2025 Author: Howard Calhoun | [email protected]. Last modified: 2025-01-24 13:10
The efficiency and problems of plasma surfacing are extremely acute for material engineers. Thanks to this technology, it is possible not only to significantly increase the service life and reliability of highly loaded parts and assemblies, but also to restore, it would seem, one hundred percent worn and destroyed products.
The introduction of plasma surfacing into the technological process significantly increases the competitiveness of engineering products. The process is not fundamentally new and has been used for a long time. But it is constantly improving and expanding its technological capabilities.
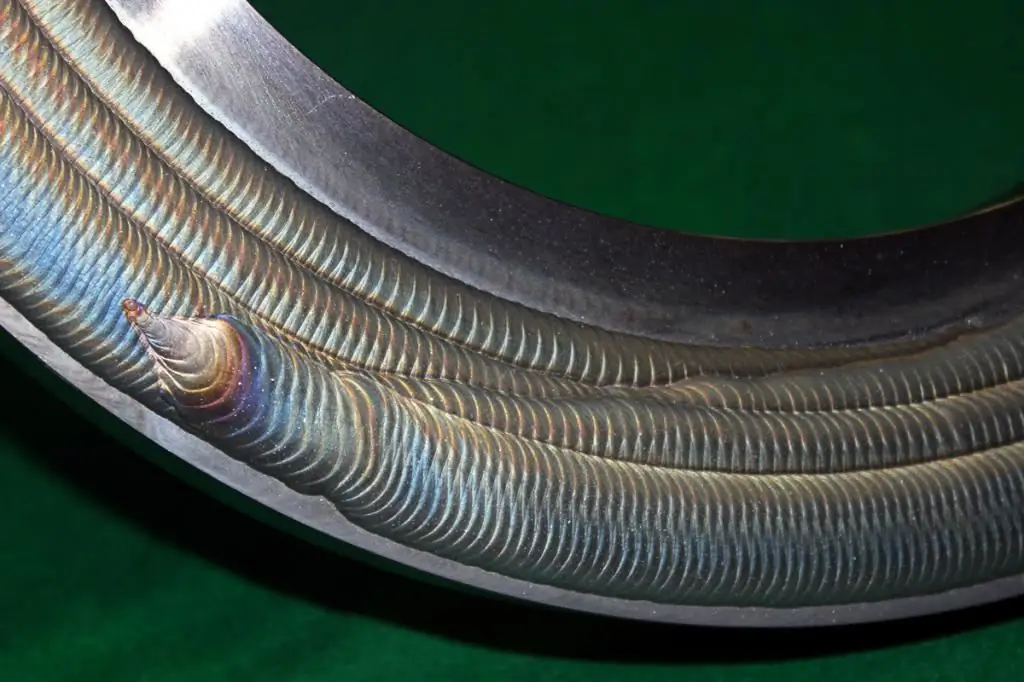
General provisions
Plasma is an ionized gas. It is reliably known that plasma can be obtained by various methods as a result of electrical, thermal or mechanical effects on gas molecules. For its formation, it is necessary to tear off negatively charged electrons from positive atoms.
In some sources you can findinformation that plasma is the fourth state of aggregation of matter along with solid, liquid and gaseous. Ionized gas has a number of useful properties and is used in many branches of science and technology: plasma surfacing of metals and alloys in order to restore and harden heavily loaded products that experience cyclic loads, ion-plasma nitriding in a glow discharge for diffusion saturation and hardening of surfaces of parts, for the implementation of chemical processes. pickling (used in electronics manufacturing technology).
