2025 Author: Howard Calhoun | [email protected]. Last modified: 2025-01-24 13:10
The entry into the market of compact devices for semi-automatic welding and their high popularity contributed to the expansion of the use of welding in almost all areas of human life. So, with the help of semi-automatic, various car body repairs are carried out. Welding is also used in industrial or private construction. With their use, various metal structures are produced.
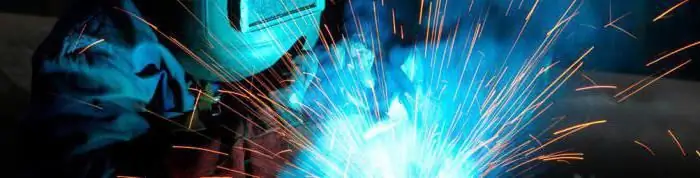
In the process of working with the device, some components tend to wear out and become unusable. One of such components of this equipment is a sleeve for a semi-automatic welding machine. During operation, the elements are subject to various external factors:
- High temperatures during welding.
- Drops of molten metal.
- Scratches.
- Various bends.
Inside the sleeve, its guides are abraded by wire,which is fed to the welding zone. Naturally, all these influences adversely affect the apparatus and disable it. Often, a sleeve for a semi-automatic welding machine breaks the very first.
Types
Modern manufacturers today offer two types of welding sleeves. It can be directly a sleeve or a burner. At the same time, the appearance of these products is no different from each other. Both of these names refer to the same accessory.
So, the semi-automatic welding torch-sleeve consists of three main elements. This is the burner itself, the sleeve, as well as the connectors for connecting them. Unfortunately, it is now difficult to find sleeves for sale separately. But you can buy almost all the components of the design or find analogues.
Device
So, the sleeve for semi-automatic welding consists of a rubber sheath. Under it is a rather complex filling. Since a special wire is needed for semi-automatic welding, a complex system is located in the welding sleeve. It is a guide channel that feeds the spiral. There may also be a Teflon tube inside. Firms that produce components for welding may have a different arrangement of the semiautomatic welding sleeve.
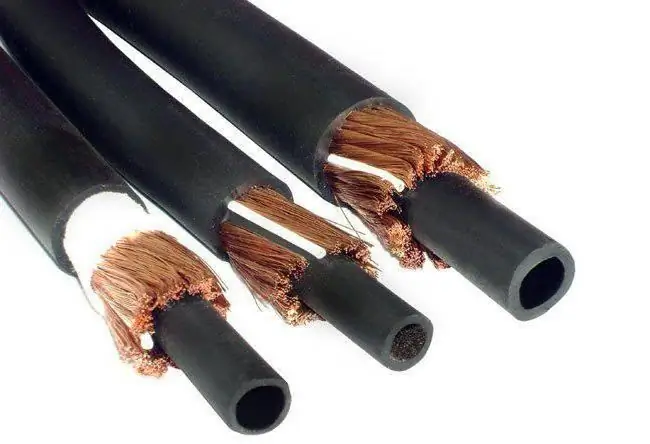
Also, the process of work requires the presence of protective gas. A separate hose is used to supply it. Depending on the brand and model of the machine, the process of transporting and supplying wire and gas to the work area may vary. Together with coaxi althere is also a parallel type.
Inside the sleeve also runs a positive power cable from the welding to the transformer. This cord goes to the current lug located on the burner. There are also two thin wires. They are connected to the start button.
Destination
A sleeve for a semi-automatic welding machine is needed to feed the wire, with the help of which the metal welding process is carried out. The component is fed through the transport mechanism. Also, the sleeve is designed to provide the burner with inert or active gases. This helps to protect the weld from the formation of oxidation. A power cable runs through the sleeve. It serves to power the welding arc; the second end goes to the start button.
Consumables
A sleeve for a semi-automatic welding machine is a consumable item, or rather, a spiral responsible for feeding the wire. This part is also called a feed channel, a guide element.
