2025 Author: Howard Calhoun | [email protected]. Last modified: 2025-01-24 13:10
The production process is a complex technological action that can be organized in different ways and means. The work of an enterprise in the conditions of in-line production of products is today considered the most efficient, but at the same time demanding in terms of labor, organizational and material costs. In a general sense, in-line production is a format of production activity in which the principles of rhythm and repeatability of technological coordinated operations come to the fore. Further, the essence of this process, its features, methods of organization, etc. will be considered in more detail.
The concept of the production process
At the heart of any production is the organization model of the main, service and auxiliary processes, thanks to which the work of the enterprise is carried out,aimed at creating certain products. Regarding the organizational model, the tools used (machines, conveyors, tools) can be considered as objects of the organization that are in direct connection with the objects of production, that is, the manufactured products.
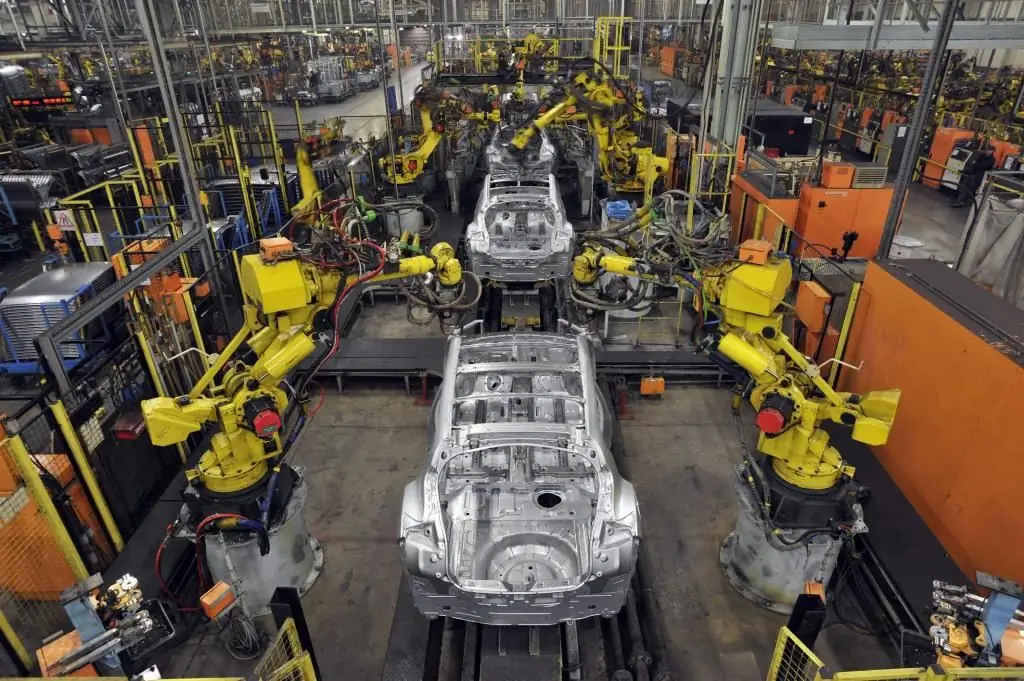
To a large extent, the function of linking between different elements of production within the organizational model is still performed by a person. As a maximum, he is directly involved in the manufacturing process, at least he manages the equipment that implements technological operations.
Among the features of the in-line production method, emphasis is placed on the automation of work activities with minimal human participation. The possibilities of organizing uninterrupted automated production can be realized for the most part in the main technological processes related to the material transformation of conditional procurement into the subject of commodity relations. For example, the manufacture of furniture at the stages of lumber processing is the main workflow of a furniture factory, which in large enterprises is now performed on machine tools under numerical control. And vice versa, service and auxiliary processes of production activities are carried out mainly by the working personnel directly, since most of these actions require the adoption of complex non-standard decisions.
The essence of in-line production
The production activity model in flow form is based on rhythmic repetitiona certain set of technological operations that are performed in the relevant workshops at the workplace. Coordination between individual operations can occur at different technical and organizational levels with division in time and space. In other words, in-line production is a pre-thought-out algorithm of actions aimed at manufacturing the target products of an enterprise.