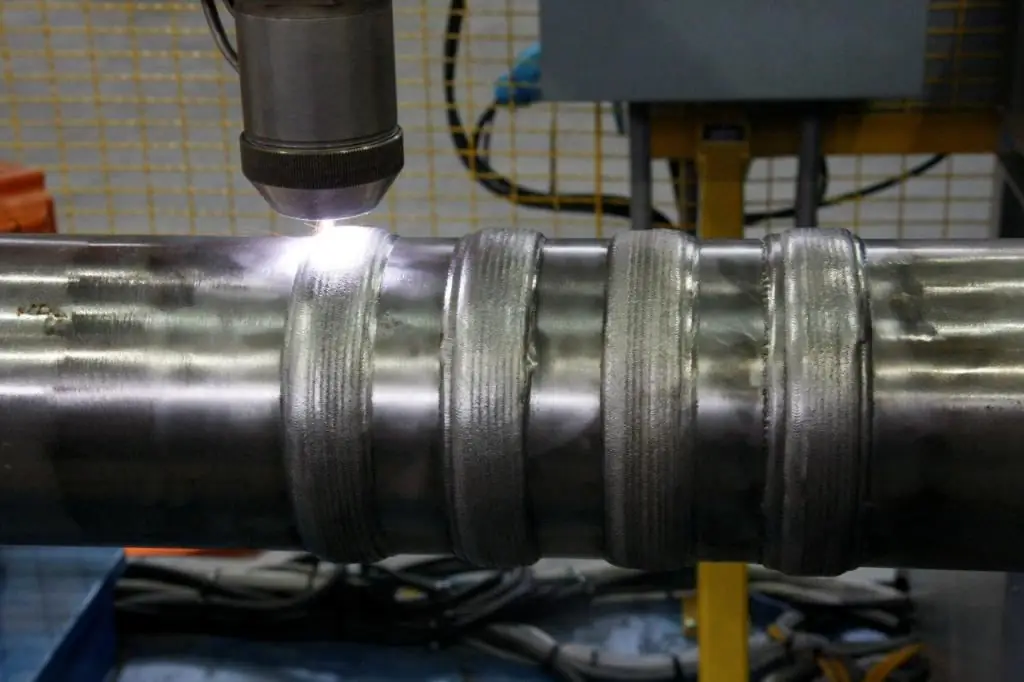
Preparation for work
Before you start surfacing, you need to set up the equipment. In accordance with the reference data, it is necessary to select and set the correct angle of inclination of the burner nozzle to the surface of the product, align the distance from the end of the burner to the part (it should be from 5 to 8 millimeters) and insert the wire (if wire material is surfacing).
If surfacing will be carried out by fluctuations of the nozzle in transverse directions, then it is necessary to set the head in such a way that the weld is exactly in the middle between the extreme points of the fluctuation amplitudes of the head. It is also necessary to adjust the mechanism that sets the frequency and magnitude of oscillatory movements of the head.
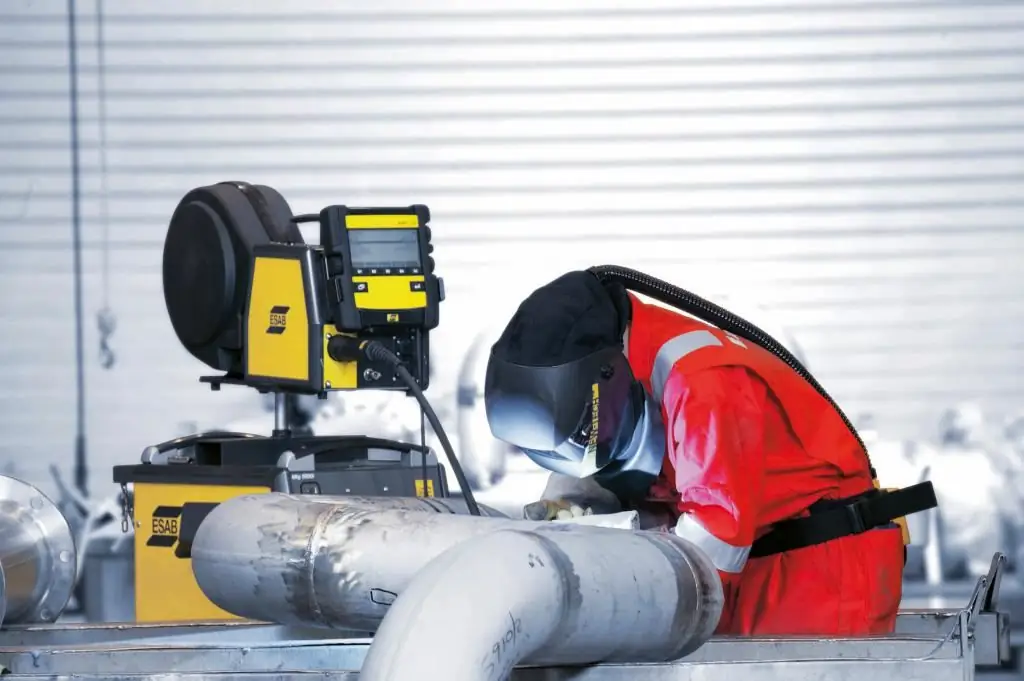
Plasma arc surfacing technology
The surfacing process is quite simple and can be successfully performed by any experienced welder. However, he requiresperformer of maximum concentration and attention. Otherwise, you can easily ruin the workpiece.
