2025 Author: Howard Calhoun | [email protected]. Last modified: 2025-01-24 13:10
Serial production of parts used in the assembly of technical products and devices involves exposure to extreme temperatures and pressing. Based on these requirements, the optimal technologies for providing mechanical processing are selected. For example, in the production of volumetric and flat thin-walled elements, the use of sheet stamping is common. This method makes it possible to cope with the production of a large number of parts in one shift with a minimum load on resources at low cost. In addition, the operation of sheet stamping is beneficial in terms of the quality of the final result. The fact is that the mass production of technical elements using metal at high frequencies is rarely characterized by high-quality output. In this case, special manufacturing conditions also ensure that the material is endowed with optimal properties for future use.
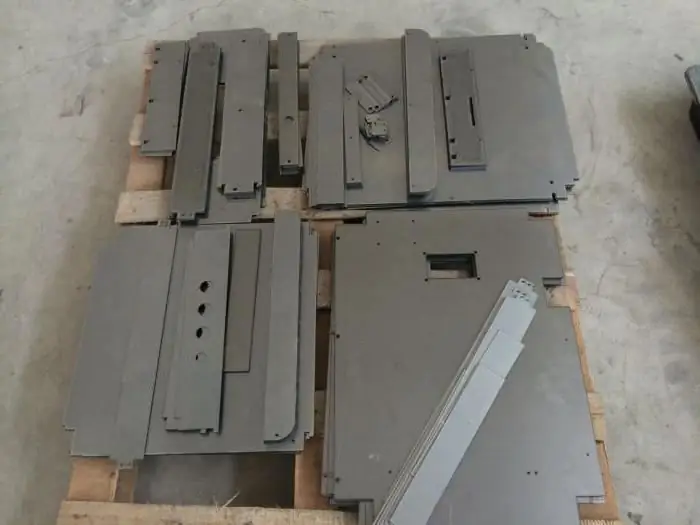
General information about the stamping process
To obtain thin-walled axisymmetric parts, modern methods of shaping are used. In particular, such methods make it possible to work with tapered and truncated products. Most often, these methodsimply the use of tools for plastic deformation of thin-walled workpieces in special environments. For example, sheet metal stamping can be performed under all-round air tension. That is, in addition to the means of mechanical action, technologists also provide for physico-chemical processes that are beneficial from the point of view of molding, affecting the source material.
As for the stamping itself, this process allows you to work with metals, providing various shaping at the output in accordance with the tasks of the project. Actually sheet stamping is only a variety of the general technology of plastic deformation. Unlike equipment for volumetric processing, this technique involves working with thin-walled workpieces, which also determines lower labor costs in the process of providing mechanical force. However, the features of the method do not end there.
Features of sheet stamping
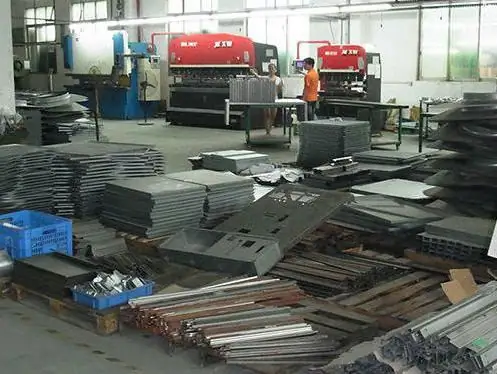
Since the technical means by which this type of stamping process is ensured involve working with thin sheets of blanks, the main emphasis is on forming operations. That is, operators perform work on bending, twisting and clamping the material, allowing the product to be formed at the output of the required shape. Forging tools will not cope with such actions - or, at least, will perform such work with less quality. There is another feature that sheet stamping has in the traditional sense. Yet again,if volumetric processing focuses on force, then in this case it is not the main one. This explains the variety of materials with which the sheet stamping method works. So, in addition to metal, manufacturers also process cardboard, ebonite, plastics, leather, rubber, fiber and blanks from other raw materials.