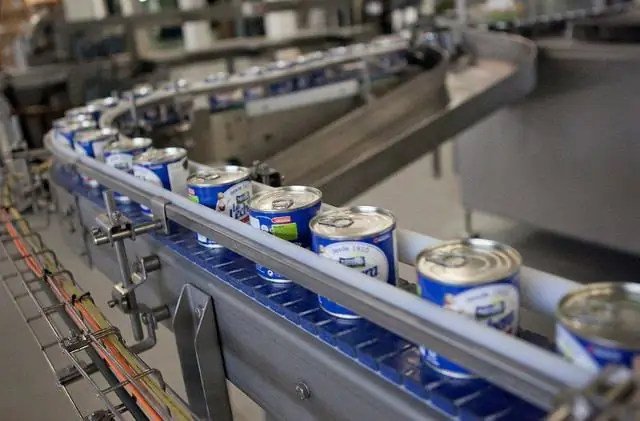
For a clearer understanding of the form of production under consideration, we can cite as an example the principle of a non-flow model. In this case, the organization of production can be used both in a single and in a serial format for manufacturing products. The difference lies in the fact that the flow technology of production is based on the relationship of several groups of work operations. In the non-flow production model, shop sections are organized according to the principle of performing the same type and rhythmic, but not coordinated processes. Production occurs intermittently between operations, and processed items and blanks are sent along complex routes to the next levels of production without interfacing.
Features of in-line production
Among the distinctive features of the technological organization of in-line production of products, the following can be distinguished:
- Workplaces serve operations performed in relation to the same items with similar technical and structural characteristics. In more complex models, the work of in-line production allows a change in the processing format in a certain rangemodes. That is, the conveyor line within the framework of even one technological process can be reoriented to different groups of processed items.
- The configuration of the location of workplaces is selected depending on the production logistics. A clear hierarchy of sequences is observed when performing technological operations.
- The transfer of an item from one working unit to another can be carried out both in piece format and in batches, but in any case, the general rhythm of production should be maintained whenever possible.
- The main and part of the auxiliary operations are performed in a mechanized or automated mode of mass production. This makes it possible to withstand the high pace of running processes, but does not exclude the possibility of a technological break, the permissible parameters of which are calculated in advance in the algorithm of the current model.
Principles of mass production
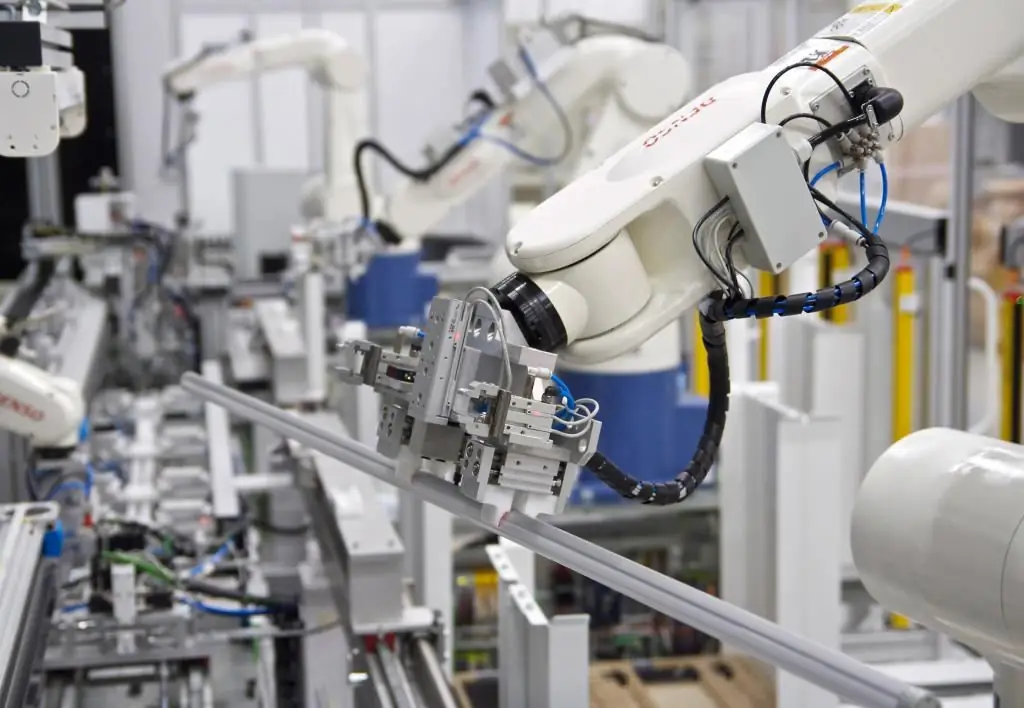
It is possible to achieve sufficient efficiency of production “on line” only if a number of principles of the technological organization of the workflow are observed, including:
- Principle of continuity. Minimizes the dependence between individual production lines on a time basis. For example, the pace of work of one workplace in this case cannot cause cyclical delays in other areas of production.