A powerful arc discharge is used to ionize the working gas. The detachment of negative electrons from positively charged atoms is carried out due to the thermal effect of the electric arc on the jet of the working gas mixture. However, under a number of conditions, the flow is possible not only under the influence of thermal ionization, but also due to the influence of a powerful electric field.
Gas is supplied under pressure of 20-25 atmospheres. For its ionization, a voltage of 120-160 volts is required with a current of about 500 amperes. Positively charged ions are captured by the magnetic field and rush to the cathode. The speed and kinetic energy of elementary particles is so great that when they collide with metal, they are able to give it a huge temperature - from +10 … +18,000 degrees Celsius. In this case, the ions move at a speed of up to 15 kilometers per second (!). The plasma surfacing unit is equipped with a special device called a "plasma torch". It is this node that is responsible for the ionization of the gas and obtaining a directed flow of elementary particles.
The power of the arc should be such as to prevent melting of the base material. At the same time, the product temperature should be as high as possible in order to activate diffusion processes. Thus, the temperature should approach the liquidus line on the iron-cementite diagram.
Fine powder of a special composition or electrode wire is fed into a jet of high-temperature plasma, in which the materialmelts. In the liquid state, the surfacing falls on the hardened surface.
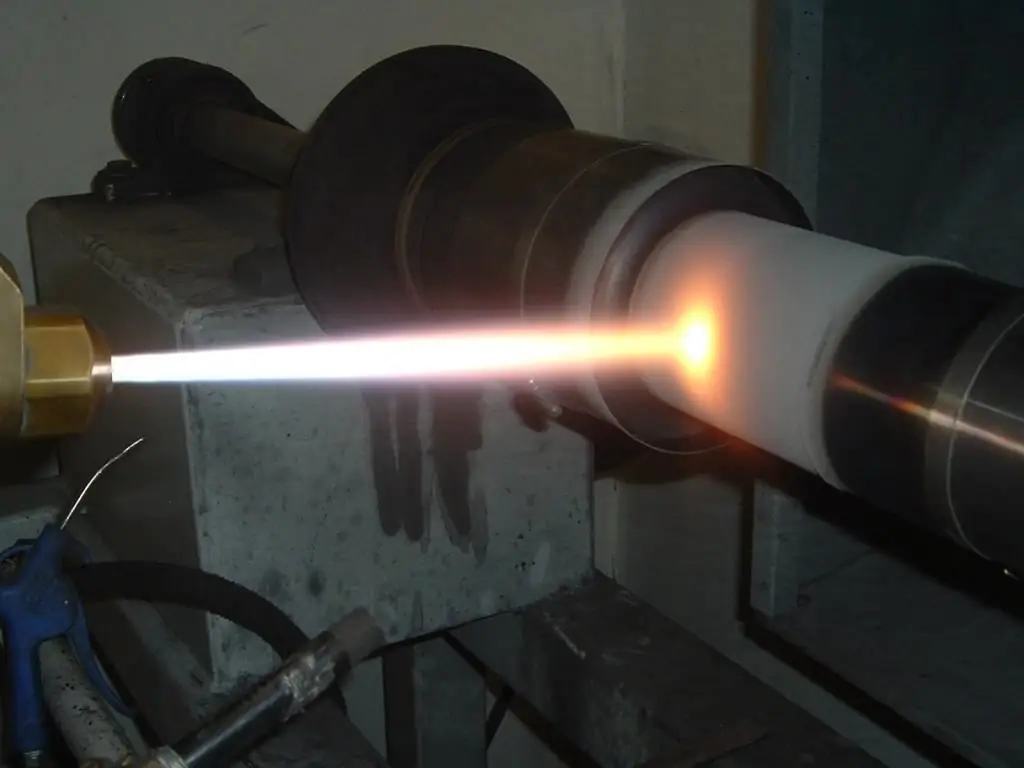
Plasma spraying
In order to implement plasma spraying, it is necessary to significantly increase the plasma flow rate. This can be achieved by adjusting the voltage and current. Parameters are selected empirically.
Materials for plasma spraying are refractory metals and chemical compounds: tungsten, tantalum, titanium, borides, silicides, magnesium oxide and aluminum oxide.
The indisputable advantage of spraying compared to welding is the ability to obtain the thinnest layers, on the order of several micrometers.
This technology is used for hardening cutting turning and milling replaceable carbide inserts, as well as taps, drills, countersinks, reamers and other tools.
