2025 Author: Howard Calhoun | [email protected]. Last modified: 2025-01-24 13:10
Production of gas blocks is currently quite profitable. The material belongs to the group of cellular concrete. This means that most of it is filled with gas bubbles, which significantly reduces their physical weight. At the same time, they have good thermal insulation characteristics and strength parameters. Thanks to the listed characteristics, gas blocks have become quite popular in a short time.
General information about gas blocks
If we talk about what constitutes aerated concrete or a gas block, then this is a stone of artificial origin, which is characterized by the presence of a large number of microscopic pores. This material is also quite often called autoclaved cellular concrete, which gives an idea of the technology for the production of gas blocks.
It is worth noting that the building material also has a high energy saving rate. This is explained by the presence of the same porous structure. Another good advantage is the small weight of each block.
The production of gas blocks has become widely popular also because of themit is possible to erect not only partitions for structures, but also load-bearing walls. It will not be possible to use such cellular concrete in industrial construction or in the construction of high-rise buildings. The main area of use is private construction. In this case, one more advantage can be distinguished, which is that the blocks do not exert strong pressure on the foundation, since they weigh quite a bit. This helps to save significant funds on the arrangement of the foundation.
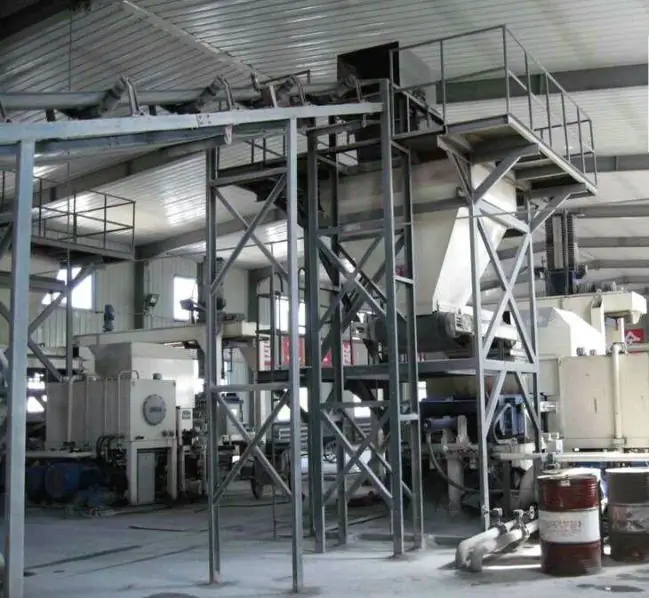
Aerated concrete materials
All the advantages mentioned above are due to the materials that serve as raw materials for the production of gas blocks. In fact, all three components are necessary for the manufacture of the material - these are cement, quartz sand and a blowing agent, the role of which is played by aluminum powder. Although it can be said that some manufacturers still add additional elements to the composition, for example, lime or ash.
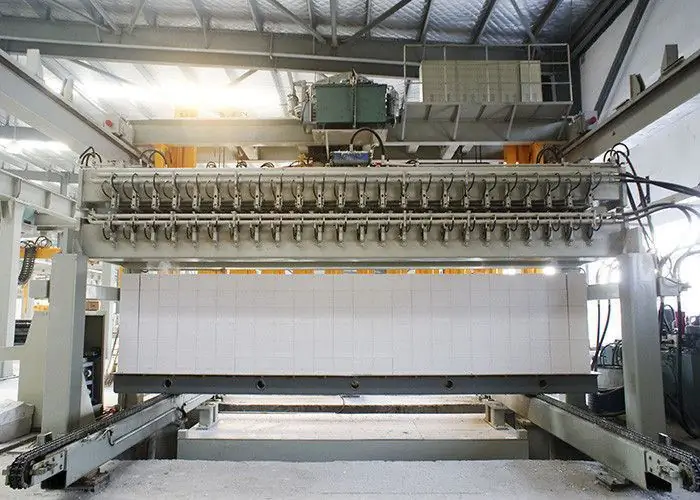
Aerated concrete production
Production of gas blocks is carried out from a group of dry materials, which are mixed with each other with the addition of water. As the latter, you can use any water of a technical type, which will be suitable according to the requirements of GOST 23732-79. When adding liquid, it is important to monitor its temperature. If it is hot enough (45 degrees Celsius), it will accelerate the hardening of the block, increasing its maximum safety factor. When it comes to industrial scale production,This will also help increase productivity. Because of these reasons, almost all companies that have gas block factories heat water before adding it to dry ingredients. Another plus of using a heated liquid is that you can save the amount of cement, since hot water stimulates the activity of dry raw materials more strongly.