Cold sheet forming technology
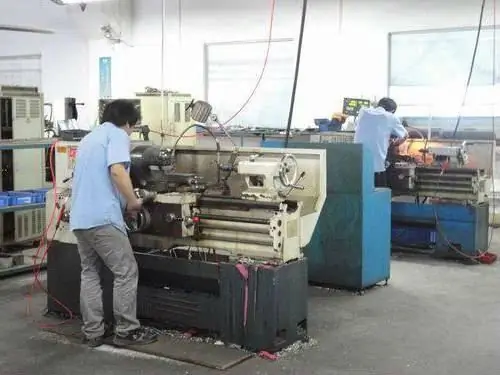
Almost all alternative stamping methods are divided into cold and hot methods. In the case of sheet stamping, it is mainly cold working. Rolled metal is used as a workpiece in the form of a tape or strip, which can initially be rolled into a roll. Further, through a special supply equipment or without it, the material enters the work site, where the main technological processes are carried out. If we are talking about metal, then the workpiece can be subjected to significant plastic deformation. That is, it is desirable that the starting material itself has sufficient plasticity qualities. At the output, cold stamping of sheet metal allows the formation of high-quality spatial and flat parts. Finished products of this kind are used in many industries, including instrumentation and electrical production.
Sheet Stamping Operations
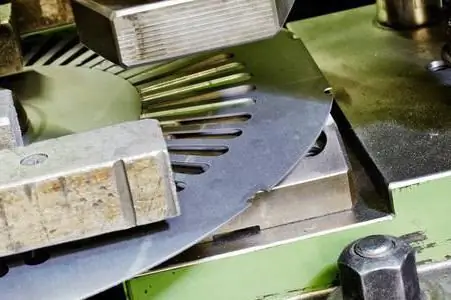
Despite the high efficiency of forming operations, the basis of the workflow at most enterprises ismechanical processing through cutting, punching and punching. Particularly, it is common to separate a portion of a workpiece along a curved or straight line. Cutting is carried out by various types of scissor installations. This technique allows cutting metal layers to obtain strips of the desired size. By the way, if volumetric processing makes it possible to work with hard and thick metals, then sheet stamping in terms of mechanical cutting is highly accurate. In practice, this means obtaining products with parameters that are optimally suited for use in further assembly. The same applies to felling and punching operations.
Mechanism of the forming process
The method of manufacturing axisymmetric elements often involves deformation by sectional expanding punches. At the same time, the formed parts after the process of stamping around the circumference may have a cut that is unacceptable from the point of view of further use of the product. That is, when performing bending, twisting and compression operations, the task is also to exclude additional refinement as much as possible. In other words, a part ready for final use must be produced in one production and molding cycle. Sheet metal stamping dies, the parameters of which correspond to the requirements of the design solution, help to achieve high quality in the formation of parts. Technically, the workflow is carried out using a matrix, an active punch, sliding sectors and auxiliary equipment, through which the workpiece is affected.
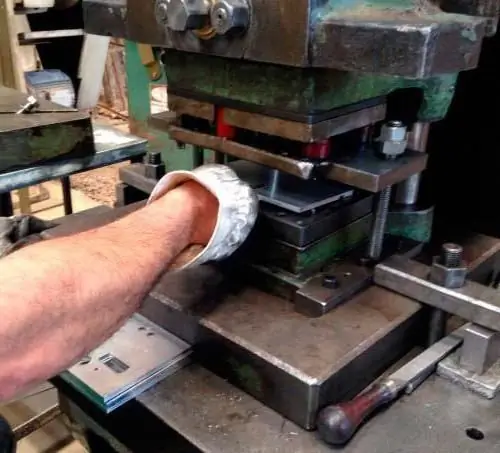
Applied equipment
Most often used are small production complexes, which are multifunctional lines for processing sheet metal. But even an ordinary private master can organize a similar line of individual components in a small room. The workflow will require the mentioned stamp, made of tool steel. It is important to use tooling made of high-strength steels, otherwise it will not last long. The basis for the operating function will be the press, which will provide the basic operations of cutting, cutting and forming. Sometimes, in order to reduce the cost of the technical organization of production, some components of the production line are replaced by improvised devices. For example, the sheet metal stamping process can also be performed using a container of water to replace the basic punch hole.