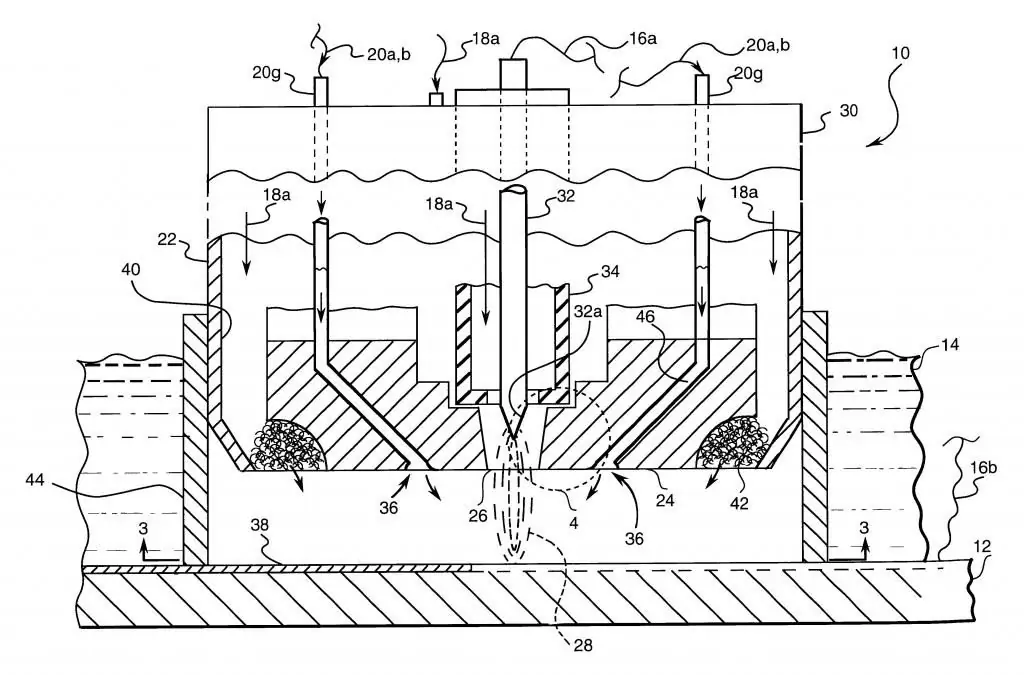
Obtaining an open plasma jet
In this case, the workpiece itself acts as an anode, on which the material is deposited by plasma. The obvious drawback of this processing method is the heating of the surface and the entire volume of the part, which can lead to structural transformations and undesirable consequences: softening, increased brittleness, and so on.
Closed plasma jet
In this case, the gas burner, more precisely, its nozzle, acts as an anode. This method is used for plasma-powder surfacing in order to restore and improve the performance of parts andmachine nodes. This technology has gained particular popularity in the field of agricultural engineering.
Advantages of Plasma Hardfacing
One of the main advantages is the concentration of thermal energy in a small area, which reduces the effect of temperature on the original structure of the material.
The process is well manageable. If desired, and with appropriate equipment settings, the surfacing layer can vary from a few tenths of a millimeter to two millimeters. The possibility of obtaining a controlled layer is especially relevant at the moment, as it allows to significantly increase the economic efficiency of processing and obtain optimal properties (hardness, corrosion resistance, wear resistance and many others) of the surfaces of steel products.
Another no less important advantage is the ability to carry out plasma welding and surfacing of a variety of materials: copper, brass, bronze, precious metals, as well as non-metals. Traditional welding methods are far from always able to do this.