- The principle of parallelism. Finished products and blanks with the in-line production method move along technological routes in parallel, which alsocontributes to the principle of continuity without delay.
- The principle of direct flow. Both workplaces and equipment are placed in a clear order, corresponding to the technological process of manufacturing products.
- The principle of specialization. Separation of production functions between separate groups of production lines is provided. That is, the universality of jobs is excluded from the point of view of the possibility of performing various operations.
- The principle of rhythm. As part of the functioning of one workplace, cyclical operations are ensured not only in the production of one product, but also in the mode of manufacturing batches of products. Thanks to this principle, serial mass production is organized with a planned approach to the mass production of the target product.
Types of production lines
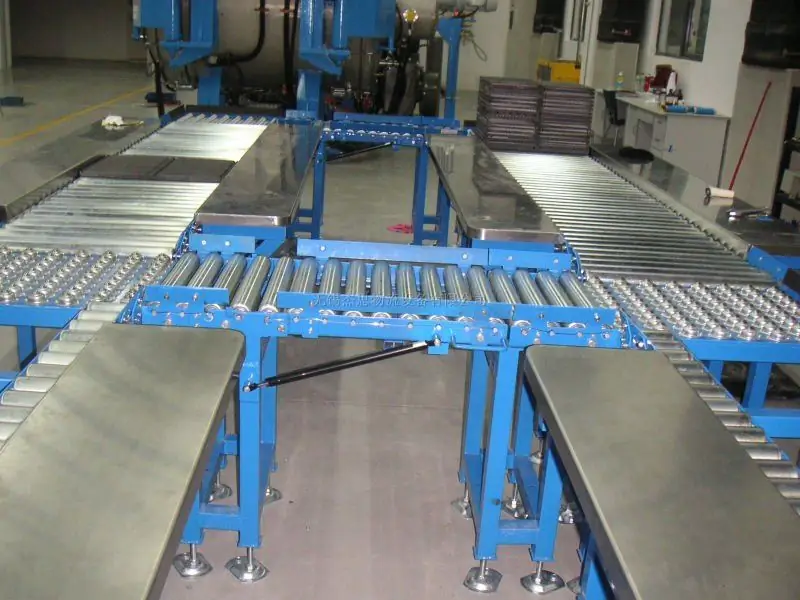
Organization of production based on production lines may include different groups of work units. In relation to them, several classification features are distinguished:
- According to the degree of specialization. The line can be one- and multi-subject. In the first case, it is supposed to perform operations with one type of product during a certain technological period. Multi-object lines are usually used in mass production processes with insufficient capacity utilization for the processing of one product. Accordingly, parallel execution of additional processes with a different processing format is organized.
- By the way of maintaining the working pace. Production lines can work infree rhythm or with a clear time schedule. According to the principle of continuity, in order to reduce the cost of production, a continuous flow regulated rhythm is more often used. A free pace of production is established in cases where the enterprise, due to the instability of the connection of capacities or raw materials, cannot maintain work processes in a stable mode.