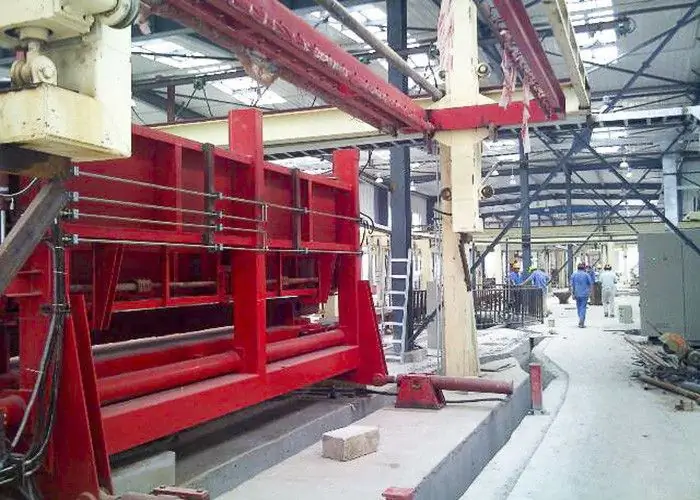
Selection of sand for production
Mini-production of gas blocks or industrial production requires careful selection of such an ingredient as sand. If we consider the issue from a theoretical point of view, then both quarry and river sand can be used. There is one most important requirement, which is that this raw material must have a minimum of silt and clay impurities. The size of sand grains also plays a significant role - no more than 2 mm.
Here it is worth highlighting the production of an autoclave gas block, since in its manufacture sand can be replaced with ingredients such as slag or ash. For example, if you use ashes from thermal power plants, then the density of the finished product will be reduced, which will reduce manufacturing costs.
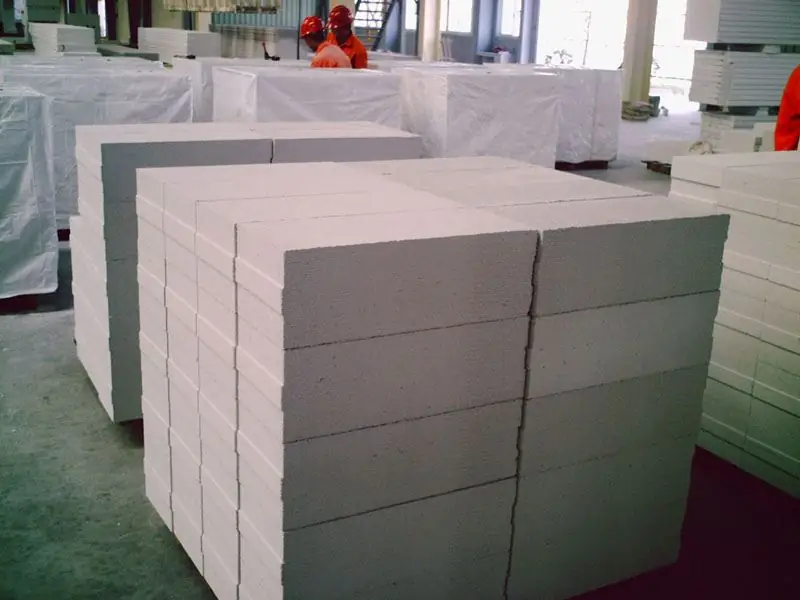
Cement and blowing agent
In order to obtain a quality product in the production of gas blocks, foam blocks and other cellular concrete, it is necessary to use cement brands such as M400 or M500. The best option would be to choose the raw material that fully complies with GOST 10178-85 in its characteristics. Concerninggasifier, then usually aluminum powder is chosen either of the PAP-1 brand or the PAP-2 brand. In rare cases, not powder, but a special paste is chosen as a blowing agent. It is worth noting that a suspension can also be used, since it is not always convenient to knead the powdered material.
The essence of the action of the powder is as follows. Aluminum will react with cement or lime mortar, which has the properties of alkali. During this process, elements such as calcium s alts (aluminates) and gaseous hydrogen are formed. These two substances will form the pores, making the structure match.