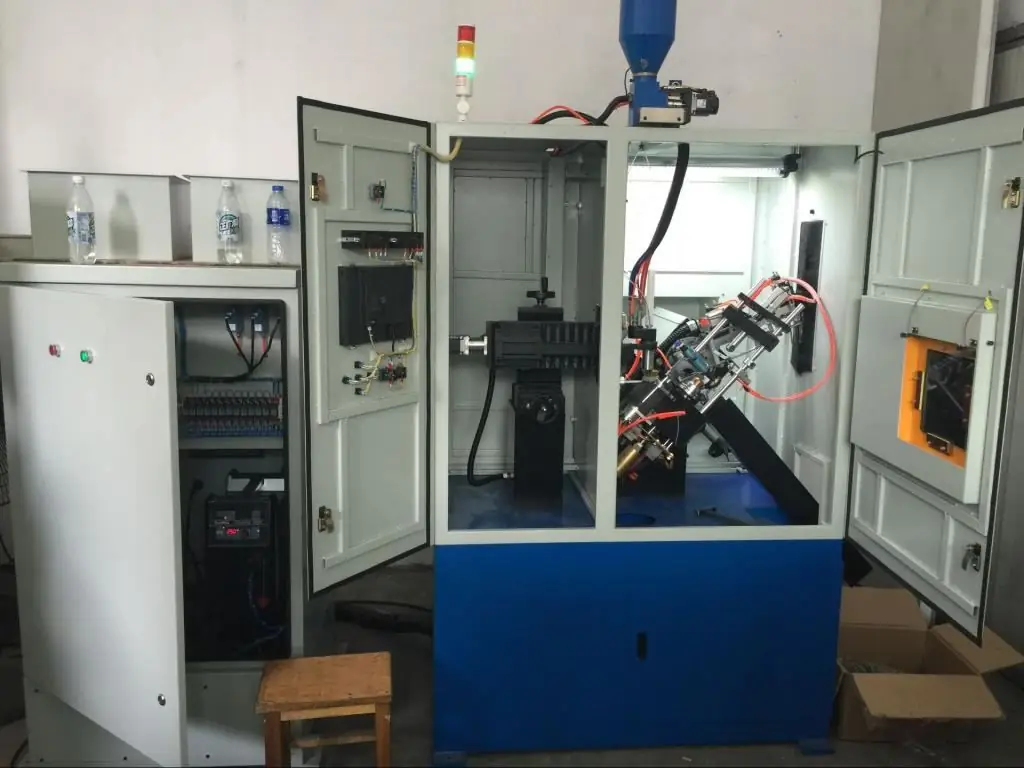
Hardfacing equipment
Installation for plasma-powder surfacing includes a choke, oscillator, plasma torch and power supplies. Also, it should be equipped with a device for automatically feeding metal powder granules into the working area and a cooling system with constant water circulation.
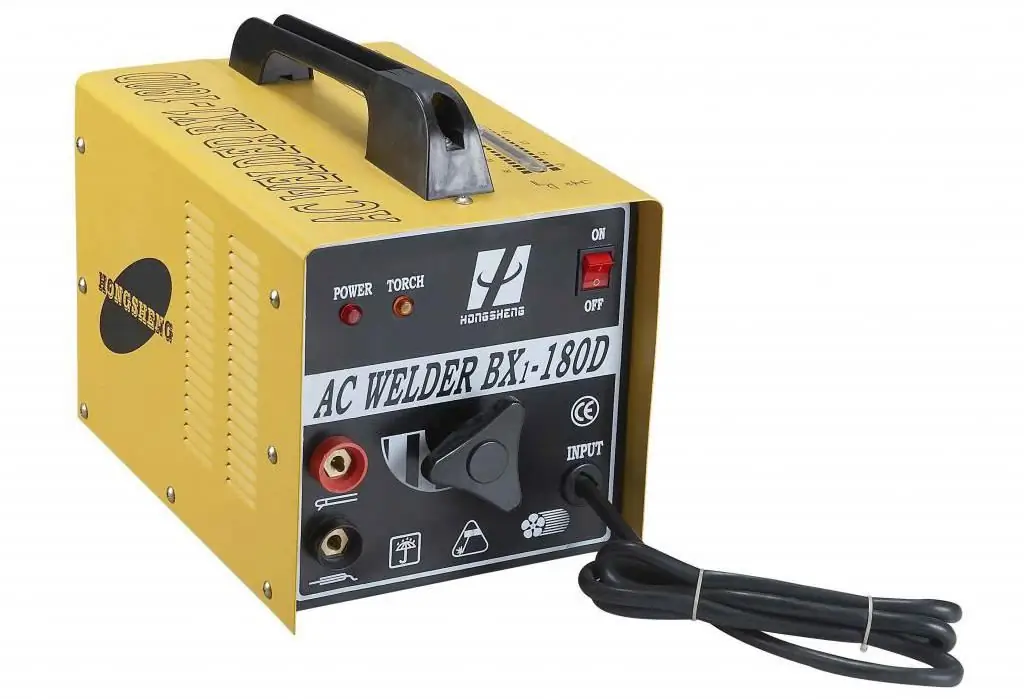
Power sources for plasma hardfacing must meet stringent requirementsconstancy and reliability. Welding transformers do the best job with this role.
When surfacing powder materials on a metal surface, the so-called combined arc is used. Both open and closed plasma jets are used simultaneously. By adjusting the power of these arcs, it is possible to change the depth of penetration of the workpiece. Under optimal conditions, warpage of products will not appear. This is important in the manufacture of parts and assemblies of precision engineering.
Material feeder
Metal powder is dosed by a special device and fed into the melting zone. The mechanism or principle of operation of the feeder is as follows: the rotor blades push the powder into the gas stream, the particles are heated and stick to the treated surface. The powder is fed through a separate nozzle. In total, three nozzles are installed in the gas burner: for supplying plasma, for supplying working powder and for shielding gas.