- According to the type of vehicles used. Conveyors along which manufactured items move can operate continuously or discretely. The movement mode depends on the pace, power load and other characteristics of the production operations.
- According to the degree of mechanization. Mostly in the classification of mass in-line production, we are talking about the level of automation. The same conveyors and processing equipment can operate under the control of automatic and semi-automatic controllers with a centralized, dispatcher or synchronized principle of operation.
Production line equipment
The technical basis of in-line production is formed by conveyors of various types - for example, plate, belt, overhead and chain. They ensure the movement of objects from one work node to another in a given rhythm. Workplaces are supplied with technological equipment that performs the tasks of processing blanks, assembling parts and consumables. These can be machine tools, as well as devices for providing thermal, chemical and mechanical effects. In the aggregate-flow production, a special role is assigned to auxiliary transportthe means by which the functions of the link between different work nodes are performed. In particular, it can be ramps, roller tables, telphers, descents, etc. This equipment also operates according to different principles - with movement along rails, in mobile or free movement mode under the direct control of the operator.
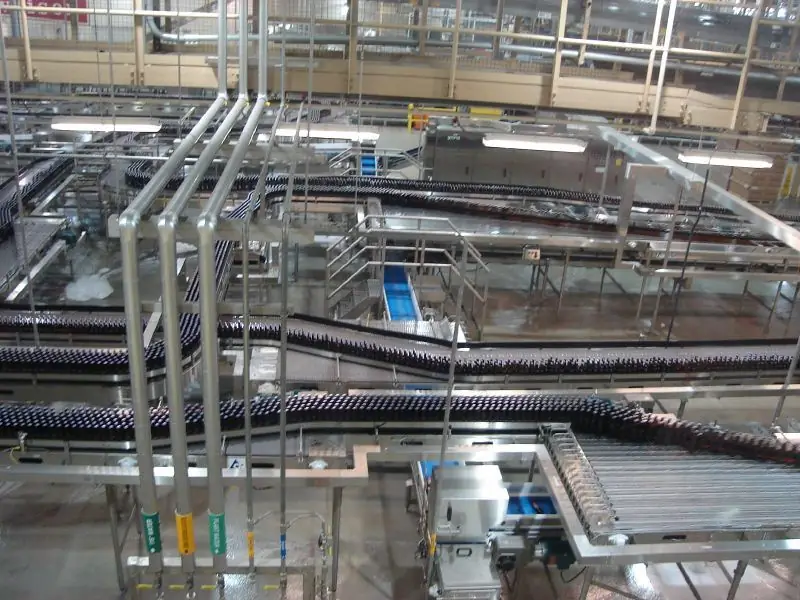
Organization of a continuous production line
Technologically, the most advanced form of production, in which the items of manufacture are transferred from one work unit to another without delay, and the time periods for performing one operation correspond to the general cycle of work. For example, in this mode, the time for the product to pass through one stage of processing corresponds to the time spent on the previous stages of the operation, which practically eliminates pauses between the arrival of parts at the working areas. A sequence of parallel operating and output units is observed within a given cycle of in-line production. The organization of such a mode is quite demanding on the primary calculations of the addressing system. Usually, a production schedule is drawn up for it, with a clear definition of the cycle of operation of the conveyor line, its capacity and speed.