In order to create a quality product, it is very important to choose the right proportions of each component. To date, there are general recommendations on the technology for the production of aerated concrete blocks: from 50 to 70% of cement of the total mass, from 0.04 to 0.09% of the aluminum mixture, and also from 20 to 40% of sand raw materials. Additionally, technical water from 0.25 to 0.8% and lime from 1 to 5% will be required. In other words, for example, to get 1 cubic meter of a product, you must have: 90 kg of cement, water up to 300 liters, 375 kg of sand and 35 kg of lime. The amount of aluminum powder is only 0.5 kg.
Although it is important to understand that these are just general composition recommendations. The number of components can be adjusted already in production, depending on the desired end result.
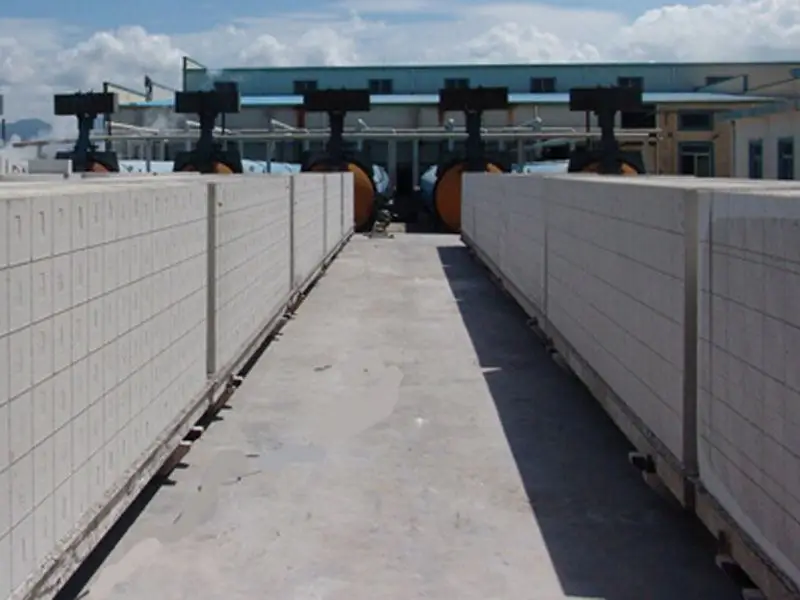
What do you need for production?
As for the production technology, itsimple enough. However, despite this, home methods or equipment will not work here. In this case, you will have to buy a special machine for the production of gas blocks, if you need to make cellular concrete for your own purposes.
However, you should understand that it will not be possible to purchase just one machine. The equipment is integrated into the production line of aerated concrete blocks. This is a kind of mini-factory. When purchasing such equipment from the manufacturer, you can get the services of a specialist who will help you figure out and set up the technological process, tell you how to choose the right components and their quantity.
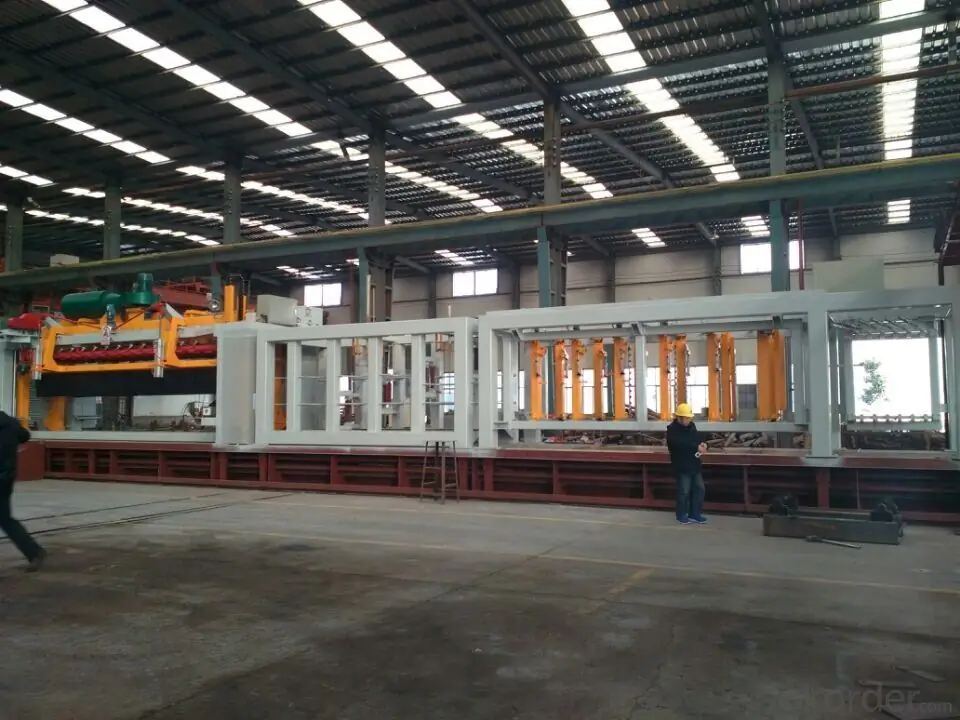
Varieties of equipment
Making fixtures are currently divided into several types. The main criterion for choosing one of them is the required productivity per day. It is also very important to understand how many people will serve such a line.