If you are using wire, it is advisable to use the standard feed mechanism of a submerged arc welding machine.
Surface preparation
Plasma surfacing and spraying of materials should be preceded by a thorough cleaning of the surface from grease stains and other contaminants. If during conventional welding it is permissible to perform only rough, surface cleaning of joints from rust and scale, then when working with gas plasma, the surface of the workpiece must be ideally (as far as possible) clean, without foreign inclusions. The thinnest oxide film is capable ofsignificantly weaken the adhesive interaction between the hardfacing and the base metal.
In order to prepare the surface for surfacing, it is recommended to remove an insignificant surface layer of metal by machining by cutting, followed by degreasing. If the dimensions of the part allow, it is recommended to wash and clean the surfaces in an ultrasonic bath.
Important features of metal surfacing
There are several options and methods for plasma surfacing. The use of wire as a material for surfacing significantly increases the productivity of the process compared to powders. This is due to the fact that the electrode (wire) acts as an anode, which contributes to a much faster heating of the deposited material, which means that it allows you to adjust the processing modes upwards.
However, the quality of the coating and adhesion properties are clearly on the side of powder additives. The use of fine metal particles makes it possible to obtain a uniform layer of any thickness on the surface.
Surfacing powder
The use of powder surfacing is preferable in terms of the quality of the resulting surfaces and wear resistance, so powder mixtures are increasingly being used in production. The traditional composition of the powder mixture is cob alt and nickel particles. The alloy of these metals has good mechanical properties. After processing with such a composition, the surface of the part remains perfectly smooth and there is no need for its mechanical finishing and elimination of irregularities. The fraction of powder particles is only a few micrometers.
Recommended:
Production of gas blocks: technological process, materials and equipment
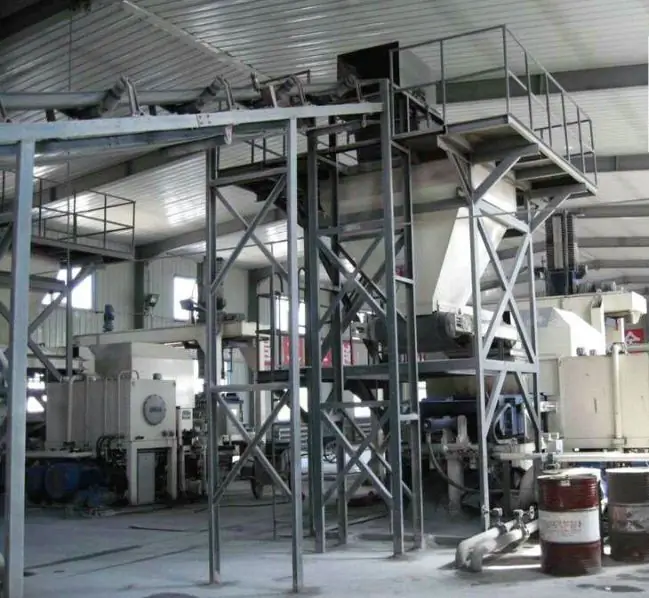
Today, there are many building materials that are popular. One of the innovations is the production of gas blocks, which belong to cellular concrete. Of these, it is profitable not only to build a private house, but also to produce for sale
Wood planing: types, equipment and process technology
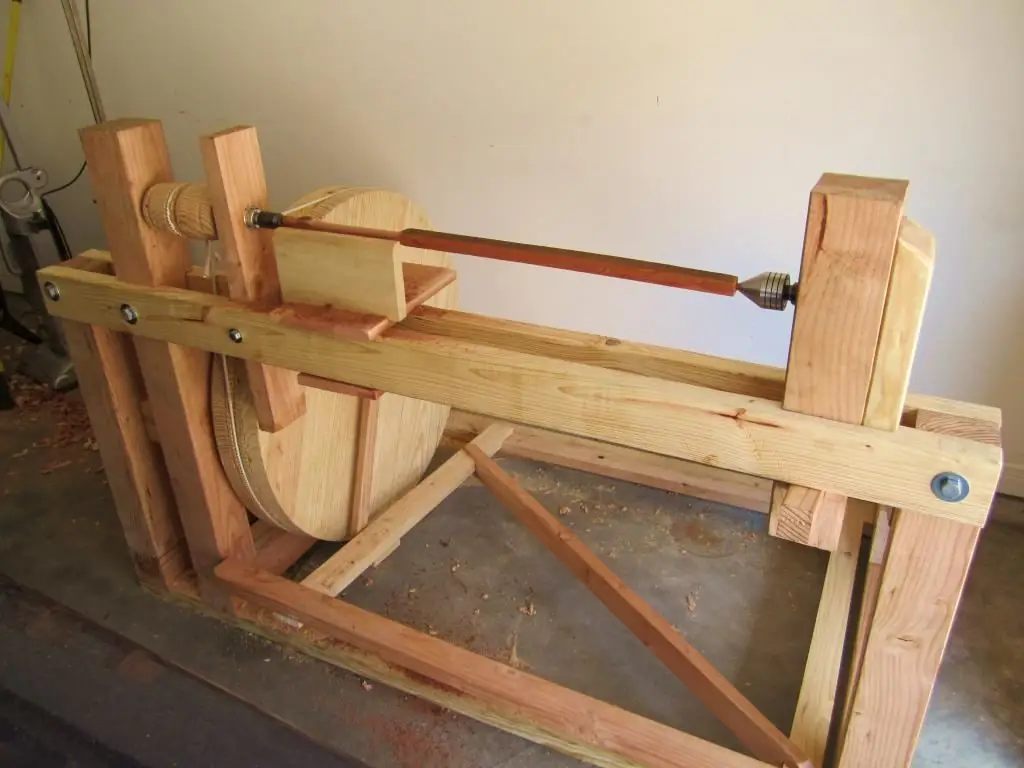
Wood planing is one of the types of processing of this material. This operation can be carried out both manually and on machines. It is important to understand that with the help of planing, any wood blank takes the desired shape and shape