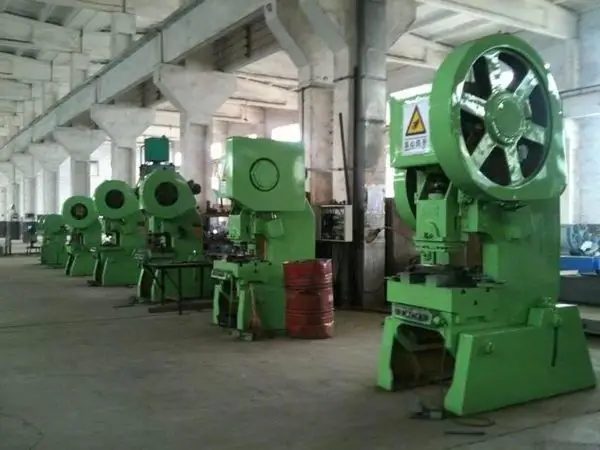
Product characteristics
The method allows you to form high quality products, which is expressed in precise dimensions and even geometric lines. Experts note that only this technology forms flat metal parts, the thickness of which practically does not change compared to blanks. Products produced by sheet stamping are distinguished by magnetic and electrical conductivity. This means that the parts can be used in the electrical industry, performing the functions of current conductors. Depending on the source material, manufacturers can endow the final parts with high strength,optimum viscosity and heat resistance.
Method advantages
In addition to the favorable technical and operational qualities of products produced by this technique, it is advisable to use this approach to processing materials for economic reasons. The fact is that a wide variety of materials that can be subjected to such processing determines the versatility of the method. Although there are obvious limitations on the use of solid and bulk blanks, the range of the same rolled metal is quite wide. At the same time, stamping of sheet metal parts is a traditional means of machining that does not require high investments. It is not difficult to organize a powerful and productive stamp if you have basic skills in the metalworking industry.
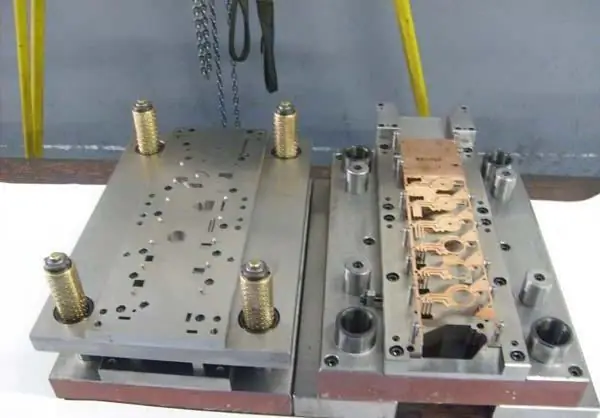
Conclusion
When evaluating the effectiveness of a particular method of metal processing, performance indicators of the resulting products are less and less coming to the fore. This is because plasma, waterjet and laser machines have virtually eliminated all barriers to achieving high precision cutting. And it is clear that in terms of the quality of their products, they are noticeably inferior to a conventional metalworking machine. Nevertheless, sheet metal stamping of parts significantly minimizes this gap, allowing you to retain the advantages of traditional equipment. These advantages in many cases are of great importance for enterprises, since they are expressed both in reducing the financial costs of processing and in simplifying theproduction organization process. Suffice it to say that, unlike abrasive cutting, stamping does not require the supply of consumables in the form of sand and water.