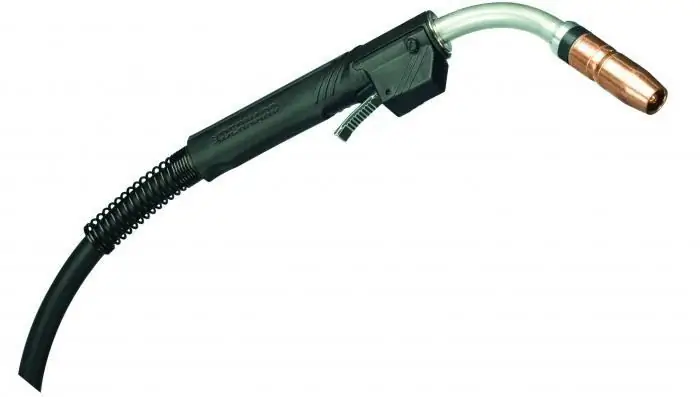
Steel wire or strip is used as materials for its production. However, the latter can also be made of plastic. The wire or tape is wound in the form of a spiral. Then it is covered on the outside with insulating materials.
Due to the fact that the wire constantly rubs against the inner surface of the sleeve, the internal elements are actively worn out. This is also facilitated by dust and dirt that gets inside along with the wire. The channel is subject to especially active wear if the work is carried out with aluminum wire. For work withTeflon tubes are used with aluminum material.
These guide channels are "consumables" that need to be replaced periodically. The gas hose must also be replaced. It is prone to tearing.
Reasons for element failure
If the sleeve of a semi-automatic welding machine with a mechanical valve is out of order or the device has received mechanical damage, the part needs to be repaired or replaced. In order not to spend extra money, you first need to diagnose the node.
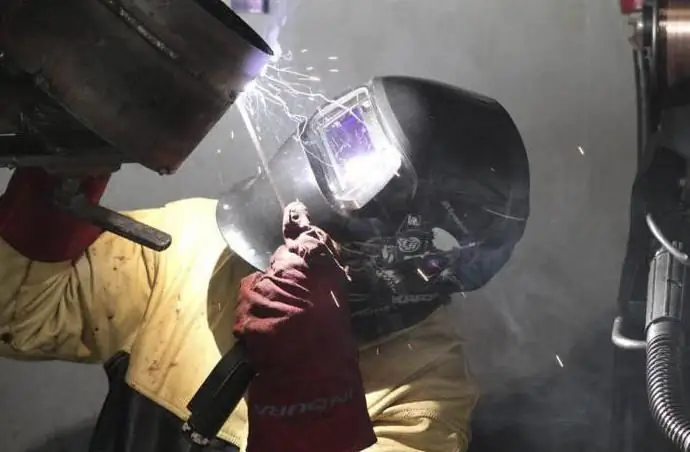
If the welding seam turns out to be of poor quality, then this directly depends on the condition of the sleeve. A bad weld can be caused by wire sticking inside the element or by not enough gas. Both reasons are the basis for replacing the sleeve separately, or together with the burner. The latter option is rarely used. More often they buy one new element, or make a welding sleeve for a semi-automatic machine with their own hands.
Market offers and prices
The cost of a part from the kit together with a burner starts from one and a half thousand rubles. The most expensive device costs about 12 thousand. Channels for transporting wire will cost a maximum of 200-400 rubles.
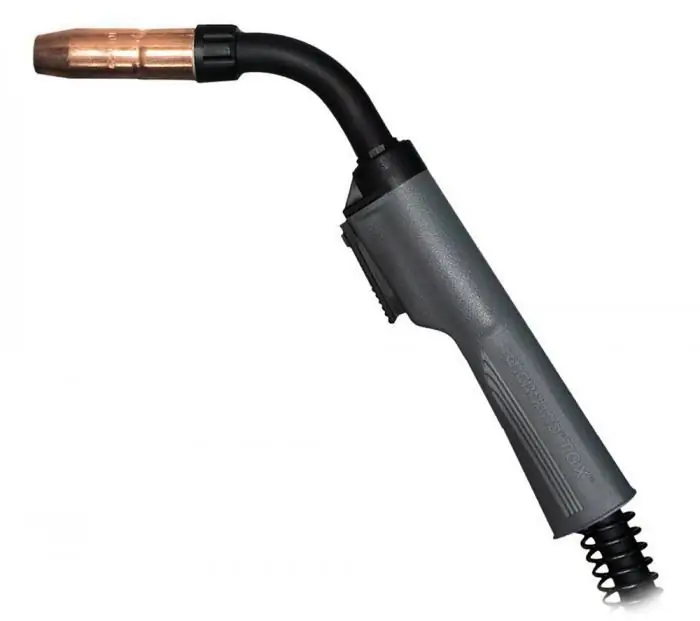
If you need a Teflon tube, then it costs a maximum of 500-1000 rubles. Sleeves of domestic production can be purchased for 20-40 rubles. for each running metre. The diameter of this hose is 6.3 mm. Therefore, it is not necessary to purchase a sleeve as a set. Frompurchased consumables, you can make an excellent home-made sleeve for a semi-automatic welding machine.