The first type of equipment is stationary. The daily output of such a line is 60 cubic meters. Most often, a warehouse or production facility is used for its placement, the total area of which is at least 500 m22. The main feature is that the molds move to a stationary mixer, where they will be filled with mortar. After that, all other technological stages of production are carried out. Only one additional worker is required to successfully operate the line.
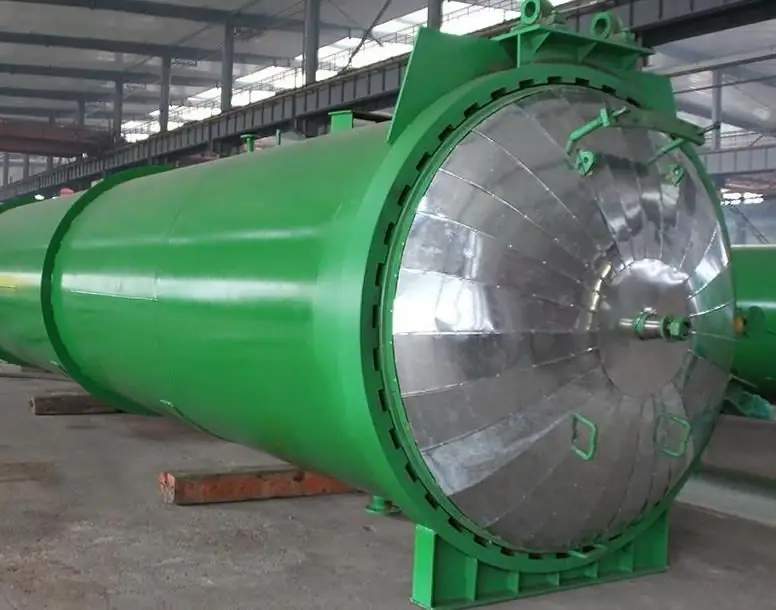
Conveyor equipment
Conveyor lines are equipped where it is necessary to significantly increase productivity. This parameter of such a complex is 75-150 cubic meters per day. In this case, the pace of production is faster, only the duration of the solidification of the blocks does not change, since this does not depend on the line. However, along with this, much more space is required than for stationary equipment. In addition, a minimum of 8 people are involved in the service, despite the fact that most of the procedures take place automatically.
Small complexes
As for mini-lines for production, these are the most inefficient plants, only 15 cubic meters per day. They differ from stationary complexes in that it is not the form that advances here, but the mixer. This greatly reduces the required amount of space to 140-160 m2. Most often, they are purchased as a starter option for a gas block production line.
There is another separate type, which is called mobile installations. They are used only during private construction. It is worth noting that, according to the calculations of specialists, such installations pay off quite quickly. In addition, they help save construction costs by about 30%. The peculiarity of mobile units is that they come with a compressor, and they can work even when connected to a regular home electrical network.
Production steps
It is important to note here that aerated concrete can be autoclaved and non-autoclaved. The difference is thatthe second option is cheaper, but its strength characteristics are also less. However, due to the fact that the cost of production is much lower, it is widely popular. For this reason, it is worth considering the stages of material production.
- The first stage is, of course, the selection of all the necessary components in their exact dosage. After that, they must be thoroughly mixed to obtain a solution. If you have the equipment, this procedure takes no more than 10 minutes.