Recommended:
Foil stamping at home. Cold and hot foil stamping
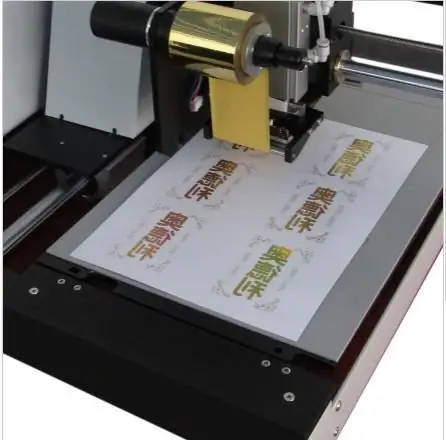
In order to make a gift or souvenir original and unusual, such an operation as foil stamping is often used. Also, using this printing technology, “wearable” leather items are often decorated, logos are applied to branded products, advertising panels are made, etc. If you wish, you can do embossing with thin metal yourself
Liquidation balance sheet is Definition of the concept, approval, form and sample of filling out the liquidation balance sheet
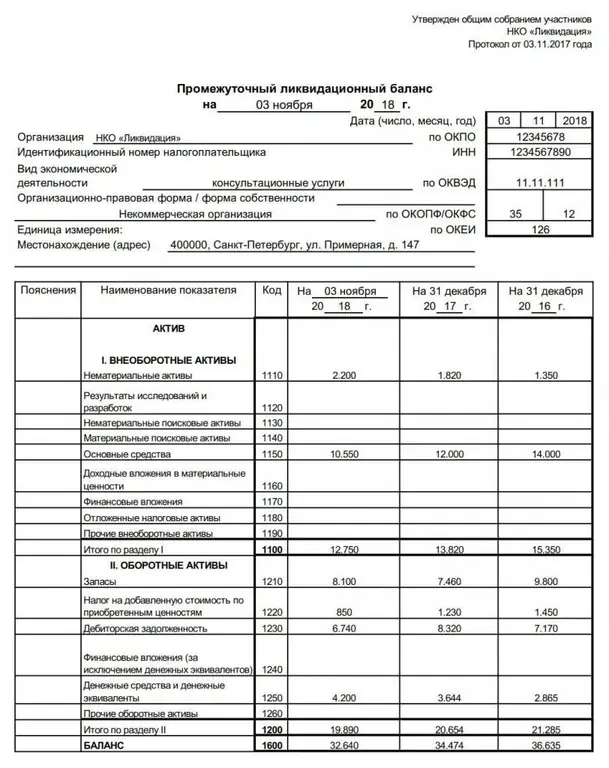
The liquidation balance sheet is an important financial act drawn up during the closing of an organization. It can be intermediate or final. The article tells what is the purpose of these documents, what information is entered into them, as well as how and when they are approved and submitted to the Federal Tax Service
Stamping is a metalworking process. Types of stamping and equipment
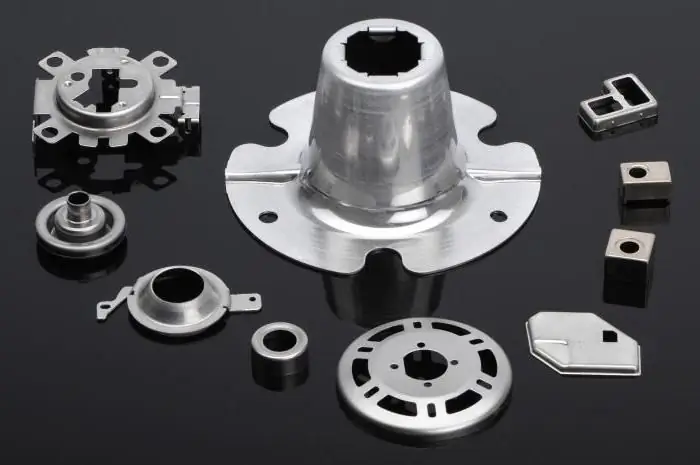