How to choose
When buying semi-automatic welding kits, there are several important factors to consider. So, you need to know the model of the device and its functions. This can be work in inert or active gas environments, argon arc welding or work with flux-cored wire. It is worth considering how the connecting elements are arranged. The most popular option is KZ-2. The ergonomic characteristics of the burner are also important. The handle should fit comfortably in the hand, and the button should be of sufficient size.
When choosing, you should pay attention to the diameter of the wire for which this or that device is intended. With ordinary welding devices, a wire with a diameter of 0.6 to 1.6 mm is used. But specific devices can work with narrower size ranges - for example, 0.2-0.6 mm.
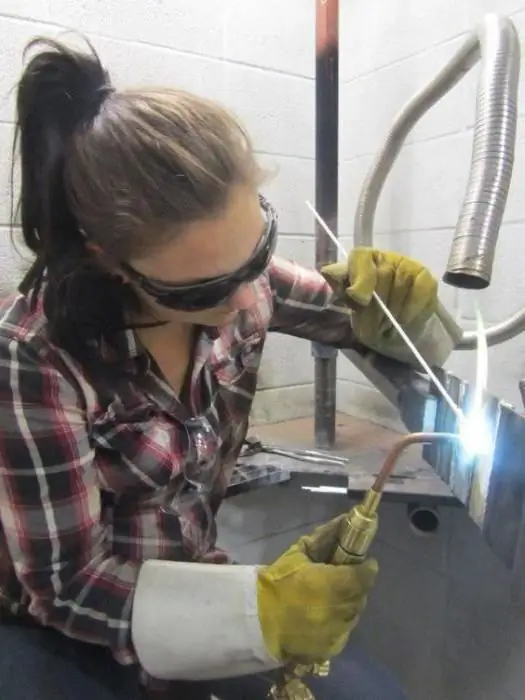
An important point when choosing is the maximum currents and the thickness of the sleeve. Optimal for any welding work - 3 mm. But on sale you can find products of longer lengths.
Gas hose selection
If it is necessary to replace not only the wire feed hose, but also the hose, it is important when choosing to pay attention to the marking and color of the element. For gases such as argon and helium, elements designed for pressures up to 0.6 MPa are used. Domestic products must be marked in accordance with GOST 9956-75. Hose for oxygen service must be class 3. Permissible working pressures of such an element are up to 2 MPa. This hose is blue.
Conclusion
This is everything you need to know about welding sleeves, replacement, selection and purchase. Home craftsmen often replace branded hoses with jackets from bicycle cables or from a speedometer cable.