- The second stage is that the previously prepared solution must be placed in special forms. The right equipment is used for this. It is worth knowing that you only need to fill the mold halfway, as the mixture will increase over time due to the formation of gas bubbles. As for the time, the process takes 4 hours, during which the mixture usually fills the mold completely. It also happens that there is not enough space. In this case, the excess must be removed 2 hours after loading.
- The last stage is the exposure of the finished block. This procedure takes approximately 16 hours. After that, you can deal with the demoulding of the material and its unloading on pallets. Next, you need to leave them on pallets so that they gain the so-called tempering strength. In time, this stage takes from 2 to 3 days. After this period, the blocks can be sent to the warehouse, but they can only be sold on the 28th day, since only by this time the strength will reach the desired level.
Production for sale
At the end it is worth adding that the productionaerated concrete blocks is a highly profitable business. This is clearly seen after comparing the cost and price. The cost of 1 cubic meter of finished products usually reaches 1800 rubles. As for the retail price for 1 cubic meter, it can reach 2500 rubles. As you can see, the net profit from just one cubic meter reaches 700 rubles.
Recommended:
Gas production. Gas production methods. Gas production in Russia
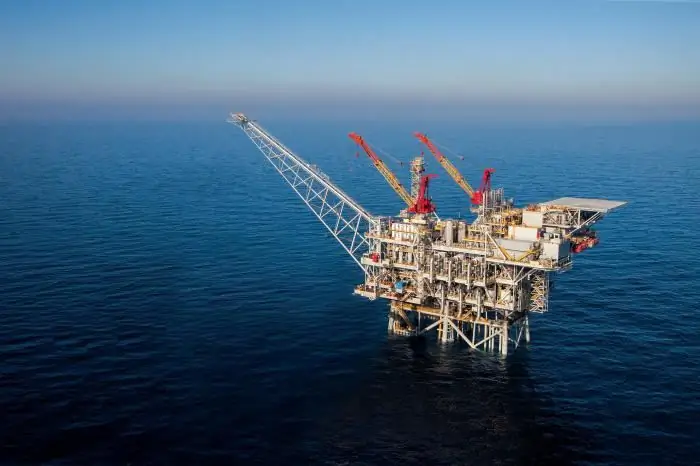
Natural gas is formed by mixing various gases in the earth's crust. In most cases, the depth of occurrence ranges from several hundred meters to a couple of kilometers. It is worth noting that gas can form at high temperatures and pressures. In this case, there is no access of oxygen to the place. To date, gas production has been implemented in several ways, each of which we will consider in this article. But let's talk about everything in order