The technological process in which workpieces are processed, which makes it possible to obtain flat or voluminous finished products of various shapes and sizes, is stamping. The working tool for this purpose is a stamp, which is fixed on a press or other equipment. Stamping is two types of technology that, depending on the conditions, are performed in a hot or cold way, and therefore both equipment and technological standards differ from each other
Chrome plating parts. Chrome parts in Moscow. Chrome parts in St. Petersburg
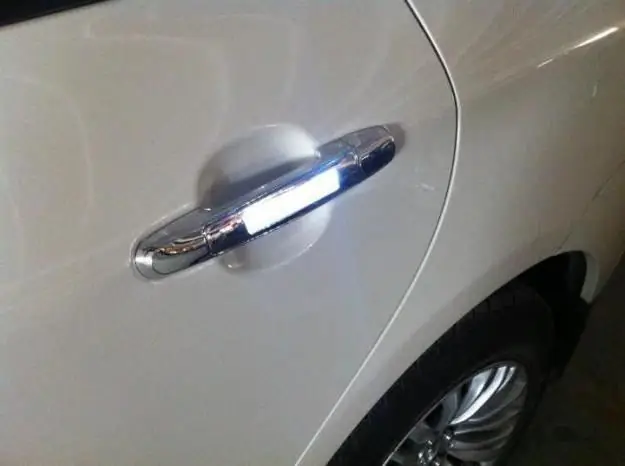
Chrome plating of parts is an opportunity to give them a new life and make them more reliable and of high quality in operation
Restoration of parts by welding and surfacing: methods and methods of restoration, features, technological process
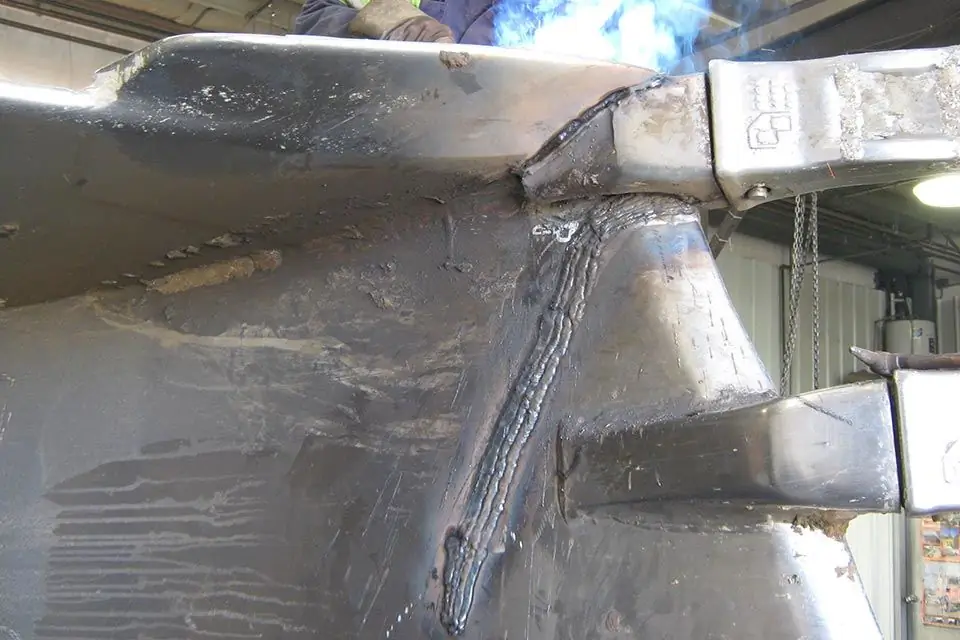
Welding and surfacing technologies allow efficient restoration of metal parts, providing a high degree of reliability and durability of the product. This is confirmed by the practice of using these methods when performing repair operations in a variety of areas - from car repairs to the production of rolled metal. In the total amount of work on the repair of metal structures, the restoration of parts by welding and surfacing takes about 60-70%