Welding in a shielding gas environment: work technology, process description, execution technique, necessary materials and tools, step-by-step work instructions and expert advice
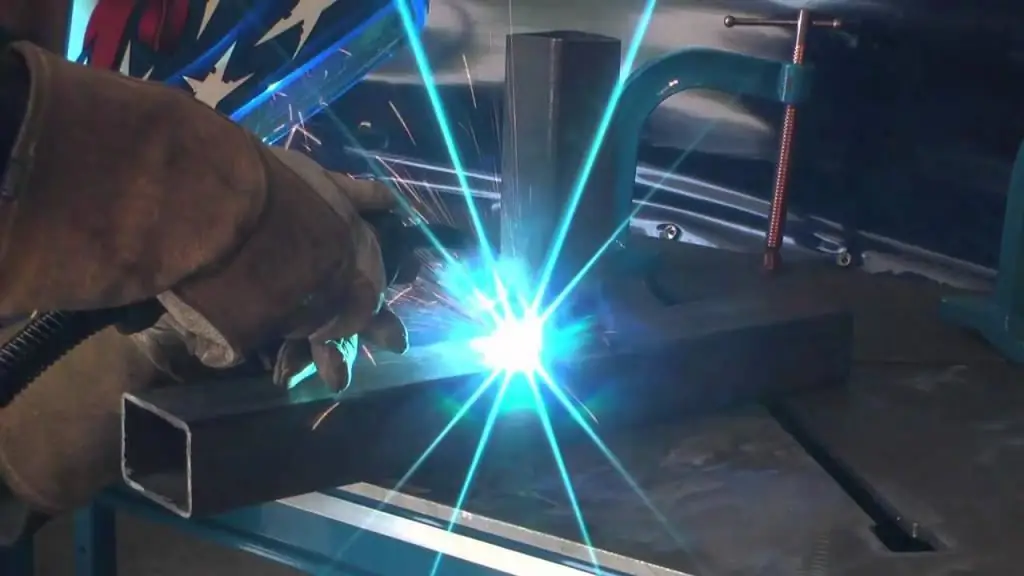
Welding technologies are used in various branches of human activity. Versatility has made welding in a protective gas environment an integral element of any production. This variety makes it easy to connect metals with a thickness of 1 mm to several centimeters in any position in space. Welding in a protective environment is gradually replacing traditional electrode welding
Butt welding: equipment, methods and process technology
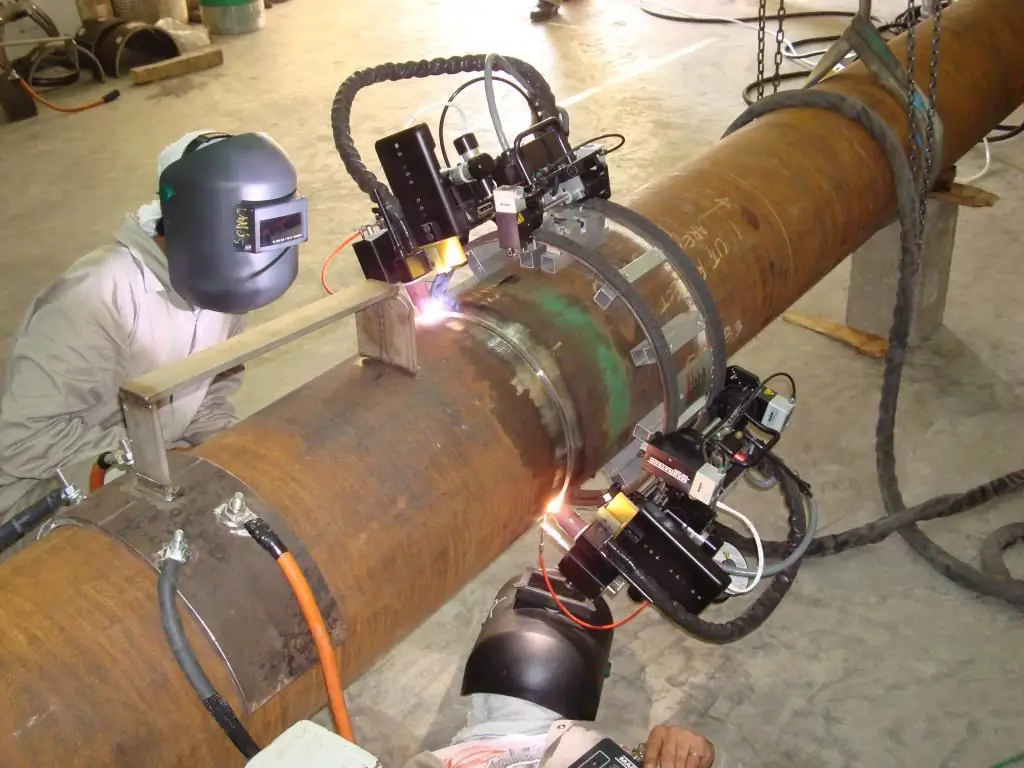
Features of flash butt welding. Types of butt welding joints, as well as equipment, methods and technology for carrying out the butt welding process. Welding seam defects arising from flash butt welding, as well as the reasons for their formation
Restoration of parts by welding and surfacing: methods and methods of restoration, features, technological process
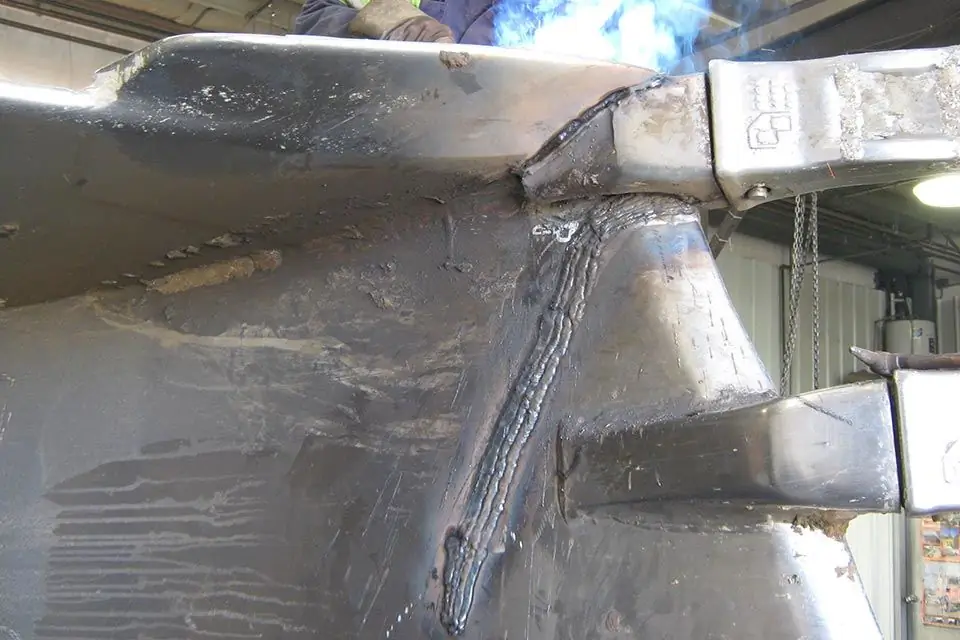
Welding and surfacing technologies allow efficient restoration of metal parts, providing a high degree of reliability and durability of the product. This is confirmed by the practice of using these methods when performing repair operations in a variety of areas - from car repairs to the production of rolled metal. In the total amount of work on the repair of metal structures, the restoration of parts by welding and surfacing takes about 60-70%