Recommended:
The main consumable for welding - welding wire
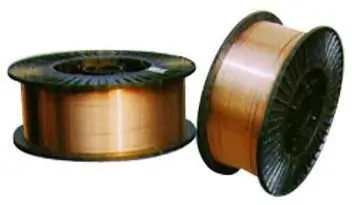
Welding wire is used in various welding operations, it is the main consumable material that acts as an electrode. Welding operations require extensive professional knowledge, a responsible approach to the choice of raw materials. For welding structures, it is unacceptable to use random wire of incomprehensible marking and unknown composition
Welding of ultrasonic plastics, plastics, metals, polymeric materials, aluminum profiles. Ultrasonic welding: technology, harmful factors
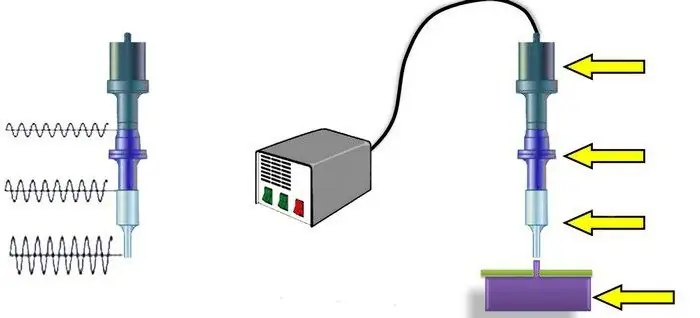
Ultrasonic welding of metals is a process during which a permanent joint is obtained in the solid phase. The formation of juvenile areas (in which bonds are formed) and the contact between them occur under the influence of a special tool
Welding consumables: definition, characteristics, manufacture, storage. Main welding material
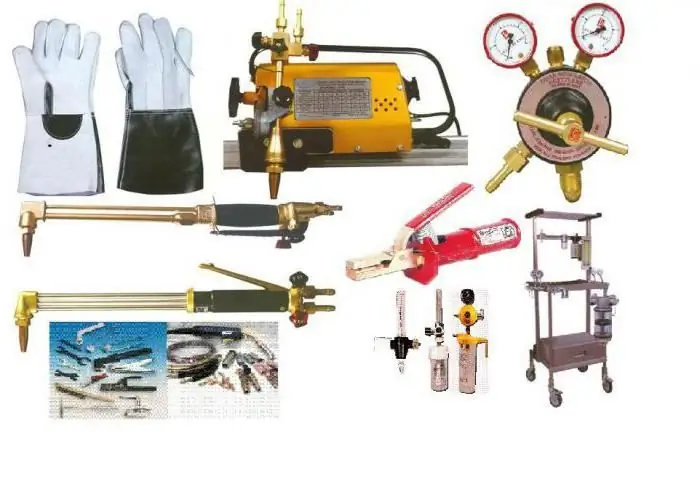
Main types of welding consumables, features of storage of explosive gases, characteristics of electrodes depending on the material and other parameters
Thermite welding: technology. The practice of thermite welding in everyday life and in the electrical industry
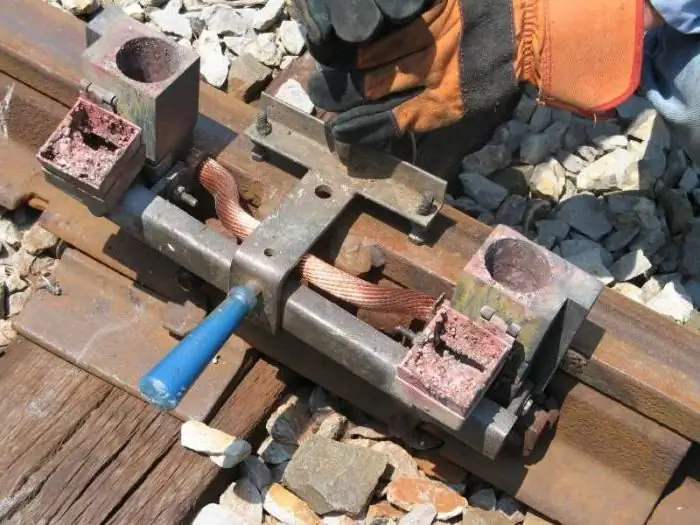
The article is devoted to thermite welding technology. The features of this method, the equipment used, the nuances of use, etc. are considered
Flux for welding: purpose, types of welding, flux composition, rules of use, GOST requirements, pros and cons of application
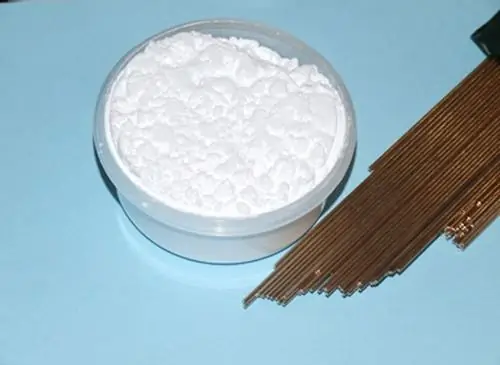
The quality of the weld is determined not only by the ability of the master to organize the arc correctly, but also by the special protection of the working area from external influences. The main enemy on the way to creating a strong and durable metal connection is the natural air environment. The weld is isolated from oxygen by a flux for welding, but this is not only its task