Organization of discontinuous production
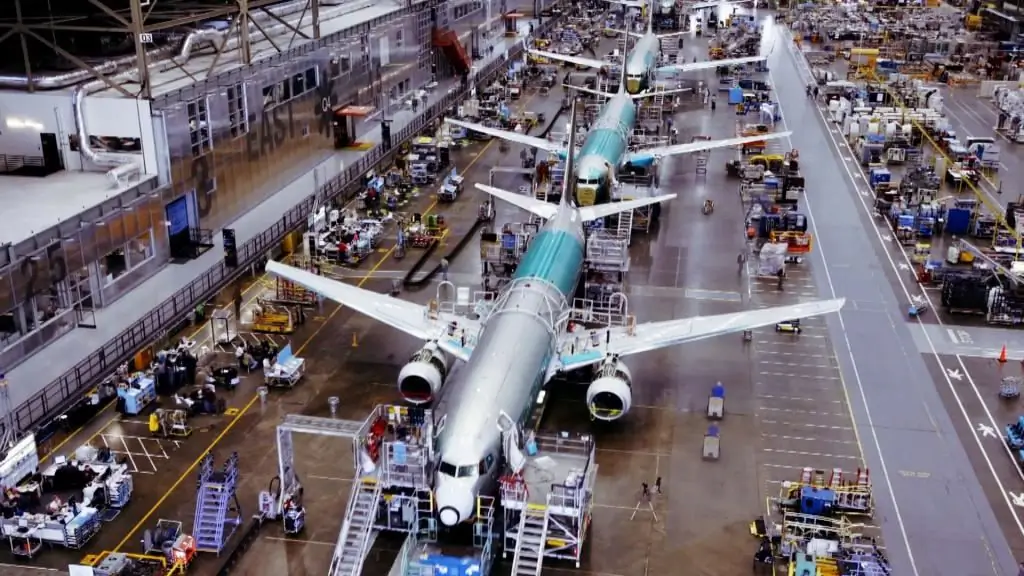
If, for one reason or another, it is impossible to maintain the general cycle of technological operations in production, then an allowance is made for possible pauses and breaks. ATotherwise, the risk of receiving defective products or disrupting supply chains increases. In the organization of in-line production of this type, due to the non-multiplicity or inequality of operations to the general rhythm, the presence of inter-operational turnover reserves is provided. This is a kind of discontinuity factor, expressed in terms of downtime of equipment in a particular area. In technical terms, the organization of discontinuous production is distinguished by the presence of distribution conveyors, thanks to which the necessary intermediate production processes are optimized, which determine the very existence of backlogs. As a rule, discontinuous production lines are organized at large enterprises with large distances between individual processing nodes.
Features of multi-subject continuous production lines
The main difference of this configuration of the production line is its wide specialization in the range of manufactured products. This characteristic determines the complexity of the organization of production with the need to ensure interoperational backlogs. At the same time, each workplace can produce several different parts, but also having related design parameters. Methods for alternating operations and parts may vary. For example, group (consecutive) and sequential-batch principles of alternation are distinguished, which are selected based on the current tasks of in-line production. The method of organizing multi-object lines is also characterized by large cycles of performing operations in a stream, which provides additional advantages forsynchronization of technological processes.
Conclusion
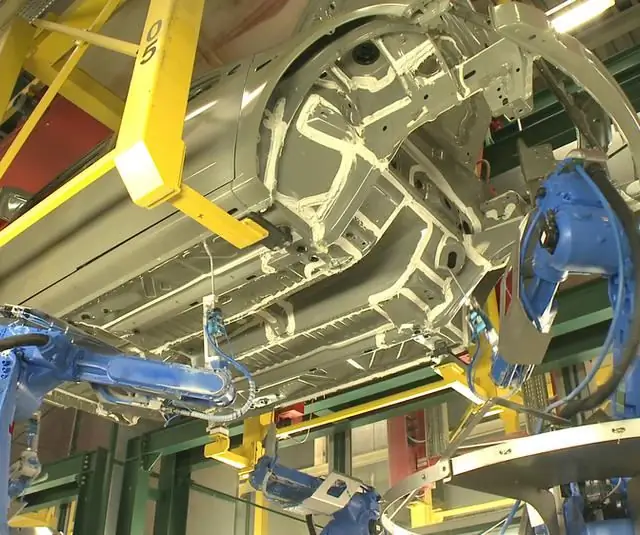
Serial production as such is an economically viable form of work for most large industrial enterprises. But at the same time, high financial and material and technical costs are assumed, without optimization of which production activities will be inefficient. In this respect, in-line production is the optimal format for mass production of complex products that require the use of many technological operations. Another thing is that for the organization of such production lines, special conditions must initially be met. Among them, one can note ample opportunities for deepening the specialization of individual jobs within the enterprise and a high degree of unification of the technical and structural parameters of manufactured products.