Machines for making cinder blocks. Equipment for the production of cinder blocks
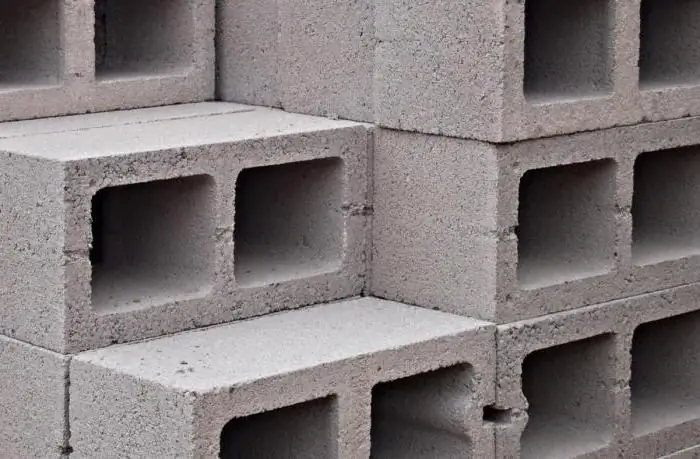
The article is devoted to the production of cinder blocks. The manufacturing technology and the equipment used are considered
Woodworking production: characteristics and technological process
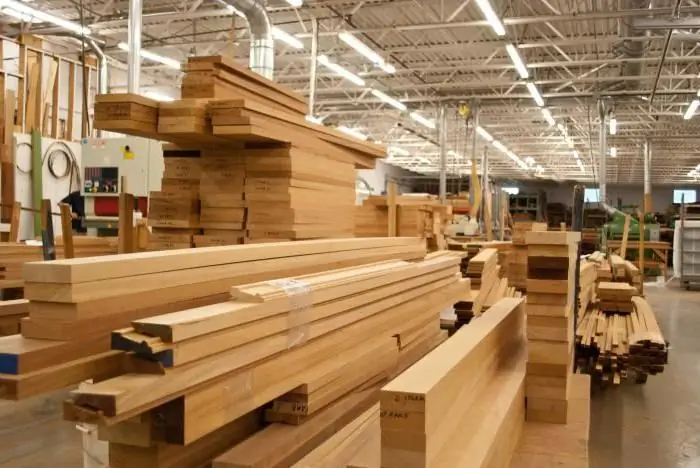
Modern woodworking production involves the use of high-tech equipment to produce high-quality lumber
Inline production is Concept, definition, methods of organization and technological process
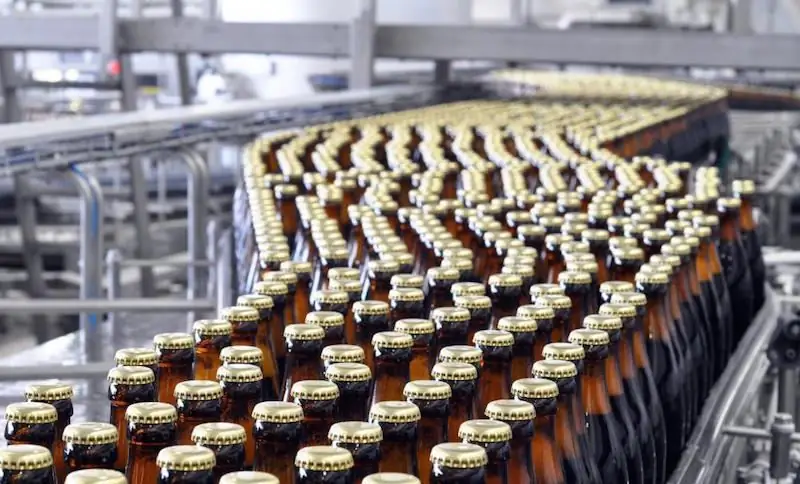
The production process is a complex technological action that can be organized in different ways and means. The work of an enterprise in the conditions of in-line production of products is today considered the most efficient, but at the same time demanding in terms of labor, organizational and material costs. In a general sense, in-line production is a format of production activity in which the principles of rhythm and repeatability of operations come to the fore
What coins are made of: materials and alloys, technological process
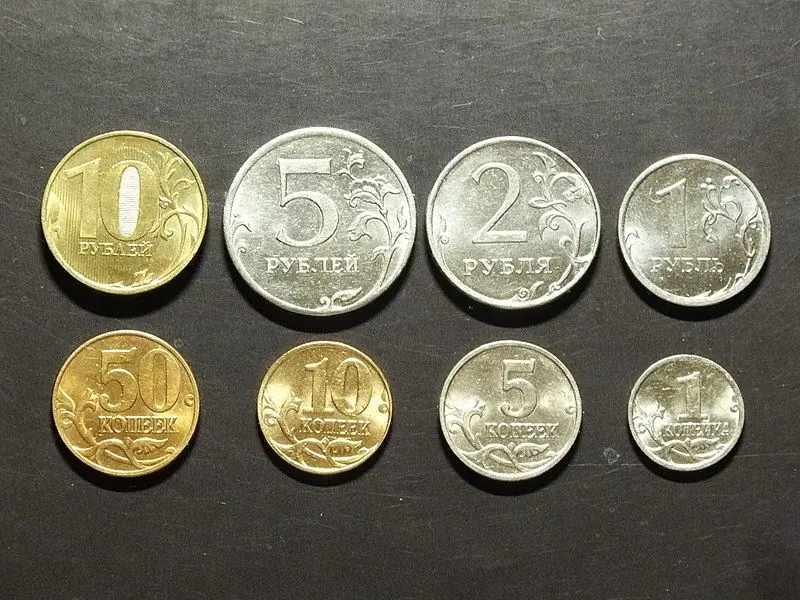
We all deal with metal money every day. Everyone will find coins in their wallet, pocket, piggy bank at home on the shelf. People pay with iron money in stores, at coffee machines and in many other places. But not many people think about how long the historical path the coin has overcome in order to appear before us today in the form in which we are used to seeing it. This article will highlight the main milestones in the development of iron money, and you will also learn how and from what coins are made