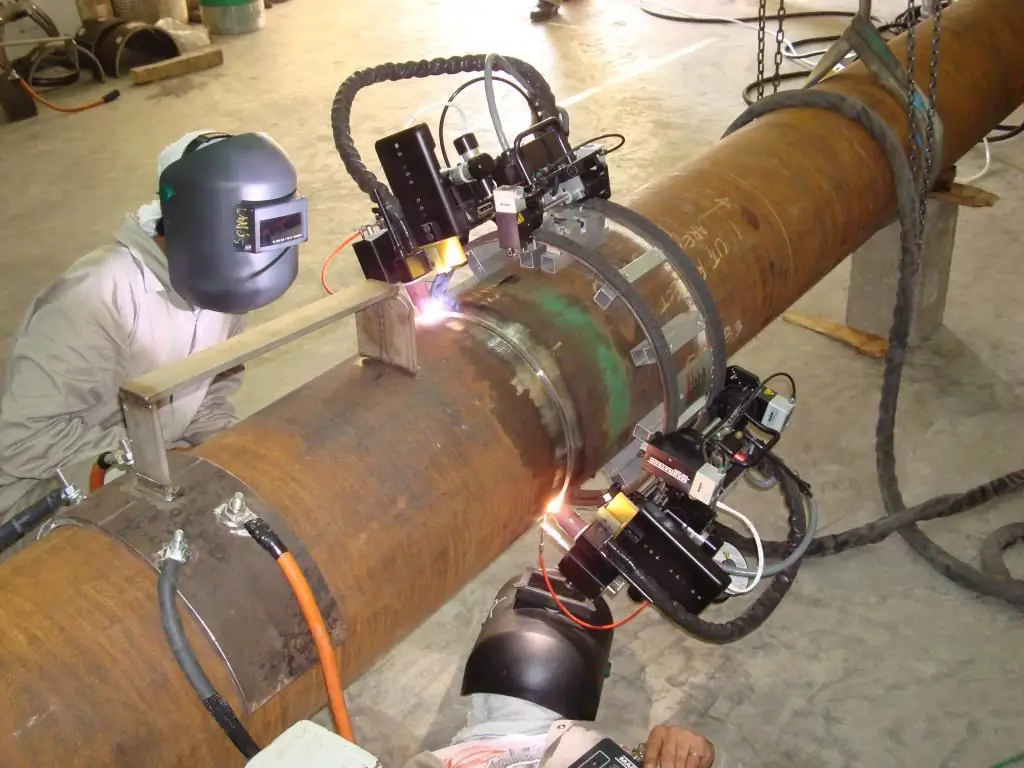
Features of flash butt welding. Types of butt welding joints, as well as equipment, methods and technology for carrying out the butt welding process. Welding seam defects arising from flash butt welding, as well as the reasons for their formation
Plasma surfacing: equipment and process technology
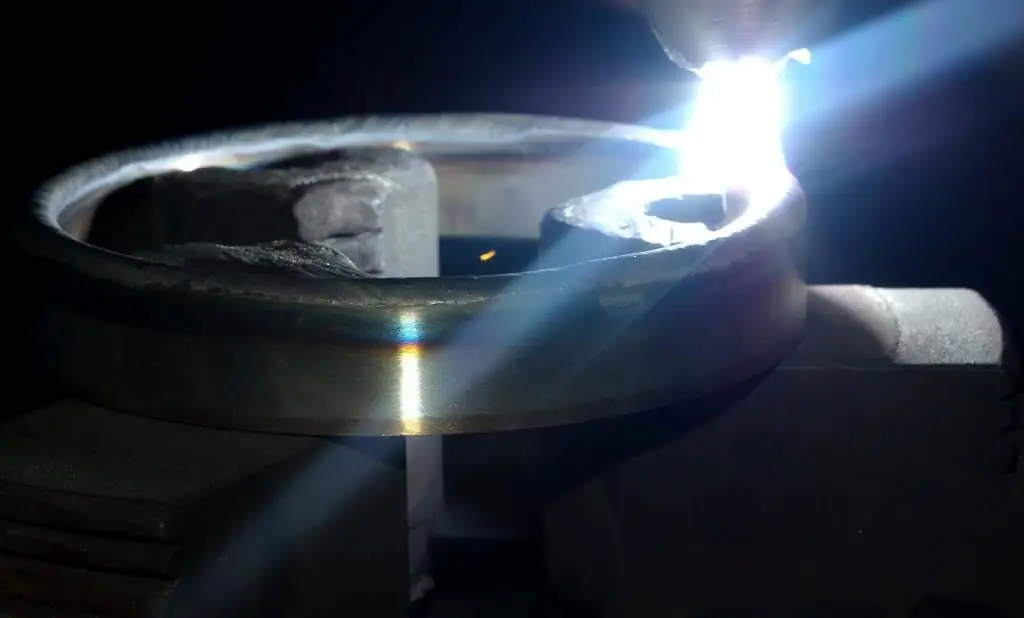
The efficiency and problems of plasma surfacing are extremely acute for material engineers. Thanks to this technology, it is possible not only to significantly increase the service life and reliability of highly loaded parts and assemblies, but also to restore seemingly 100% worn and destroyed products