Recommended:
Essence and concept of organization. Form of ownership of the organization. Organization life cycle
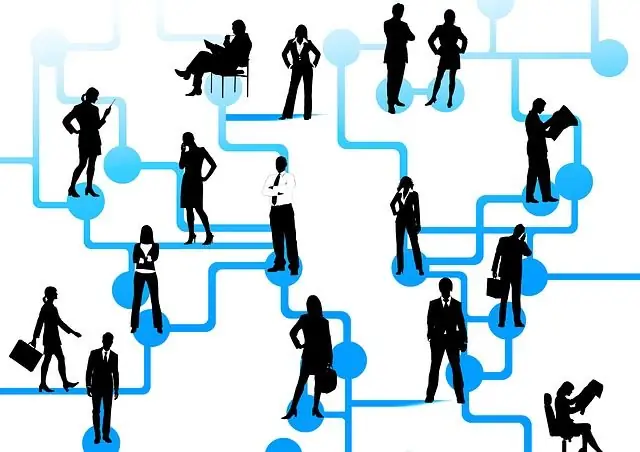
Human society consists of many organizations that can be called associations of people pursuing certain goals. They have a number of differences. However, they all have a number of common characteristics. The essence and concept of organization will be discussed in the article
Production of gas blocks: technological process, materials and equipment
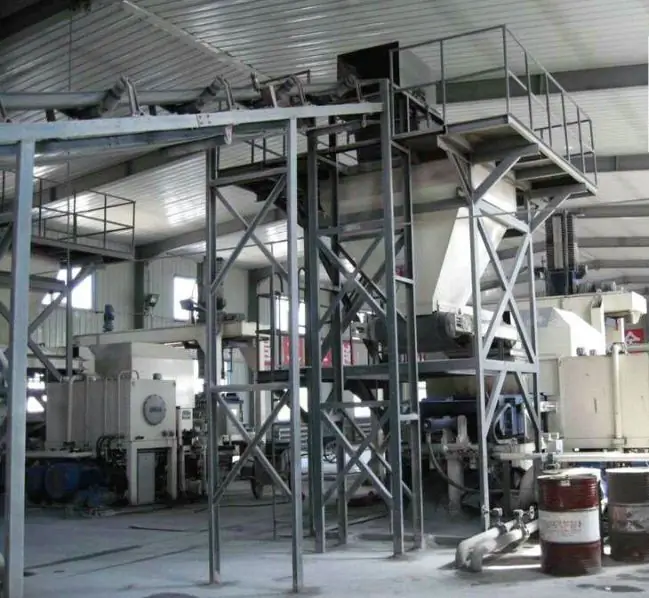
Today, there are many building materials that are popular. One of the innovations is the production of gas blocks, which belong to cellular concrete. Of these, it is profitable not only to build a private house, but also to produce for sale
Woodworking production: characteristics and technological process
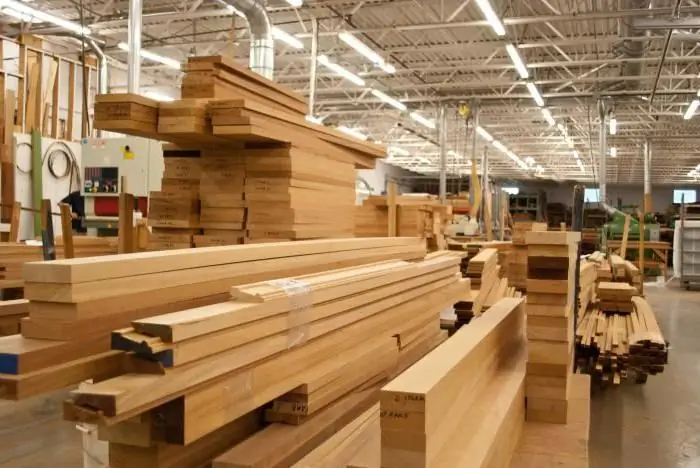
Modern woodworking production involves the use of high-tech equipment to produce high-quality lumber
Flow methods of production organization: parameters, characteristics and standards. The need for this method in production
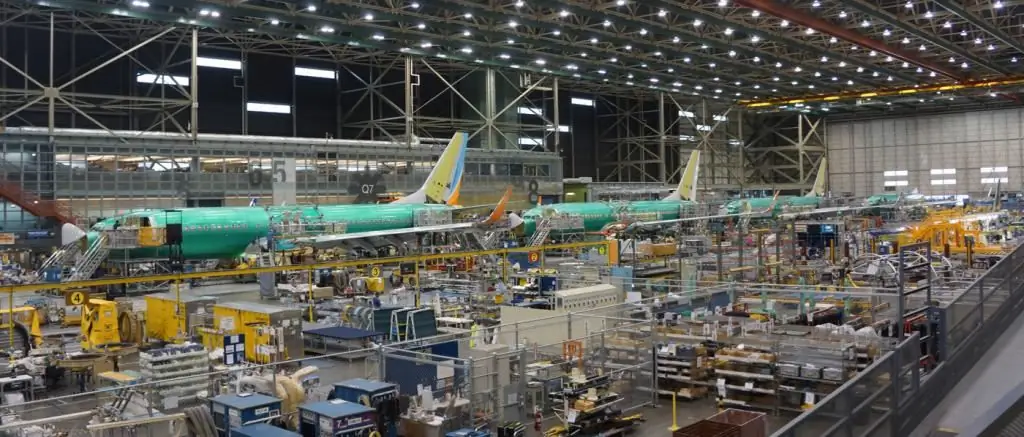
Today, in-line production is the most progressive form of organization of the production system. Optimal speed of work, minimum labor intensity and maximum quality of production - this is not a complete list of the advantages of the method under consideration
Restoration of parts by welding and surfacing: methods and methods of restoration, features, technological process
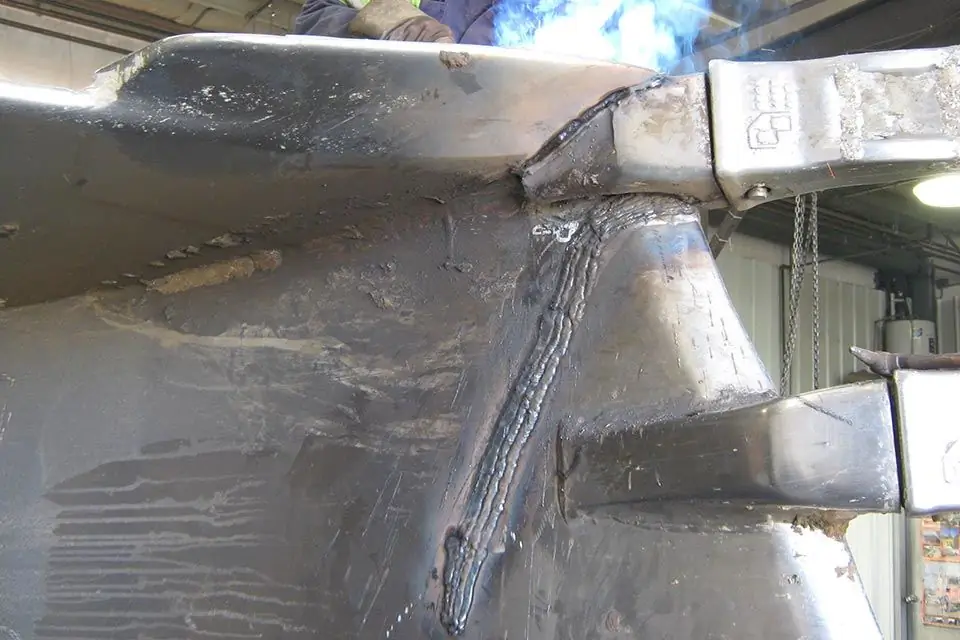
Welding and surfacing technologies allow efficient restoration of metal parts, providing a high degree of reliability and durability of the product. This is confirmed by the practice of using these methods when performing repair operations in a variety of areas - from car repairs to the production of rolled metal. In the total amount of work on the repair of metal structures, the restoration of parts by welding and surfacing takes about 60-70%